Welcome to our article on Motion Control Systems. This article will explore the essential components of closed-loop motion control and how they connect and interact in a control loop to ensure automation precision.
We’ll also provide a quick overview of the different types of motion controllers and how they are used in a control loop.
What is motion control?
Ok…so, what is Motion Control?
Motion control refers to the methods used to precisely regulate and control the movement and position of mechanical systems. The two keywords in that statement are “movement” and “position.”
On the other end of the control spectrum is Process Control, where we manage and regulate processes. We're interested in measuring and regulating process variables such as temperature, pressure, and flow rate in process control.
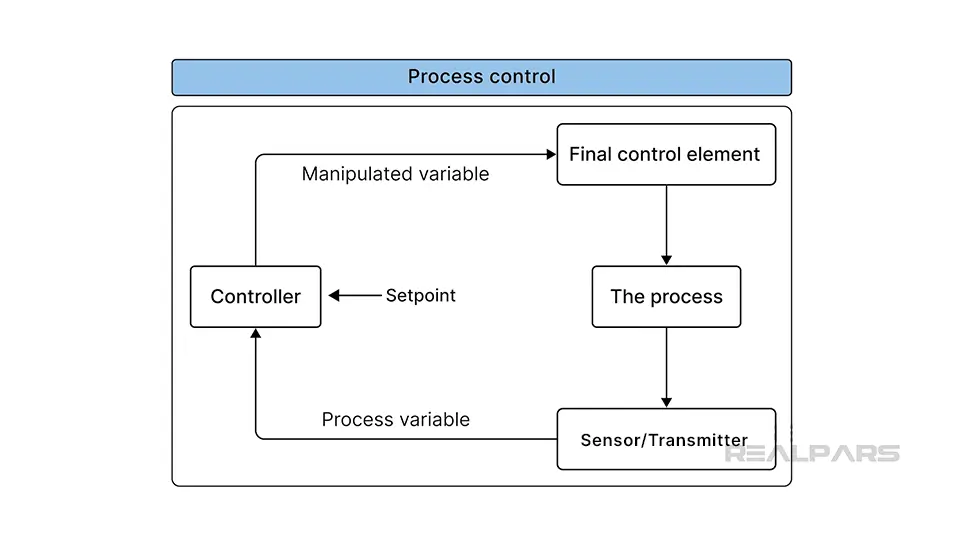
Acceptable responses to setpoint changes or disturbances differ in Motion and Process Control. A quarter-wave damped response is usually desired and accepted in Process control but possibly disastrous in Motion Control.
In a well-tuned Motion Control system, the actual position must closely follow the target or setpoint position.
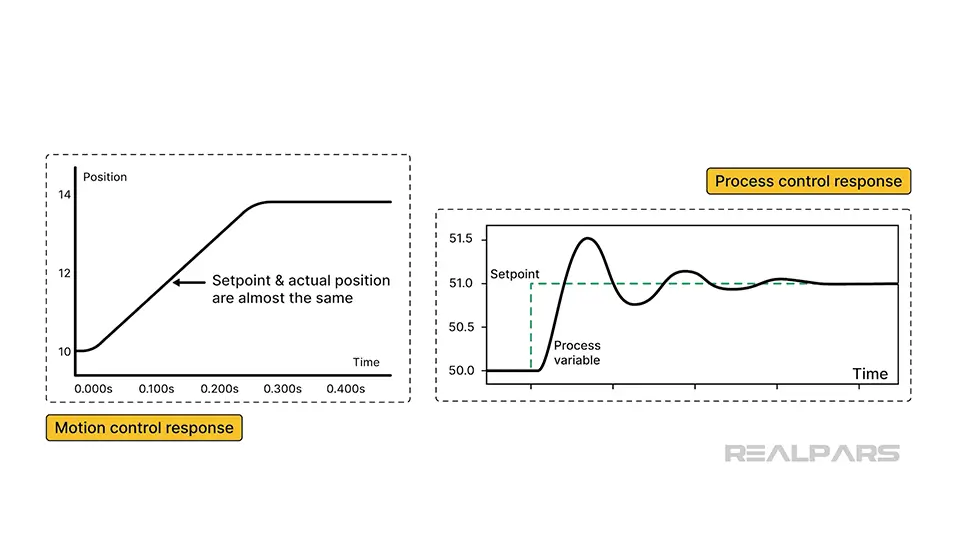
Motion control is used in the manufacturing industry on CNC machines, assembly lines, and packaging equipment.
It is also used in Robotics, where the precise movement of robot arms is required. Aerospace, another field that uses motion control, controls the motion of aircraft components.
Essential components
The four essential components of a motion control system are the controller, driver/amplifier, sensing/feedback devices, and actuator.
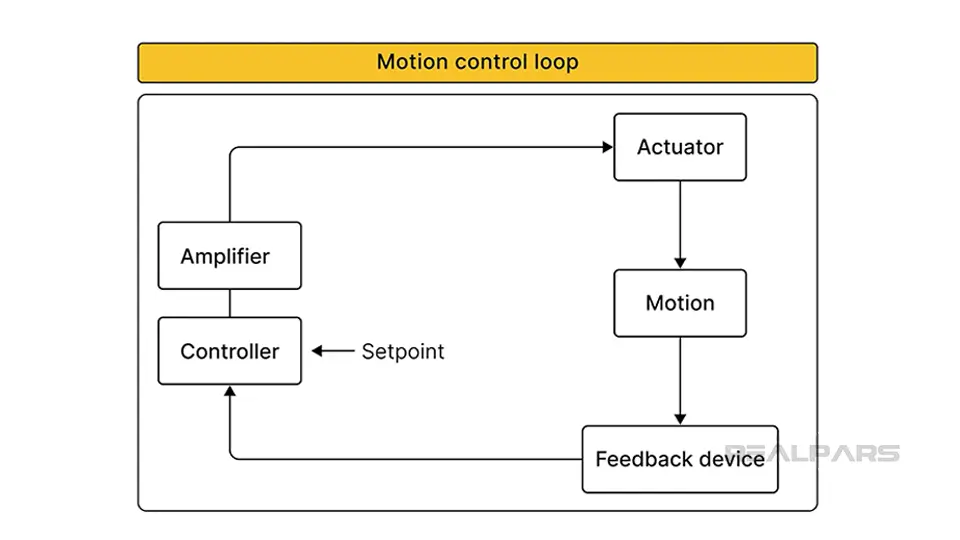
If the Motion control system control loop block diagram looks similar to a process control loop, it’s because they are the same.
Depending on the system requirements, the controller and amplifier may be housed together as a single device.
The difference between motion and process control becomes evident when we examine the feedback devices.
OK…That's our cue to explore the motion control loop components more closely.
We will base our discussion on a system where we control the position of saw blades on a sawmill conveyor belt to ensure precise and accurate lumber cutting.
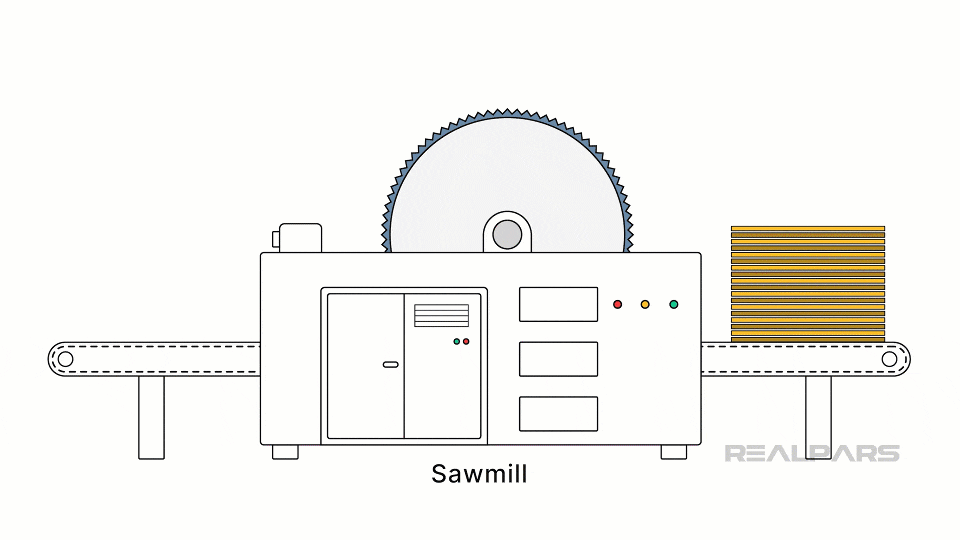
Actuator
Actuators convert electrical, hydraulic, or pneumatic energy into mechanical motion.
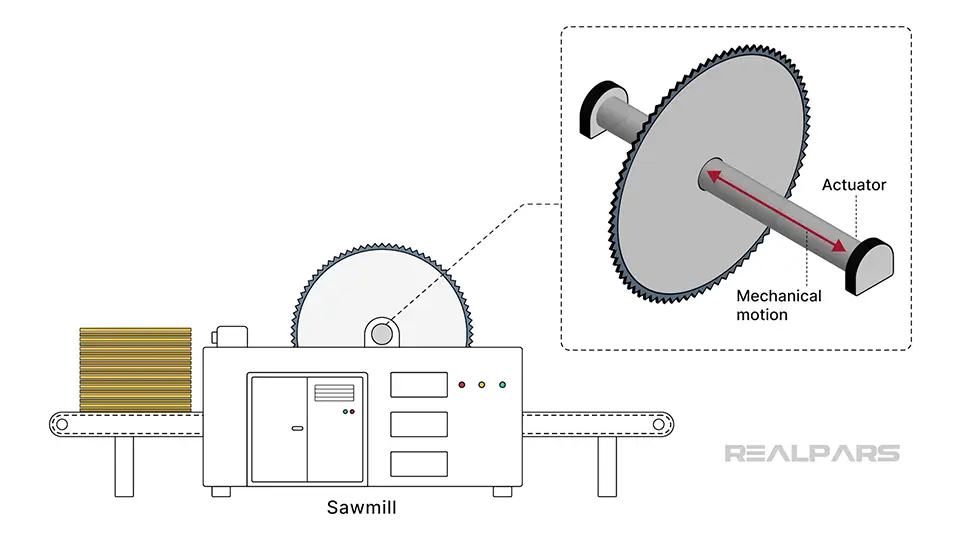
In our sawmill scenario, the actuator must move the saw blades to a precise position relative to the lumber passing through the conveyor.
Proportional valves control the movement and speed of actuators such as hydraulic cylinders or motors.
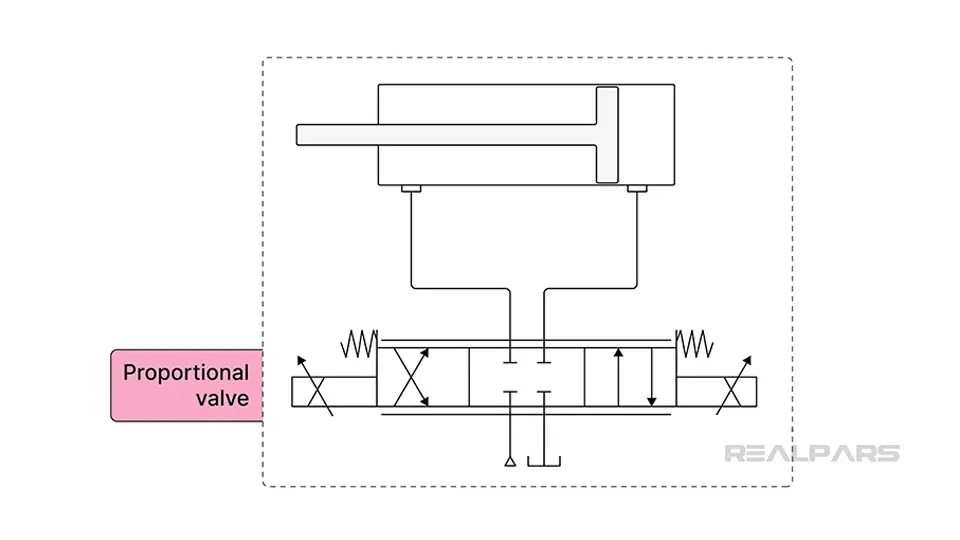
Controller
The Controller is the Device that examines the difference between our controlled Variable's current state and its desired state. The controller determines what action is to take place and generates an output signal that is a function of the result of this comparison.
Motion controllers create and calculate the commands that guide a machine's function. You can choose motion controllers based on the number of axes, update time, resolution, and the type of motion supported.
Can you use the same device for process control and motion control? Several years ago, the answer to that question would have been a “hard no.” Many of today’s controllers are capable of both process and motion control.
Vendors like Delta have dedicated motion controllers like the RMC75, which can control two axes. This little beauty has full PID loop control with velocity and acceleration feedforwards.
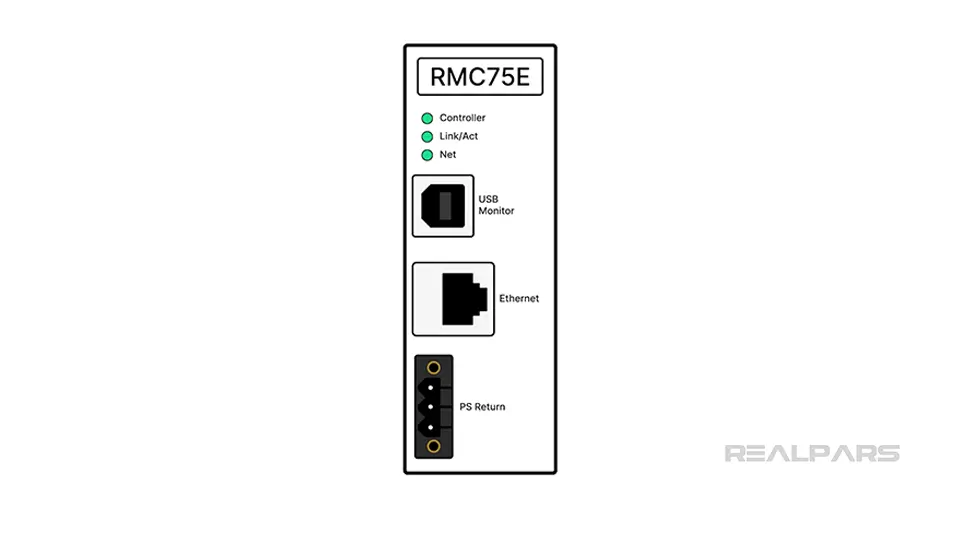
Older traditional PLC controllers cannot offer the precision control available on the Delta controller.
Amplifier
The RMC75 requires an additional device, such as the Delta MA1, to provide the drive and amplification needed to move the actuator.
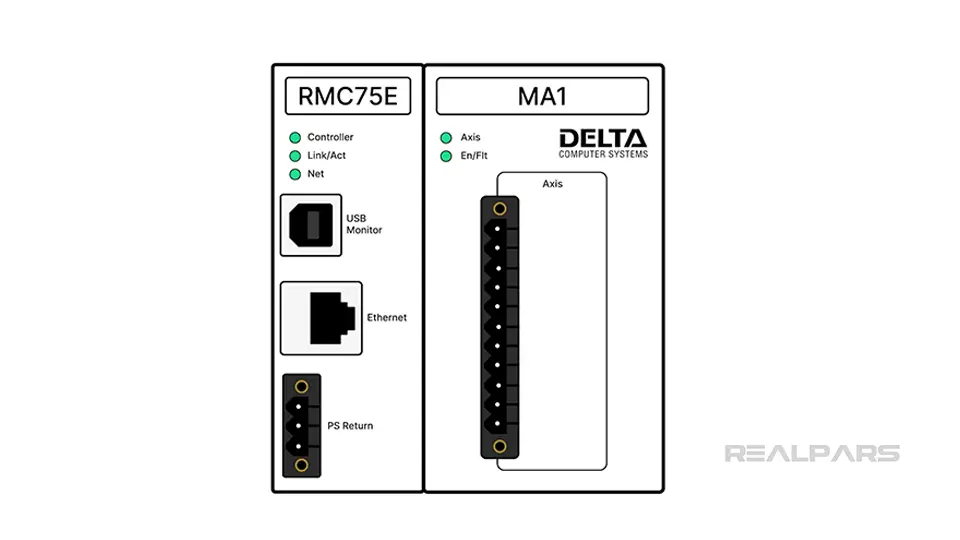
Amplifiers convey the amount of current and voltage needed to drive the actuator. In other words, the amplifier receives information from the motion controller and relays it to the actuator through a driver.
Vendors such as Omron offer multi-function controllers. The Omron NX5 can be both a process and motion controller while simultaneously controlling up to 64 axes.
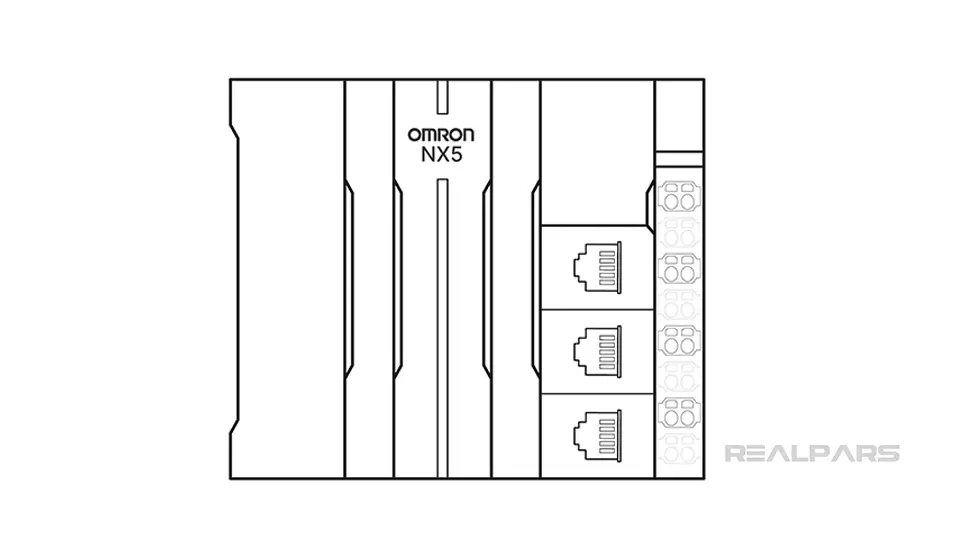
Feedback device
Feedback devices are sensors that provide information about the moving parts' position, speed, and other parameters.
Standard feedback devices include encoders to measure the position and speed of rotating shafts and linear displacement devices such as a magnetostrictive linear displacement transducer or MLDT.
Encoders provide real-time position data of a motor or a moving part in a machine. In an incremental encoder, the position is tracked by counting the number of pulses from a reference point. In an absolute encoder, the exact position is always known without needing a reference point.
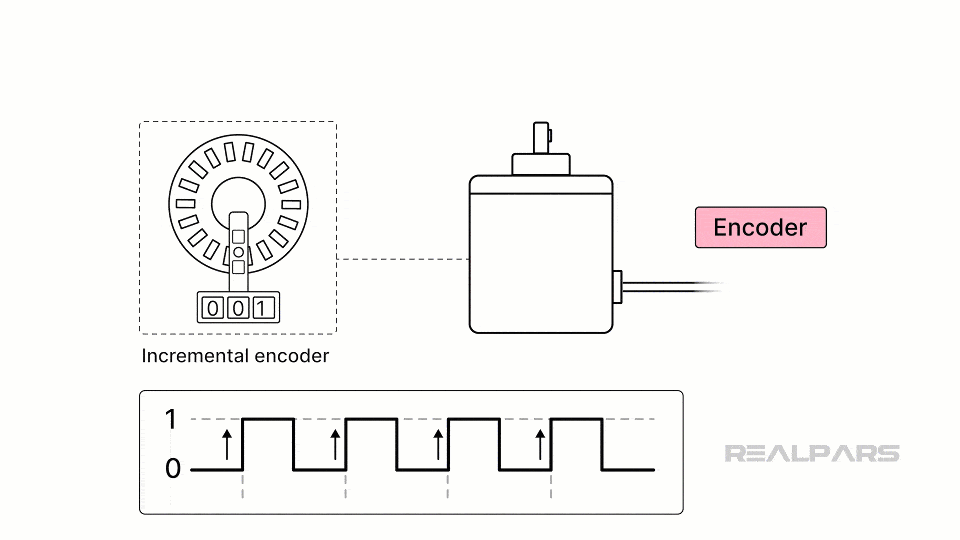
In an absolute encoder, the exact position is always known without needing a reference point.
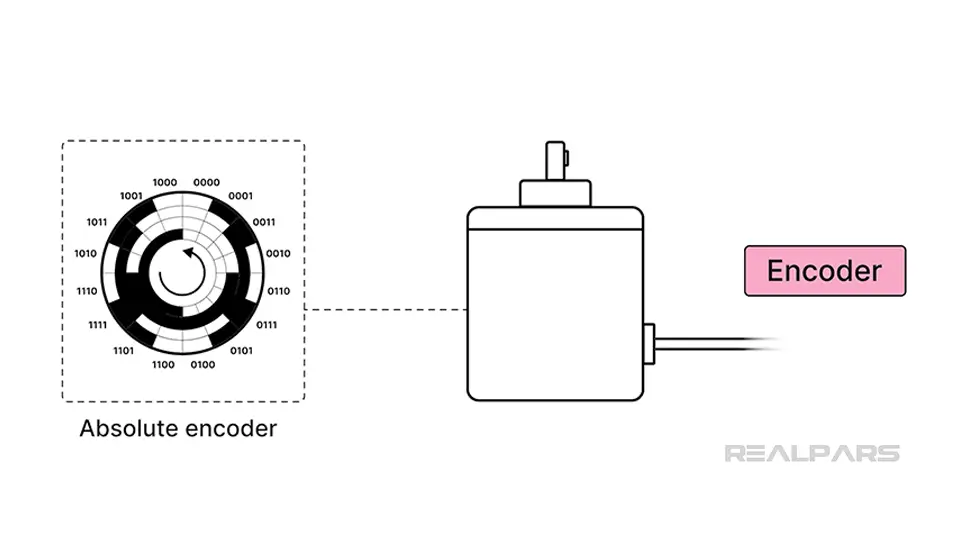
Encoders are also used to determine speed by measuring the frequency of the pulses generated by an incremental encoder.
A commonly used MLDT in the sawmill industry to determine position and speed is the Temposonics L-Series Start-Stop.
An MLDT works based on the principle of magnetostriction, which is the property of certain ferromagnetic materials to change their shape or dimensions in a magnetic field. The Temposonics website is an excellent source for more detailed information.
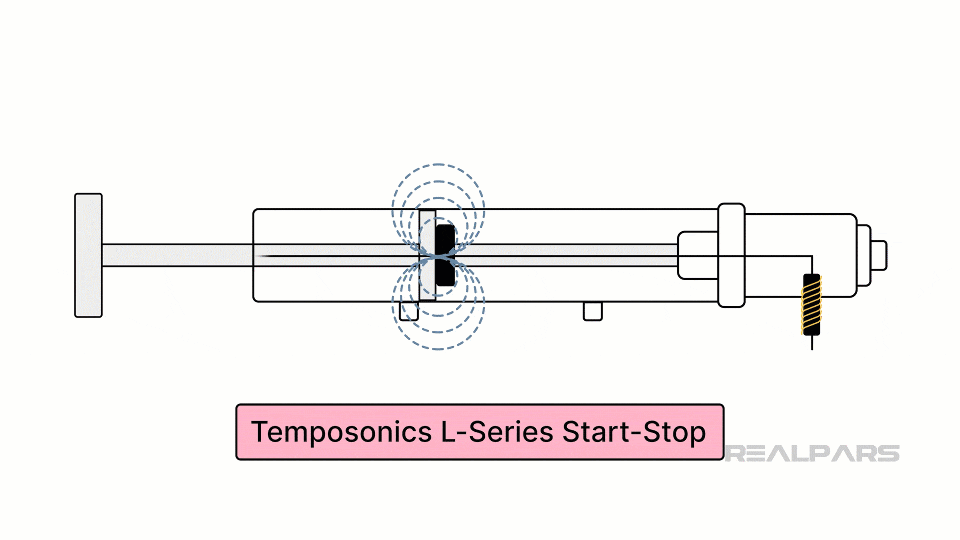
Control loop
When we put it all together, this is what we get. The Temposonics MLDT informs the controller of the saw position. The Controller compares the actual position with the desired Target Position.
The controller performs rapid calculations based on preset conditions and provides corrective action to the amplifier. The hydraulic proportional valve moves the saw actuator to the desired position.
As you can imagine, this action needs to be precise and occur in the blink of an eye. Having the saw in the right position is essential, and any deviation from the target position could result in defects or worse.
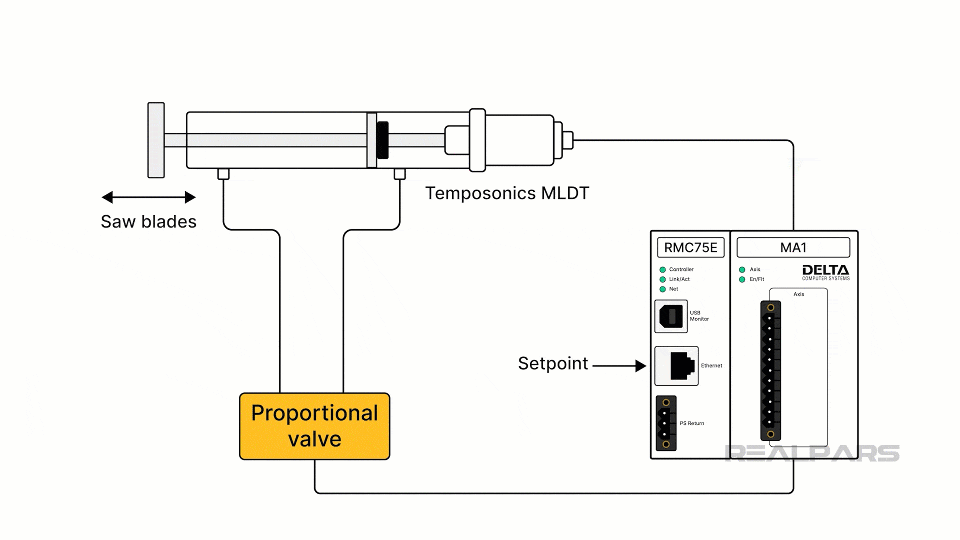
Summary
That’s enough for now…
Let’s have a quick summary of what we’ve discussed…
- Motion control refers to the methods used to precisely regulate and control the movement and position of mechanical systems.
- Motion control is used in many areas, such as manufacturing, Robotics, and Aerospace.
- The four essential components of a motion control system are the controller, driver/amplifier, sensing/feedback devices, and actuator.
- The Motion control system control loop block diagram resembles a process control loop.
- Acceptable responses to setpoint changes or disturbances differ in Motion and Process Control.
- Many vendors offer multi-function controllers that can be both process and motion controllers.
If you want to learn more about motion control, check out the Motion Control skill path at realpars.com.