Inductive Sensor Explained | Different Types and Applications
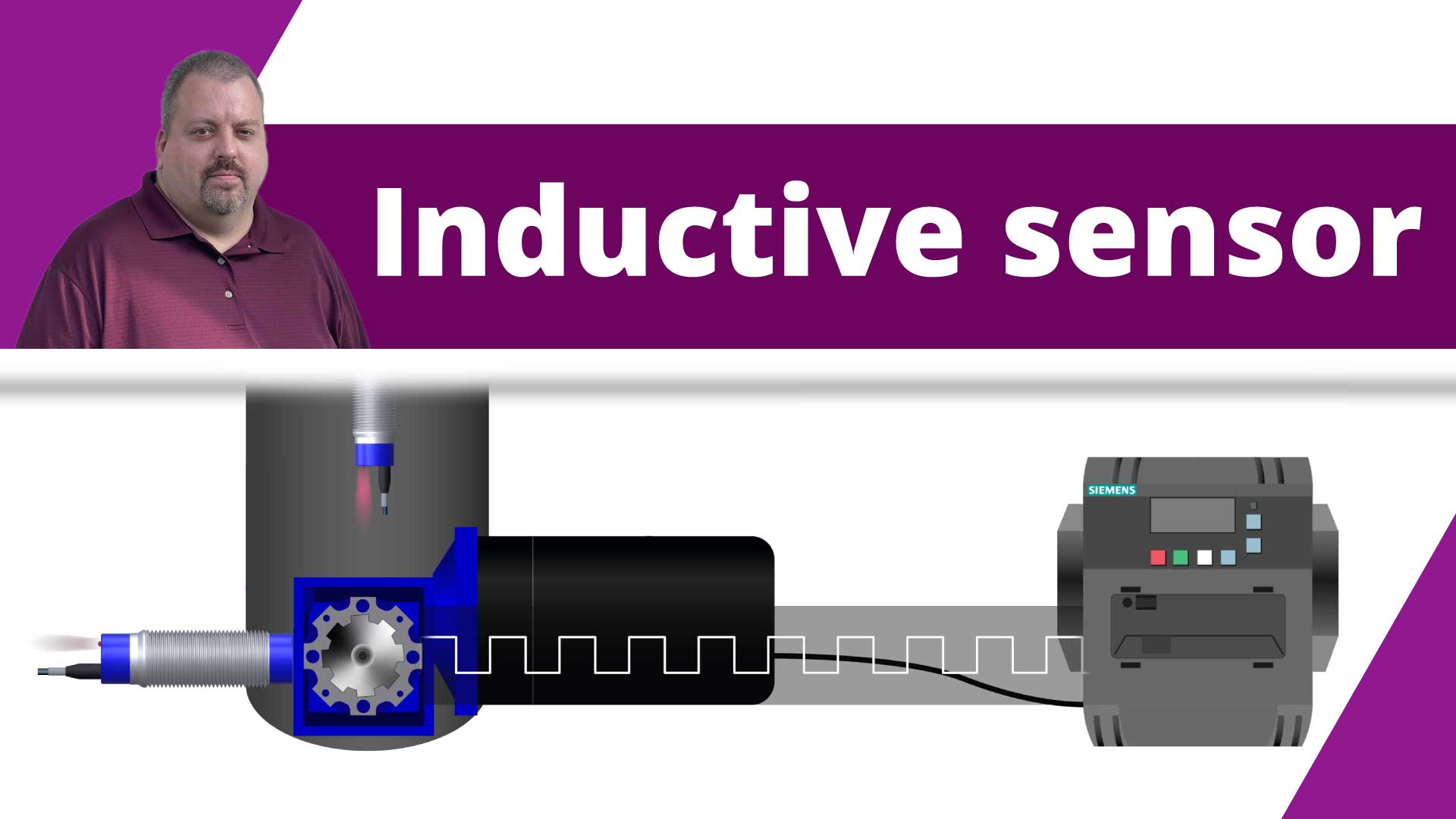
In this article, we will talk about inductive sensors. We will explain what an inductive sensor is, how an inductive sensor works, some of the different types of inductive sensors, and we will also talk about some of the ways these sensors are used in automation.
What is an inductive sensor?
An inductive sensor is an electronic device that can detect ferrous metal targets without physical contact.
Inductive sensors will also detect non-ferrous metal targets like aluminum, brass, and copper. But using non-ferrous metal targets decreases an inductive sensor’s sensing range.
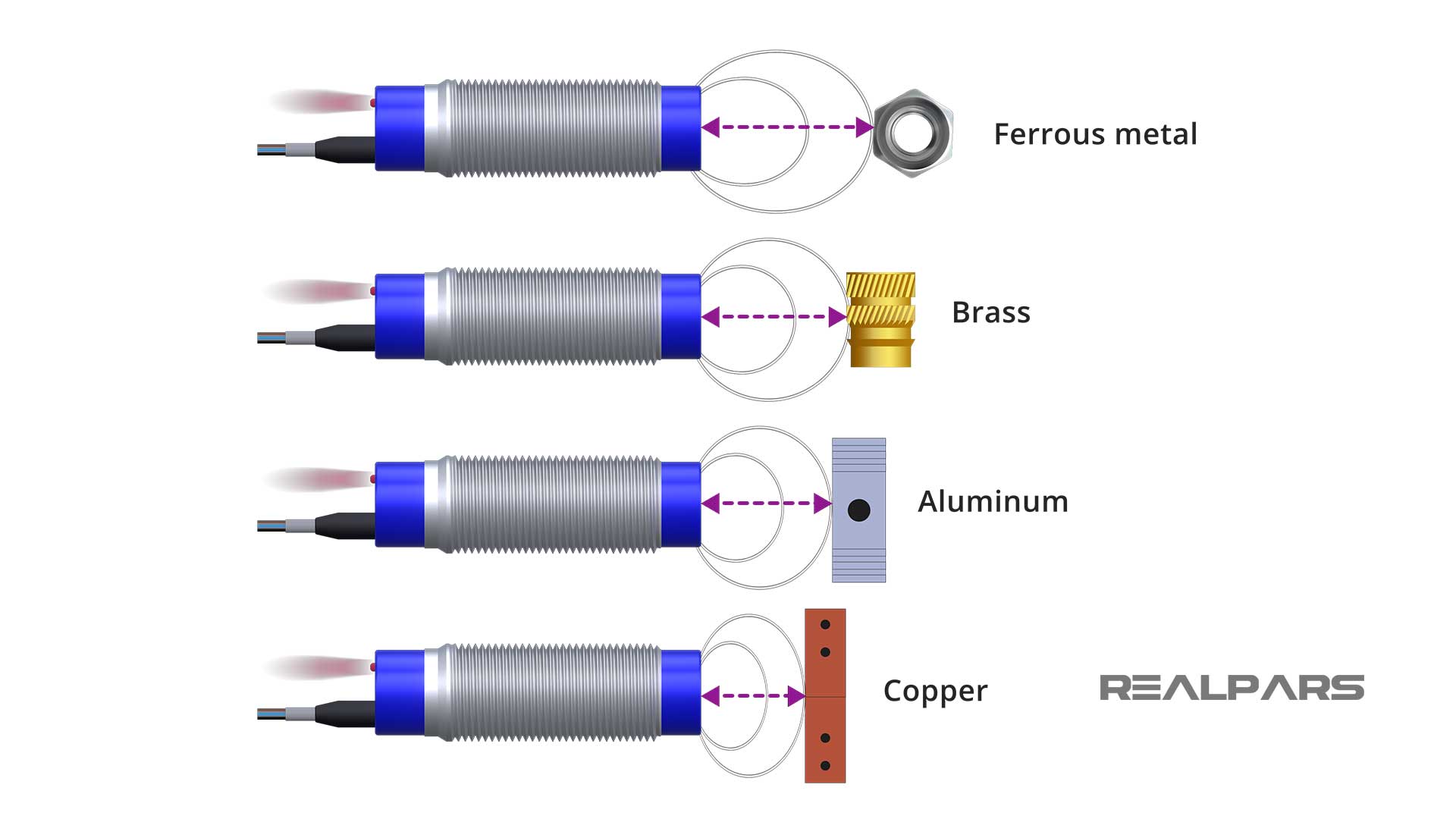
Sensing range
The sensing range of an inductive sensor is the distance from the sensor’s face to the maximum distance the sensor can detect a metal target.
The sensing distance can be found on the sensor’s datasheet.
The datasheet will also show some correction factors when you want to detect a non-ferrous metal.
Non-ferrous metal is a type of metal that does not have a significant amount of iron in it. Brass, aluminum, and copper are examples of non-ferrous metals. This means these metals do not have a significant amount of iron within them.
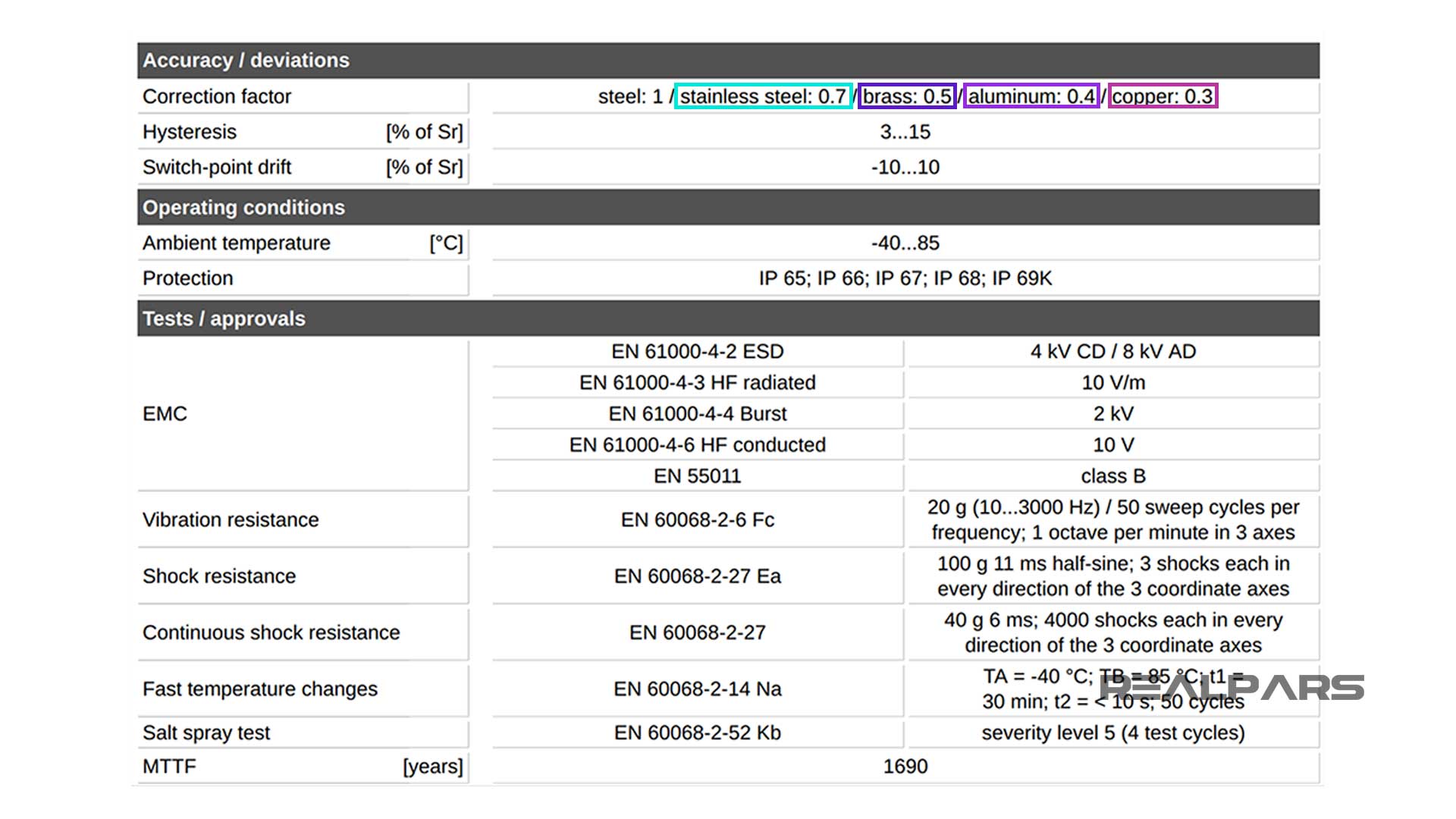
Here for this inductive sensor, the datasheet shows the sensing distance as 12 mm. This works only when the object is steel which has a significant amount of iron in it.
Correction factor
If the object is a non-ferrous metal, meaning it does not have a significant amount of iron within it, you need to consider a simple correction factor when defining the sensing distance.
For example, here it says if the object is made of brass, you simply need to multiply the normal sensing distance for the sensor by 0.5.
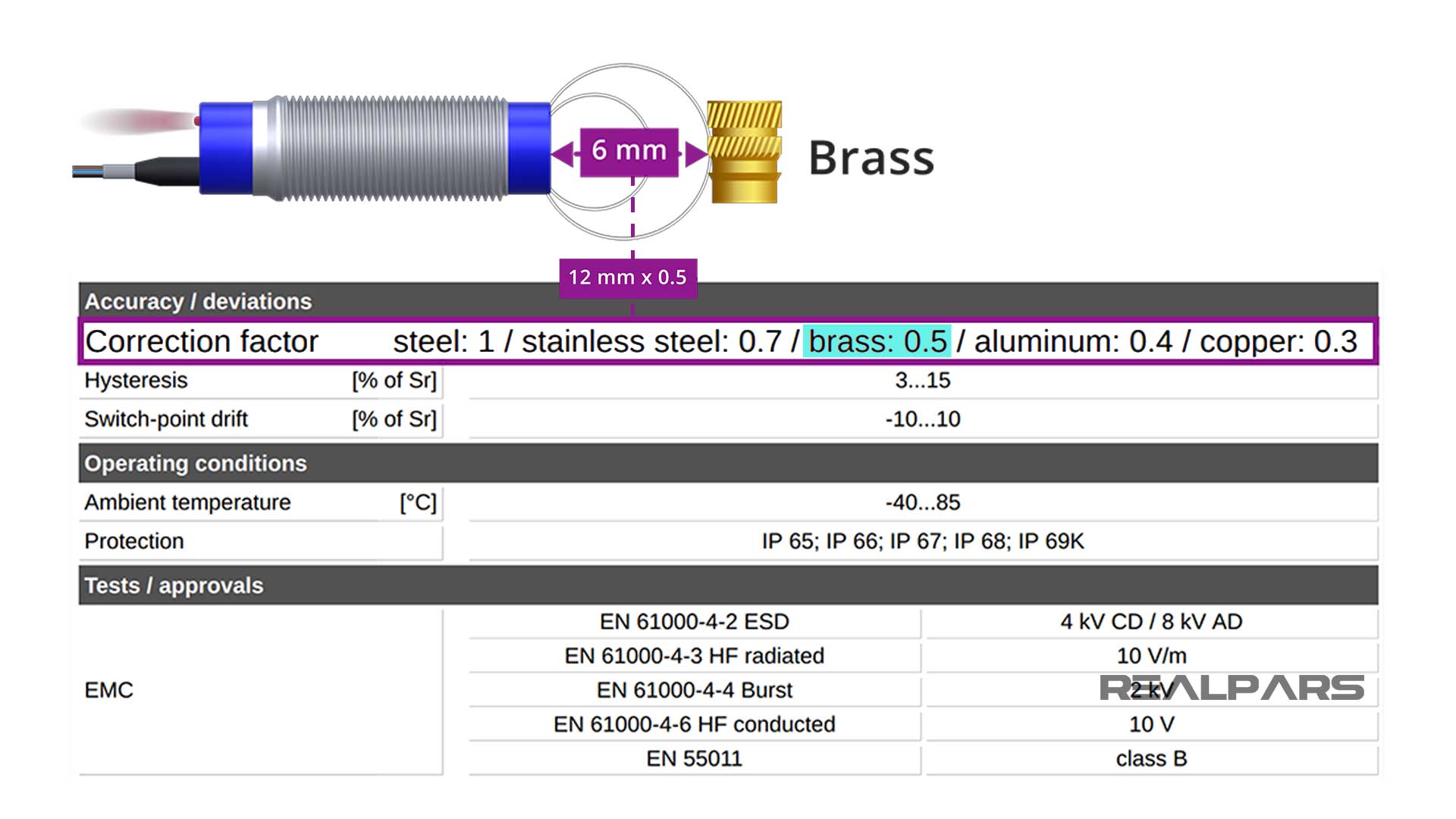
So, if we multiply 12 mm by 0.5, we will end up with 6 mm as the sensing distance for a brass object.
This means if we want to sense an object that is made of brass, the distance between the sensor and the object should not be more than 6 mm for this sensor to be able to sense the object.
The same goes for other non-ferrous metals as well. For example, if we have an object that is made of aluminum, the sensing distance for this inductive sensor is 12 mm multiplied by 0.4. This gives us a sensing distance of 4.8 mm.

For a copper object, the sensing distance will be 12 mm multiplied by 0.3 which is equal to 3.6 mm.
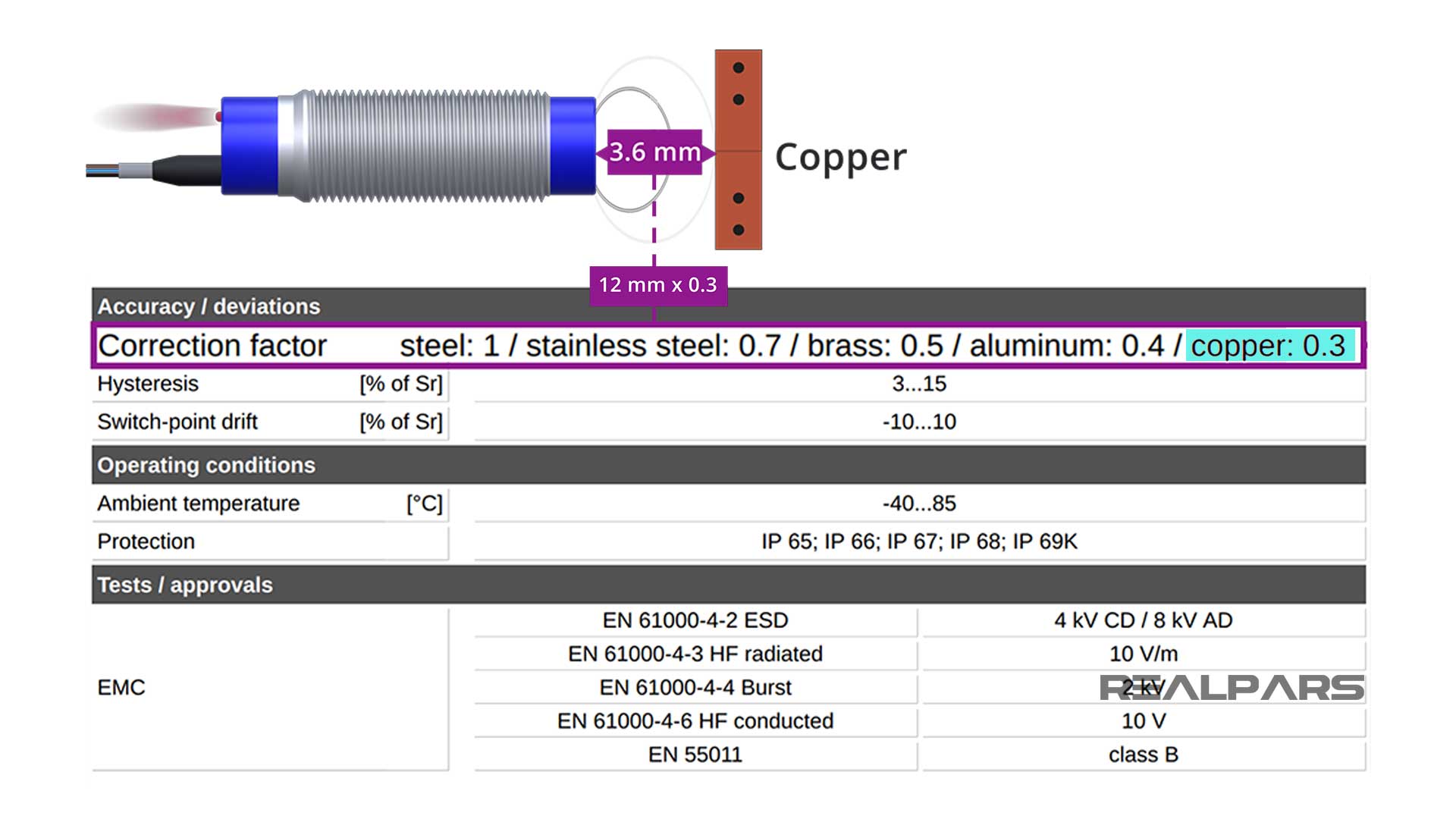
As you can see, here it shows the correction factor for steel as 1. Steel is a ferrous metal as it has a significant amount of iron in it. So, the sensing distance for an object that is made out of steel is 12 mm multiplied by 1 which is equal to 12 mm.
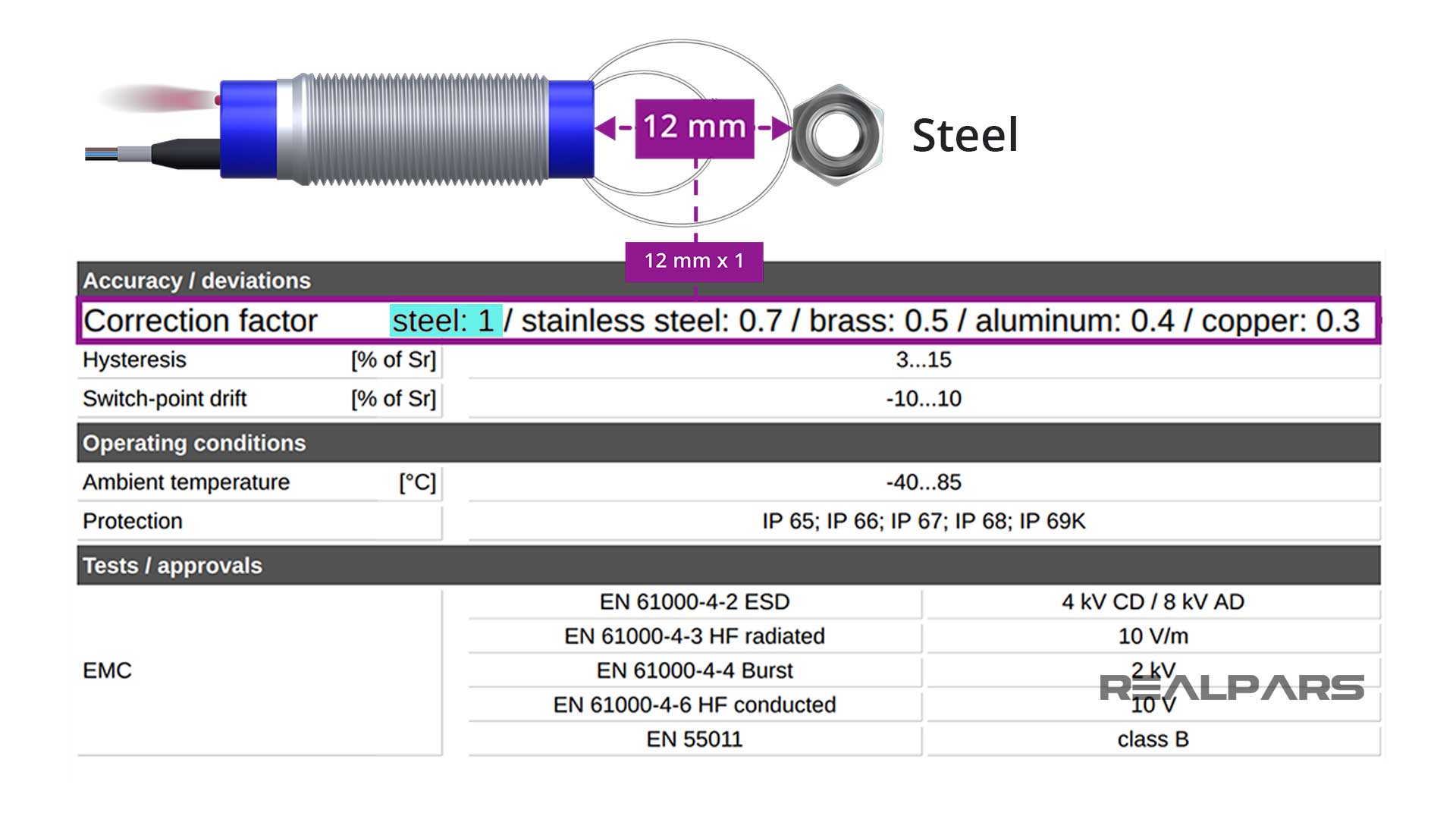
If you need the sensor datasheet and cannot find it, you can go to the sensor manufacturer’s website to get it.
Inductive sensor parts
The four major external parts of an inductive sensor are the body of the sensor, the sensor’s face, the indicator light, and the cable end or cable connector end.
Inside the sensor’s body is where the circuitry that makes the sensor work is located.
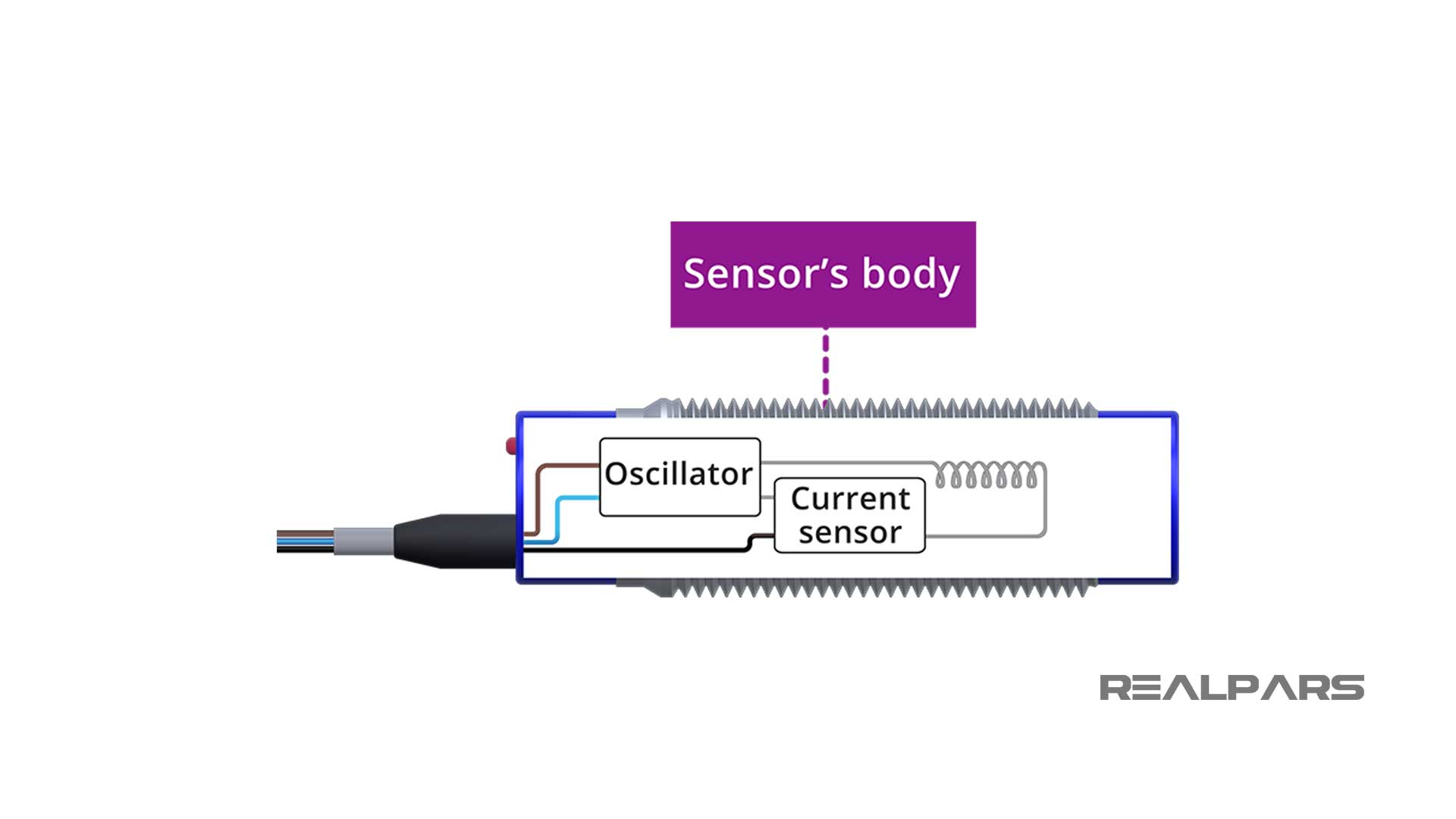
The face is the part of the sensor that detects the targets.
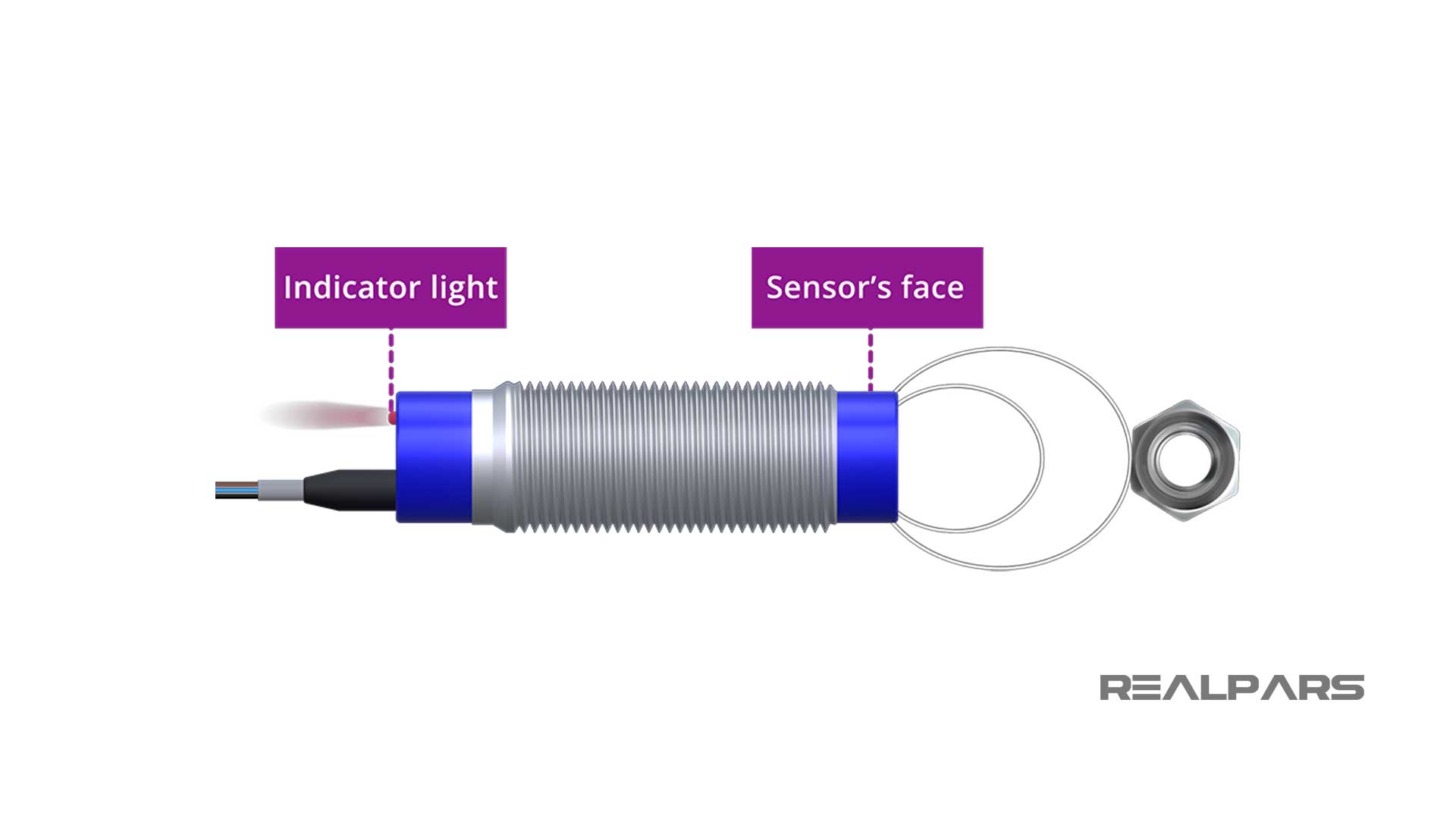
The indicator light is usually near where the cable gets connected to the sensor. The indicator light turns on when the target is within the sensors sensing range.
The sensor’s cable has three different colored wires in it, brown, blue, and black.
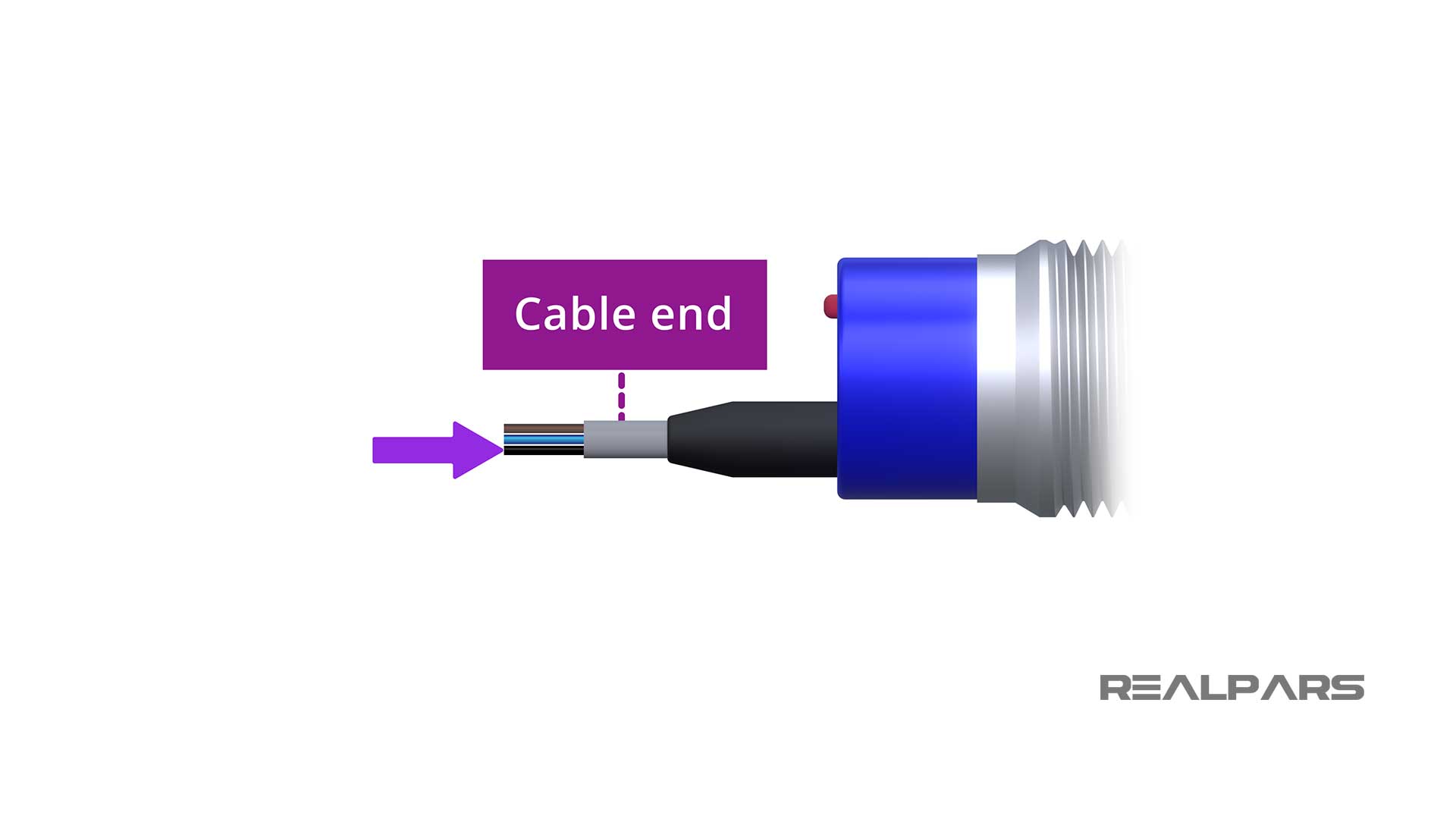
These sensors are available with a cable that is already attached or they can have a connector that the cable screws on to.
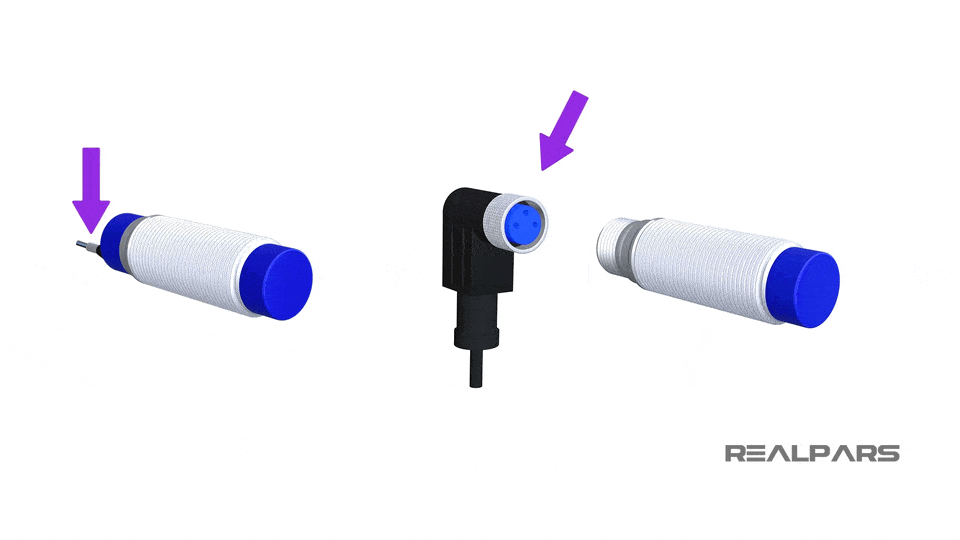
How does an inductive sensor work?
How inductive sensors work is the sensor creates an electromagnetic field that emits from the sensor’s face. Putting a metal target near the sensor’s face will disrupt the electromagnetic field, causing the sensor’s output and indicator light to turn on.
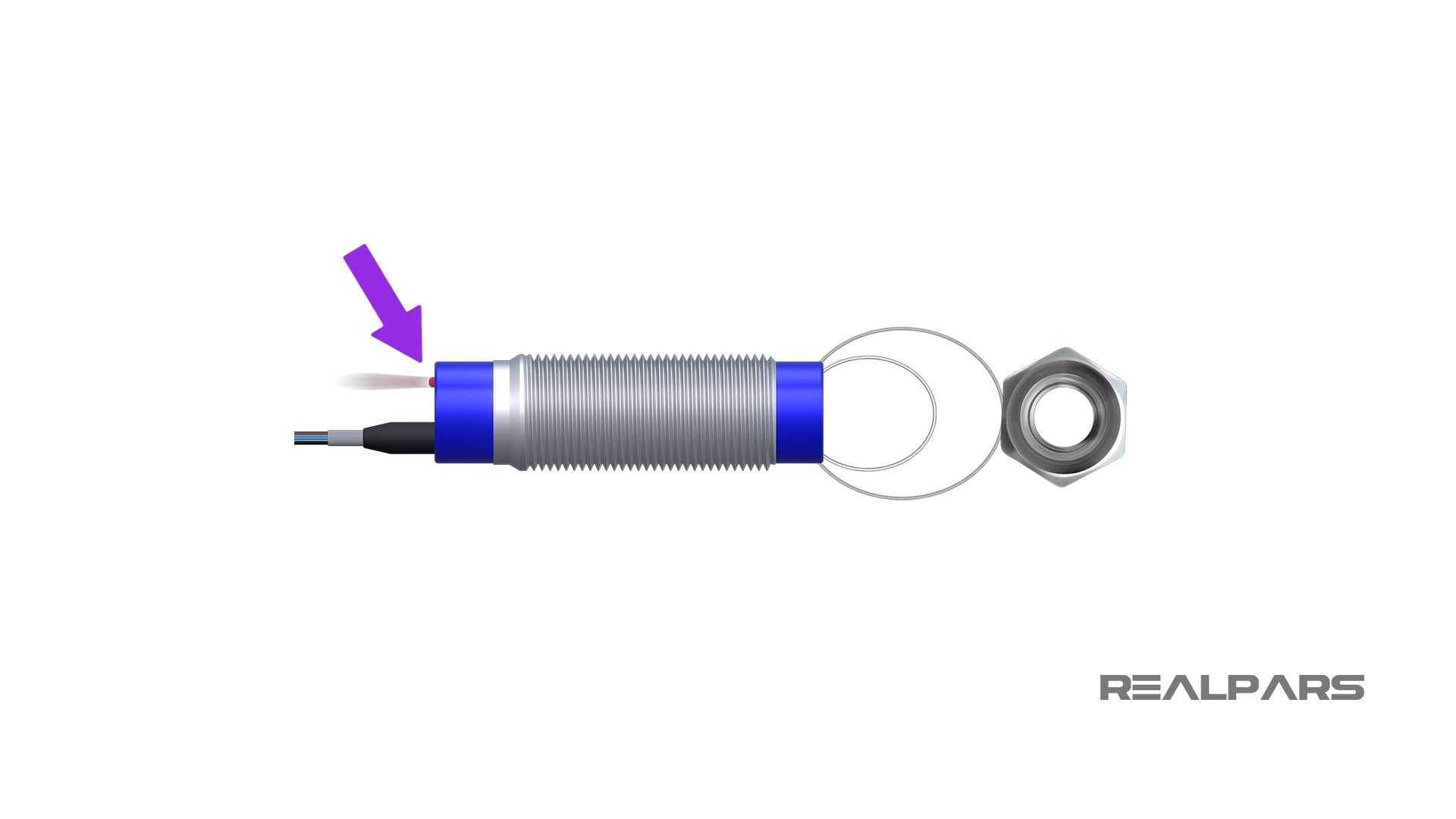
Types of inductive sensors
Inductive sensors are available in a lot of different configurations. They can be
– AC or DC,
– shielded or unshielded,
– normally open or normally closed,
– NPN or PNP, just to name a few.
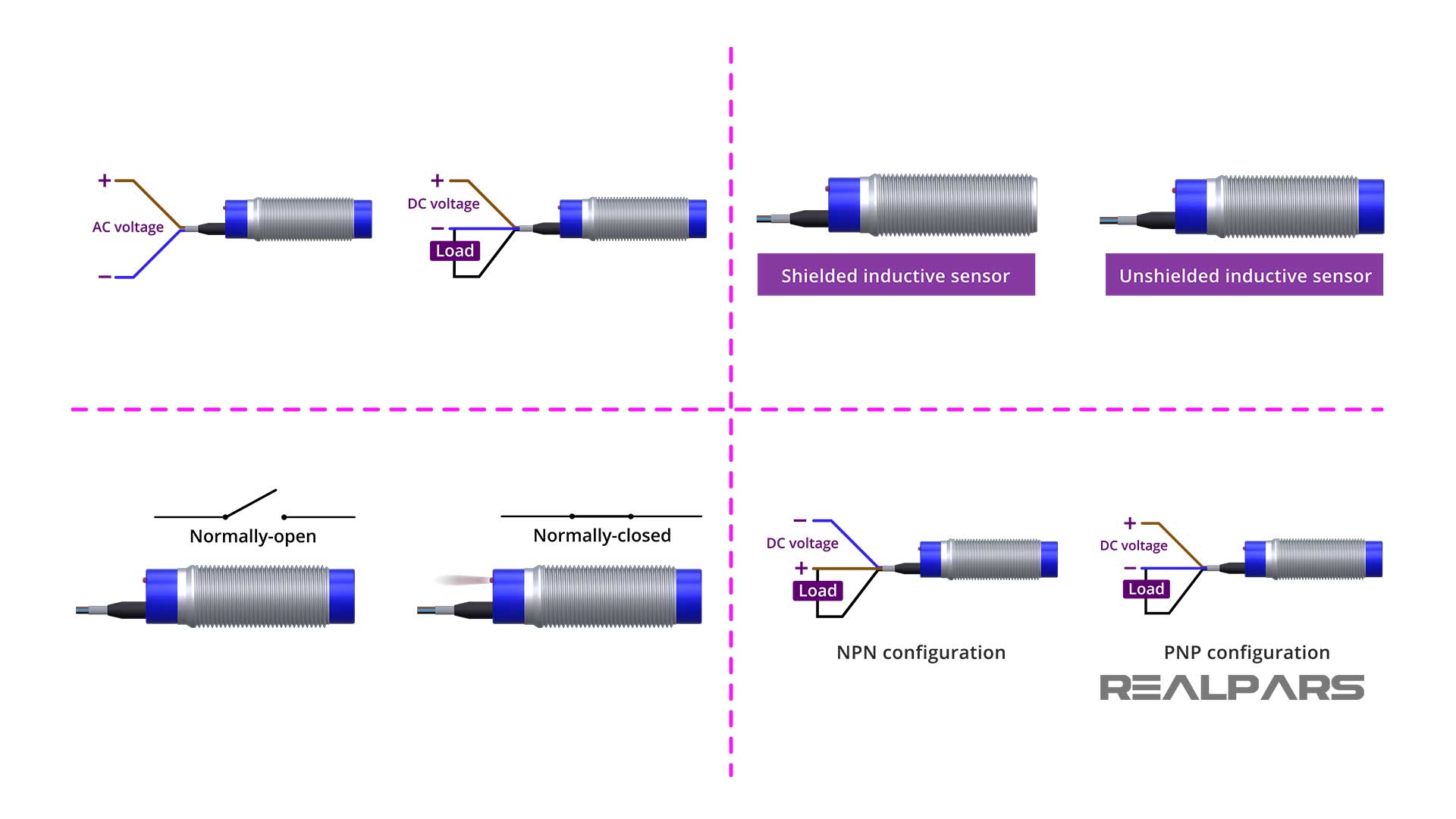
They also make inductive sensors for hazardous, high-temperature, and washdown locations.
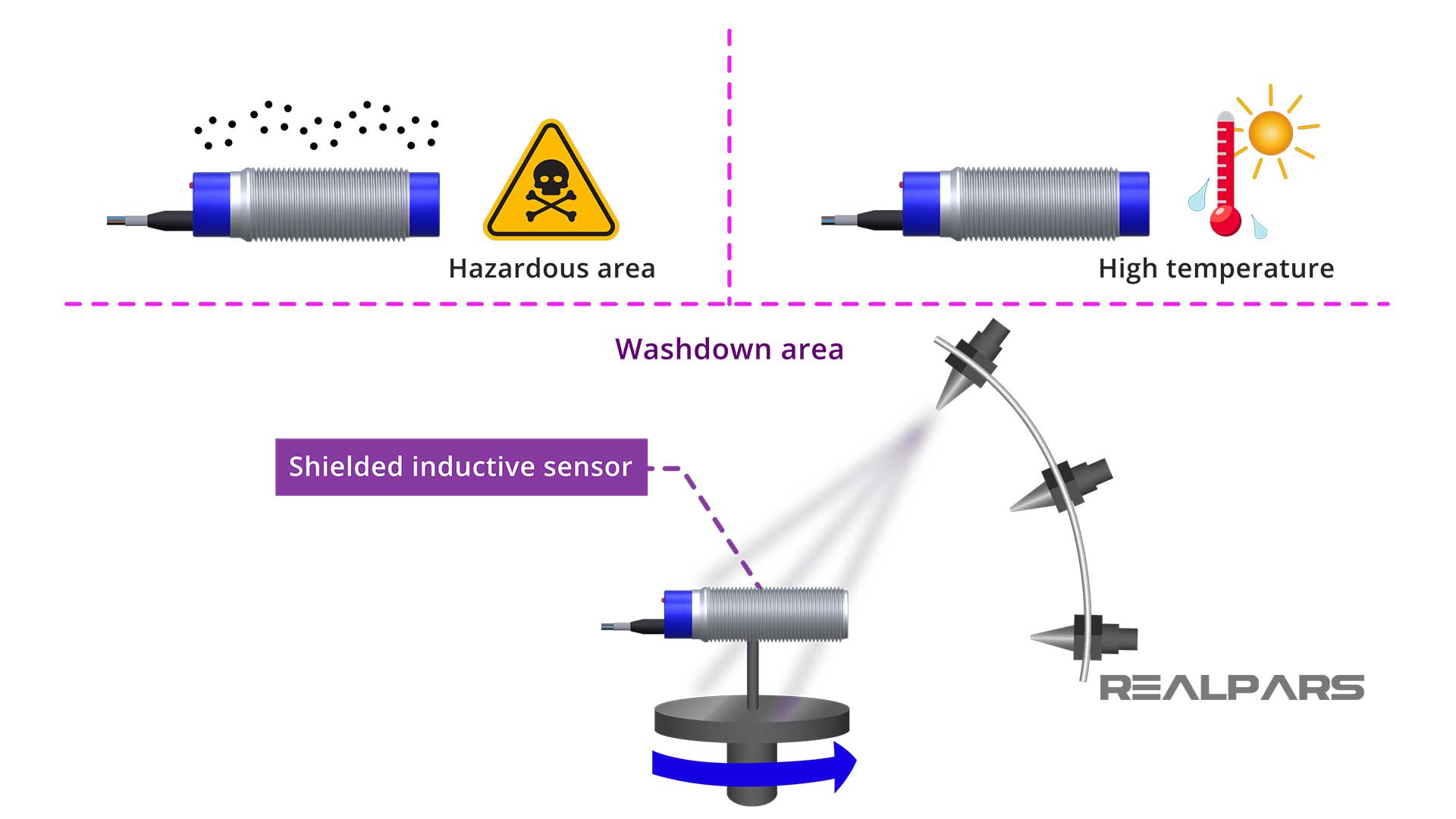
For washdown locations, we need to use a shielded inductive sensor.
The Advantages of an inductive sensor
Here are some advantages of using inductive sensors compared to other types of sensors.
Inductive sensors are solid-state and do not have any moving parts.
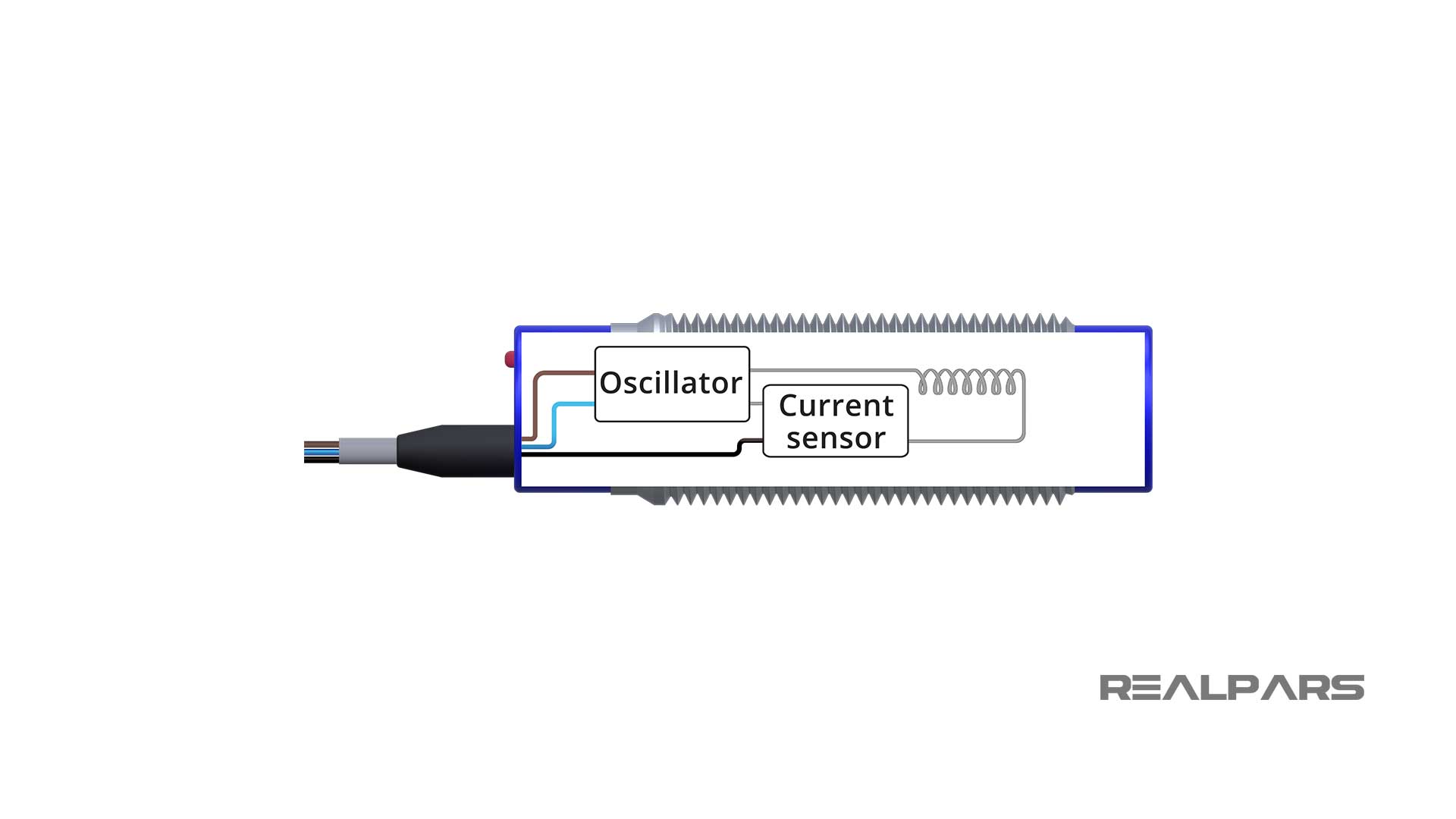
This makes them very reliable because they usually only need to be replaced when they get physically damaged.
Inductive sensors can get dirty and still work. Things like dirt, sawdust, oil, and grease will not affect how inductive sensors detect targets.
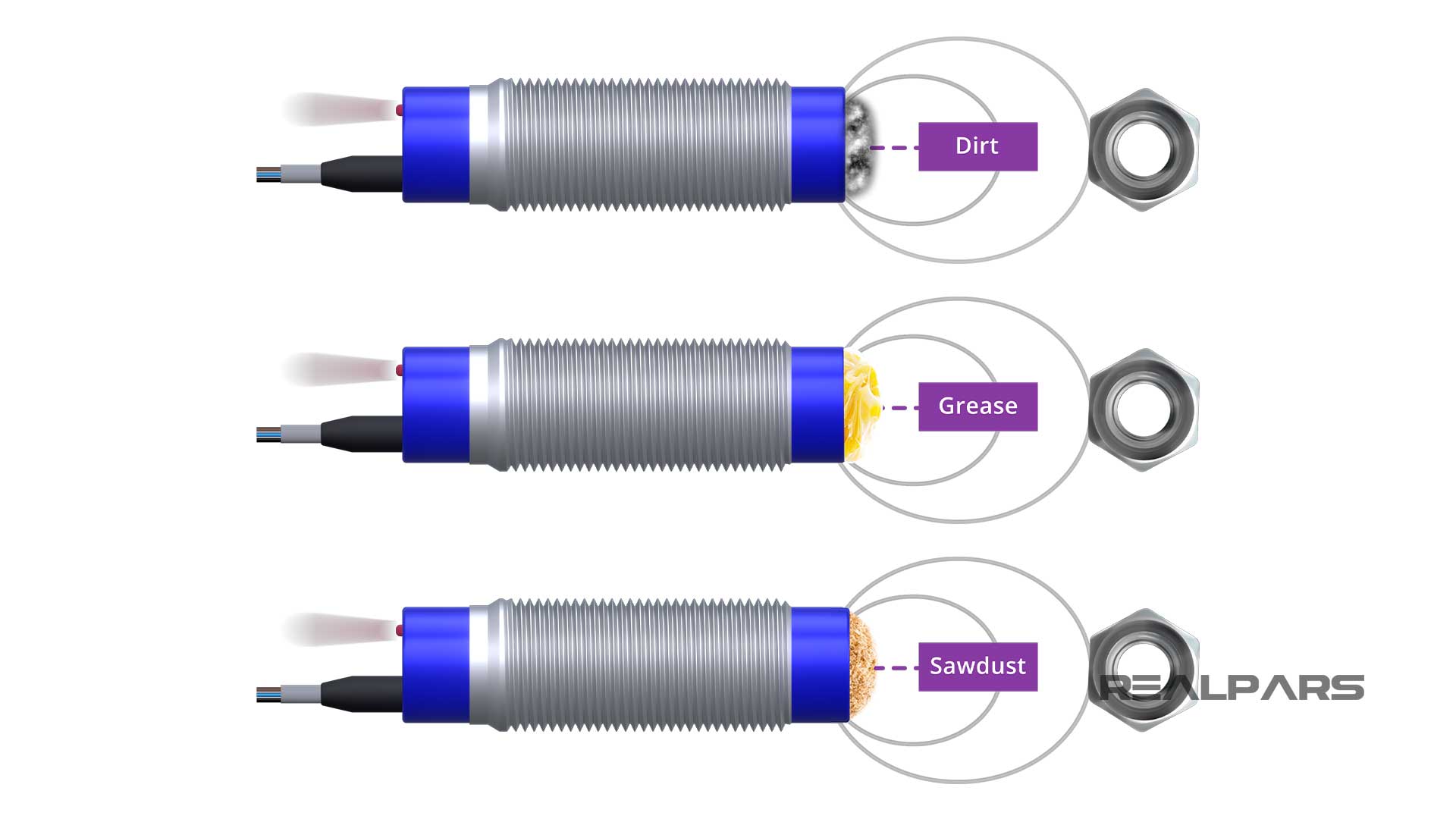
Inductive sensor mounting
Inductive sensors can also be mounted in many different ways. Depending on the type, some of these sensors can be mounted by just bolting them in place or drilling and tapping a hole that is the same size and thread as the sensor.
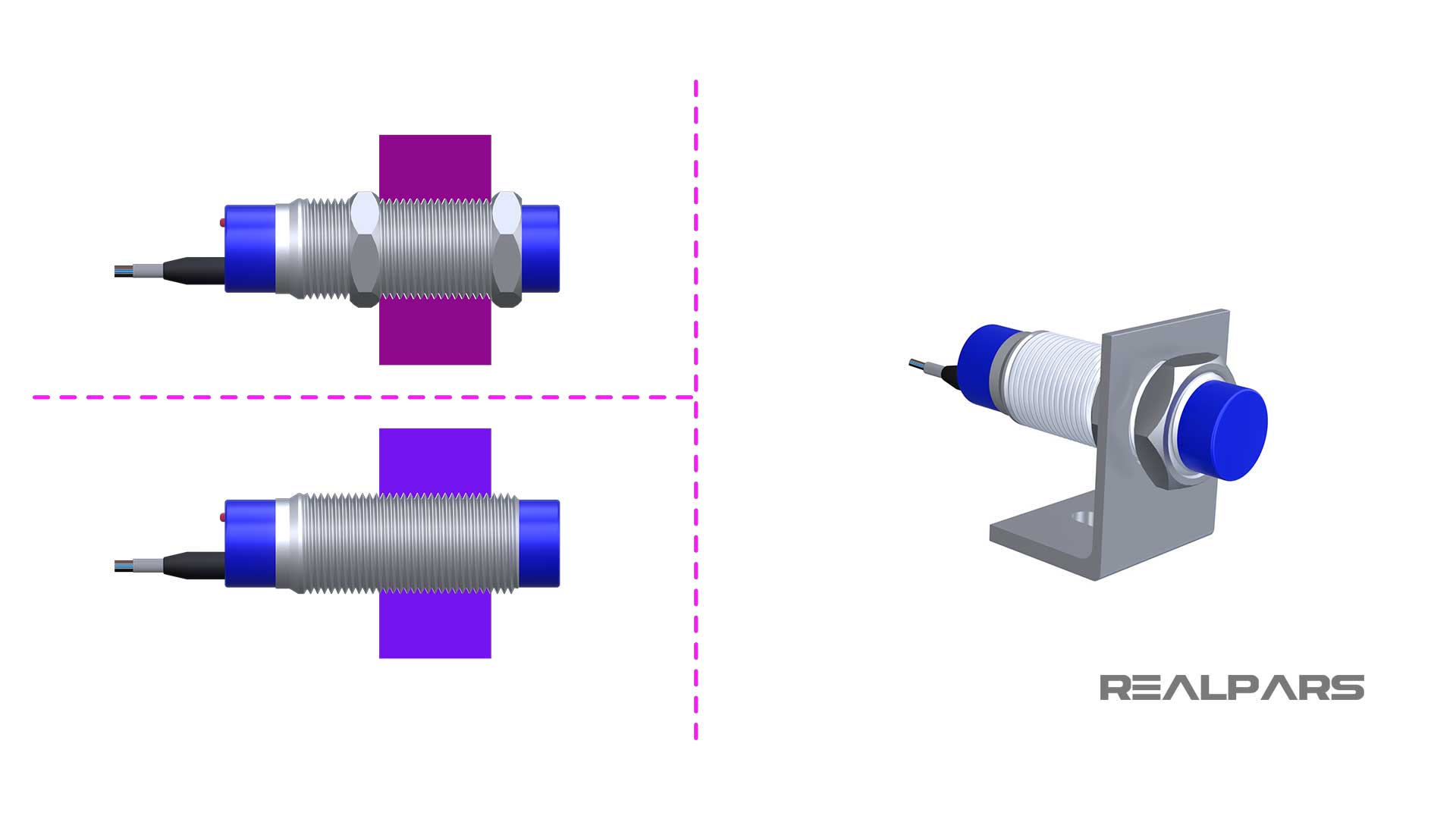
They also make a lot of different factory mounts for inductive sensors to make them quick and easy to install.
For example, we will be using a general-purpose 24-volt DC twelve-millimeter inductive sensor, that is normally open and has a three-wire cable already attached.
We will use a bolt to trigger the sensor. To connect the sensor to the tester, connect the brown wire to the sensor voltage + terminal, connect the blue wire to the sensor voltage – terminal, and connect the black wire to the sensor outputs #1 or #2 terminal.
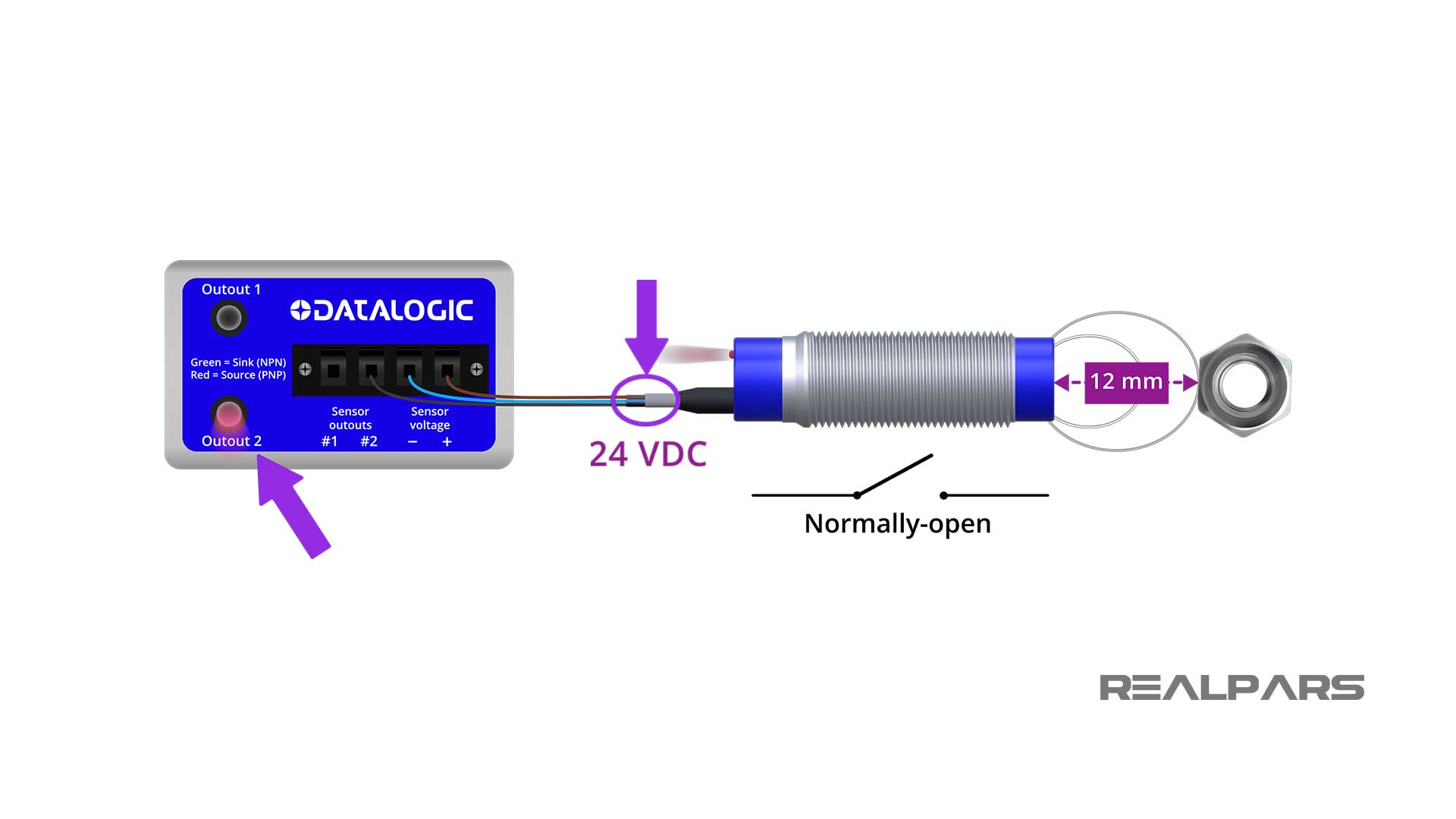
Now how do inductive sensors work? Notice when the bolt and sensor are not close together, the indicator light is off.
When we move the bolt into the inductive sensors sensing range, the indicator light turns on and stays on.
Notice if we move the bolt so that it is touching the sensor, the indicator light stays on. When we move the bolt away from the sensor, the indicator light turns off.
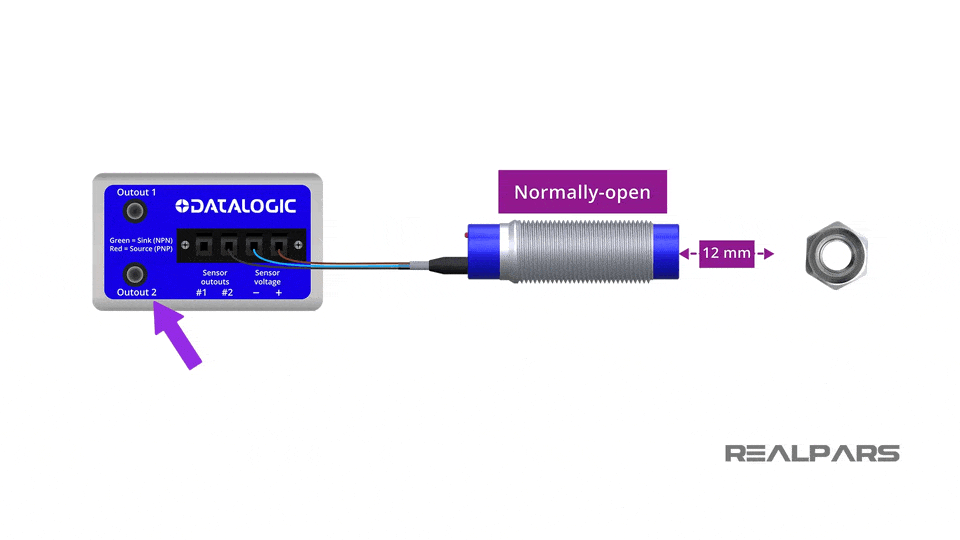
If this sensor’s output was normally closed, the indicator light would be turned off when the bolt is at the sensor and the light would be turned on when the bolt is away from the sensor.
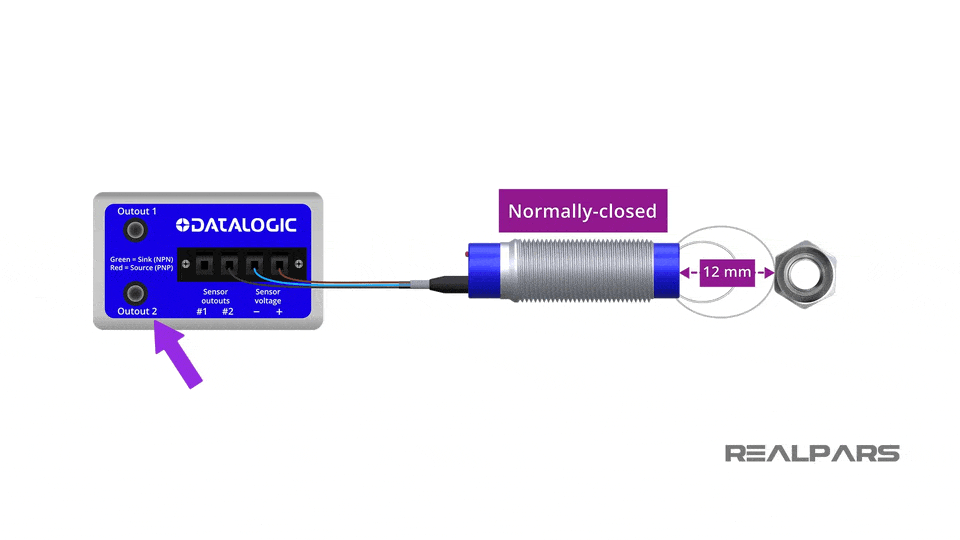
Inductive sensor applications
Now let’s talk about some examples of how inductive sensors are used with automation.
Inductive sensors can be used to detect part in place at workstations, at conveyor stops, and even at robots.
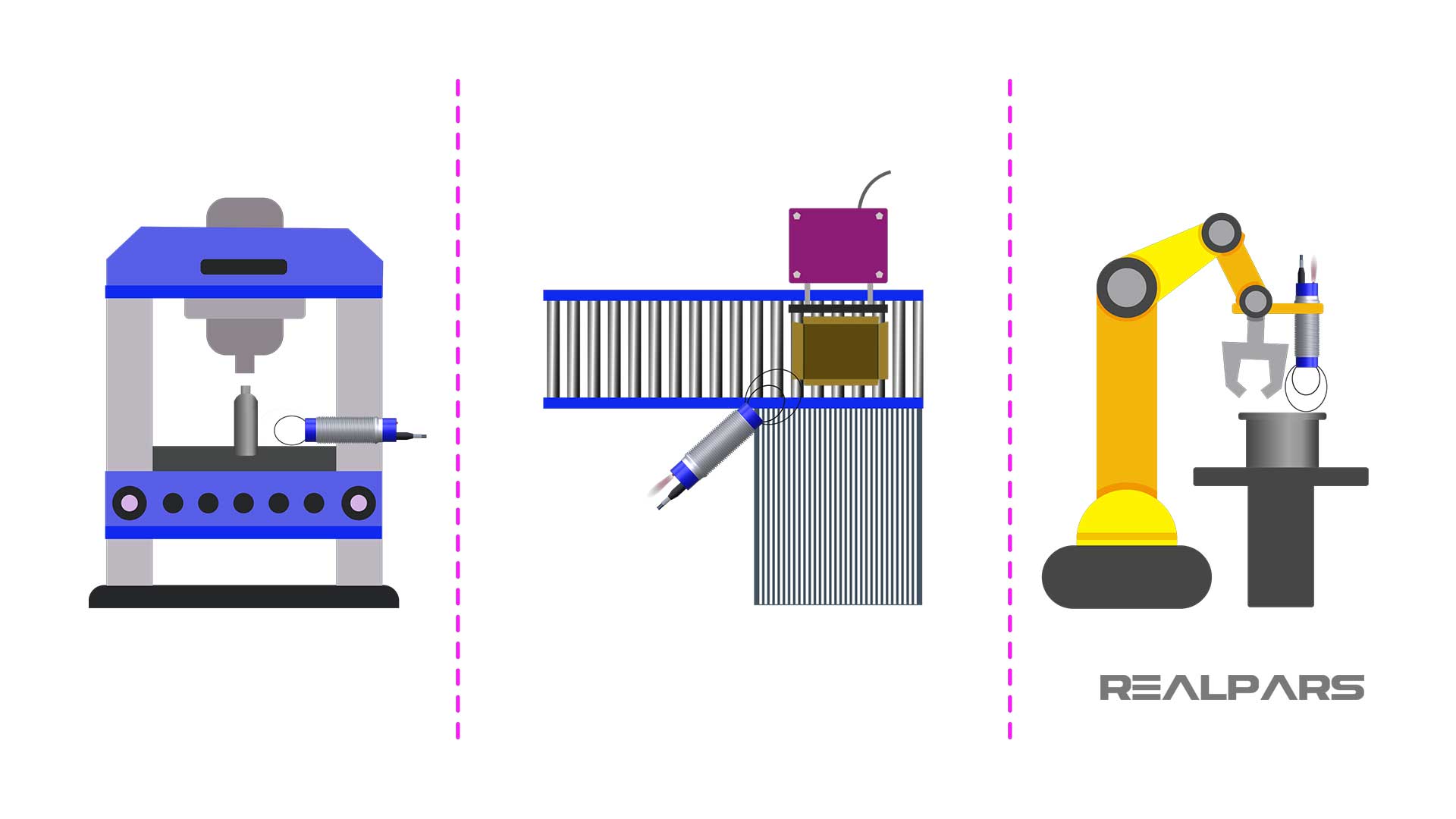
They can be used to detect if an air cylinder is extended or retracted and if a pallet stop or chain transfer is raised or lowered.
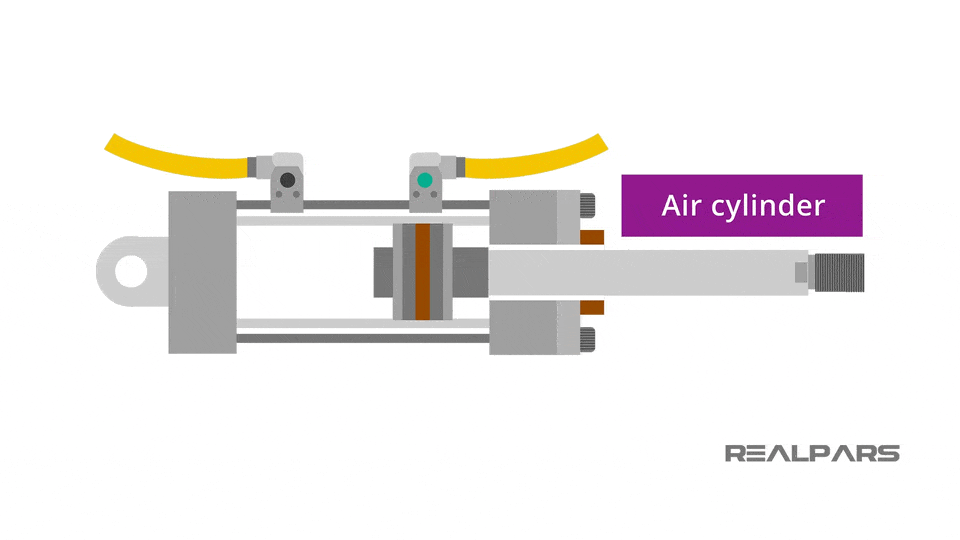
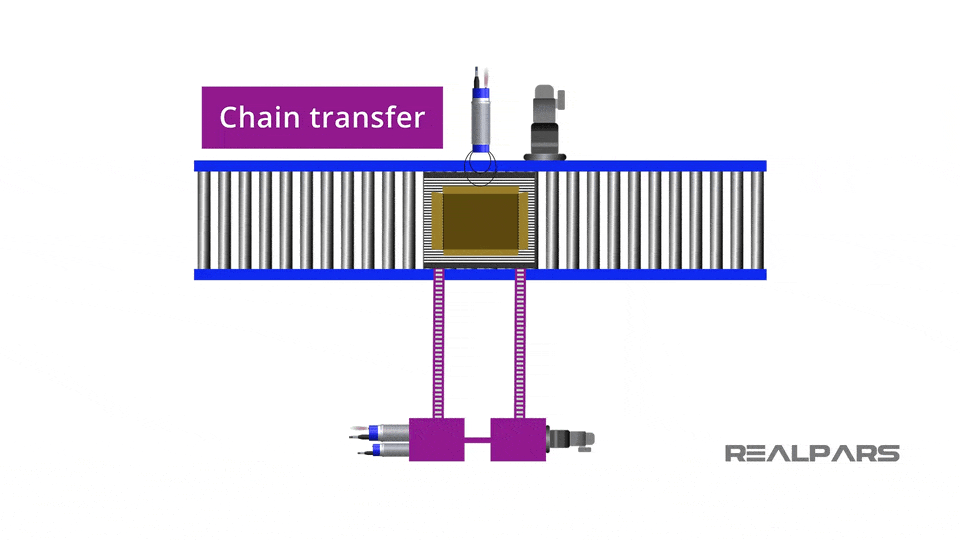
Inductive sensors can be used to detect if a pallet is centered on a turntable before it starts to rotate.
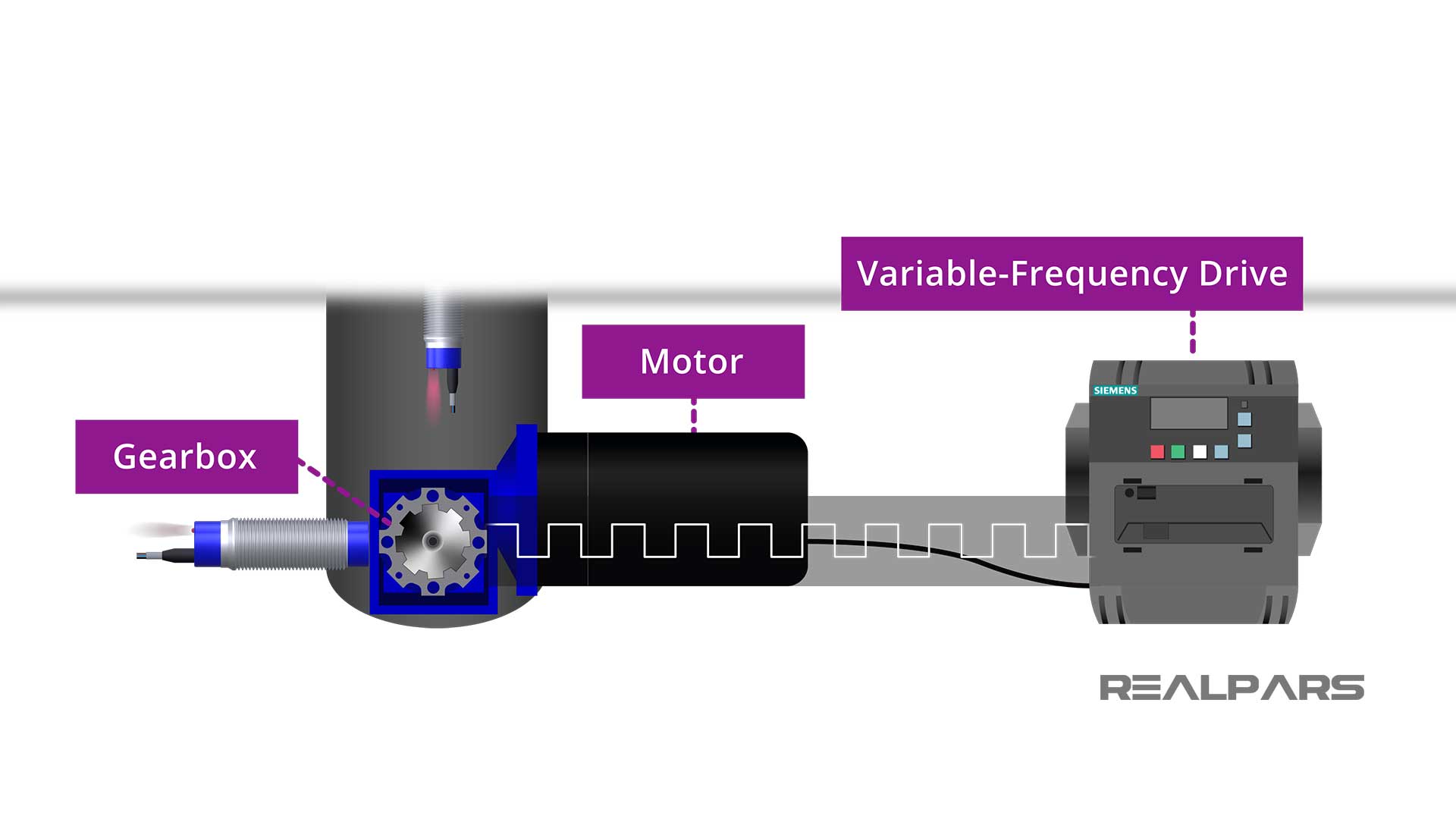
Let’s say this turntable is rotated by a motor with a gearbox and the motor is controlled by a VFD (variable-frequency drive). Inductive sensors can be used to tell the VFD when to slow down and stop.
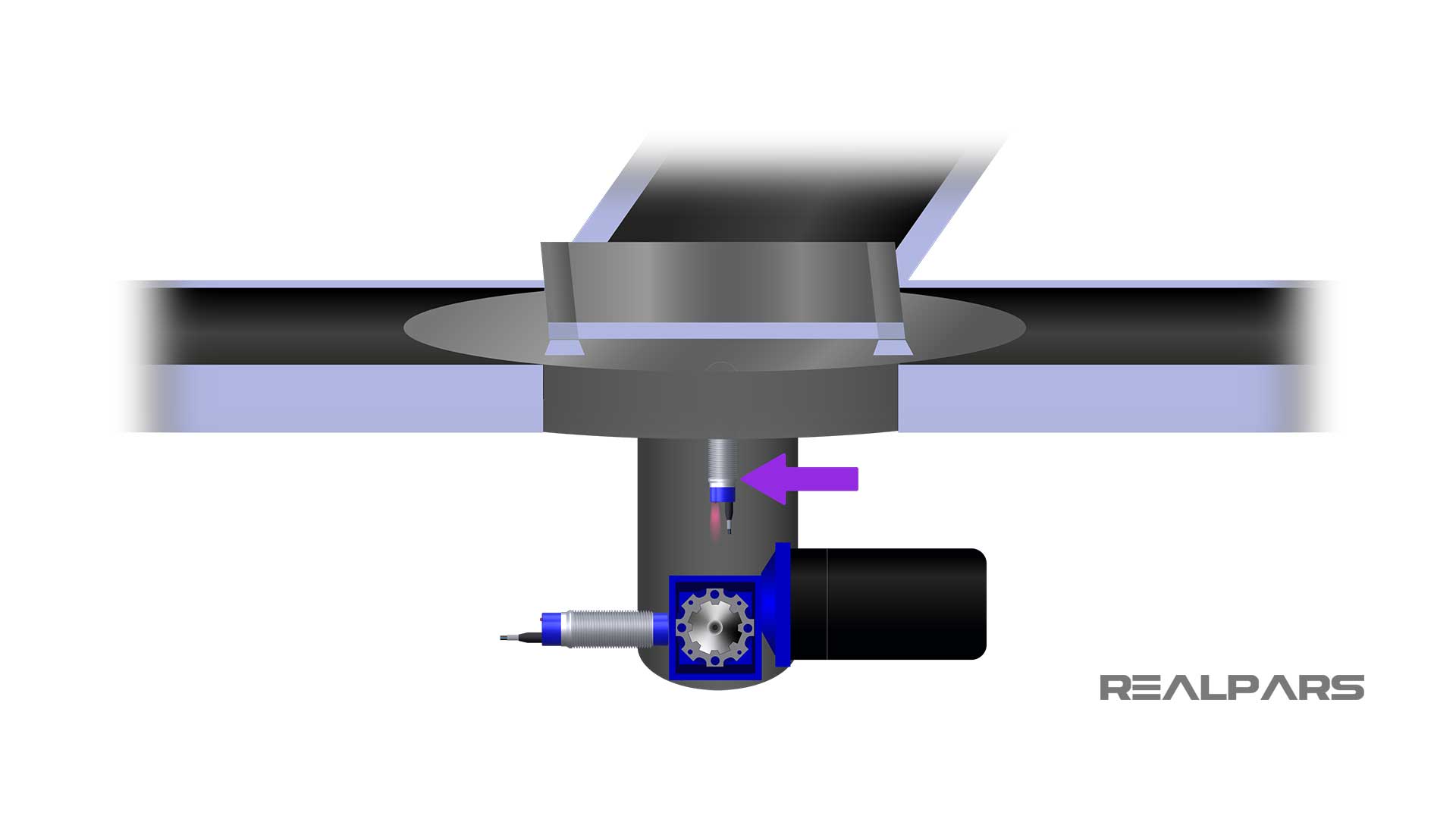
Summary
In review, by reading this article you have learned about inductive sensors. That they detect metal targets without physical contact by creating an electromagnetic field.
You learned the four main parts of an inductive sensor and that they have many different options to fit the needs of most applications.
Please let us know if you have any questions about inductive sensors or about sensors in general in the comments below and we will get back to you in less than 24 hours.
Got a friend, client, or colleague who could use some of this information? Please share this article.
Frequently asked questions
Learn from Industry Experts
With a 7-day trial, then €35/month