What is intrinsically safe? In this article, we will explain what it means to be intrinsically safe. We will explain why being intrinsically safe is important to an automation professional.
We will also explain where intrinsic safety should be considered. Then we will provide a few examples of how to design intrinsically safe circuits.
Intrinsic safety
Intrinsic safety has to do with preventing fires that could occur because of sparks or heat sources.
Being intrinsically safe in an electrical sense means restricting the current flow or preventing sparks in a hazardous environment.
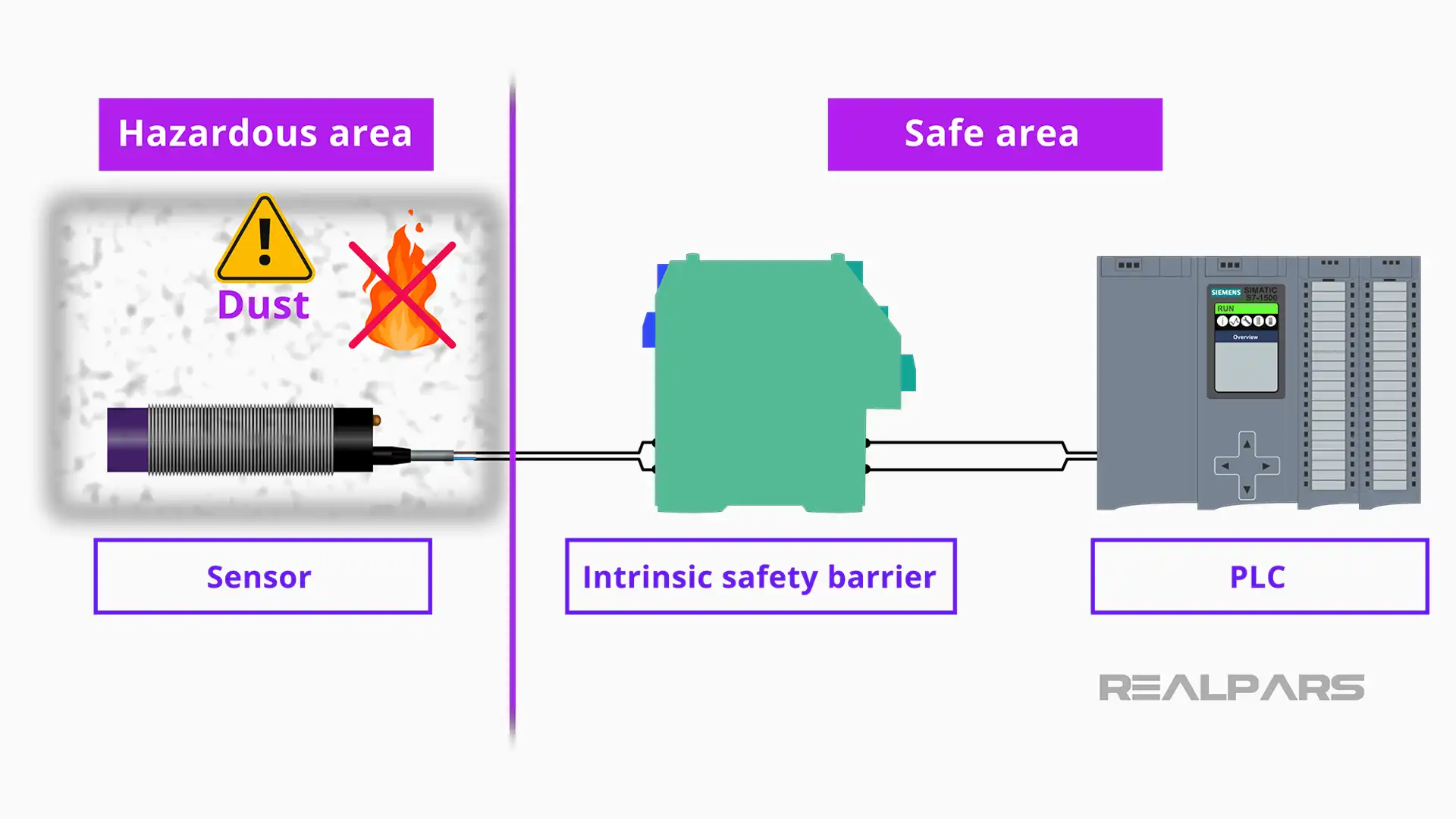
Why do we care about intrinsic safety? We care because an intrinsically unsafe environment could cause a fire or even an explosion by something as simple as a wire being cut.
Risk assessment
We need to be aware of the environment we are working in, especially when working in potentially hazardous environments.
If you are working in or around hazardous environments, it is imperative that a risk assessment is done to help identify the risks. Knowing the risks in any environment will help you mitigate those risks and keep you and others safe.
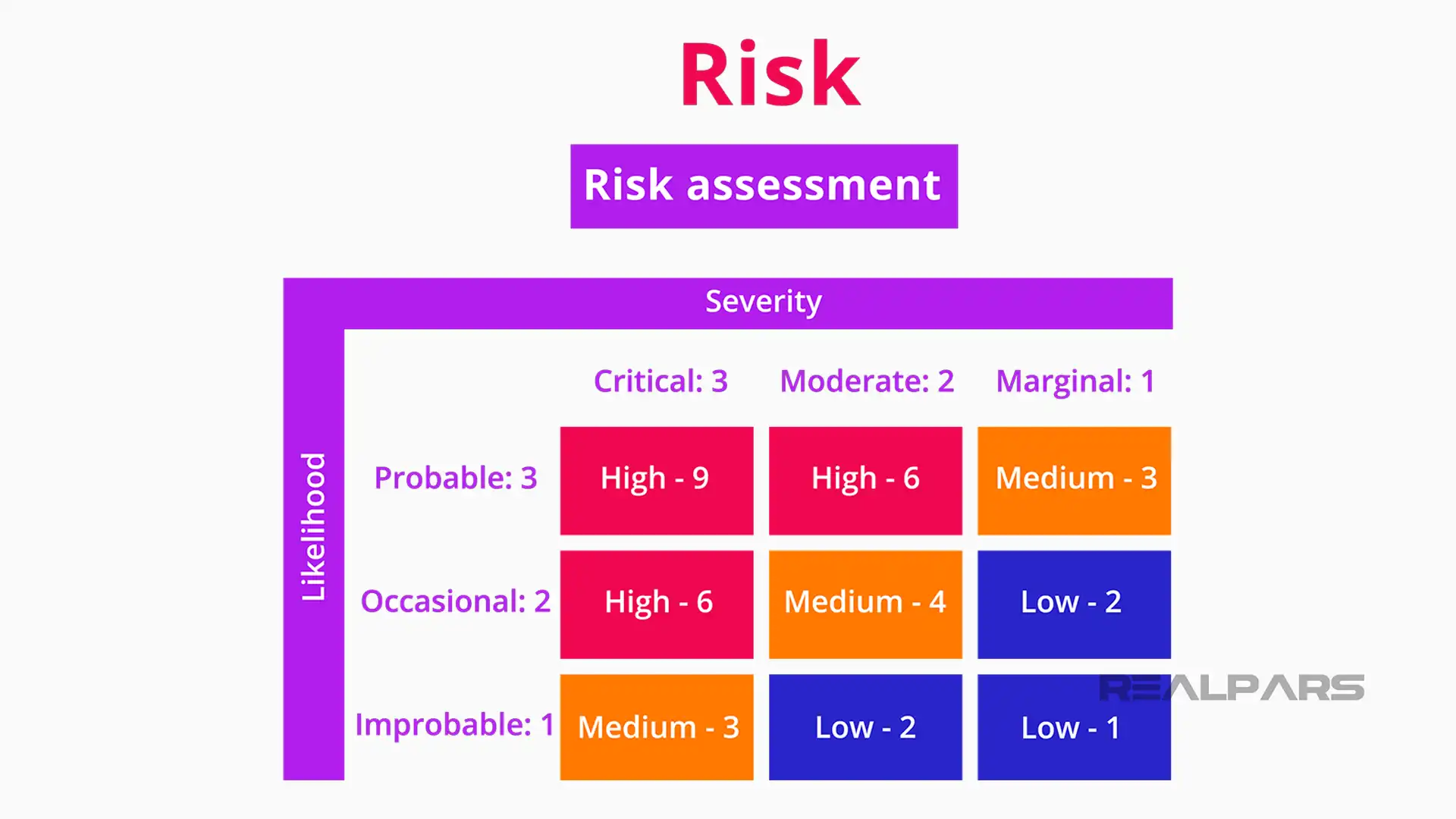
We will now explain some environments in which intrinsic safety measures are important.
There are two main types of classifications:
– ATEX,
– NEC (NFPA70).
For this article, we will focus on the UL (Underwriters’ Laboratories) standard for intrinsic safety.
Intrinsically safe levels
There are three main types of NEC 70 intrinsically safe levels: Class I, Class II, and Class III.
Class I: The Class I environment has to do with flammable gasses and vapors. These vapors could be gasoline, hydrogen, natural gas propane, ethanol, or methane. These gasses exist under normal operating conditions and abnormal operating conditions.
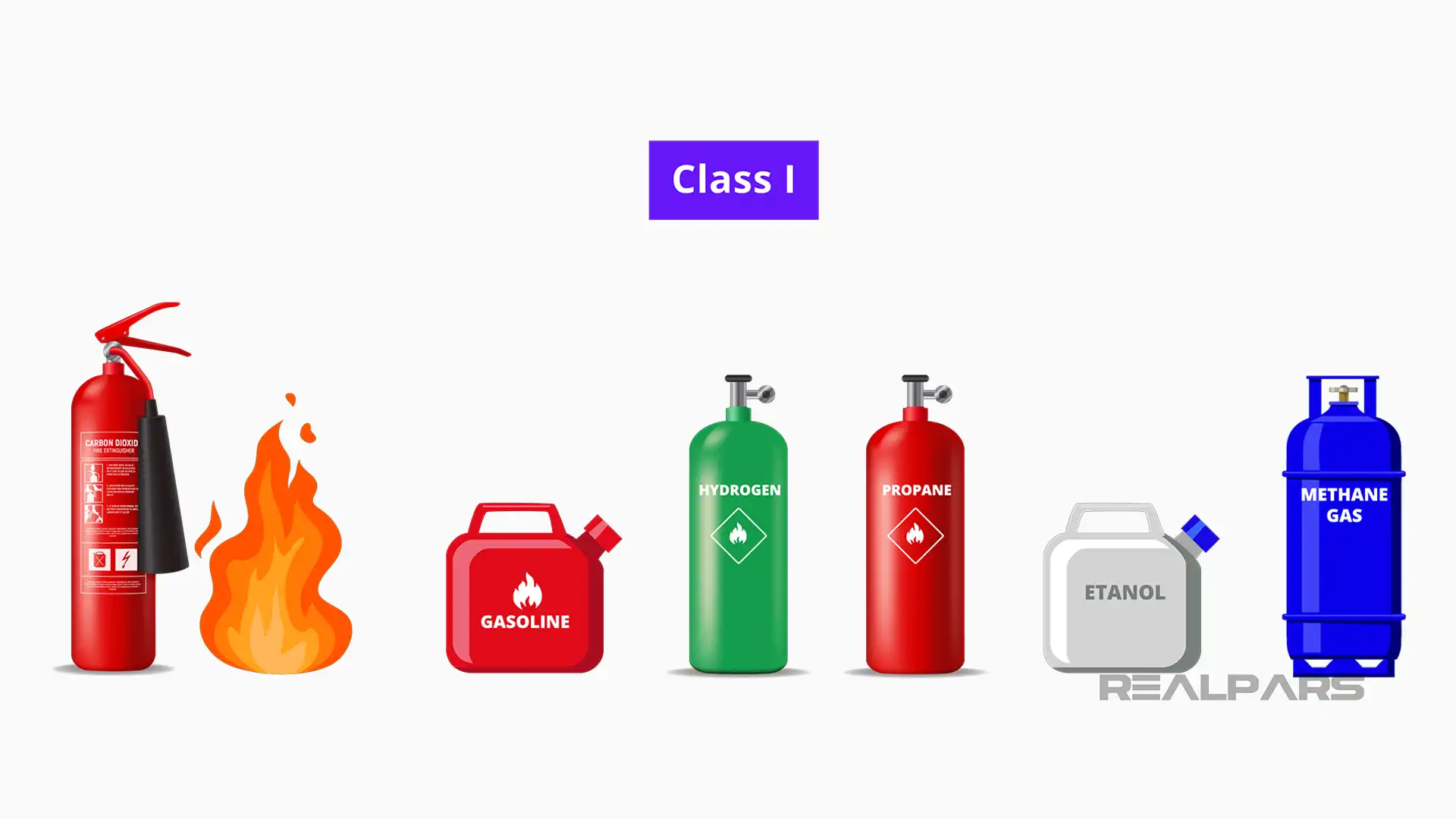
Class II: The Class II environment has to do with combustible dusts. Some possible dusts include metal and metal alloys, charcoal, carbon black, flour, plastics, grains, and wood. These dusts exist under normal operating conditions and abnormal operating conditions.
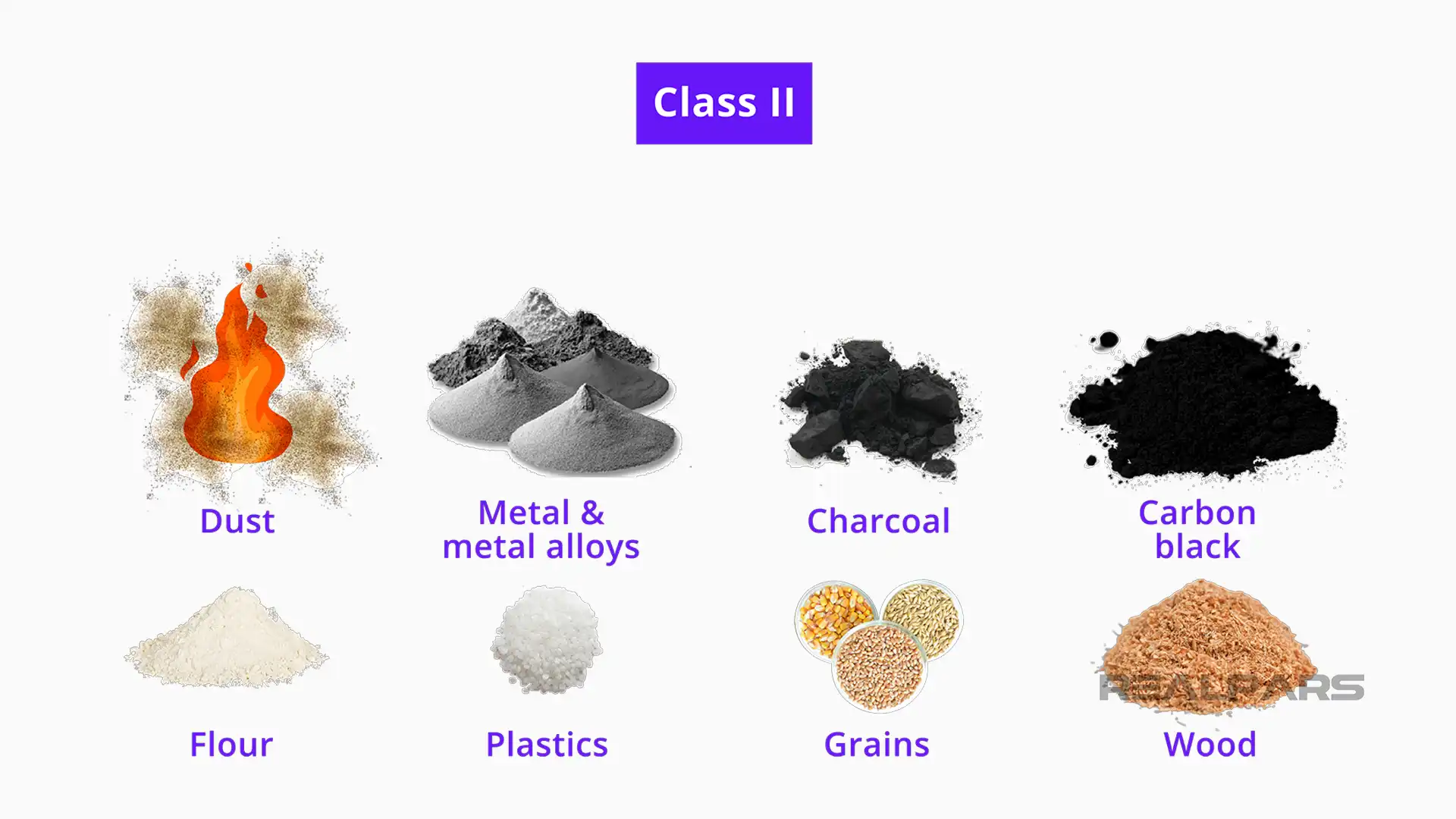
Class III: Class III has to do with flying objects or fibers. These conditions exist but we will not be focusing on them in this article.
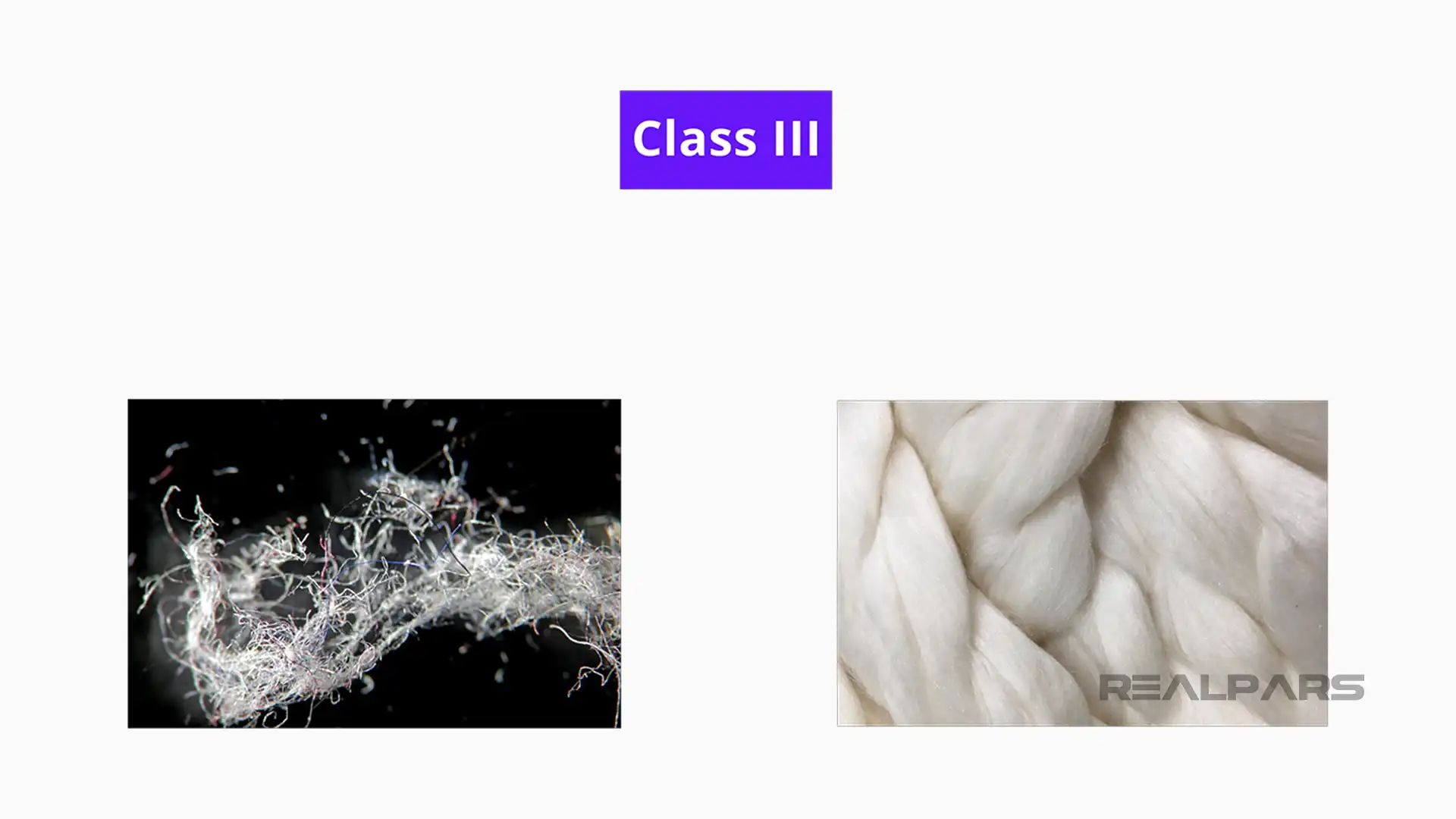
How to apply intrinsically safe standards
Now we will explain how these standards apply for those who want to design automated intrinsically safe equipment in these environments.
In intrinsically safe environments it is necessary to use special circuits to help protect from explosions and fires. Electrically speaking we do this by using optic isolation or by current-limiting devices.
The industry term is a barrier.
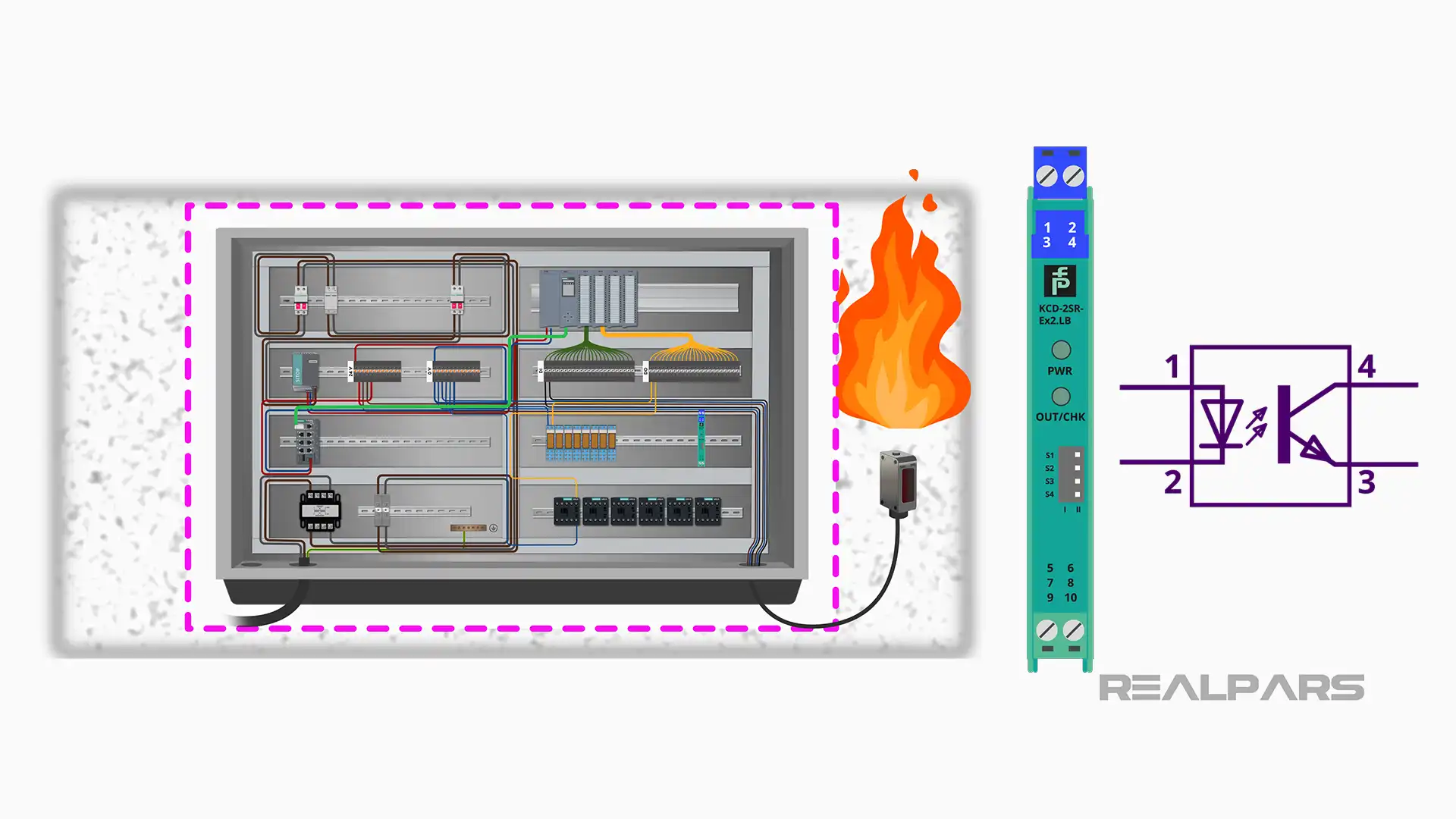
Barriers come in many shapes and sizes but they all optically isolate the sensor in the environment from the electrical cabinet.
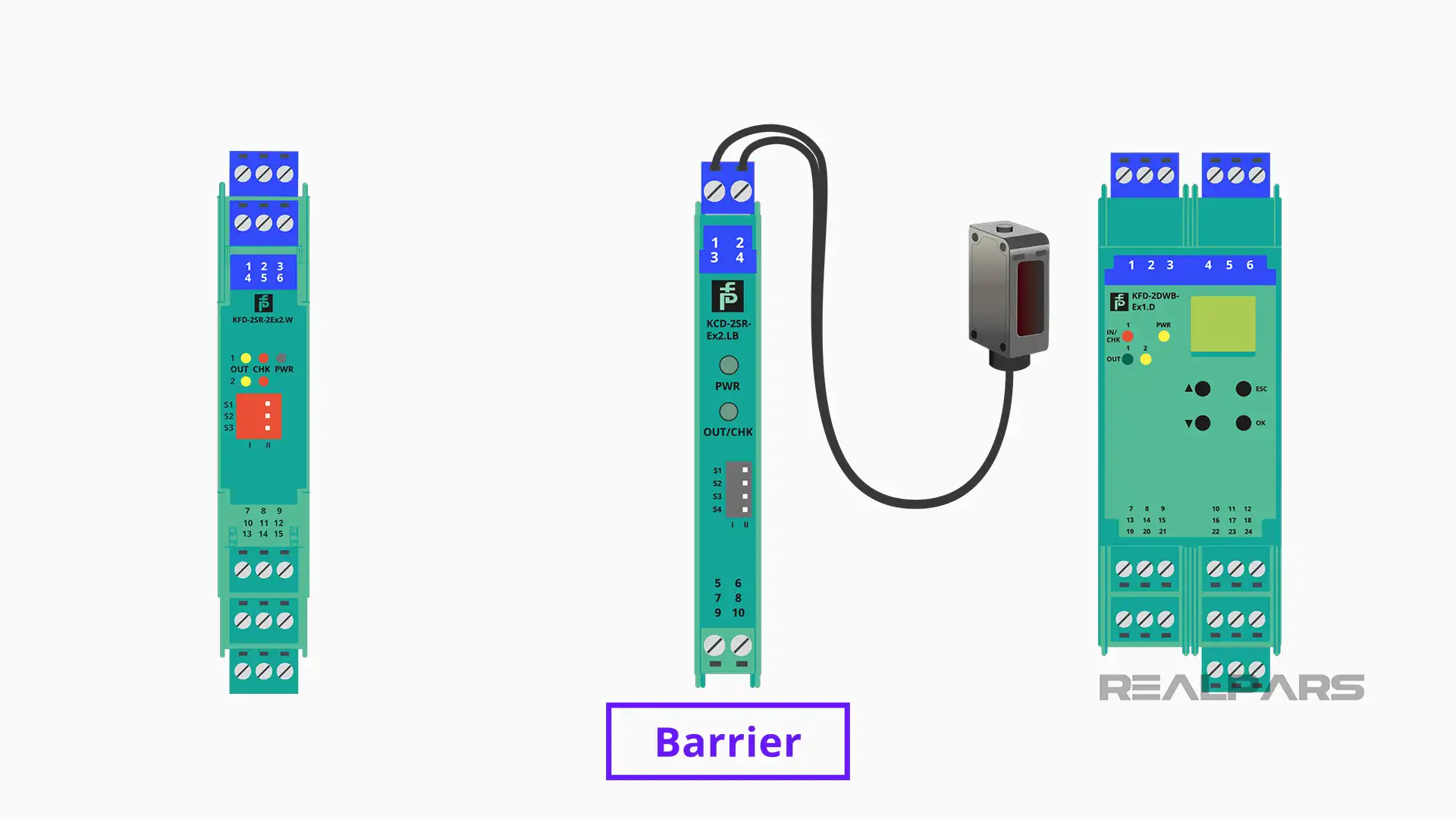
We will now explain what an optic isolator is. An optic isolator is a set of electrical components that connect two circuits optically. The components of an optic isolator are a diode and a light-sensitive transistor usually packaged in a chip.
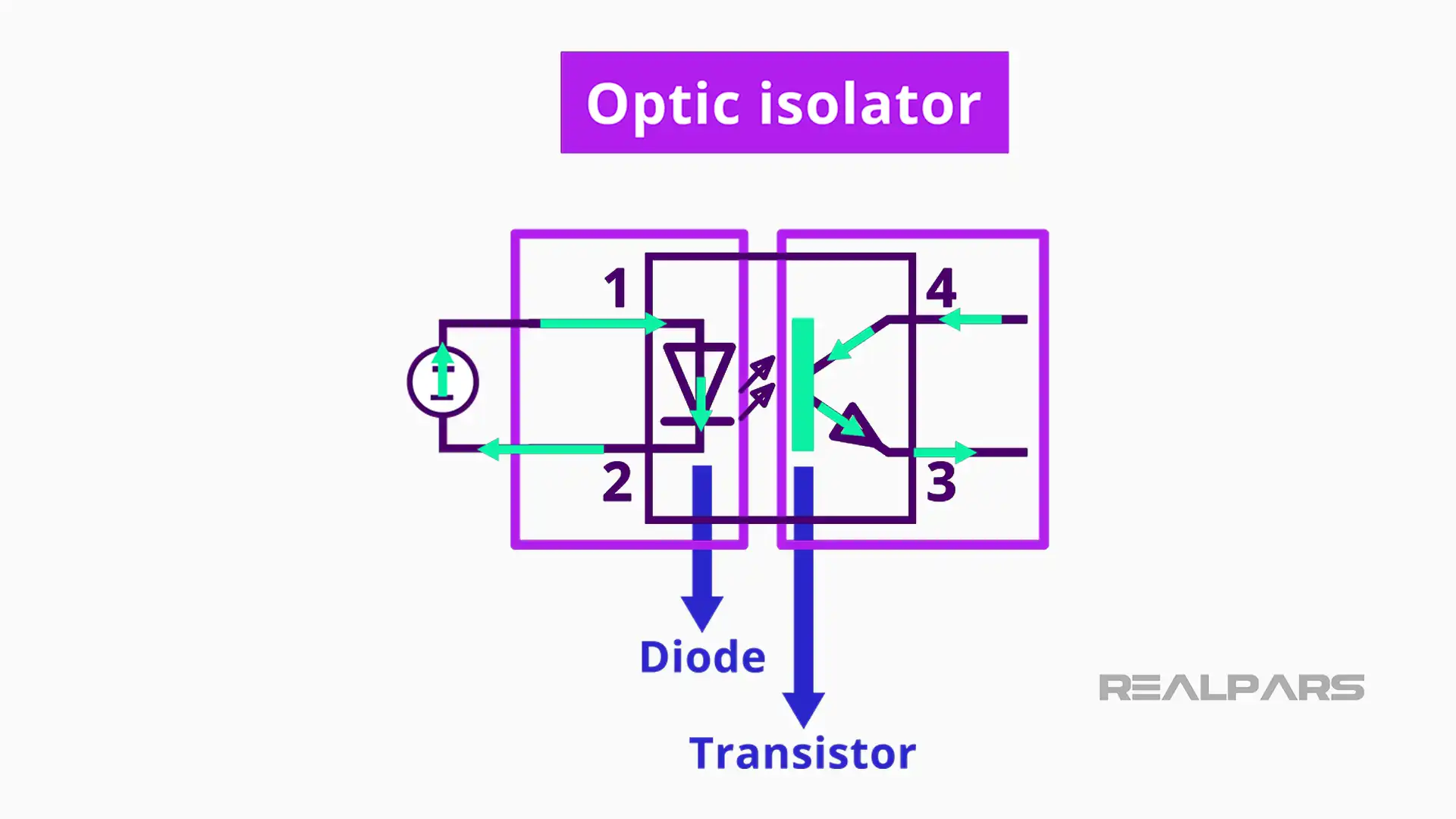
When there is a current flowing through the diode, the diode will illuminate. The transistor will sense the light on its base and then allow current to flow through its collector and emitter.
Because of optic isolation different voltages can be used, which helps in an environment that needs intrinsic safety devices.
Intrinsically safe circuit examples
1. Photo-eye on a conveyor
Here is an example of intrinsic safety in an automation environment. You have the photo-eye on a conveyor in a flour plant. Due to the dust ignition hazard, you are tasked with specifying a solution to safely use the photo-eye.
Because of the environment, you will need to first look up the requirements for the room. You then perform a risk assessment and decide that the room with the conveyor is Class II, DIV 2. DIV 2 refers to the presence of a hazardous atmosphere under normal operating conditions.
You then need to find an intrinsically safe barrier to place in the electrical panel you are designing.
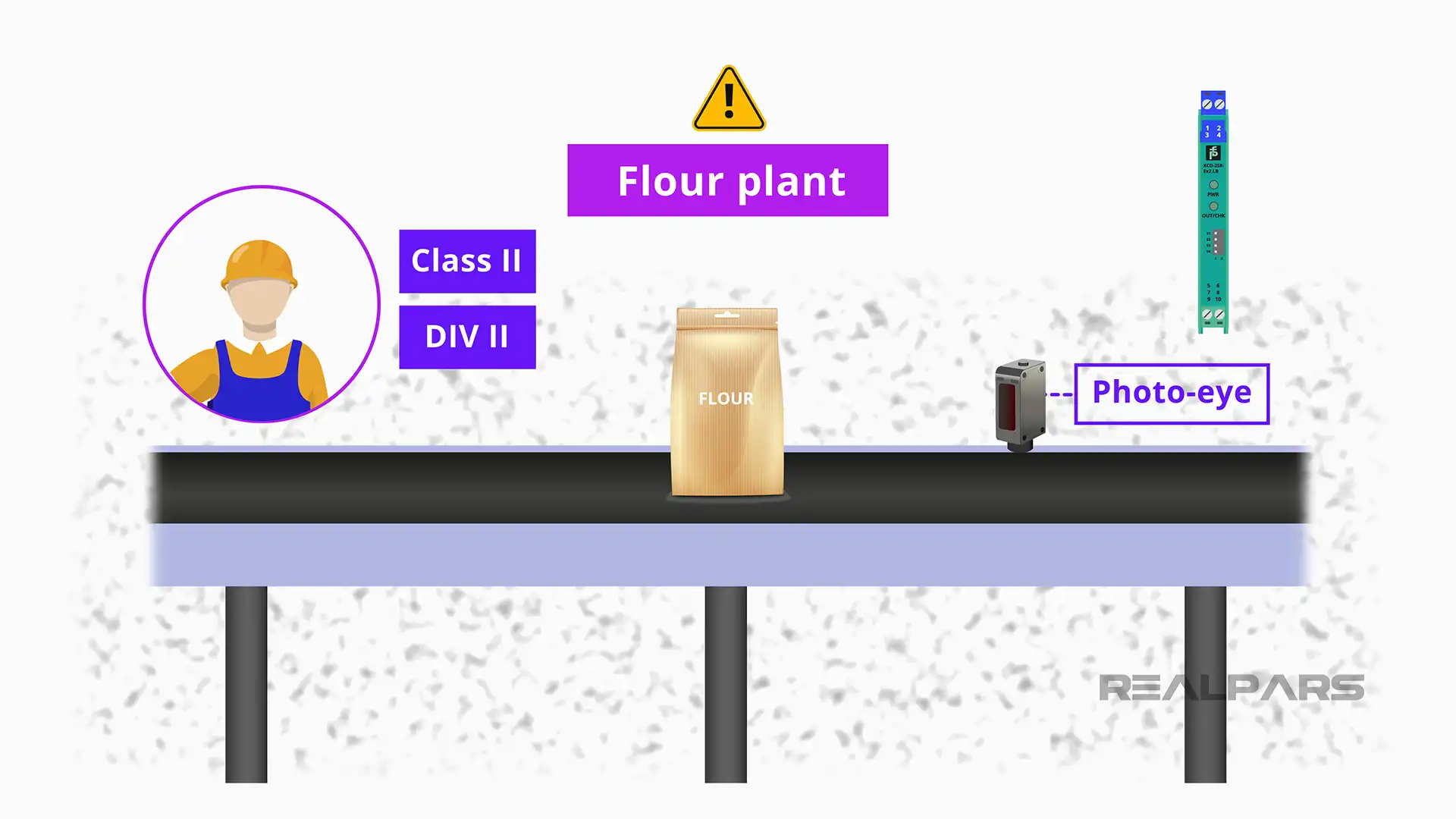
You will also need to find a photo-eye that is compatible with the intrinsically safe barrier.
Some intrinsically safe barriers have a way to toggle between normally open and normally closed. In this example, we will set the intrinsically safe barrier to normally open.
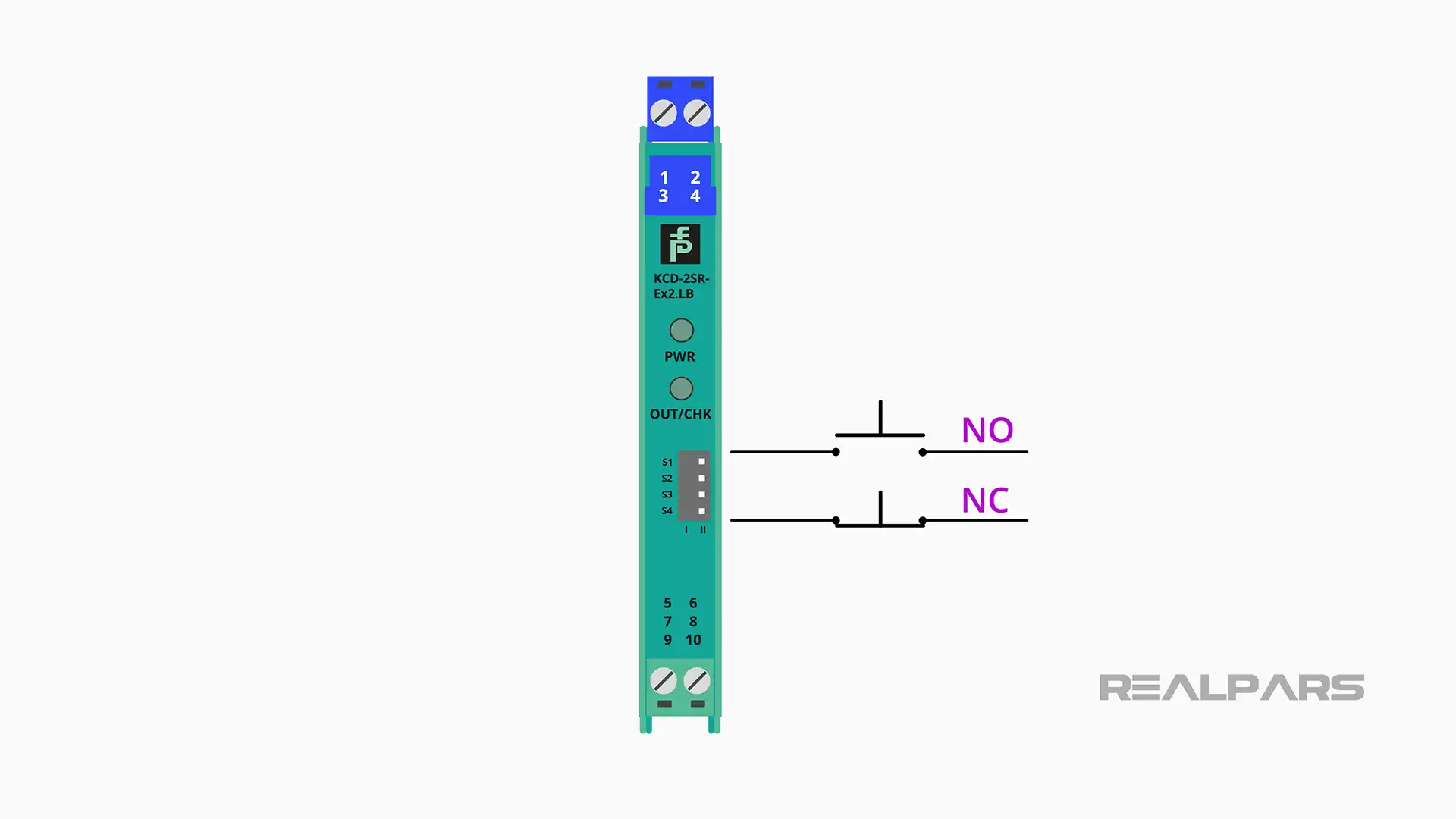
When the photo-eye is toggled on by a bag of flour, the photo-eye will turn on a diode in the intrinsically safe barrier. This photo-eye will use safe voltage and current levels for the Class II, DIV 2 environment.
The transistor will then allow current flow which will output a signal from the intrinsically safe barrier into your PLC.
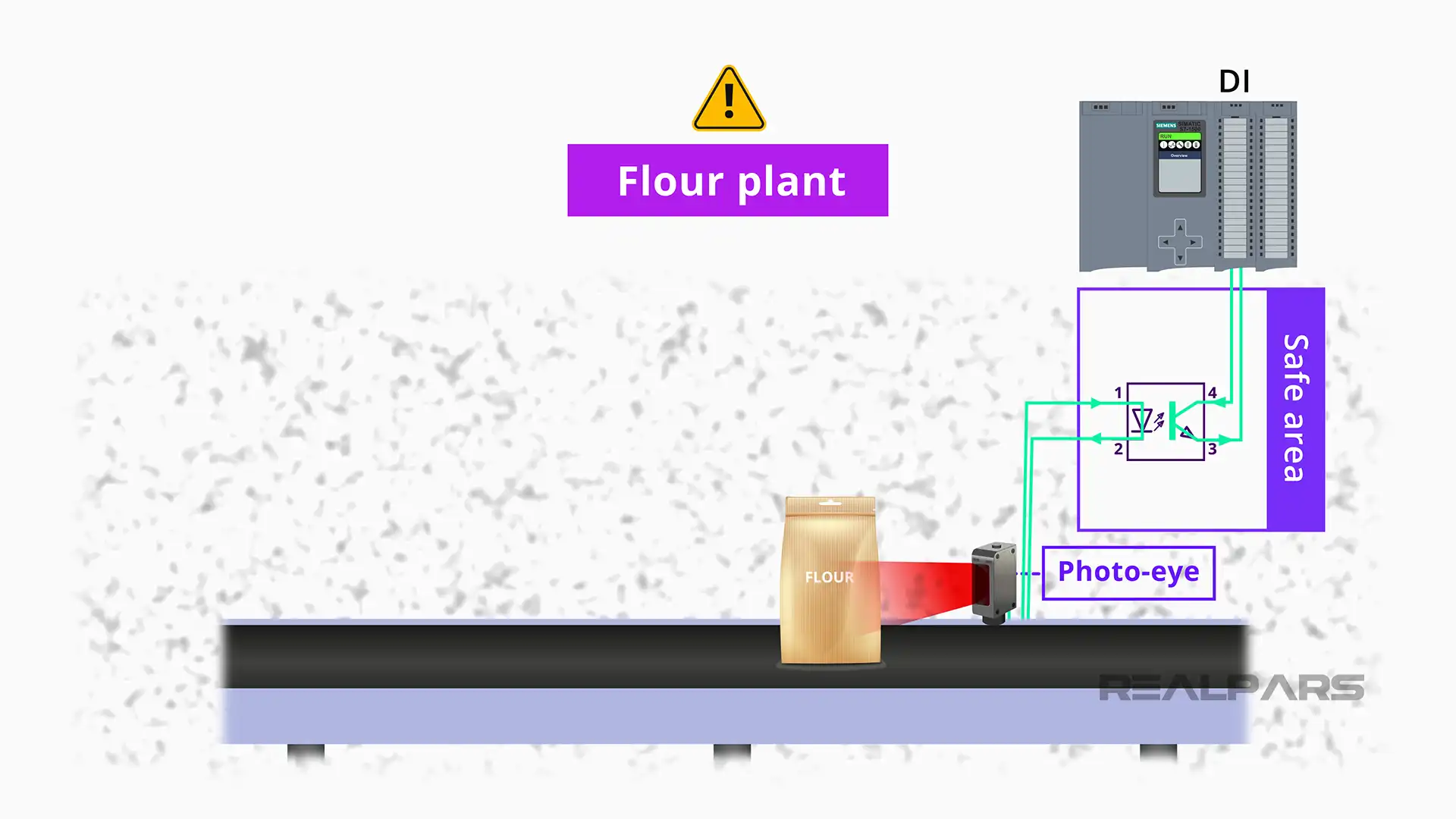
It is worth mentioning that not all photo-eyes will work with intrinsically safe barriers. Make sure to read the manufacturer’s requirements for any photo-eyes that will be used with intrinsically safe barriers.
It is also important to wire the photo-eye according to the wiring diagram provided by the manufacturer. Because of the intrinsically safe barrier being introduced into a normally simple circuit, there is another point of possible failure when something goes wrong.
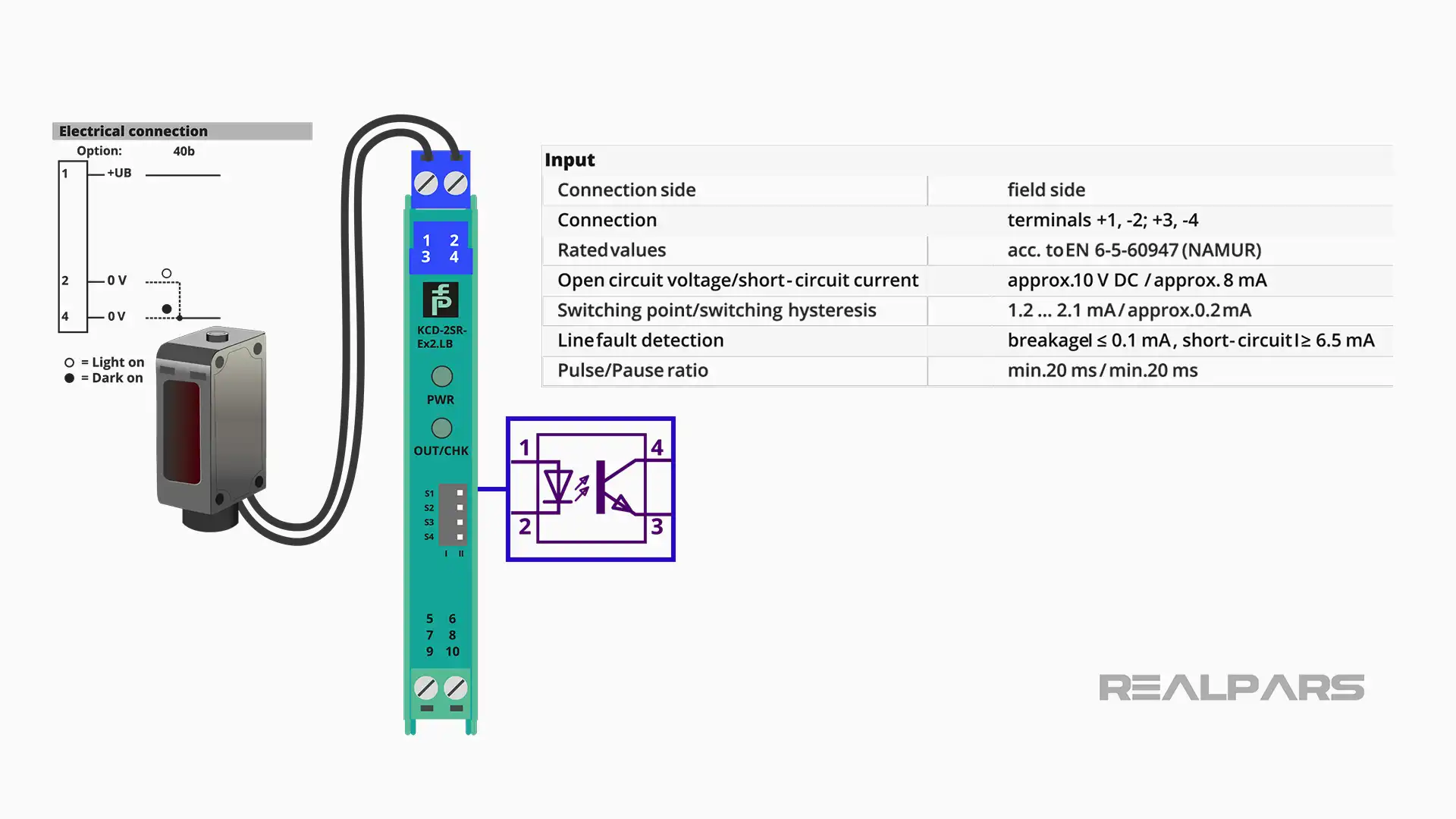
2. Decreasing the dust
We will now discuss some other requirements that are essential in an intrinsically safe environment. In some situations, there will need to be more done with the electrical panel than just installing barriers.
For the example with the flour, the panels in the room with the flour conveyor will need to be pressurized with some sort of compressed gas. This is usually compressed air, which causes positive pressure on the panel and decreases the likelihood of the flour dust getting in the panel.
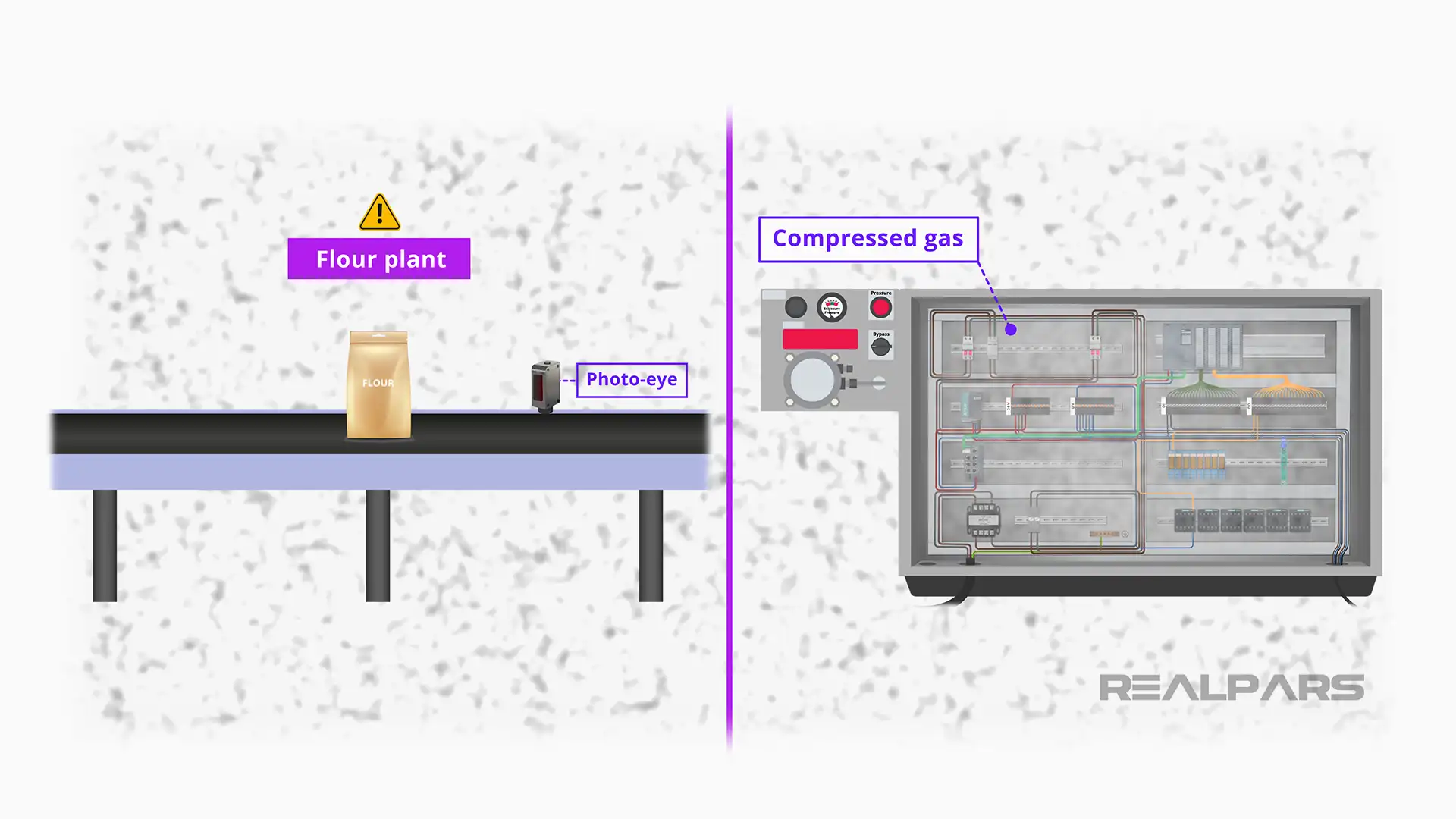
Because of the compressed air, each panel will need to be sealed with some sort of putty or sealant.
To follow the Class II, DIV 2 standard pressure switches will need to be installed.
When a panel is opened, the switches will turn on a red strobe light, alerting those working nearby that the room is unsafe.
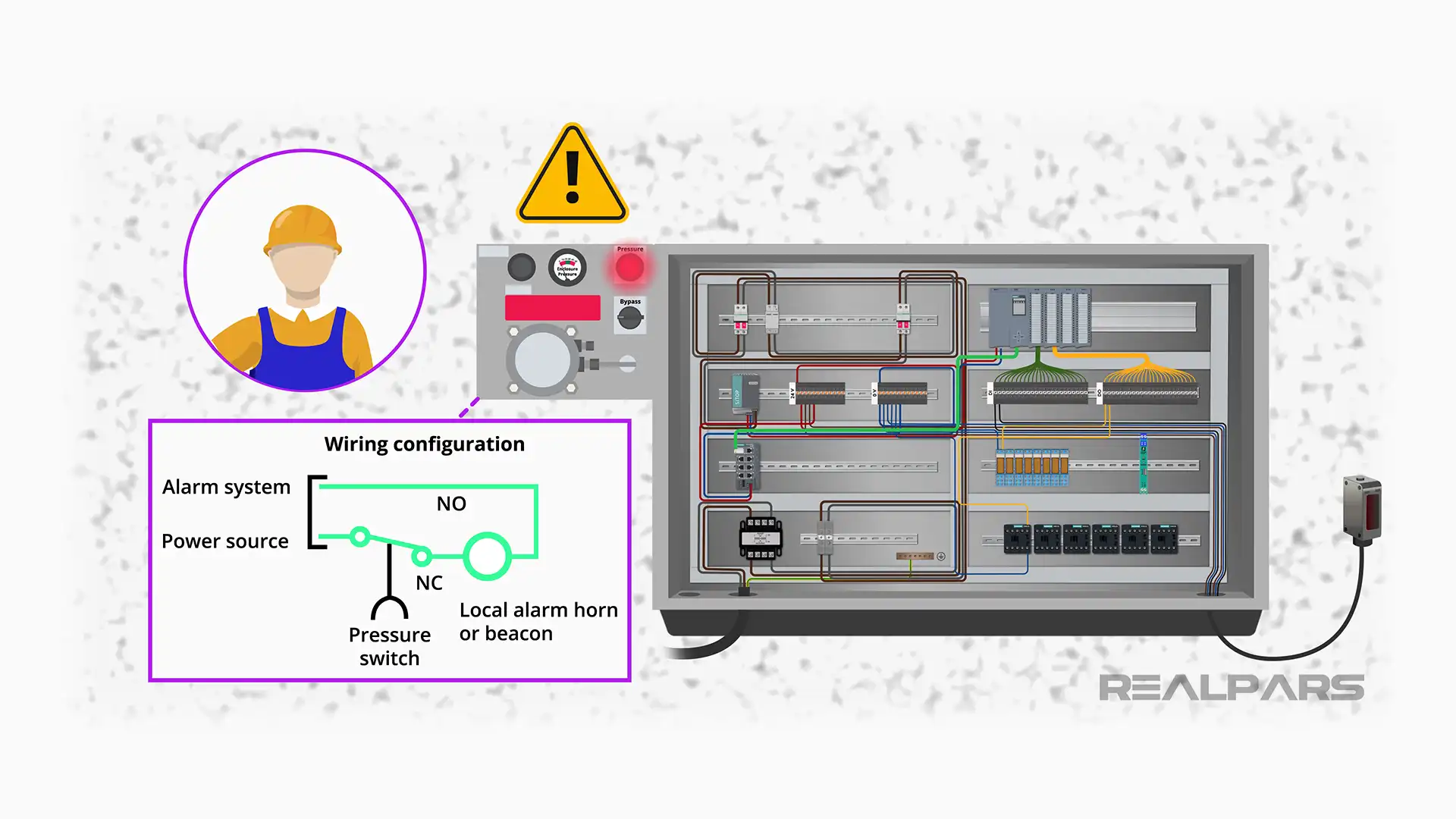
When designing a Class II, DIV 1 panel there are more restrictions. DIV 1 refers to the presence of a hazardous atmosphere under abnormal operating conditions.
Just like the Class II, DIV 2 environment, a Class II, DIV 1 will need pressure switches for loss of pressure and they will additionally need to remove line power to every panel in the room when the pressure is not safe.
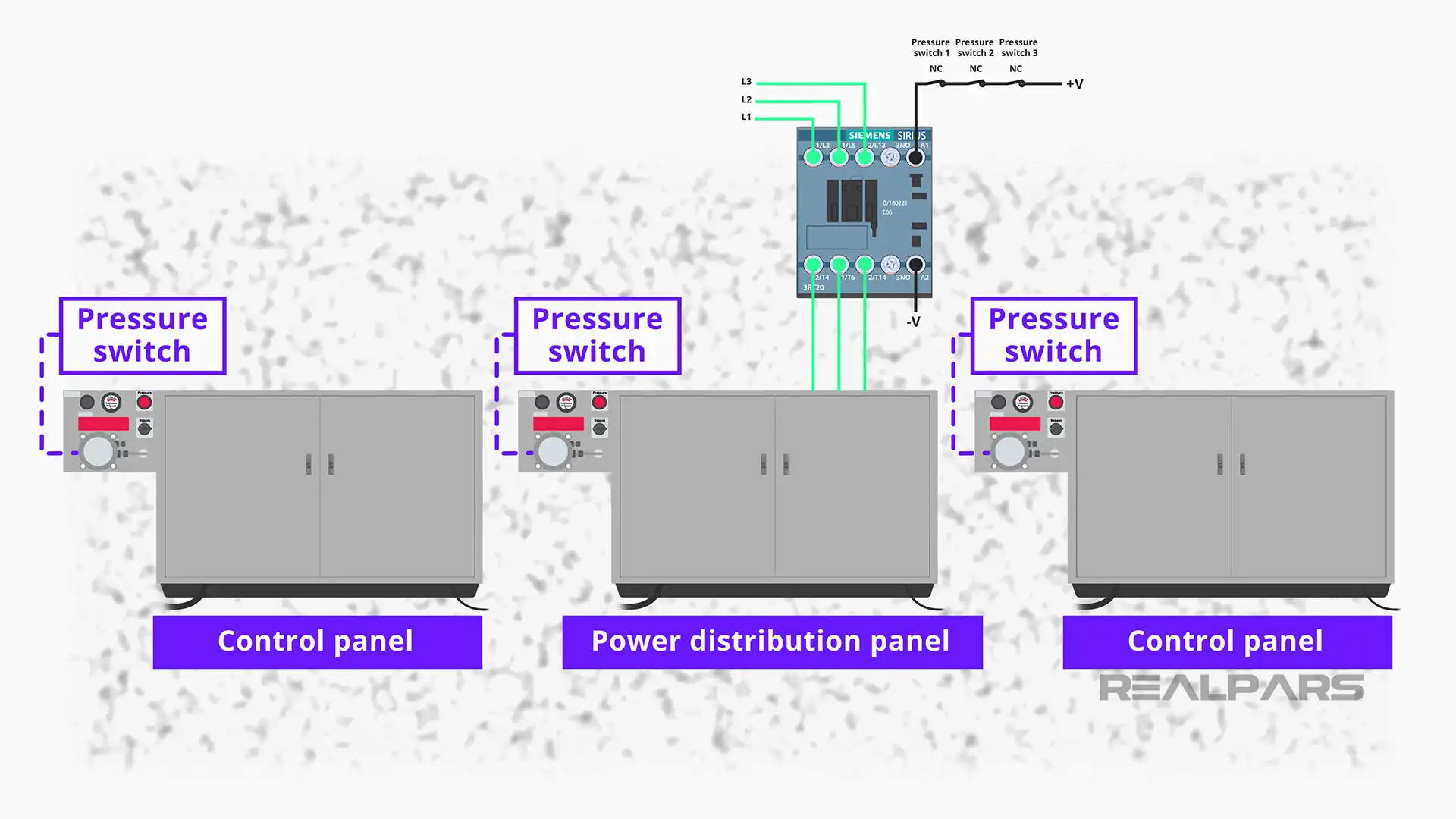
There are circumstances where maintenance or troubleshooting must be done on the pressurized intrinsically safe electrical enclosure. This is a problem because when the panels are opened it will shut down the power to the whole system.
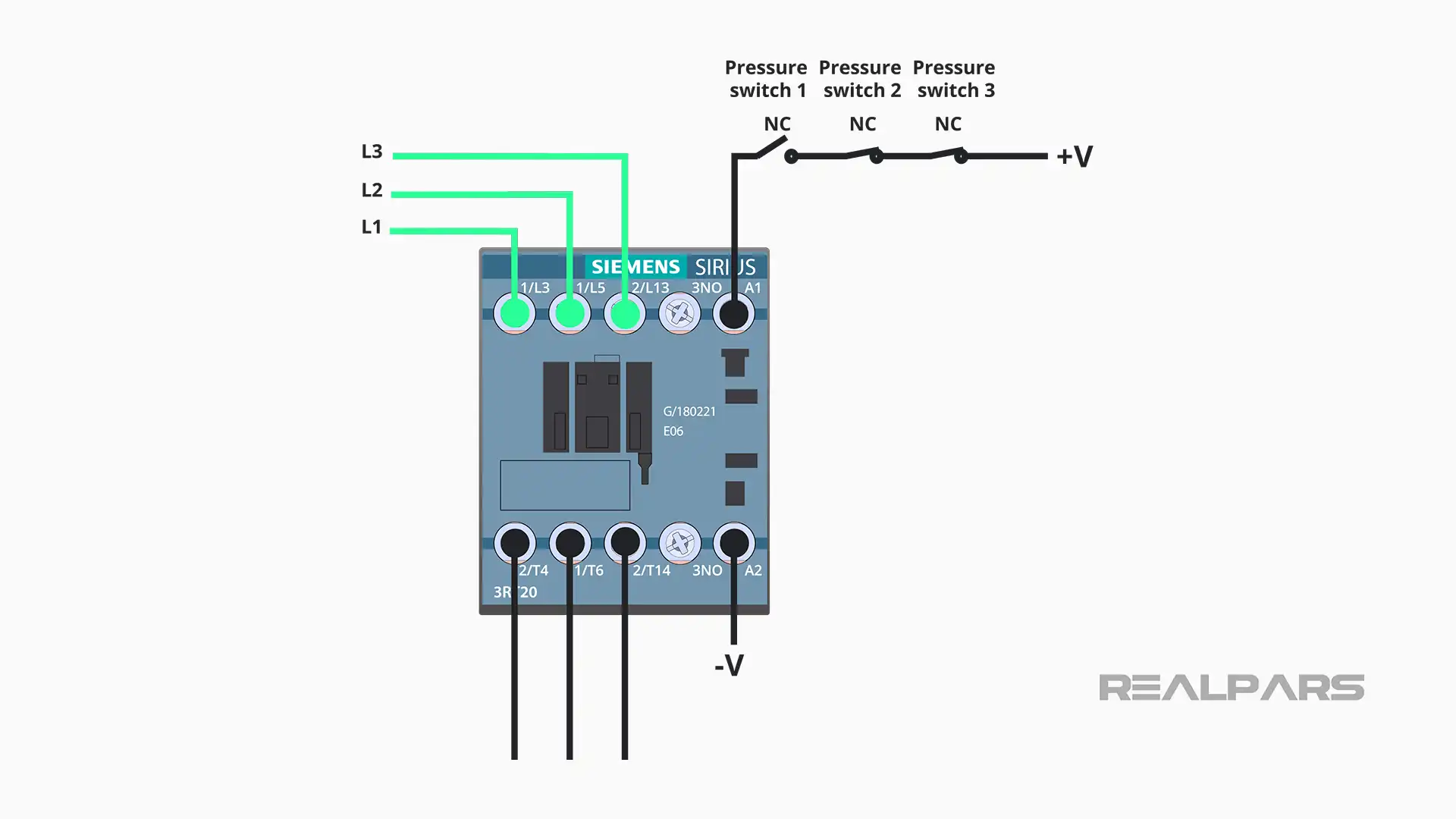
To help mitigate this issue, a keyed bypass switch can be used to keep the power on during troubleshooting or maintenance.
While work is being performed the loss of pressure red strobe light will illuminate. When the work is done, the keyed bypass switch needs to be turned into a safe state.
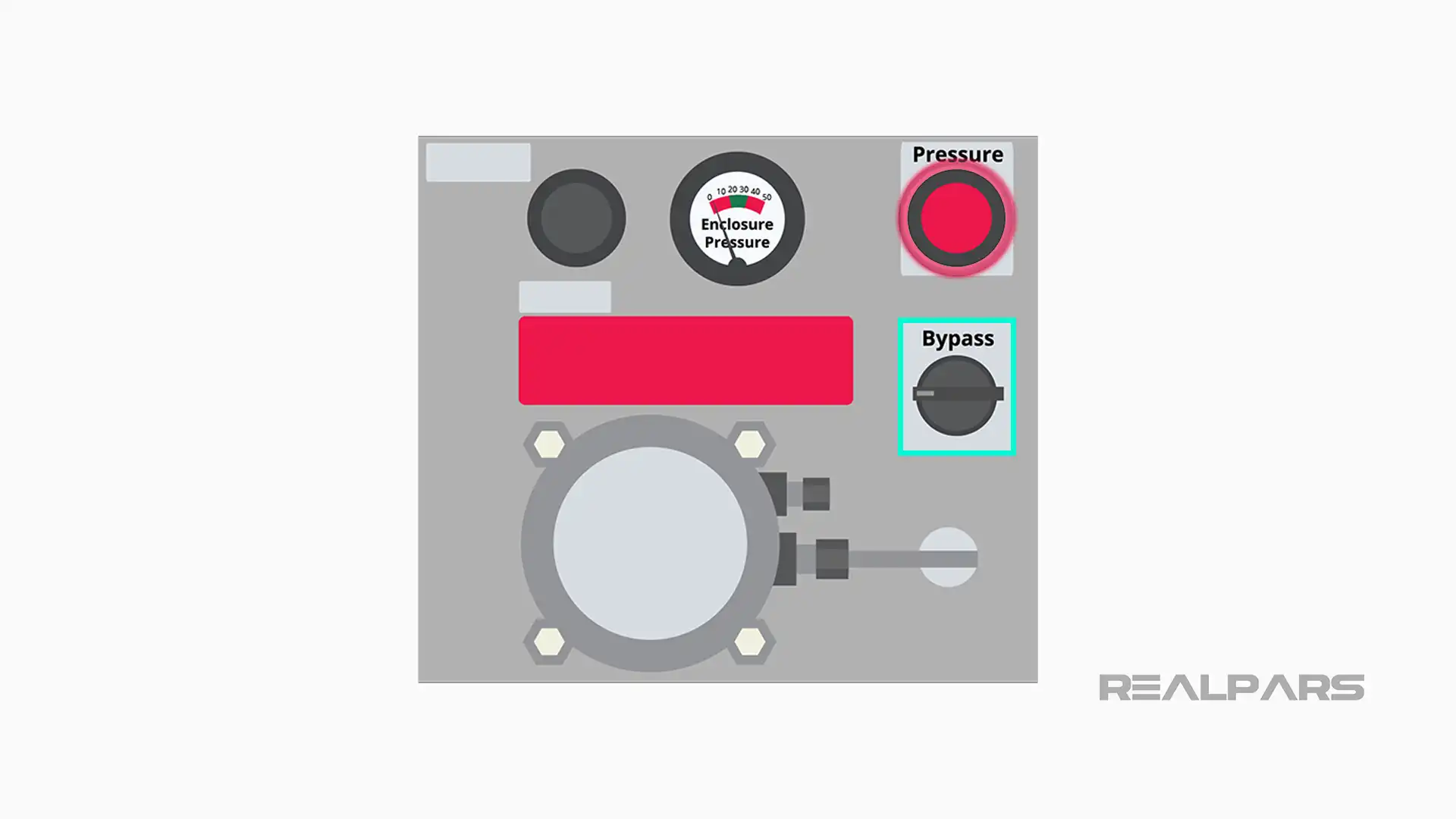
3. Weight scale conveyor
We will now explain one more example of an intrinsically safe barrier. You need to have a check weigher scale conveyor to check the weight of the flour bags. You will need to use an intrinsically safe barrier to limit the current and voltage of the load cell.
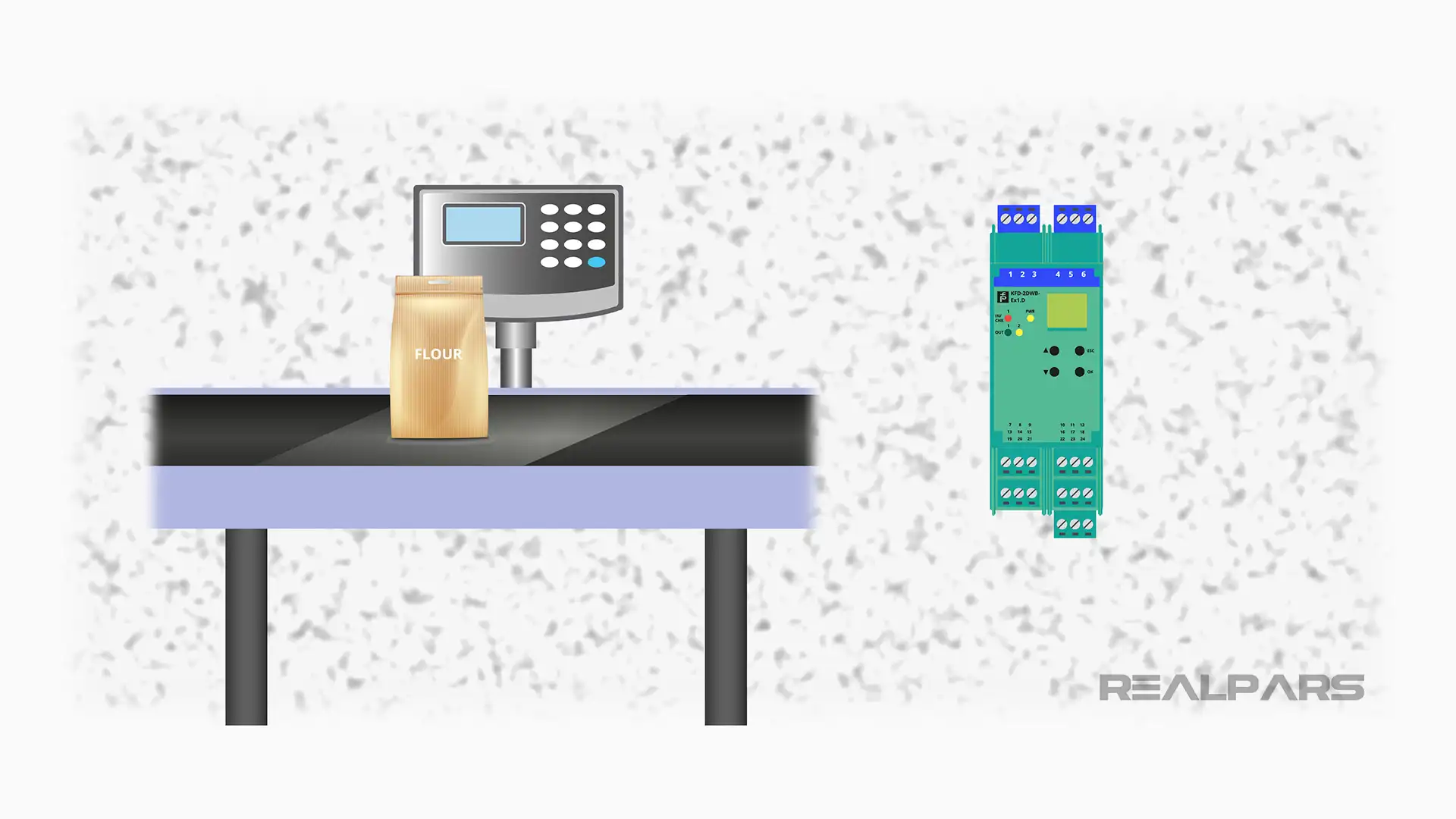
Make sure you use a compatible load cell with an intrinsically safe barrier according to the manufacturer’s recommendations.
Summary
In summary, intrinsically safe devices and equipment can prevent fires or even explosions. Knowing the hazards of the environment will help you choose which intrinsically safe devices to use.
If you want to learn more, you might want to review our other article, What is a NAMUR Sensor?.
If you have any questions about intrinsically safe or about IS required equipment, add them in the comments below and we will get back to you in less than 24 hours.
Got a friend, client, or colleague who could use some of this information? Please share this article.