In this article, we will introduce you to the OMRON NX5 machine controller. We’ll discuss many of the NX5 features and highlight the Automation Playback function.
Alright, let's kick things off with a bit of history.
History
Omron launched the first machine automation controller NJ series in 2011.
The NJ controller is a member of the PAC or Programmable Automation Controller category and supports both EtherCAT and EtherNet/IP making it easy to speak with other devices and networks.
NJ controllers incorporate advanced motion control capabilities, making them suitable for applications such as robotics and precision motion.
Two years later, Omron introduced NX I/O modules to provide seamless and flexible I/O expansion options for NJ controllers.
These I/O modules support the safety controller NX-SL3 series using FSoE, or Safety over EtherCAT communication.
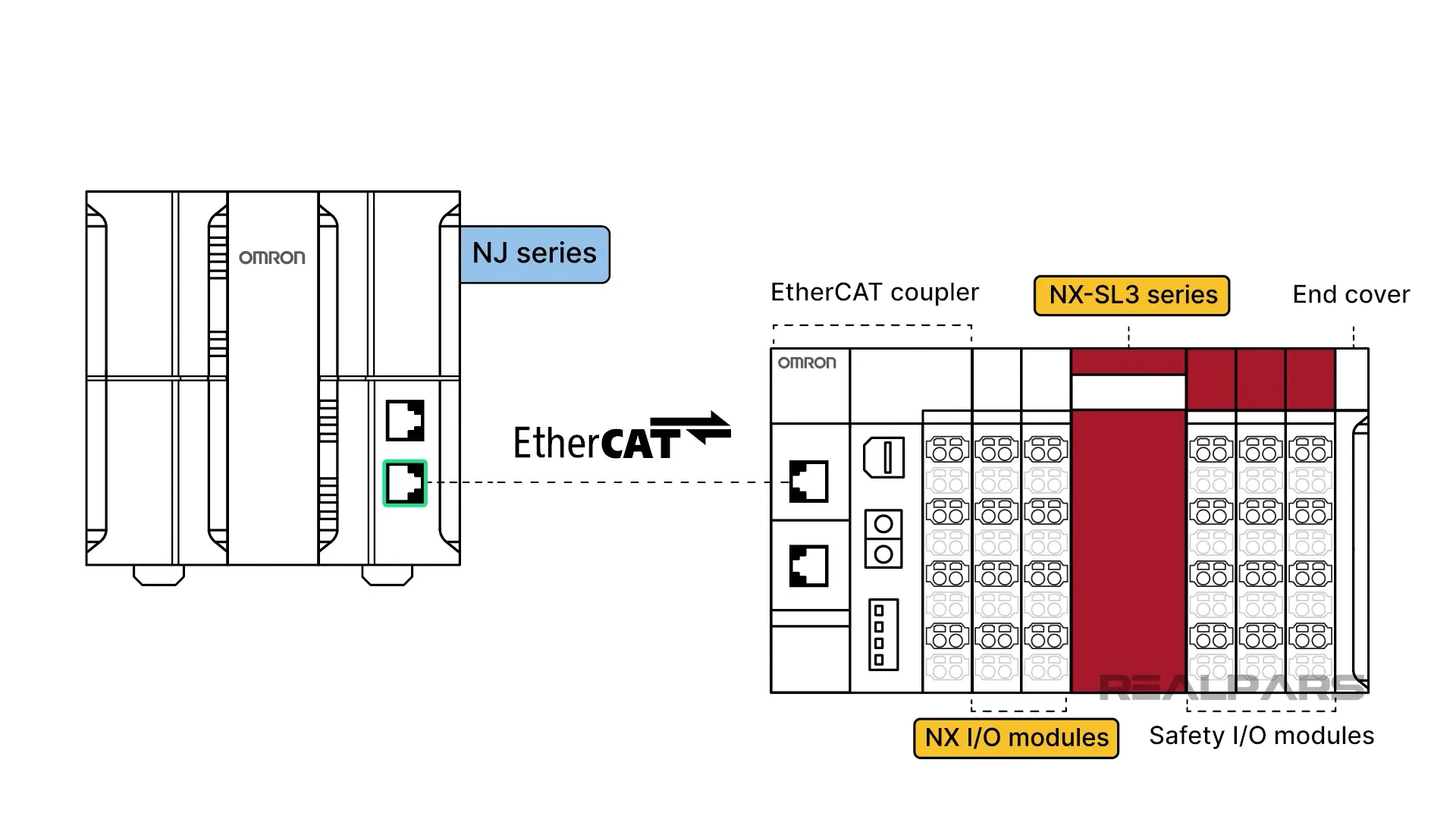
In 2015, Omron introduced the new machine automation controller NX7 Series. The NX7 architecture was based on the Intel® Core™ processor significantly increasing instruction speed.
NX7 began to integrate machine learning and artificial intelligence (AI) capabilities, enabling predictive maintenance and data-driven optimization.
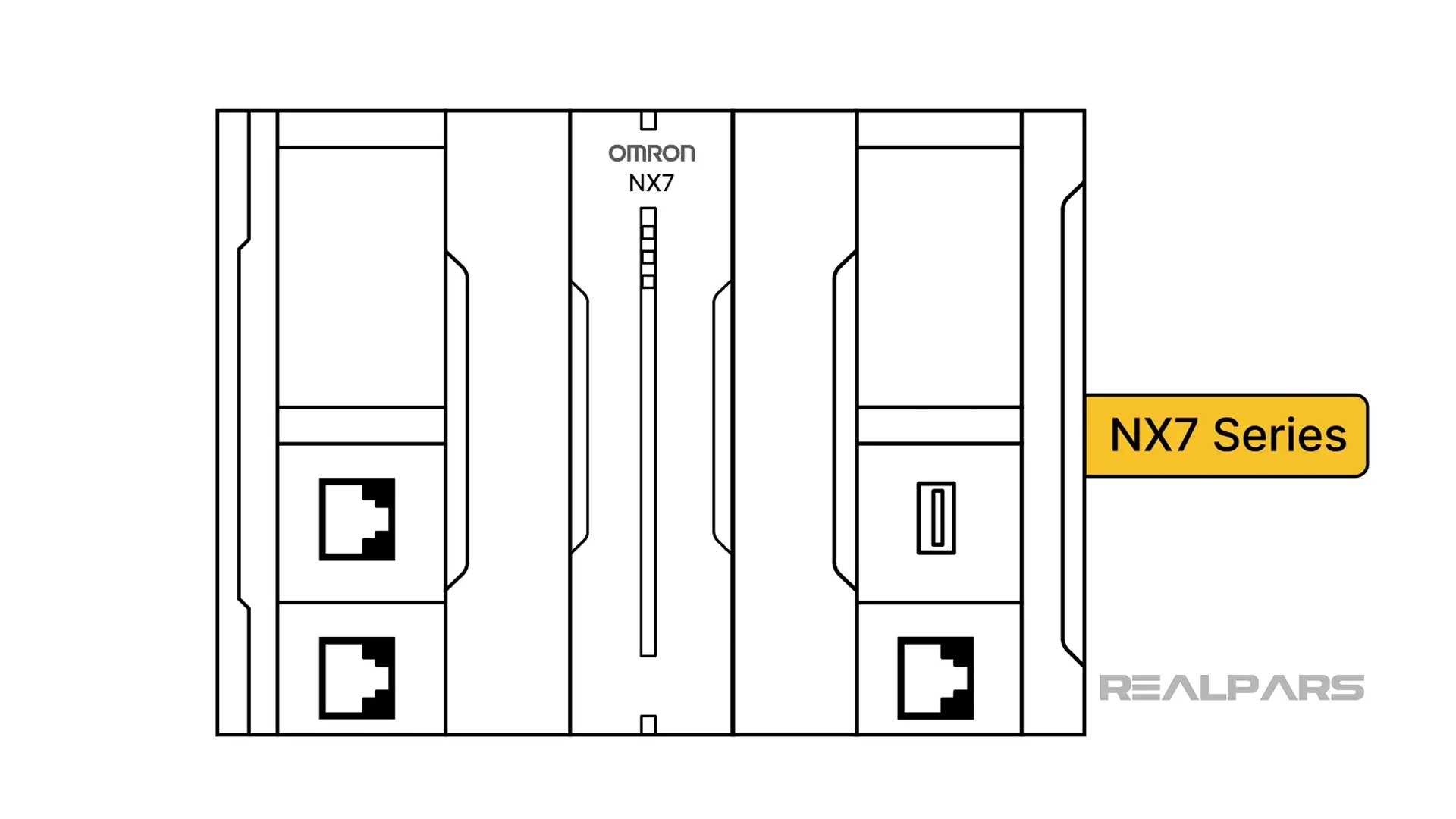
In 2018, Omron added the new NX1 controller series and the new safety controller NX-SL5 series. The NX-SL5 provides integrated CIP, or Common Industrial Protocol Safety within the NX series.
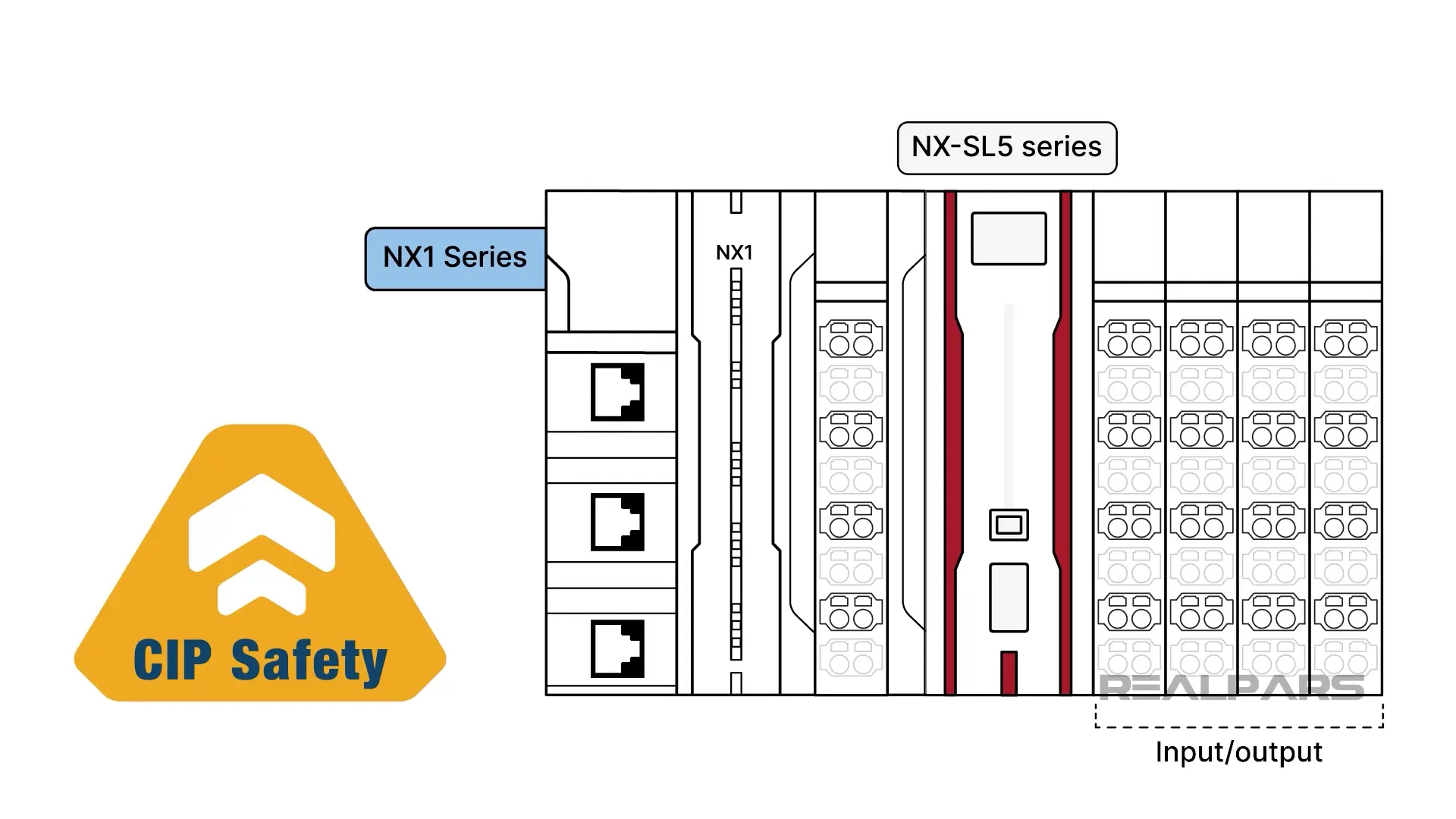
Then along came the NX5 Programmable Automation Controller in April 2023.
As with the NJ/NX controller series, the NX5 controller is part of Omron's Sysmac automation platform thus providing a range of advanced features for industrial automation applications. Programming is accomplished using Omron's Sysmac Studio.
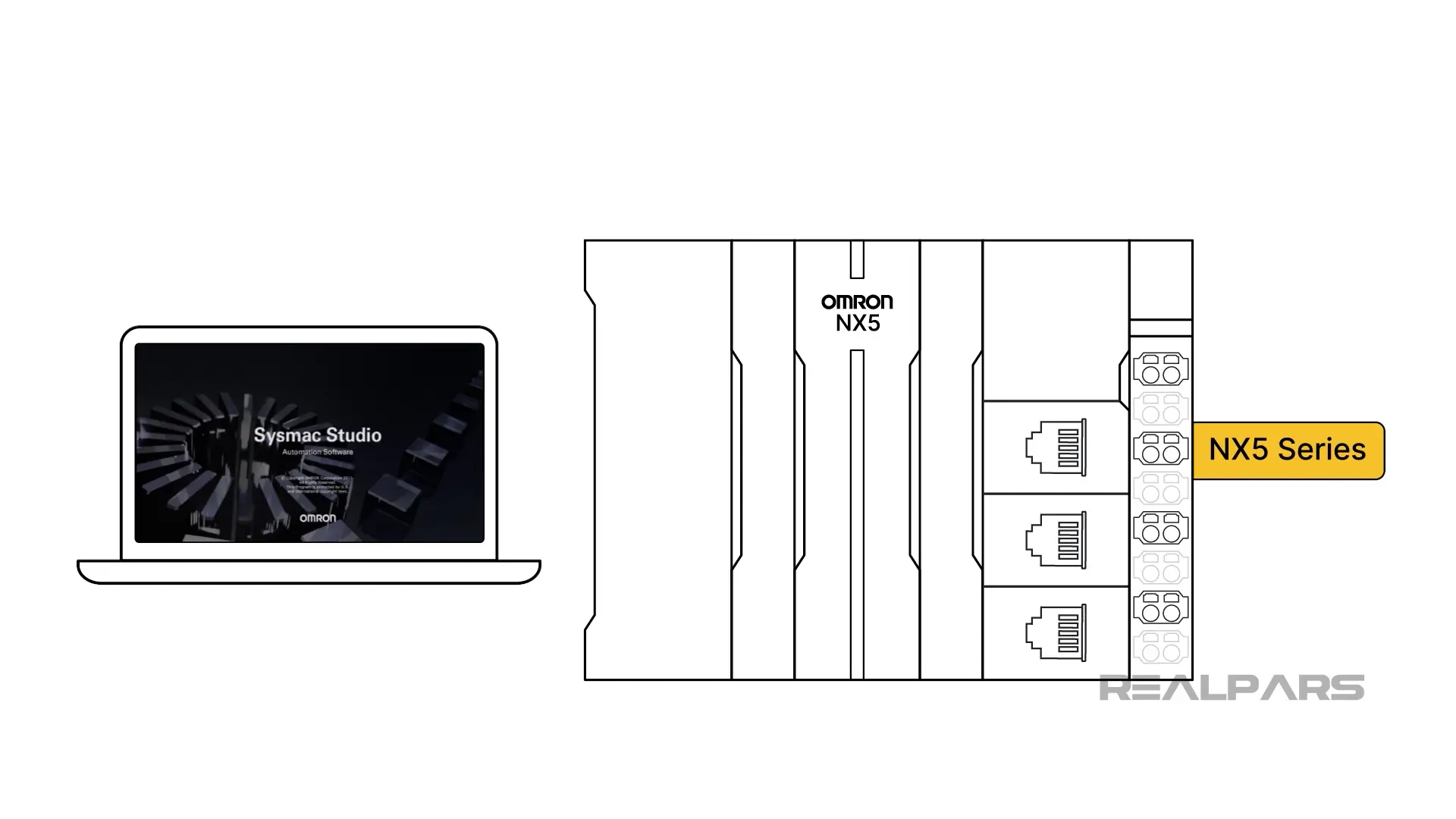
Alright…that’s the end of the history lesson.
NX5 features
Enhancements and developments are ongoing but let’s introduce you to the NX5 current features.
High-Speed database communication
The NX5 controller offers fast processing speeds enabling quick execution of control programs and efficient handling of complex automation tasks. It supports real-time data handling and connectivity to other systems and devices, including cloud integration and IIoT features.
In today’s highly automated production facilities, high-speed database communication is imperative when real-time production line analysis is required.
The NX5 is capable of direct connection to an SQL database as a standard feature requiring no extra software or middleware further reducing real-time analysis time.
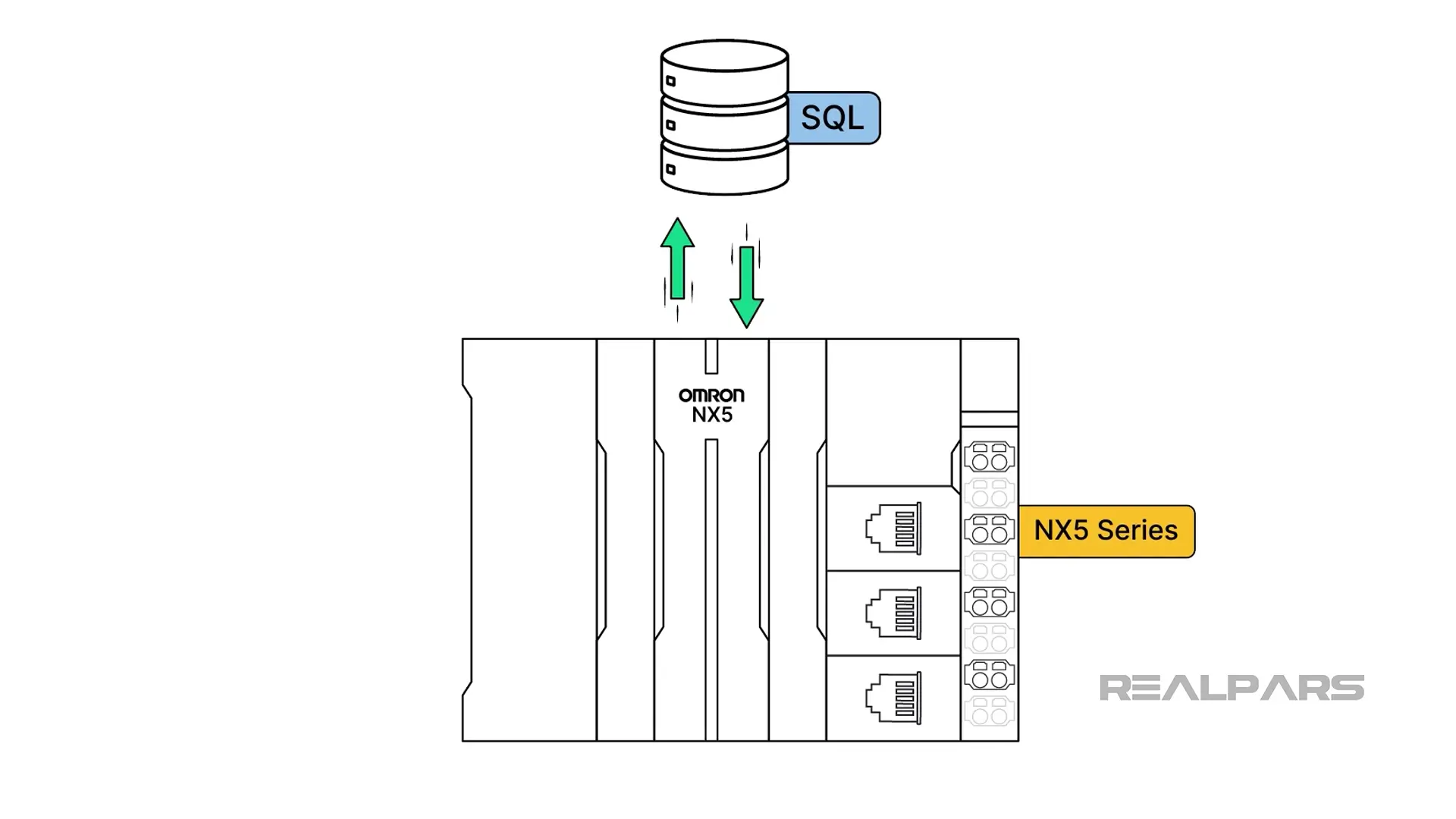
The NX5 also works well with MQTT and OPC UA.
The NX5 can collect data from all EtherCAT® I/O synchronously and can have up to 4 Ethernet/IP units mounted to it. Each Ethernet/IP unit has two ports.
Up to 10 Ethernet/IP networks can be built using the built-in NX5 Ethernet/IP ports alongside expansion Ethernet/IP units. Each Ethernet/IP port is capable of high-speed communication up to 1Gbps.
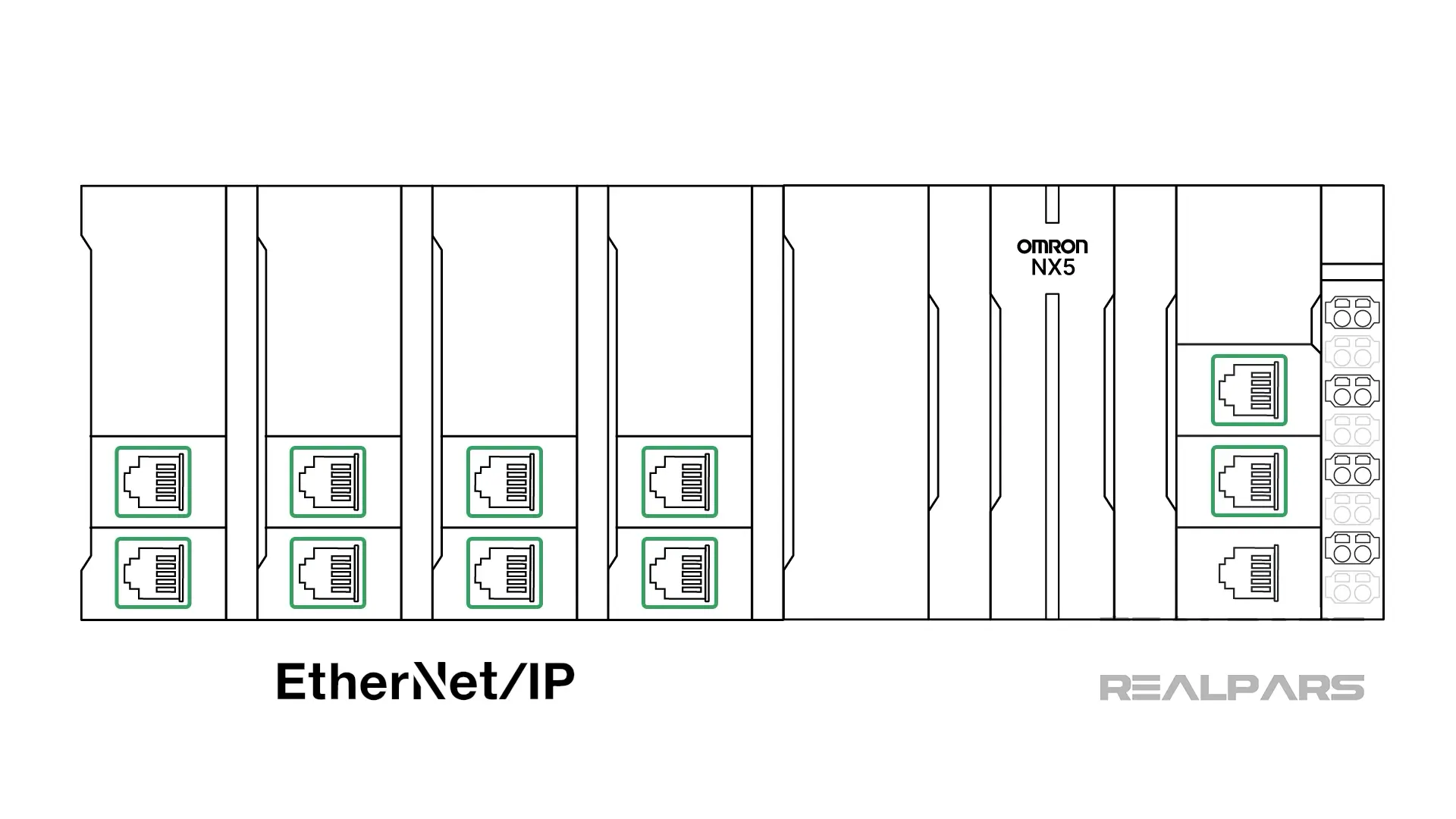
Having the capacity for 10 separate Ethernet/IP networks goes a long way in satisfying the need for large-capacity data communication.
Safety
Ok…let’s move on to Safety Systems.
NX5 controllers can integrate safety control functions within the same system, ensuring safe and efficient operation.
Traditionally, production line safety communications are configured on a single network. The NX5 multi-network ability allows production line modules to be controlled as isolated processes that can be shut down without stopping the entire line.
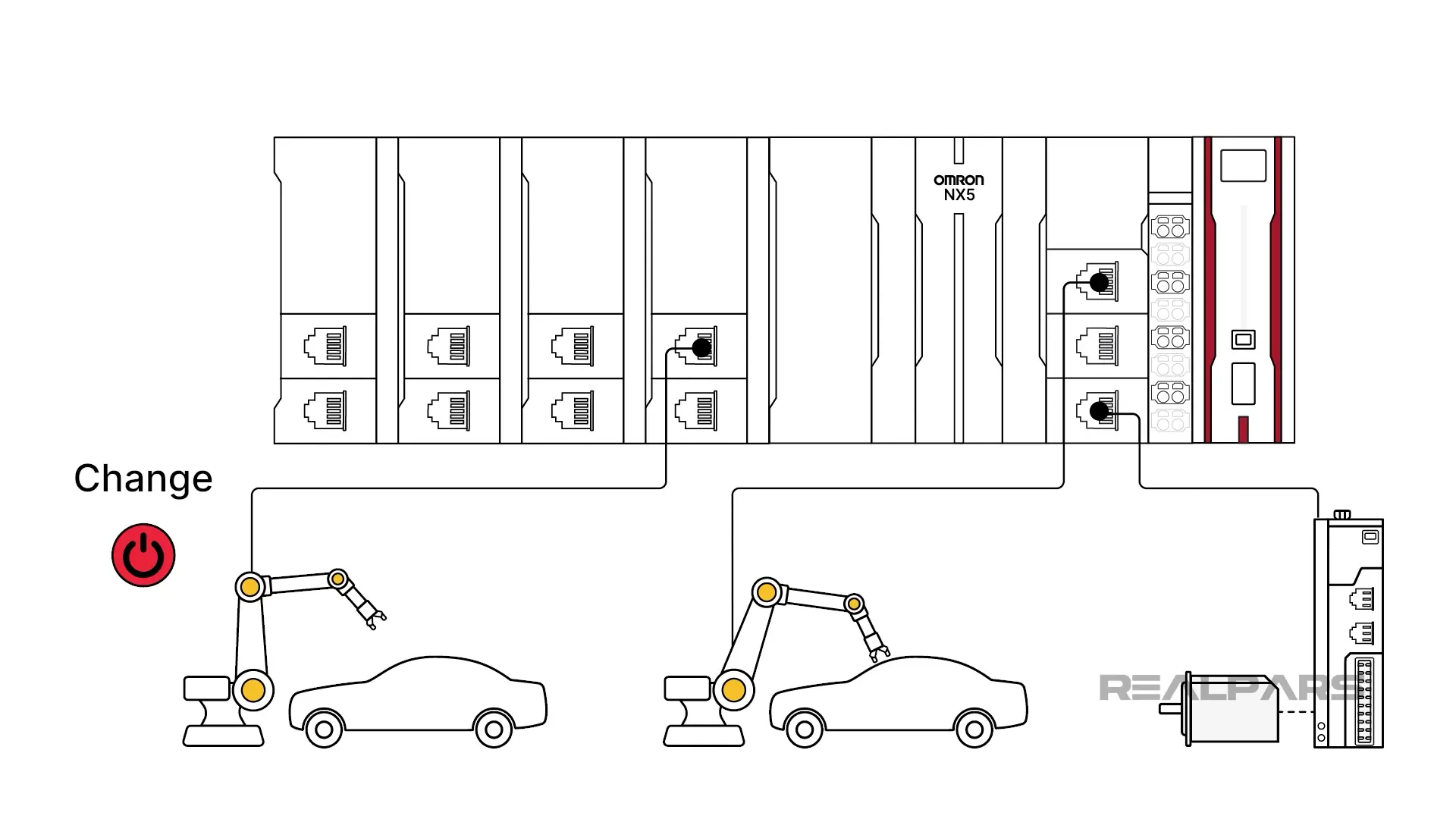
Ten separate networks and 254 safety connections are possible.
The NX5 is programmed using Omron's Sysmac Studio software that supports programming in various languages such as Ladder Diagram, Function Block Diagram, and Structured Text.
Automation Playback
The last new feature we’ll introduce is Automation Playback.
What is Automation Playback?
This feature combines the power of Sysmac Studio with the NX5 controller to visually collect and playback control behavior data to identify problems that are hard to reproduce.
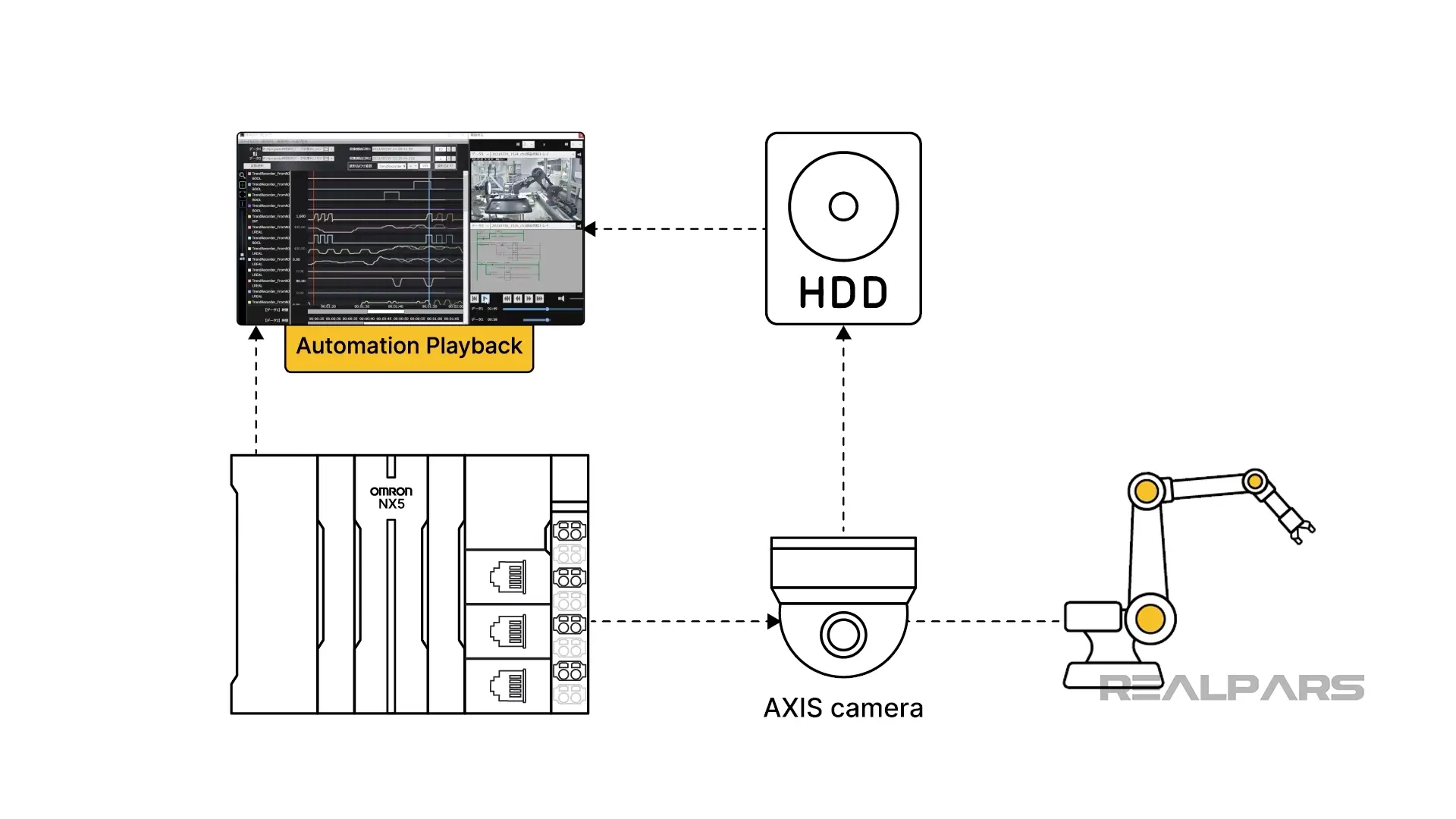
Automation Playback provides some interesting features…
You can record and replay the status of equipment in the event of a short-time or intermittent breakdown. The lead time for identifying the faulty culprit is reduced significantly. You don’t even have to be onsite to identify the fault.
Automation Playback benefits
So…how advantageous can this be to your production line?
Let’s say you are starting up some new equipment using trial and error. There are problems, but the movement is too fast, the change is too subtle, and you can’t see the problem with the human eye.
Maybe there are problems caused by machinery hidden under protective covers. Or, it’s a nasty intermittent fault that occurs randomly and you don’t have time to watch until it happens again.
You are in a situation where your production line can’t start as equipment acceptance cannot be confirmed.
What about problems in remote areas? How do you identify the problem if you need to send a maintenance technician each and every time? The operating rate is poor and quality is compromised, not to mention the increase in maintenance costs.
Many companies attempt to troubleshoot problems using PLC programming tools and rely on the skills of engineers and technicians. Not every company has the skilled people onsite to perform this type of troubleshooting resulting in wasted time and expensive skill transfer.
Using a typical system layout, as the ladder logic program is executed, a camera records and stores visual actions in a Hard Disk Drive. Sysmac Studio is used to review the video recording and observe I/O and program operation.
Demonstration of Automation Playback
OK…We’ve got a short Sysmac Studio demonstration for you…
Once Playback is started, you can see the recorded video footage of the actual piece of equipment being observed.
The actual logic program is displayed.
And a dynamic playback of the variable conditions is also displayed.
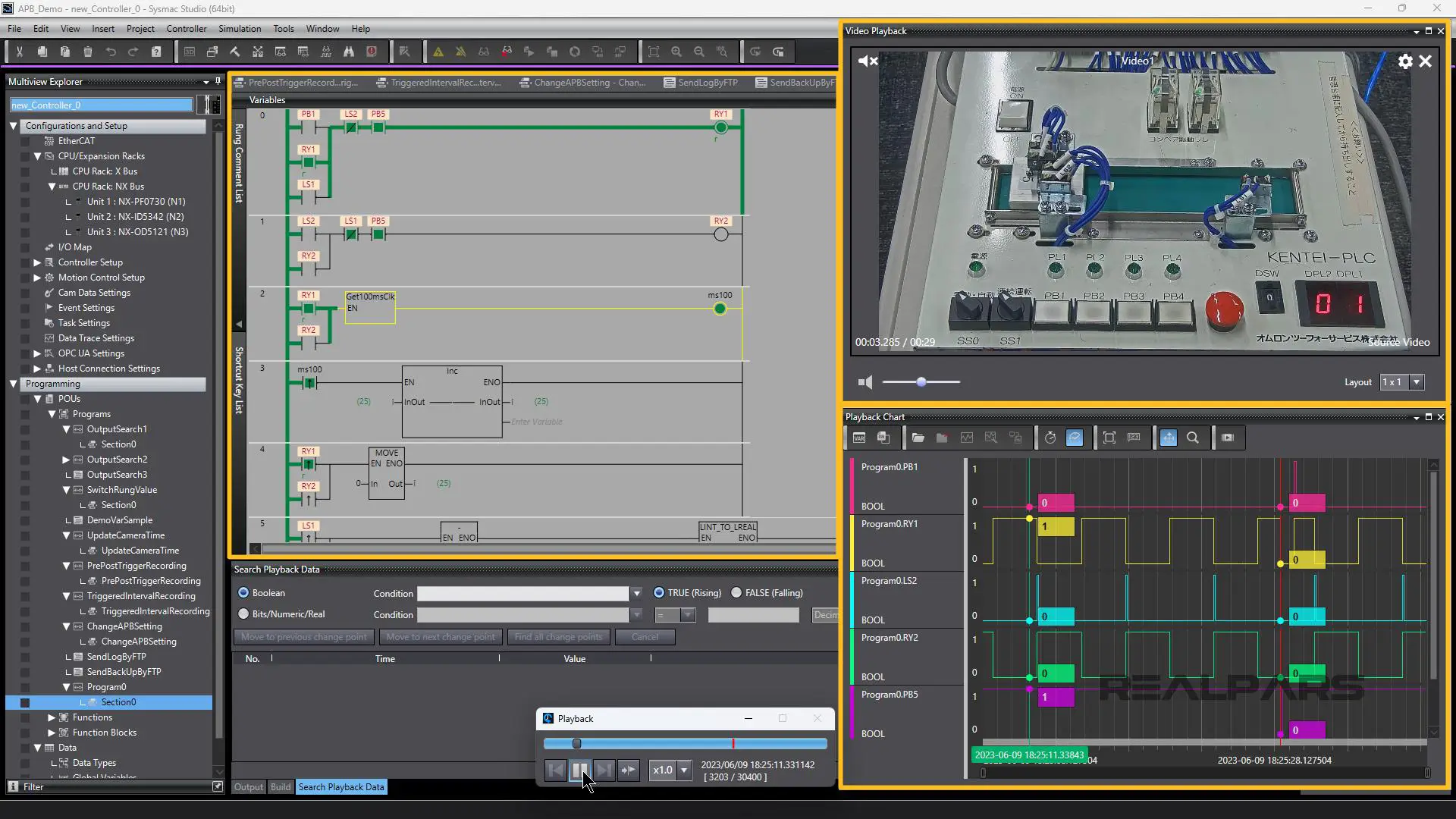
Keep your eye on the action when PB5 is pushed. We can see the PB5 change of state on the LD program and the Playback Chart.
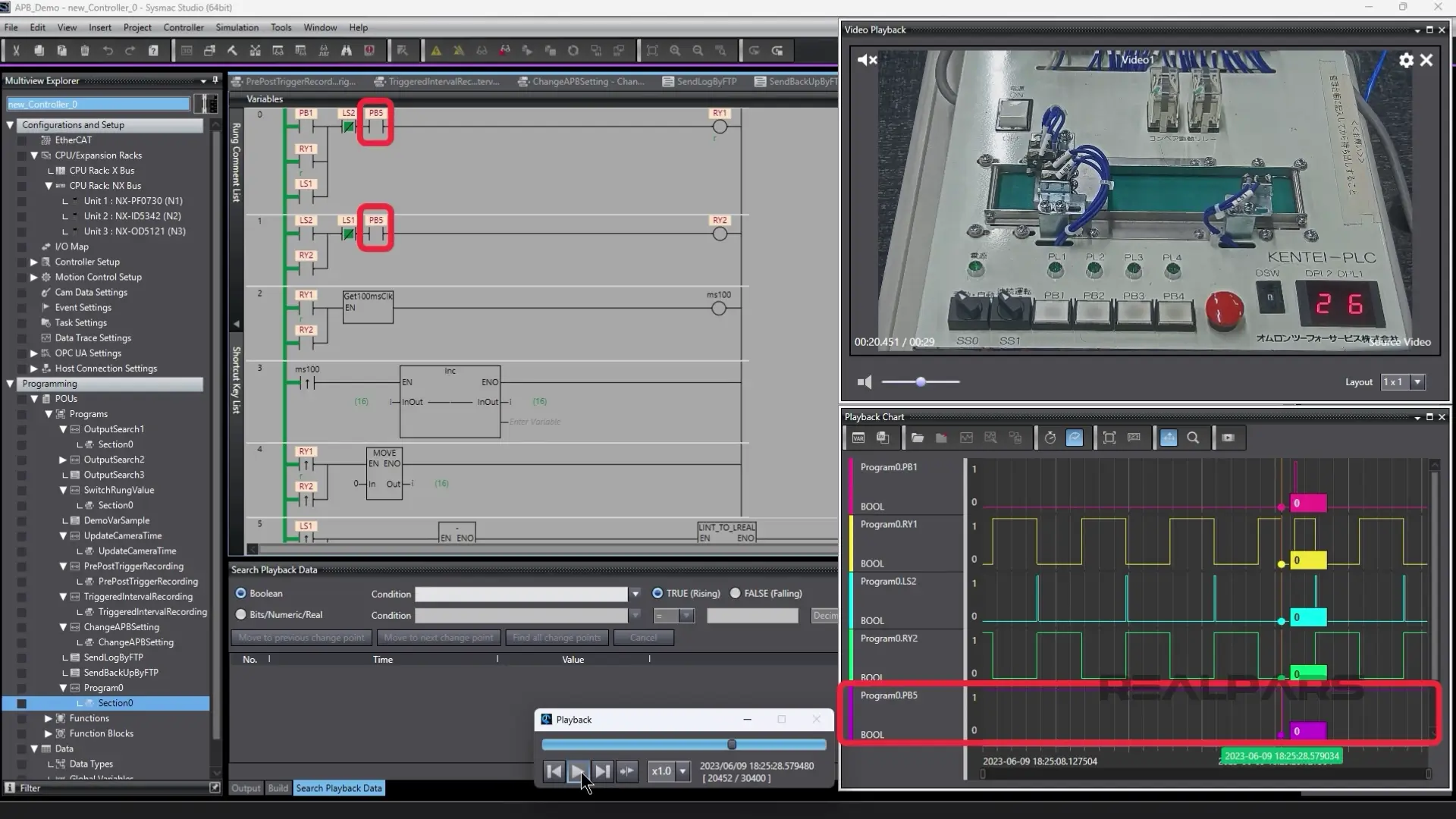
As you watch the camera footage, you can simultaneously examine sequences, flags, and variables to help pinpoint abnormalities.
Since the behavior of the equipment in the event of an abnormality can be reproduced offline using the Automation Playback feature, you don’t have to shut the production line down.
If you would like to know more about the features and functionality of the OMRON NX5 PLC, check out our course called Omron PLC Advanced Skills – NX5 Controllers. This course dives deeper into the NX5 controller and its advanced features.
This course was developed in partnership with Omron. At the end of the course, you will receive a certificate of completion from Omron Automation.