In the world of industrial automation, control systems play a crucial role in ensuring processes run smoothly and efficiently. There are two primary types of control systems: discrete control and process control.
Discrete control systems are used to manage specific, distinct events. Think of them as controlling the on-and-off states of machinery.
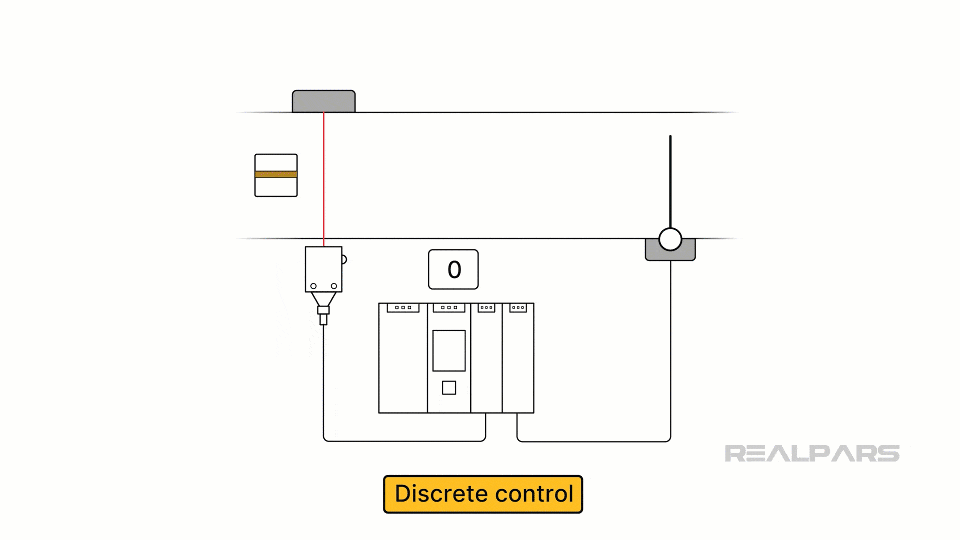
For instance, in manufacturing, a conveyor belt lines up boxes before a solenoid-operated gate, ensuring they are queued properly for the next stage.
or in automotive assembly lines, robots weld car parts in precise sequences, ensuring high efficiency and accuracy.
In discrete control systems, sensors include detectors such as photo eyes and proximity sensors, mechanical actuators such as drives, and mechanical systems such as conveyor belts and robots.
Process control, on the other hand, involves continuous monitoring and regulation of processes to maintain a desired output.
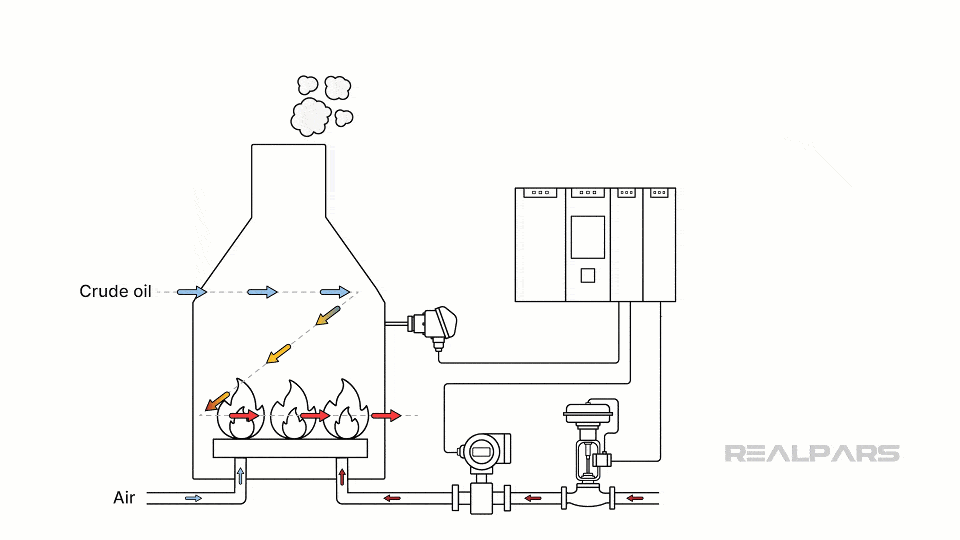
This is vital in industries like oil refining, where maintaining specific flow and temperature ensures product quality, or in food and beverage manufacturing, where consistent mixing and heating processes are crucial.
In process control, sensors that continuously measure pressure, temperature, flow, and level are used. Actuators include control valves and variable frequency drives.
Both types of control systems are foundational in industrial automation, ensuring products are made correctly, safely, and efficiently. Control systems are able to monitor and control 24 hours per day, providing reliability and consistency in the process.
Focus on process control
Process control is all about maintaining stability, consistency, efficiency, and safety in industrial operations.
These are essential qualities in industries such as manufacturing, oil and gas, and pharmaceuticals, where precise control over conditions directly impacts the quality and safety of the final product.
Whereas an operator can only view 4 or 5 parameters at a time, process control systems can monitor hundreds, even thousands of sensors and actuators at the same time, providing input data to determine the required changes to outputs to maintain a consistent operation.
There are four main goals of process control. First, the control system must maintain stability by maintaining consistent process conditions. Second, the control system must maintain consistency in order to ensure uniform product quality.
Third, the control system must be effective and efficient, minimizing waste and optimizing resource use. And finally, the control system must ensure safe operation, protecting workers and the environment from hazardous conditions.
Programmable Logic Controllers (PLCs) are the backbone of process control. They are specialized computers used to automate and monitor industrial processes, providing the precision and reliability needed to achieve the goals of process control.
PLCs come in many different configurations, with varying capabilities and requirements. There are over 25 major manufacturers of PLCs worldwide, each with its own set of features, and each with its own strengths and weaknesses.
So how do I choose the best PLC for process control?
Criteria for evaluating PLCs
First, when choosing a PLC for process control, I need to consider the following criteria.
- Performance
- Ease of programming
- Scalability
- Integration
- Cost
I need to understand the performance of the PLC hardware. I look for PLC models with the speed, reliability, and processing power to efficiently handle the complex tasks I need it to perform.
Every PLC needs to be programmed to execute the process logic I need. The software should be user-friendly, with intuitive interfaces that simplify programming and troubleshooting.
Many programming languages are available, so I look for PLCs that have standard programming languages available, such as ladder diagrams and function blocks.
The PLC chosen should be able to scale or be expanded, from a small system to a larger system as your needs grow. I look for memory capabilities, remote I/O capabilities, and types of input and output cards supported.
The PLC I choose should integrate seamlessly with other systems in the plant, such as HMI stations, and devices to ensure smooth operations. The PLC should support standard Industrial Ethernet communication protocols.

Finally, cost is always a concern. I must not consider only the initial purchase price, but also ongoing maintenance and overall cost of ownership. Higher-cost systems generally have higher reliability, richer programming features, and more options for I/O.
But many times those additional features are not required for my specific application, so a lower-cost system may be better. Many manufacturers provide a range of processors, from low-cost basic PLC models to higher-cost, feature-rich PLC models.
Top PLCs for process control
I will highlight four of the top PLCs for Process Control. These are some of the most popular PLC manufacturers and models in the industry and were chosen to highlight the similarities between these models.
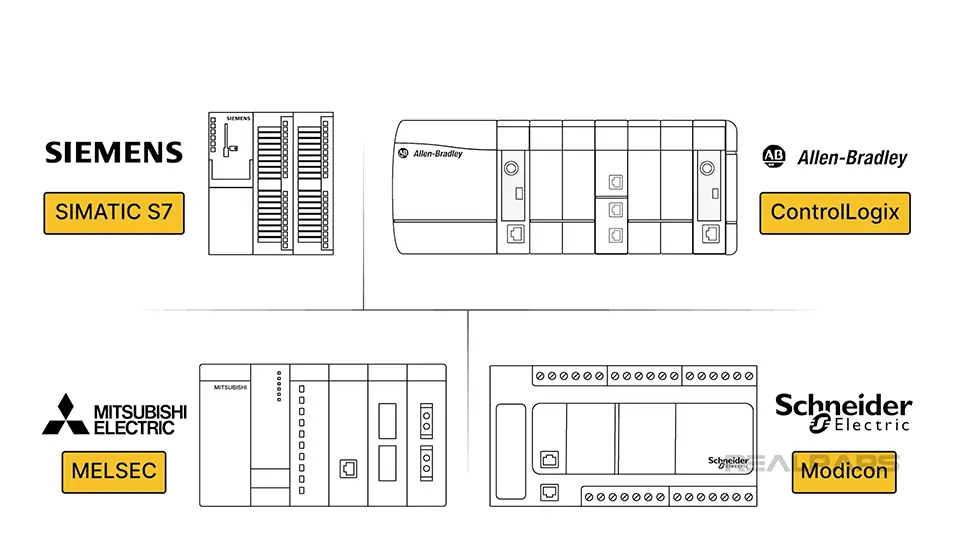
Siemens SIMATIC S7
The Siemens' SIMATIC S7 has been a leading choice in the industry for 30 years, known for its robustness and reliability.
Some of its strengths include excellent performance, a high level of modularity and scalability, and broad compatibility with various systems using standard industrial ethernet communication protocols, including OPC-UA.
On the downside, an S7 system can be costly and moderately complex to set up and program.
Allen-Bradley ControlLogix
Allen-Bradley's ControlLogix is renowned for its user-friendly programming and robust performance.
The ControlLogix is the latest evolution of the first Allen-Bradley PLCs which came to market 50 years ago. ControlLogix is easy to program, reliable in demanding environments, and provides a wide array of I/O interfaces.
ControlLogix, however, generally has a higher processor cost than other systems, and messaging between processors can be challenging.
Mitsubishi MELSEC
Mitsubishi's MELSEC series is a cost-effective PLC option, ideal for small to mid-sized applications.
It is affordable and reliable. Its main limitation is its limited scalability as compared to other high-end competitors. Also, non-Mitsubishi communication protocols can be difficult to integrate.
Schneider Electric Modicon
Modicon by Schneider Electric is known for its versatility and strong integration capabilities. The first Modicon PLCs came on the market over 50 years ago.
Modicon is versatile and scalable and is easily integrated with other systems. Its biggest weakness is its moderate performance capabilities as compared to other top-tier PLCs.
As you can see, no PLC is perfect against all the evaluation criteria I discussed earlier, and it really comes down to which system can provide the features and functionality you need at a price you can afford.
Real-world examples
Now I will briefly discuss three real-world case studies using PLCs from some of the manufacturers I introduced you to.
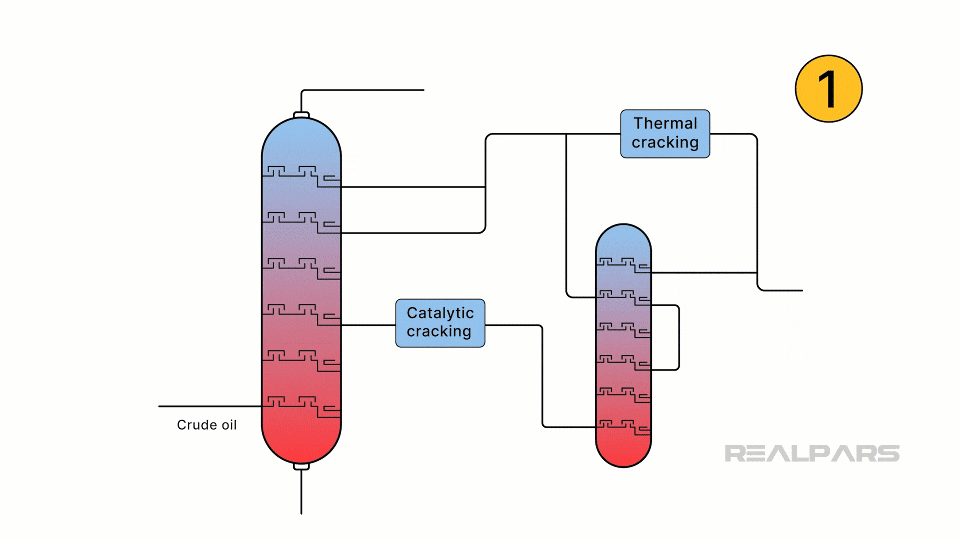
Case study 1
A large oil refinery uses multiple Siemens SIMATIC S7 processors and dozens of remote I/O panels to maintain precise control over its refining processes, ensuring product quality and safety for the 10,000 I/O points in the plant.
The SIMATIC S7 PLCs are able to monitor and control various stages of the refining process, from distillation to cracking, ensuring that each step operates within the set parameters.
This level of control not only enhances product consistency but also minimizes the risk of accidents by maintaining safe operating conditions.
Case study 2
A manufacturing plant utilizes an Allen-Bradley ControlLogix for seamless automation of assembly lines, resulting in increased efficiency and reduced downtime.
The plant has integrated ControlLogix PLCs with robotic arms and conveyor systems using its feature-rich motion control capabilities, enabling synchronized operations that significantly boost production rates.
Additionally, the intuitive programming interface of ControlLogix allows for quick adjustments and troubleshooting, minimizing operational disruptions.
Case study 3
A mid-sized food processing facility uses a Mitsubishi MELSEC processor for reliable and cost-effective process control, ensuring consistent product quality.
The MELSEC PLCs manage various processes such as mixing, baking, and packaging, with real-time monitoring of its 1500 I/O points to maintain optimal conditions.
The plant uses multiple compact MELSEC F-series controllers for the individual process areas, coordinated by a larger, feature-rich Q-series controller.
This system has enabled the facility to reduce waste and energy consumption, leading to lower operational costs while meeting stringent food safety standards.
Conclusion
In summary, both discrete and process control systems are essential for industrial automation.
When choosing a PLC, consider factors like performance, ease of programming, scalability, Integration, and cost. Siemens SIMATIC S7, Allen-Bradley ControlLogix, Mitsubishi MELSEC, and Schneider Electric Modicon are all excellent choices, each with their strengths and weaknesses.
For budget-friendly solutions, Mitsubishi MELSEC is a solid option. For high-performance needs, Siemens SIMATIC S7 and Allen-Bradley ControlLogix are top contenders. Remember, the best choice depends on your specific requirements.
To learn more about various PLCs and get started with programming them for different control systems, explore our PLC programming skill path.