In today’s article, I will show you how Artificial Intelligence and Machine Learning are being used in industrial automation. Specifically, you will see how AI models are being used to improve the way machine vision systems are set up and deployed.
In case you aren’t familiar with the term machine vision, let me give you a quick explanation of machine vision and the way traditional machine vision systems work.
Introduction to machine vision
Machine vision, in the context of industrial automation, is the process of performing automated visual inspections on parts using cameras and software algorithms.
A machine vision system is made up of a camera, inspection software running on a computer, and an interface to a control system.
The way a machine vision system works is quite simple.
When the control system detects a part, it sends a trigger to the inspection software.
The inspection software sends a trigger to the camera.
The camera takes a picture of the part and sends it to the inspection software.
The software runs an algorithm on the image to determine if the part is good or bad and sends the result to the control system.
The control system rejects the part if it is bad.
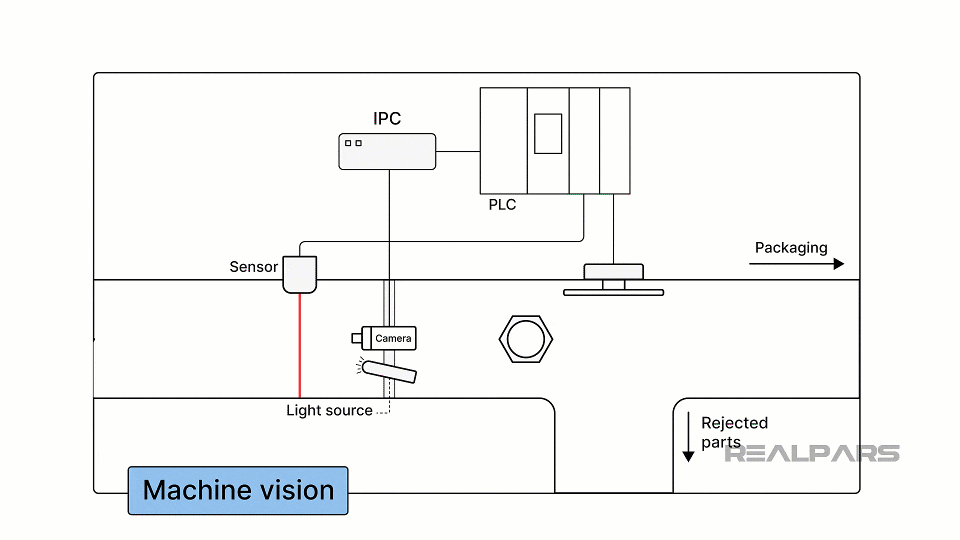
Although machine vision systems are simple to understand, they can be very complex to set up.
That’s because, with traditional machine vision systems, the algorithm used to inspect parts is a rule-based algorithm. In a rule-based algorithm, an engineer manually defines the limits that the algorithm uses to determine if a part is good or bad.
Rule-based algorithms work well for defects that are easy to define such as dimensions, shapes, and counts.
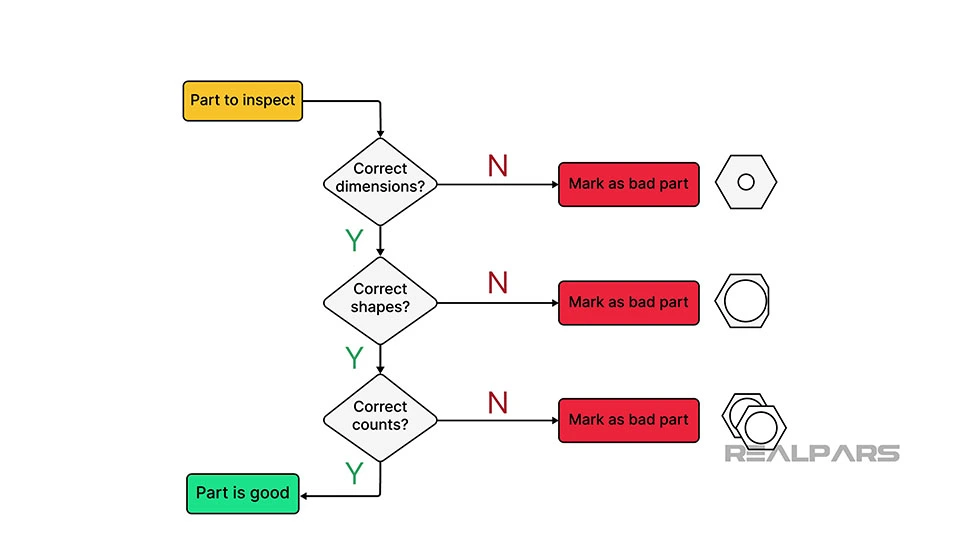
They do not work as well for more abstract defects that require judgment, such as scratches, stains, and contamination.
Thanks to advances in computing technology, AI-powered machine vision systems can now be deployed to improve the results of these difficult inspections. Let me show you how.
AI-Powered visual inspection
Modern visual inspection software like Mitsubishi’s MELSOFT VIXIO lets engineers easily build AI-powered algorithms to detect anomalies on parts without defining limits.
To do this, an engineer uploads photos of good parts and uses them to train an AI model.
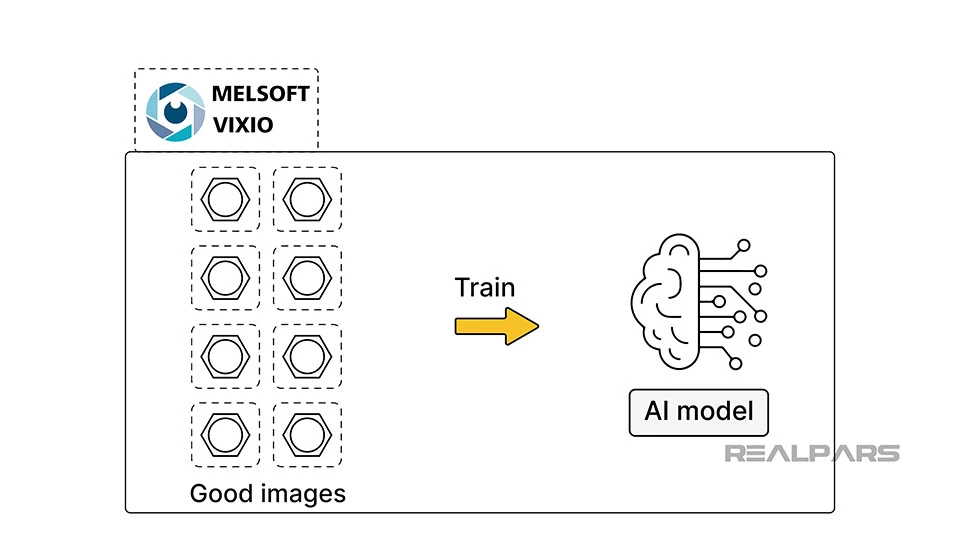
A general rule is that you will use around 100 images to train a model. The actual number that you will need depends on the complexity of the application and the amount of variation in the parts to be inspected.
Once the model is trained on images of good parts, the engineer can validate the model by uploading more photos of good and bad parts and running the algorithm on those parts.
Depending on the results of this validation, the engineer can further refine the AI algorithm to achieve optimal inspection results.
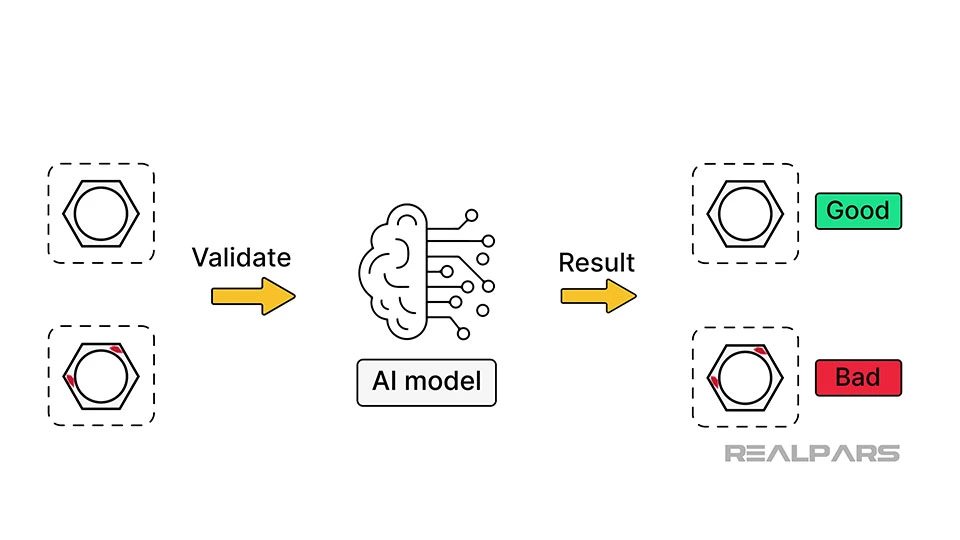
After validation, the AI model can be deployed to a production environment and be used to inspect all of the parts on a production line.
Without ever being shown what is a bad part or having limits set, the algorithm can consistently and accurately identify bad parts that have difficult-to-define defects like color imperfections and scratches.
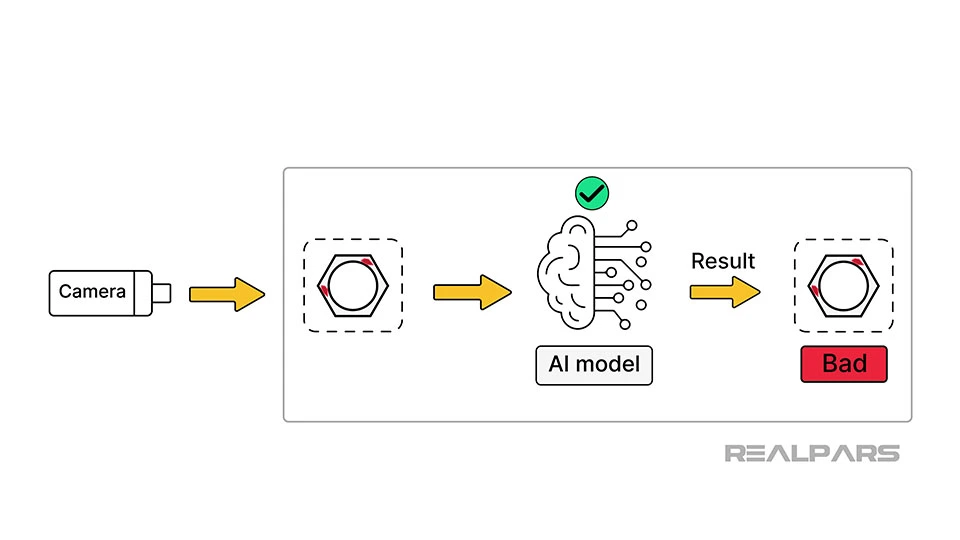
AI-powered machine vision algorithms make it much easier for companies to deploy automated visual inspections on their production lines. Let’s look at an example of how companies are using AI-powered visual inspection.
AI-powered visual inspection use case - Primary inspection
A very common use of AI-powered visual inspection is for primary inspection of products on a production line.
In a primary inspection use case, a machine vision system is used to inspect every part on a production line. Unlike an operator, the machine vision system can inspect thousands of parts per hour in a consistent and reliable way.
If the machine vision system detects a defective part, the control system rejects the part from the production line. These rejected parts accumulate in a manual work area where they are double-checked by an operator.
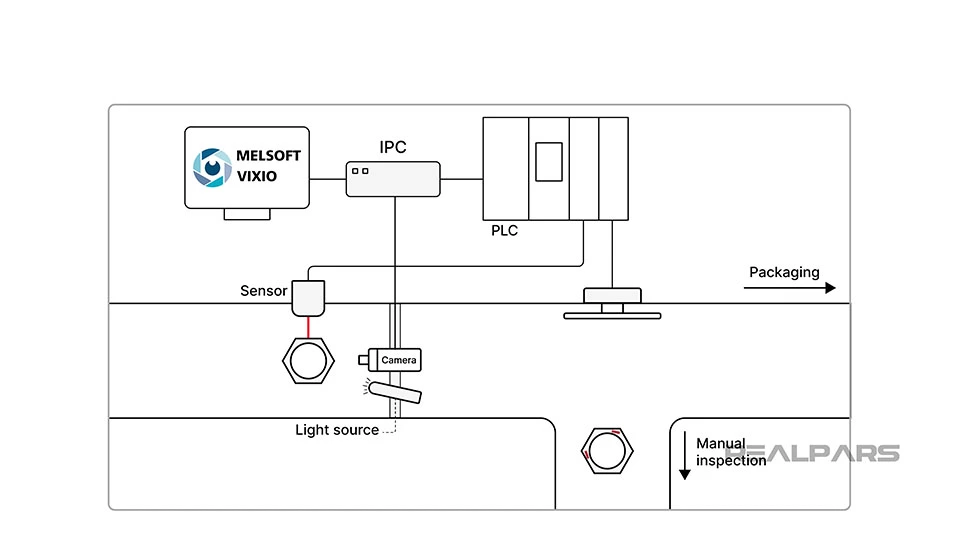
If the part is genuinely bad, the operator can triage the part for rework.
If the part is a false reject, the operator can add this image to the algorithm's training data to improve its performance and reintroduce the part to the production line.
This is a very good solution for manufacturing companies because it limits the amount of manual inspection that is required for a production line, limits the amount of unnecessary scrap material produced, and provides an opportunity to continuously improve the performance of the system.
Wrap-Up
In this article, we saw how AI can be applied to industrial automation to improve the way certain applications, like automated visual inspection, are being solved.
As companies continue to adopt AI, AI skills will become more important for control engineers to have.
If you want to stay ahead of the competition check out our course MELSOFT VIXIO: AI-Powered Visual Inspection Software for Industrial Automation.
In this course, you will learn how to build and deploy AI-powered visual inspection algorithms using Mitsubishi’s MELSOFT VIXIO software.
This course was developed in partnership with Mitsubishi Electric. At the end of the course, you will get a certification from Mitsubishi Electric stating that you are able to build, deploy, and test AI models using MELSOFT VIXIO software.
See you inside.