What is the Difference between VFD and Soft Starter?
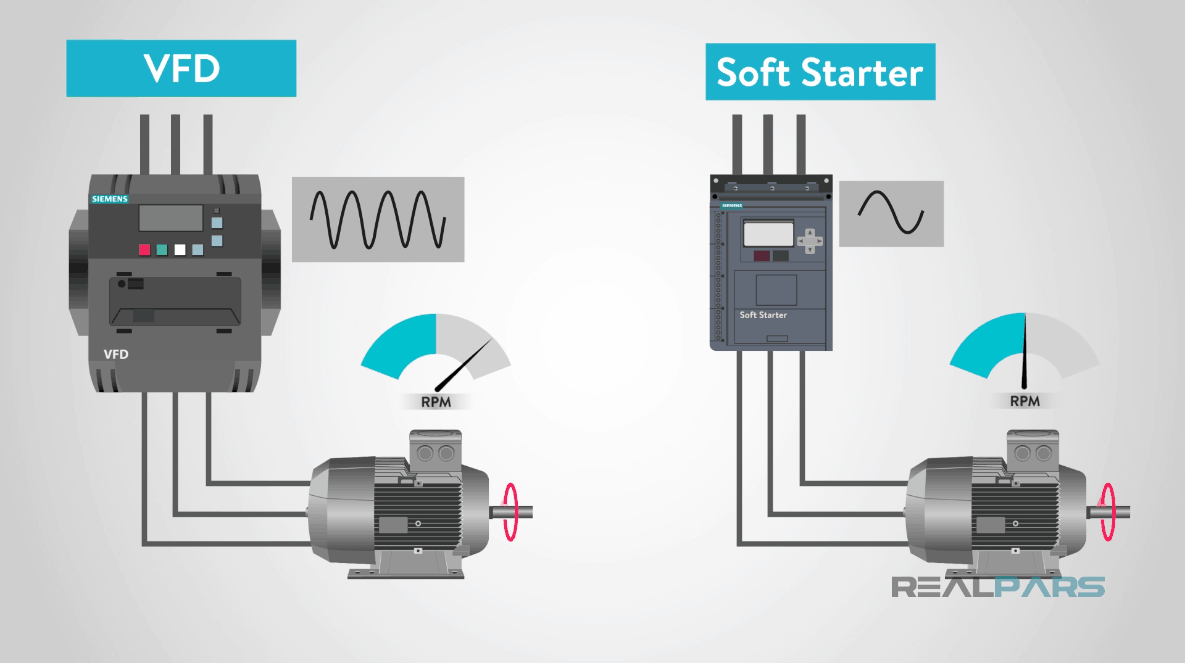
In previous articles, we have talked about variable frequency drives (VFD) and soft starters. If you need a refresher on the detailed working of either a VFD or Soft Starter be sure to look back at those articles by clicking the links below.
The devices are similar in that they control the starting and stopping of industrial motors but have different characteristics that we will identify in this article.
The Basics
A soft starter is generally used in applications where there is a large inrush of current that could damage a motor while a VFD controls and can vary the speed of a motor.
In this article, we will look at:
– Internal workings of these devices
– How to determine which device you might want
– Look at some applications to better understand their differences
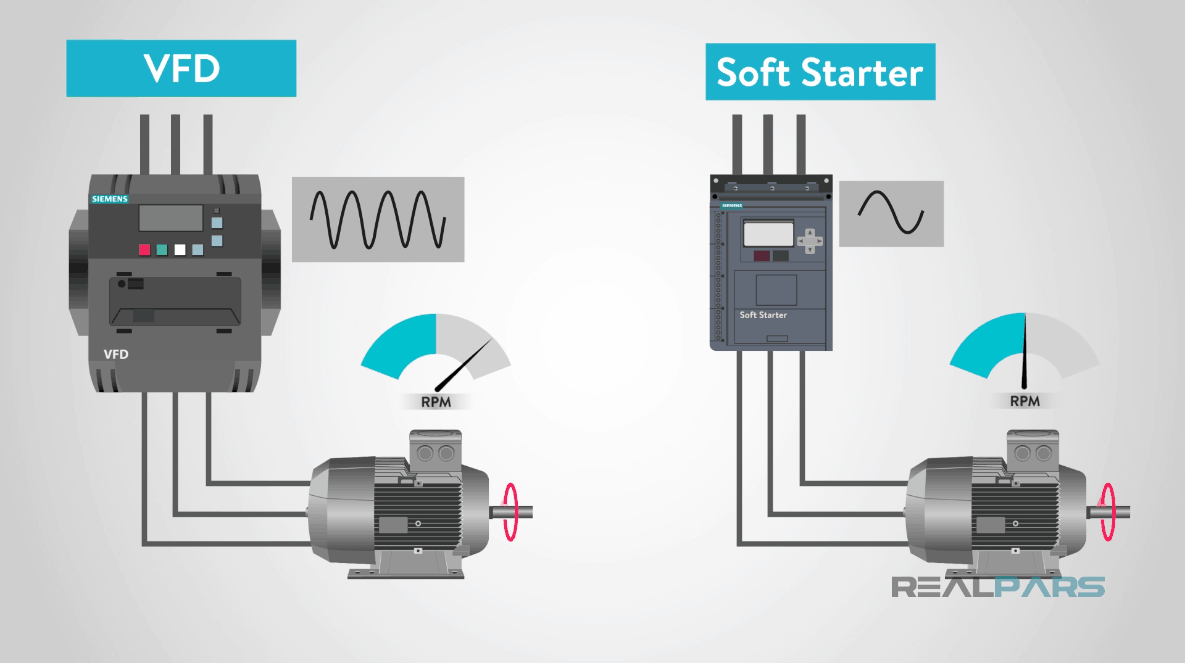
Let’s first talk about the internal working of these two devices.
Internal Workings of a Soft Starter
A typical three-phase soft starter uses six Thyristors or Silicon Controlled Rectifiers, oriented in an anti-parallel configuration to start the electric motors smoothly.
A Thyristor is made up of 3 parts:
– Logic gate
– Cathode
– Anode
When an internal pulse is applied to the gate, it allows current to flow from Anode to Cathode which then sends current out to our motor.
When the internal pulses do not apply to the gate, the SCRs (Silicon Controlled Rectifier) are in the OFF state and therefore they restrict the current to the motor.
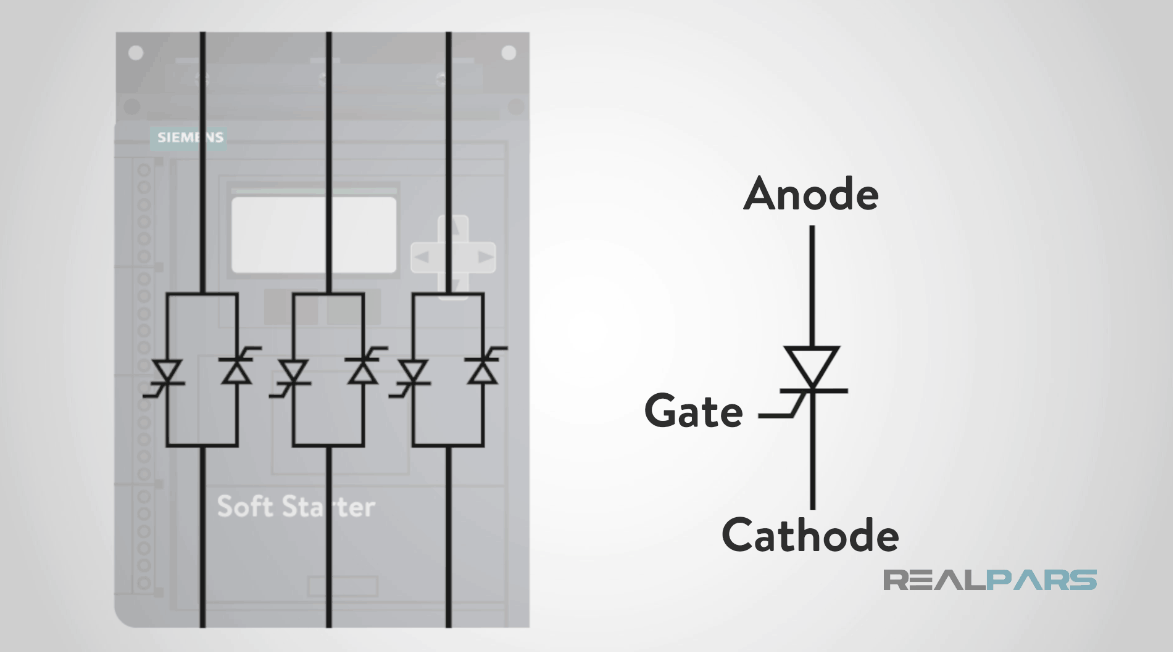
These internal pulses limit the applied voltage to the motor slowing down inrush current.
The pulses are sent based on ramp time so the current will be slowly applied to the motor. The motor, attached to the soft starter, will start up at a nice smooth current and top out at the preset maximum speed.
The motor will stay at that speed until we stop the motor where the soft starter will ramp down the motor in a very similar way as the ramp up.
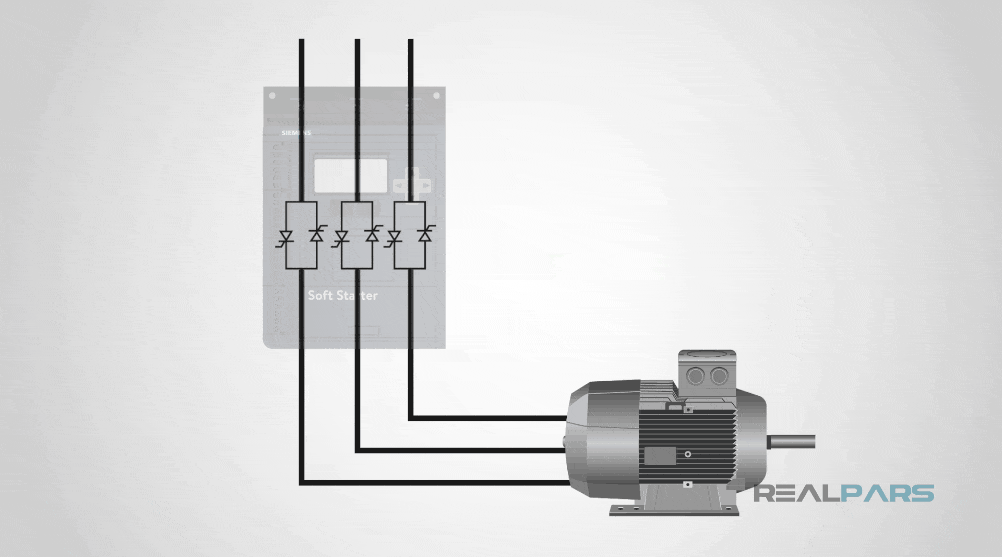
Internal Workings of a VFD
VFDs have three main components:
– Rectifier
– Filter
– Inverter
The Rectifier acts like Diodes, takes the incoming AC voltage and changes it to DC voltage.
Next, the Filter uses Capacitors to clean the DC voltage making it a smoother incoming power.
Finally, the Inverter uses transistors to convert the DC voltage and sends the motor a frequency in Hertz. This frequency drives the motor to a specific RPM.
We can set the ramp up and down times just like in a soft starter.
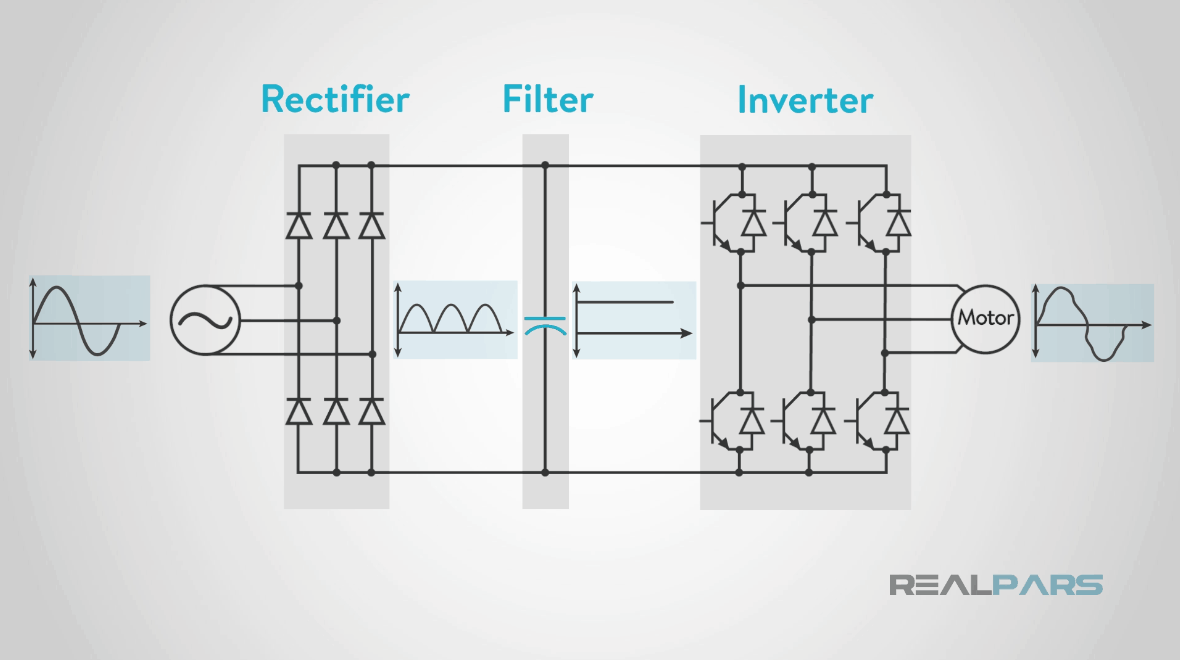
VFD or Soft Starter? Which One should I Choose?
From what we just covered, we can see that a VFD is basically a soft starter with speed control. So how do we know which device is needed for our application?
The decision on which device you choose comes down to how much control your application requires. There are other factors that we should consider in our decision.
1. Speed Control
If your application requires a large inrush of current but does not require speed control, then a soft starter is the best option.
If speed control is required, then a VFD is a must.
2. Price
Price can be a determining factor in a lot of real-world applications. Since a soft starter has fewer control features, the price is lower than a VFD.
3. Size
Finally, if the size of our device is a determining factor, soft starters are generally smaller than most of the VFDs.
Now, let’s look at some real-world applications to help us see the difference between a VFD and a Soft Starter.
Application Example of VFDs and Soft Starters
1. Water Treatment Facility
The first application will be a wastewater pump. A water treatment plant typically has a constant flow of water coming into the plant. Let’s assume the demand for water exiting the plant is constant with the supply entering the plant.
Which device would be the best option?
That’s right! A soft starter would be a great choice because in this application when starting the water pump there would be a large inrush of current on our motor that our soft starter could handle and gradually ramp up the pump.
Since the demand for water exiting the plant is the same as supply into the plant the speed of our pump would not vary.
However, if the demand for water exiting the plant raises or lowers, we would want to vary our speed making a VFD a better choice for the application.
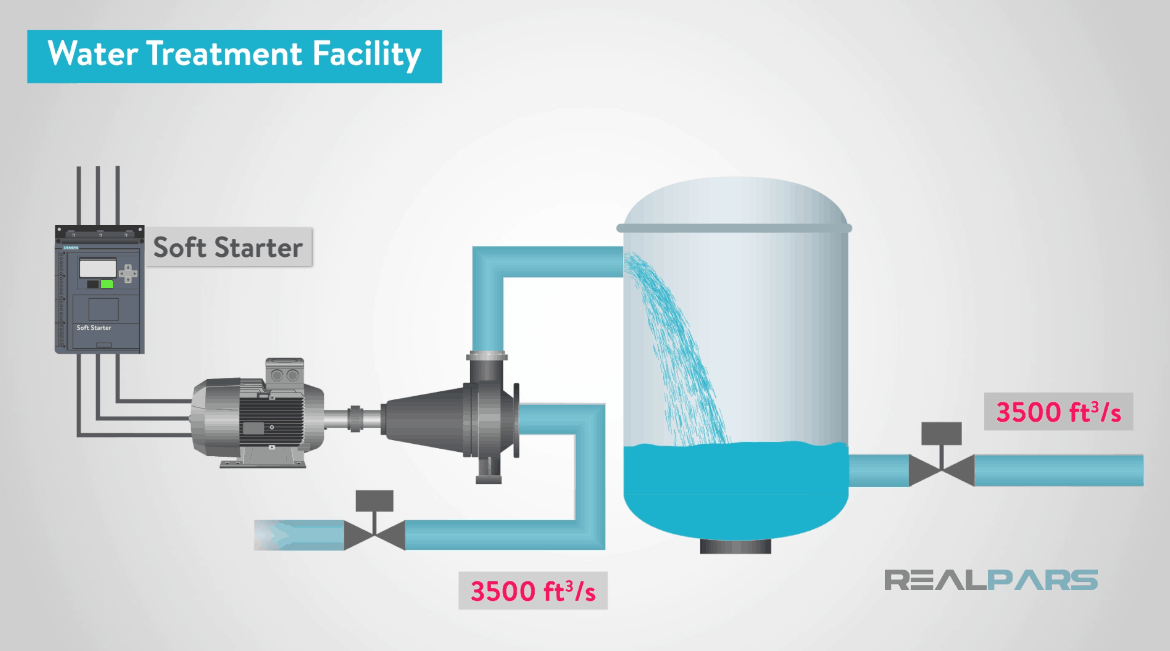
2. Cooling Fan System
The next application we will look at is a cooling fan.
In this scenario, a cooling fan will turn on when the plant air temperature hits a high-temperature set-point.
Once the set-point is reached, the cooling fan will slow down to maintain the air temperature unless it drops below a low-temperature setpoint, where it will shut off.
However, if the temperature continues to rise and pass the high-temperature setpoint, the fan will need to move faster.
Which device would work best in this situation?
That’s right! A VFD would be better than a soft starter because the speed of the fan will need to vary.
If our scenario was only turning the fan on or off based on temperature and not changing speed, then a soft starter would be a better option.
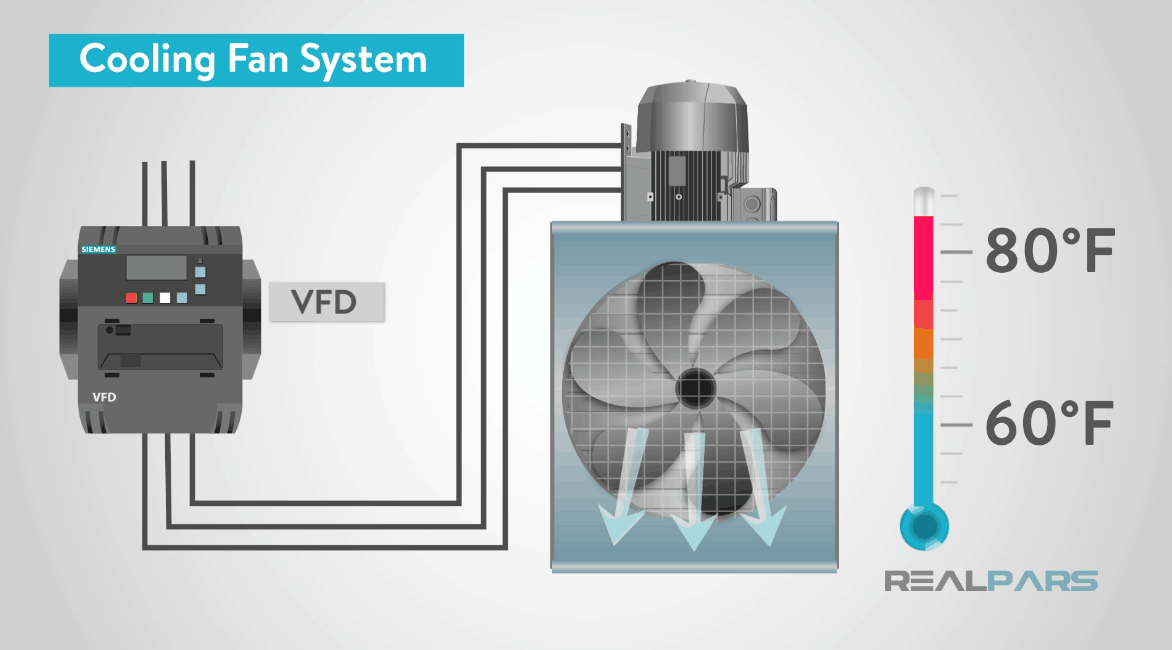
Summary
In closing, a VFD and a Soft Starter can do similar functions when it comes to ramp up or down a motor.
The main difference between the two is that a VFD can vary the speed of a motor while a soft starter only controls the starting and stopping of that motor.
When faced with an application, price and size are in the favor of a soft starter. A VFD is the better choice if speed control is required.
The good news is that if an existing application has a soft starter in place and speed control is later determined to be a requirement, a VFD can easily replace a soft starter. The opposite is true as well, a soft starter can replace a VFD.
Got a friend, client, or colleague who could use some of this information? Please share this article.
The RealPars Team
Frequently asked questions
Learn from Industry Experts
With a 7-day trial, then €35/month