RTD vs. Thermocouple: Which is Better for Your Needs?
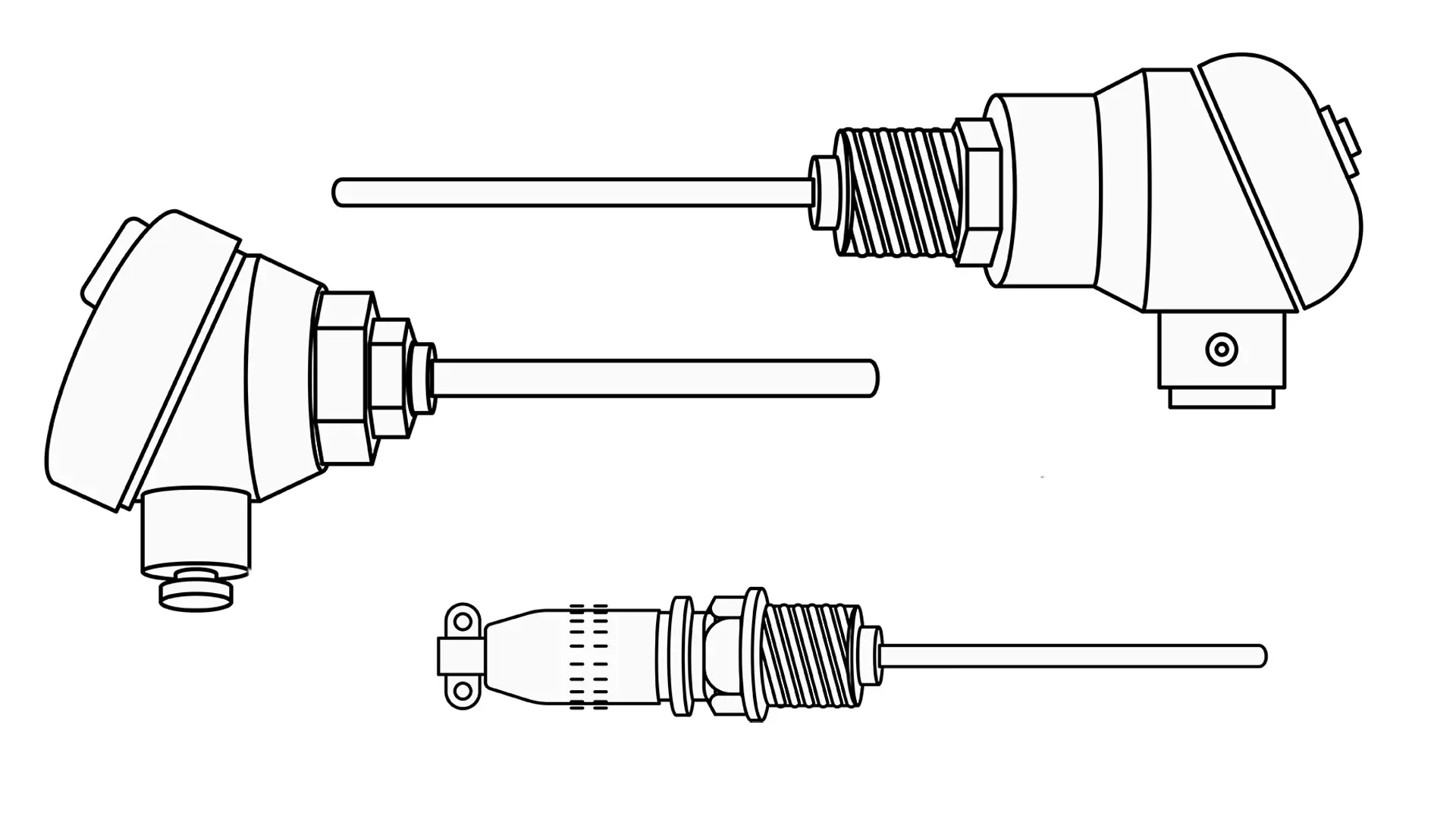
How do we measure temperature?
Temperature is an essential measurement for effectively monitoring and controlling various industrial applications.
Not ensuring accuracy, incorrect temperature measurement, and control can lead to insignificant and faulty temperature recordings.
Incorrect measurements can cause equipment failure, inferior quality of a product, and even severe risks to human health.
For example, controlling the right temperature in the food and beverage industry will ensure the food’s quality, flavor, and freshness. If the temperature monitored is not correct, the wrong temperature can lead to health risks for consumers.
Devices are used to measure the temperature accurately, depending on specific applications.
An example of two devices used in industry is thermocouples (T/C) and Resistance Temperature Detector (RTD).
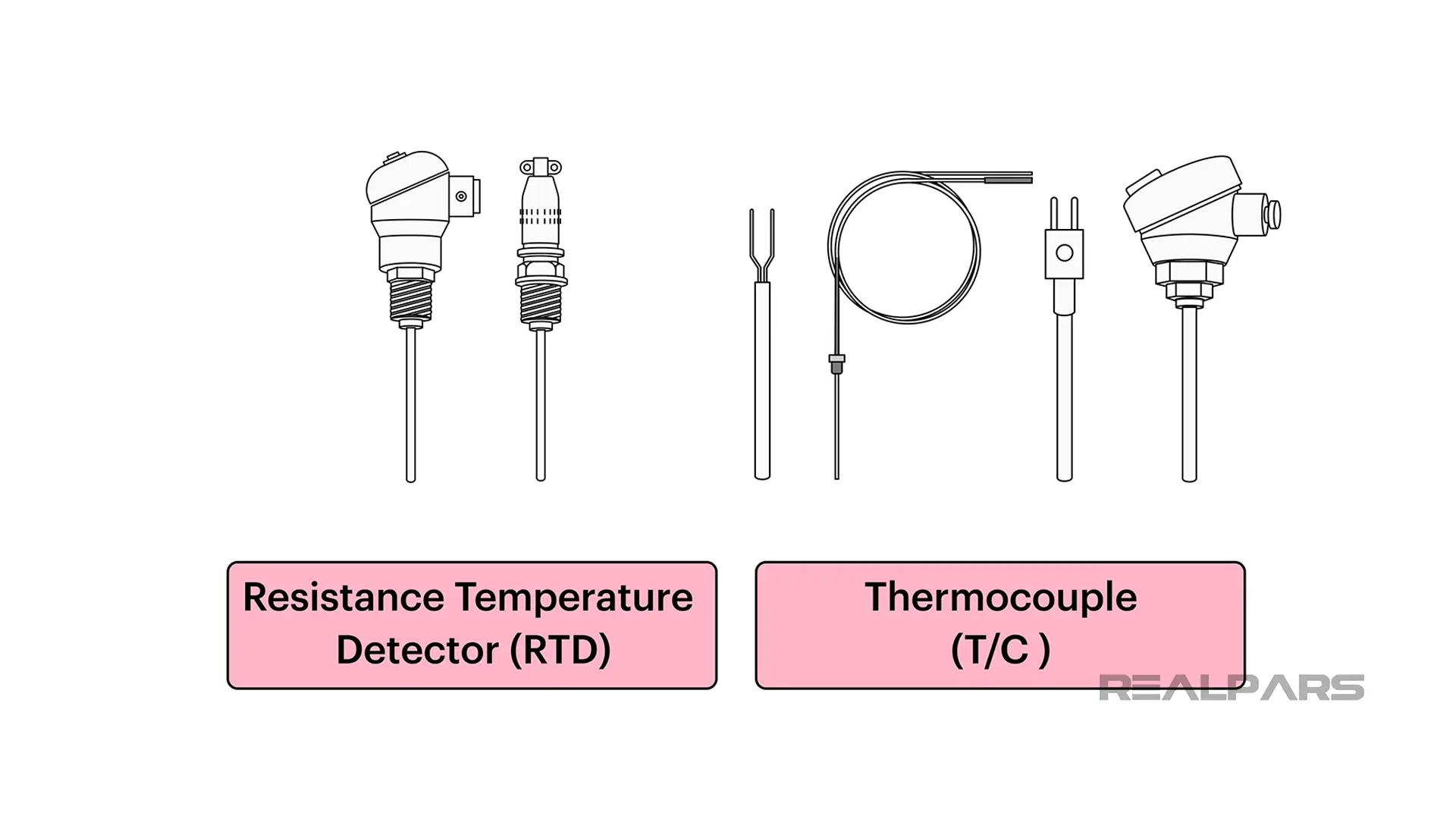
Basic characteristics of RTD and thermocouples
Definition of RTD and thermocouples
We will start by defining the Resistance Temperature Detector (RTD) sensors. The RTD can be constructed as a small coil made of a wire wound element as a precise value resistor, mainly around a glass or ceramic bobbin.
This construction will allow it to expand and contract over temperature ranges freely. The winding is generally done in helix or birdcage construction.
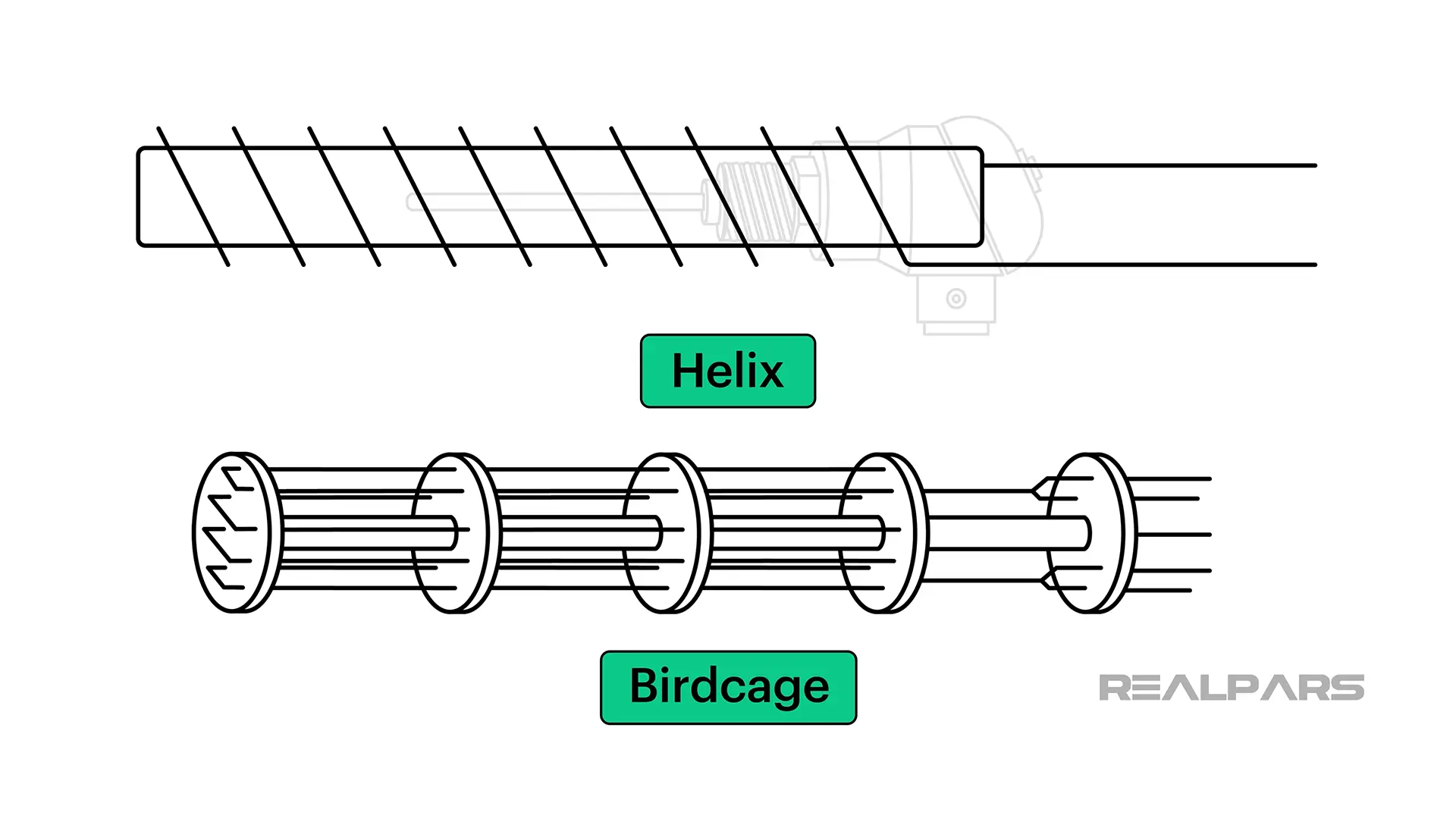
The RTD is also a passive device. It must be powered by an external electronic device to measure the resistance as the RTD temperature changes.
The electronic device generates a small electrical current through the RTD resistor sensor to generate a voltage output as the result of the measurement.
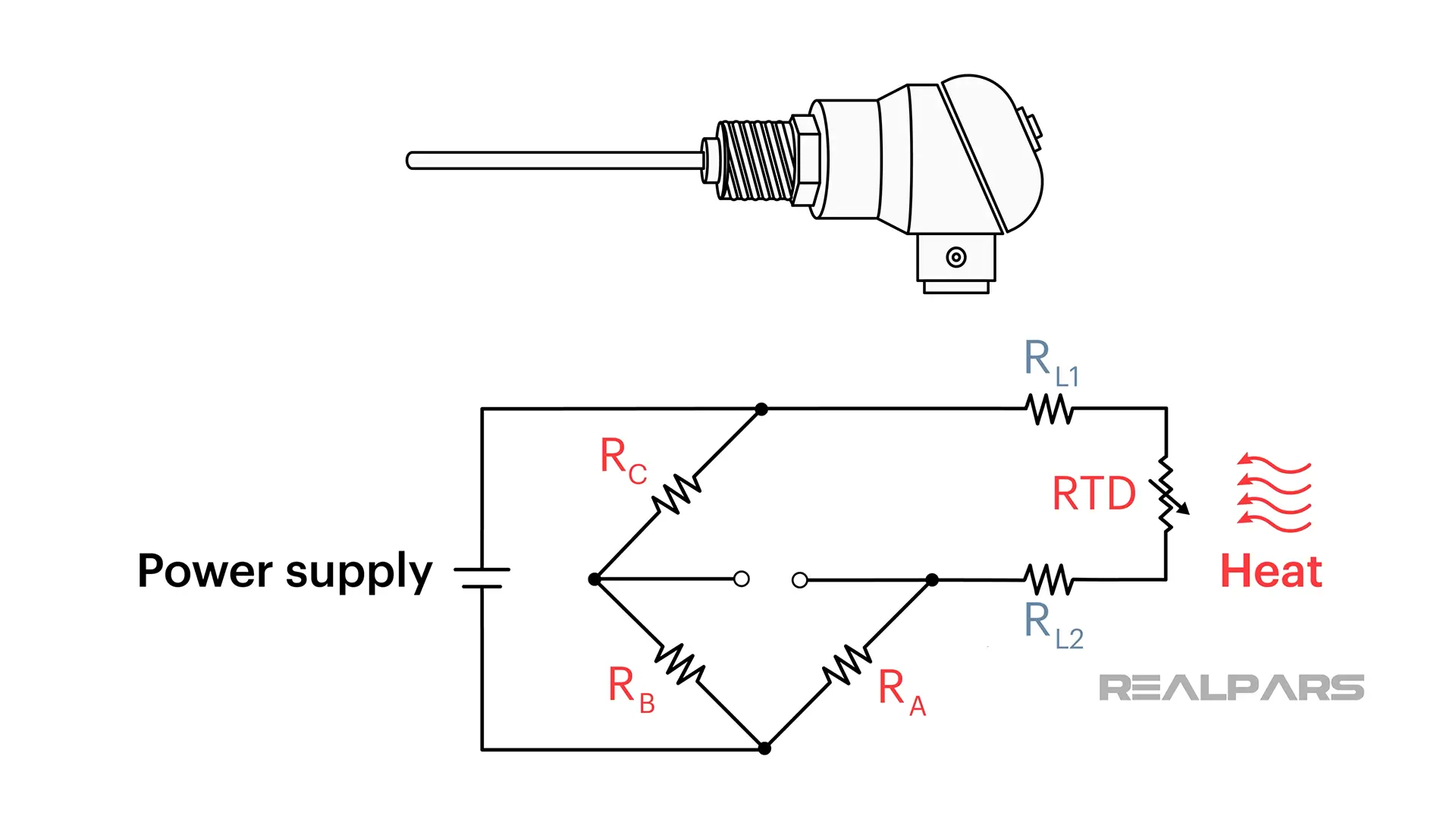
Next, let us define the thermocouple (T/C) sensors. The thermocouple is two different types of metals welded together at one end, creating a junction.
Therefore, when the junction of the two metals is heated or cooled, a small voltage is produced from the heating or cooling effects and can be correlated directly back to the temperature.
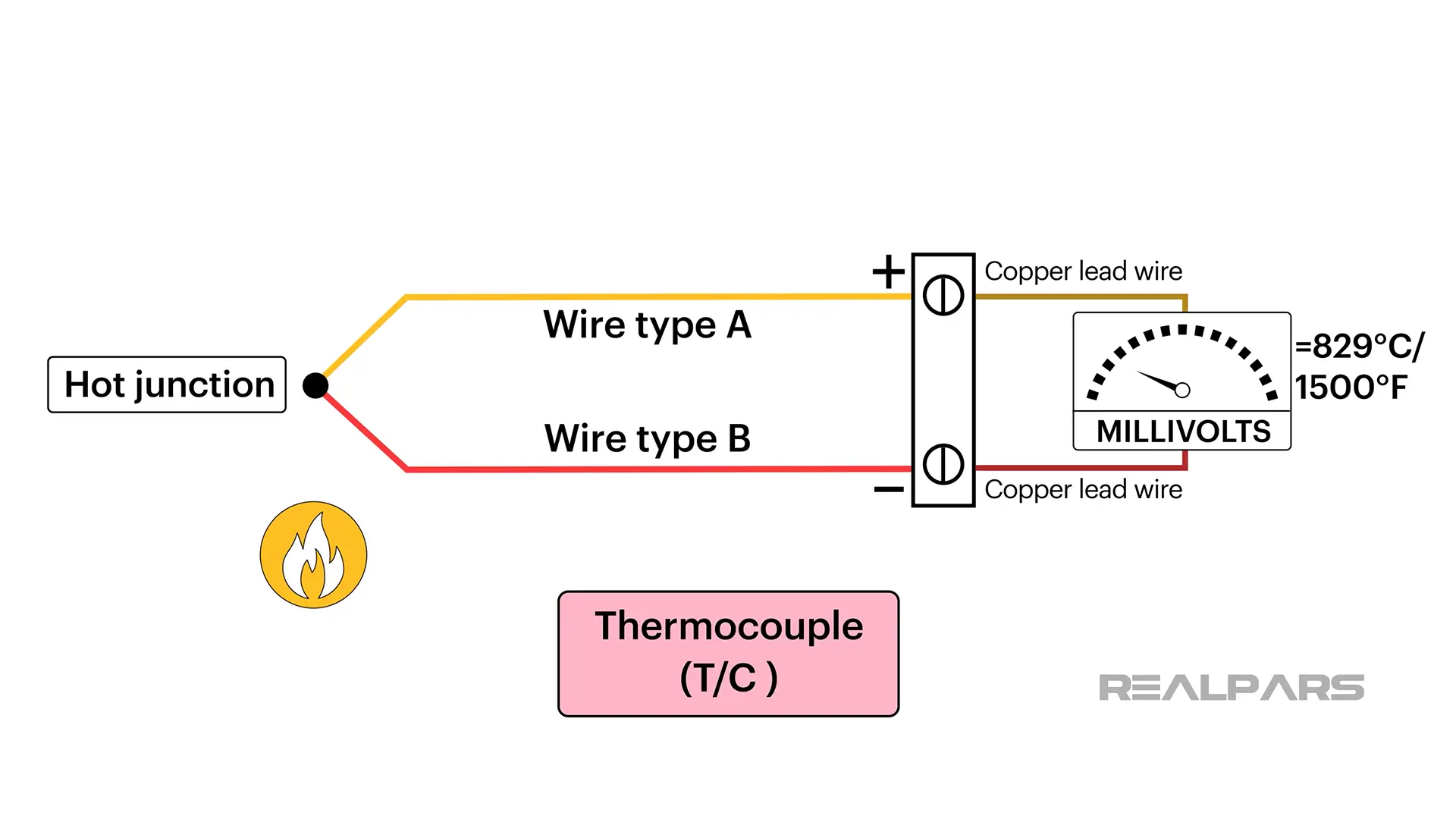
The thermocouple is an active device.
What materials are used to make an RTD or thermocouple sensor? For the RTD sensor, the most common elements used are nickel, platinum, or copper wire.
Materials used for RTD
Nickel has a high resistance to corrosion, making it ideal for use in harsh environments. It also has a relatively low cost compared to other materials, making it a popular choice.
However, nickel has a relatively High-temperature coefficient, which means that its resistance changes only rapidly with temperature.
Platinum, on the other hand, has a high-temperature coefficient, making it highly accurate for temperature measurement. It is also corrosion-resistant, making it ideal for use in harsh environments.
However, platinum is much more expensive than nickel, which can make it less desirable for some applications.
Finally, copper has a high electrical conductivity, making it ideal for use in applications where a fast response time is required. It is also relatively low in cost compared to platinum.
However, copper is not as corrosion-resistant as nickel or platinum, making it less suitable for use in harsh environments.
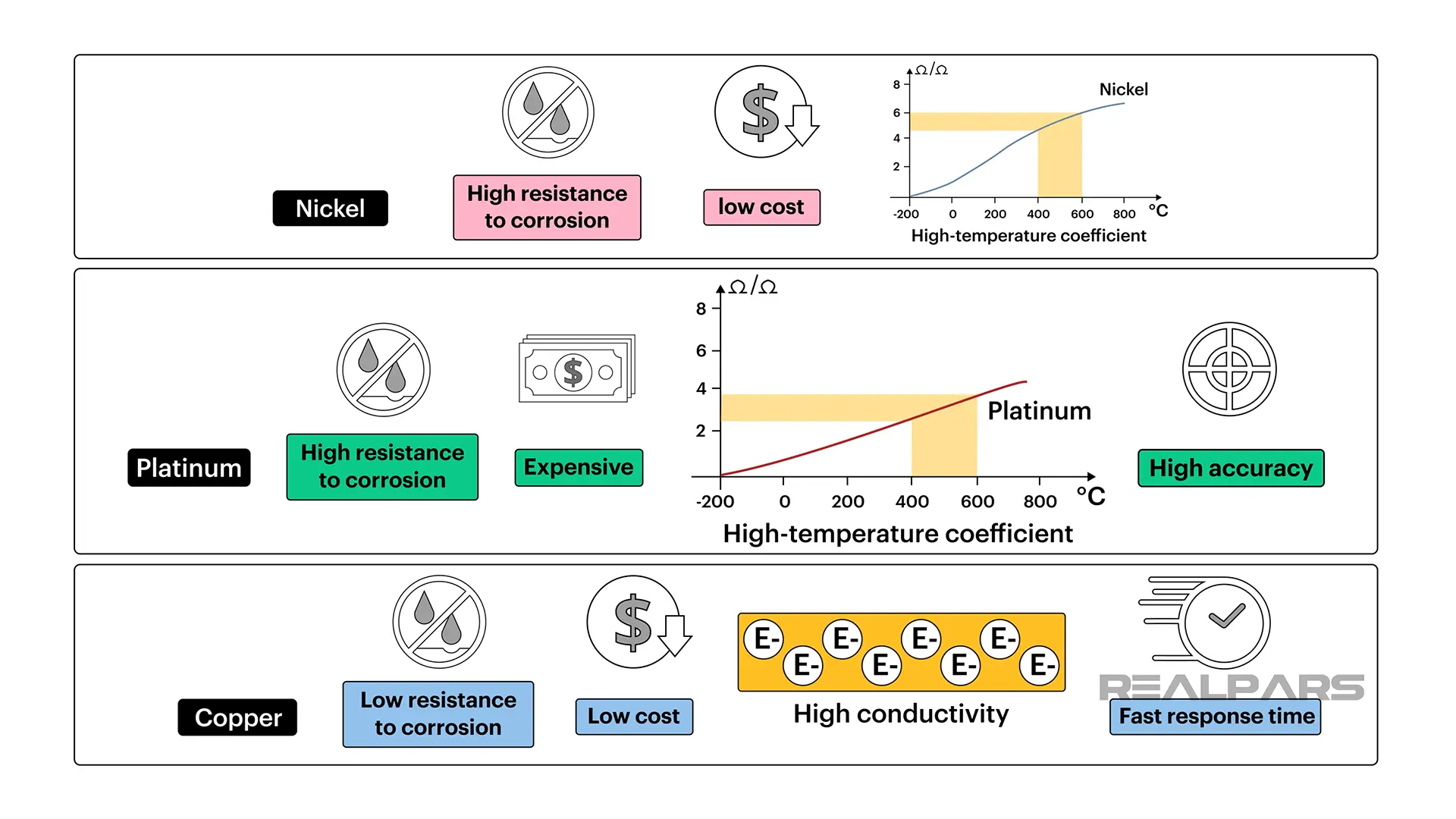
Materials used for thermocouple
As for the thermocouple sensor, different conductive metals will produce different levels of small voltage or charge.
The most common types of thermocouples are denoted by a lettering system, such as K, J, T, and E. Each letter refers to a specific combination of two different metals used in the thermocouple.
These metal combinations are selected for their unique characteristics, such as accuracy, response time, and temperature range.
For example, a K-type thermocouple is made of Chromel and Alumel metals and is often used in high-temperature applications like furnaces and boilers.
On the other hand, a J-type thermocouple is made of Iron and Constantan metals and is used in low-temperature applications like refrigeration systems.
The choice of the right thermocouple type depends on the specific application, so it’s essential to choose the right one to get accurate temperature readings.
Temperature range
The RTD and thermocouple sensors have a measuring range depending on the material type used and the application. An RTD can be used in temperatures ranging from -200 degrees Celsius to +850 degrees C.
In comparison, the thermocouple can measure from -250 degrees C to +1800 degrees C.
Accuracy and sensitivity
When we compare some of the most common features of RTD and thermocouple temperature sensors, we find, as shown by the chart, some of the PROS and CONS.
So, what are some of the pros and cons of RTD and thermocouples to be considered before making your selection?
Here are just a few points to consider before you select the RTD or a thermocouple,
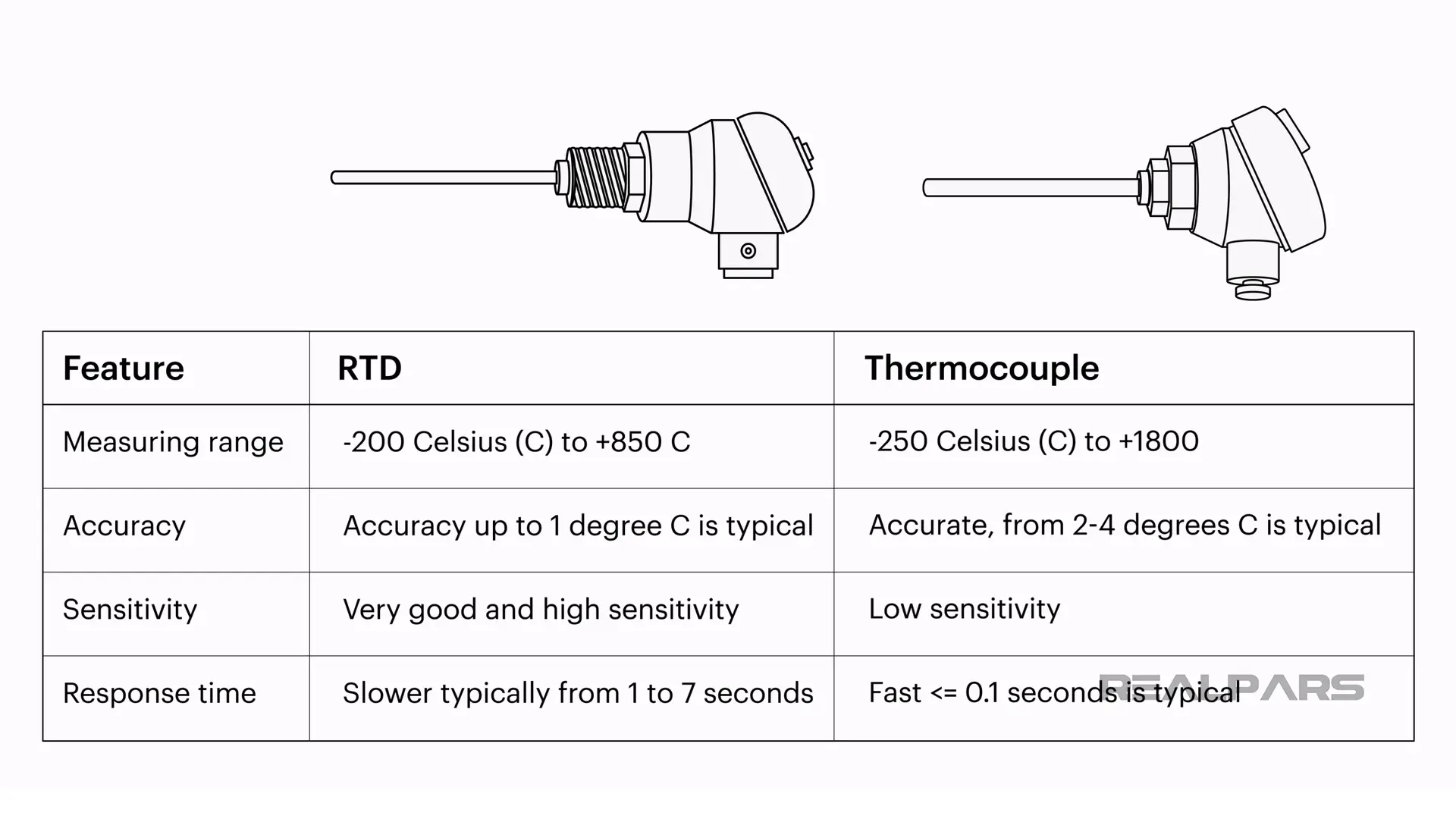
For example, the measuring range for an RTD is between -200 degrees C and +850 degrees C, but for a thermocouple, this is -250 degrees C to 1800 degrees C.
So if you need to measure a temperature that can go as high as 1000 degrees C, then thermocouple is the sensor you can choose. Or, if you need more sensitivity, RTD is a better option.
Response time refers to the amount of time it takes for a temperature measuring device to indicate a change in temperature after the temperature has actually changed.
In the case of RTDs (Resistance Temperature Detectors) and thermocouples, response time can vary based on several factors, including the size and material of the device, the surrounding environment, and type of thermometer used.
Generally, RTDs have a slower response time than thermocouples but are more accurate over a wider temperature range.
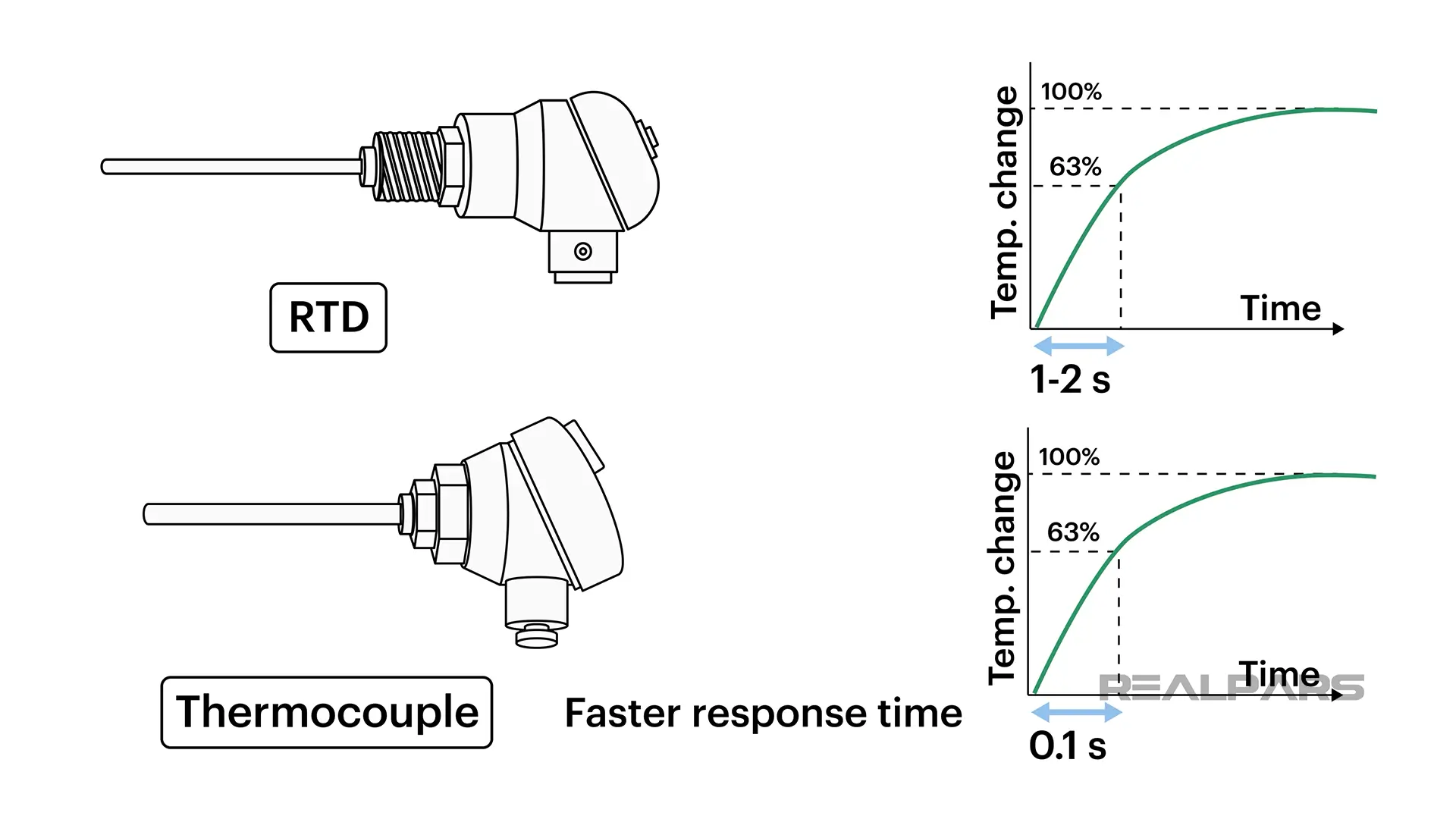
In high-temperature applications, thermocouples tend to have a faster response time, but their accuracy can be affected by electromagnetic interference.
In order to choose the appropriate temperature-measuring device, it is important to consider the specific requirements of the application, including the required accuracy, temperature range, and response time.
These are just a few of the most common features. Always refer to the data sheets for each temperature sensor before selecting it.
Advantages and disadvantages of RTD and thermocouples
So, what are some of the pros and cons of RTD and thermocouples to be considered before making your selection?
Here are just a few points to consider before you select the RTD or a thermocouple,
PROS of the RTD
– RTDs can measure lower ranges,
– RTD is more accurate,
– RTD output is linear.
CONS of the RTD
– RTD is more expensive,
– RTD is unsuitable for temperatures over +850 degrees Celsius or, in other words, 1562 degrees Fahrenheit,
– RTDs have a slower reaction time as related to temperature changes.
And these are some thermocouple points to consider,
PROS of the thermocouple
– Thermocouple is cheaper than RTD,
– Thermocouples can measure a higher range,
– Thermocouple reaction time is faster.
CONS of the thermocouple
– The output of the thermocouple is non-linear,
– Thermocouple has poor accuracy,
– Thermocouples have poor stability with output results.
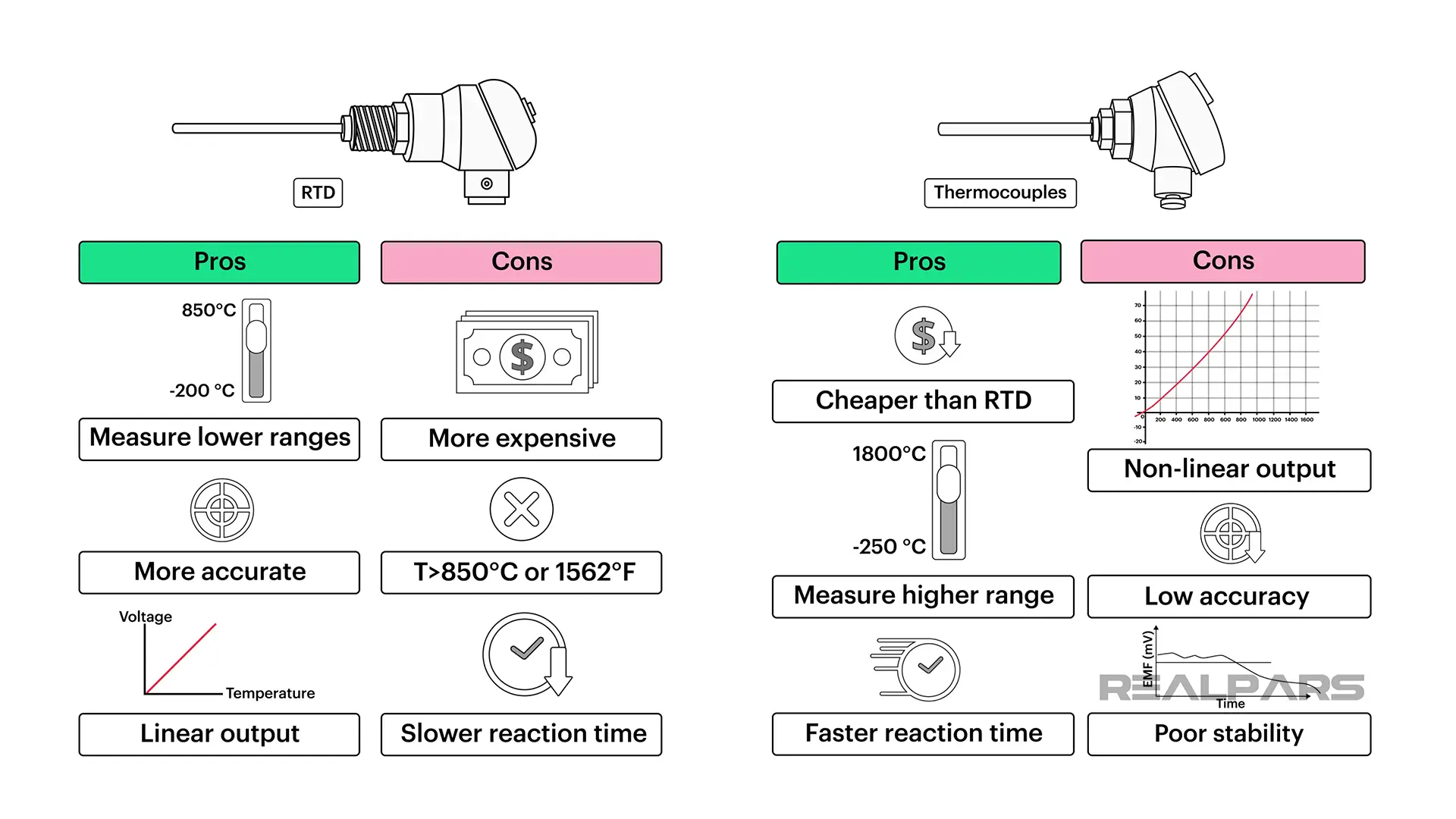
When to use RTD and thermocouples
In applications where you require the highest accuracy, where cost is not a concern, and your measuring temperature is less than +800 degrees C, then the choice of an RTD is the best one.
And as for thermocouples, where temperatures exceed +800 degrees C, then your best sensor would be the thermocouple. Many factors should be looked at first before choosing the correct sensor for your application.
Here are some factors to consider when choosing a sensor for your control application:
– The measuring range of your application,
– Measurement accuracy you will need from your application,
– The measurement drifts over time of use,
– Single-point measurement narrowed down to the exact spot,
– Sensitivity of the sensor,
– Cost of the sensor.
These are just a few factors for consideration before making your decision.
Real-world examples
We mentioned at the beginning of this article that RTD and thermocouples could be found in all types of industrial applications, like the food and beverage industry controlling the process of temperatures in ovens, heaters, and freezers.
They can also be found as close as in your automobile, monitoring the exhaust gas temperature of your tailpipe, engine temperatures sensor, and even your engine oil temperature.
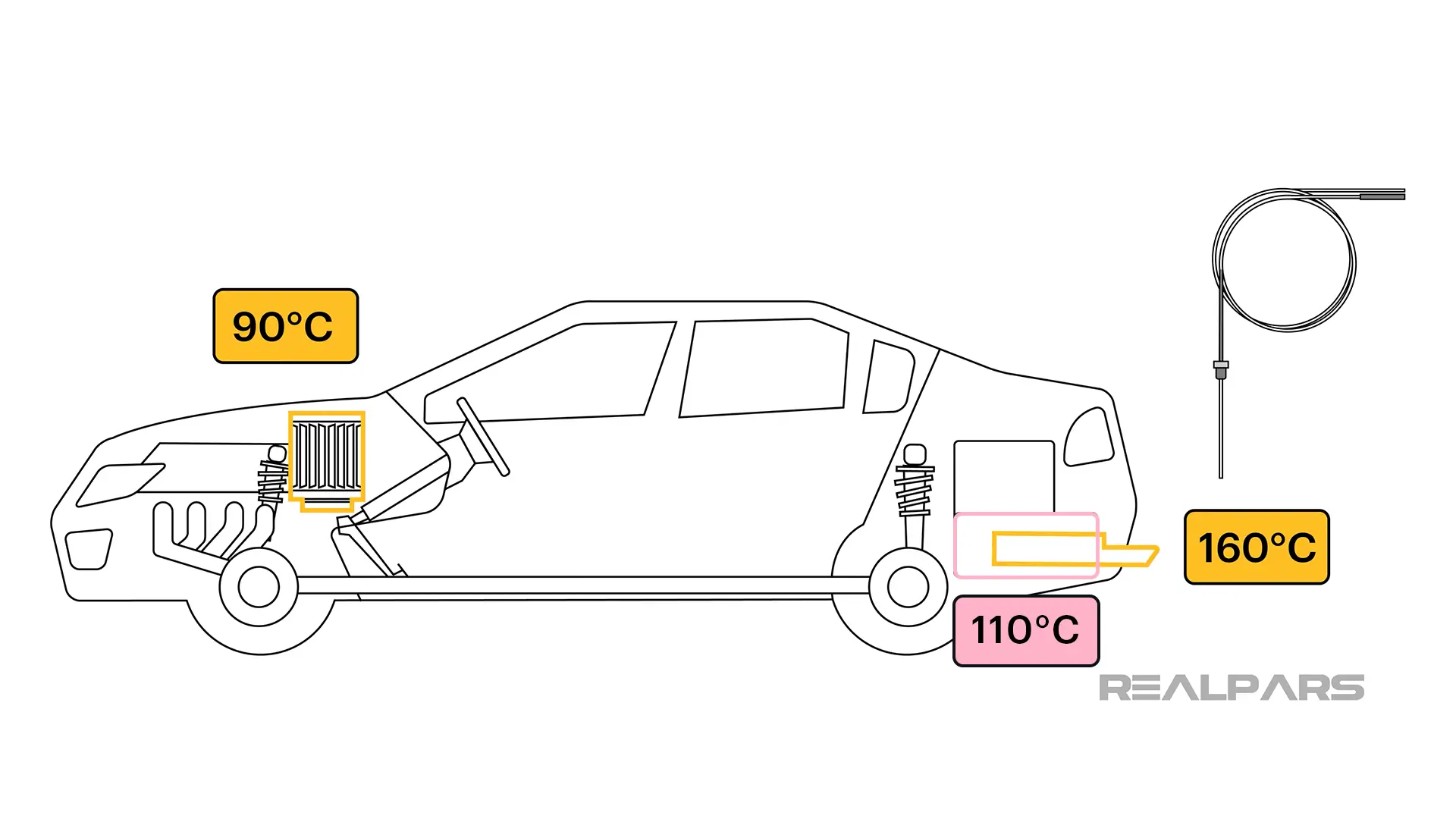
Conclusion
These are just a few considerations the design Engineer must consider before deciding.
In conclusion, in this article, you learned the difference between RTDs (Resistance Temperature Detectors) and thermocouples for temperature sensing applications. Here are the key takeaways from this article for you:
Accuracy: RTDs are more accurate than thermocouples in temperature measurement. RTDs have a temperature accuracy of ±0.5°C, while thermocouples have an accuracy of ±2°C.
Temperature Range: Thermocouples have a wider temperature range compared to RTDs and can measure temperatures from -250°C to +1800°C, while RTDs can measure temperatures from -200°C to +850°C.
Response Time: Thermocouples have a faster response time compared to RTDs, with RTDs having a slower response time of 1-2 seconds.
Cost: Thermocouples are less expensive than RTDs, making them the preferred option for applications that do not require high accuracy or where cost is a major concern.
Stability: RTDs are more stable and long-lasting compared to thermocouples, as RTDs are made of high-quality materials and are less susceptible to damage.
As you can see, both RTDs and thermocouples have their advantages and disadvantages, and the choice between the two depends on the specific requirements of the temperature sensing application.
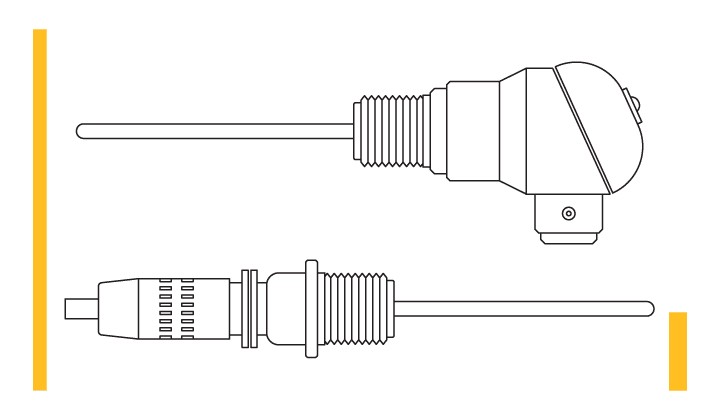
Ready to take the plunge into RTD knowledge?
The Complete Introduction to RTDs course on RealPars is your perfect guide. Designed for all skill levels, it’s an easy-to-follow class that will teach you everything you need in no time!
In this comprehensive lecture series, we’ll take each one of these crucial stages step-by-step: from installation, calibration, and maintenance all the way through troubleshooting.
Frequently asked questions
Learn from Industry Experts
With a 7-day trial, then €35/month