In this article, we are going to discuss differential pressure transmitters. Simply put, a differential pressure transmitter is a device that measures two opposing pressures in a pipe or vessel. How do pressure transmitters work?
To understand how a differential pressure transmitter works, we need to know some principles of pressure.
Pressure Principles
Pressure is the result of force applied onto a unit of area.
In the case of fluid and gas, this area would be the inside of a pipe, tank, vessel or other sealed housing.
Since pressure is a physical quantity, it can be measured.
Pressure is measured in one of the following five units.
– Pascal
– Bar
– Standard atmosphere or atm
– Torr
– Pounds per square inch or psi
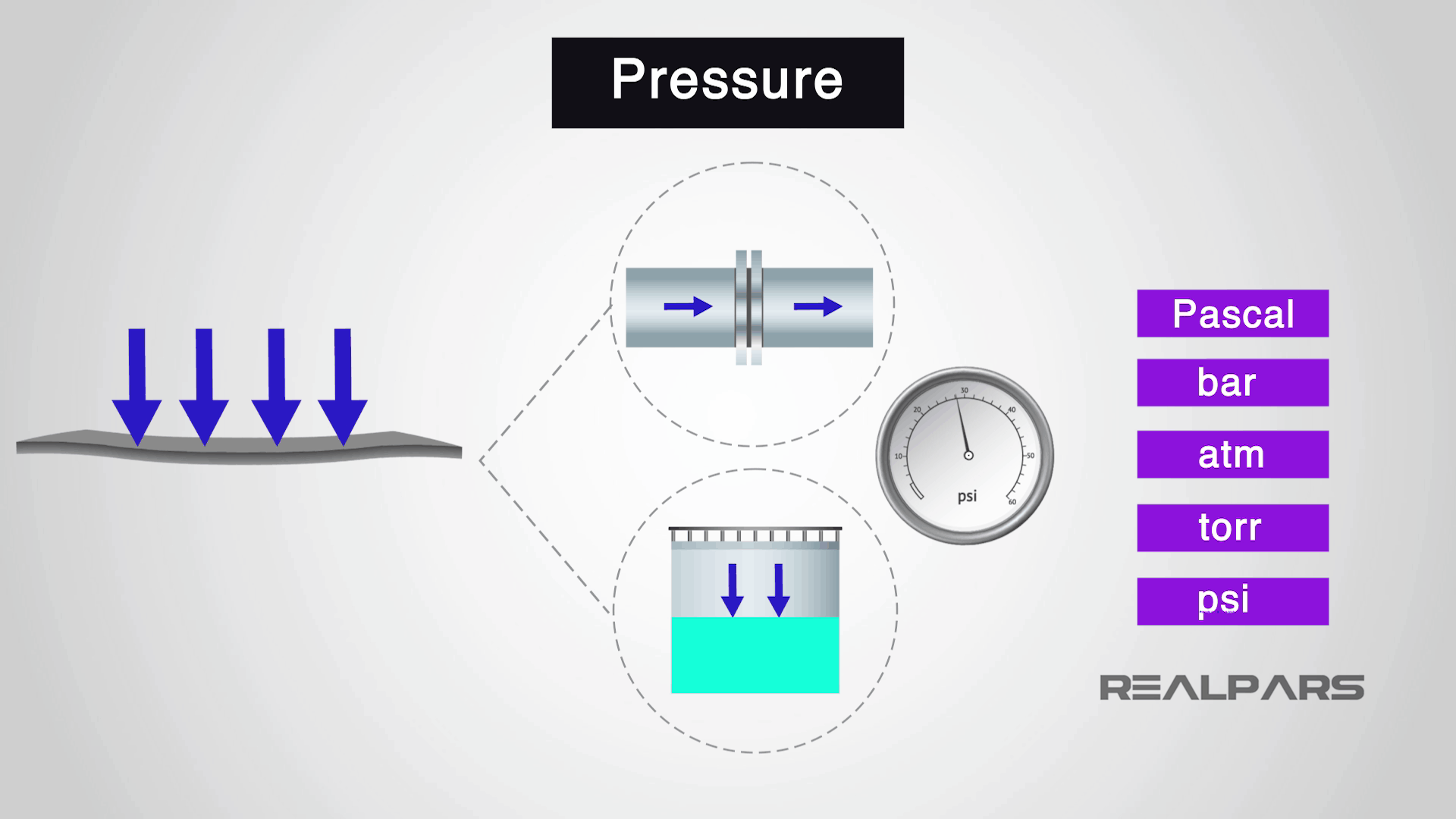
Common Industrial Units of Pressure
The most commonly used measurements of pressure in an industrial fluid and gas processing environment are bar and psi.
One bar is the equivalent of the earth’s atmosphere at mean sea level.
A pound per square inch is the force of one pound on an area of one square inch.
You will most likely use these units of measurement in your work as they are commonly used and almost every manufacturer of pressure measurement devices calibrate them to these units of measurement.
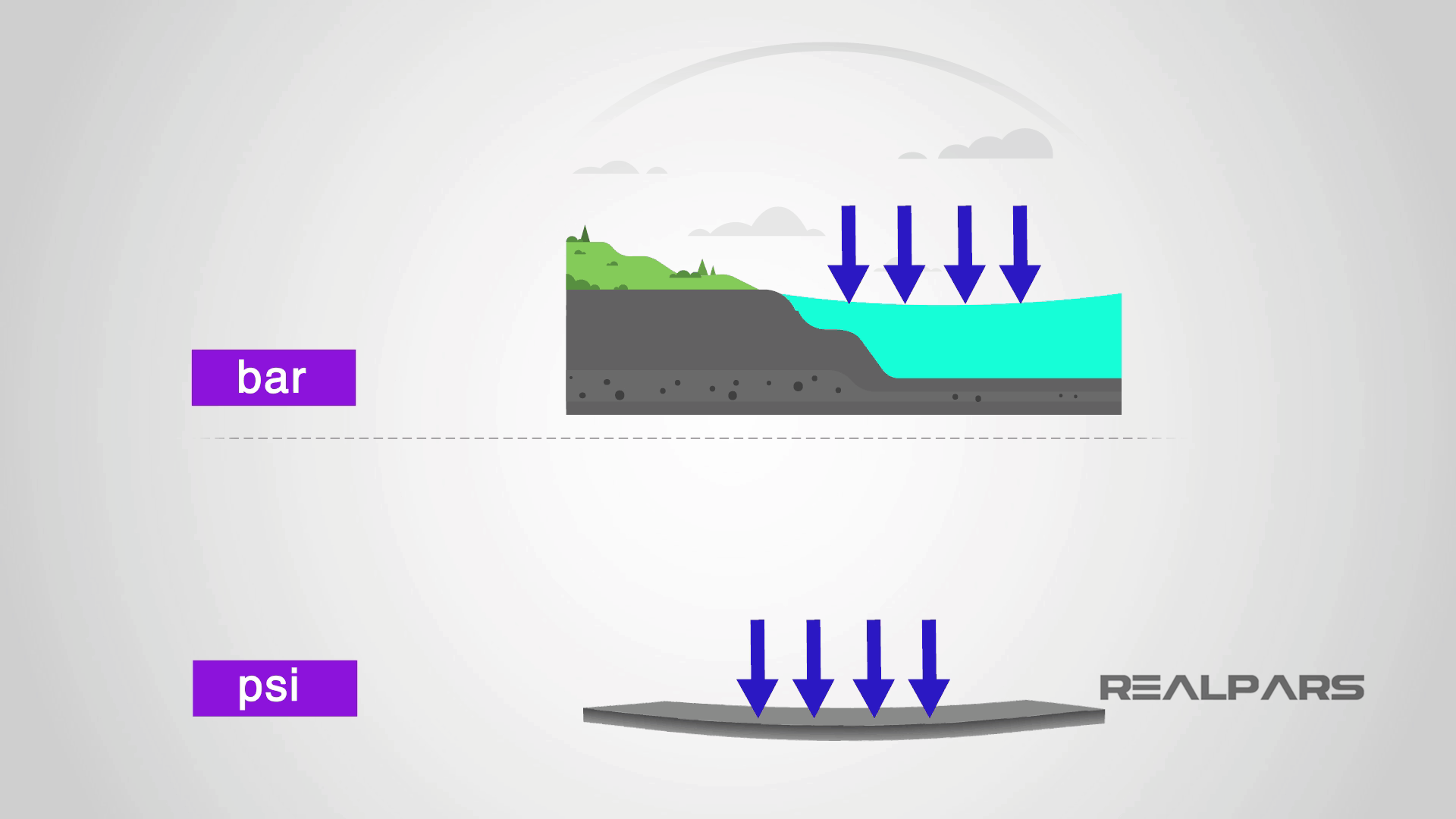
How Does a Differential Pressure Transmitter Work
Now that we know a little bit about pressure, let’s discuss how a differential pressure transmitter actually measures pressure and tells us what the pressure is.
From now on in this lesson, we are going to use the terminology that is utilized in the industry when we talk about differential pressure transmitters. Delta-P or DP is the industry-standard term for the measured differential pressure.
Delta, meaning change in, and P meaning pressure.
In addition, most people will simply call a differential pressure sensor a DP sensor or transmitter.
From now on, we will refer to these devices as DP transmitters.
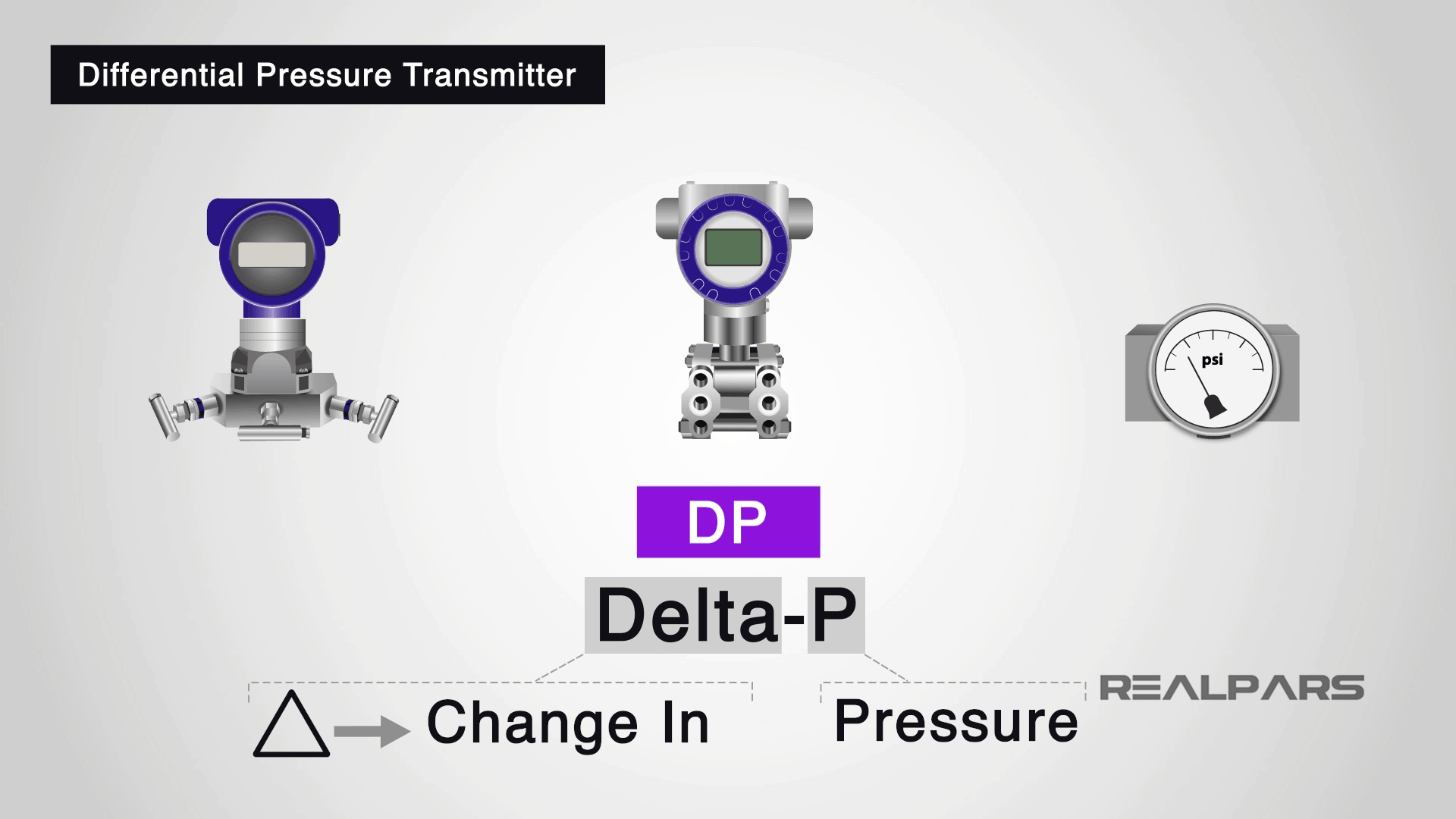
Differential Pressure Transmitters Elements
A DP transmitter is a pressure-measuring gauge or an electrical device that uses two elements to measure the differences of pressure in a sealed container such as a pipe. DP transmitters will have
– A primary element
– A secondary element
– An electronics housing
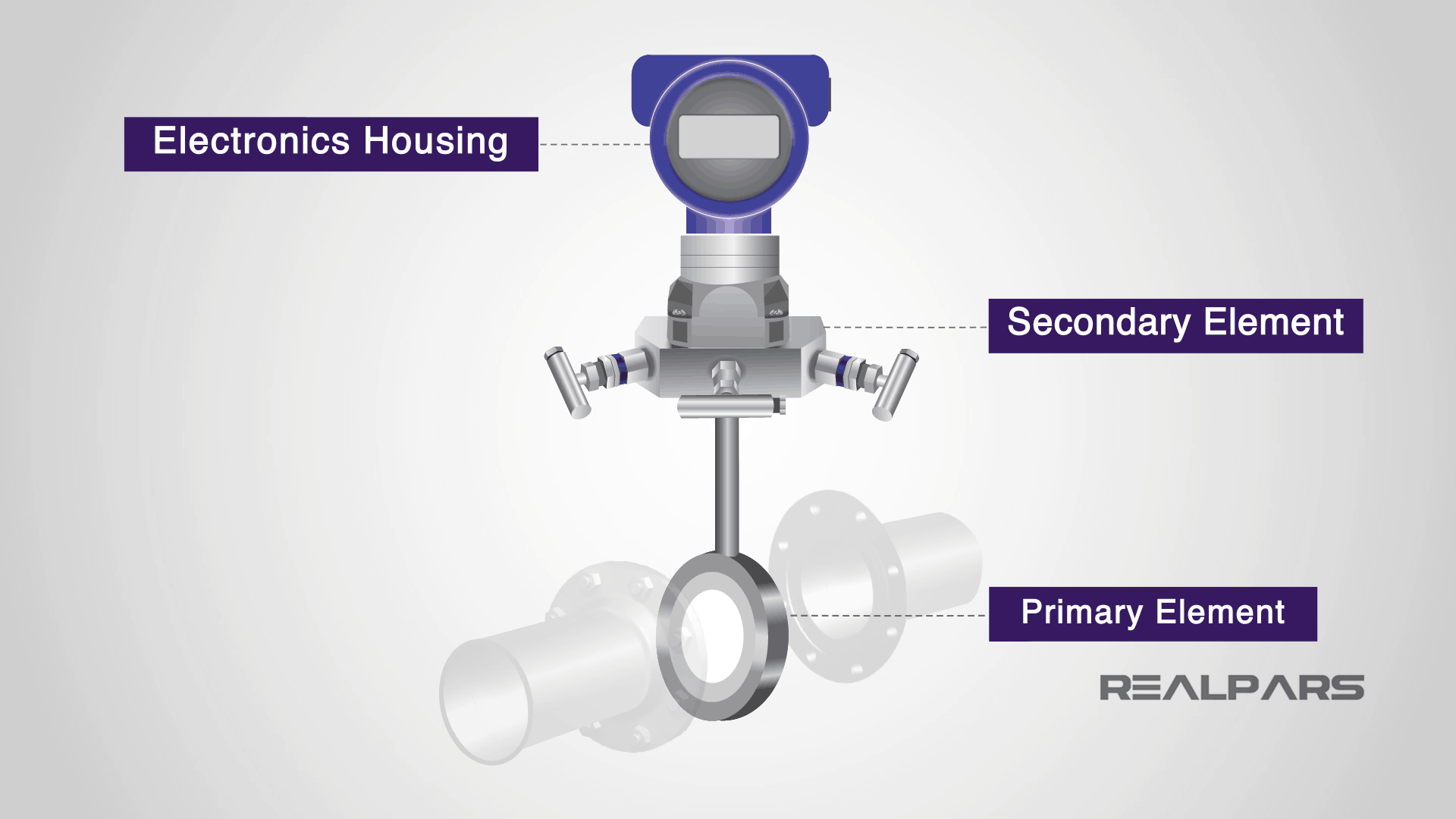
Differential Pressure Transmitters Primary Elements
The primary element will produce a difference in pressure as the flow in the pipe increases.
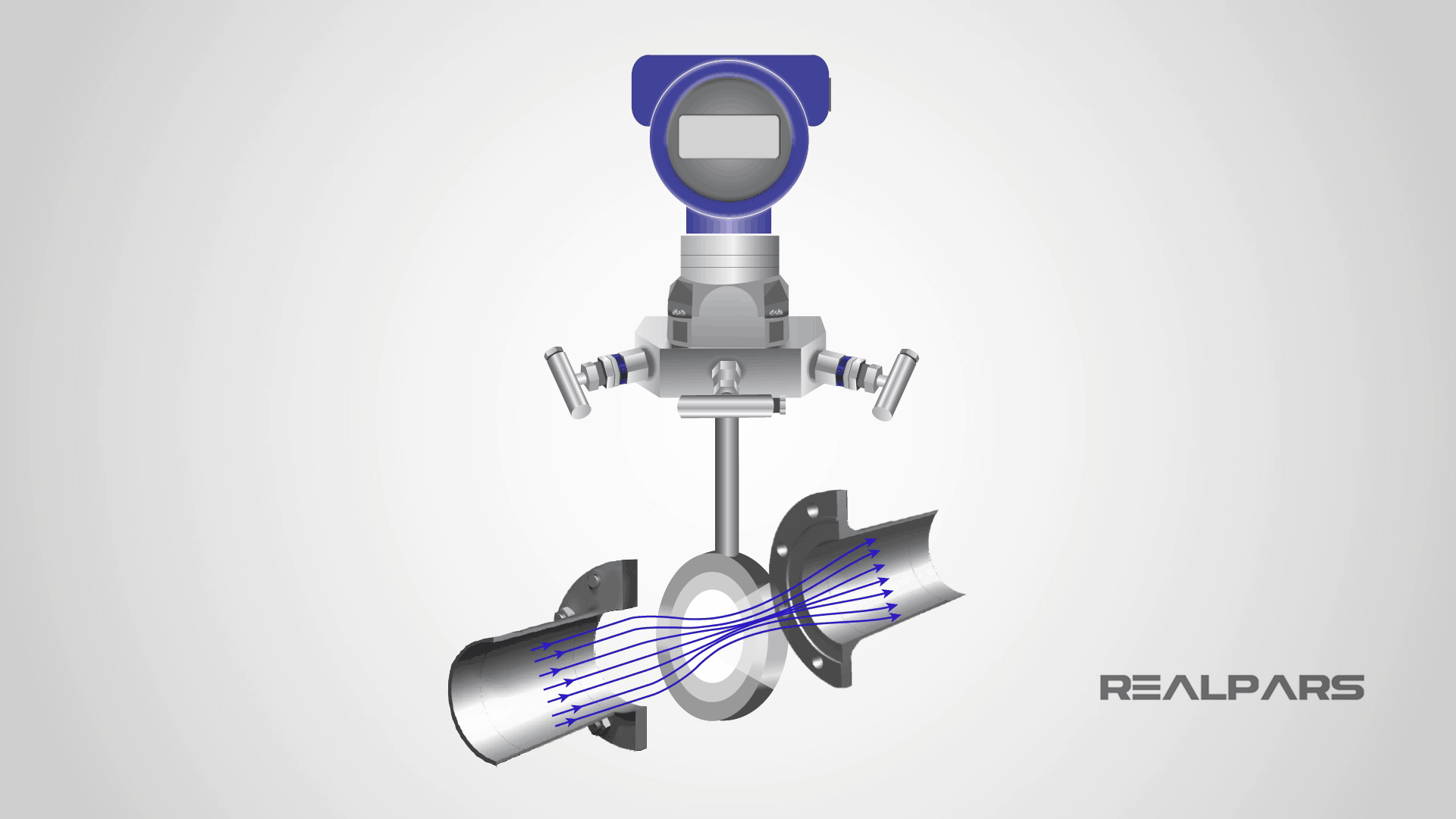
Different Types of Primary Elements
Different types of primary elements include
– Orifice plates
– Venturi tubes
– Pitot tubes
– Flow nozzles
– Laminar flow elements
– Wedge elements
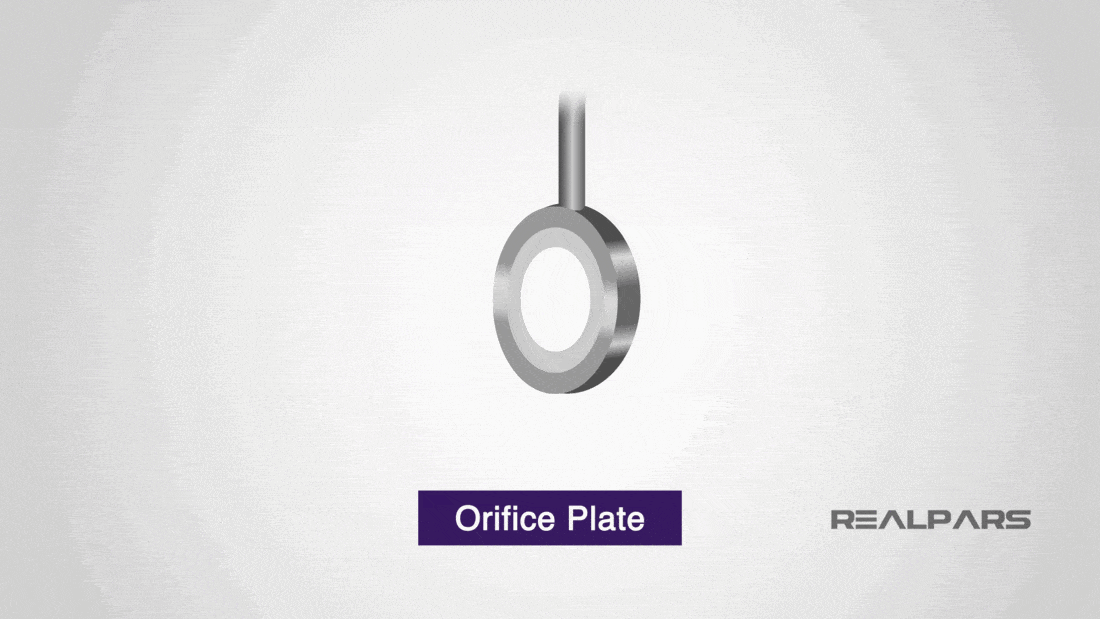
Differential Pressure Transmitters Secondary Elements
The secondary element will measure the difference of pressure produced by the primary element as accurately as possible.
The primary element is sometimes called the high side, and the secondary element is called the low side.
It is important to remember that the high side and low side aren’t always on the respective high and low-pressure sides of the pipe.
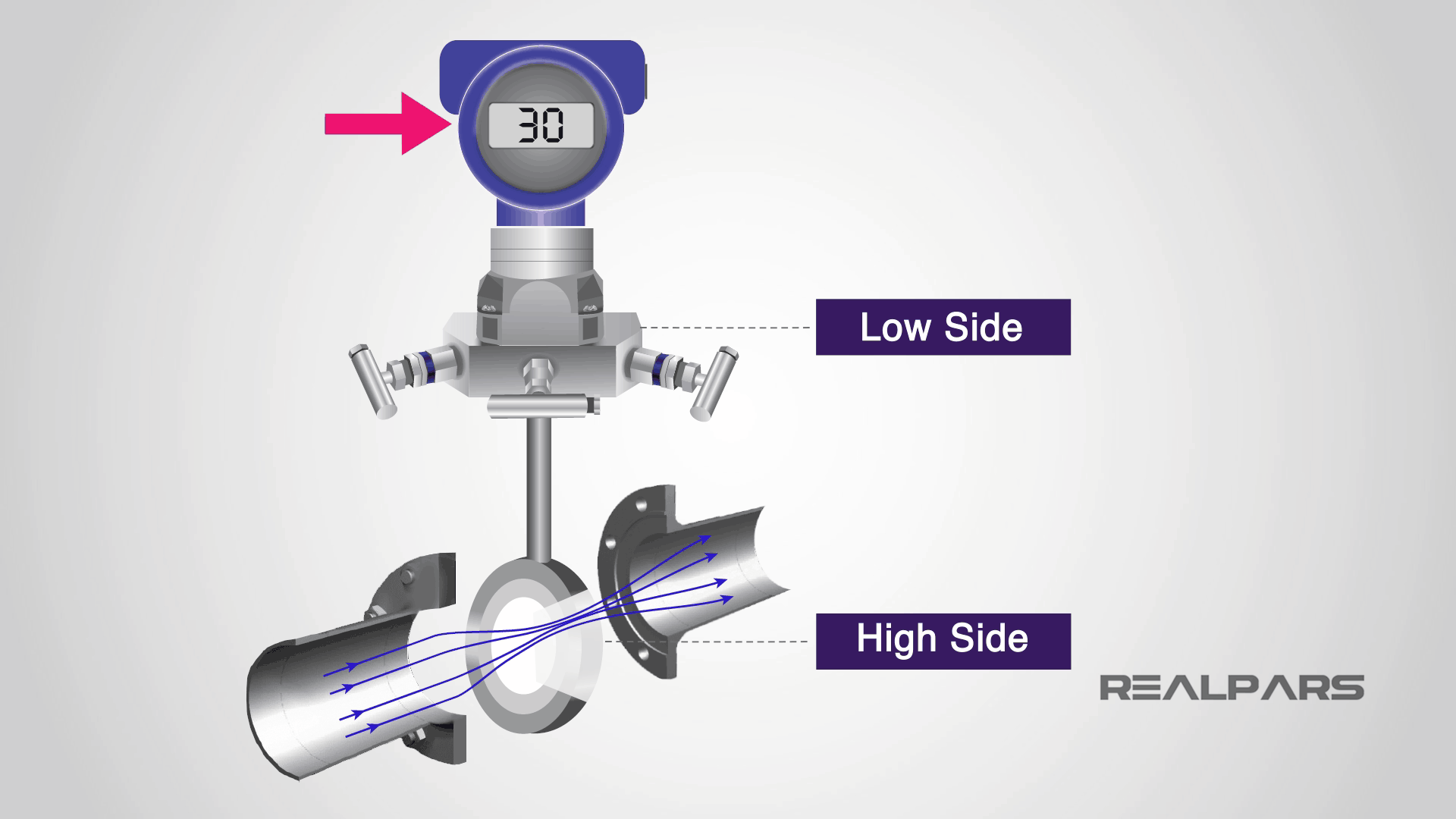
Sealed Diaphragm in a Differential Pressure Transmitters
The elements in a DP transmitter will have sealed diaphragms and one of several ways to convert the pressure applied onto the diaphragms into an electrical signal.
Different Types of Sensors in a Differential Pressure Transmitter
Sensors such as differential capacitance, vibrating wire or strain gauges are used to produce the electrical signal that will be sent to the electronics housing, where it is processed, converted and amplified into a current or voltage output that can be read by the control system.
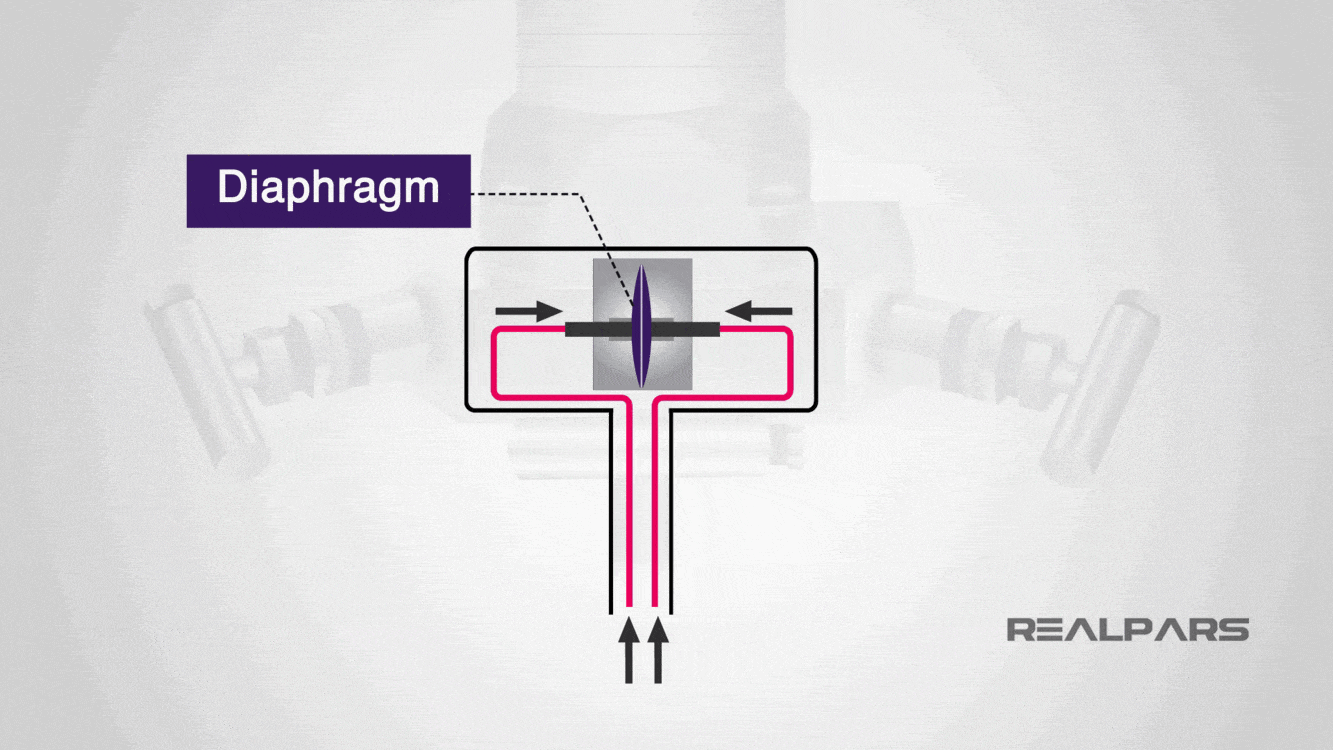
The Electrical Output of a DP Transmitter
The current output is commonly a 4-20 milliamp signal, or in some cases a 0 to 5 or a 0 to 10 volt signal.
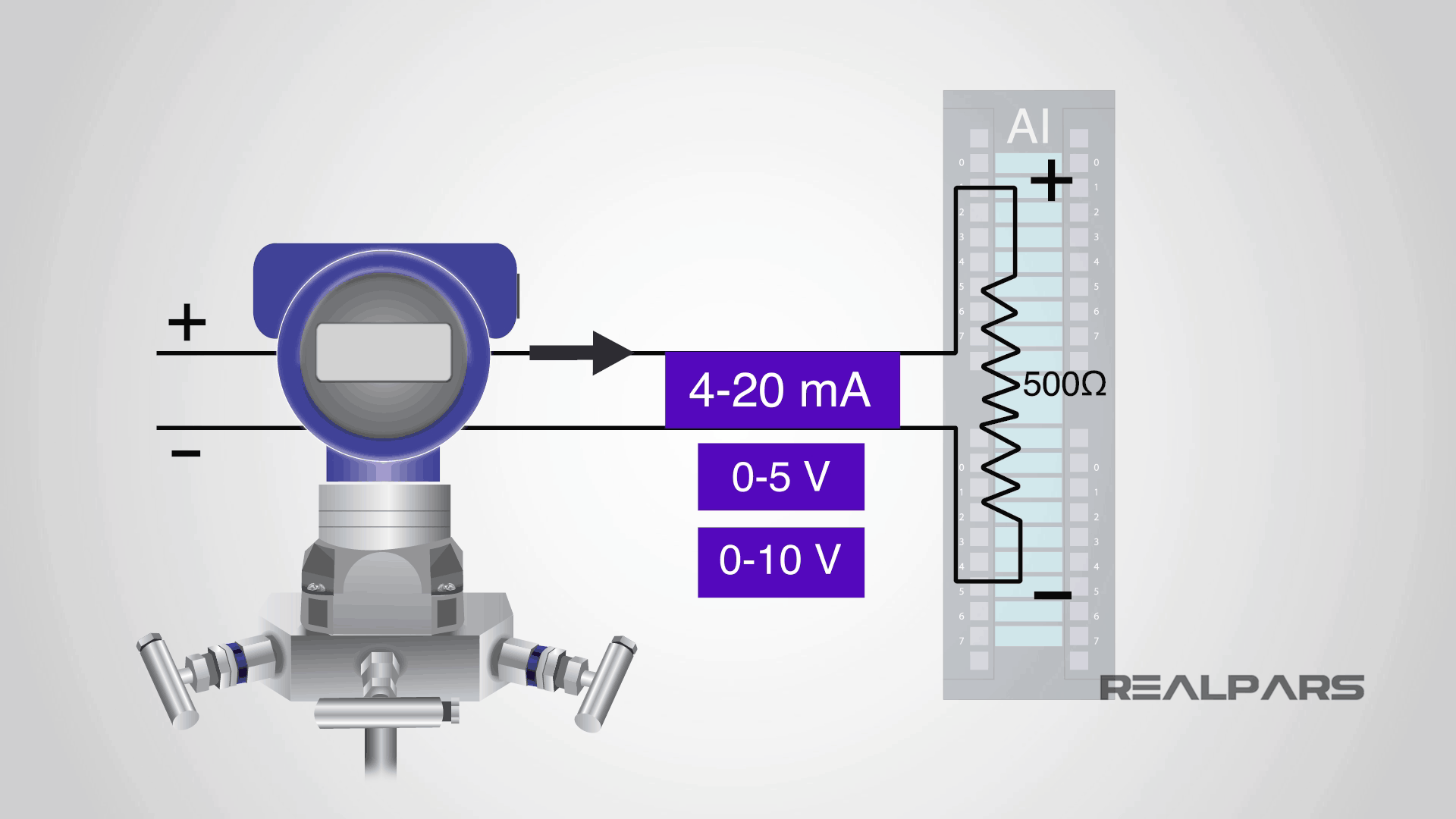
The electrical output generated by the DP transmitter electronic module is linear and proportional to the actual measured Delta-P.
Depending on the range of measured pressure, a 4 milliamp signal would equal a measured Delta-P of 0 psi and a 20 milliamp signal would equal the maximum measurable value. In this case, we’ll say that the maximum Delta-P is 100 psi.
Using these variables, we would know that a 12 milliamp signal would equal 50 psi Delta-P.
The relationship of the produced electrical signal to the units of measure is called the scaled output.
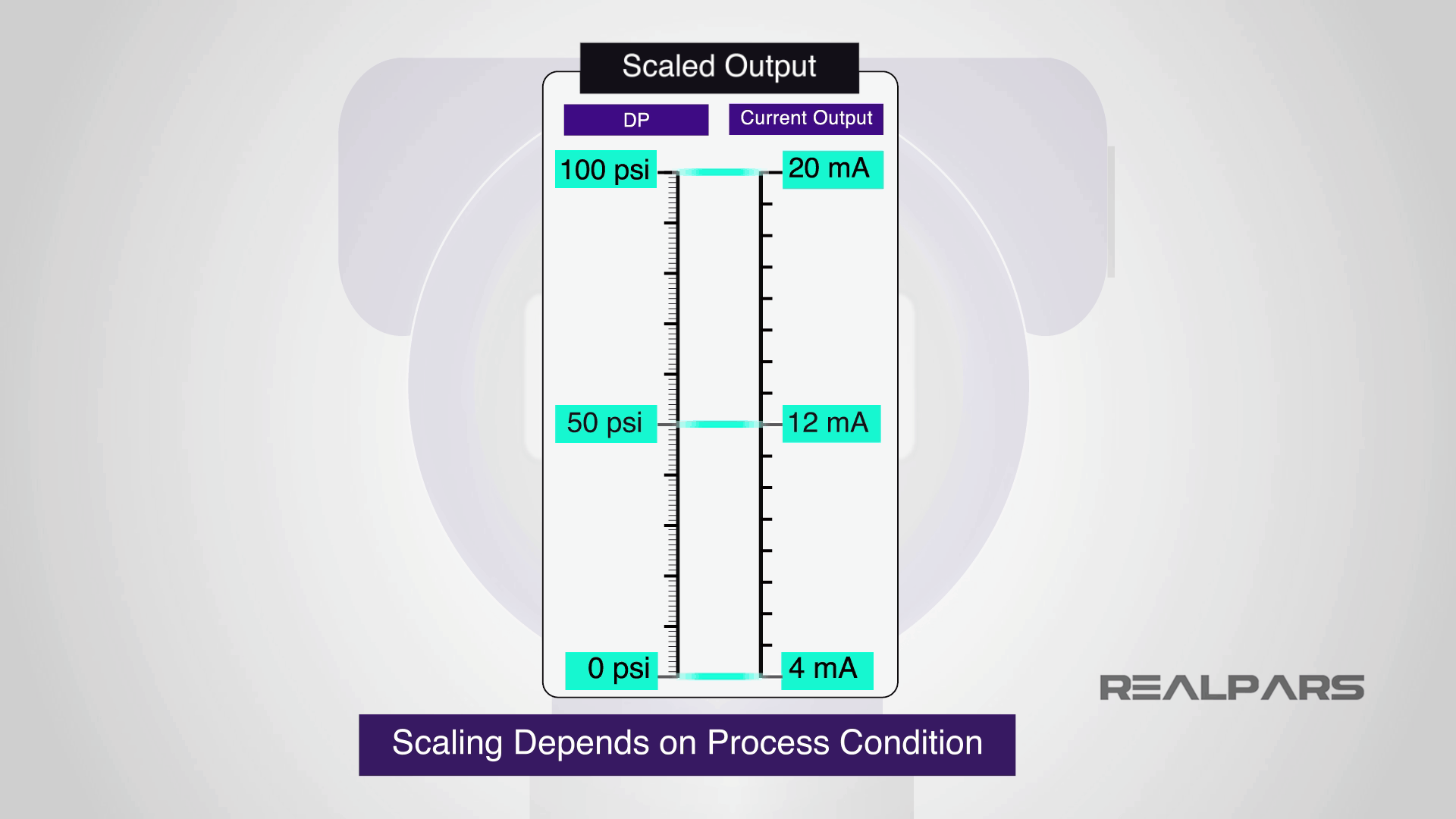
So, now that we know what pressure is and how a DP transmitter works, what is it used for? Well, the most common applications are for measuring level and flow.
Here we’ll discuss how a DP transmitter measures the flow of water in a pipe.
How Does a DP Flow Transmitter work?
One very common way of measuring flow using a DP transmitter is for the primary element to introduce a constriction in the pipe.
Using a restrictive element on the primary side will create a high and low pressure.
When the flow increases, more pressure drop is created.
As we remember, the secondary element will measure the difference in pressure created by the primary element.
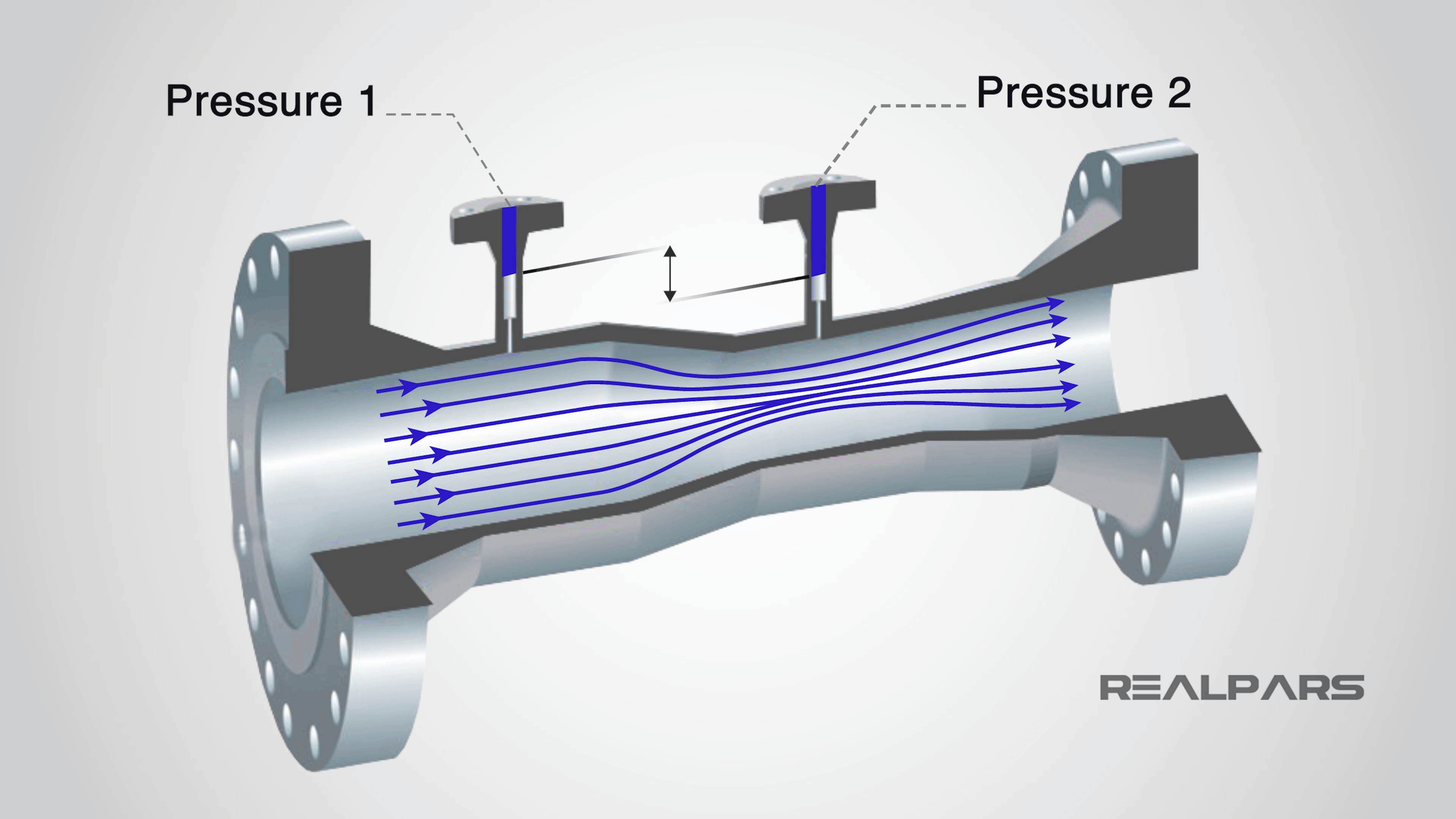
These measurements are sent to the electronics housing where the signal processing is done.
Bernoulli’s Equation
By using Bernoulli’s equation, which states that the pressure drop across the constriction is proportional to the square of the flow rate, the Delta-P is then converted into units of flow.
P1 + ½ ρv12 + ρgh1 = P2 + ½ ρv22 + ρgh2
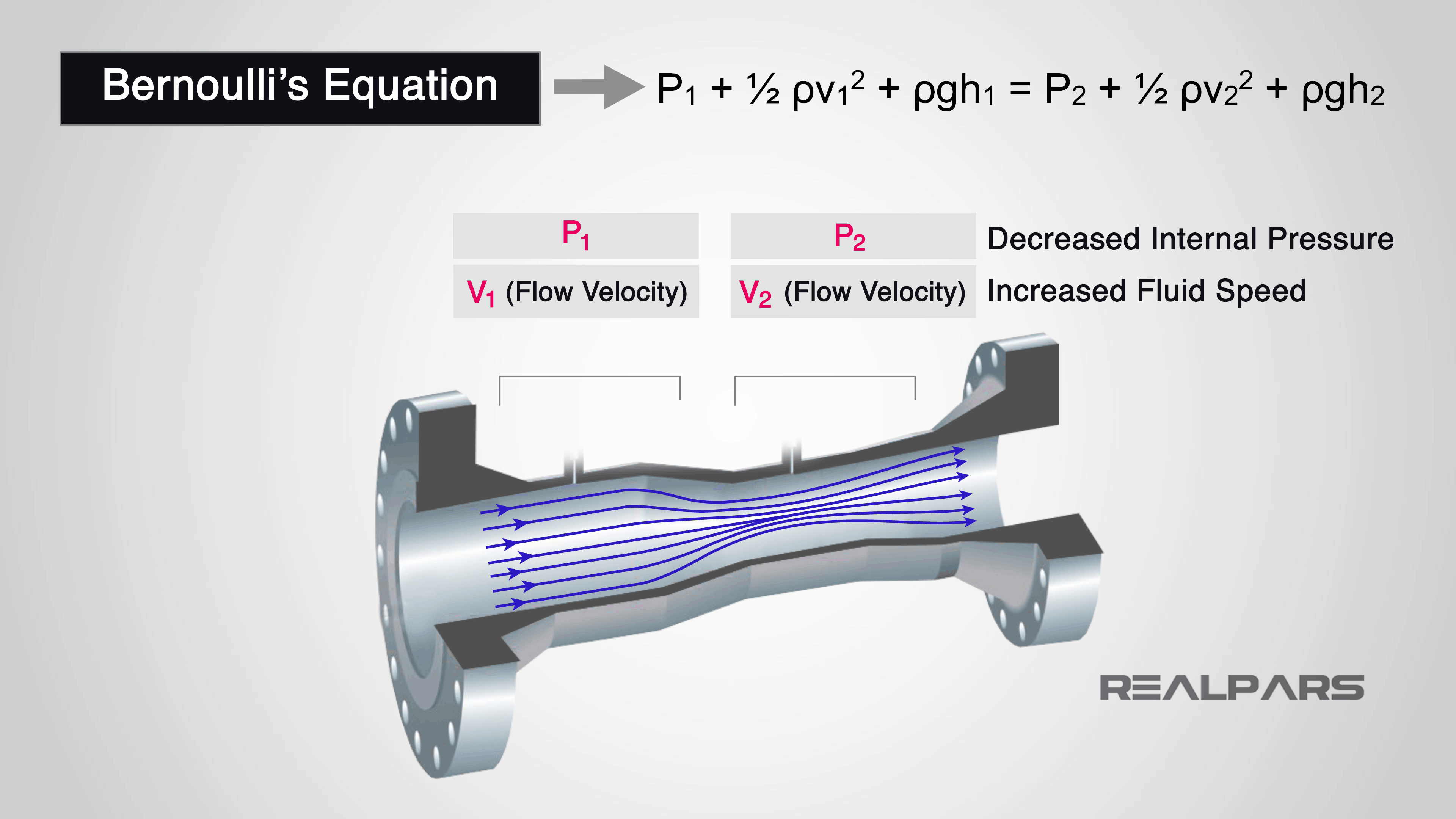
Flow Units
These units of flow can be gallons per minute (GPM) or cubic meters per hour (m³/h). Using DP transmitters as a method to measure flow works best on fluids that are relatively clean and of low viscosity.
Delta-P flow transmitter supports a small span or range which is why they are very commonly used in water and wastewater applications.
Summary
Now let’s go over what we have discussed.
A differential pressure transmitter is an instrument that can consistently and accurately create a pressure drop in a pipe and then use the pressure measurement on either side to provide the rate of flow within the pipe.
A differential pressure flow transmitter can be easily installed in many applications. Manufacturers today are providing a wide range of electronic outputs and protocols that are compatible with nearly any industrial control system on the market.
They are an efficient tool for measuring flow, and used in the right application will provide years of reliability and ease of maintenance. With a simple and reliable design, a long history of use across a broad range of industries, the differential pressure transmitter is sure to be in use for many years to come.
If you would like to get additional training on a similar subject please let us know in the comment section.
Got a friend, client, or colleague who could use some of this information? Please share this article.
The RealPars Team