What is predictive maintenance? Every device has a point of failure. What does that mean? Well, a new device fresh from the manufacturer is healthy and problem-free. Due to wear and tear on the device as it ages, its health slowly deteriorates and eventually it fails.
At this point, you need to perform maintenance for the device to get it back to a healthy condition.
Types of maintenance
There are three main types of maintenance: Reactive, preventive, and predictive. Below I will explain each type, give examples of maintenance, and compare the differences.
1. Reactive maintenance
With reactive maintenance, you simply wait until a device breaks down and then perform maintenance on that device.
That means that you wait until the device fails and requires maintenance and then react, hence reactive maintenance.
For example, let’s say that you have a microwave oven at home. You use it for a few years until it gets to the point of failure and It won’t turn on anymore.
In this case, you repair the microwave or buy a new one. But it may take a couple of days for you to either repair the microwave or buy a new one.
That means, with this wait and react way of maintenance, you may not be able to use your microwave for a couple of days and that may not be a big deal.
However, if the same thing happens in a big industrial enterprise like an oil refinery, there might be huge consequences.
For example, if you wait for a pressure transmitter to fail and then perform maintenance on it, there might be considerable financial losses.
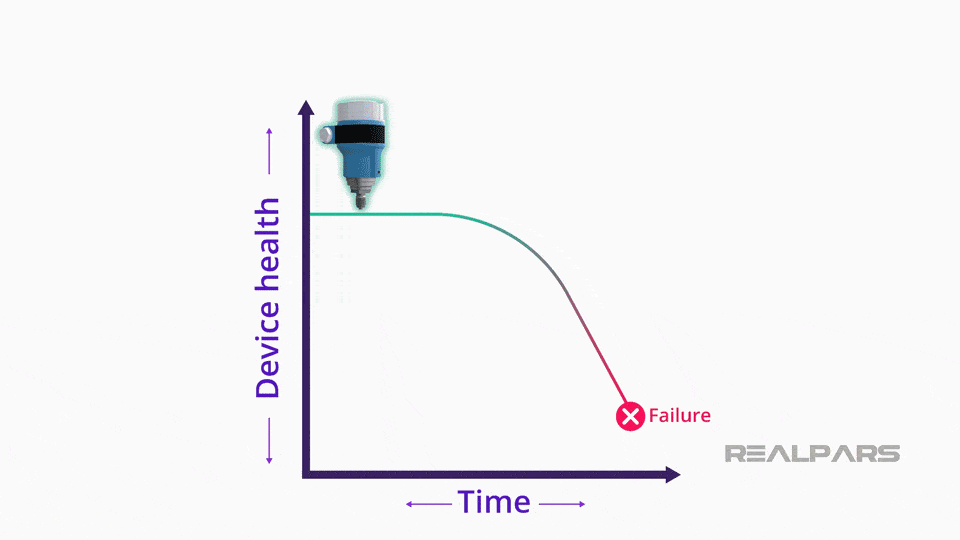
This is because every minute of interruptions in the manufacturing process may cost hundreds of thousands of dollars if not more.
So the wait and react or reactive maintenance may work fine for your microwave oven but it is probably not the best choice for industrial processes.
So what is the solution? The solution is to use preventive maintenance.
2. Preventive maintenance
With preventive maintenance, you try to perform maintenance for the device long before the device gets to the point of failure.
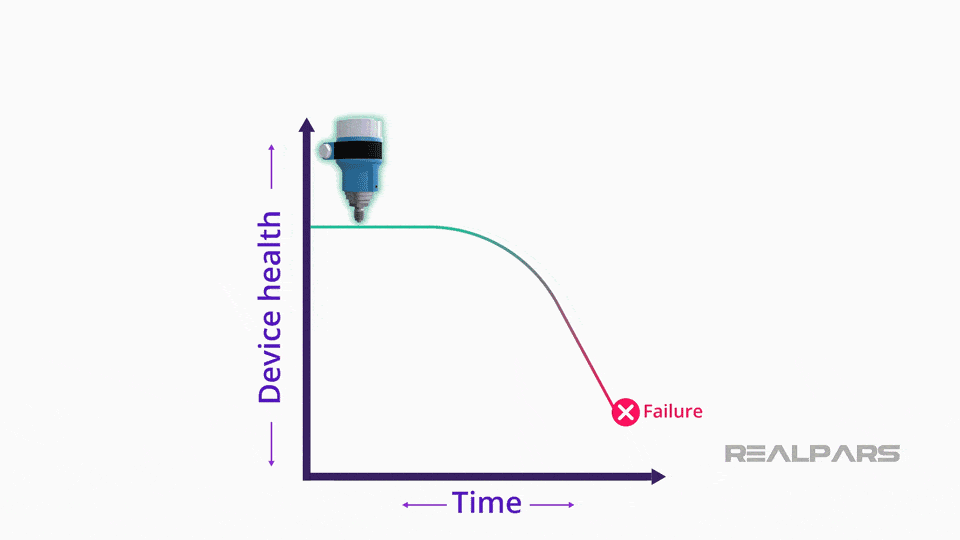
For example, you can check the pressure transmitter regularly and before it gets to the point of failure to make sure that there won’t be any sudden interruption to the industrial process.
However, this is not very cost-effective. Why, you ask? Because by performing the maintenance early, you waste device life that is still usable.
This is the time that we could still use the device without any maintenance but now we’re losing that because of early preventing maintenance.
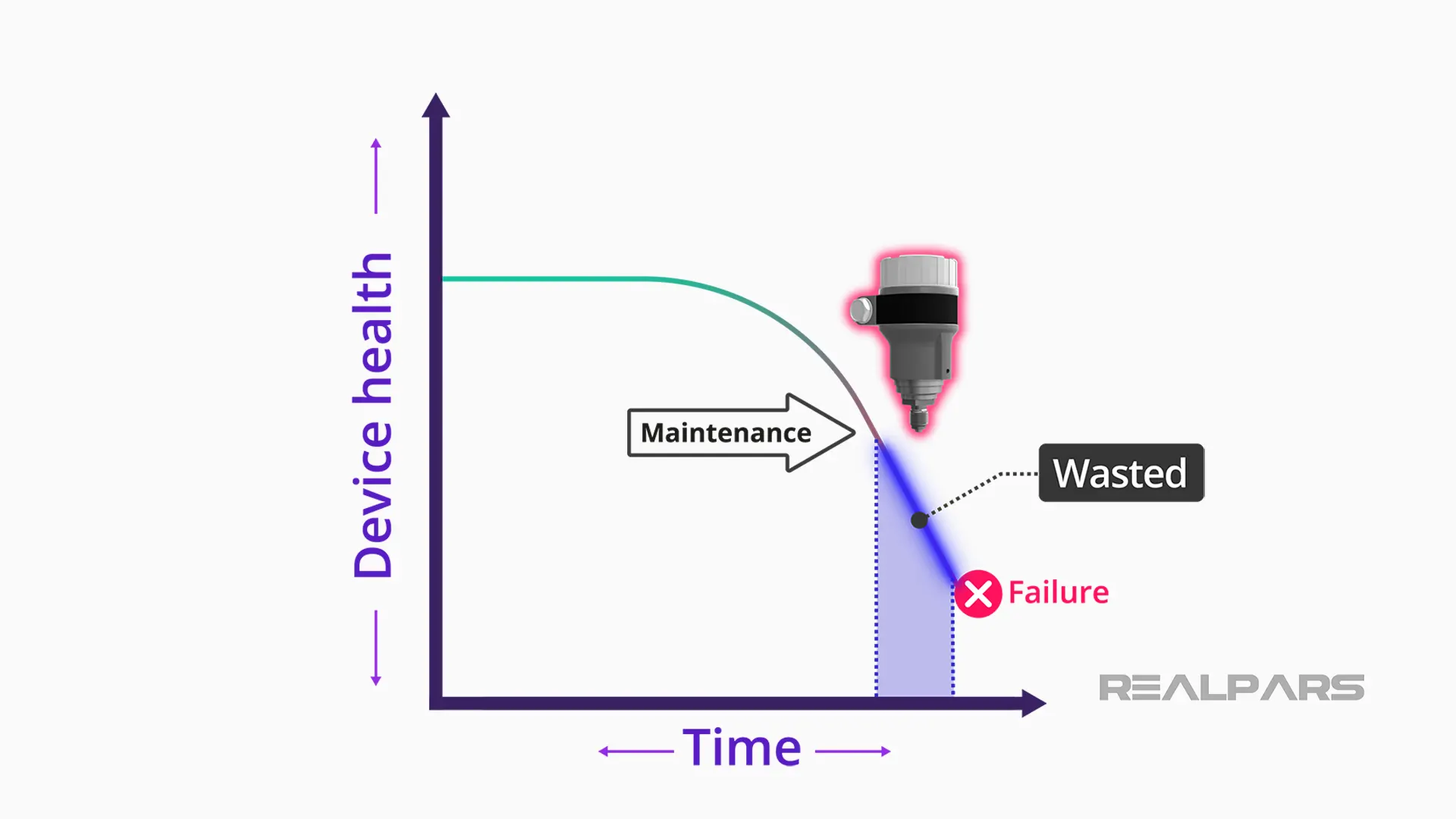
This is where predictive maintenance can help.
3. Predictive maintenance
As the name suggests, with predictive maintenance, you predict when the device fails and schedule maintenance just before that.
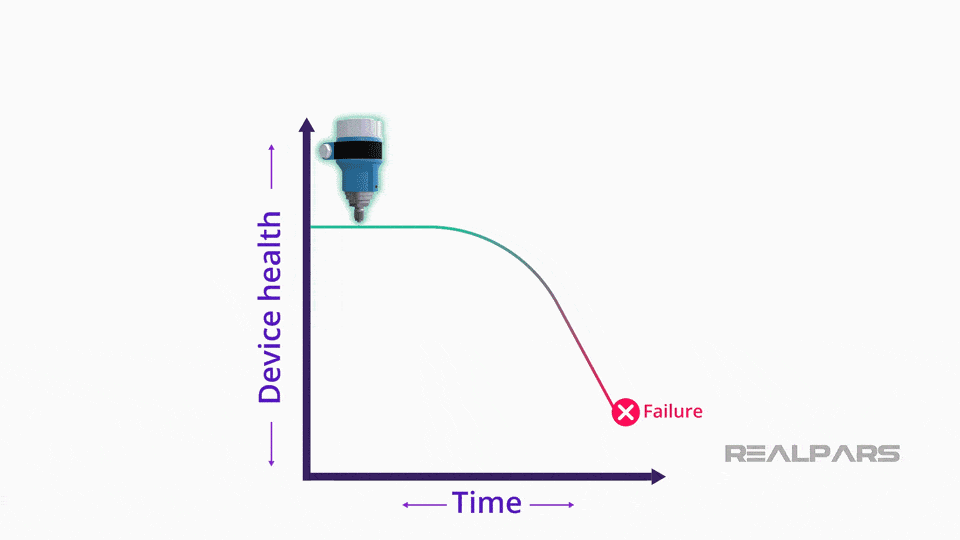
Following this process, you minimize the device or machine downtime and maximize its lifetime.
So with preventive maintenance, you solve the downtime issue and prevent it from happening but you lose on device lifetime, meaning the time you could use the device without any issue.
However, with predictive maintenance not only can you solve the device downtime issue, but there will also be little to no wasted device lifetime.
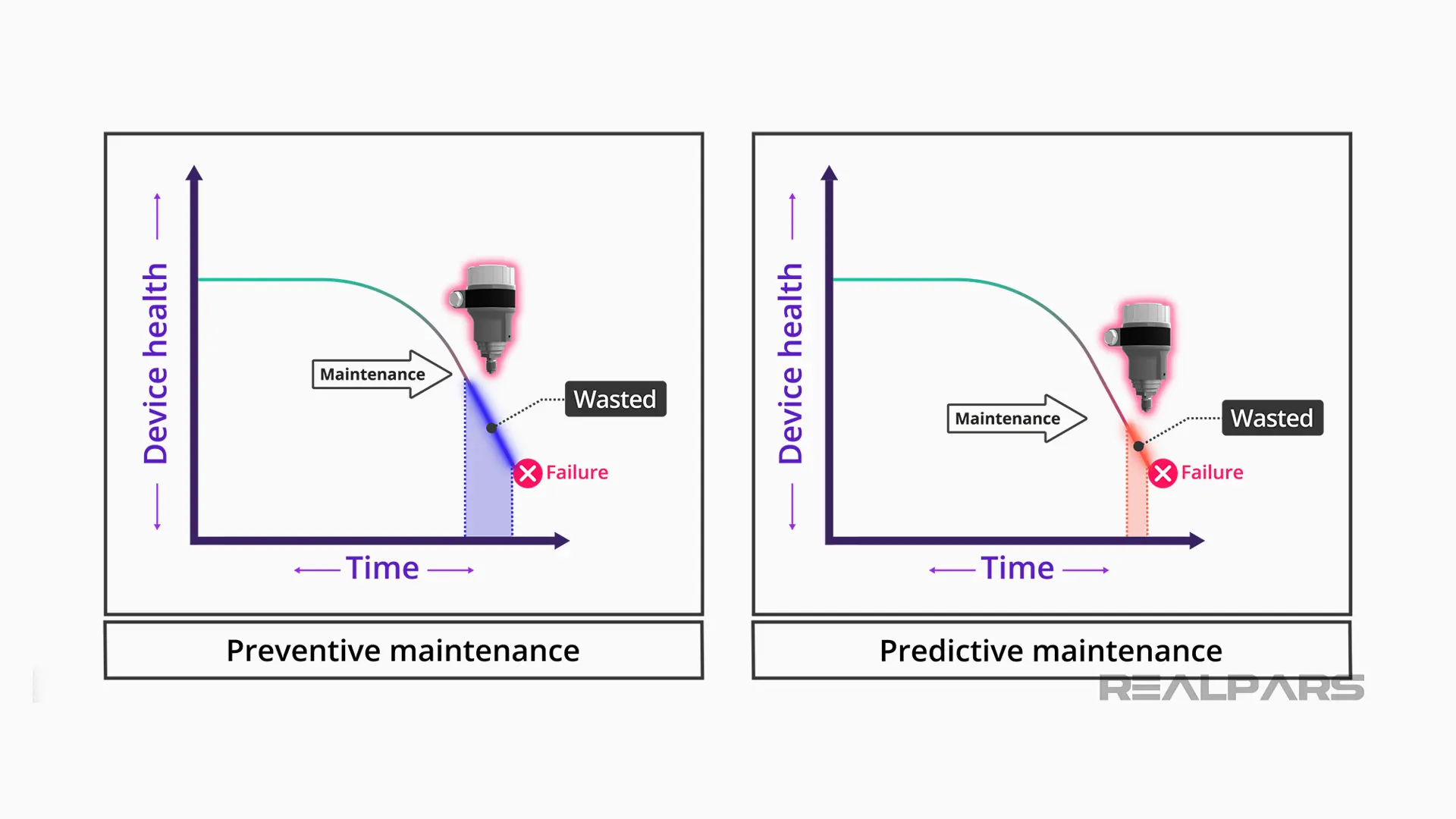
This is cool, right? It’s like you’re cheating 🙂 You know when the device might fail, you wait and play it cool, and then right before the device fails you perform maintenance on it.
Now, you may ask how we are doing this? How can we predict when a device fails? Well, this is simply done using the previous data that we have collected from a similar device in the past.
For instance, with the pressure transmitter example, there are already thousands if not millions of similar devices installed all over the world from the same brand. By analyzing the available data from these current devices, we can pretty accurately predict when a similar device fails.
The fancy term that we currently use or maybe overuse for utilizing this data is AI or Artificial Intelligence.
But, the basic principle comes down to analyzing historic and current data and making intelligent decisions for the future.
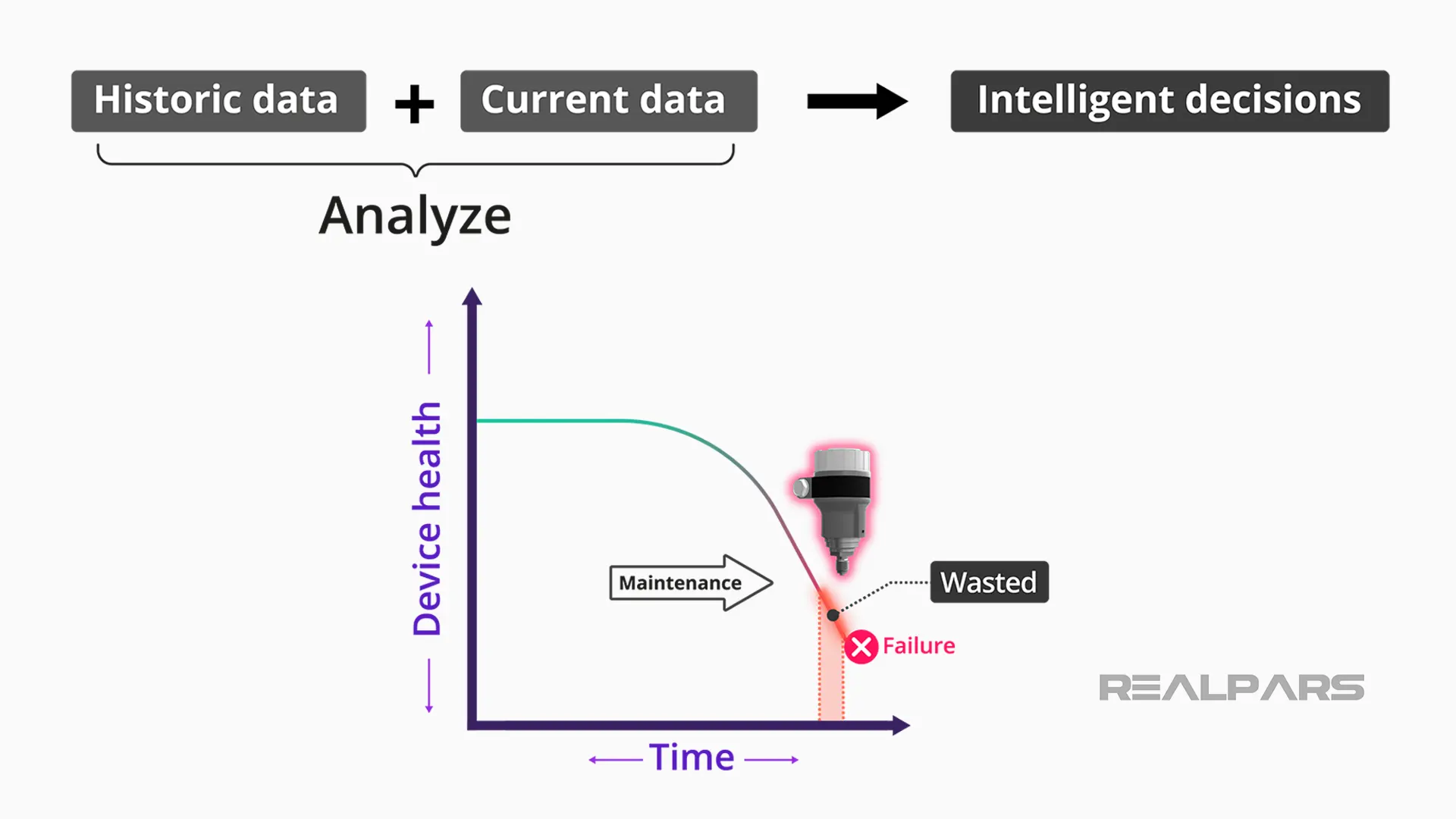
One of these intelligent or smart decisions that we can make is to predict when a similar new device will fail in the future and perform maintenance right before that, hence predictive maintenance!
Now, at the time of posting this article, we’re still at the beginning phases of this whole predictive maintenance stuff. You may argue that this will never work as accurately as it sounds on paper or it is very expensive to implement and you may be right my freind.
With all the recent years’ advancements, we, I mean people in industry, are still in the learning and adaptation phase of predictive maintenance so it may take a few years or maybe a couple of decades for us to properly transition from preventive maintenance to predictive maintenance but, hey, we’re getting there.
Predictive maintenance and human organs
It may be off the topic here but as I was working on this article I had some interesting thoughts that I’d like to share with you.
What if we could apply this whole concept of predictive maintenance to human body organs? I mean what if we could replace a heart before it fails for example? Could we then live forever? What if aging is a disease? Consider how the world would change if we could live forever?
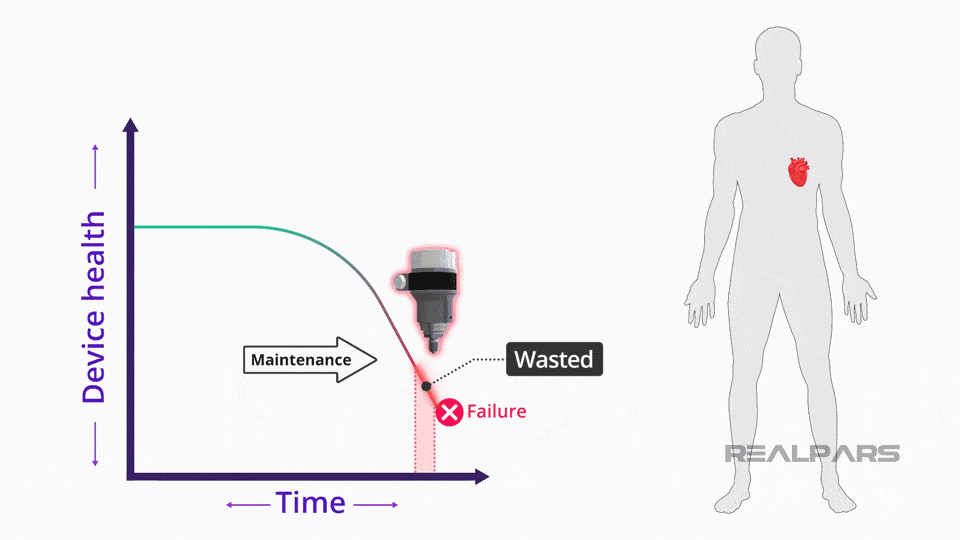
The plan that Elon Musk and SpaceX have started for making humans multi-planetary seems in line with living a considerably longer life. Let me know in the comments below what you think of this. Ok enough of crazy futuristic ideas. Let’s get back to the present time.
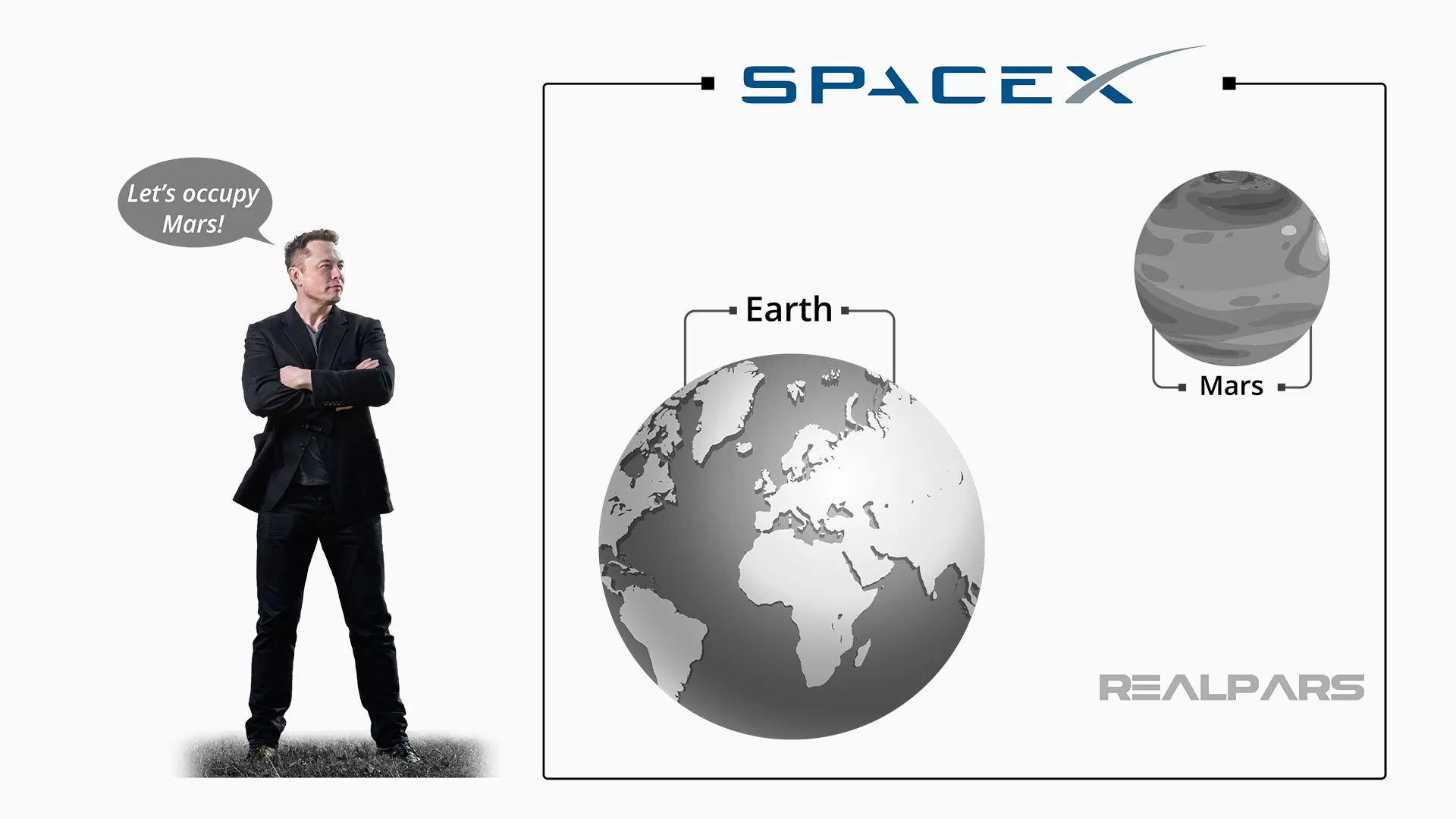
Summary
In summary, we have three types of maintenance. Reactive, preventive, and predictive.
– Reactive maintenance is when you wait until the device fails and then you fix it. This causes your production line to stop and results in financial losses.
– To prevent this, you can use preventive maintenance. This is when you perform regular checks and maintenance before the device fails. But the challenge with preventive maintenance is that by performing the maintenance early, you waste device life that is still useable.
– With predictive maintenance, however, you can predict when the device fails and schedule maintenance right before that. By doing this you can minimize the device or machine downtime and maximize the lifetime.
If you have any questions about Predictive Maintenance or about Maintenance in general, add them in the comments below and we will get back to you in less than 24 hours.
Got a friend, client, or colleague who could use some of this information? Please share this article.