OPC-UA Application - Oil & Gas
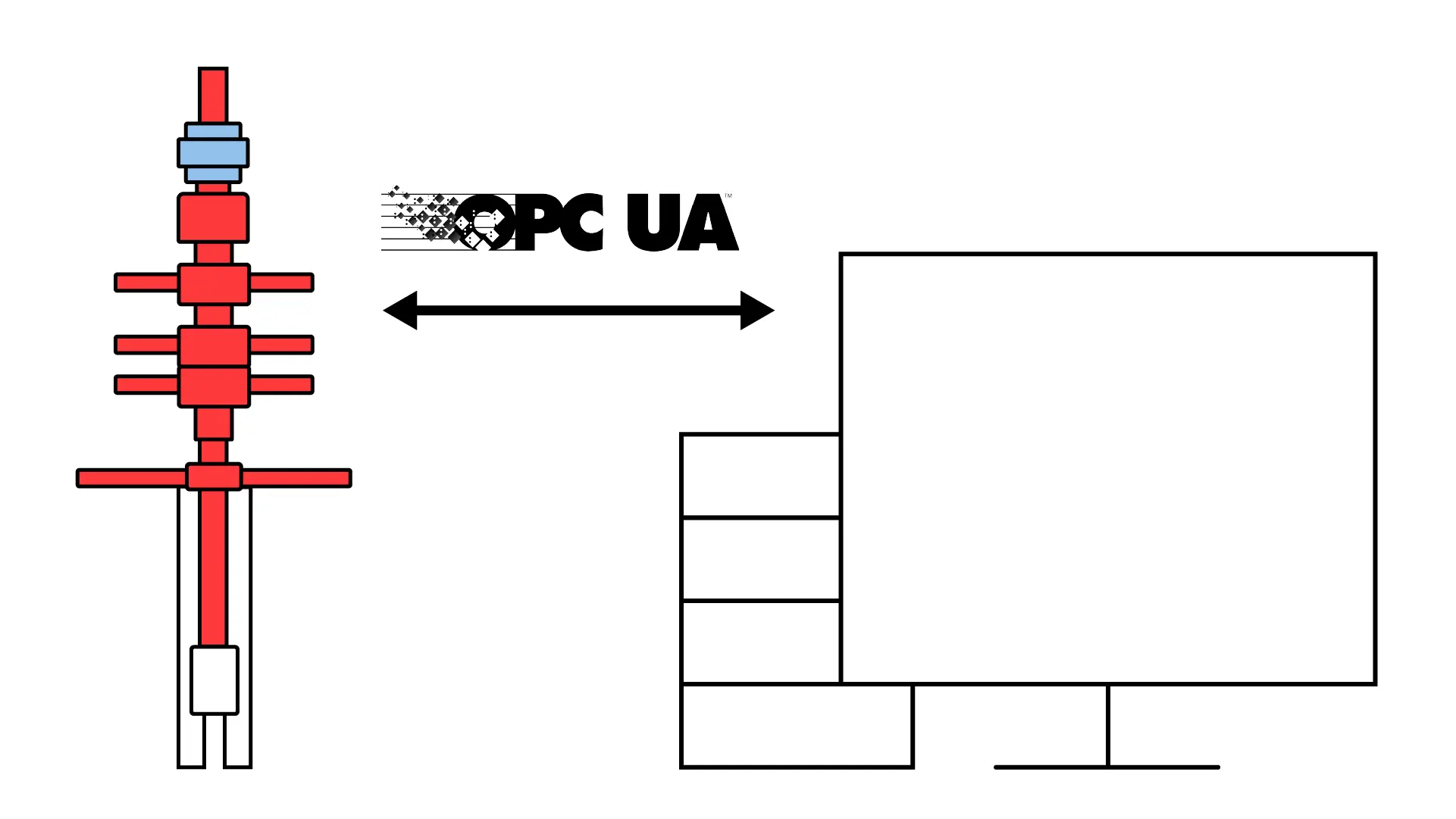
In previous articles, I have covered how OPC Unified Architecture, or OPC-UA, allows automation engineers to share data at the control system level in real-time in different industries.
Now, I will show how OPC-UA can provide benefits to the Oil & Gas industry. Before I begin this OPC-UA case study, you might be wondering how you get up to speed on OPC-UA and more fully understand its benefits, like high-speed data transfer and communications reliability.
There is an amazing RealPars course, OPC-UA: Learn the Basics, that offers comprehensive lessons on this topic. I hope you will check it out!
The Oil & Gas industry is a vital industry for the world economy. Petrochemical products are used in products including plastics, medications, heating fuels, gasoline, cosmetics, and tires.
The extraction of these raw materials is expensive, resource intensive, and dangerous. It is imperative to monitor and control operations reliably at the wellhead, with real-time collection and analysis of data to ensure a safe and efficient operation.
Oil & Gas rigs and platforms are typically located away from population centers, but there is a need to transfer data quickly and reliably in real-time to central control centers that could be located hundreds or thousands of miles away.
OPC-UA, built on TCP/IP is perfectly suited to provide data transfer services from wellhead to central servers and monitoring systems.
Because OPC-UA communicates using TCP structured command statements, communication with the wellhead is easy to configure and is as fast and reliable as two computers connected in the same room.
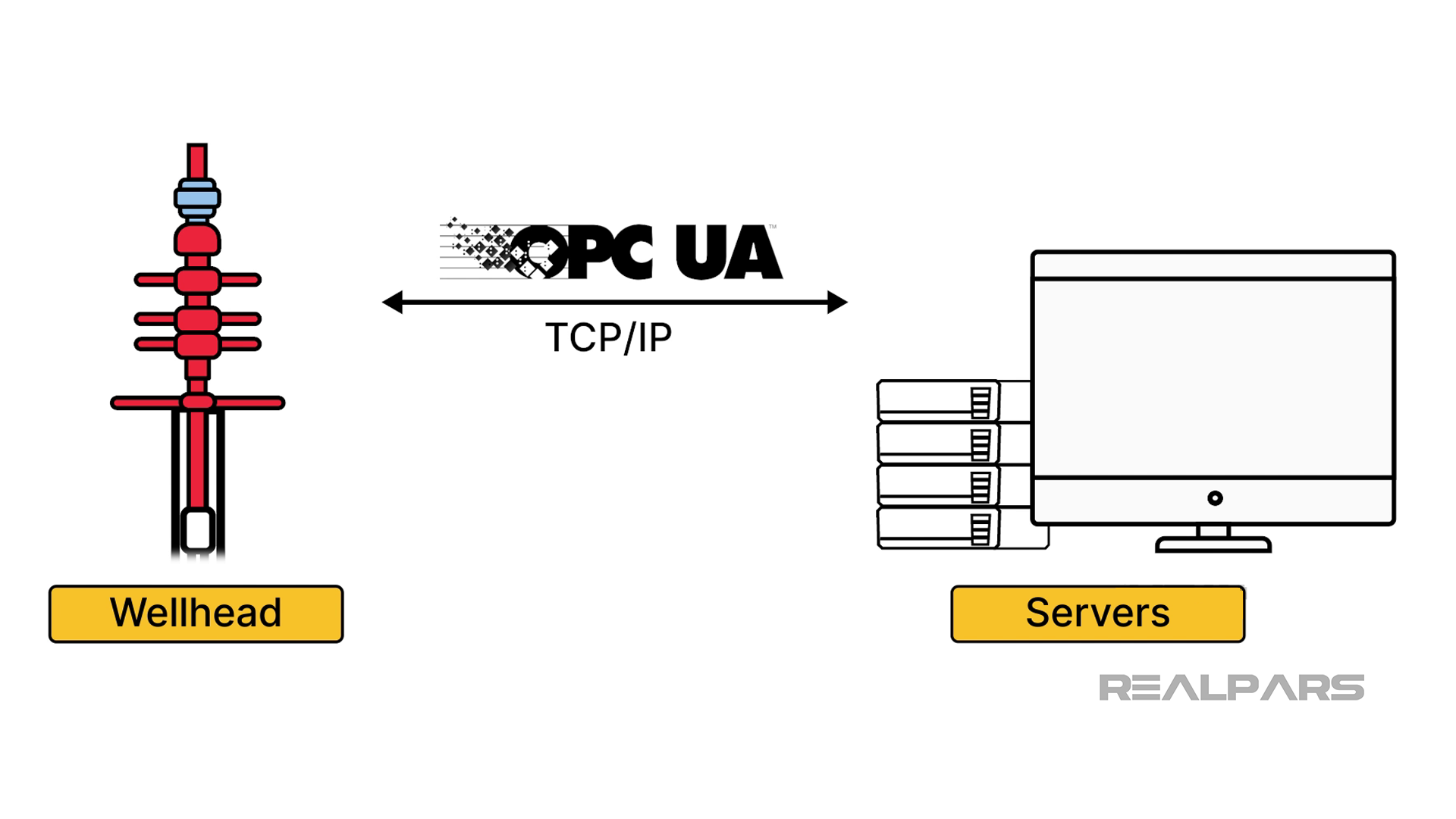
Sensors
In the vast expanse of an oil rig, danger lurks in every corner, making vigilant monitoring paramount. Let's spotlight the guardians of safety on these rigs: the sensors.
One such family of sensors found on every rig includes hazardous and flammable gas detectors. These sensors use catalytic bead or infrared sensing methods, which can accurately detect specific compounds in the atmosphere as dilute as 1 part per million.
They monitor the atmosphere for hazardous gases like methane, an explosive gas, and hydrogen sulfide, which is toxic and corrosive. Early detection is crucial to prevent potential fires or exposure risks.
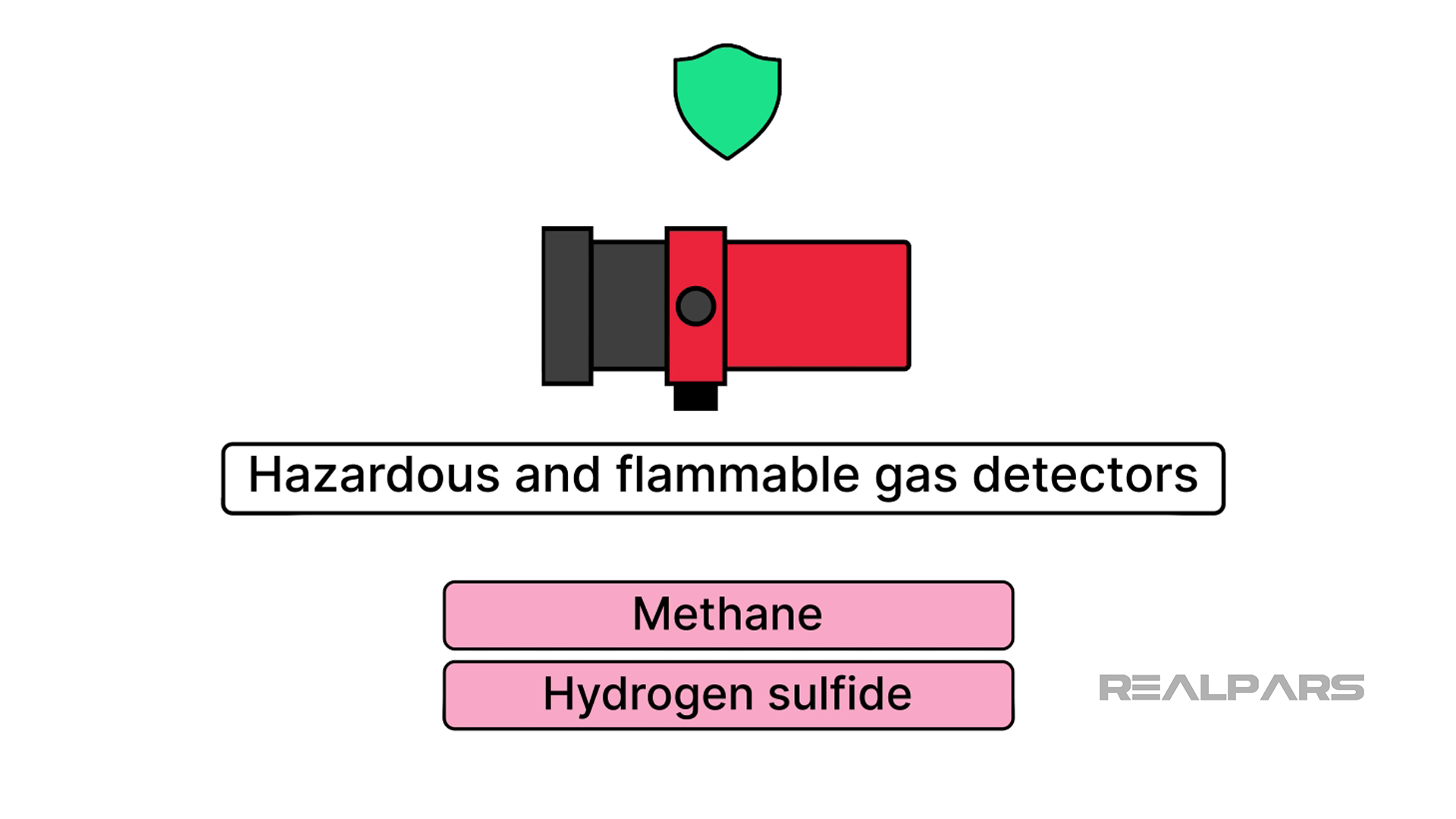
Also important in Oil & Gas production are temperature sensors. RTDs, or Resistance Temperature Detectors, and thermocouples are strategically placed around the rig, especially near drilling and extraction areas, to monitor temperature variations.
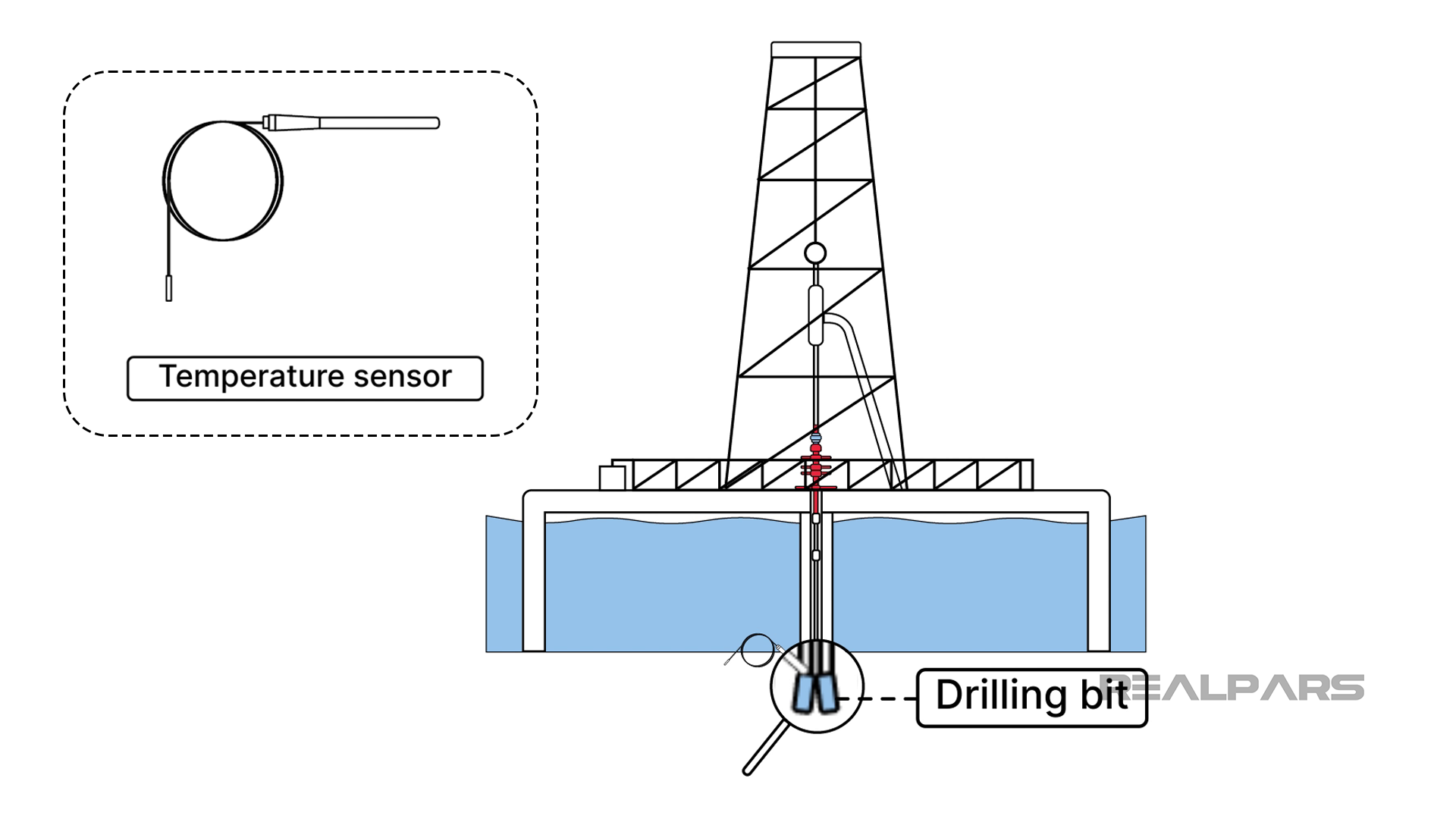
Unexpected spikes can indicate equipment malfunction or an impending fire. Temperature profiles, or temperature maps, give an overall picture of the well operations and trends over time can help operators and engineers identify problems long before they become big issues.
Another important sensor is the pressure sensor. Piezoelectric pressure sensors monitor the well's pressure.
Sudden drops or rises in pressure can indicate a potential blowout or equipment failure. Wellhead pressures can exceed 900 pounds per square inch, which requires accurate measurement and control.
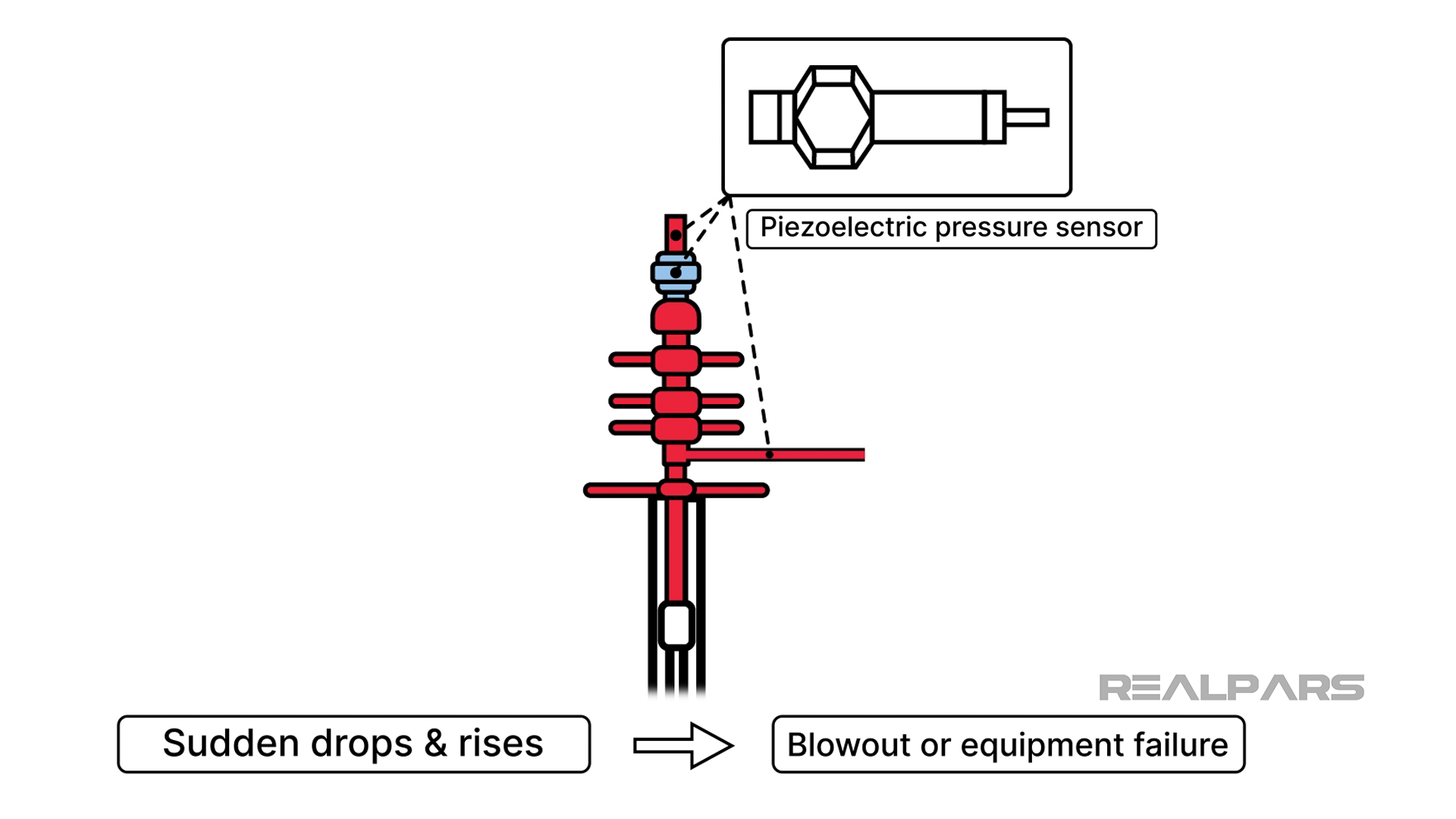
Oil & Gas wells feature a wide range of pumps, compressors, and other mechanical equipment that are continuously operated, sometimes in extreme conditions.
The stress on this equipment can be severe, so vibration monitors are critical to ensure that these mechanical components operate reliably and safely.
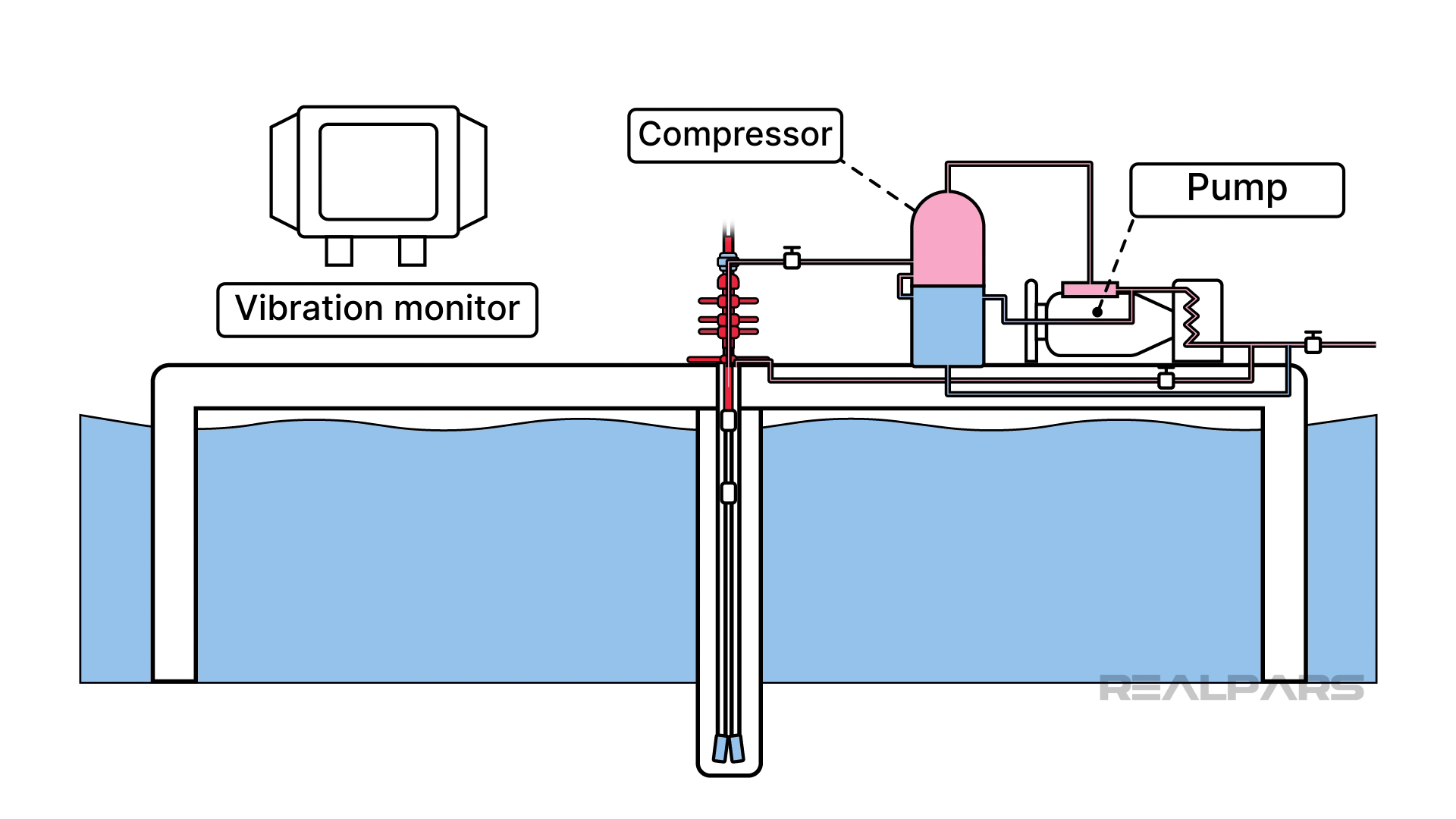
These monitors are typically accelerometers. They monitor equipment vibration to detect imbalances, wear, or malfunctions in critical components like pumps or drill heads.
Hydraulic safety valves or blowout preventers are designed to seal off a well in emergencies. They are automatically triggered in situations where sensor data indicates abnormal conditions.
Position sensors on these safety valves detect when an emergency situation is occurring. Hydraulic systems are complex and require continuous monitoring and control to provide large, powerful hydraulic safety valves.
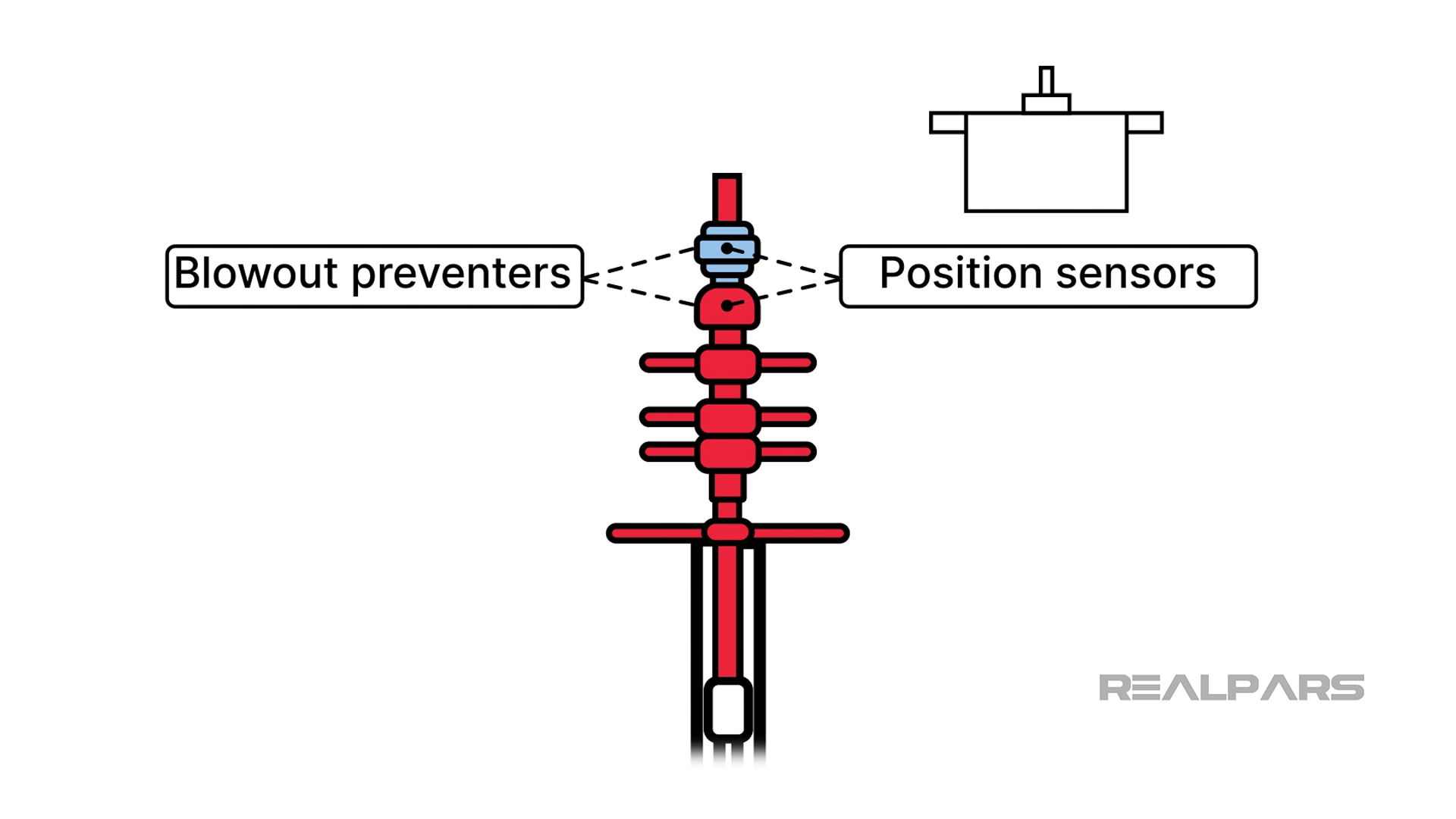
OPC-UA configuration
But what coordinates this intricate dance of sensors, devices, and safety measures? That would be OPC-UA! Every second, it processes a deluge of data, ensuring real-time, razor-sharp responses. And its reach is global.
Experts, miles away from the rig, can access, analyze, and advise on rig conditions, thanks to OPC-UA's seamless remote accessibility.
In the rare moments when things don't go as planned, its backup systems leap into action, ensuring uninterrupted vigilance.
OPC-UA has the latest cybersecurity features built directly into the protocol. This ensures that as the plethora of data is transferred from the wellhead to the operations center, no data is lost, interrupted, or stolen.
This keeps the oil and gas flowing to the sites and plants that refine, transform, and manufacture the products the world needs.
With the high risks involved in oil extraction, OPC-UA allows the monitoring of data in real-time, with minimal latency.
Data collection rates are as high as once every 50 milliseconds can be realized.
This ensures rapid response to any anomalies that are detected in the intricate extraction process. There are three main advantages that OPC-UA provides to these operations.
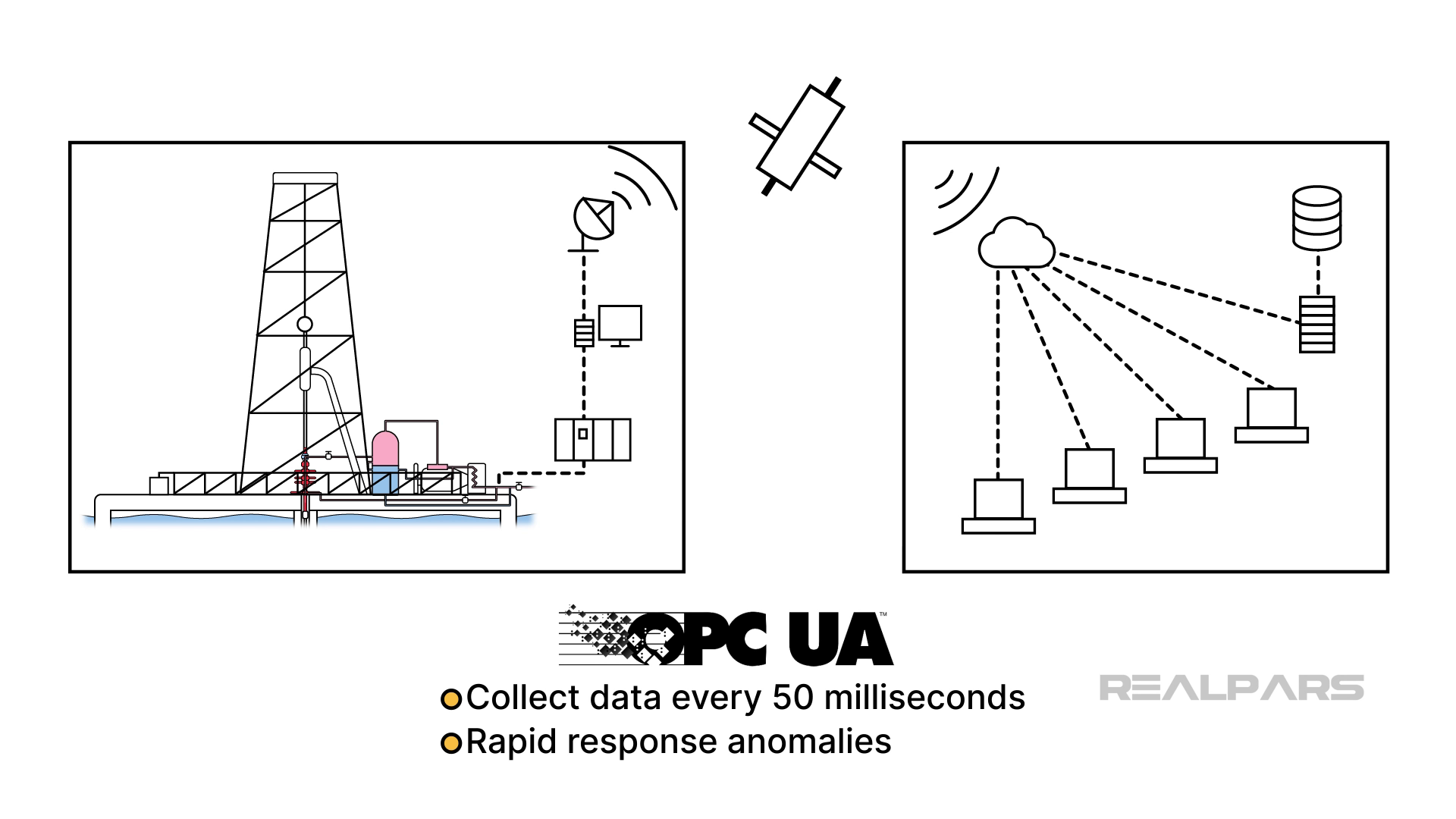
Remote accessibility is the backbone of OPC-UA. Given the often remote locations of oil rigs, OPC-UA allows experts worldwide to monitor rig conditions and provide insights in real-time without being on-site.
With the dangers present with good operations, integrated alarm systems provide a continuous watchdog over the process.
Directly tied to sensor inputs, OPC-UA can trigger alarms, through physical, on-site strobes and sirens and through digital alerts to off-site control centers. Alarms can be programmed within OPC-UA to trigger if any metrics go beyond safe thresholds.
Backup Systems provide continuous monitoring of every facet of the operation, OPC-UA is configured with redundant servers and backup power systems. Any failure in the primary system immediately switches control to the backup, ensuring no loss in data monitoring.
Summary
Thousands and thousands of points are processed by OPC-UA interfaces every minute at the wellhead, all provided to local operators and back to central control centers to ensure safe, reliable, and efficient operation.
OPC-UA truly is the workhorse that communicates over TCP/IP protocols seamlessly and securely, linking data sources to the users that require this data for monitoring, control, and analysis.
That concludes this case study of the benefits of employing OPC UA in the oil & gas industry.
If you're eager to dive deeper and truly master more of these OPC-UA concepts, don't forget to check out OPC-UA: Learn the Basics.
This course will provide you with a comprehensive understanding, along with practical exercises to solidify your knowledge. Thank you for your time, and happy learning!
Learn from Industry Experts
With a 7-day trial, then €25/month