Mastering Omron Vibration Analysis for Predictive Maintenance
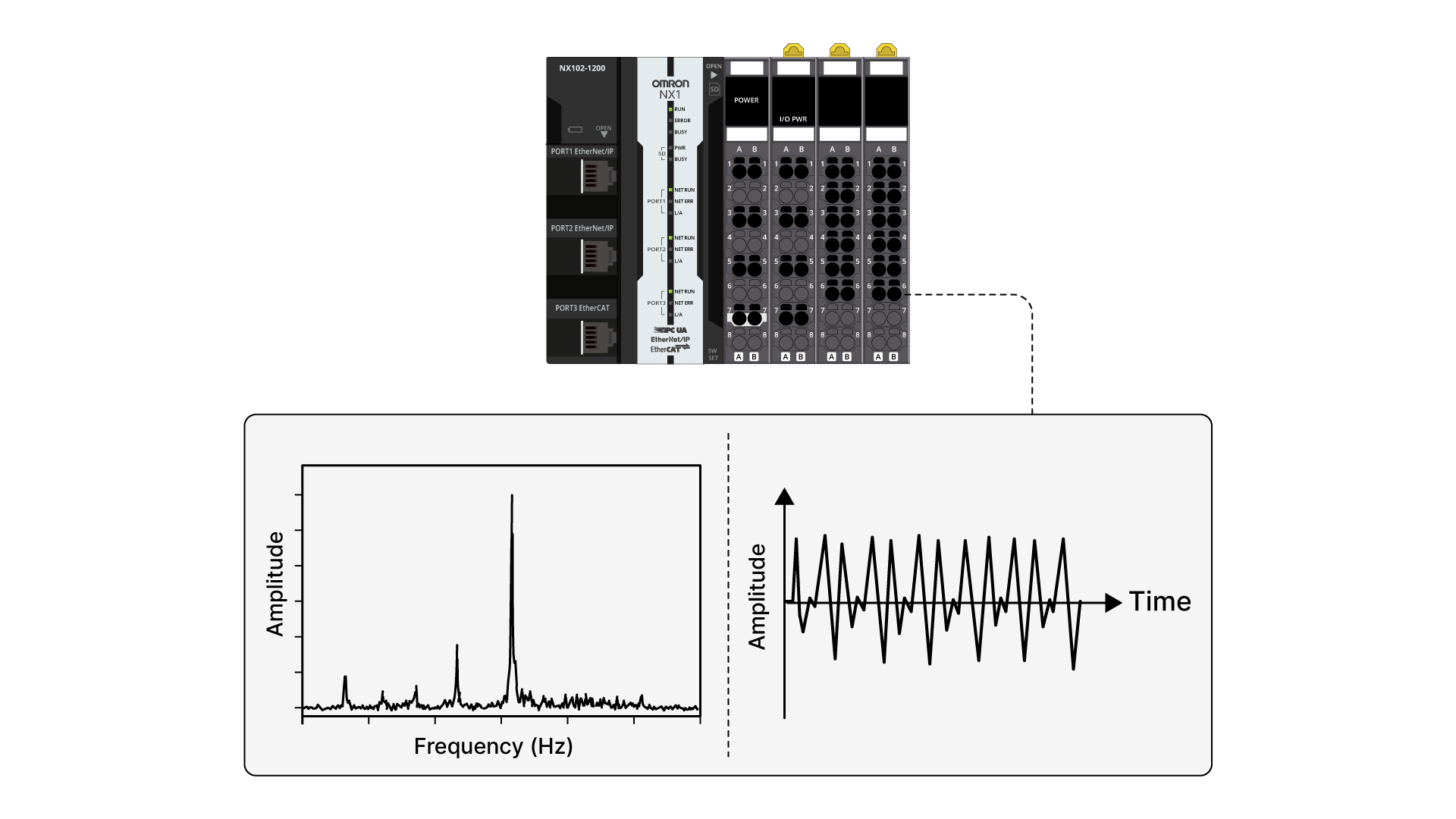
In this article, we will introduce you to the Omron Vibration Analysis Solution. The Omron process of Vibration analysis will be explained in detail, illustrated, and supported by Sysmac Studio vibration waveform analysis library.
These programs are executed on the Omron NX machine controller. But, before we get into the nitty-gritty of the analysis solution, we'll explain why vibration analysis is so important as part of a predictive maintenance scenario.
OK… let’s begin by discussing equipment failures and maintenance philosophies. It wasn’t that long ago that many companies relied on the mantra of Run it until it breaks.
Why? Well, downtime equals lost revenue, and the thinking was We can afford to fix it when it breaks.
That maintenance method proved ineffective and evolved into a preventive maintenance philosophy that involved planned routine inspections, servicing, and/or replacement of equipment parts based on predetermined intervals, usage, or elapsed time.
The idea was to prevent potential failures, reduce downtime, and extend the equipment's lifetime.
Many of you recall a Plant Shutdown of the entire production line or machine to perform such preventative maintenance. But, downtime equals lost revenue, so alternative maintenance methods evolved.
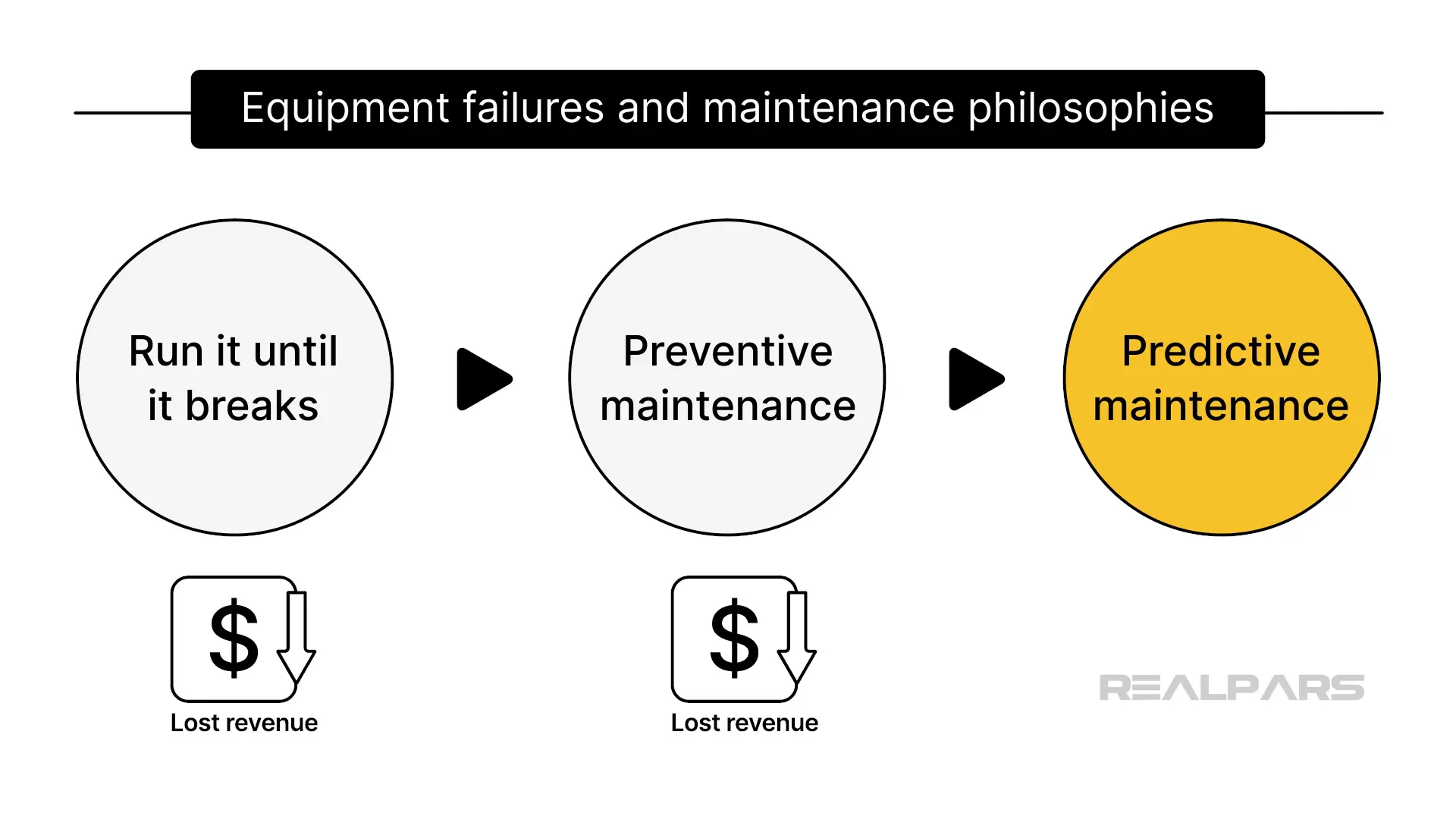
Vibration analysis for predictive maintenance
Along came Predictive Maintenance relying on real-time data and condition monitoring to predict when equipment maintenance is required in advance.
Maintenance activities are initiated when indicators suggest that deterioration or failure is imminent, optimizing the timing of maintenance tasks.
So, how do we obtain the indicators suggesting that maintenance is required?
The idea is to obtain the key data of the machine that could help us to anticipate the failure.
In predictive maintenance, there are several methods, like ultrasound, oil analysis, temperatures, and vibration analysis. Moreover, if the use of these key features is not enough, is where Machine Learning comes into the picture.
Machine learning refers to the use of algorithms and statistical models to analyze historical and real-time data from sensors and other sources to predict equipment failures or degradation before they occur.
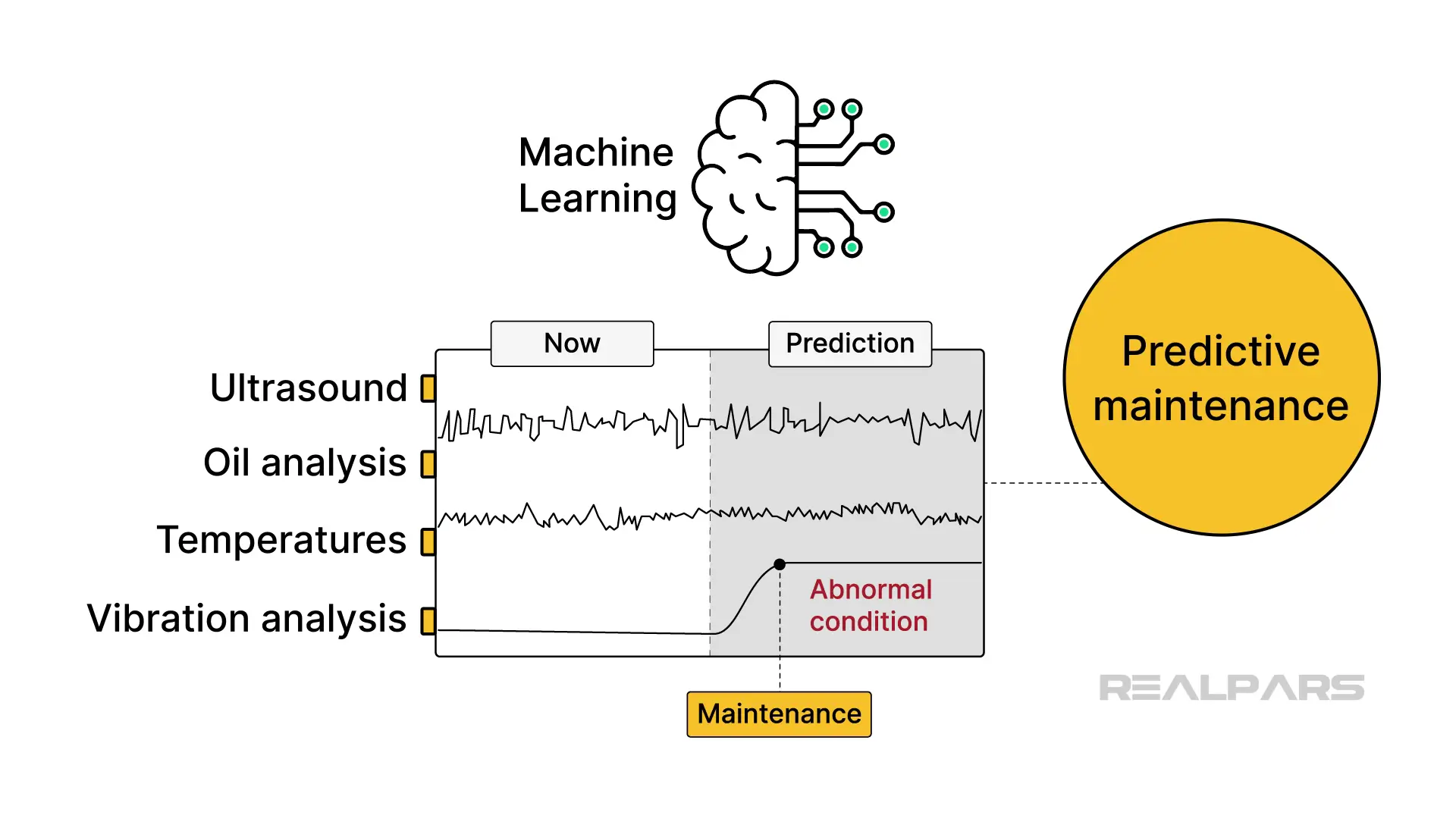
Analyzing equipment vibration detected by sensors is the cornerstone of the Omron Vibration analysis process as part of the Predictive Maintenance solution.
In a nutshell, vibration analysis is essential for predictive maintenance as it enables early detection of machinery faults, prevents catastrophic failures, optimizes maintenance schedules, reduces costs, improves equipment reliability, and enhances safety in industrial settings.
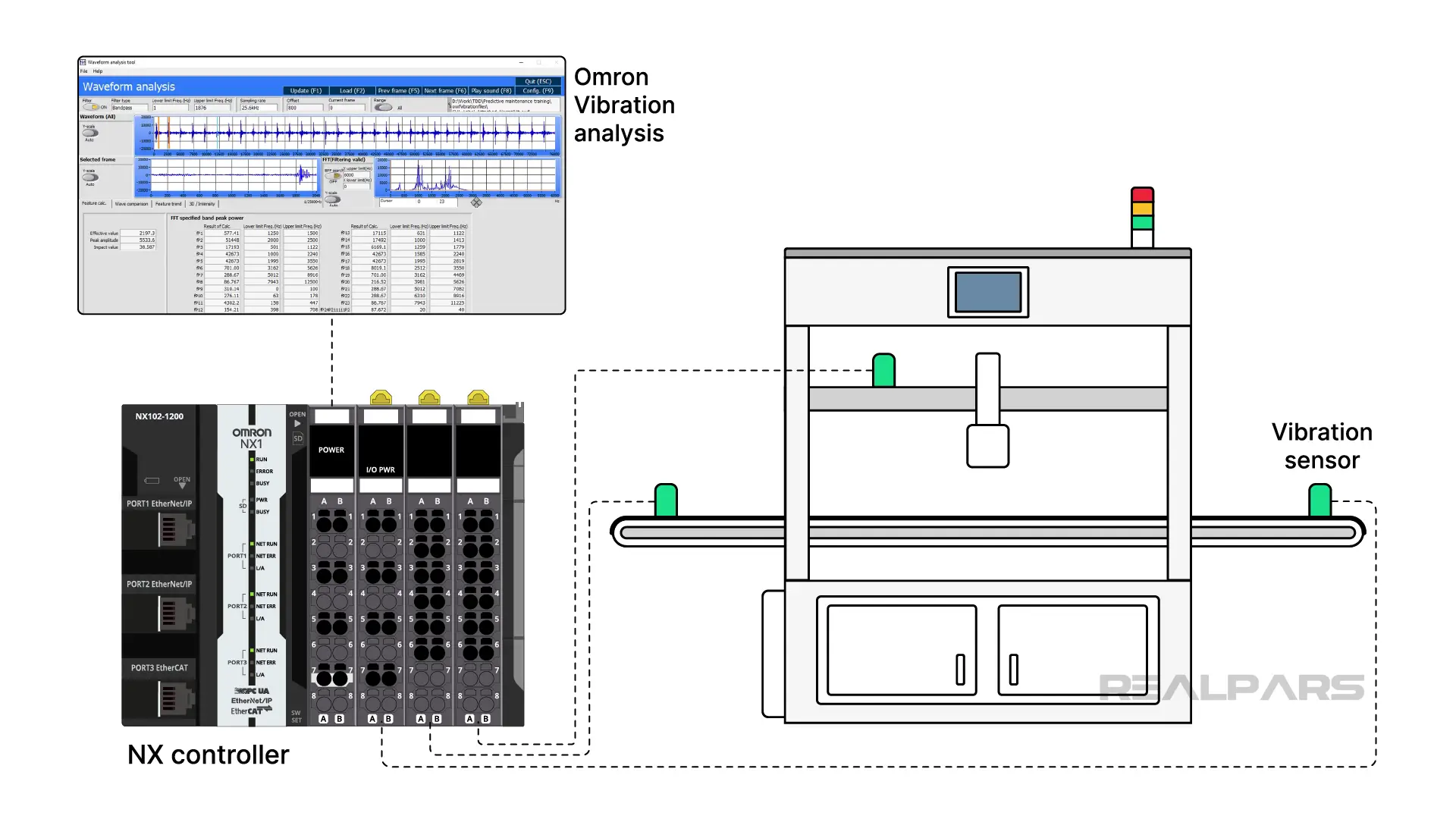
What is vibration?
Okay. So what is vibration and why is analyzing it so important in predictive maintenance?
Vibration is a mechanical phenomenon whereby oscillations occur at an equilibrium point.
We use Vibration Analysis to determine if the machine is exhibiting abnormal behavior.
Using vibration sensor data, we study the time waveforms of the vibration signal directly.
We also study the frequency spectrum which is obtained by applying a Fast Fourier Transform (FFT) converting a signal from the time domain (amplitude versus time) into the frequency domain (amplitude versus frequency).
Studying both the time waveform and the frequency spectrum of machine vibration signals provides a comprehensive understanding of machinery behavior, enabling effective condition monitoring, and fault diagnosis, and ultimately results in predictive maintenance decisions.
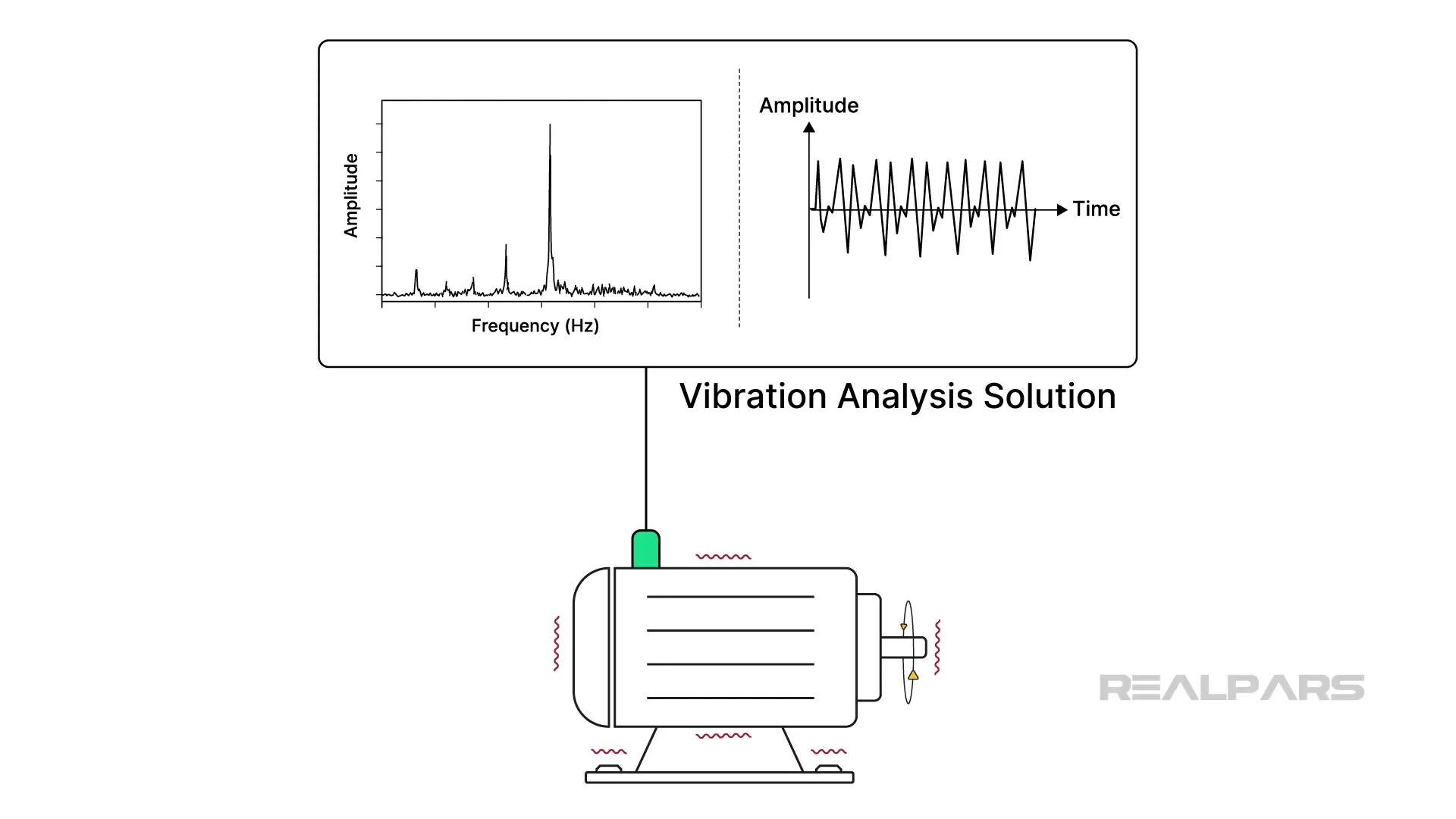
Omron Vibration Analysis Tool
Omron has developed an easy-to-use Vibration Analysis Tool. This tool calculates temporal features (like RMS-Root mean square) and spectral features like FFT automatically, provides filter options, and provides a variety of visualizations. We’ll tell you more about the Vibration Analysis Tool later.
Omron has also developed a template program that runs on Sysmac Studio. We’ll talk more about that later as well.
Let’s look at the overall architecture of the Vibration analysis solution.
Sysmac Studio is the host for the Vibration Analysis template program which contains the Waveform Analysis library Function blocks.
An Omron NX Controller is the host for the Sysmac Studio program. Connected alongside the controller is the high-speed, high-resolution NX-HAD Analog input unit.
The actual vibration sensor is an accelerometer producing very low piezoelectric charges requiring an amplifier to amplify these weak signals and convert them into a proportional voltage signal fed to channels of the NX-HAD High-Speed Analog Input Unit.
An external PC is required to receive and store the vibration data sent by the PLC via FTP. This data is analyzed by the Omron Visualization and Analysis Tool residing on the PC.
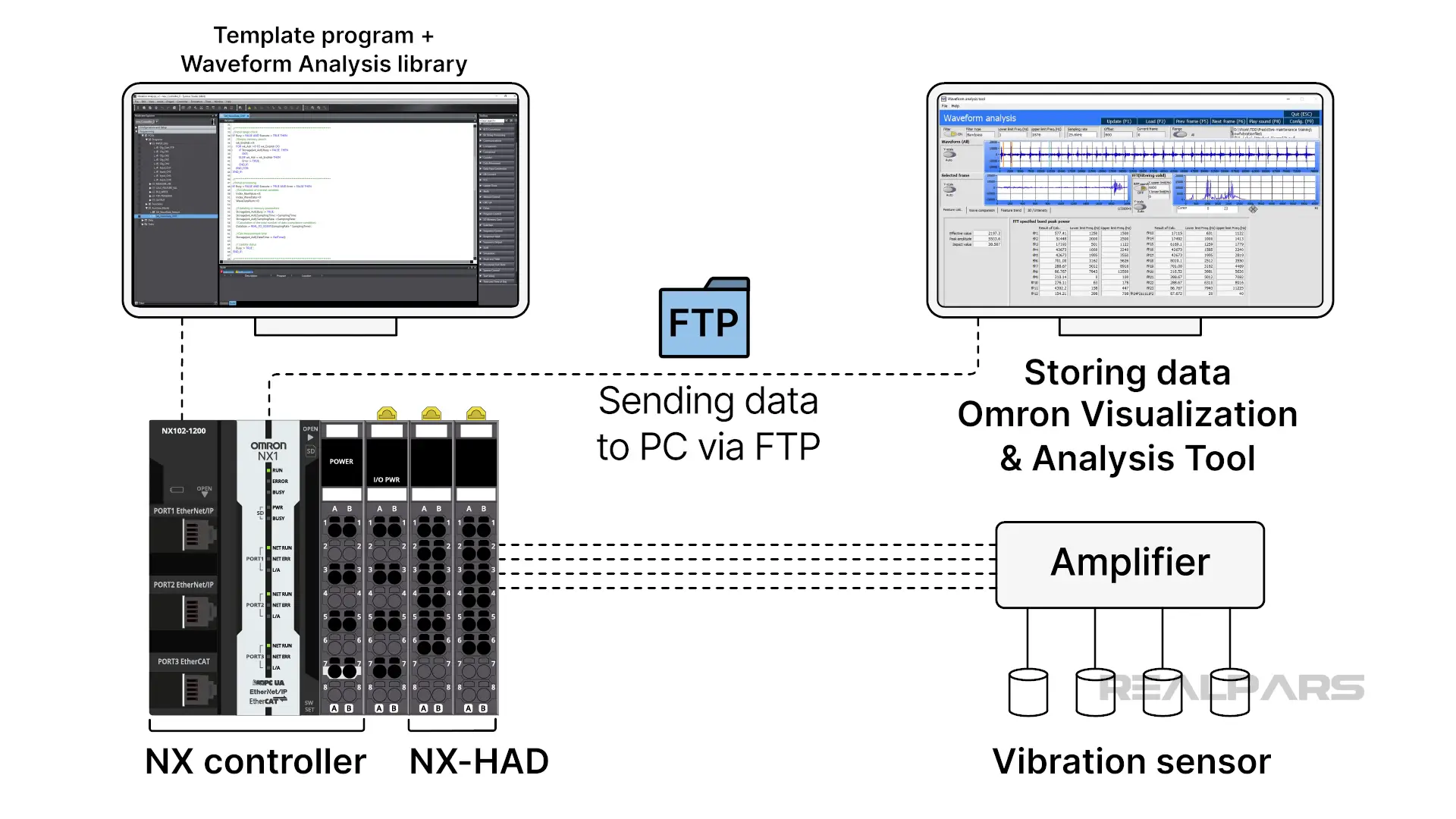
Sysmac Studio VA template
Ok… let’s go back and talk about the Sysmac Studio VA template that links all the parts together to make a usable application.
The VA template includes programming to:
Acquire data from accelerometers using the NX-HAD analog input unit, scale, and store them in a long array at 25KHz sampling frequency.
Store the data in dedicated files of a few seconds duration and send them to a repository for future analysis.
Divide the captured data into Frames and extract relevant features from it.
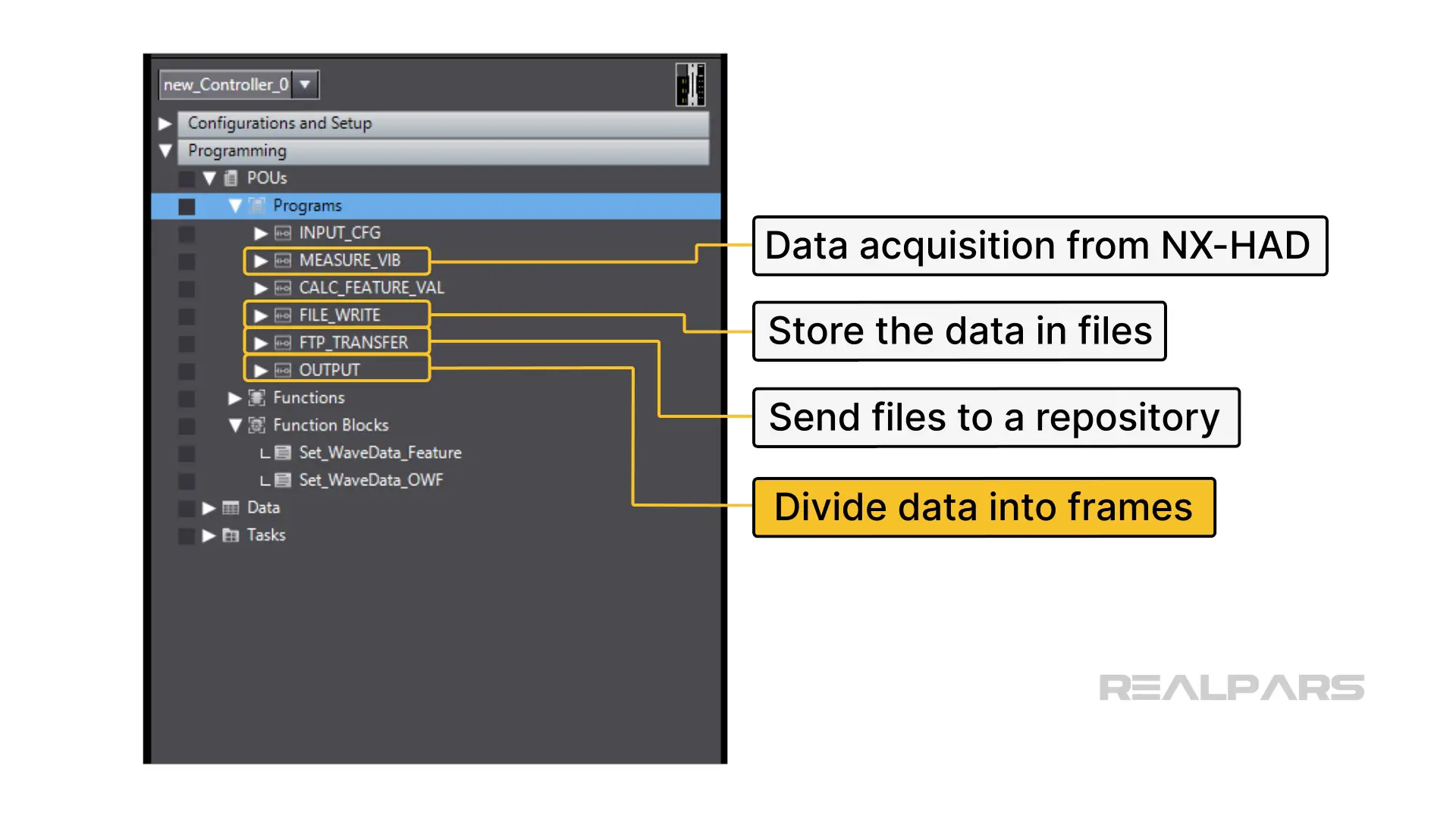
Let’s look at the Vibration analysis process.
The process has three steps:
Step 1 is Data Collection where the vibration data is measured and collected. The data is stored in a repository such as a local or remote laptop or the cloud.
Step 2 is Data Analysis using the Omron Waveform Analysis Tool on the PC. Users decide which are the right features that better identify the potential anomalies.
The ISO Standard ISO 20816-3:2022 defines the norm for the Measurement and evaluation of machine vibration.
Step 3 is optional as some customers just want to collect key data to be monitored. This is the Data Utilization step where the feature values detected during Data analysis are used to devise an abnormality detection program.
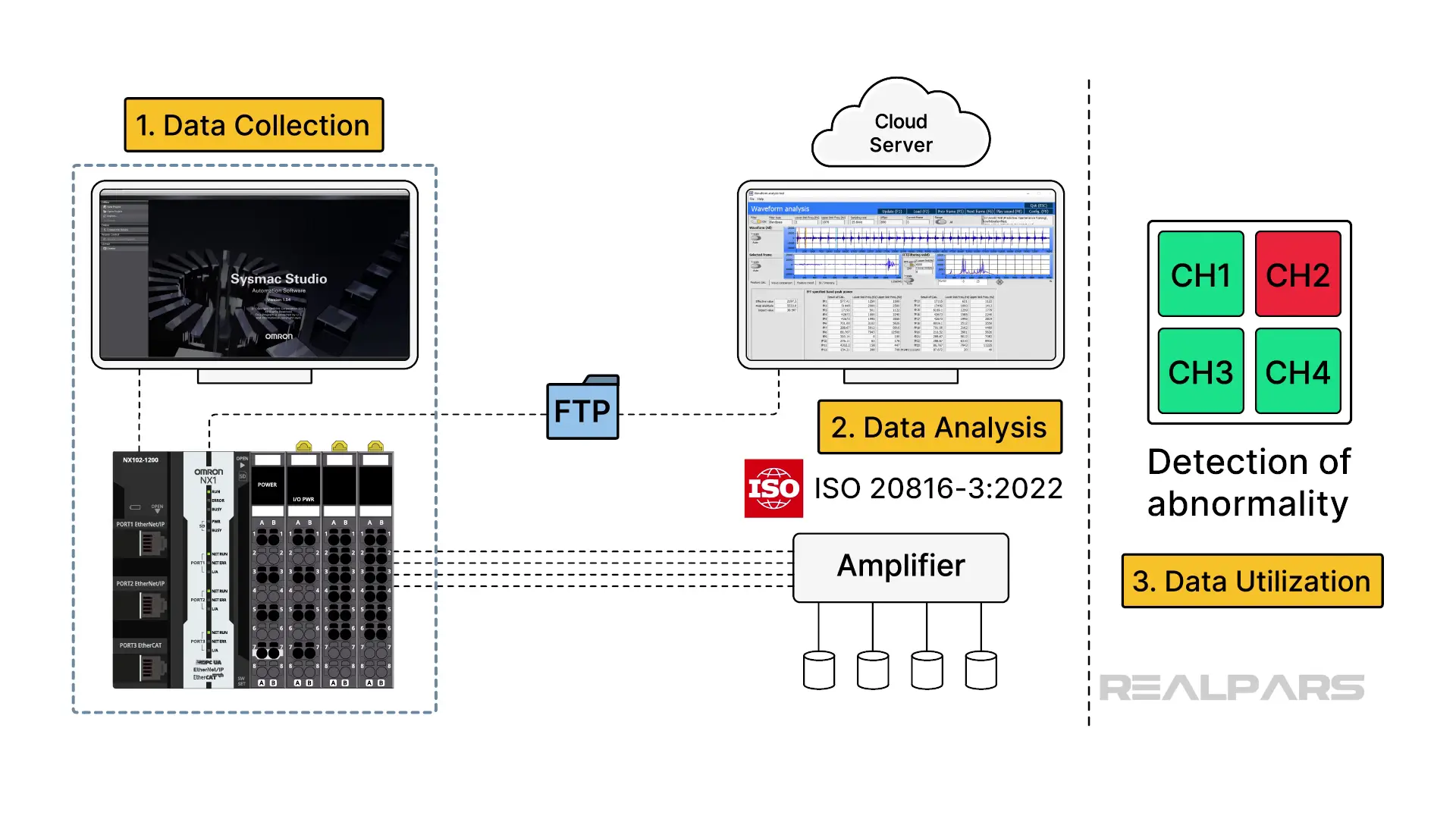
The Vibration Analysis template programs
We’ll start by drilling down into the POU Programs of the Vibration Analysis Template program running on Sysmac Studio.
The first program establishes the System Configuration, including FTP communication setup, measurement settings for and scaling for the NX-HAD analog input signals from the accelerometers, and also input channel measurement start/stop settings.
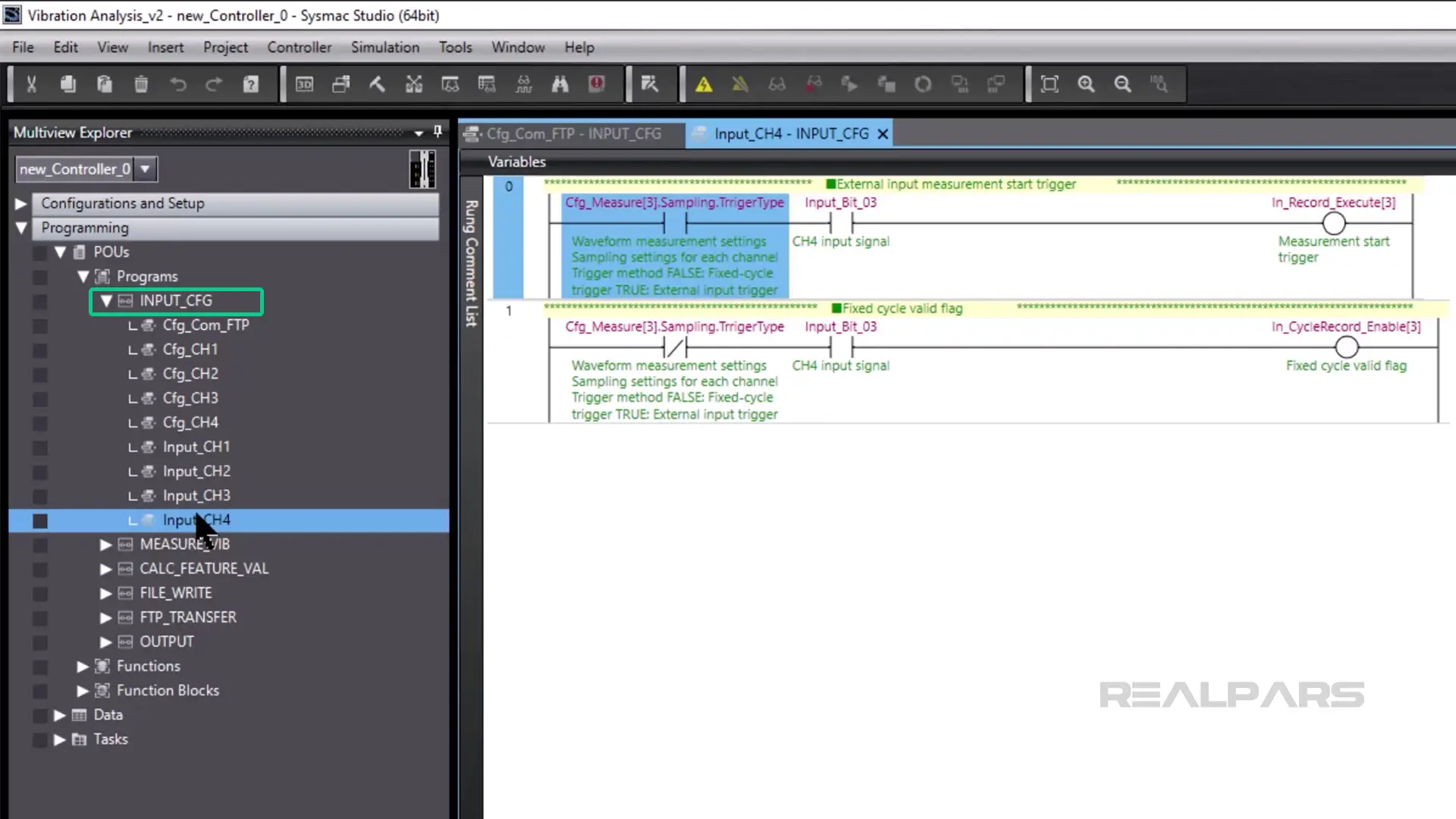
The next program executes the Data acquisition from the NX-HAD analog input units.
In this example, a variable is created to store the 50 samples during every primary task.
Once the data is obtained, a linked array is captured and scaled using the Sysmac Studio Function Blocks.
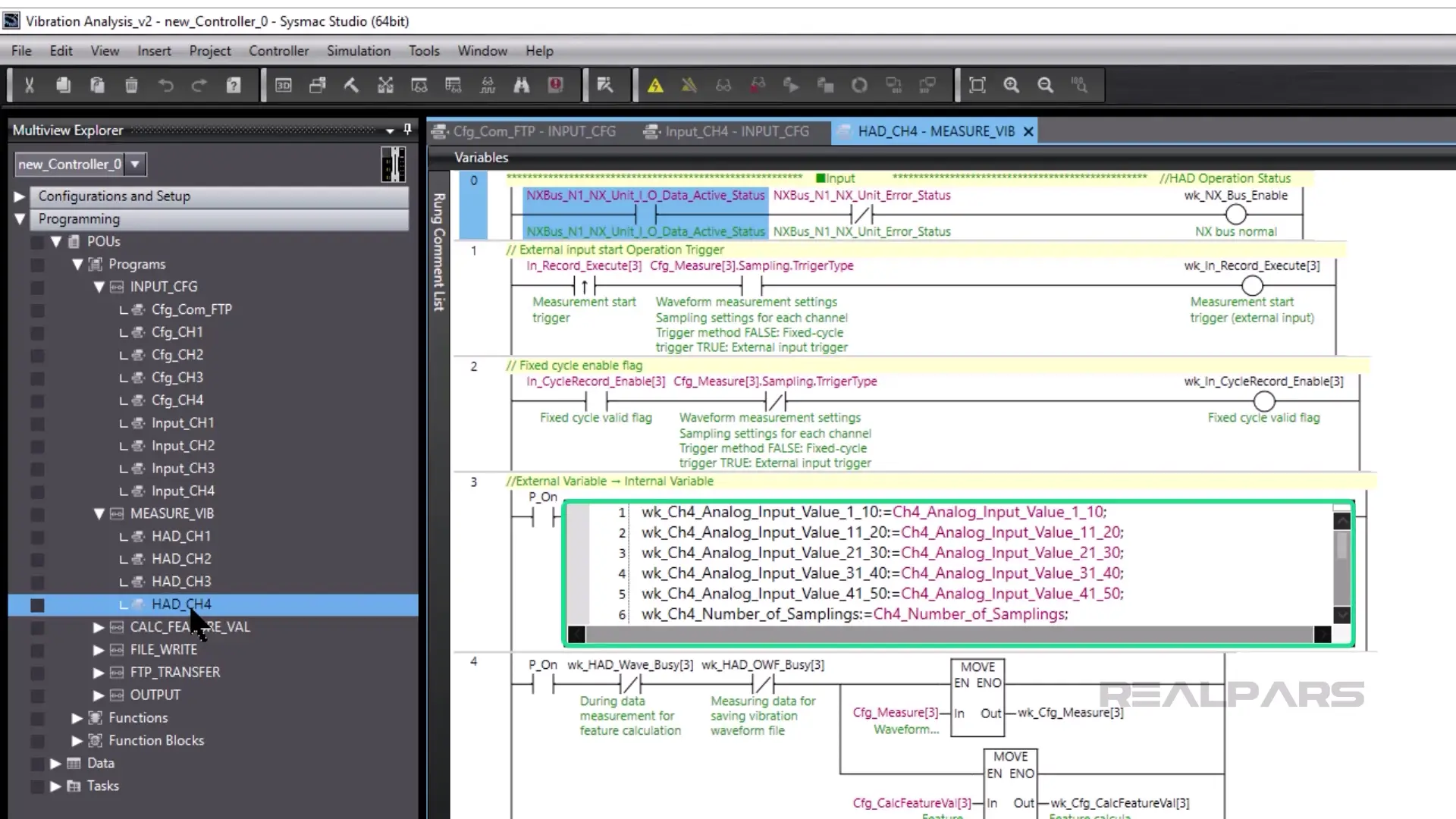
The Data Analysis calculation program is next.
Analysis starts from the oldest stored data as indicated by the FIFO structure.
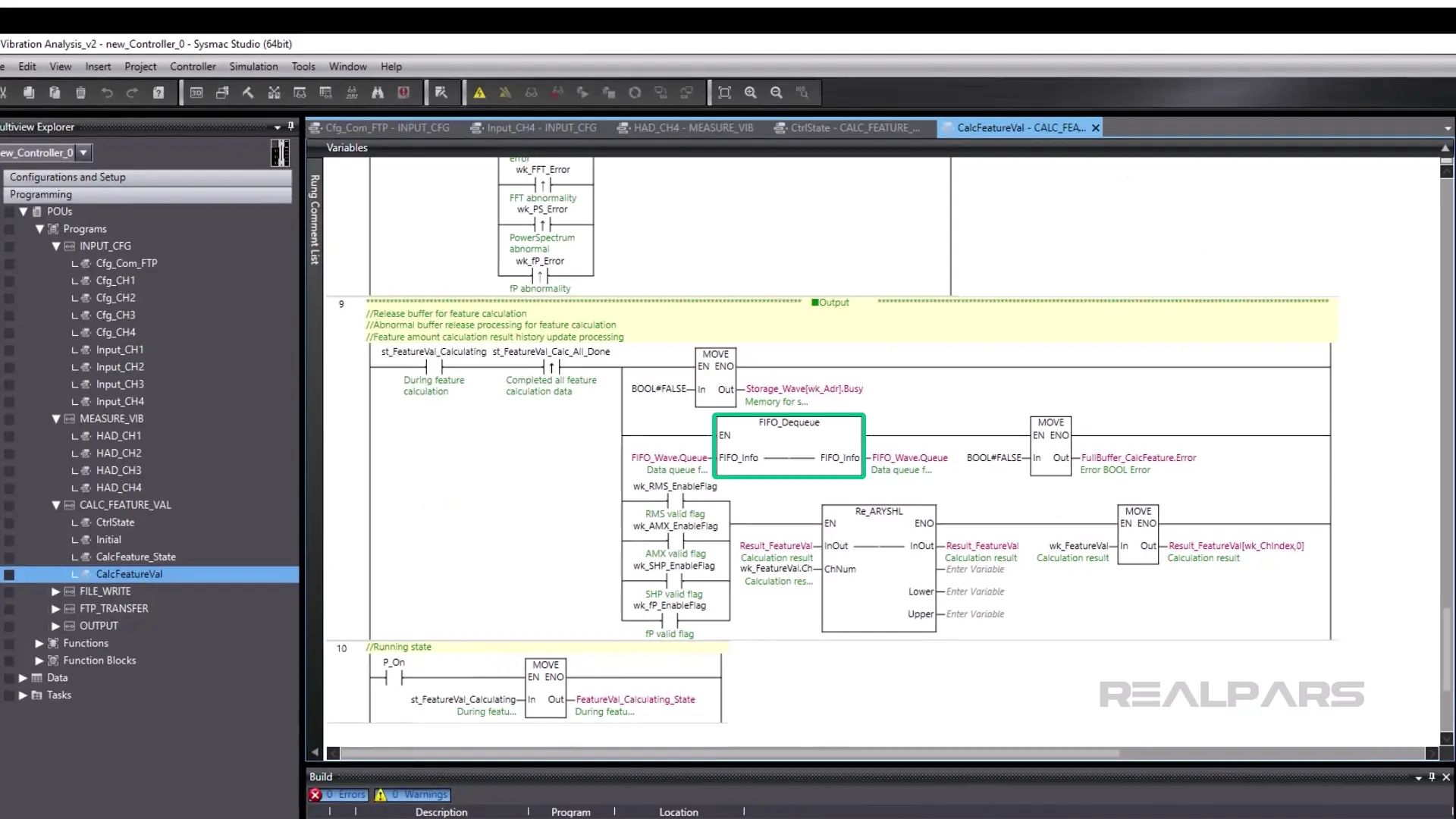
When the calculation on the waveform is finished, the FIFO is updated. The data is stored in an SD card.
The File_Write program transforms the SD card stored data into the Omron Wave format (OWF).
The OWF file format is a special file format readable by Omron’s wave analysis tool.
File writing includes important FB processes such as Generate_FileInfo and FileWriteVar.
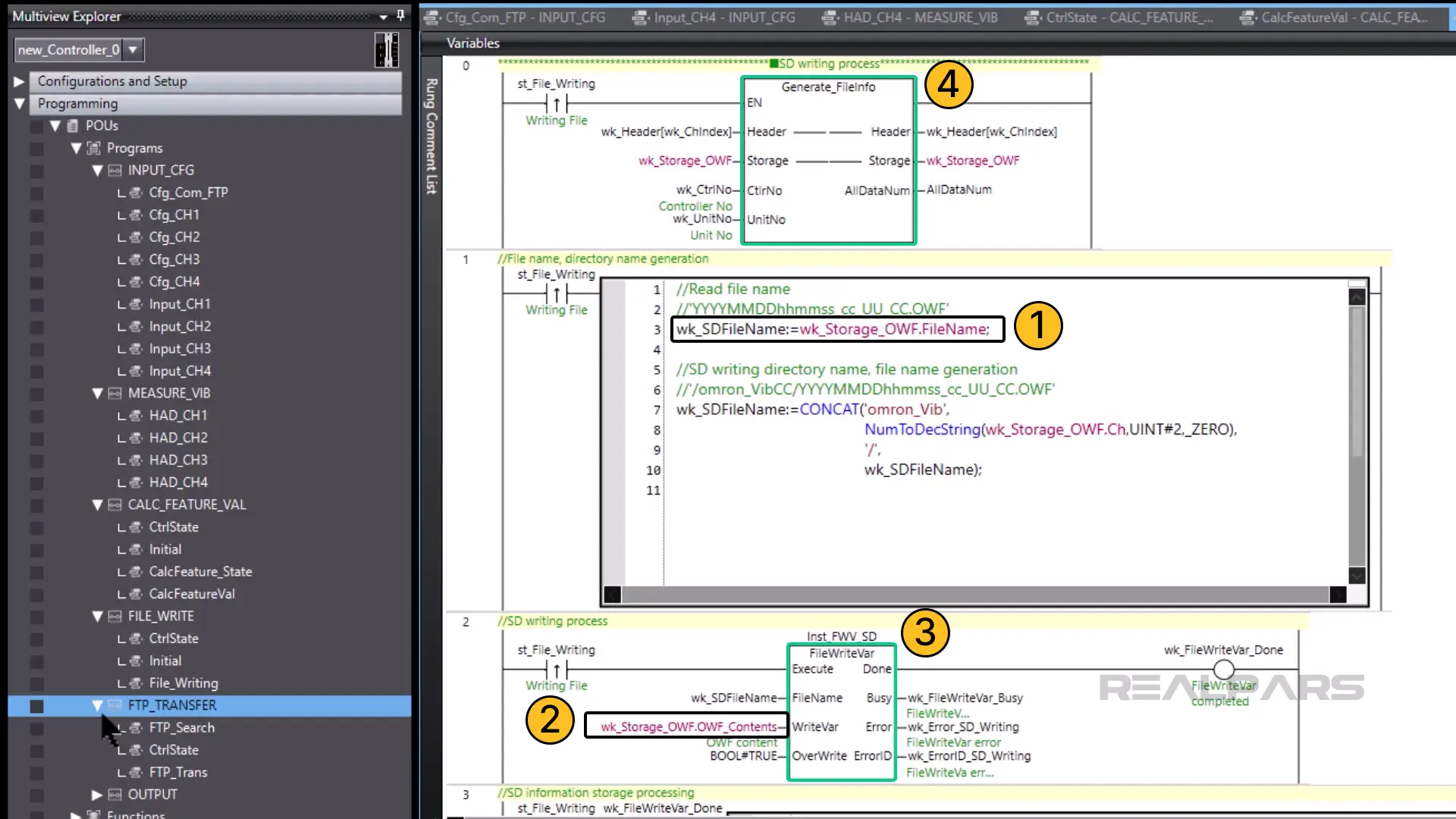
The FTP_Transfer program moves the SD card OWF files via the FTP Server.
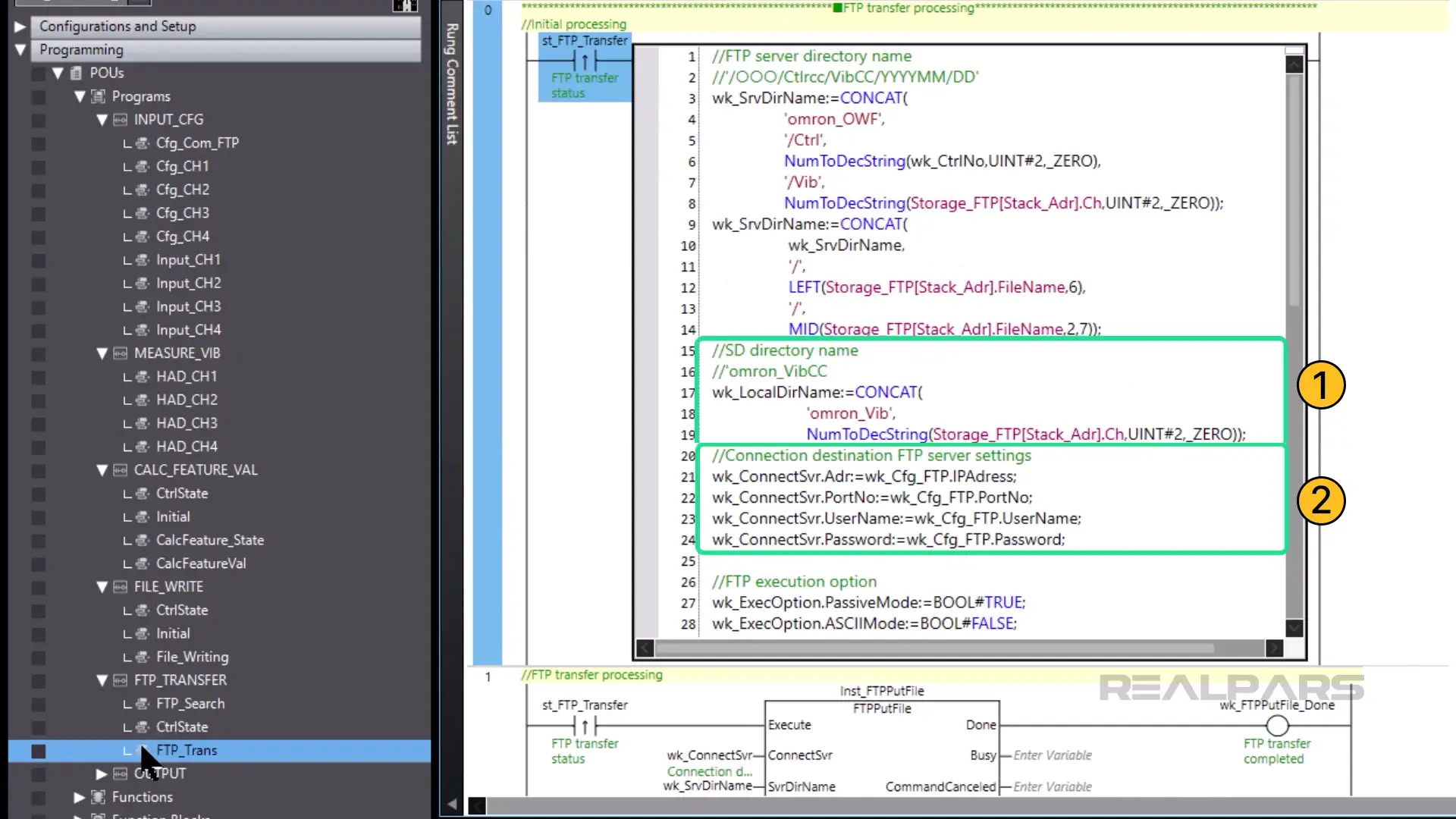
The Output program deals with the Feature values calculated, states, and possible errors.
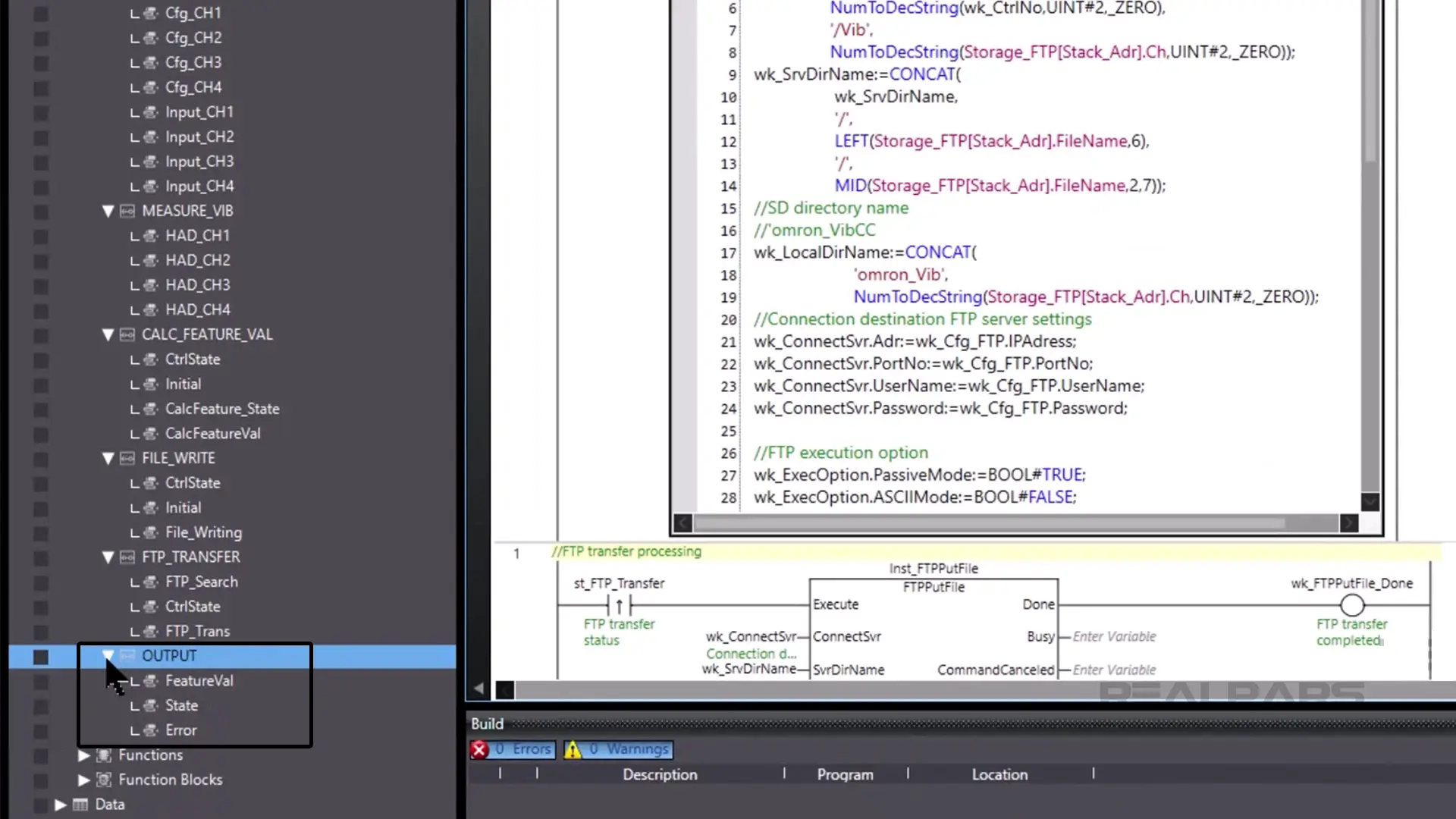
The feature value result is a calculated output saved in a variable called Out_FeatureVal [X, Y] where X is the channel number and Y is the feature value result history number.
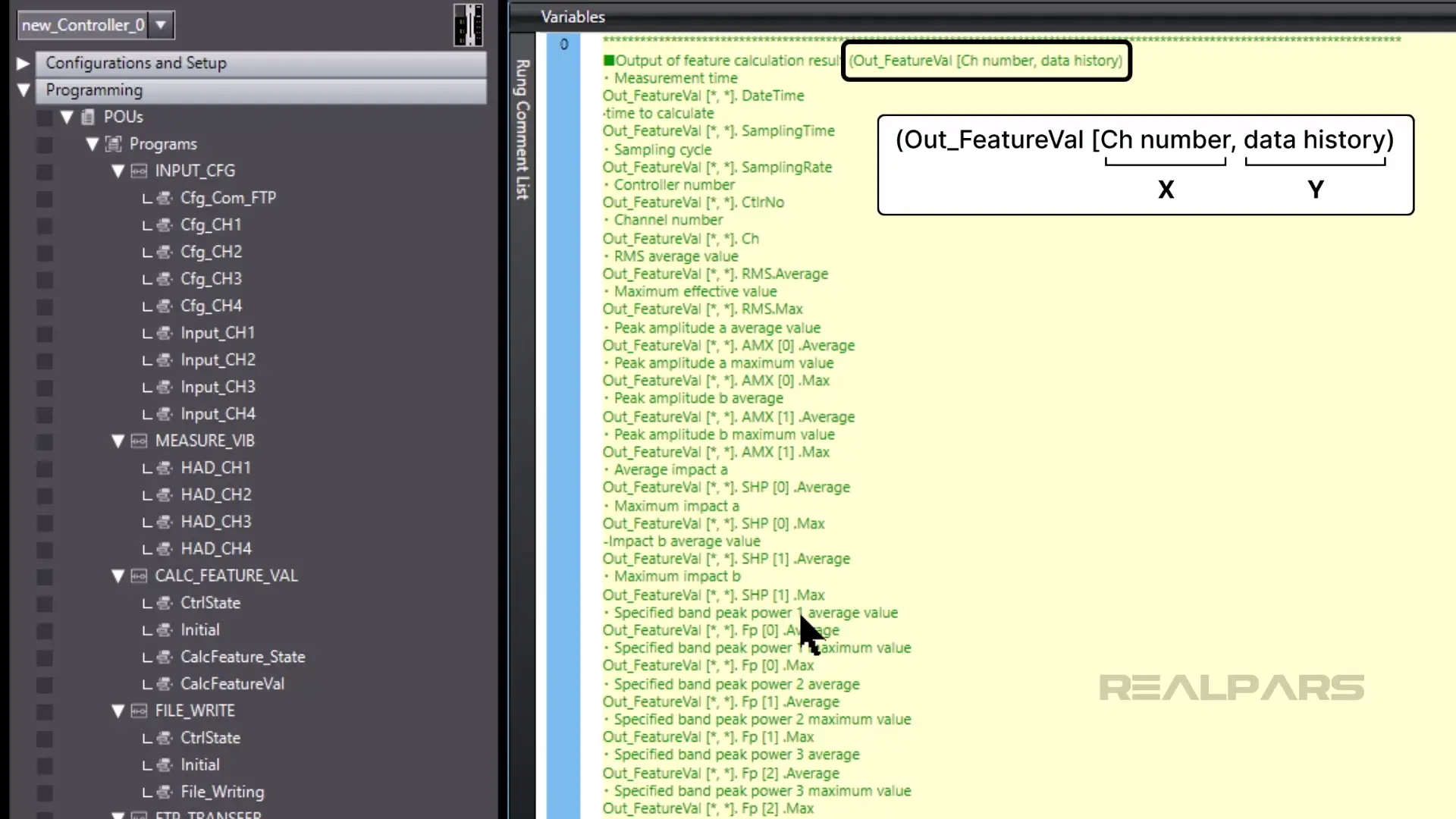
State and Error provide status information and details on any possible errors. The program provides details on where the error is made and sometimes provides an ErrorID.
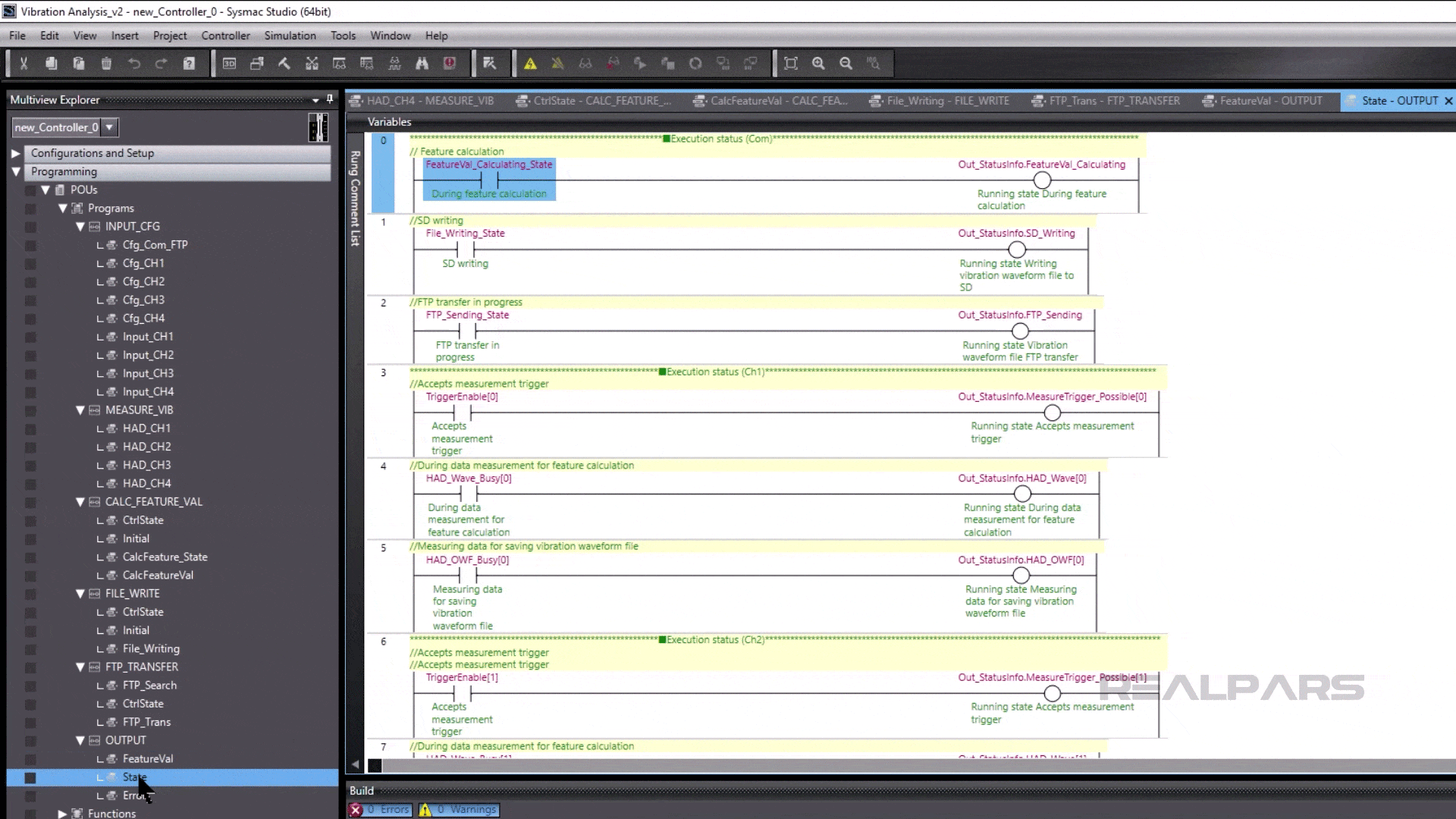
Visualization tool
As we mentioned earlier, Omron has developed an easy-to-use Vibration Analysis Tool that you can install on your PC. This analyzer reads and deciphers the OWF files created during the analysis phase.
We should mention that there are two different vibration tools: the Multiviewer and Viewer. The Viewer can visualize one or compare a few. The multiviewer allows you to visualize several waveforms.
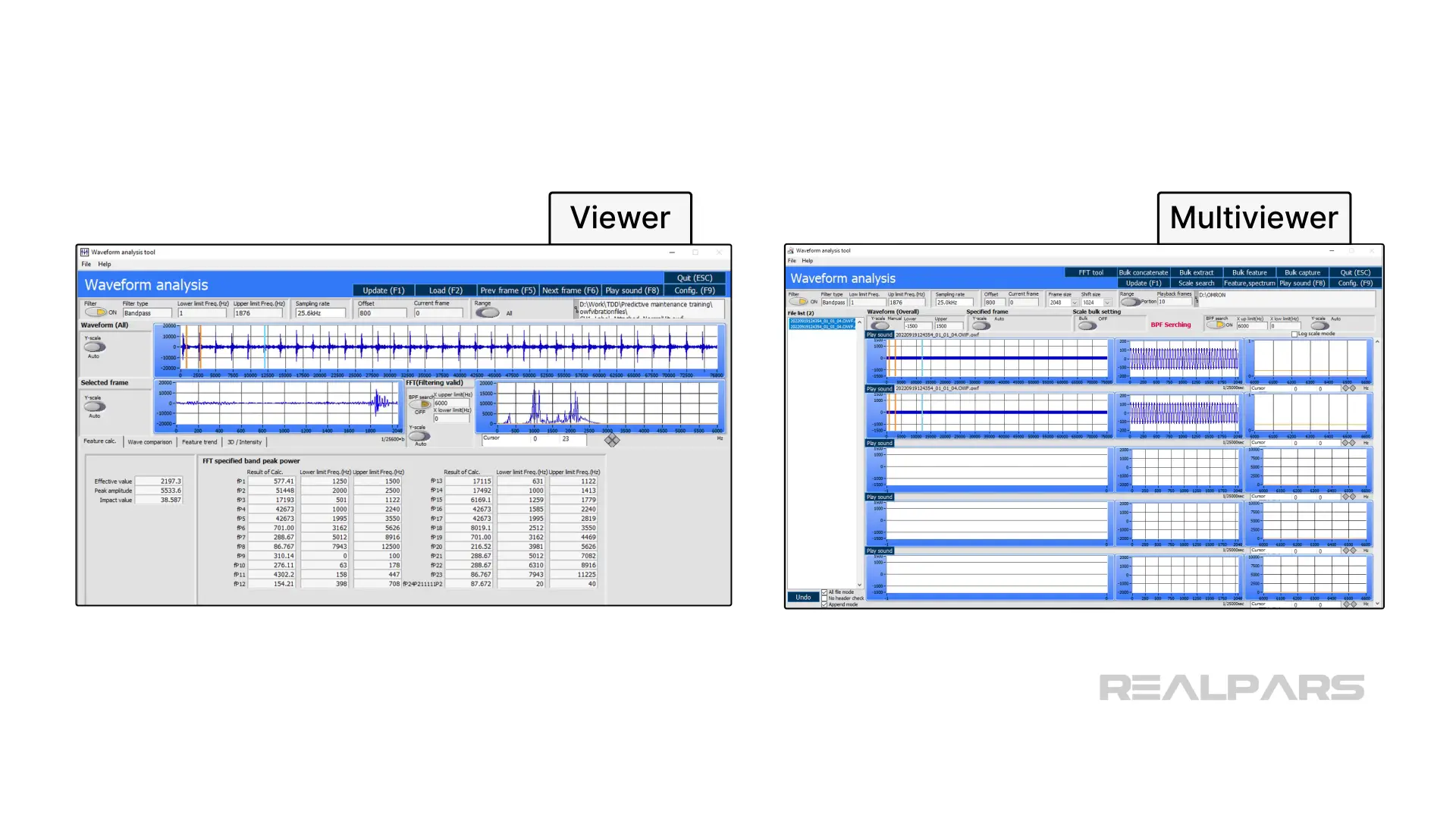
The visualization tool is available free of charge from Omron.
Once the Vibration Analysis Tool is downloaded and installed, it’s a simple matter of running the MultiVibAnalysis Application.
The Waveform analysis tool operates with LabView in the background and offers many analysis options.
Once the Multiviewer tool is open and running, you drag and drop OWF files into the File List where they can be analyzed.

Using a different OWF file let’s see what the analyzer can do.
The Viewer can assist by producing a variety of visuals such as:
- A time series graph of raw vibration waves,
- A Power spectrum calculated by FFT,
- Several wave shapes with multi-window comparison analysis,
- Time-dependent trend of feature values calculated by each frame,
- And Time series FFT intensity in 3D.
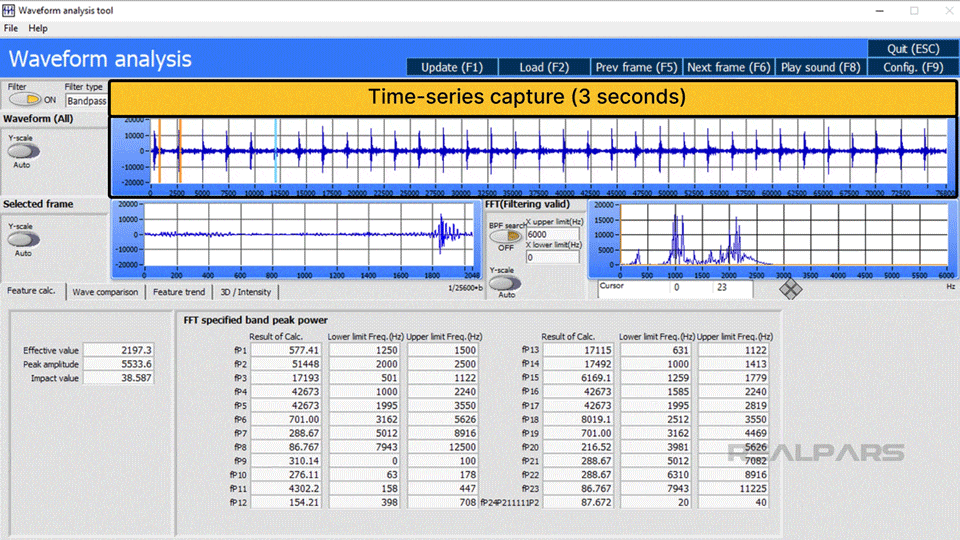
We have an NX controller and an NX-HAD402 4-channel Analog Input unit on the hardware side.
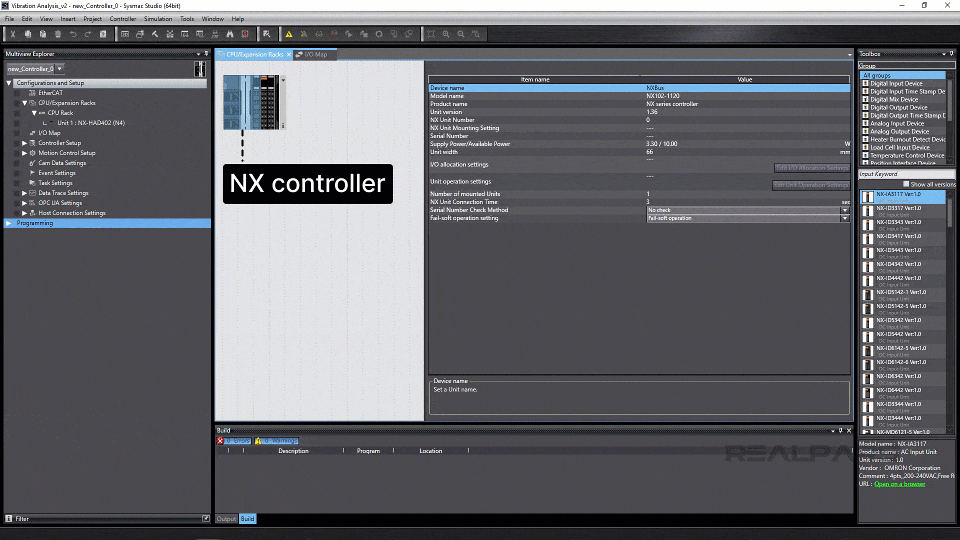
Global variable arrays are configured for each of the 4 channels of the NX-HAD unit.
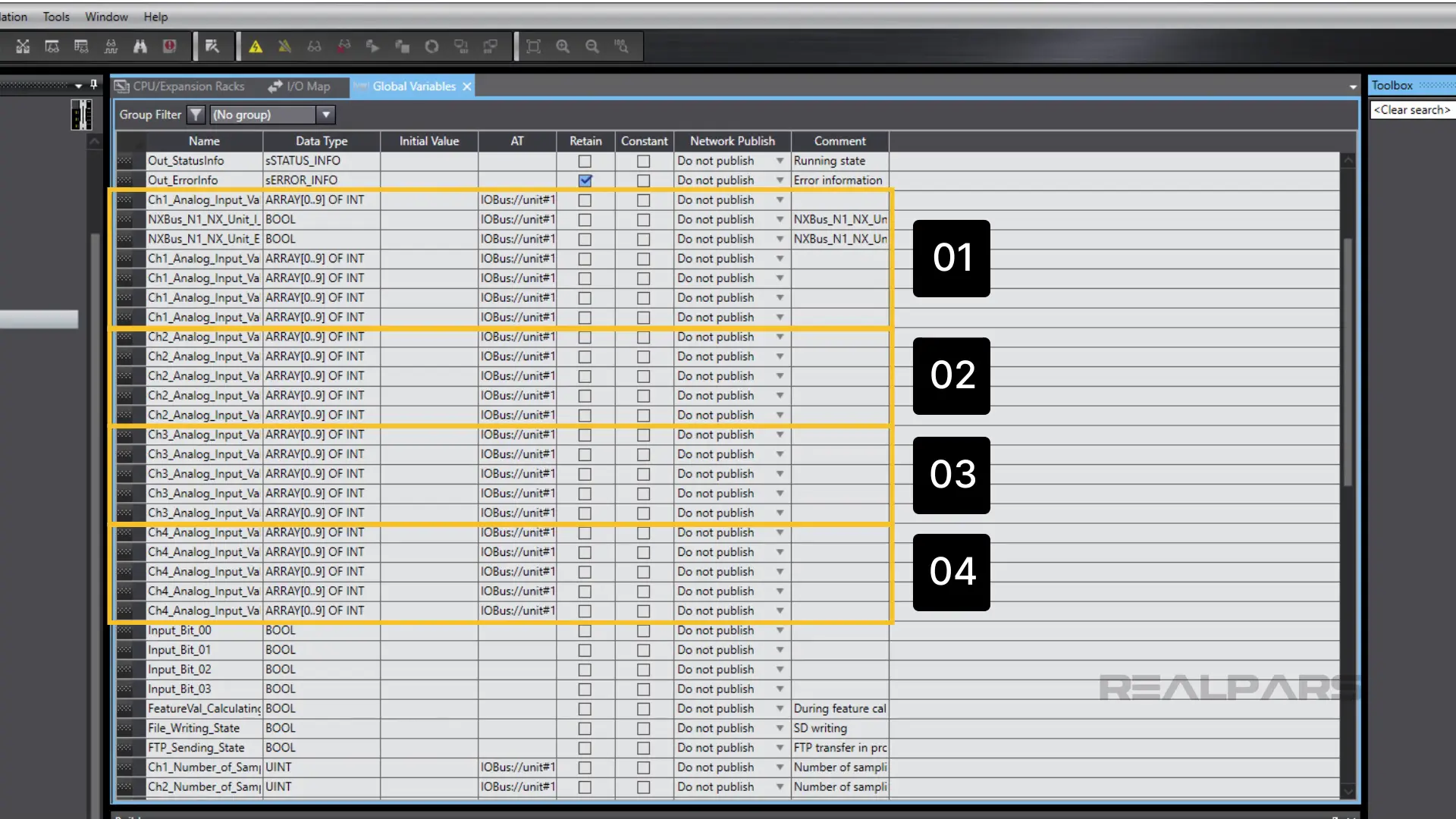
Why use the Omron Vibration Analysis solution?
Why use the Omron Vibration Analysis solution as part of your predictive maintenance?
Here are a few reasons:
- You can use the same NX controller to perform machine control and vibration analysis at the same time.
- The Sysmac Studio Vibration analysis template is free of charge as well as the Visual analysis tool for your PC.
- You can use standard hardware parts such as stock accelerometers and charge amplifiers.
Who is using the Omron Vibration Analysis solution now?
Omron EU currently works mainly with customers in three industries:
- Corrugated packaging (monitoring robots, gearboxes, and rollers)
- Food and Beverage (monitoring bottling machines, conveyor chains, packaging,...)
- Automotive (monitoring robots)
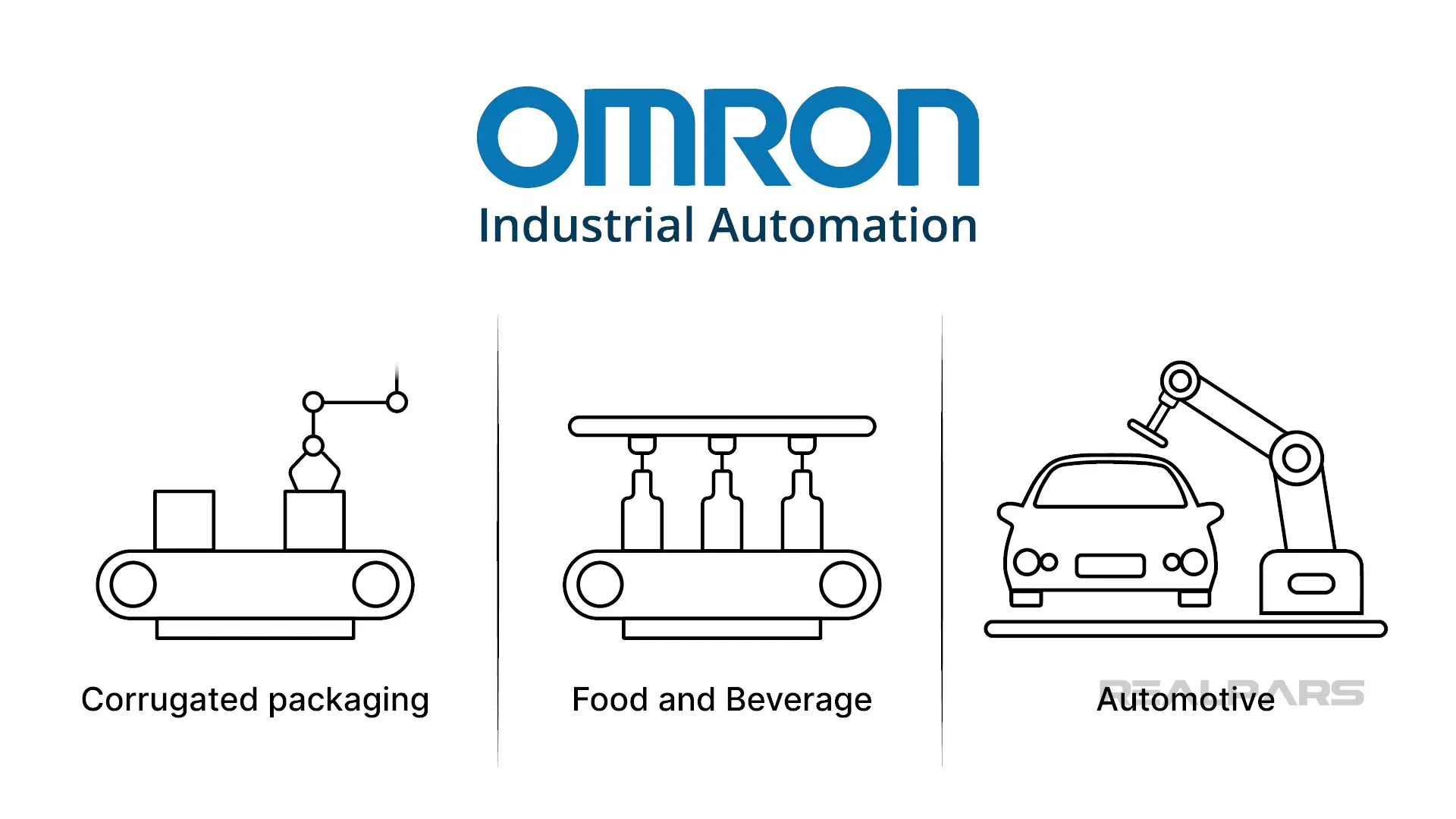
Alright…that’s all we wanted to show you for now.
Summary
Let’s recap a few key points.
- Vibration analysis is an essential part of a predictive maintenance regimen.
- Analyzing equipment vibration detected by sensors is the cornerstone of the Omron Vibration analysis process.
- Omron has also developed a Vibration Analysis template program that runs on Sysmac Studio.
- Omron has developed an easy-to-use Vibration Analysis Tool that you can install on your PC. This free-of-charge tool calculates FFT automatically, provides filter options, and provides a variety of visualizations.
If you want to learn about how to create the program for the controller, refer to the RealPars course Omron PLC Programming Basics - Sysmac Studio.
This course was developed in partnership with Omron. At the end of the course, you will receive a certificate of completion from Omron Automation.
Frequently asked questions
Learn from Industry Experts
With a 7-day trial, then €35/month