OPC-UA Application - Automotive Industry
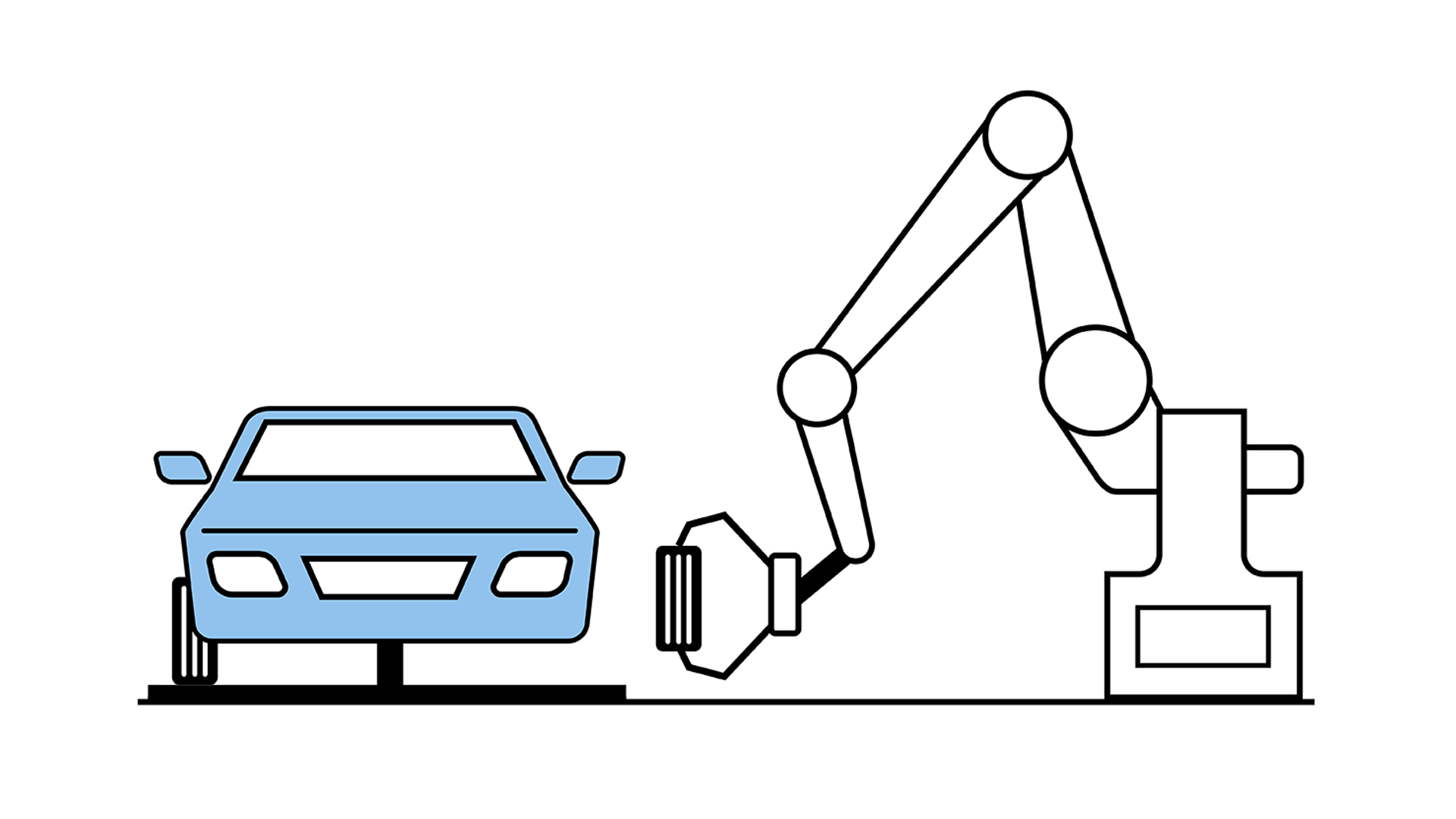
OPC Unified Architecture, or OPC-UA, allows data to be shared in real time between devices, systems, and applications in many different industries. Realpars has produced many articles featuring OPC-UA, and now, I will show how OPC-UA can provide benefits to the automotive industry.
Before I begin this OPC-UA case study, you might be wondering how you get up to speed on OPC-UA and more fully understand its benefits, like high-speed data transfer and communications reliability.
There is an amazing Reallpars course, OPC-UA: Learn the Basics, that offers comprehensive lessons on this topic. I hope you will check it out!
The automotive industry is a vast and vital industry for the world's economy. Automobiles, trucks, and other vehicles move people, goods, and materials from place to place, providing the movement that keeps the economy thriving.
Automobile manufacturing is a complex assembly of multiple work cell operations that form, weld, attach, paint, test, and inspect each of the tens of thousands of parts that are used to assemble a vehicle.
It is imperative to collect and analyze a wealth of data from these many operations.
As with the other industries we have highlighted in this series, there is a need to collect plant floor data quickly and reliably in real time in order to ensure an efficient assembly process.
OPC-UA, built on TCP/IP is perfectly suited to provide these data collection services from each work cell in the plant and to supply these data to central servers and monitoring systems. Because OPC-UA communicates using TCP structured command statements, it can integrate seamlessly into the plant’s manufacturing networks.
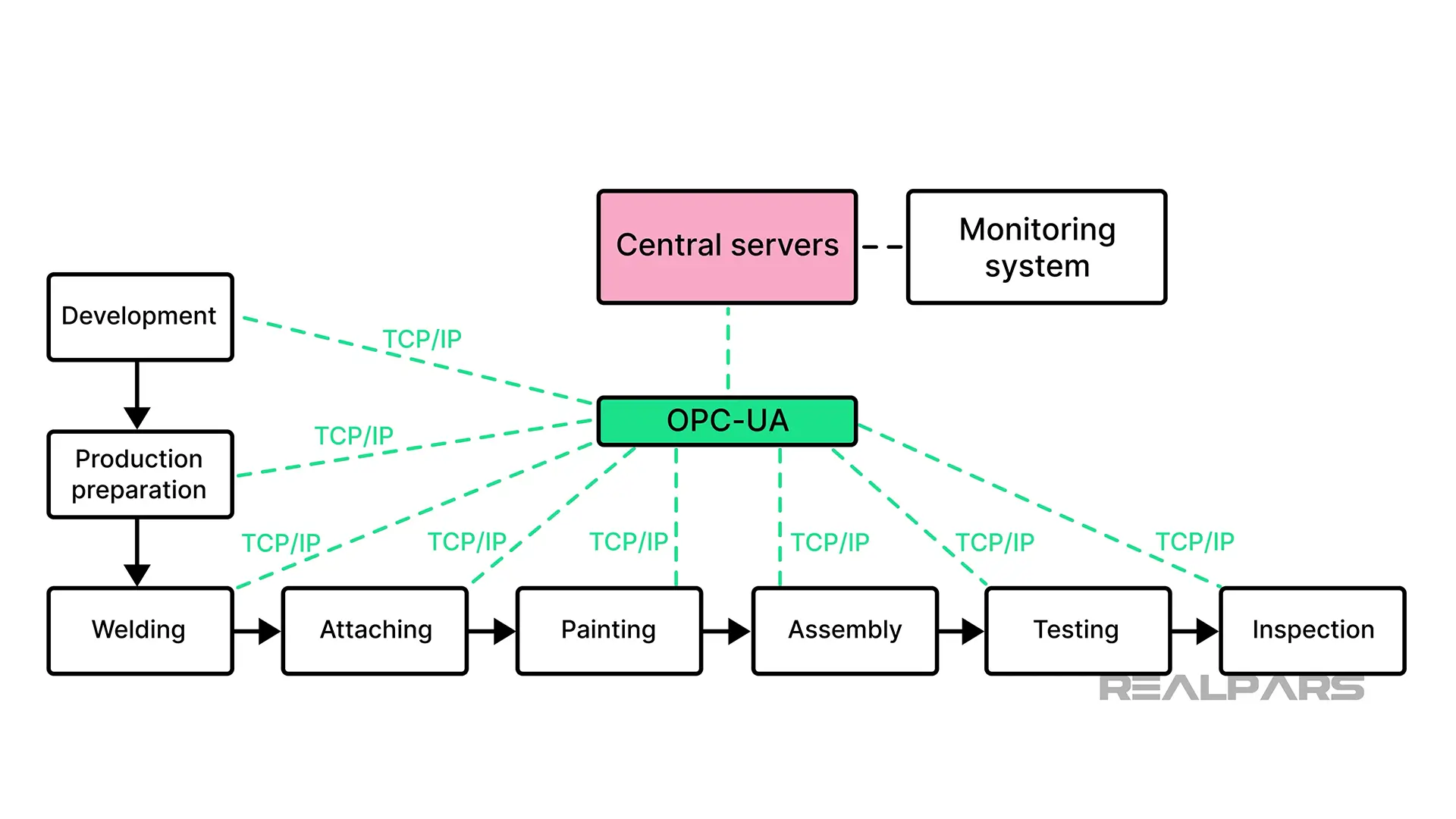
Sensors
The automotive factory floor is a symphony of precision and coordination. This coordination is made possible through the use of various sensors. Leading this effort are position sensors, which stand vigilant, ensuring parts are delivered to each work cell precisely when and where they are needed and ensuring that every car part aligns perfectly, down to the millimeter.
These position sensors use inductive or capacitive technology, detecting the exact position of car parts during the assembly process and ensuring precise alignment and fit.
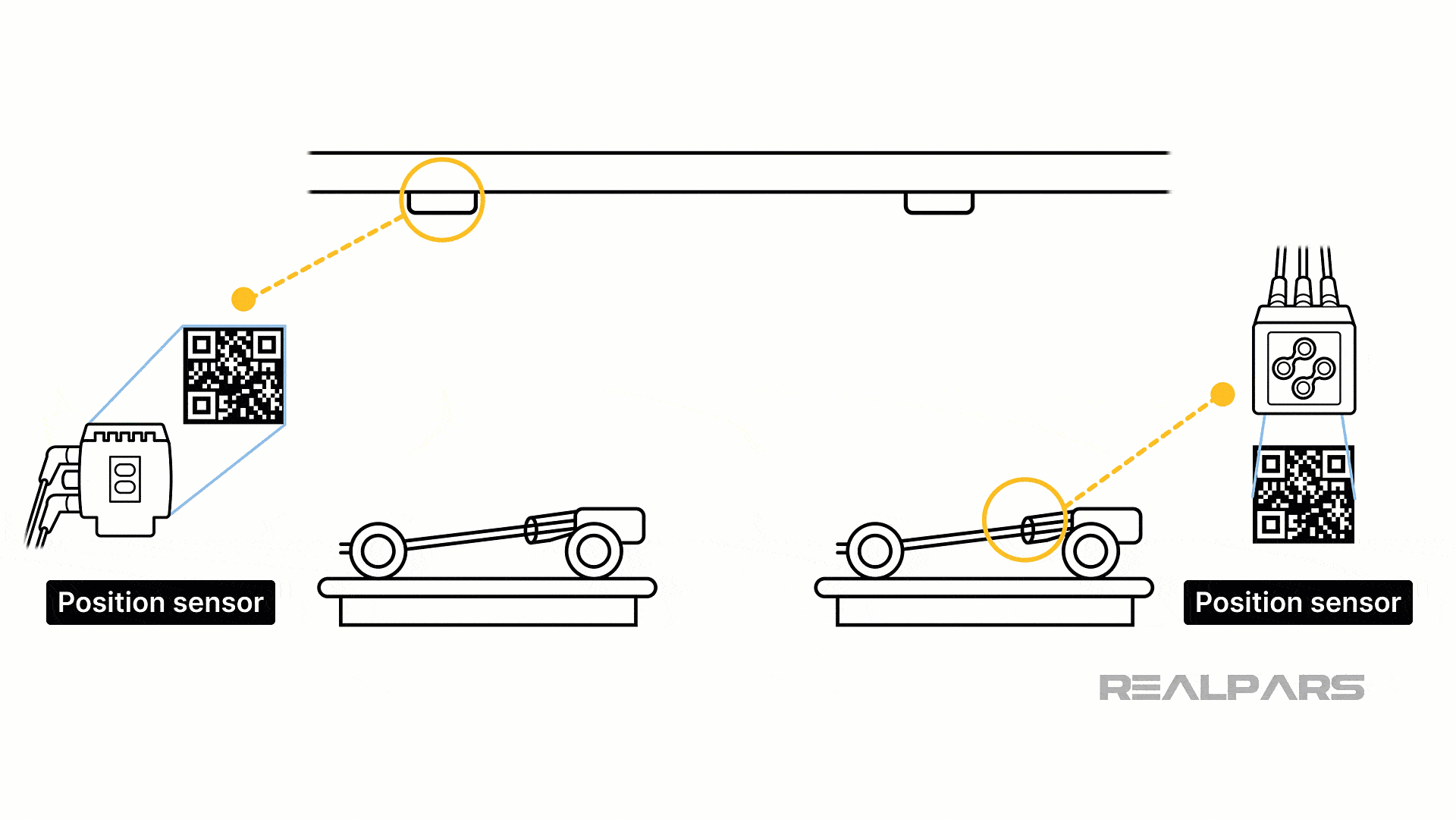
Torque sensors, deployed on robotic arms and tools, help guarantee that the correct force is applied when attaching components, like fasteners and bolts. Too little torque and components might come loose; too much torque, and there is a risk of damage.
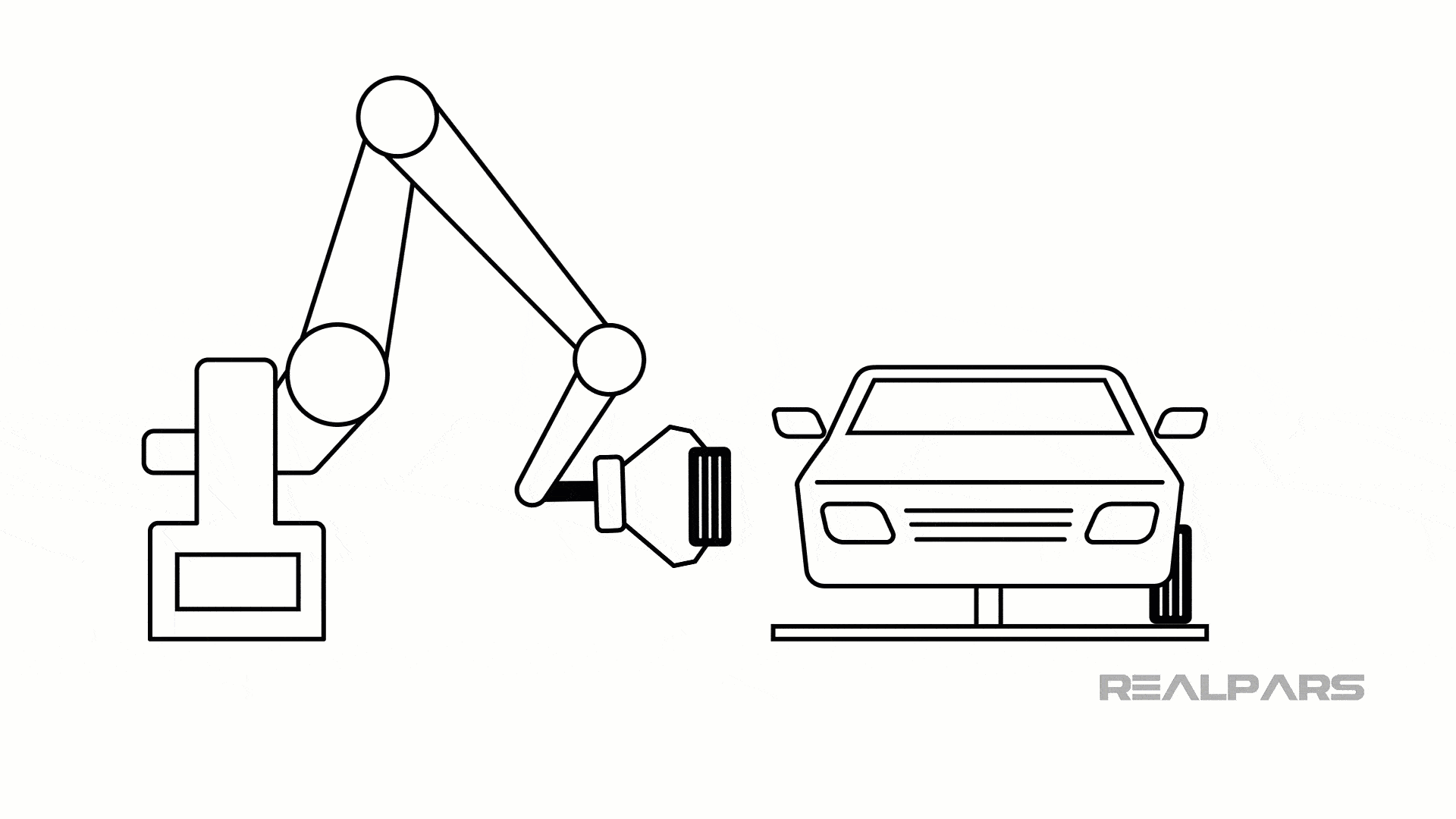
Optical sensors are used for many purposes, including inspection of sub-assemblies to verify proper fit and to monitor the quality of paint and coatings application, checking for uniformity and spotting any imperfections.
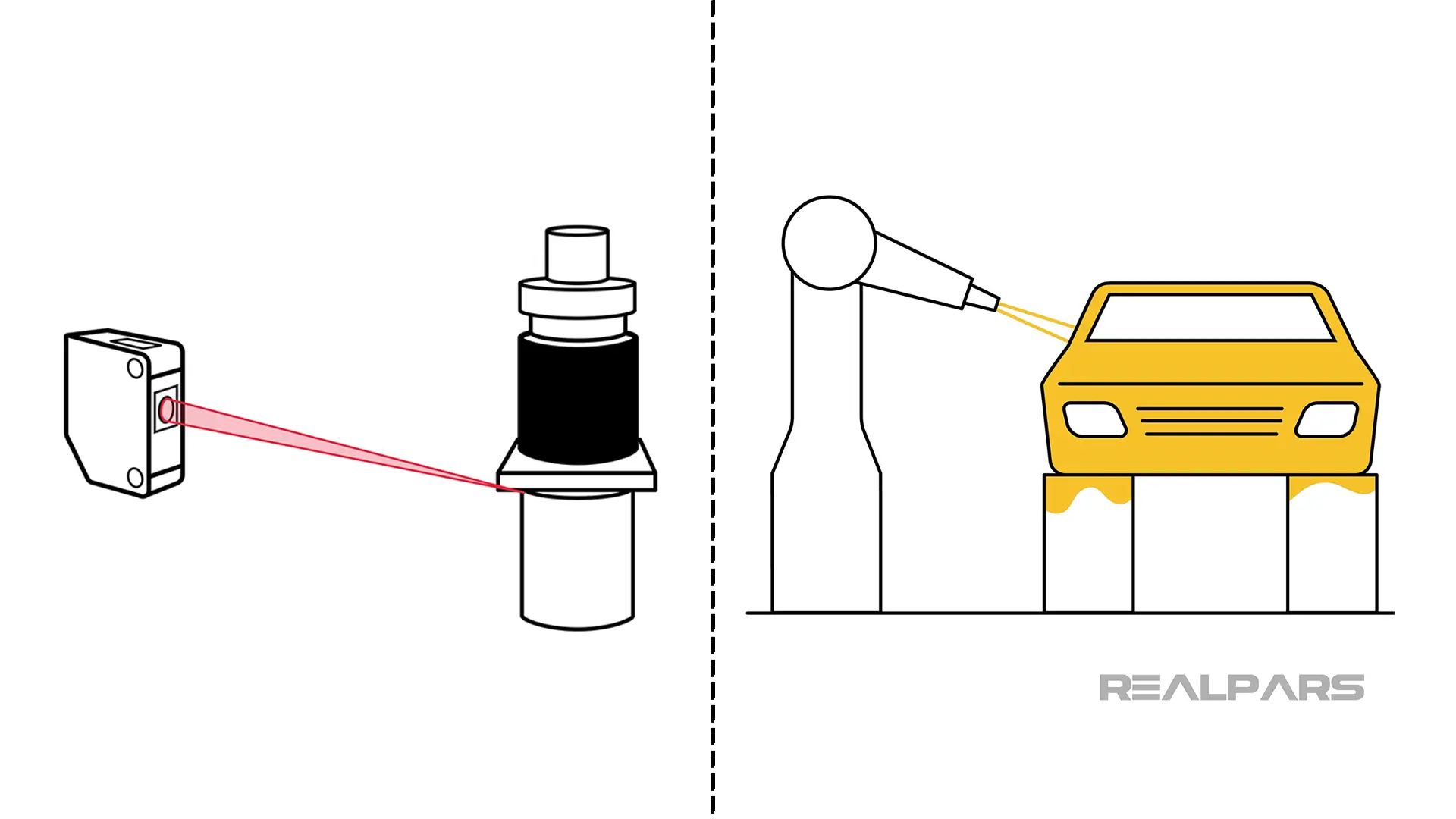
Each car component, especially critical ones like the engine or transmission, carries an RFID 'identity' embedded on a small tag. An RFID tag consists of a tiny radio frequency transponder that is triggered by an electromagnetic interrogation pulse from a nearby RFID scanner.
Scanners read the embedded data from these tags to ensure the right components find their way into the right car model.
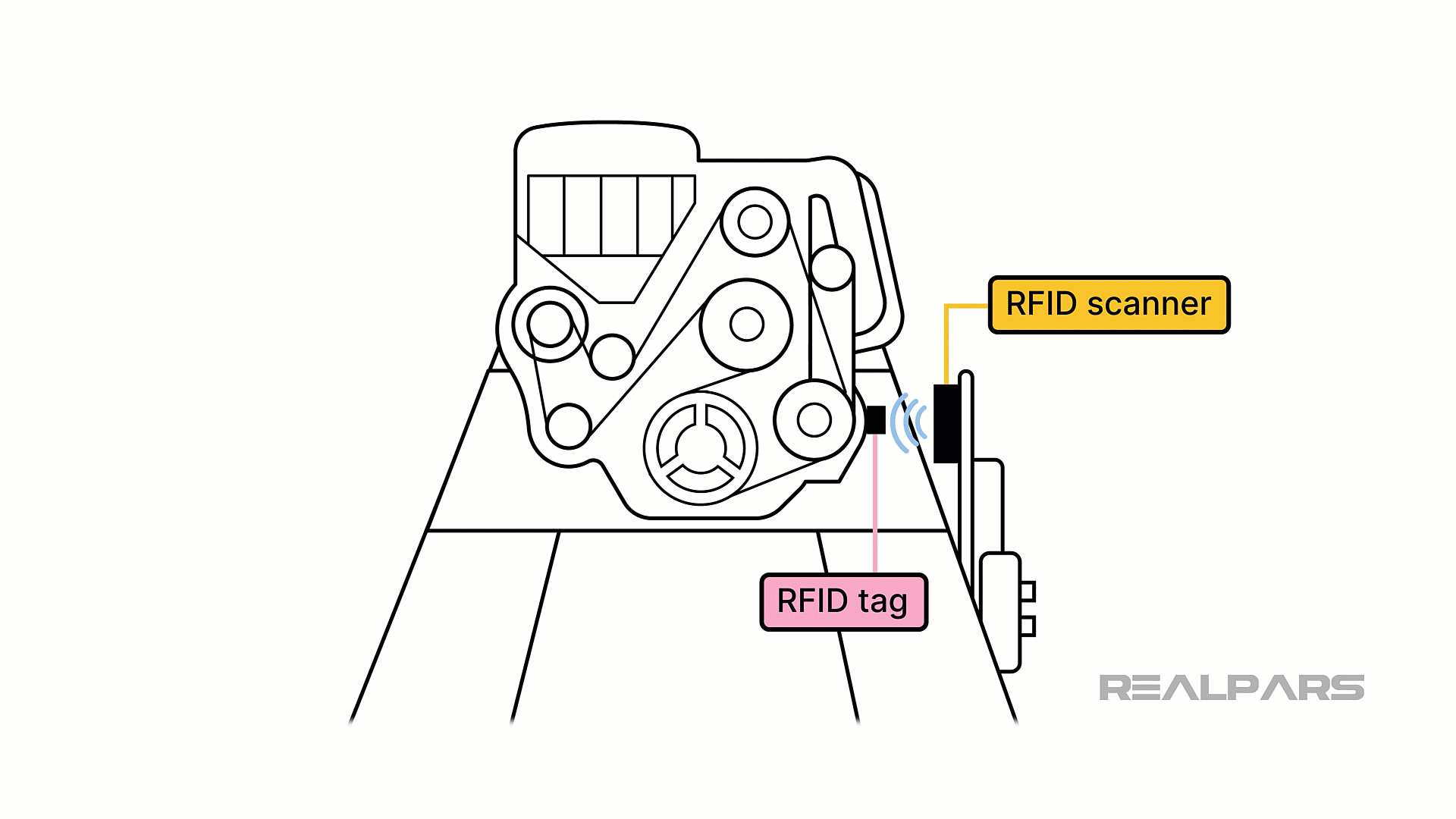
Robots
Automotive plants require the movement and placement of oddly shaped and heavy parts, such as side panels, axles, stiffeners, and roof sections. Each must be placed precisely and welded together.
These movements and welds are -performed by robot arms, providing a safe and efficient way to complete these tasks. Controlled by PLCs (Programmable Logic Controllers), these robot arms can execute these tasks precisely.
Their actions need to be synchronized to prevent collisions and ensure efficient assembly as the vehicles move down the assembly line.
OPC-UA configuration
But what coordinates this intricate dance of sensors, devices, and safety measures? That would be OPC-UA! By consolidating diverse data streams, OPC-UA can give the plant floor a panoramic view of operations. It allows for a nimble operation too! If a different car variant enters the assembly line, OPC-UA ensures the production adapts in real-time.
OPC-UA is a central part of collecting, analyzing, and storing multiple streams of data. Records specific to each vehicle, customer order, and the assembly process are captured and securely stored to provide proper order fulfillment, to assist marketing efforts, to support maintenance reminders, and to support any future recall, if required.
Data obtained from engine tests and onboard computer checks at the end of the assembly line are critical to ensuring the trouble-free performance of each vehicle.
OPC-UA operates in real-time and can adapt to changes in the production line. This is called adaptive production. As an example, if an RFID scanner detects a variant or change, such as unavailability of a required part, the subsequent assembly steps can be adjusted automatically.
Workflow is continuously monitored and production steps can be altered to improve the flow of materials through the work cells.
A very important function OPC-UA can assist with is predictive maintenance. Collection of runtime data, diagnostic codes, number of movements or cycles of operation, and time in service are used to determine when failures in production equipment may occur or need routine maintenance.
Accessing historized data via OPC-UA can help determine optimal maintenance cycles, thereby maximizing uptime and work cell efficiency.
To protect data streams and to ensure data integrity, OPC-UA has the latest cybersecurity features built into directly into the protocol.
As an interconnected factory can be a target for cyber-attacks, OPC-UA incorporates advanced encryption and authentication methods to secure data such as VIN numbers, customer data, and part serial numbers.
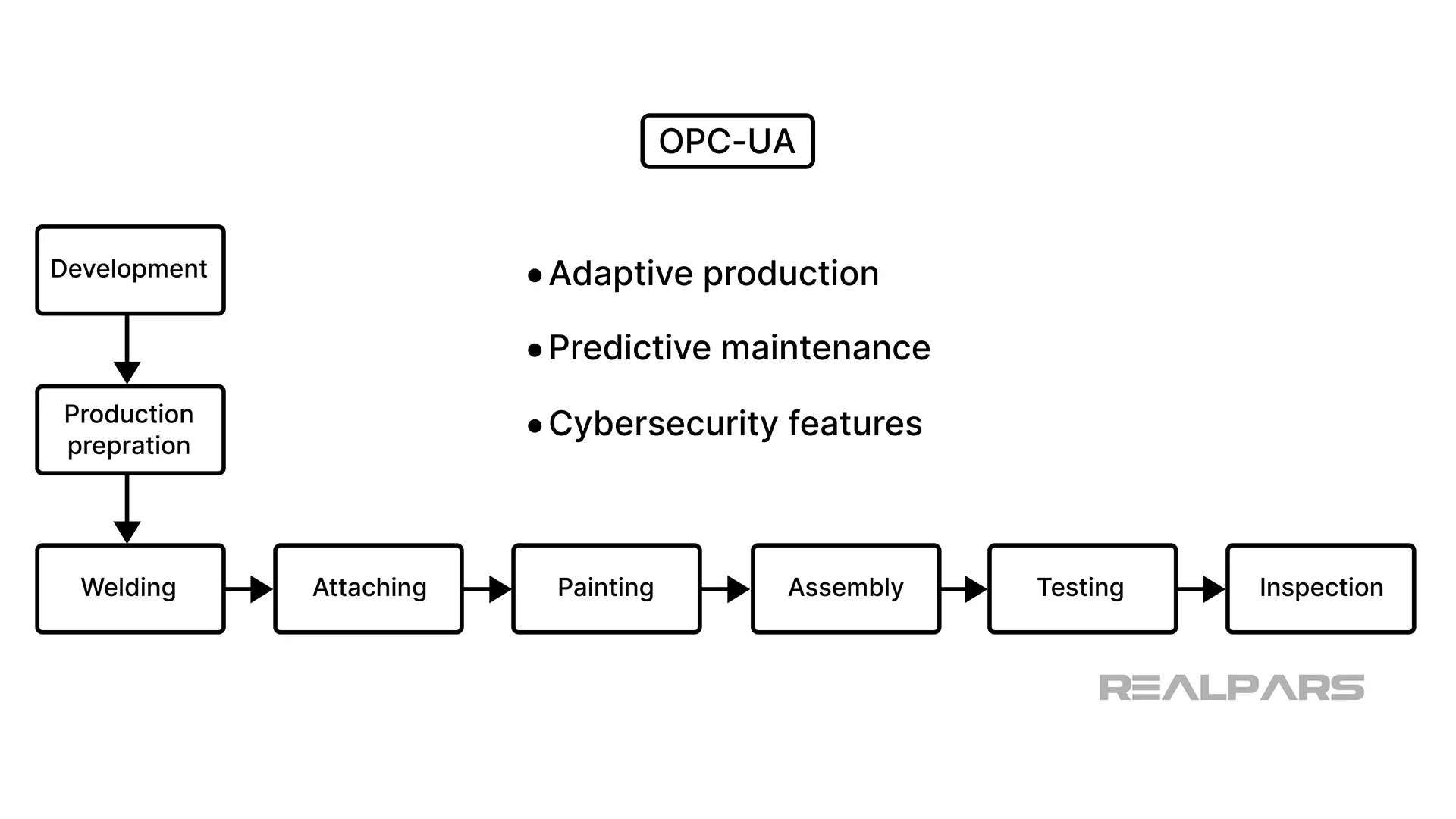
Summary
I trust this detailed perspective on OPC-UA offers a clear picture of the marvels of an interconnected automotive factory and the pivotal role OPC-UA plays in orchestrating seamless operations.
The next time your auto dealer sends a reminder that your transmission fluid needs changing, think about the data that was obtained through an OPC-UA link that helped determine when to send the reminder based on your specific vehicle’s construction.That concludes this case study of the benefits of employing OPC UA in the automotive industry.
If you're eager to dive deeper and truly master more of these OPC-UA concepts, don't forget to check out OPC-UA: Learn the Basics. This course will provide you with a comprehensive understanding, along with practical exercises to solidify your knowledge. You can find the link below. Thank you for your time, and happy learning!
Frequently asked questions
Learn from Industry Experts
With a 7-day trial, then €35/month