In previous lessons, we discussed SCADA applications and systems, and the components within them. Here is a quick recap of what was previously discussed.
SCADA is a collection of hardware and software components. Plant floor devices such as pumps, valves, and transmitters transfer real-time data to processors such as RTU’s or PLC’s.
That data is then disseminated to various devices within the network such as Human Machine Interface terminals or HMI’s, servers, and computers. Images of these processes are presented to operators for various types of interaction.
SCADA system applications
In this lesson, we are going to discuss the role that a SCADA system may play within a Water Treatment Plant.
With the short recap, we know that we are going to have both a hardware and software collection.
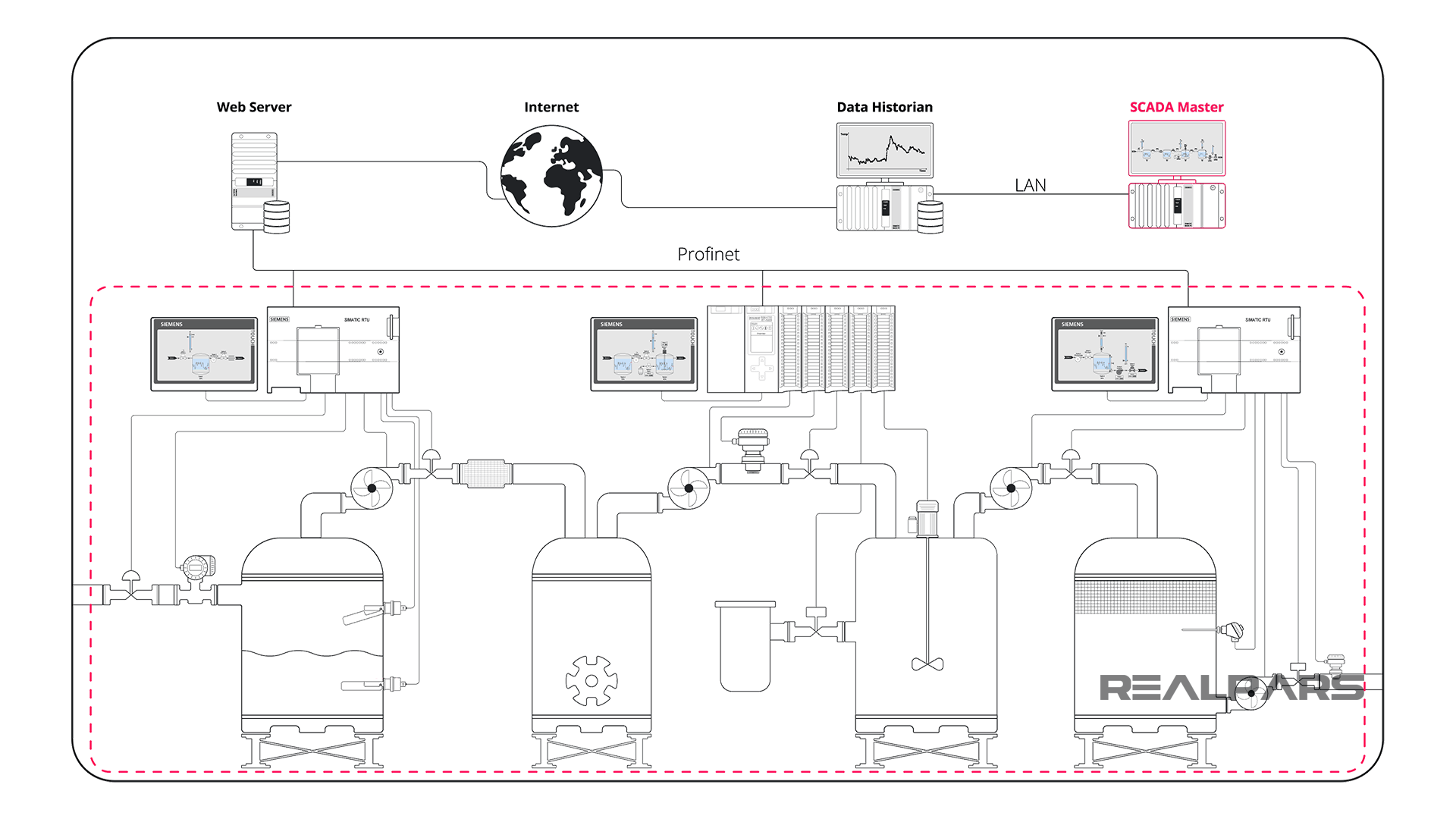
SCADA software
For the software, we will use a software package such as Wonderware, Citect, FactoryTalk SE, etc.
That software will be used to create the interface required to view and operate the control system.
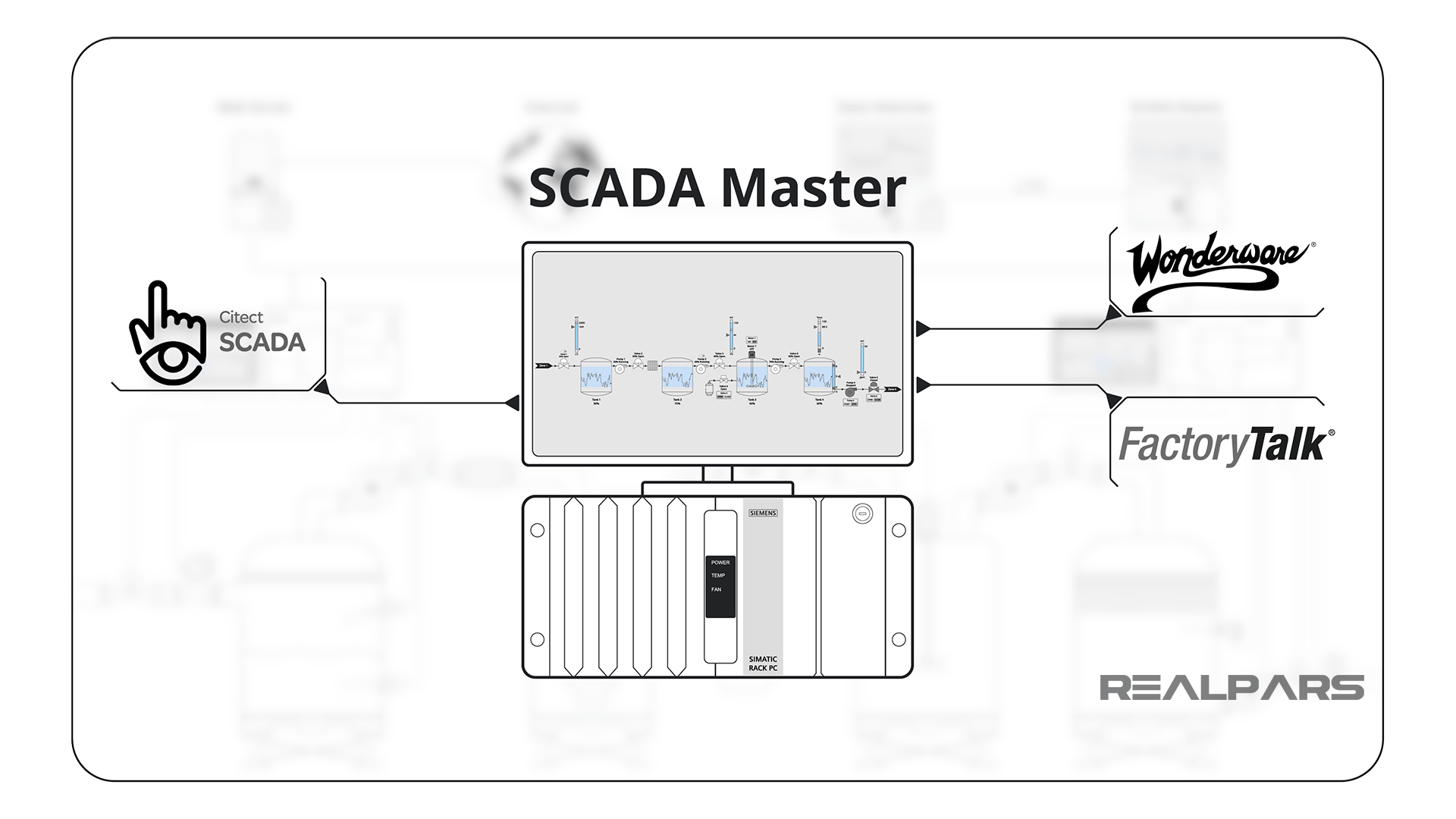
SCADA hardware
We will also have a hardware collection. That group of items will likely consist of pumps and motors, valves, switches, and transmitters among other things.
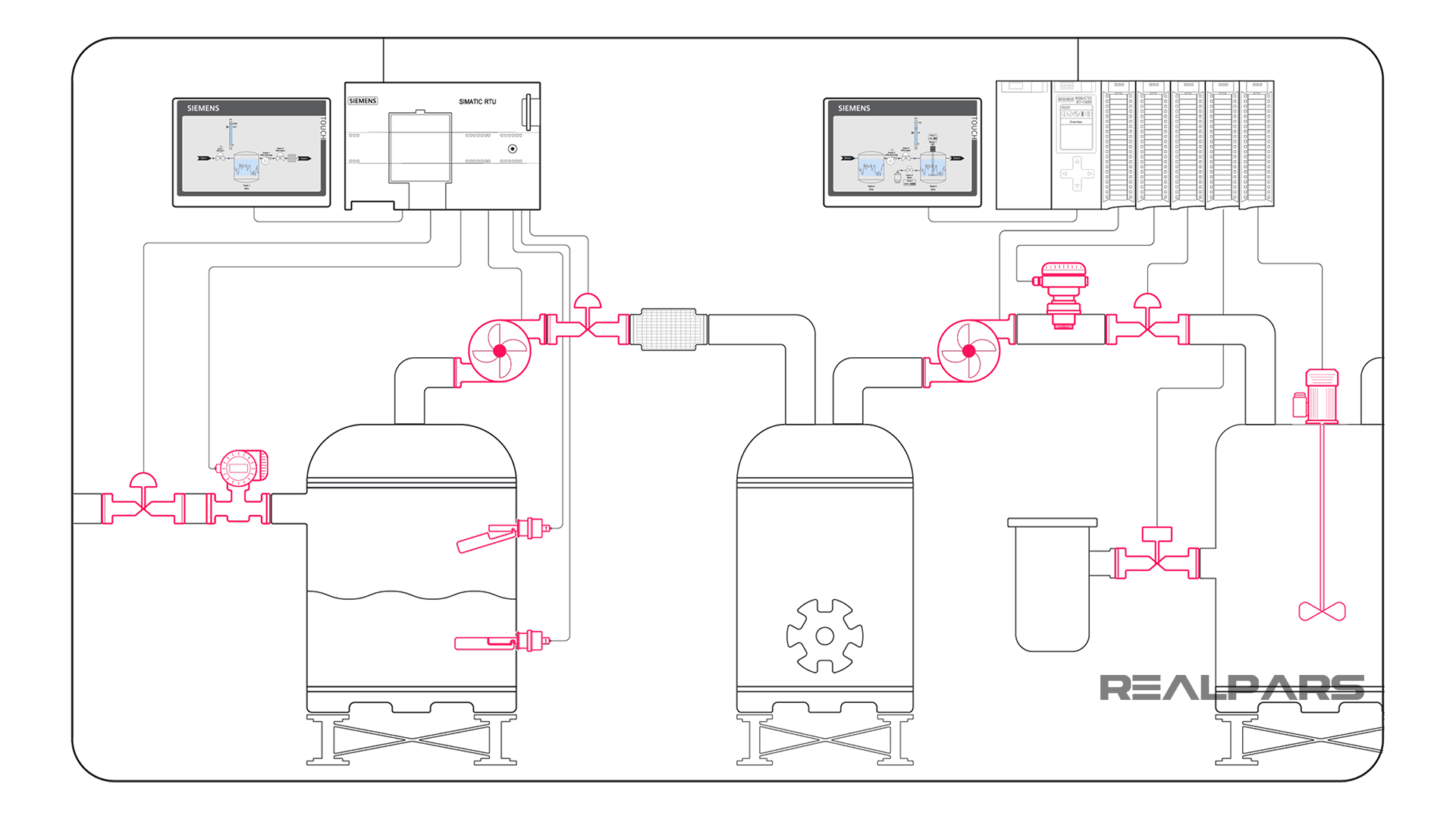
We also know that these components will communicate with a processor of some type. These processors, in turn, will allow the components to be viewed, graphically, on the SCADA system.
SCADA graphic representations
Pictorially, this hardware presentation may be as simple as flat lines that represent pipes, simple graphic representations of valves, and motors that may change color according to current status such as opened or closed for valves and running or stopped for the motors.
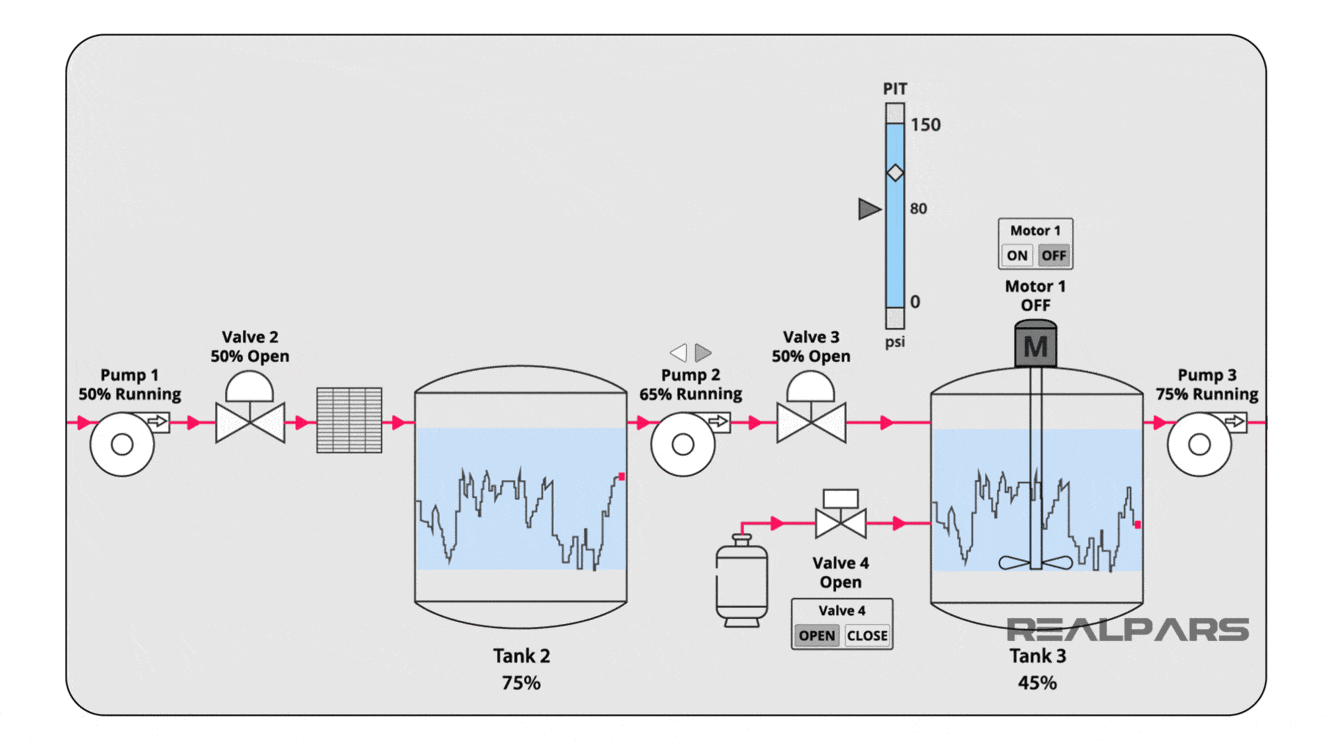
The appearance can also be very elaborate with 3D graphics of spinning motors and rotating valves.
More likely though, something in between with 2D piping that is possibly color-coded based on process and field device graphics that change color according to conditions.
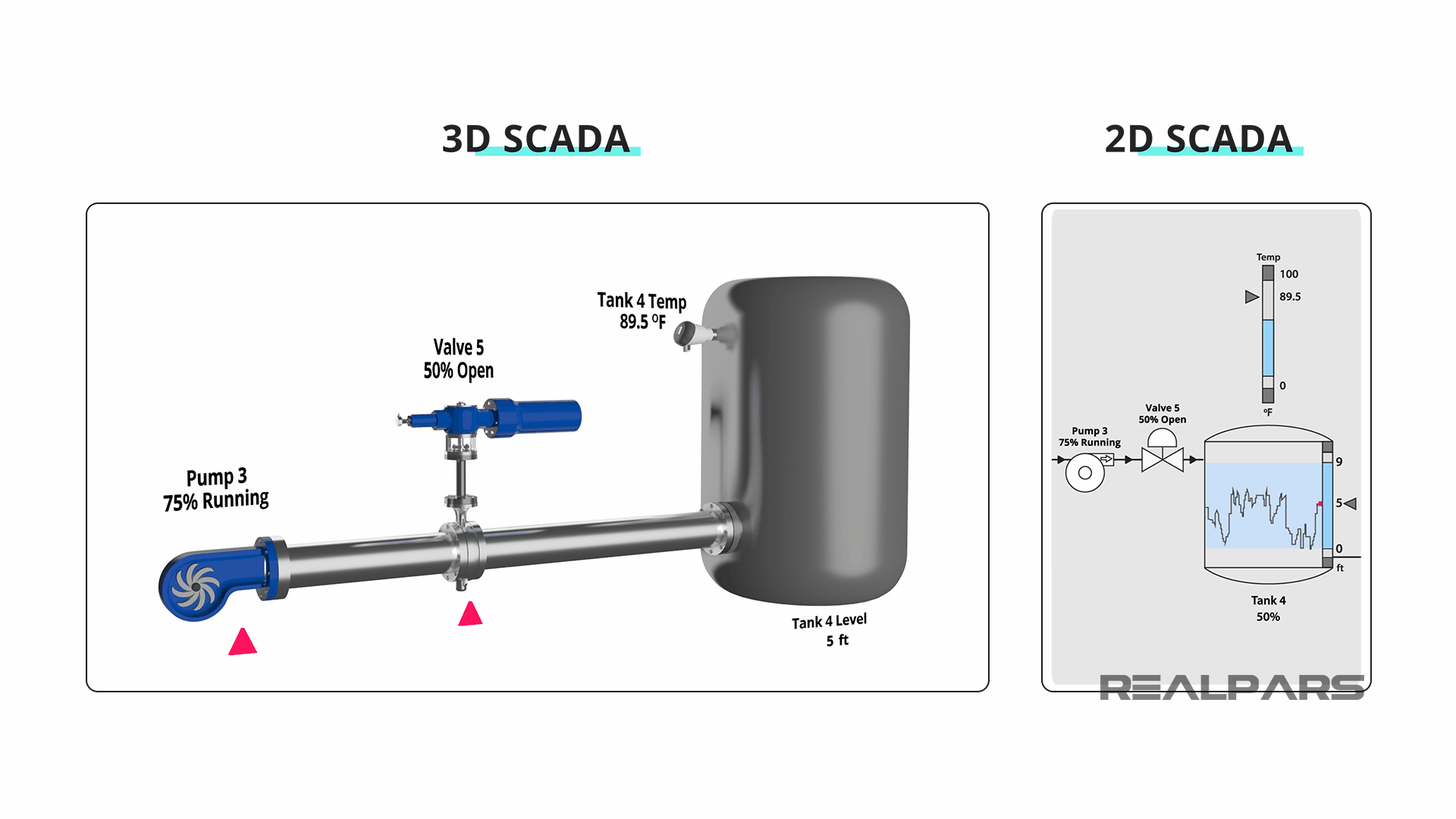
The reason the latter is more likely is many plants are interested in graphics that are less complex such as textual displays or simple gray tone objects that only change color when in a fault or abnormal condition versus spinning or complicated 3D graphics that may create distraction versus provide immediate information.
SCADA applications in Water Treatment
The role that the SCADA system plays within a Water Treatment system is vital for ensuring the quality of the finished product.
The function of SCADA in water systems begins with the graphical interface. Typically, the layout of the graphics would be similar to what may be seen on Process/Piping and Instrumentation Diagrams or P&ID’s.
If you are not familiar with what a P&ID is, essentially it’s a two-dimensional drawing that depicts the layout of the hardware collection we said we would have in the SCADA system.
These drawings would show the piping layout with pipe sizes.
The location of instruments, valves, motors, etc within the piping, as well as symbols indicating what signals will be passed to and from the processors in the system.
The controls engineer would take those P&ID’s and create a group of graphical screens that would contain all pertinent information that an operator may need to interact with and control his or her water treatment system.
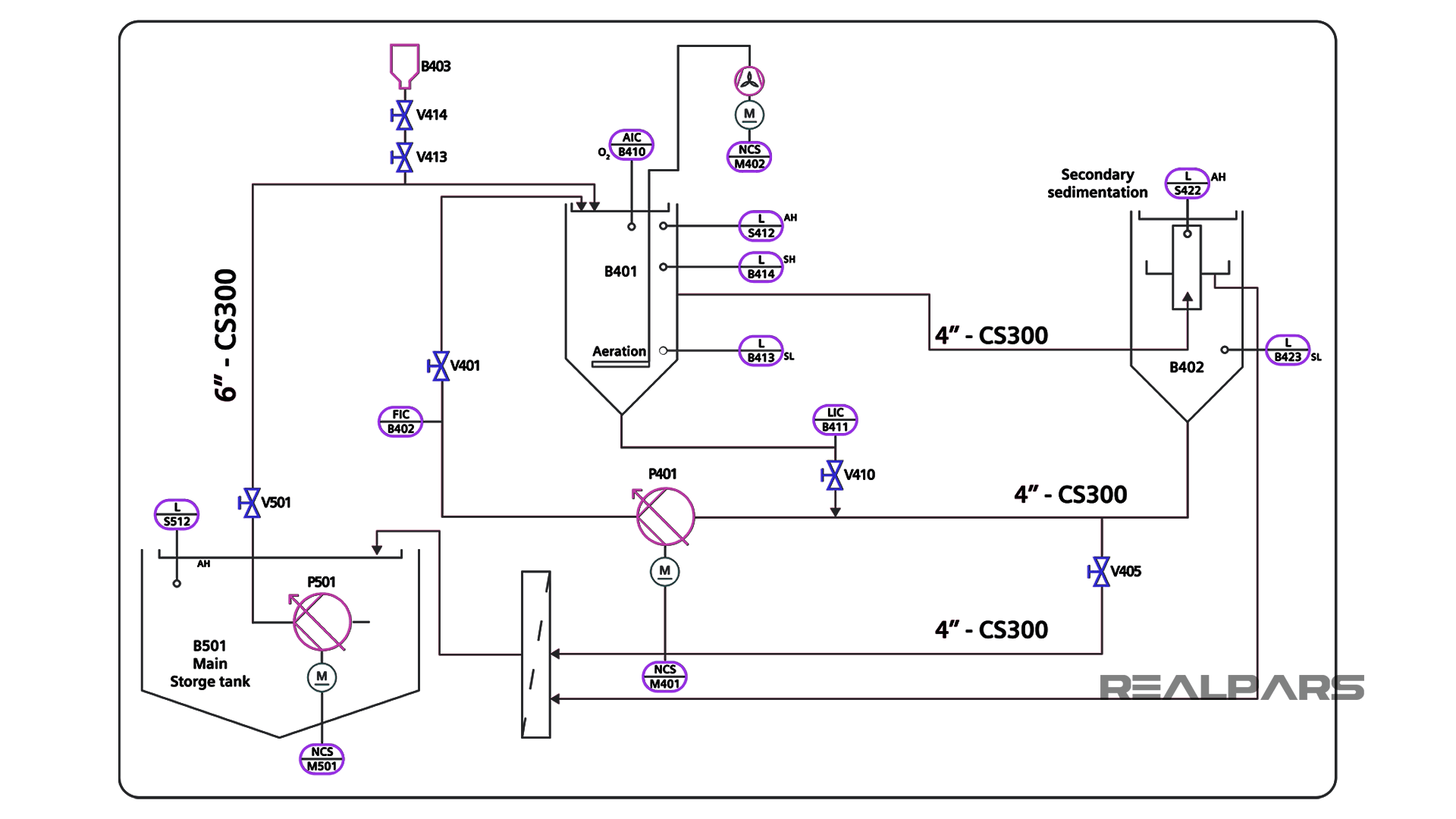
SCADA numerical information
Depending on the plant preference for graphics, minimally the screens would include some numerical information for process instruments and probably the unit of measurement such as GPM or gallons per minute, pressure readings in psi, etc.
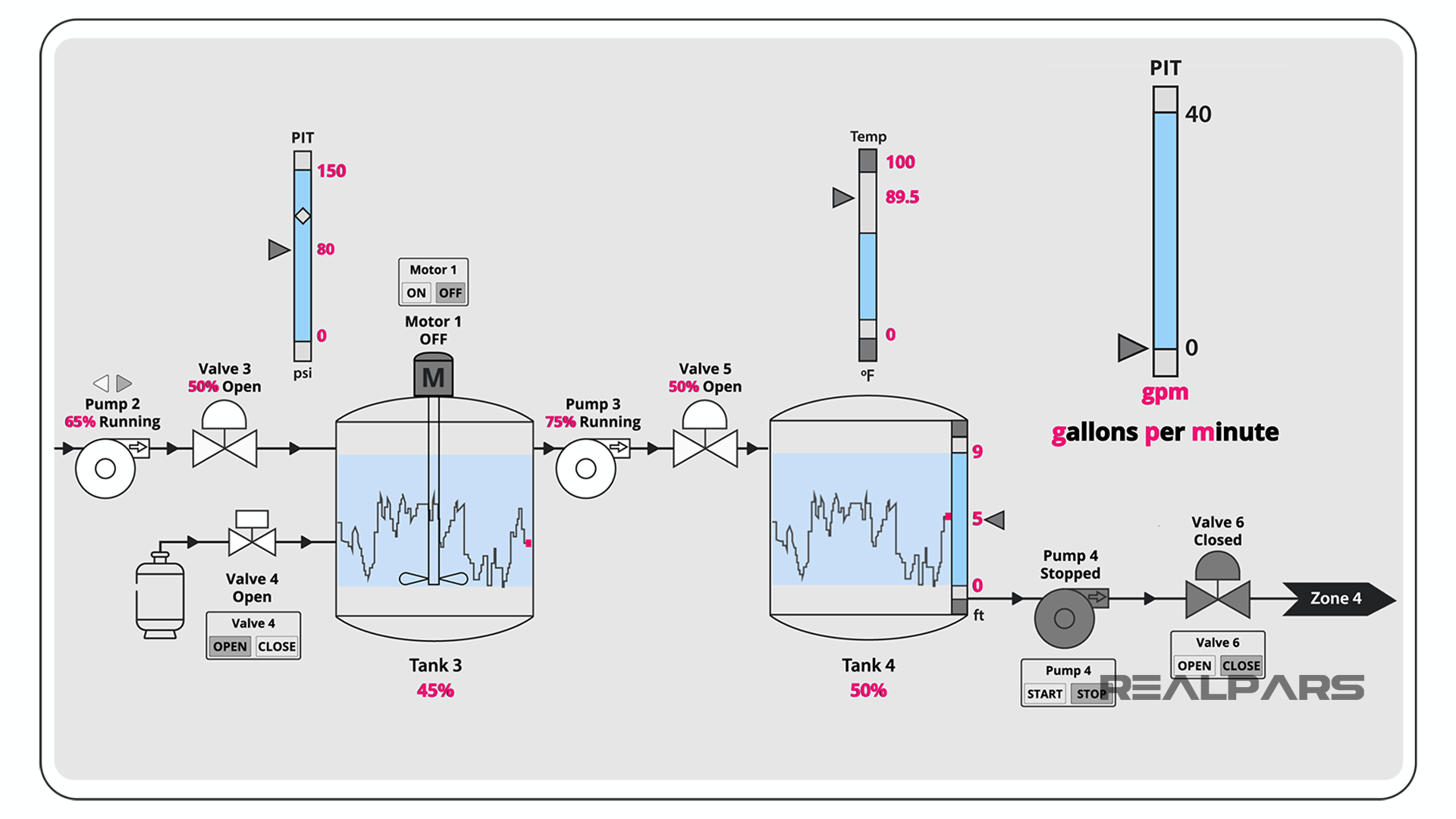
Most systems would allow for some sort of manual manipulation of devices such as manually opening or closing valves or running motors via buttons located on the screen.
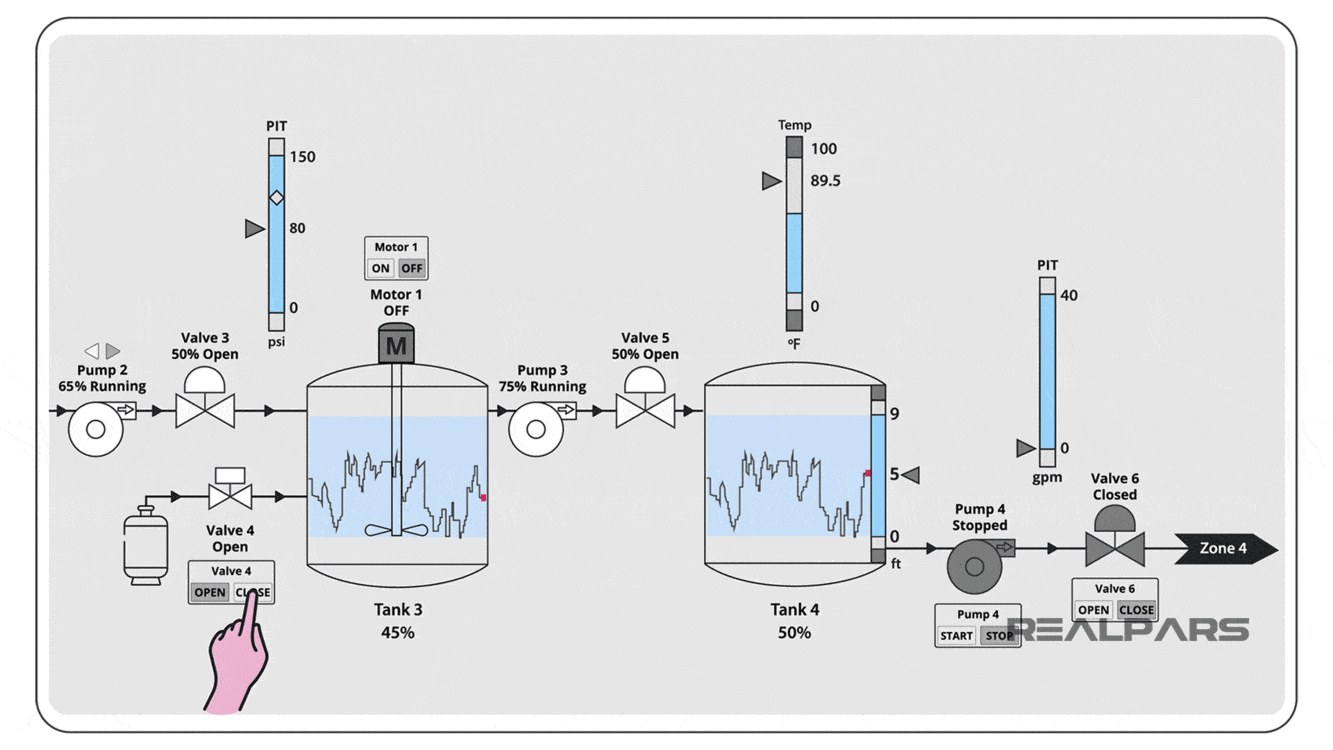
Process setpoints would also be located on a screen.
These setpoints may be used to modulate valves to maintain flows or pressures, start, stop or vary the speed of motors, select which equipment to run or how many pieces of equipment to run to produce the desired quantity of water.
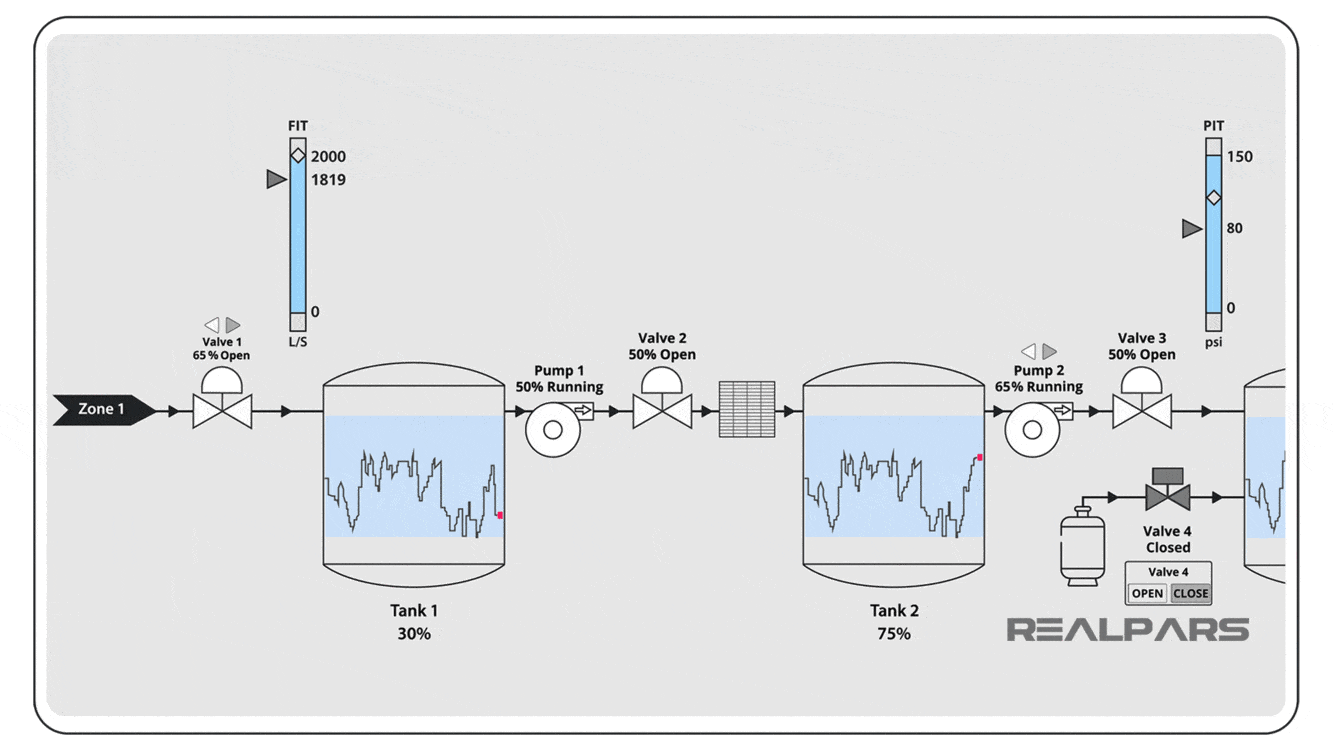
The setpoints might also be used to indicate alarming when a process reading is outside of some defined limit.
This alarming function, which is an integral part of a SCADA system, would inform the operator of process excursions, alerting plant personnel that the expected quality may be impacted.
With this knowledge, personnel can apply various changes in order to bring processes back within the expected limits.
Considering the SCADA system is the collection of various components, we know that they will all work together in order to accomplish the expected goals.
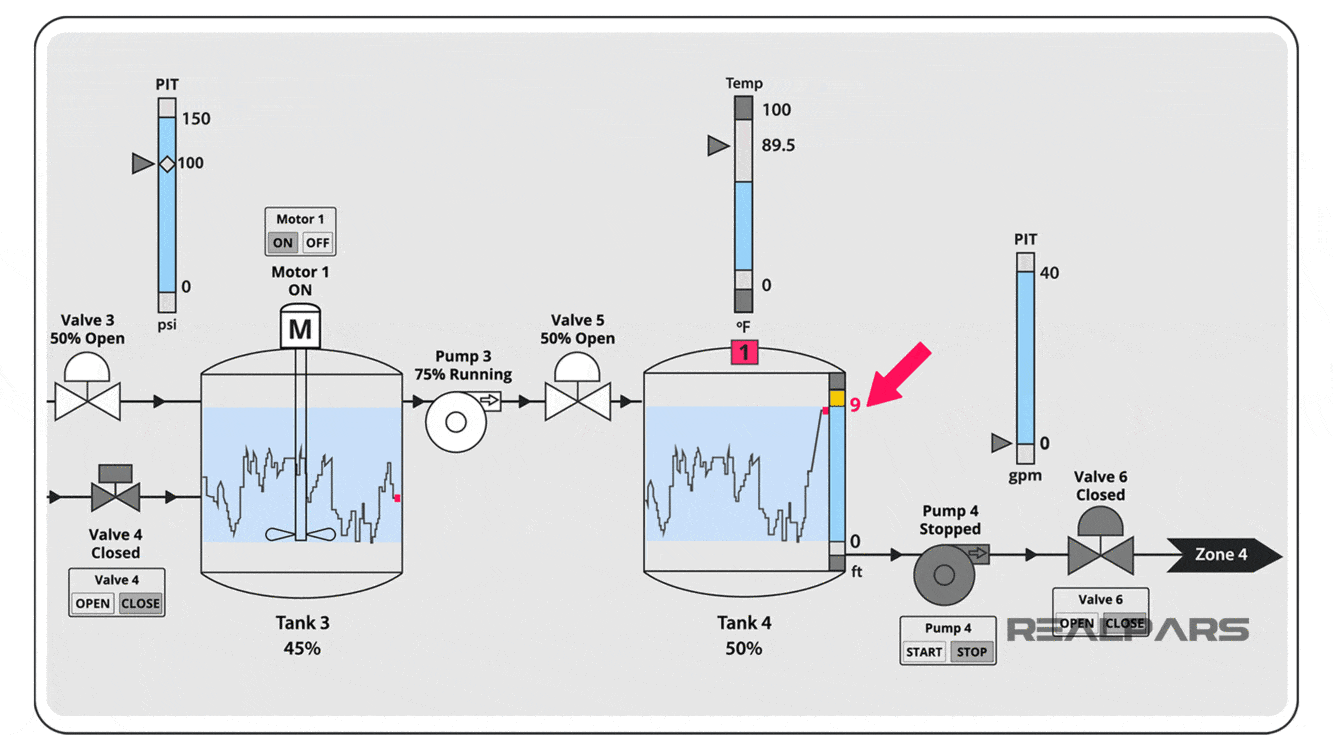
SCADA applications historical data
We also know that the SCADA can historically log process variables and in some very advanced systems, use this historical data to predict outcomes, and provide advanced warning to personnel when something seems amiss.
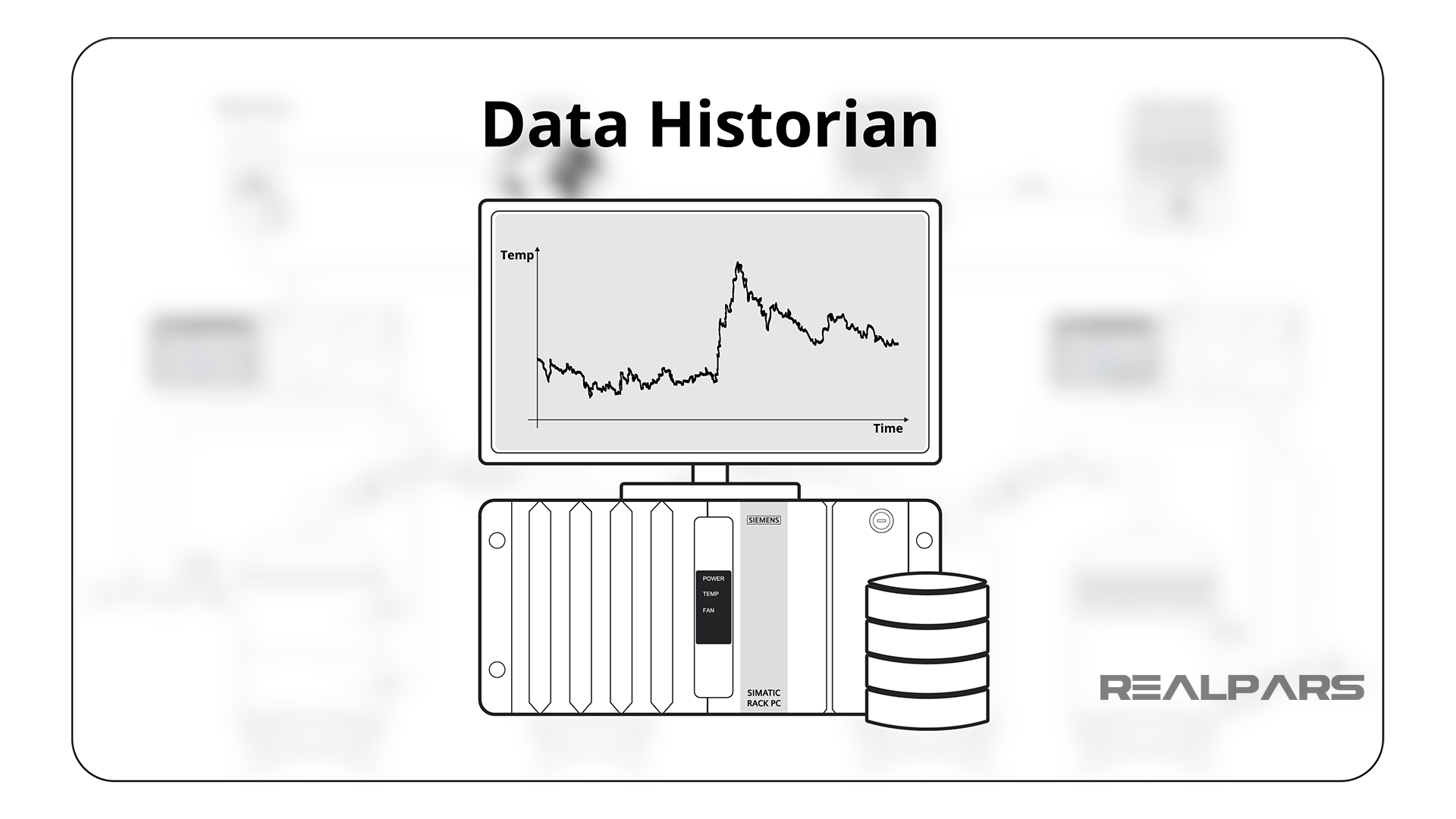
Summary
In summary, today’s SCADA systems play a vital role in the implementation and control of Water Treatment plants.
Whether we’re talking about fresh drinking water or the processing of wastewater, controls engineers, plant personnel, and city/industry managers all are likely pleased with the advances made over the decades.
That progress with SCADA has allowed for more remote control of these processes, less manual interaction and control, and more advanced functionality, which helps to ensure a quality finished product.
If you have any questions about SCADA applications, add them in the comments below and we will get back to you in less than 24 hours.
Got a friend, client, or colleague who could use some of this information? Please share this article.
The RealPars Team
You might want to review 3 of our other articles:
1) What is the difference between SCADA and HMI?
2) What is SCADA? (Supervisory Control and Data Acquisition)
3) What are the Differences between DCS and SCADA?