In this article, we’re going to talk about Remote I/O vs Distributed I/O.
Depending on who you talk to, some say Remote I/O and Distributed I/O are the same thing and the terms are interchangeable … Not so says others.
So, who’s correct? Let’s investigate the history of the terms Remote I/O and Distributed I/O and discuss what they mean today.
Direct Digital Control or DDC system
Let’s go back a few decades to early computerized control. The predecessor of the DCS and the PLC was the Direct Digital Control or DDC system, only seen today in museums.
Many vendors such as Taylor Instruments, Bailey Control, and Foxboro had DDC systems that centered on a mini-computer connected to several proprietary I/O devices located at remote locations around the plant.
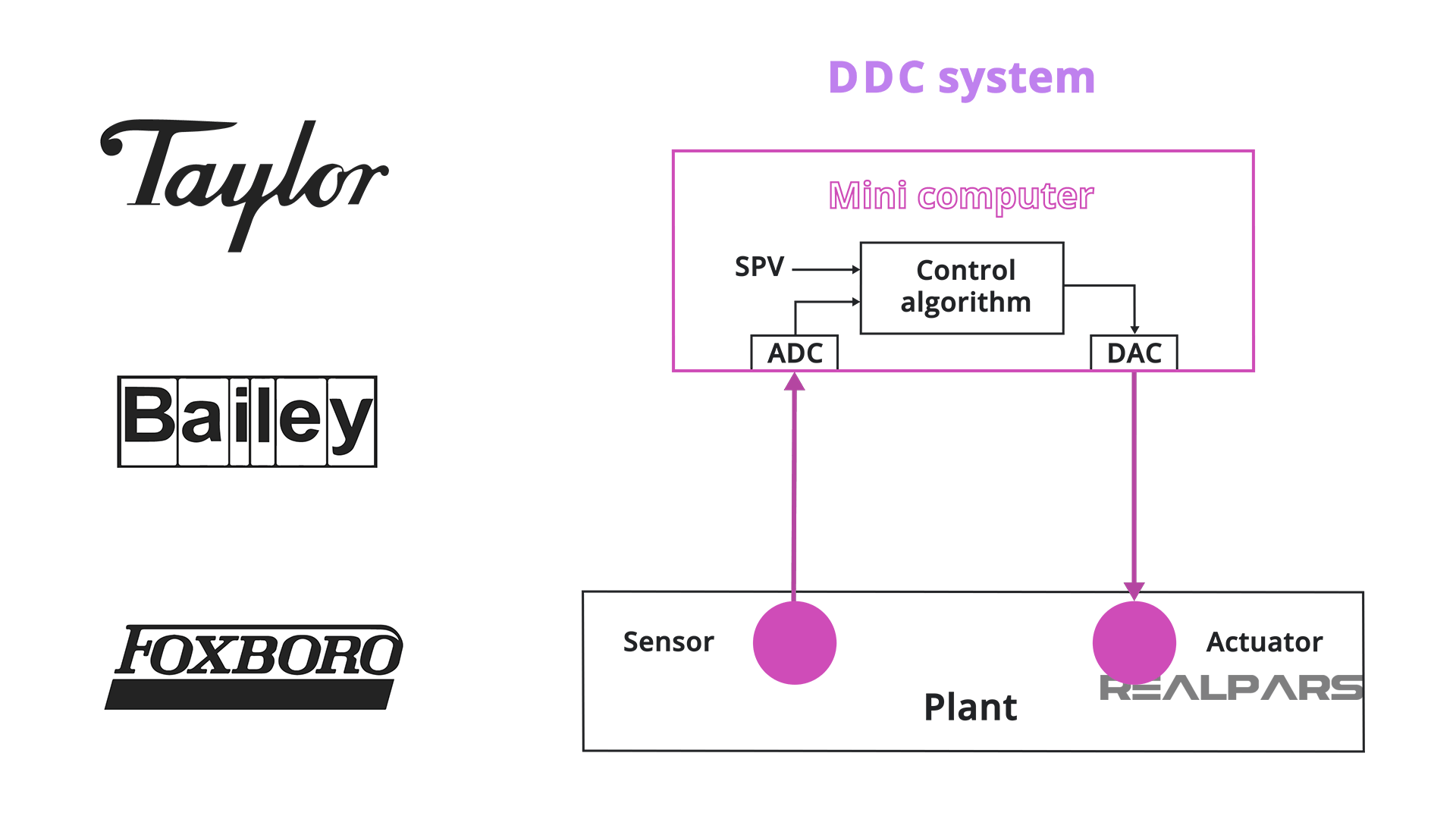
Remote I/O vs Distributed I/O
Remote and Distributed in the context of locations
Today’s DCS is a control system that has a number of Distributed autonomous controllers each operating a number of continuous operations. The controllers are tied together via a centralized supervisory controller.
We’ve already used the terms Remote and Distributed in the context of locations of both I/O and controllers. It’s easy to see how the terms can be misunderstood.
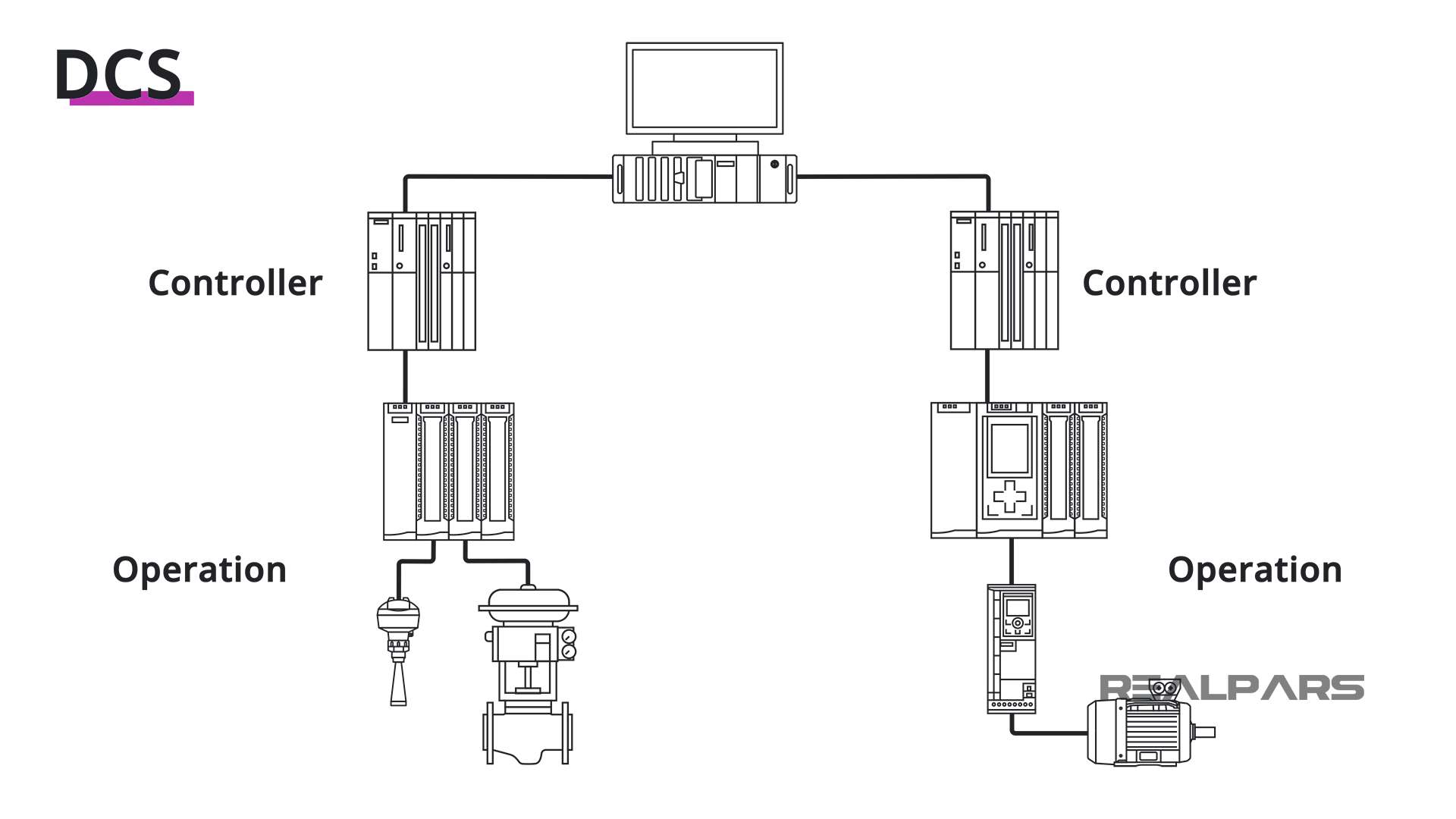
Remote and Distributed I/O from PLC perspective
OK. Let’s have a look at Remote I/O and Distributed I/O from a PLC perspective. Remote I/O means that the I/O module is at a remote place physically located a distance from the control PLC.
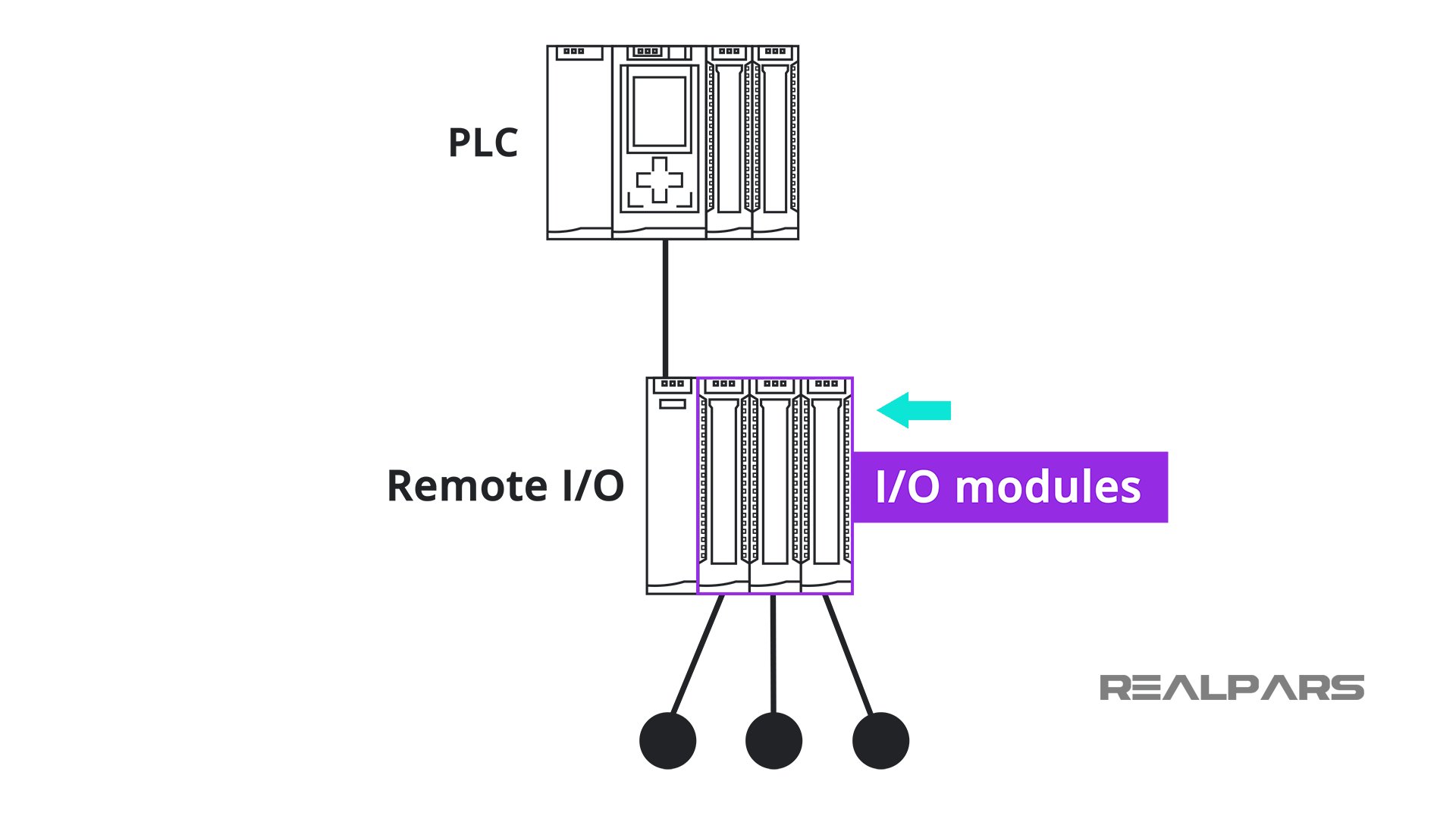
Distributed I/O has a brain
As we mentioned earlier Remote I/O is sometimes also referred to as Distributed I/O. Let’s look at a definition for Distributed I/O that differentiates it from Remote I/O.
Generally speaking, Distributed I/O has a brain or some computing capacity. By default, it is Remote.
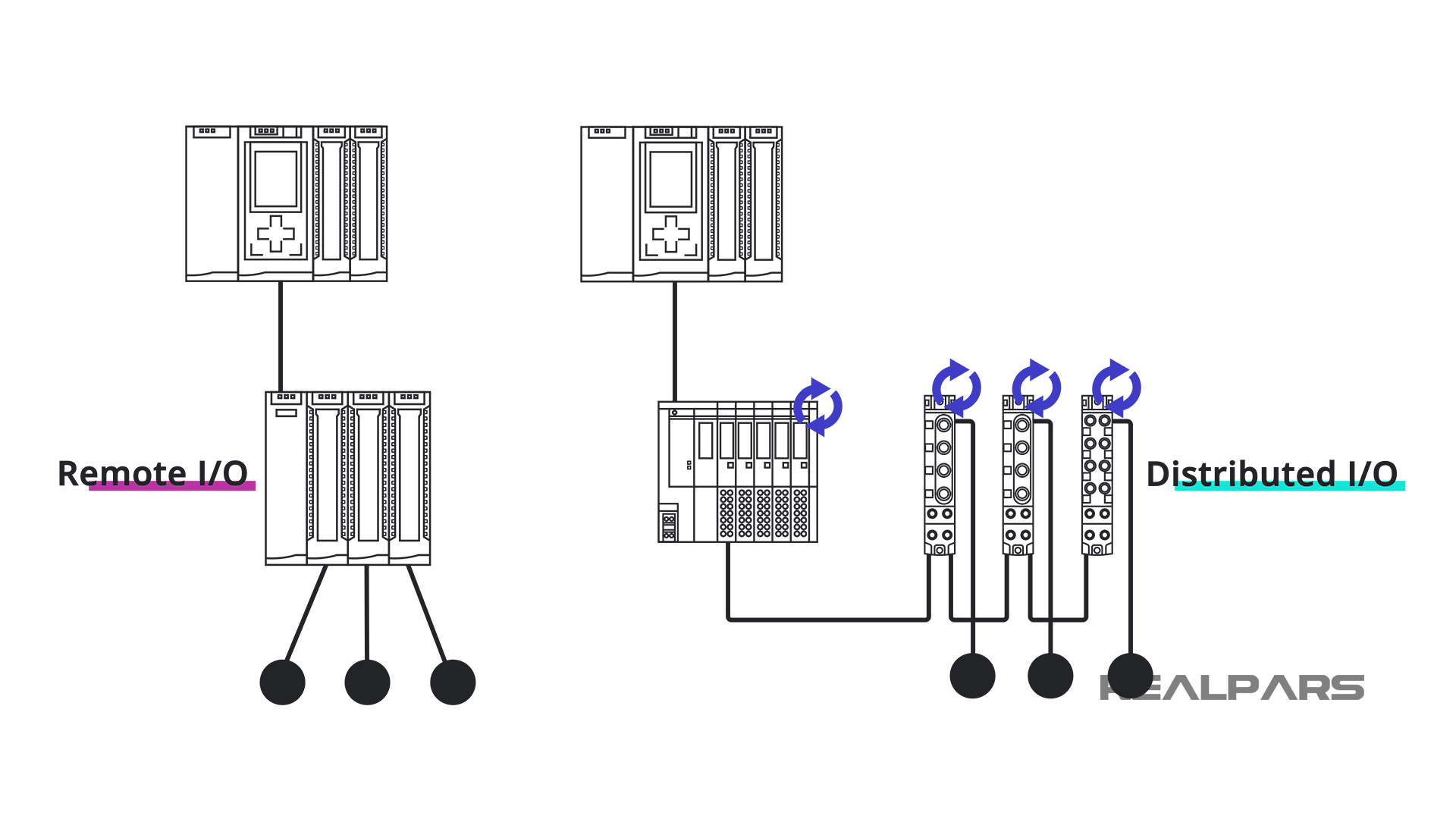
Allen-Bradley FLEX I/O
Allen-Bradley has FLEX I/O which is a modular I/O system for distributed applications. The Flex I/O allows for the connection of up to eight I/O modules and transfers I/O data to and from a central controller or PLC.
Flex I/O is an example of Distributed I/O and the eight modules connected to the Flex I/O are examples of Remote I/O.
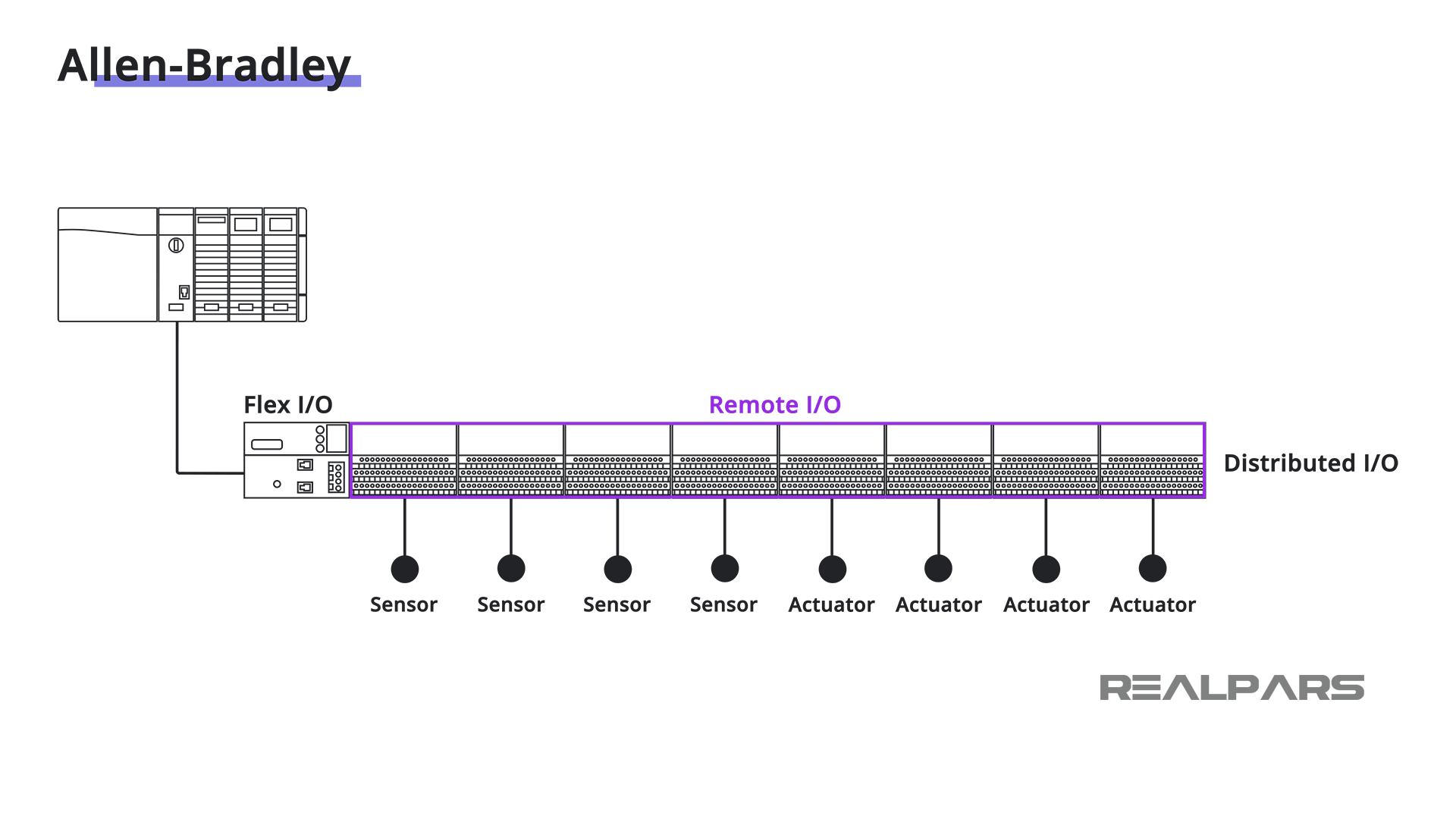
Siemens ET 200SP
Siemens has the ET 200SP series of Distributed I/O that can connect up to 16 channels of digital or analog I/O with a single-wire connection.
The ET 200SP is an example of Distributed I/O and is connected to the bus system via an interface module. This system is very flexible as it can accommodate either PROFINET interface modules or PROFIBUS interface modules.
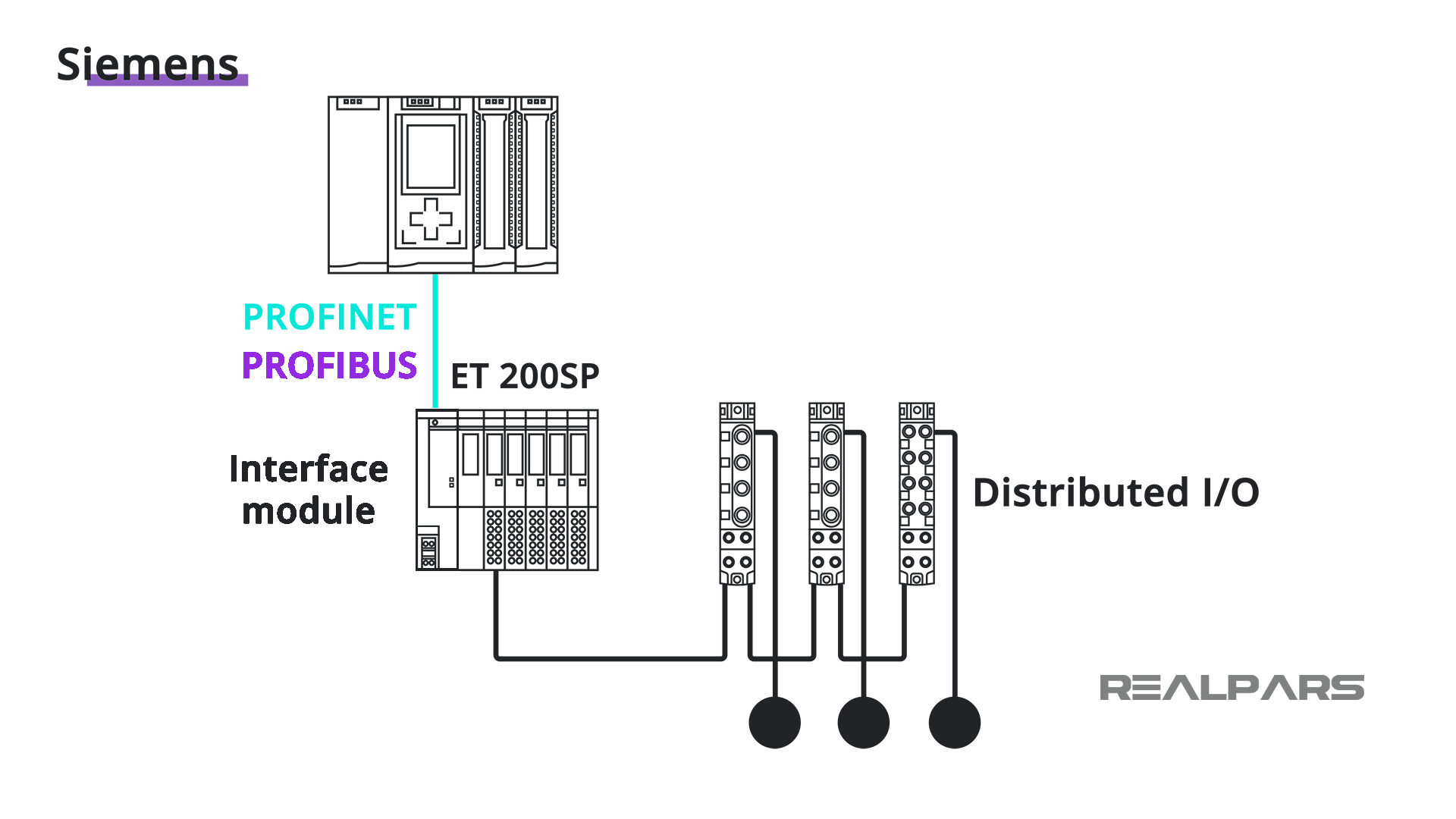
As we said earlier, Remote I/O is at a remote place physically located a distance from a control PLC. Remote I/O does not have a brain and is not capable of any computing function at all.
It’s likely safe to say that when you hear the term Remote I/O there is only one controller, or PLC, involved as opposed to Distributed I/O which has multiple controllers.
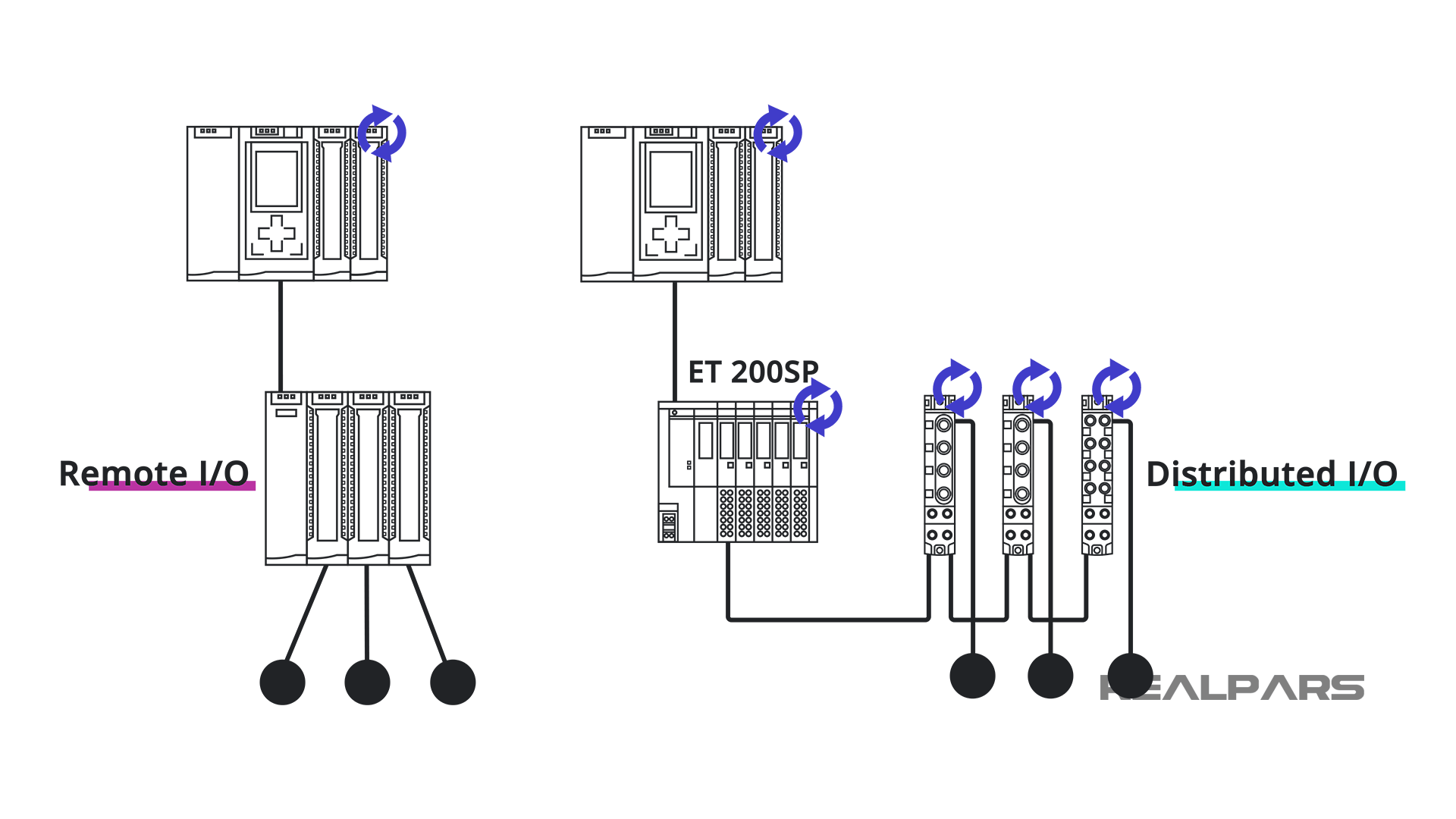
Summary
Let’s review what we’ve discussed.
– The predecessor of the DCS and the PLC was the Direct Digital Control or DDC system which centered on a mini-computer connected to several proprietary I/O devices located at remote locations around the plant.
– A modern DCS is a control system that has a number of Distributed autonomous controllers.
– Generally speaking, Distributed I/O has a brain or some computing capacity.
– Remote I/O does not have a brain and is not capable of any computing function at all.
– The term Remote I/O suggests a single controller such as a PLC, whereas the term Distributed I/O suggests multiple controllers.
You might want to review 2 of our other articles:
2) What is DCS?
Want to Learn More?
If you would like to get additional training on a similar subject please let us know in the comment section.
Check back with us soon for more automation control topics.
Got a friend, client, or colleague who could use some of this information? Please share this article.
The RealPars Team