CompactLogix PLC Application: Tray Stacker
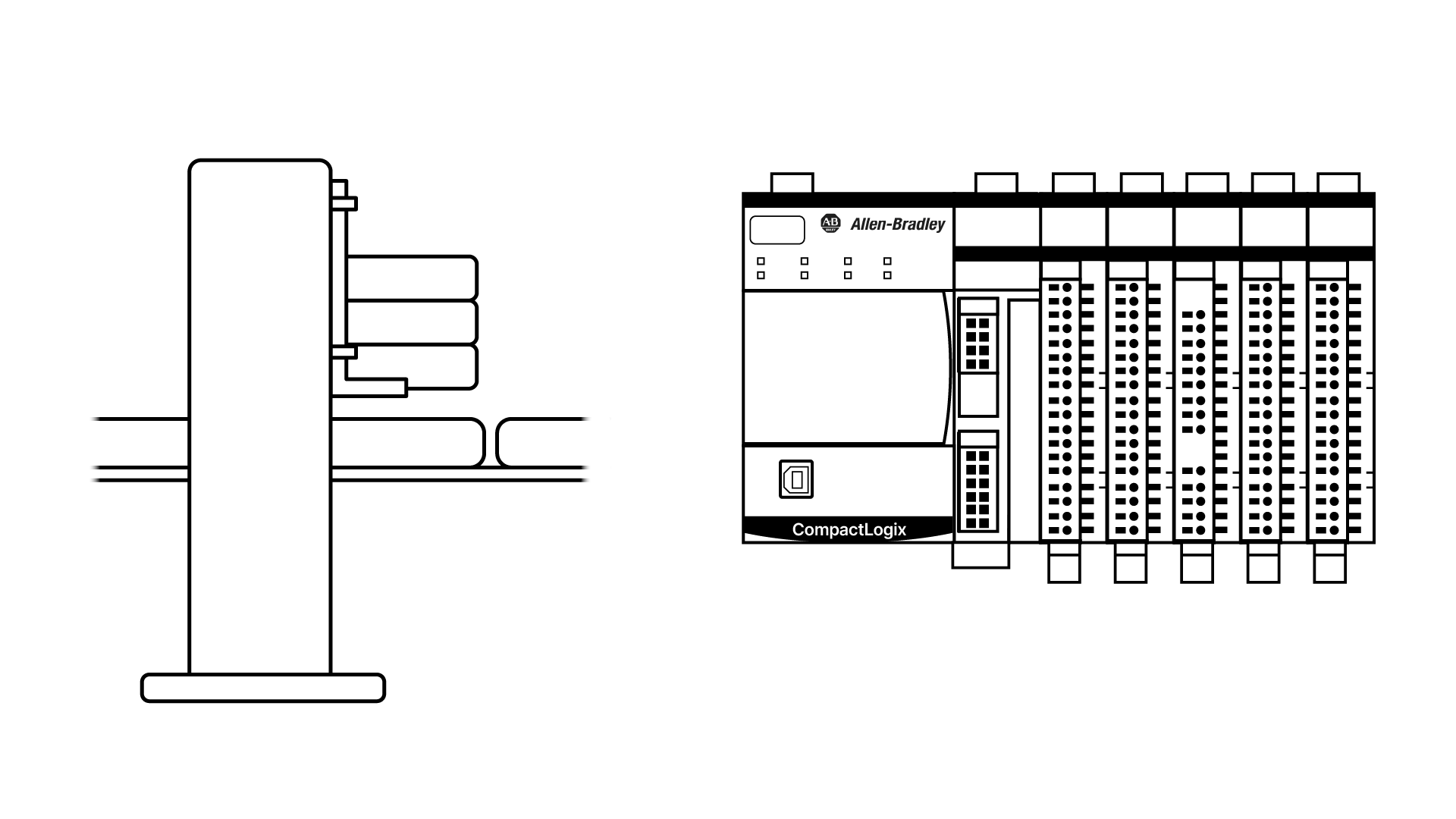
Hello and welcome back to another article from RealPars, the world’s largest online learning platform for industrial automation.
In today’s article, we will learn about Allen Bradley CompactLogix PLCs by looking at a typical application of a CompactLogix PLC. Along the way, we will see how a CompactLogix system can be used to control a mid-sized machine and what components make up a CompactLogix system.
If you want to learn more about Allen Bradley CompactLogix PLCs and how to program them using Rockwell Automation’s Studio 5000 Logix Designer software, check out the Learn Logix skill path on RealPars.
This series of courses teaches you everything you need to know to be a confident, competent PLC programmer specializing in programming Logix 5000 PLCs.
Let’s start by looking at the machine that we will break down in this article.
Tray stacker
In this article, we’ll see how a CompactLogix system can be used to control a tray stacker machine.
The tray stacker has three conveyors that are used to transport trays through the machine.
When trays are stopped on the middle conveyor, an arm is lowered and a set of actuators are used to grab the tray. Once the tray is secure, the arm lifts the tray from the conveyor to make room for the next tray.
The arm is lowered to place any currently stacked trays in the new tray and then grab the bottom tray.
This process is repeated to build a stack of trays. Once a stack is complete, it is transported out of the machine using the conveyor belts.
Now that we know what the machine does, let’s take a look and see how a CompactLogix PLC system could be used to control this machine.
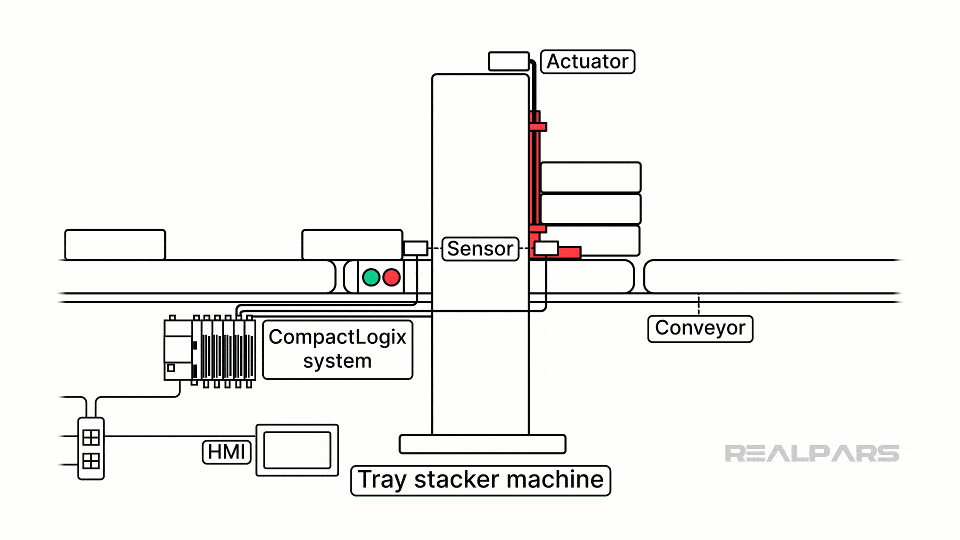
Controls
The control system for this machine is made up of a CompactLogix PLC, which controls the machine. The CompactLogix PLC is connected to several other devices to monitor and control the machine.
Let’s look at some of these devices.
I/O modules and devices
The PLC understands the state of the process by monitoring inputs from sensors and controls the process by controlling actuators.
A CompactLogix controller can be extended with I/O modules to interface with these devices. The most common types of I/O modules are digital input and digital output modules.
The sensors in the application are wired to input modules and tell the PLC important information about the process like if a button is pressed or if a tray is in position on the conveyor.
The actuators in this application are wired to output modules. The PLC controls the process by sending electrical signals to these devices. Using these electrical signals, the PLC can control the actuators to grab the tray or sound a horn to warn operators that the machine is about to start.
Variable Frequency Drives
Variable frequency drives are devices that are used to control motors. In this application, PowerFlex variable frequency drives are used to control the motors because they are designed to be integrated easily into CompactLogix systems.
The PLC sends commands to the variable frequency drives over EtherNet/IP, an industrial network, to run the conveyors. The drive also sends status information back to the PLC to tell the PLC if the motor is running or if the drive has a fault.
If you want to learn more about variable frequency drives, check out the RealPars article Variable Frequency Drives explained.
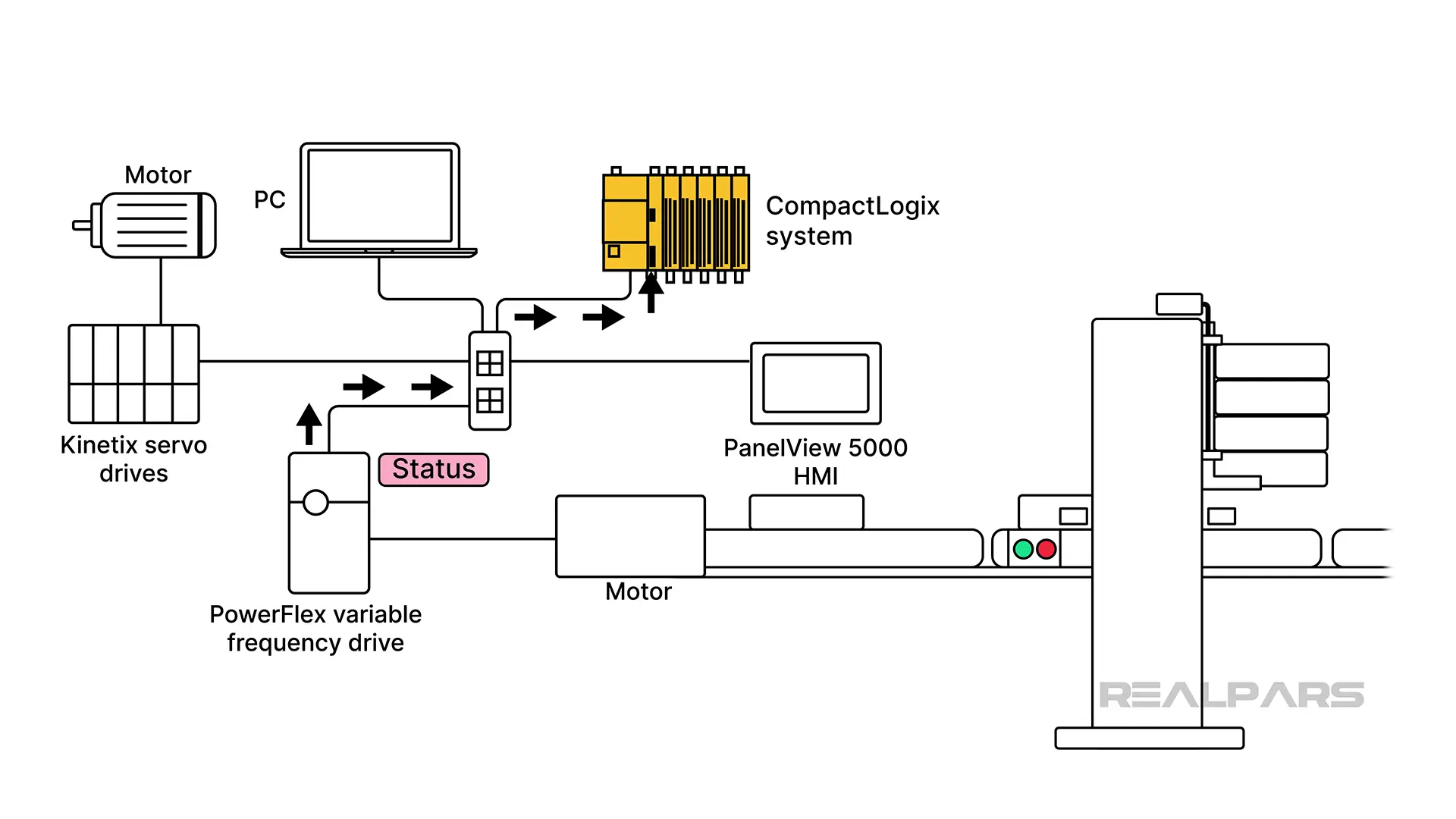
Servo drives
Variable frequency drives are used when you want to control the speed of a motor and servo drives are used when you want to control the position of a motor.
In this application, the lifting arm has to move to a precise position to lift the stack of trays from the conveyor belt. For this positioning application, an Allen Bradley Kinetix servo drive is used.
Just like PowerFlex variable frequency drives, Kinetix servo drives are designed to integrate easily into CompactLogix systems over an EtherNet/IP network.
When the PLC wants to move the lifting arm, it sends a position command to the servo drive and the servo drive moves the arm to the correct position. The drive sends the PLC back information about its status and current position so that the PLC knows when the arm is in position.
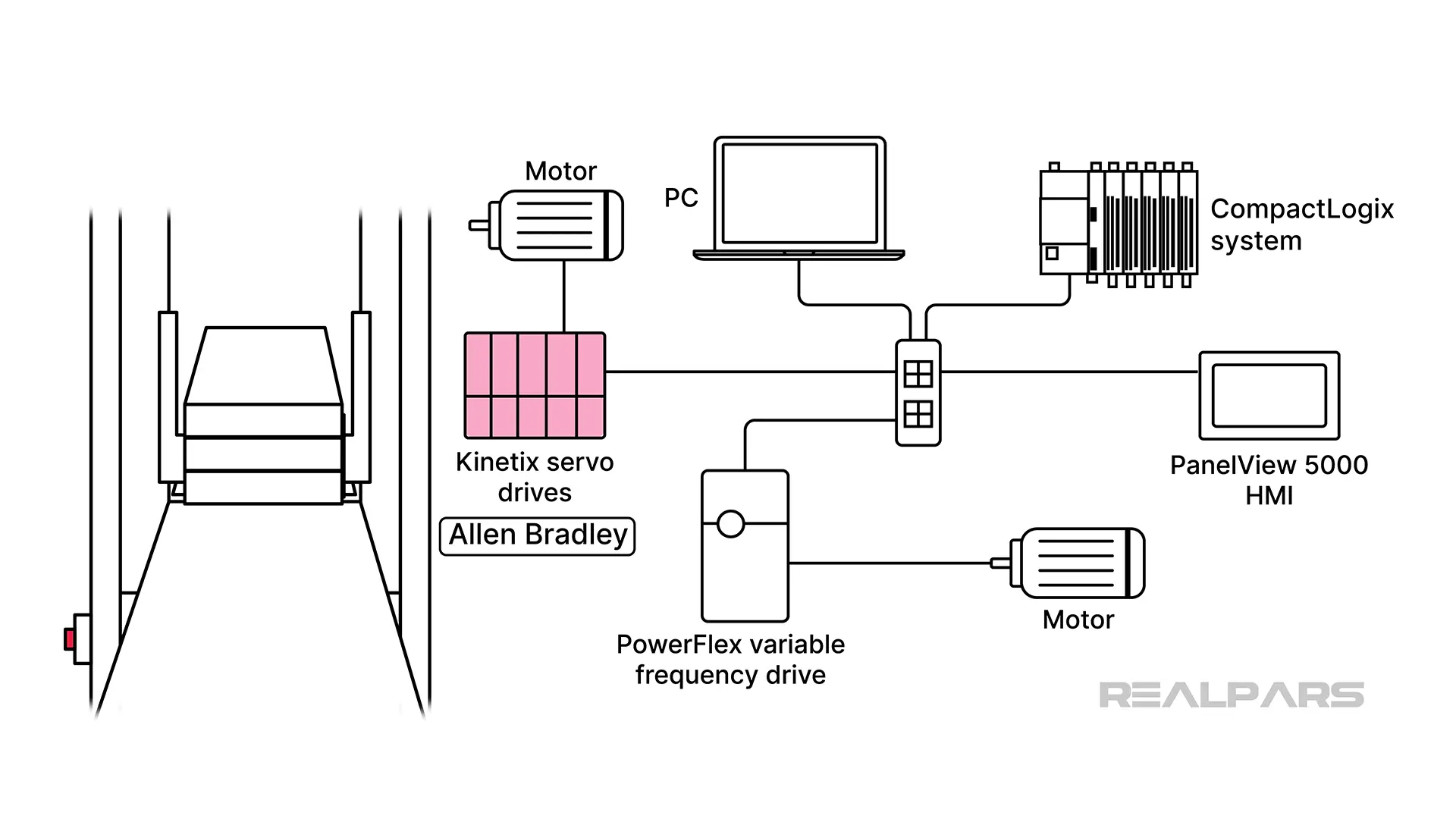
HMI
The machine is equipped with a Human Machine Interface, also known as an HMI. In this case, a PanelView 5000 HMI is used and communicates with the PLC over an EtherNet/IP network.
This device is a touchscreen terminal that lets an operator see the status of the machine and send commands to the PLC. Some common commands may be reset to reset a fault, start to start running the machine, and stop to stop the machine.
An HMI may also have additional screens that are only accessible by maintenance or engineering staff that are used to troubleshoot the machine or modify the behavior of the machine.
To learn more about HMIs in industrial automation, check out the RealPars article What is an HMI?
Safety devices
Finally, safety devices are used to ensure that the machine can stop safely in case of an emergency.
Although there are safety-rated CompactLogix PLCs available, mid-sized machines like this one often use hardwired safety equipment.
With hardwired safety, the PLC doesn’t control the safety logic. Instead, safety devices like emergency stops and safety light curtains are connected to safety relays which inhibit movement of the machine when a safety event has occurred.
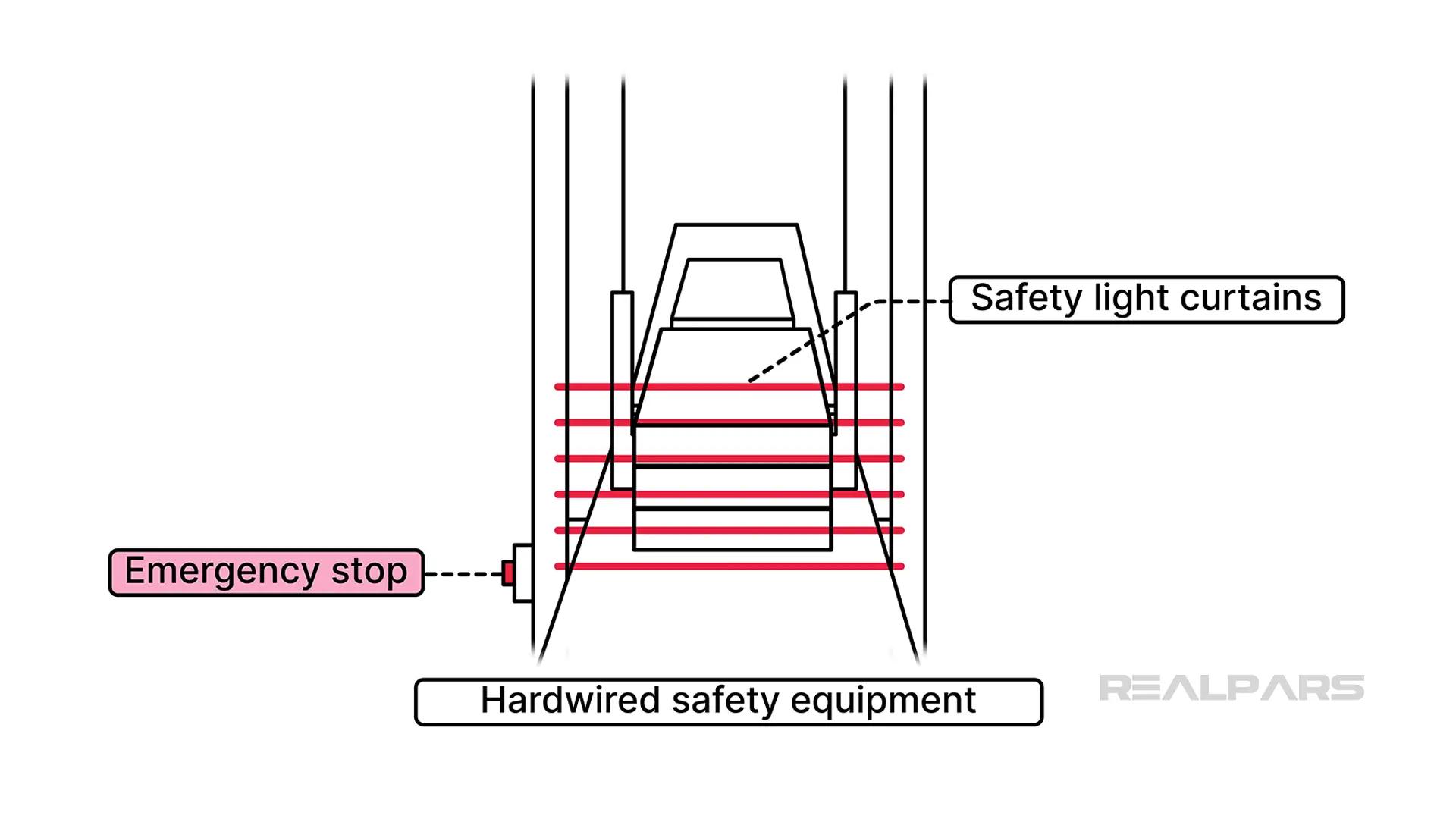
Conclusion
In this article, we saw a typical application of a CompactLogix PLC system and the components that make up a CompactLogix PLC system.
As you can see, there is much more to controlling a machine than just the logic in the PLC. Many devices have to work together in harmony including sensors and actuators, variable frequency drives, servo drives, and HMIs.
Although controls engineers need to understand how to configure and program these other devices, the most important skill that you can have as a controls engineer is PLC programming since PLCs are at the heart of every automation project.
If you want to learn how to program Allen Bradley CompactLogix PLCs using Studio 5000 Logix Designer, don't forget to check out the Learn Logix skill path.
This skill path will teach you everything you need to know to be a confident, competent PLC programmer with an Allen Bradley specialization.
Learn from Industry Experts
With a 7-day trial, then €25/month