Industrial boilers are designed to heat water to produce steam or hot water for various industrial processes like power plants, chemical production, and oil refining.
Ok….. Let’s take a look at a few types of boilers and how they work with a simple form of boiler design.
In a fire-tube boiler, fuel is burned in a furnace, which then creates hot gases. These gases flow through tubes surrounded by water,
so the main characteristic of a fire-tube boiler is that the water is outside the tubes. As the gases move through the tubes, they transfer their heat to the water, and that’s what creates steam.
For high-pressure over 200 PSIG or high-capacity needs over 10 MMBtu, fire-tube boilers aren't ideal because the pressure vessel can be at risk of failure under these conditions.
In a water-tube boiler, it works a bit differently. Water moves through small tubes, and then the tubes are heated. As the water heats up, it eventually turns into steam.
This is how this type of boiler operates. Due to their design, water-tube boilers can handle higher pressures than fire-tube boilers, making them ideal for heavy industrial applications.
To familiarize you with these two types, I’ve shown a simple design of both boilers.
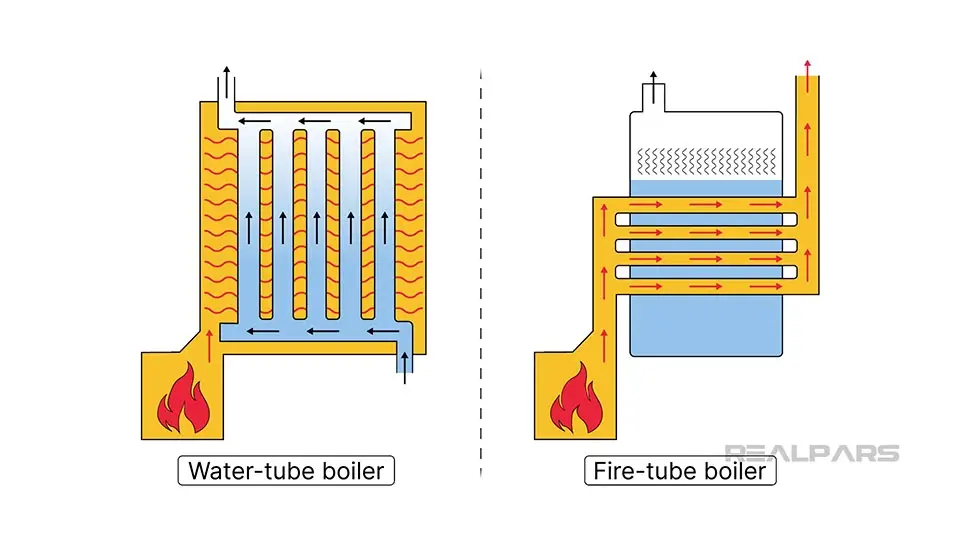
However, these boilers are commonly used in the industry for various applications and come in different sizes and designs.
Water-tube boilers, which are commonly used in power plants heat water to create superheated steam, which is then used to drive turbines connected to generators, producing electricity.
The steam is also reheated again after the first stage of the turbine. Why do we need superheated steam? Because we shouldn't allow the steam to condense back into water to prevent damage to the turbine blades.
In the next part, I'll explain how the boiler’s superheater makes this happen.
Boiler parts and function
To understand the way an industrial boiler works, first, we should look at the main components that start the whole process and keep the operation efficient.
Economizer
The first component that feedwater passes through is the economizer. The economizer preheats the feedwater supplied by the feedwater pump by absorbing energy from the combustion gasses, which raises the temperature of the fluid.
This process boosts boiler efficiency by recovering heat that would otherwise be lost. Corrosion caused by low water temperature can also be prevented by controlling the incoming feed water.
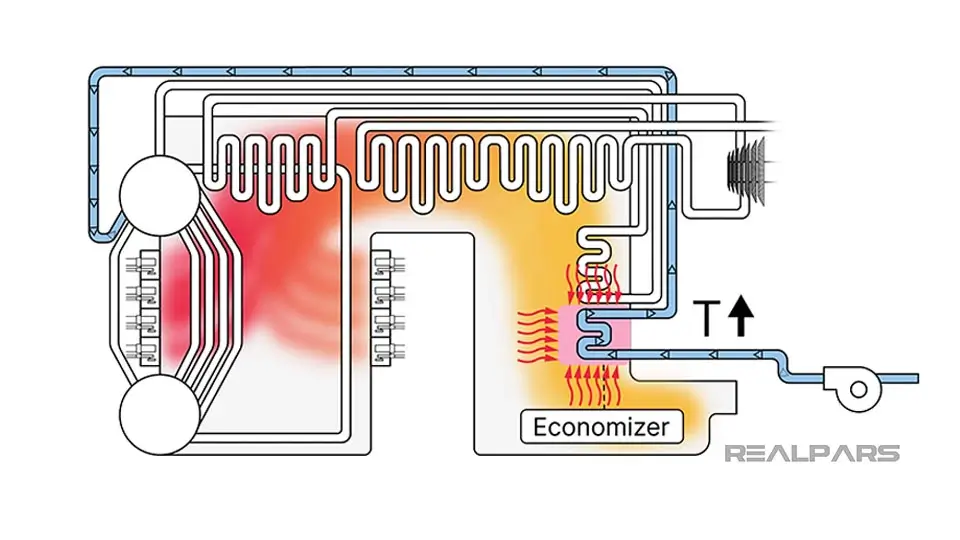
Combustion chamber
The necessary heat to convert water to steam is provided by combustion in a boiler, and the following elements are needed: Oxygen, fuel, and heat, to initiate a chemical reaction.
A boiler typically has multiple burners positioned around the furnace. the oxygen that is needed for combustion comes from air supplied to the boiler, and the fuel nozzle sprays fuel into the furnace.
The fuel and air (Oxygen) combustion needs energy. The electric igniter first provides the energy required for ignition. This spark ignites the pilot flame, which in turn ignites the main flame and creates tremendous energy.
By creating a flame and confirming it, the heat from the igniter is no longer needed.
Steam drum - Water wall
Let's go back to the heated feed water that came out of the economizer, it then enters the steam drum via the feedwater inlet. Next, it flows through the downcomer, mud drum, and water wall.
The water wall, consisting of closely spaced tubes lining the interior of the boiler's combustion chamber, absorbs heat from the combustion gases. Heat transfer in the combustion chamber occurs through radiation and convection, heating the water inside these tubes.
The heated water reaches the top of the water wall tubes, and it’s often a mixture of water and steam, then it goes toward the steam drum where further separation occurs. steam drum is partially filled with water, and the upper part of it is reserved for steam.
Inside the drum, the water-steam mix hits baffles that change its direction, helping to separate the steam from the water. Then, it moves to cyclone separators, which use centrifugal force to remove any remaining water drops, and the steam rises to the top part of the drum. To make sure the steam is completely dry, it might go through extra moisture separators or drying devices.
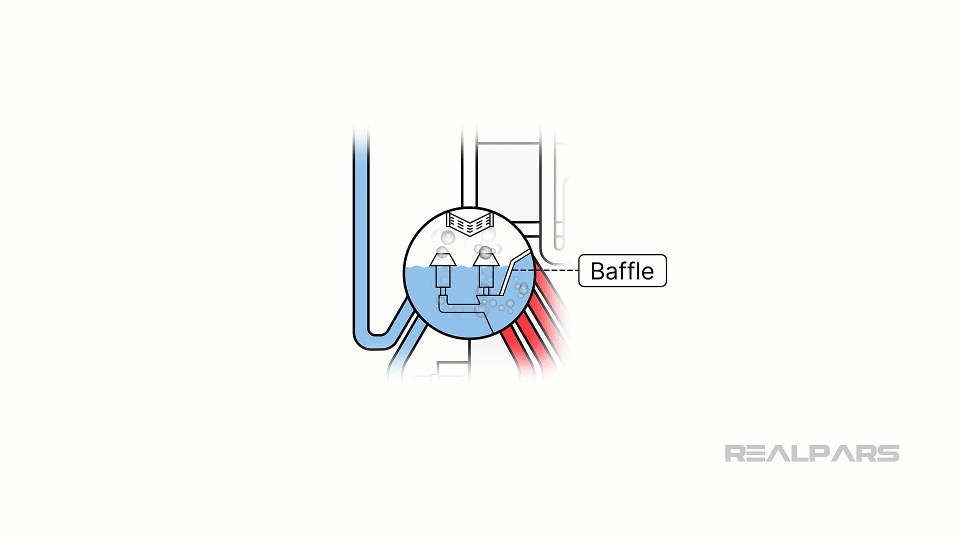
Mud drum
If more solutes enter the boiler along with the feed water, these solutes will be concentrated and may reach a point where their solubility in water decreases and they are separated from the water as sediment.
The mud drum which is located at the bottom of the boiler and is connected to the steam drum above it through the downcomer and water wall tubes is filled with water and serves as a collection point for dirt and impurities. Over time, these settle at the bottom of the mud drum.
So…To prevent this from happening, the solutes in the water should be limited. This process, called blowdown, is controlled by removing part of the boiler's condensed water. It can be done manually or automatically through the drain valve at the point with the highest concentration of solutes.
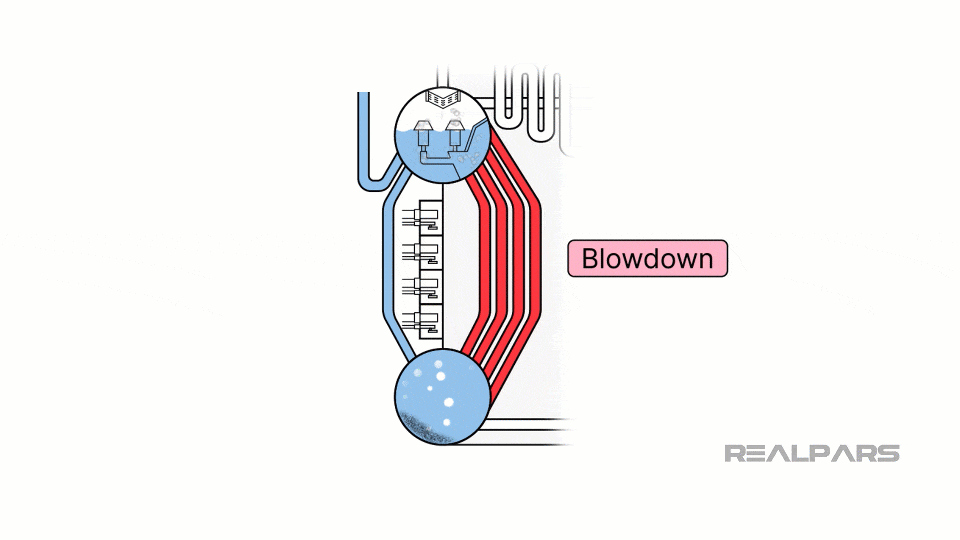
Superheater
superheaters are tubular heat exchangers placed in the path of the boiler's combustion heat or hot gases, with steam flowing through the tubes. The purpose of the superheater is to increase the steam's temperature and remove moisture.
In power plants, the needs of the steam turbine are the determining factors for the boiler control conditions. Therefore, to provide the desired temperature of the steam turbine, temperature control equipment is needed.
This requires having at least two zones called primary and secondary superheaters. In some boiler designs, additional temperature controllers, known as desuperheaters are used between the primary and secondary superheaters. If the steam gets too hot, the desuperheater sprays water into the steam, which lowers the temperature of the superheated steam.
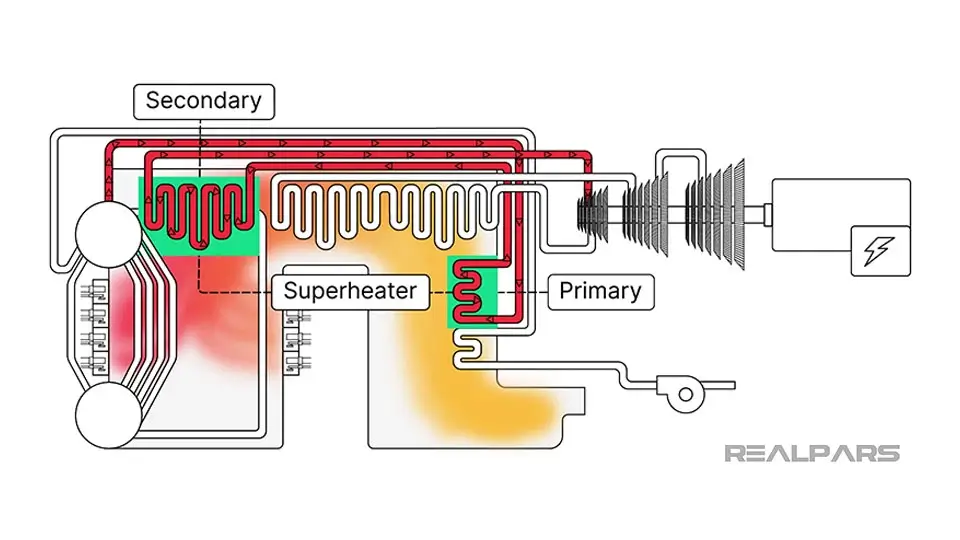
from the secondary superheater, the steam goes to the high-pressure or HP section of the turbine, it expands and loses some temperature as it drives the HP turbine blades, generating mechanical energy.
Once the steam exits the HP section of the turbine, it typically moves to a reheater, which functions similarly to a superheater.
Reheaters use heat from the hot combustion gases to raise the steam's temperature,This restores heat lost during the HP expansion. This reheated steam then flows into the intermediate-pressure (IP) or low-pressure (LP) sections of the turbine for further expansion.
The rotation energy produced by the steam turbine is transferred to the electric generator. Caution must be taken by using sensors to monitor vibration, as this can resonate with unwanted sounds and cause unwanted harmonic disturbance. This can lead to bearing failures and wear and tear.
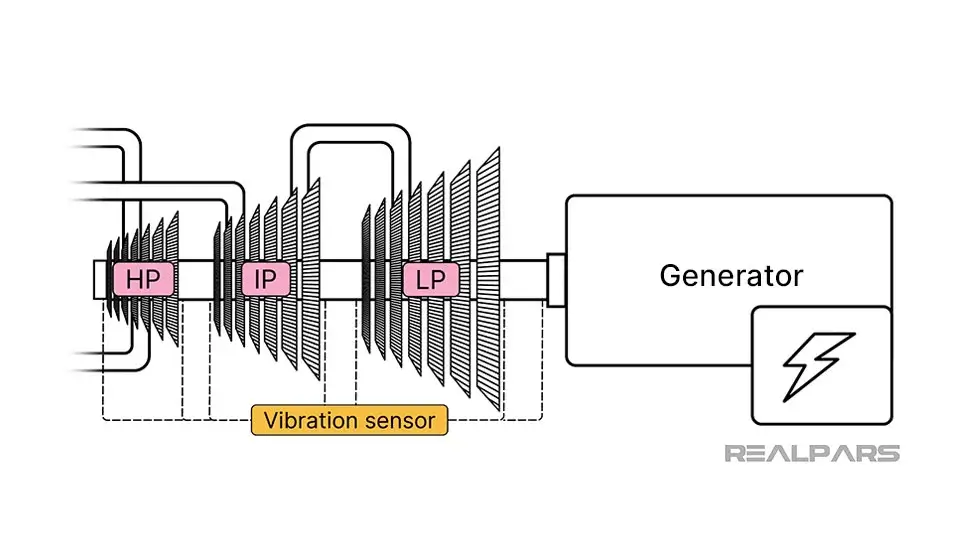
Wrap-Up
Just to recap, here’s what you learned in this article:
We looked at the role of the economizer, water wall, and mud drum and what happens inside the combustion chamber and steam drum.
we also talked about the role of superheaters to provide the desired temperature for the steam turbine.
If you want to learn about power generation, be sure to check out our course Power Generation Essentials: From Turbines to Hydroelectricity on Realpars.com.