3 Skills That Set You Apart in Industrial Electrical Maintenance
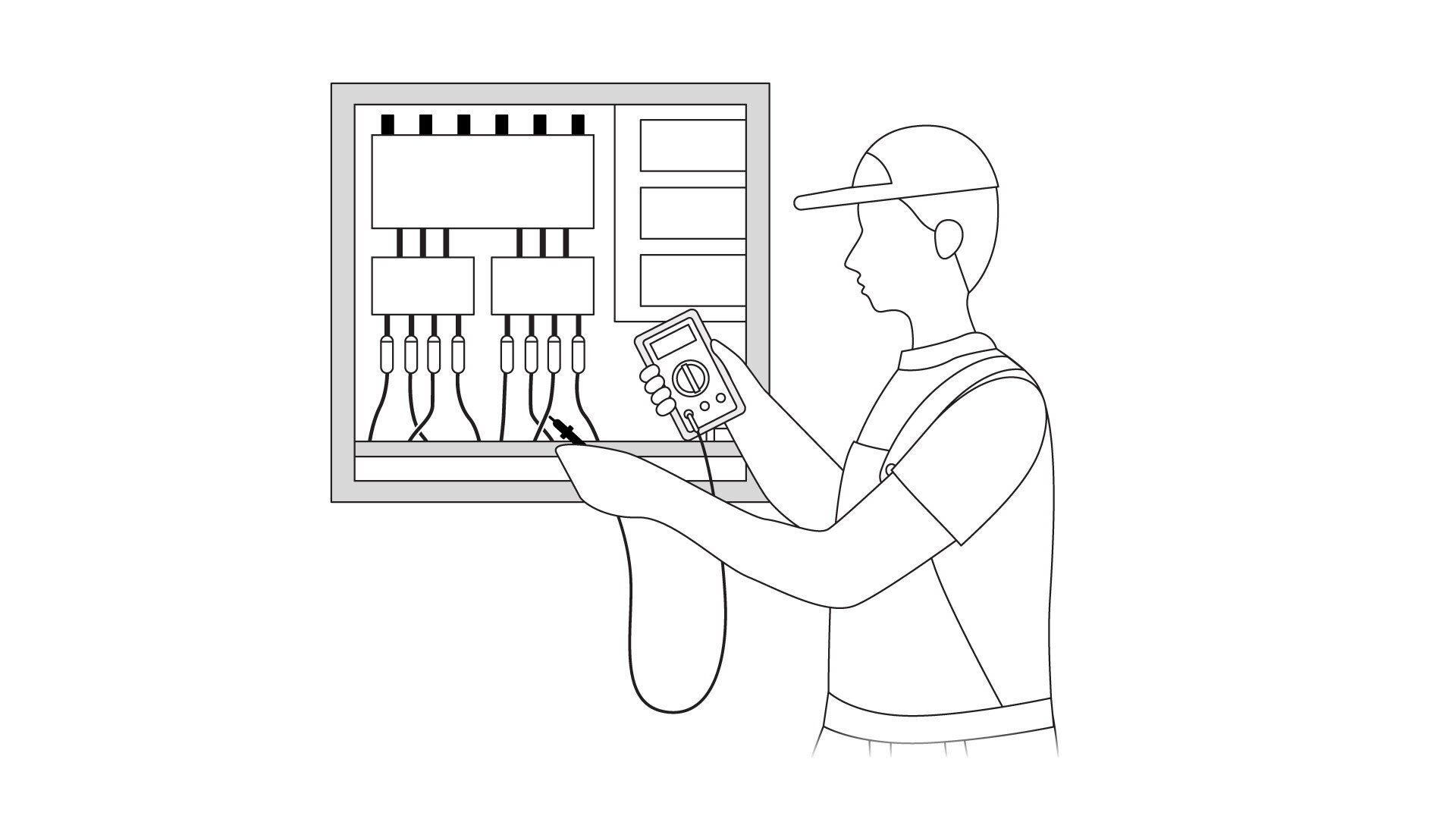
Industrial electrical maintenance is essential to keeping factories, power plants, and other industrial systems operating properly, as failing to maintain them can lead to costly downtime, equipment damage, and safety hazards.
From machines that make our products to systems that control power, everything relies on electrical systems that need to be regularly maintained to avoid costly failures.
These days with the fast-changing industrial environments, Industrial Maintenance technicians must be knowledgeable, competent, and have the necessary skills in various aspects in areas like mechanical and electrical devices, contactors, PLCs, electrical safety, and automation systems, just to name a few.
In this article, you'll learn what skills you need in industrial electrical maintenance, including technical skills, safety awareness, and troubleshooting techniques.
But before we dive into this, if you're a maintenance or plant manager looking to reduce downtime by training your team, you can fill out this form for a RealPars Business Membership, and our team will call you back in just a few minutes.
Skill 1: Technical Skills
Identifying Basic Electrical Circuits
Having a solid understanding of electrical basics and circuits is key to really getting electricity. As a technician, it’s not just about fixing stuff when it breaks,It’s about knowing how things work, recognizing problems before they turn into big issues, and ensuring everything runs safely and efficiently.
Learning about voltage, current, resistance, conductors, insulators, and Voltage Line drops is very important for keeping electrical systems safe and working well. It helps you choose the right wires and materials, which is key to making sure everything gets the power it needs without breaking down. Plus, knowing these things makes it easier to fix problems and follow safety rules.
In industrial systems, the circuits might be more complex, involving multiple power sources, control devices, and feedback systems, but they still follow this basic principle.
Identifying Electrical Symbols on Schematics
Schematics are like blueprints for electrical systems. They use symbols to represent components like switches, resistors, motors, and transformers.
It's important to know these symbols and how they're represented in drawings, diagrams, and abbreviations.
A maintenance technician working in the electrical industry needs to have this knowledge and be able to read drawings and diagrams to understand how electrical circuits operate and troubleshoot problems.
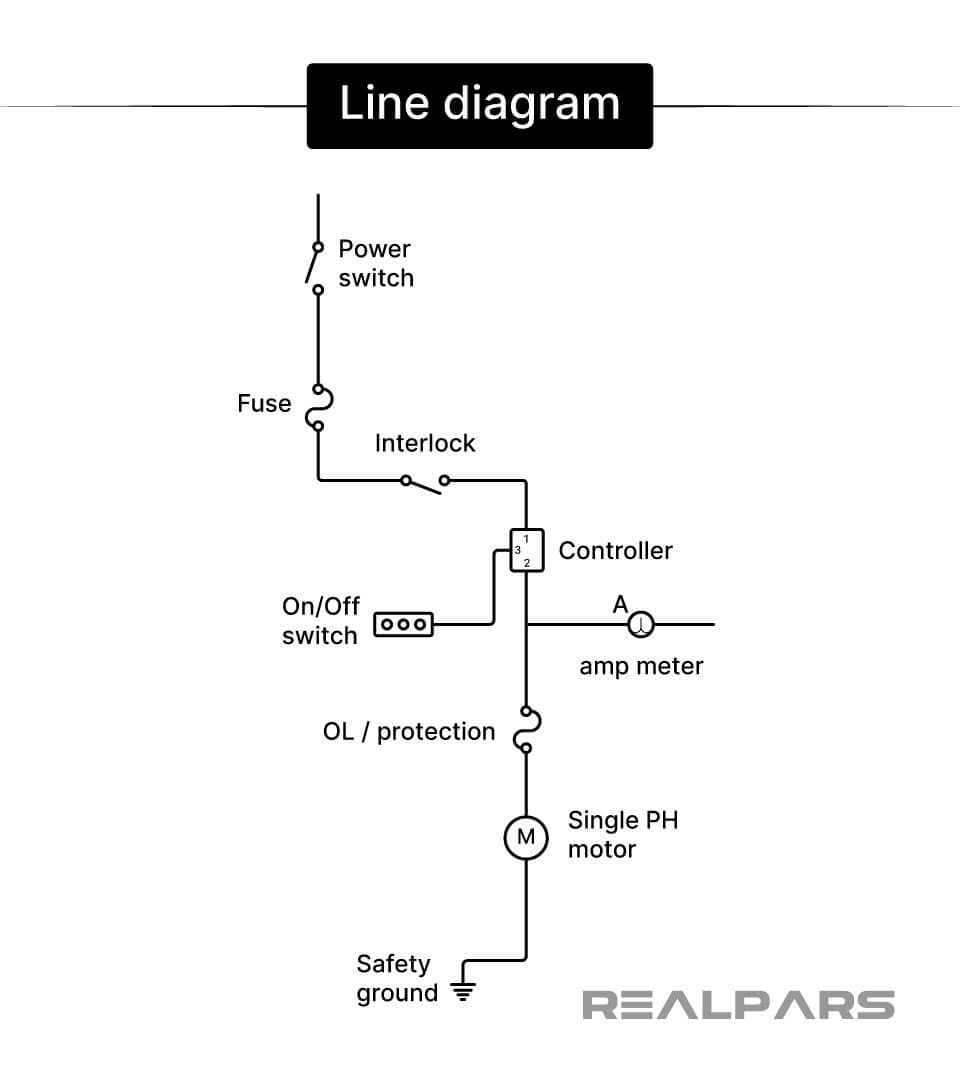
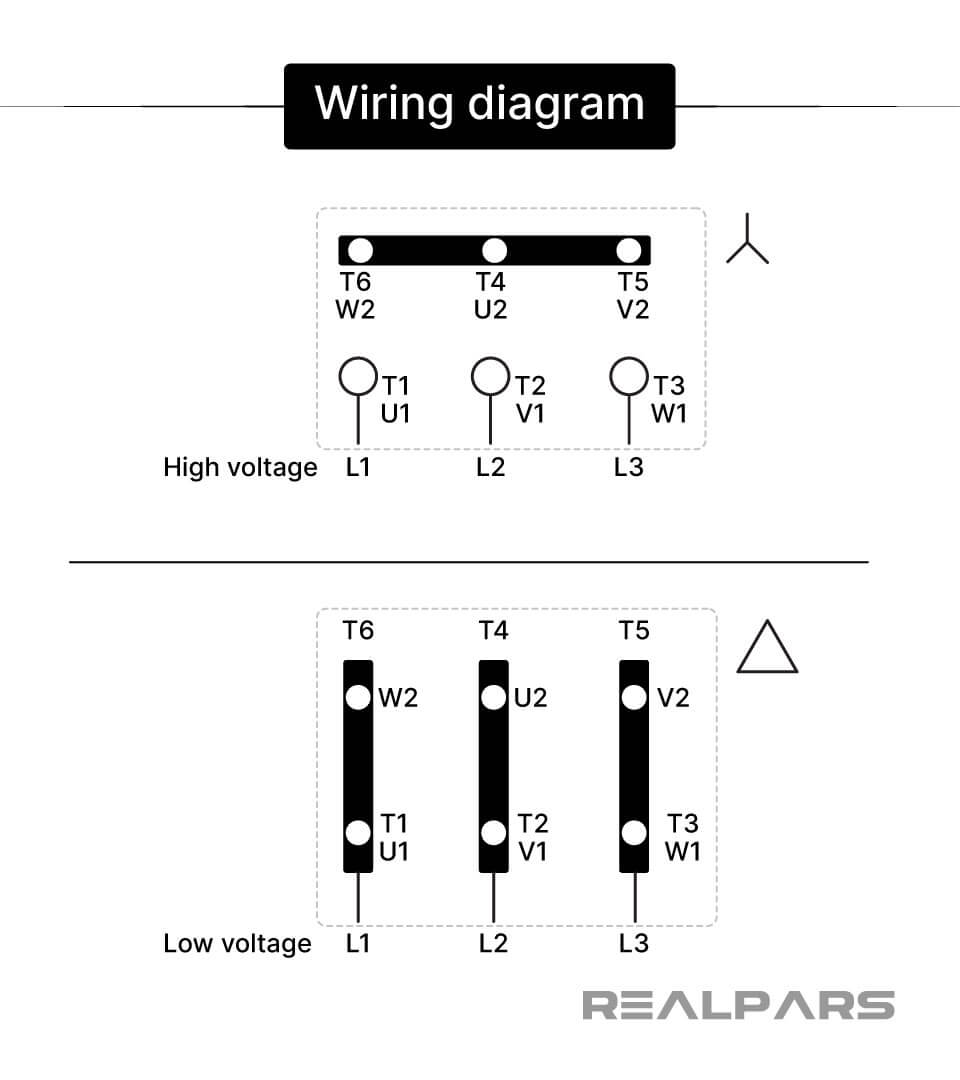
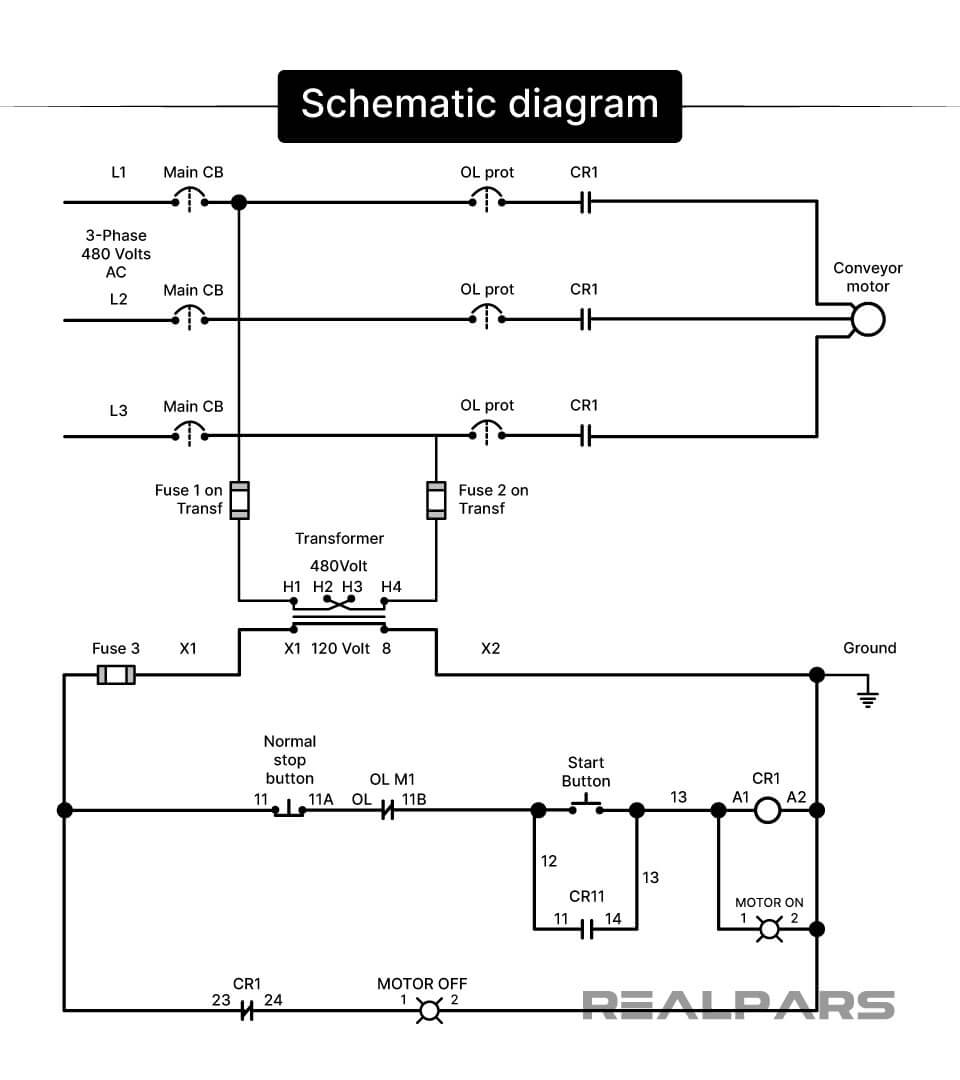
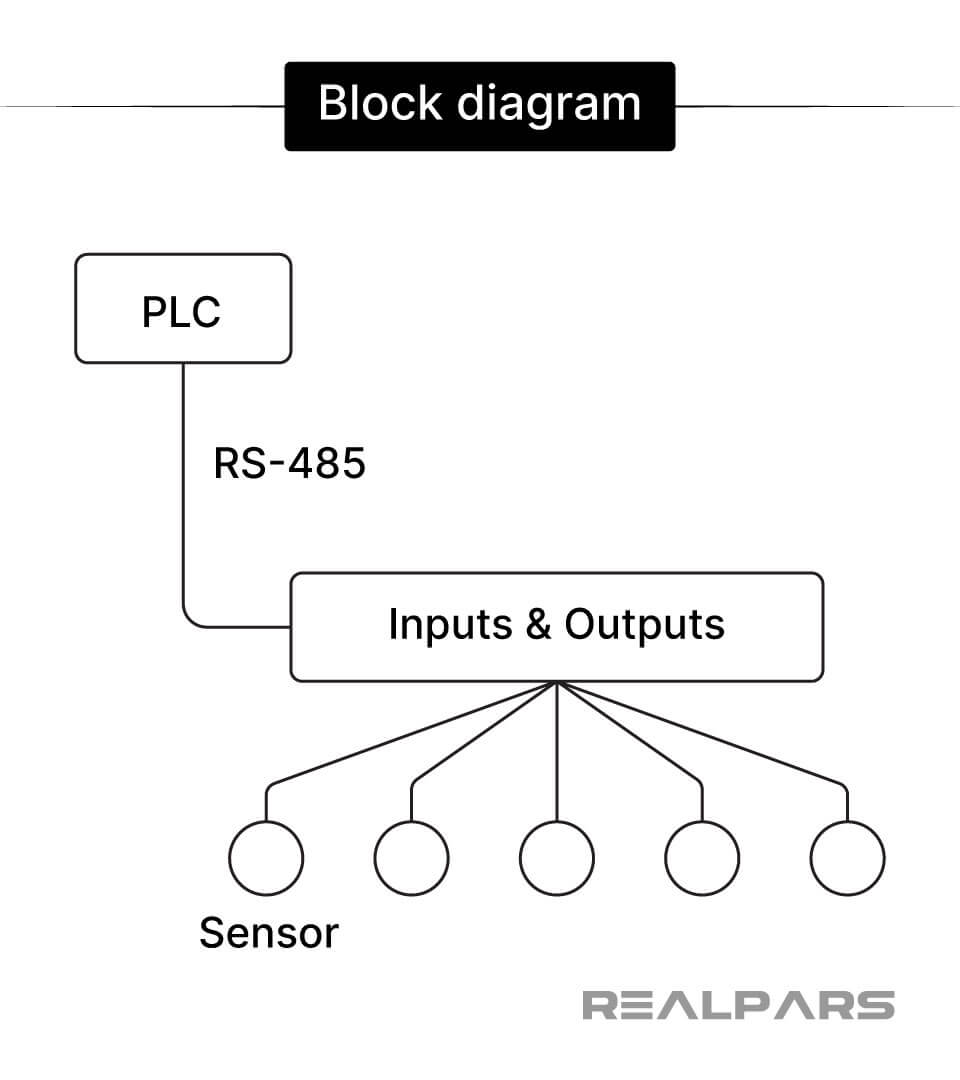
If you want to learn more about Electrical Quantities, the operation of basic electrical circuits, and Identifying Electrical Symbols on Schematics we suggest checking out our course Industrial Electrical Maintenance Essentials 1: Safety, Inspection & Repair.
Diagnostic and Troubleshooting Techniques
Once you understand the system and how it works, you need to be able to diagnose and troubleshoot problems when things go wrong. Troubleshooting is a skill that gets better with experience, but there are key steps you can follow to make the process more efficient and effective.
Recognizing Electrical faults like Short Circuits, Open Circuits and Ground Faults, Blown Fuses and Tripped Breakers early can save time and prevent more serious damage. these are a major part of maintenance work.
To effectively troubleshoot these Electrical faults, you need the right tools. The most important tools that you can use are a Multimeter, Digital Clamp-on Ammeter, and Receptacle Ground Fault Interrupter (GFCI) Socket Tester, just to name a few.
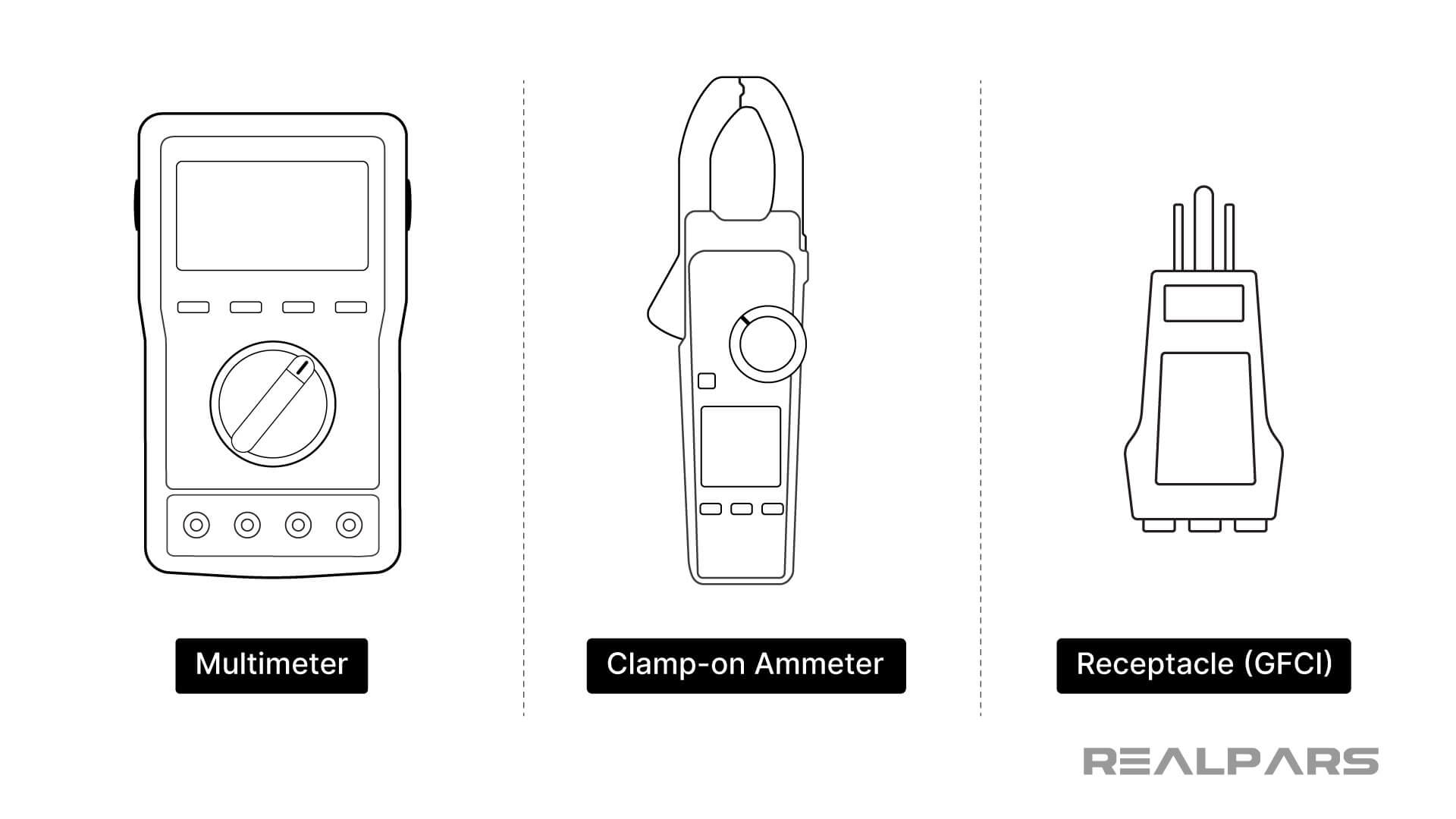
Again If you want to learn more about these tools and test instruments, be sure to check out Industrial Electrical Maintenance Essentials 1: Safety, Inspection &Repair.
In level two of Industrial Electrical Maintenance Technology, we will explain more about the applications of these devices and additional test instruments you might be using in the field of Industrial Maintenance.
After completing each course, you’ll receive a certificate that you can proudly share on your LinkedIn profile and find your next career opportunity in the industrial automation field.
Maintenance and Repair Strategies
It is important to stay ahead of problems rather than wait for something to break. In this way, you reduce the risk of longer downtime and higher repair costs.
By having a preventive maintenance procedure, meaning regularly checking equipment to make sure it's working properly and staying in good condition.
For example, cleaning equipment helps prevent dirt from causing wear and tear, and lubricating parts reduces friction. Tightening loose connections helps prevent overheating, and testing safety systems ensures alarms and emergency systems work properly.
If something does break, you need to know how to fix it quickly, whether it’s replacing a burned-out motor or fixing damaged wiring. After any repair, always test the equipment to make sure it’s working right. By taking action ahead of time, you’ll catch issues before they turn into expensive problems.
So, you need to learn how to replace faulty components, make wiring repairs if a wire is damaged, and test after repairs. When equipment does fail, you need to know how to repair it quickly and effectively.
Skill 2: Safety Awareness
All the theoretical knowledge you've gained about how electrical circuits and systems work is meaningless if you can’t prevent or minimize the risk of receiving an electrical shock or worse, being electrocuted. Electrical Maintenance Technicians must always work safely in a real-world environment.
You need to understand the common hazards in your industrial environment and familiarize yourself with the National Electrical Code (NEC) or any local codes that apply to your work. Learn about terms like NFPA® 70E, PPE, and Lockout/Tagout, which is commonly known in the electrical industry as LOTO.
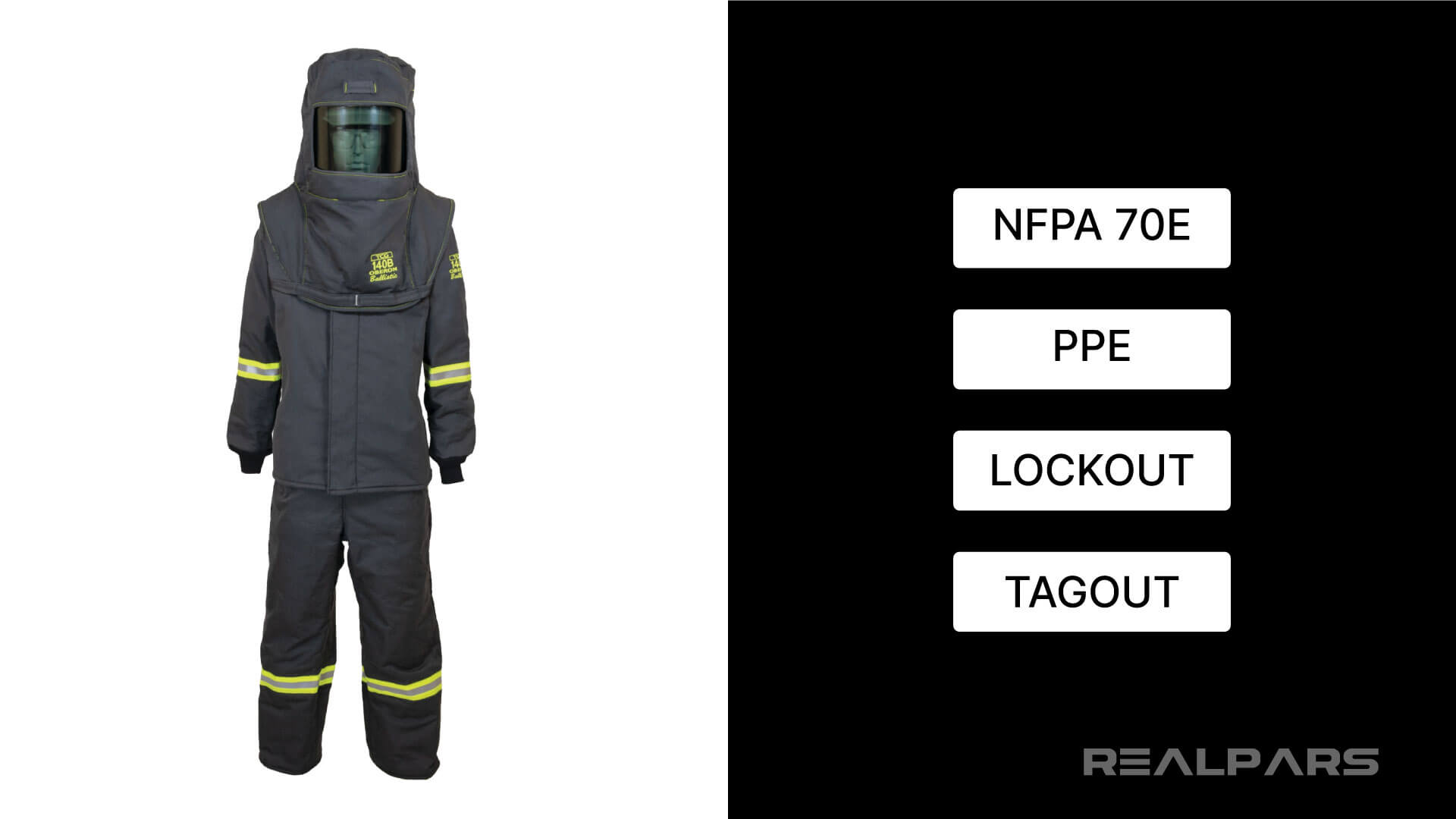
Want to learn more about electrical safety? We also cover this in Industrial Electrical Maintenance Essentials 1: Safety, Inspection & Repair.
Skill 3: Advanced Troubleshooting and System Optimization
As industries grow, more systems are becoming automated. Automation means there’s less need for people to do things by hand, but it also makes the electrical systems more complicated.
Understanding Control Systems like Programmable Logic Controllers (PLCs) and Distributed Control Systems (DCS) can help you a lot in troubleshooting automated systems.
When something goes wrong in these systems, it’s often not just an electrical fault. It could be sensors, software configurations, or even network issues. Advanced troubleshooting means not only understanding the electrical side but also the integration of automation and control systems.
If you’re interested in PLCs and troubleshooting them, make sure to check out realpars.com/courses.
Wrap - Up
Thats it. industrial electrical maintenance is all about being skilled, staying safe, and always getting better at what you do.
As technology keeps changing, it's important to keep learning. Remember, your skills help keep everything running safely and efficiently.
Also, if you want to train your team of engineers and technicians and reduce your downtime, you can check out RealPars Business Membership and submit your request.
Frequently asked questions
Learn from Industry Experts
With a 7-day trial, then €35/month