In this blog post, I want to talk about Analog Automation and things that may be processed with this method of production but first, I would like to refresh your memory about Discrete Automation. In a previous lesson, I discussed the different aspects of discrete automation and what may be produced while using this process.
This method of Industrial Automation is used to create items that may be countable or perhaps something that may be manufactured and then used, with other parts, to produce a final product, which can also be measured.
The analog automation method is different in that while the final product may be countable, such as a carton of ice cream or package of cookies, the process to create these items is considered Analog Automation because of the way the manufacturing takes place.
In analog automation, ingredients are treated and blended to create the final product. As with discrete automation, the manufacturing of a product doesn’t necessarily have to be done in one process.
Take ice cream for example. Company A may combine heavy cream, half and half, egg yolks, sugar, and salt into a cooking vessel to make an ice cream base.
This base may then be shipped to company B that will combine it with flavors such as vanilla, strawberry, or chocolate.
While the ingredients of the completed product were made separately, the final product was treated and blended to create ice cream.
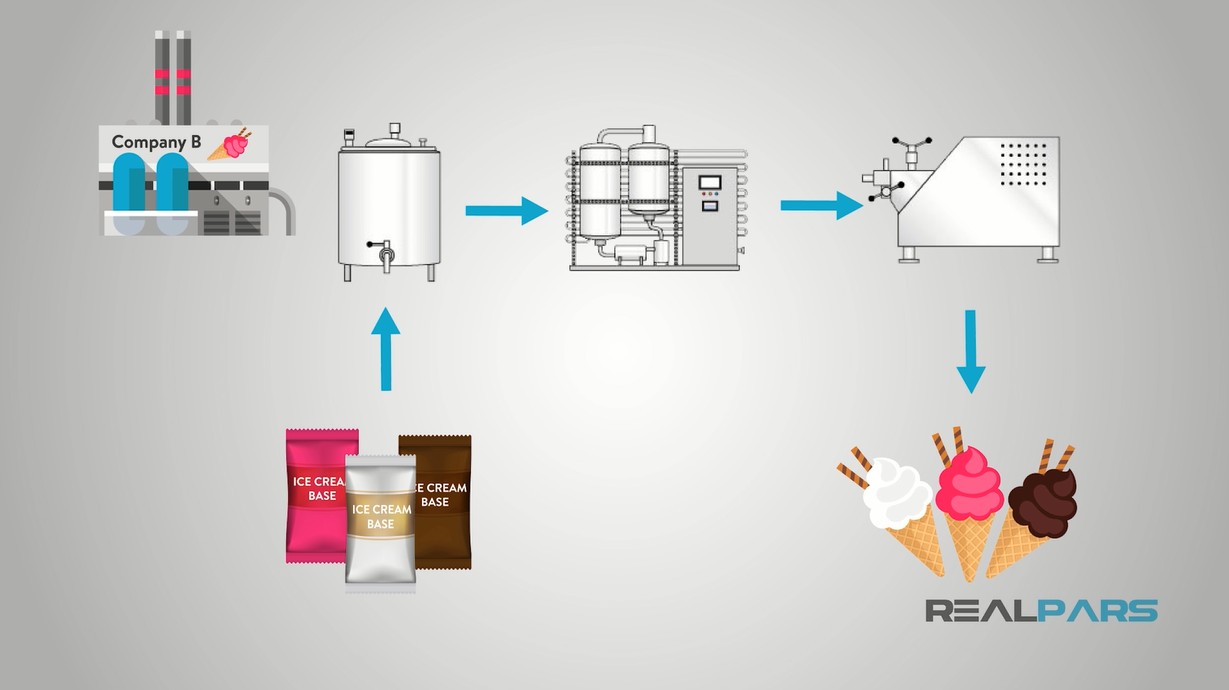
This is just one of many examples. Let’s take a more easily explained procedure to demonstrate an analog automation process. I’ll talk about a possible water treatment process to further explain this concept.
The first thing that is needed for our water treatment plant is water. Let’s say that our treatment plant has a few water sources which are a reservoir, a lake, and some underground wells.
Well obviously you don’t want to drink water straight from a reservoir and the thought of drinking a little lake water would frighten most snobbish fish and certainly most humans. These water sources need to be cleaned and disinfected, not only because we prefer it but also because law typically mandates it.
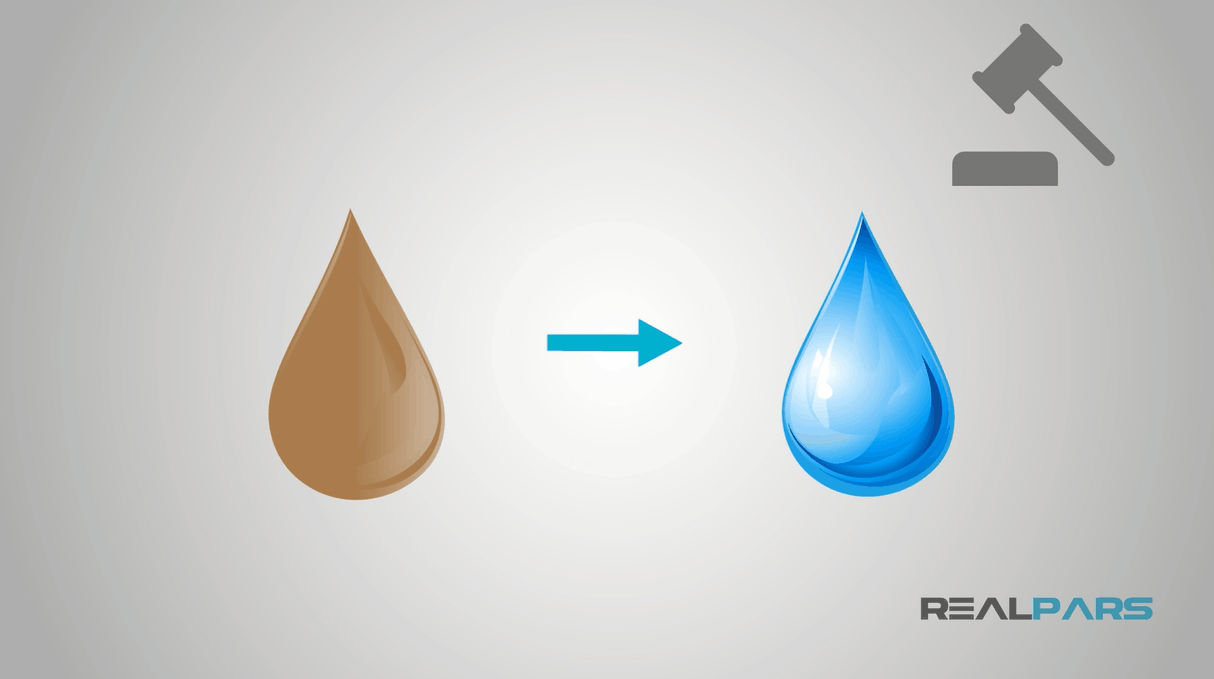
We’re bringing water, into the plant, that is not so desirable and the first thing we want to do is remove the “big stuff”. There may be leaves, sticks, trash, or even small fish or other animals in the water and the first line of defense to remove these things may be some sort of straining system.
Once the water exits the strainer system, it may enter a process of rapid mixing where it would be treated to balance the pH, if needed, as well as add specific chemicals that would make the particulates in the water stick together and form a substance of larger particulates called floc.
The floc may then be pumped to a basin where everything is slowed a little and the floc is allowed to grow even larger. After the floc has had time to develop, it may then be pumped to another basin where it is allowed to settle.
This process would allow the large floc to settle to the bottom of the basin and be removed while the top of the water would flow out of the basins to some sort of filtration system.
The filtration system typically consists of gravel, sand, and a type of coal called anthracite. As the water travels through these levels of media, smaller particles and organisms are removed from the water.
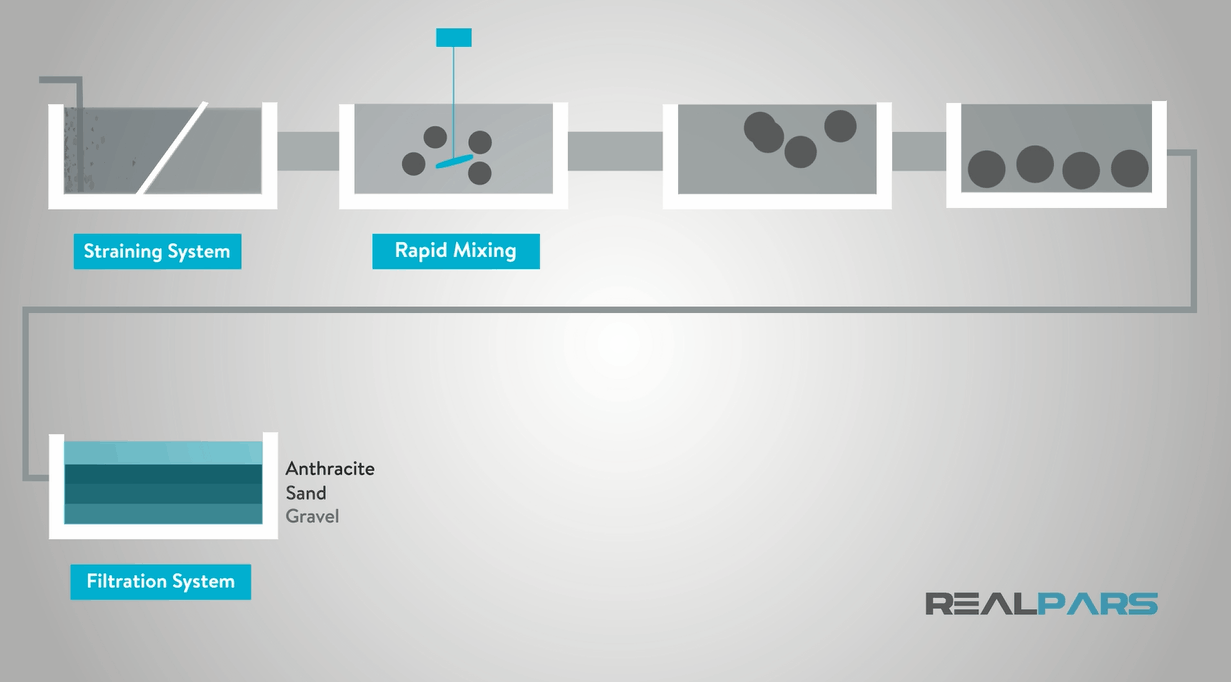
The water may then travel to a disinfection system. This system may be as elaborate as another type of filtration system such as membrane, UV, reverse osmosis, ozone, or any other type.
The disinfection process is determined widely by what the water quality is and the challenges for particle and organism removal. Are there bacterial or virus concerns, does the water small or taste particularly bad, those are the sorts of issues that may require additional treatment.
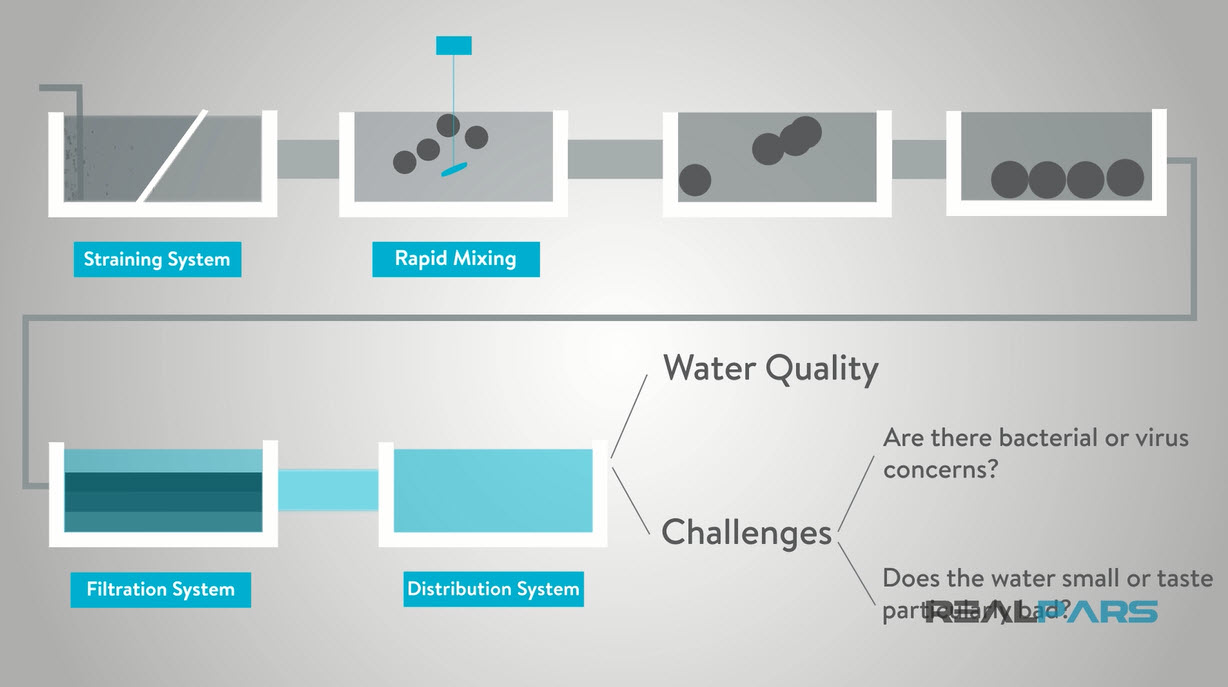
If the challenges are minimal, the disinfection may be as simple as adding chlorine to the water to ensure all remaining organisms are removed. Government typically mandates that there is some sort of residual chlorine remains prior to the water traveling to the distribution system.

Once the water has been properly disinfected it may travel to a holding reservoir that is used to store the finished product or the water may then be pumped to travel through distribution lines that lead into the city that requires it.
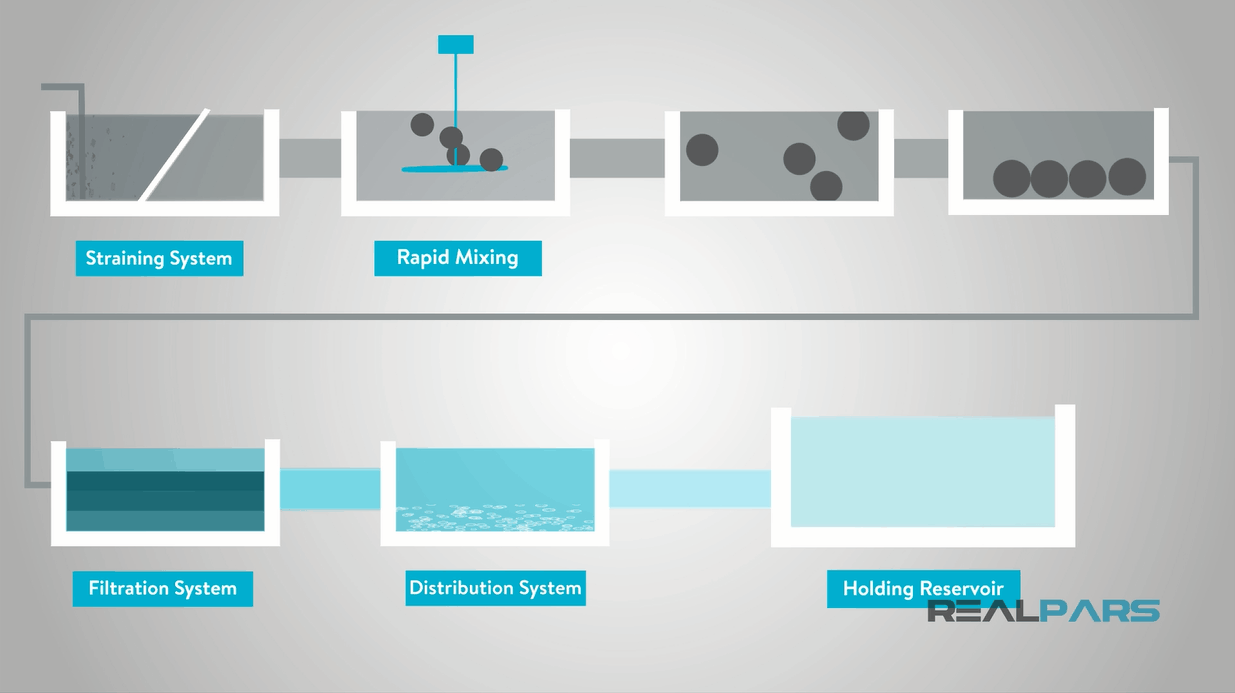
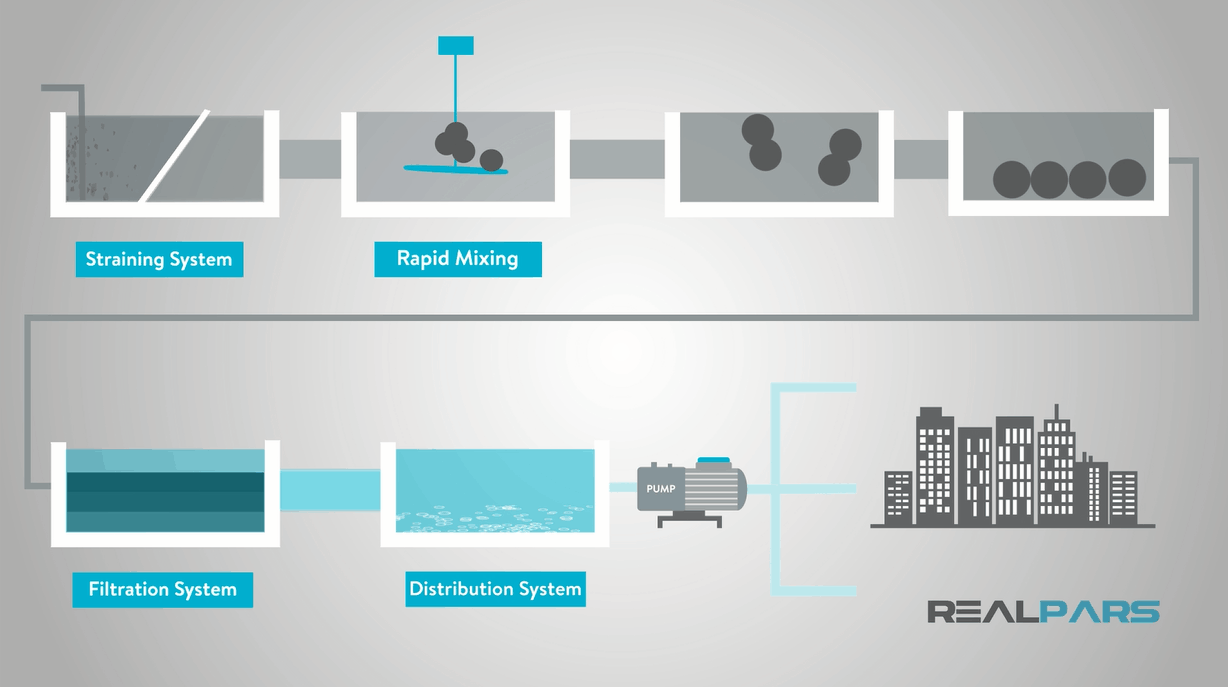
Other examples of analog automation are the continuous stream of gas and oil, pulp and paper, chemicals, and that sort of thing.
While most of these products can be measured in some sort of way, a gallon of gas, a quart of oil, a drum of chemicals, again this doesn’t necessarily qualify them as discrete automation because of the way that the process is handled.
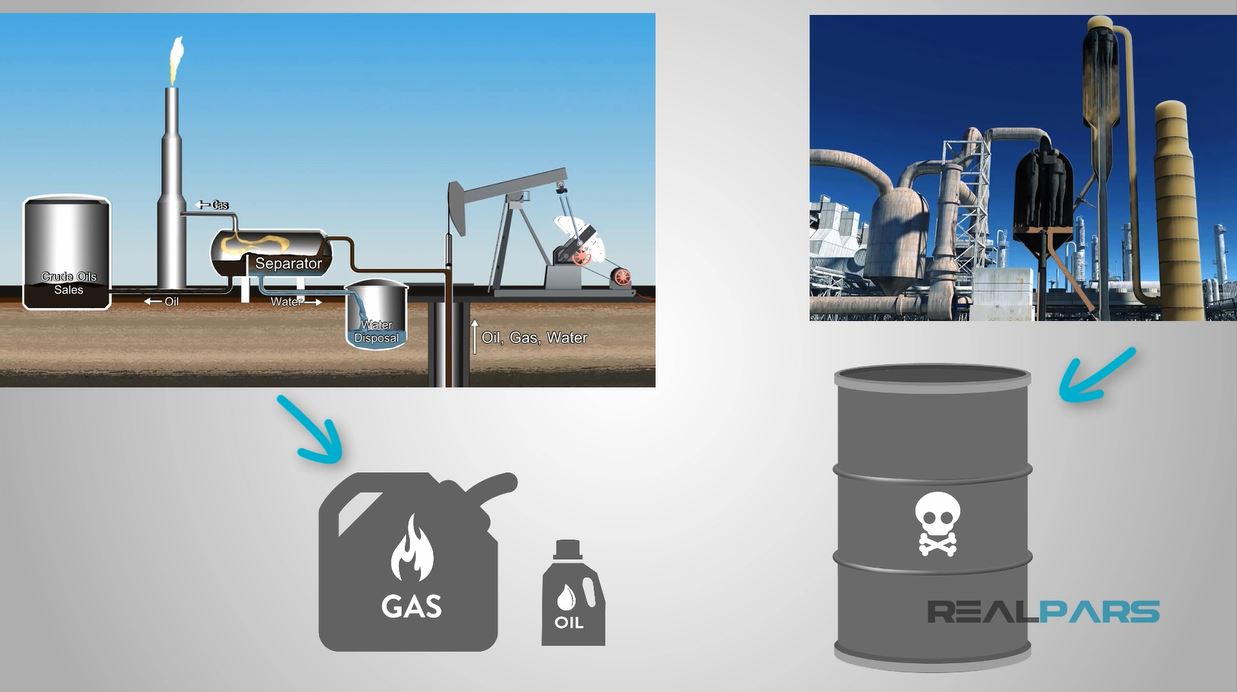
The creation of a widget that ships to a company is much easier to quantify than a water treatment product. The definition of an analog automation process is more about what happens to produce the end result. Analog automation is about treating and blending things while discrete automation is more about assembling different components to create a final product.
As I iterated in the discussion about discrete automation, starting and stopping of an automation process can be done in either discrete or analog automation.
However, the starting and stopping of a discrete process is as easy as stopping a machine. The starting and stopping of an analog automation process requires not only careful planning but also advanced preparation.
For instance, in order to stop a water treatment plant the city must first determine where the water that the city needs will come from. If there aren’t many possibilities of other city treatment plants to furnish the water then the city may consider some short term option such as filling all storage reservoirs to capacity and ensuring that the shutdown time is monitored and production is resumed in a relatively short time.

Let’s say that this is the option that the plant has chosen to take. They would first have to stop the influent plant flow. This may or may not be easy. If the plant has some motorized valves, they could command those valves to close and begin the shutdown process.
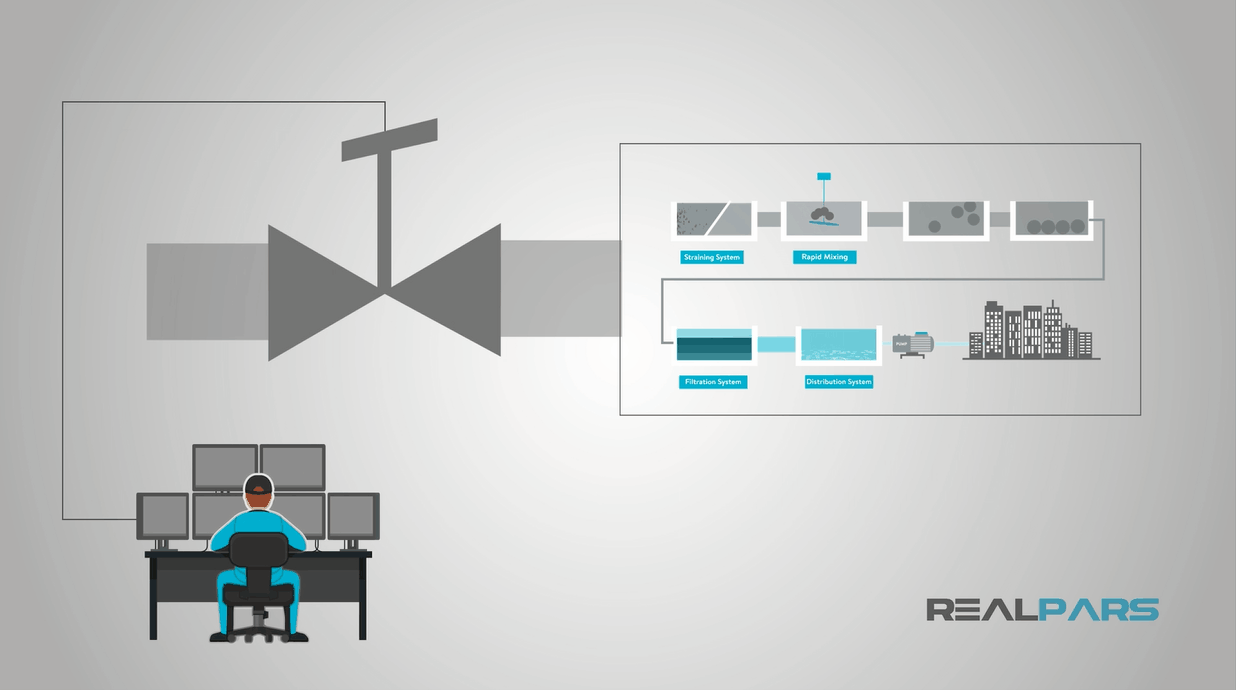
If they did not have the motorized valves, the staff would have to travel to the location of the influent valve and manually close the valve. While this may sound relatively easy, some of these valves are on pipes that may be 96 inches in diameter. That indeed would be a very large valve to manually crank until it was fully closed.
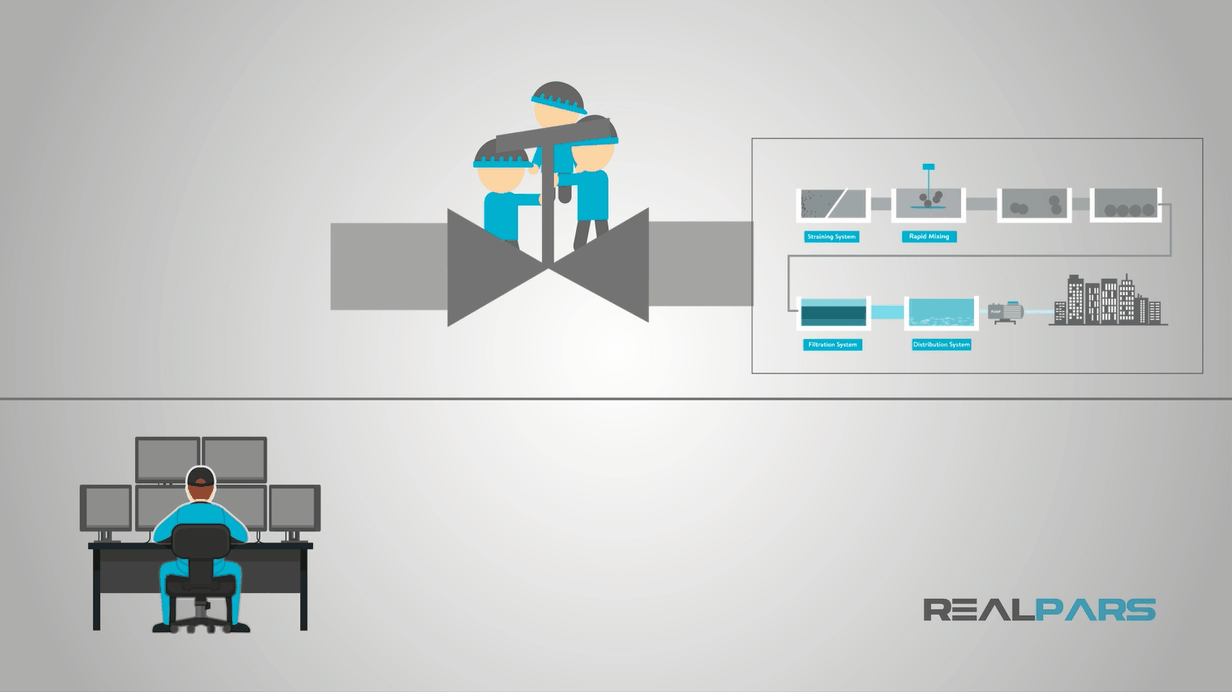
With that chore out of the way, the staff will then have to stop the addition of all chemicals as well as possibly drain the rapid mix basin. The reason for draining the basin would be that the floc would settle to the bottom of the basin and cause many problems for pumping to the next station as well as equipment impact considerations.
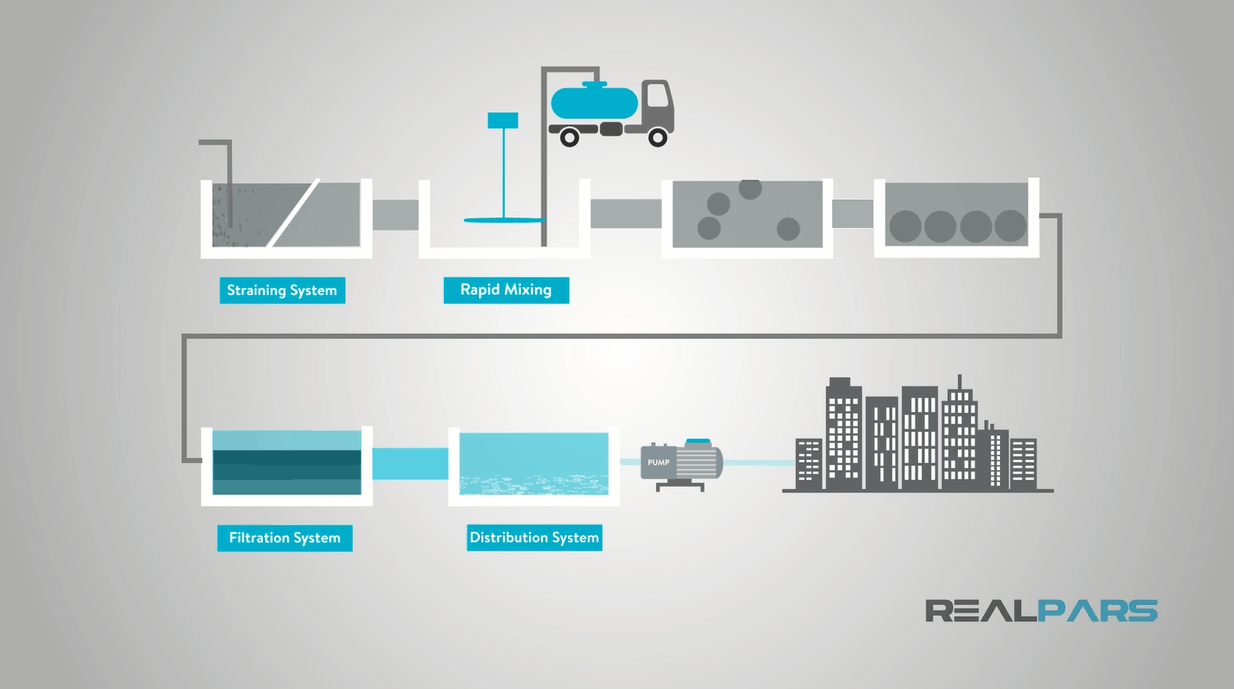
Of course, if they have to drain that basin, they may have to drain the downstream basins as well for the same reasons. The filters would need to be drained as the stagnant water sitting in the filter would create an environment for breeding algae and other undesirables.
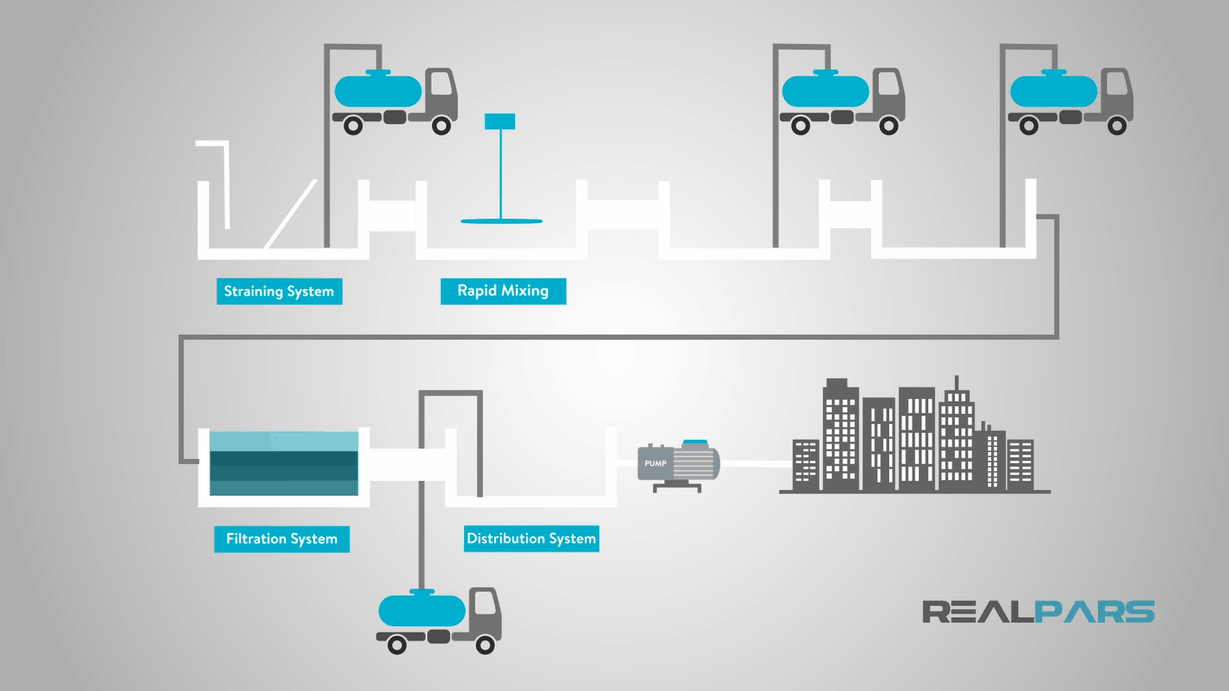
In other words, all of the processes that it takes to treat water are affected by both short and long term shutdowns. As you can imagine, the shutdown ramifications may be much greater with the analog automation method than they are with discrete.
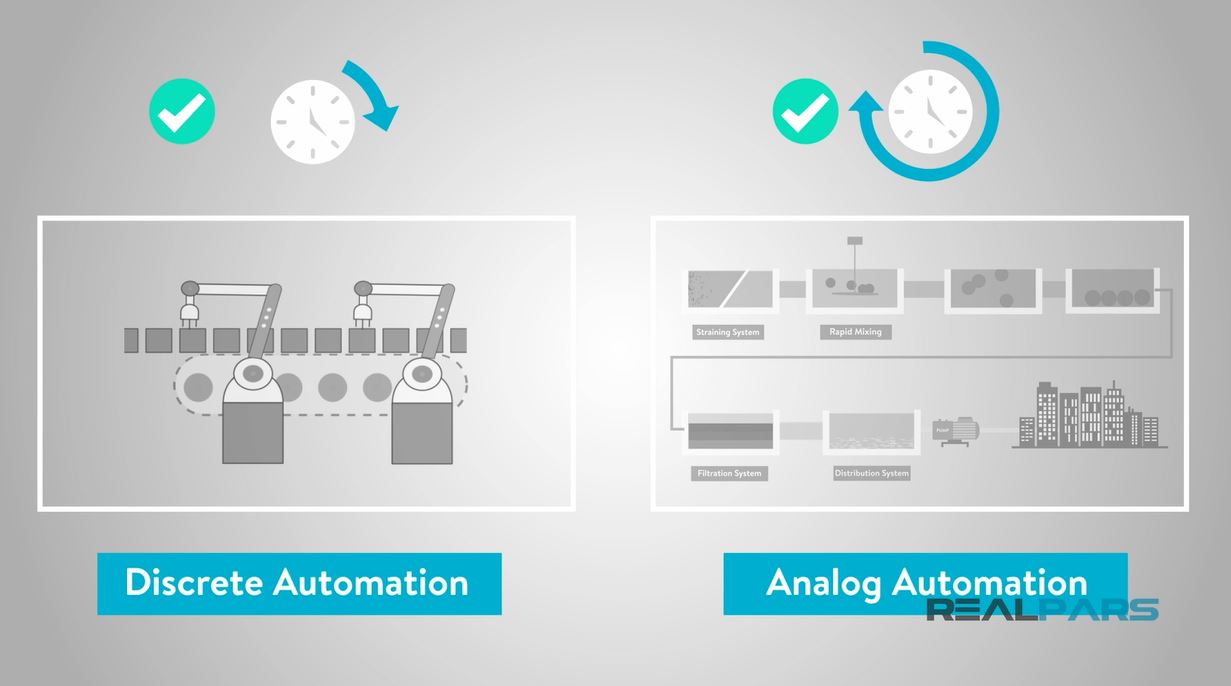
Thank you so much for your valuable time visiting our website. Leave a comment to let us know what you think and make sure to subscribe to our newsletter to get the latest content first.
With endless love,
The RealPars Team