In this article, we will explain what interlocks are. We will describe the different types of interlocks and give a few examples. After reading this article, you should understand what an interlock is and how to use it while programming and also designing systems.
What is an Interlock?
Interlocks are defined as a way to prevent something from happening in a system.
A simple example of an interlock is pushing the brake pedal or clutch in your car before shifting it into drive or first gear. You need to press on the brake pedal to release the shifter into the drive position to prevent the car from lurching forward.
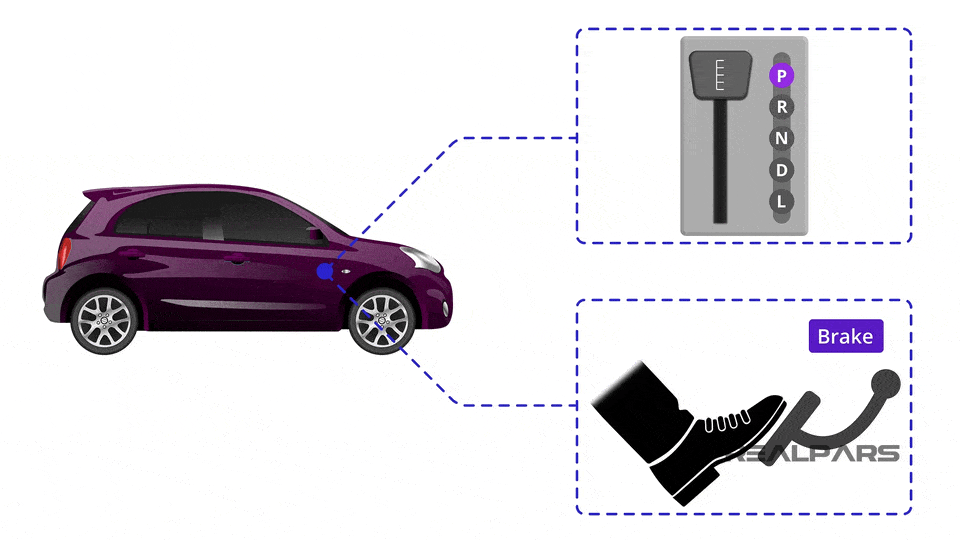
Different Types of Interlocks
There are two main types of interlocks: safe and non-safe.
Some systems require safe and non-safe interlocks to create a control system.
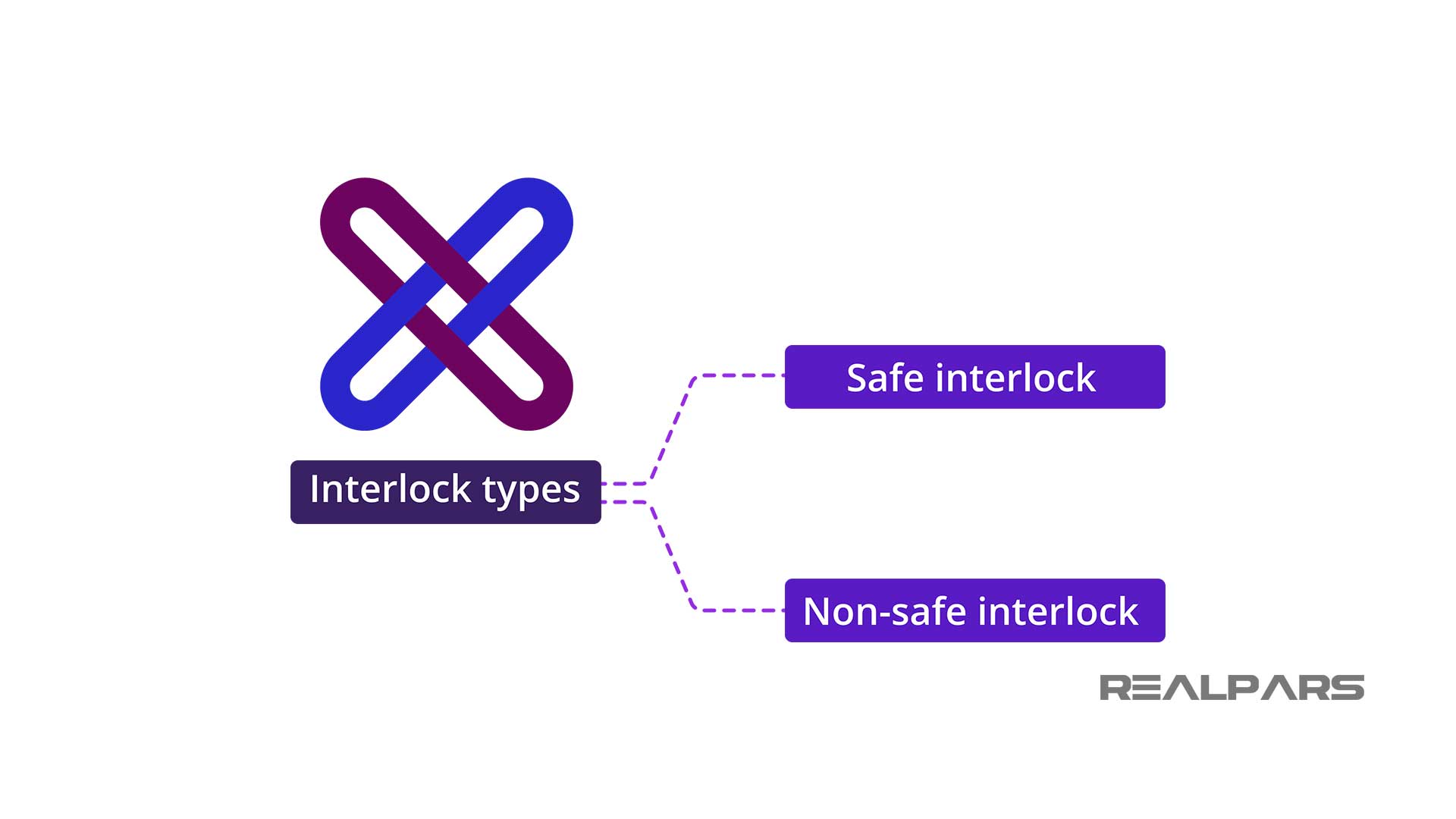
1) Safety interlocks
Safety interlocks are redundant designs. Be sure to read the RealPars article, What is a Safety PLC?, to understand how a safety PLC works.
The safety interlock shows how a programming instruction looks. These interlock devices prevent people or things from receiving harm while the machine is running.
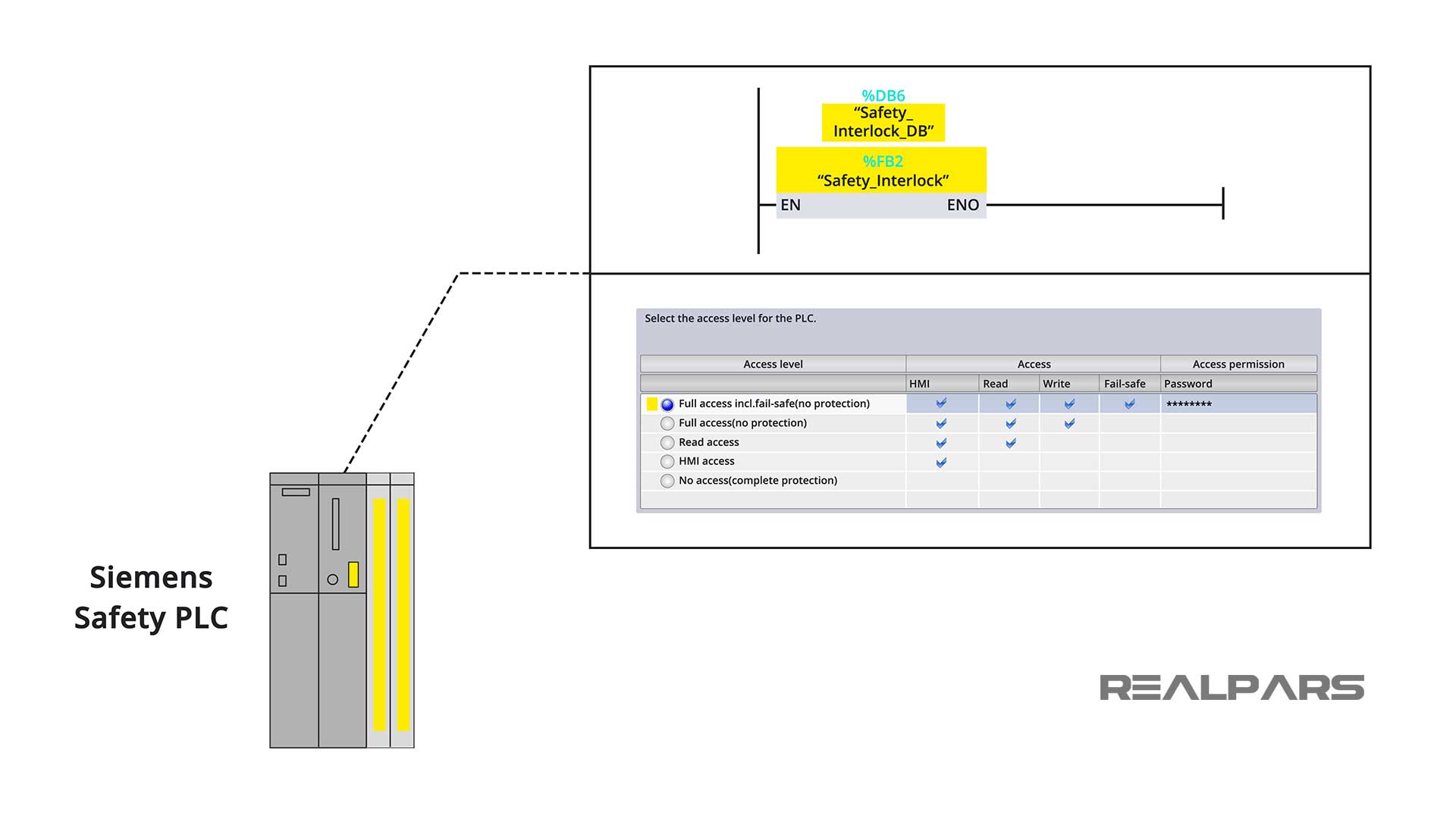
For example, a safety fence on a robotic cell keeps people out of the cell to protect them from contact with moving objects.
When the fence gate of the cell is opened the safety circuit cannot be reset because the circuit is waiting for the gate to be closed. This prevents a person from walking into a robot cell while the robot is running.
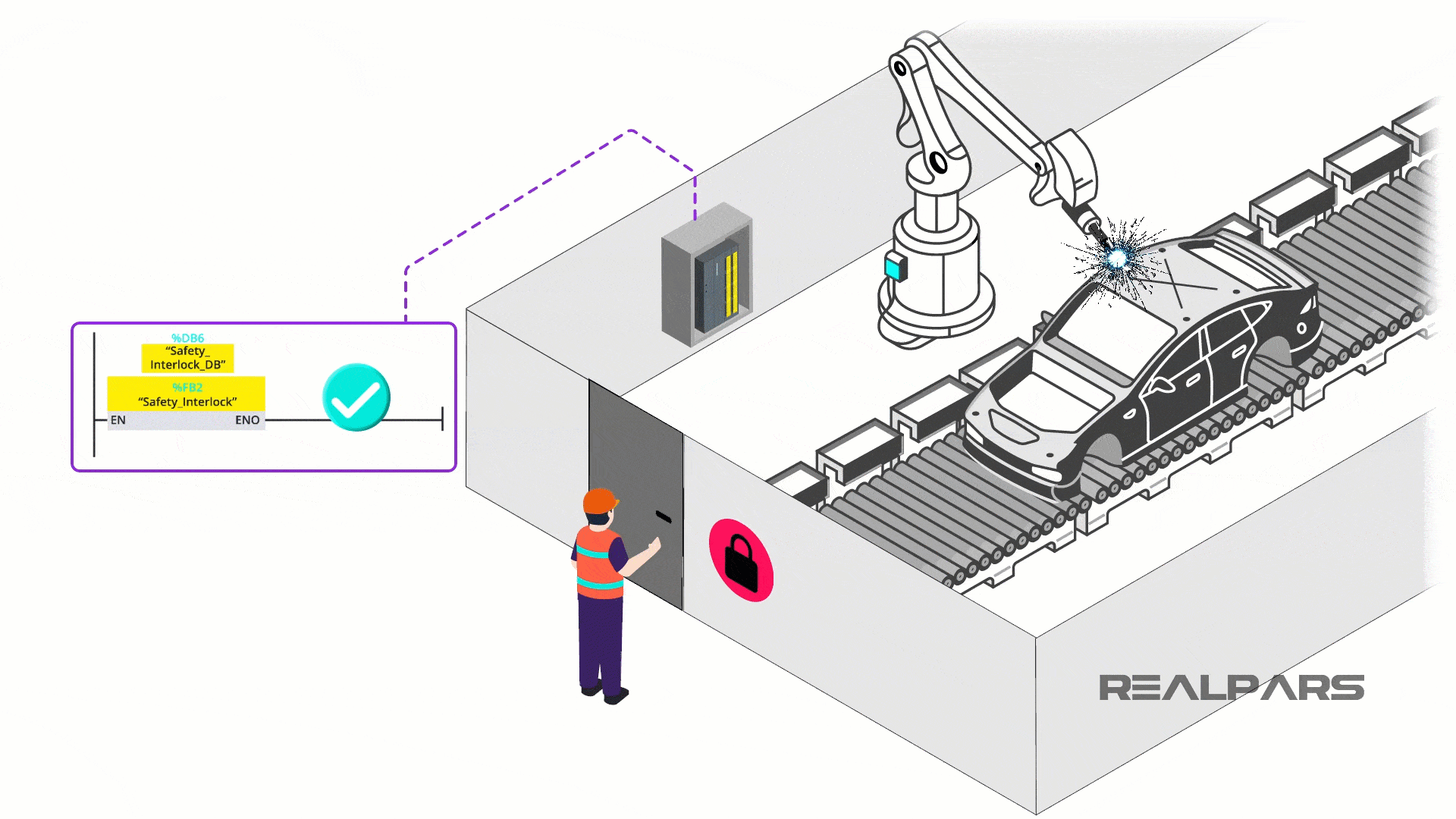
2) Non-safe interlock
The other main type of interlock is a non-safe interlock. These are used to protect equipment or unintended operations.
Different kinds of non-safe interlocks
There are three different kinds of non-safe interlocks. These types of interlocks can be mechanical, electrical, or logic interlocks.
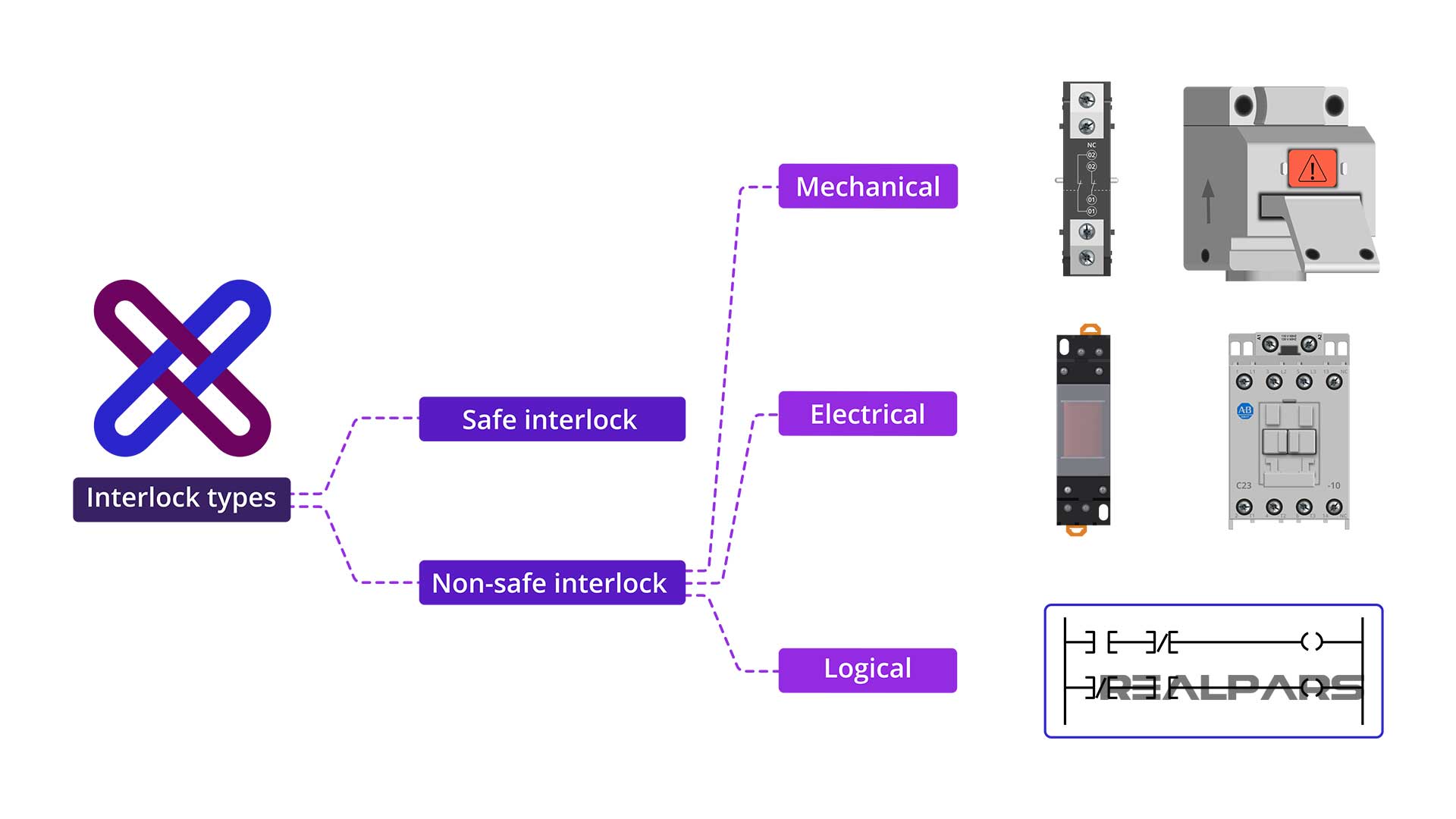
1) Mechanical interlock
A mechanical interlock is an interlock that is physically connected to another device to prevent unintended actions.
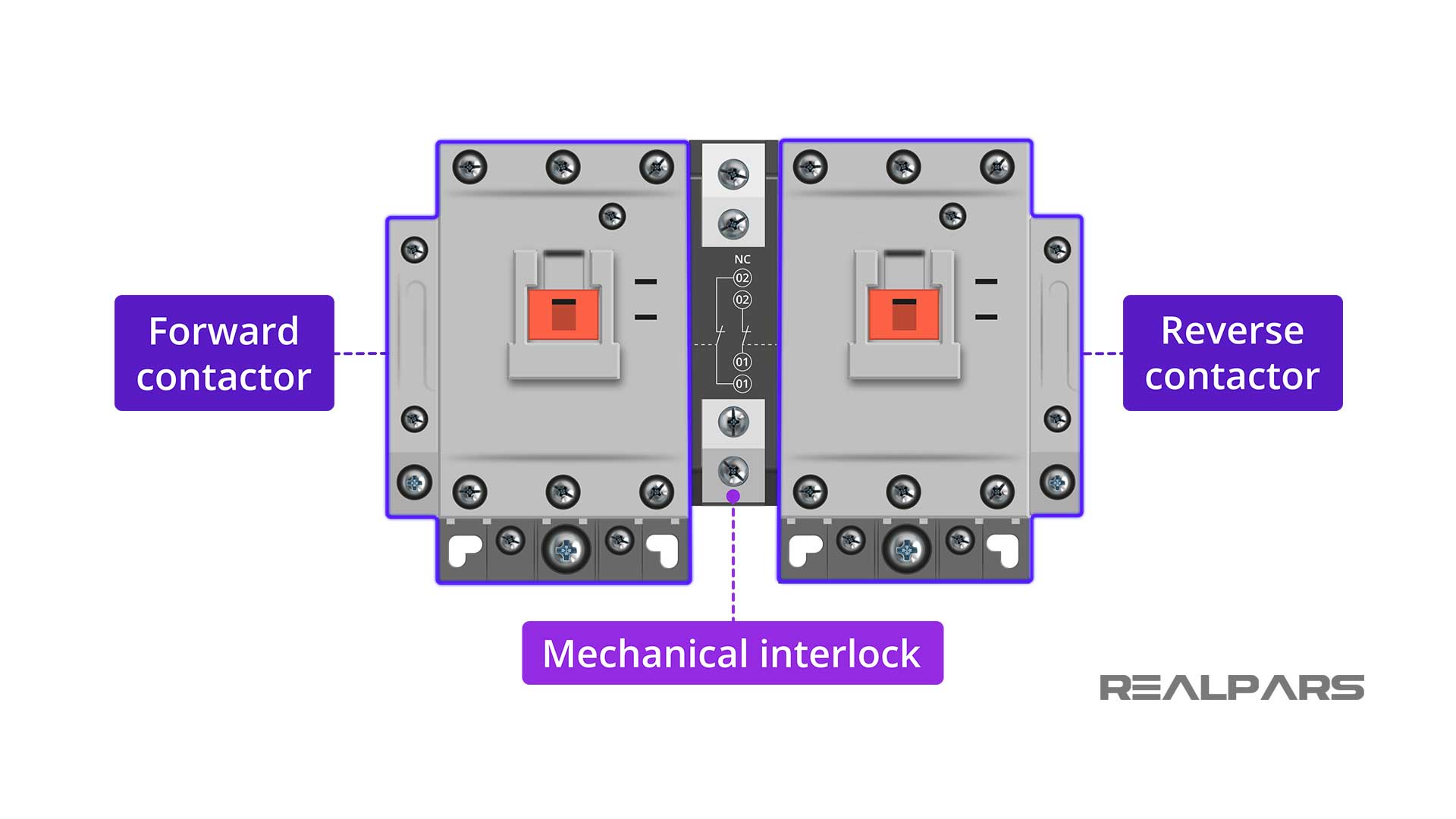
Mechanical interlock example #1:
Full voltage reversing motor starter
A simple example of a mechanical interlock is a full voltage reversing motor starter.
Example 2 of the article, Motor Starter Explained | Motor Starter Types, details a full voltage reversing motor starter.
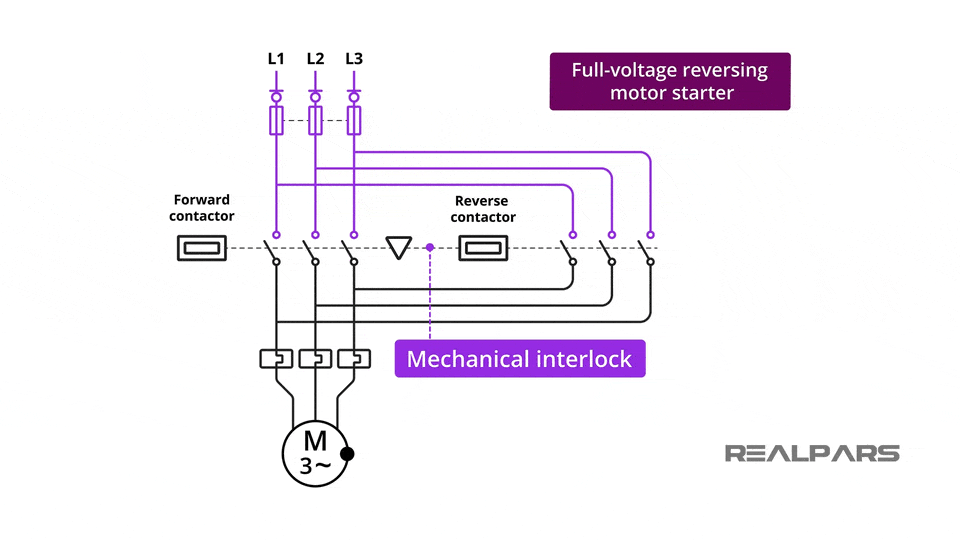
The dashed line in between the forward and reverse contact indicates that there is a mechanical interlock. This prevents the motor’s forward and reverse contactor coils from energizing at the same time.
Energizing both contactor coils at the same time would cause damage to the motor.
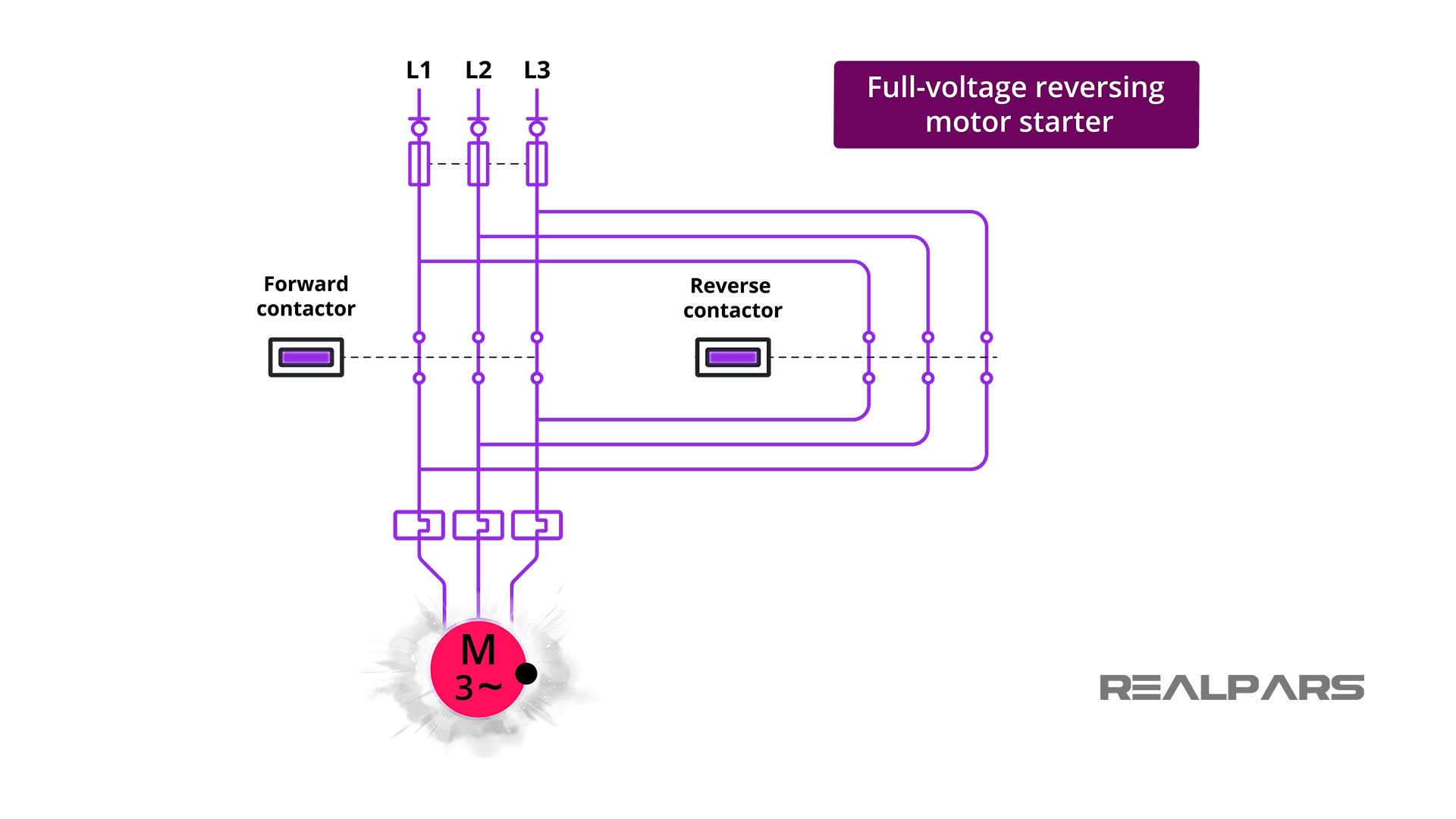
Mechanical interlock example #2:
Car steering wheel
Another example of a mechanical interlock is in the steering wheel of your car. There is an anti-theft device that restricts the turning of the steering wheel without the key inserted.
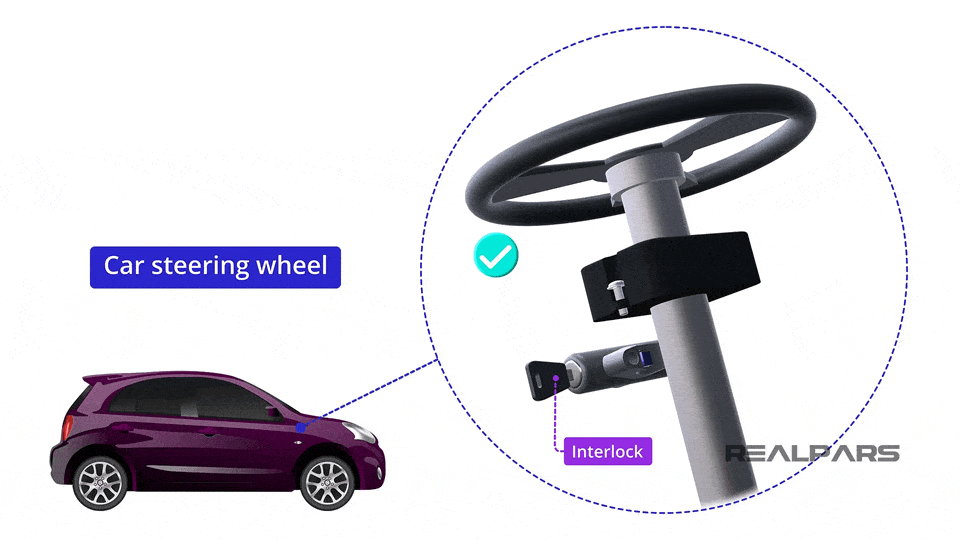
This is to prevent movement of the drive wheels to deter people from pushing the car since the mechanical interlock restricts directional motion on the front wheels.
The key in this example is the interlock that unlocks the steering wheel allowing both movements of the steering wheel and the ability to start the vehicle.
Mechanical interlock example #3:
Trap key system
Another example of a mechanical interlock is a trap key system, where one key is used to unlock another key which will allow you to open up a device such as a trap key safety fence.
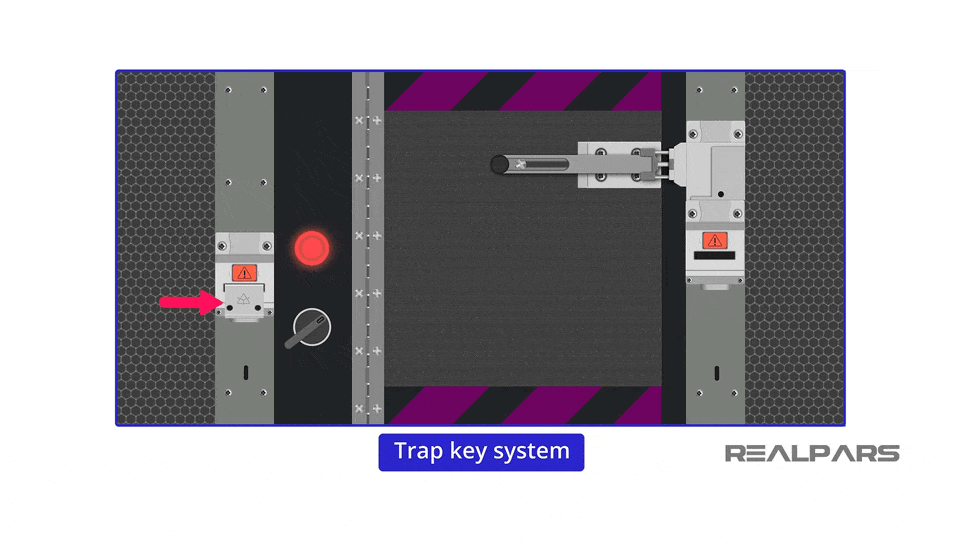
The first key must be removed and placed in the keyhole of the second key to unlock the second key. The second key will unlock the device you are trying to unlock. This system forces operators to do sequential actions. The keys in this example are the interlocks.
2) Electrical interlock
An electrical interlock is an interlock that is used to restrict current flow between two or more devices.
These types of interlocks use normally open and normally closed contacts to prevent another device from turning on.
Electrical interlock example #1:
Relays and contactors
Relays and contactors are typically used as electrical interlocks.
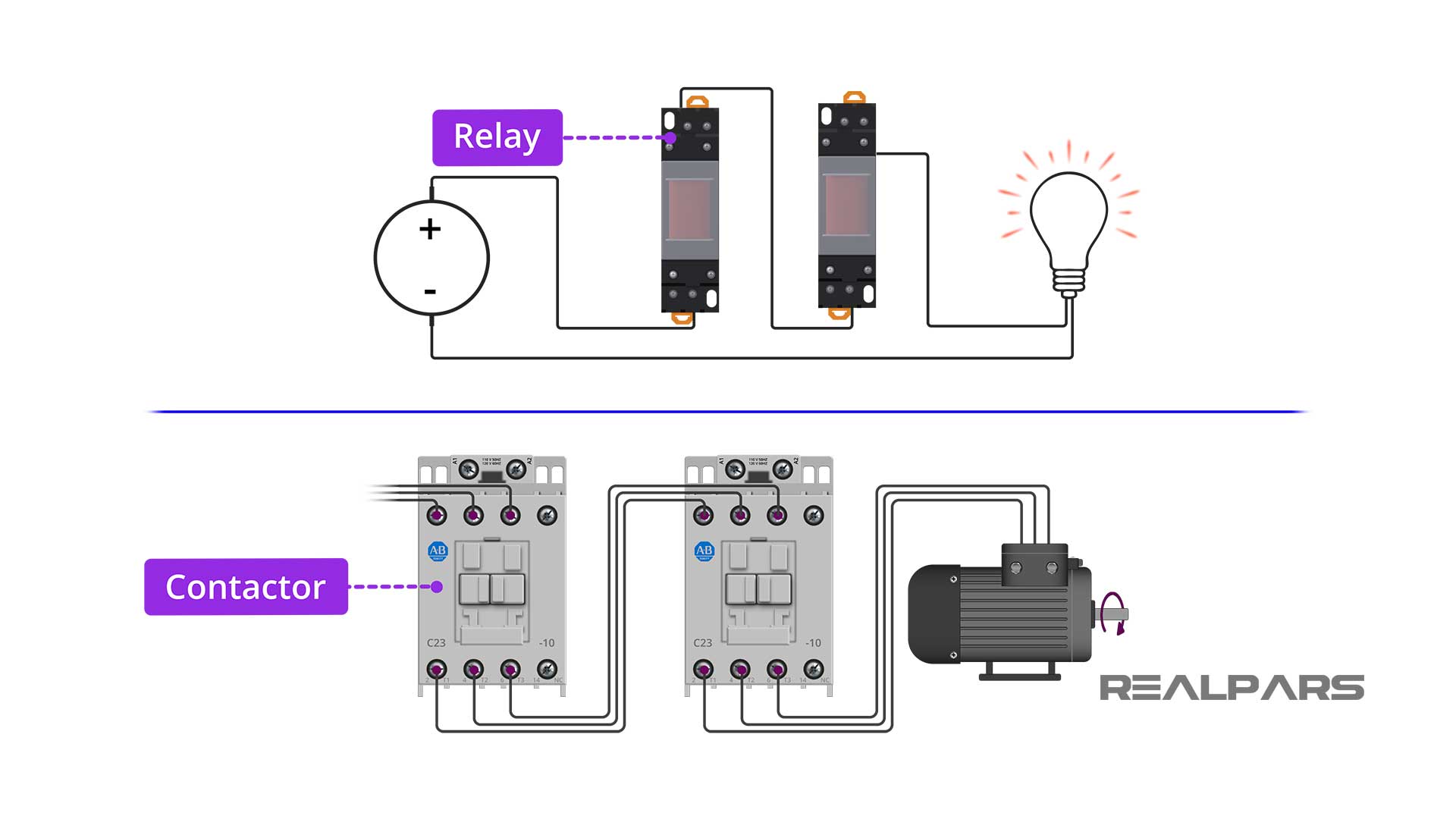
Say for example you have two relays, CR1 and CR2. You want to prevent CR1 from turning on if CR2 is on.
You would wire the coil in series from CR1 into the normally closed contacts of CR2 to ensure that for CR1 to energize CR2 must be de-energized. This type of interlock is often used when designing an electrical circuit or system.
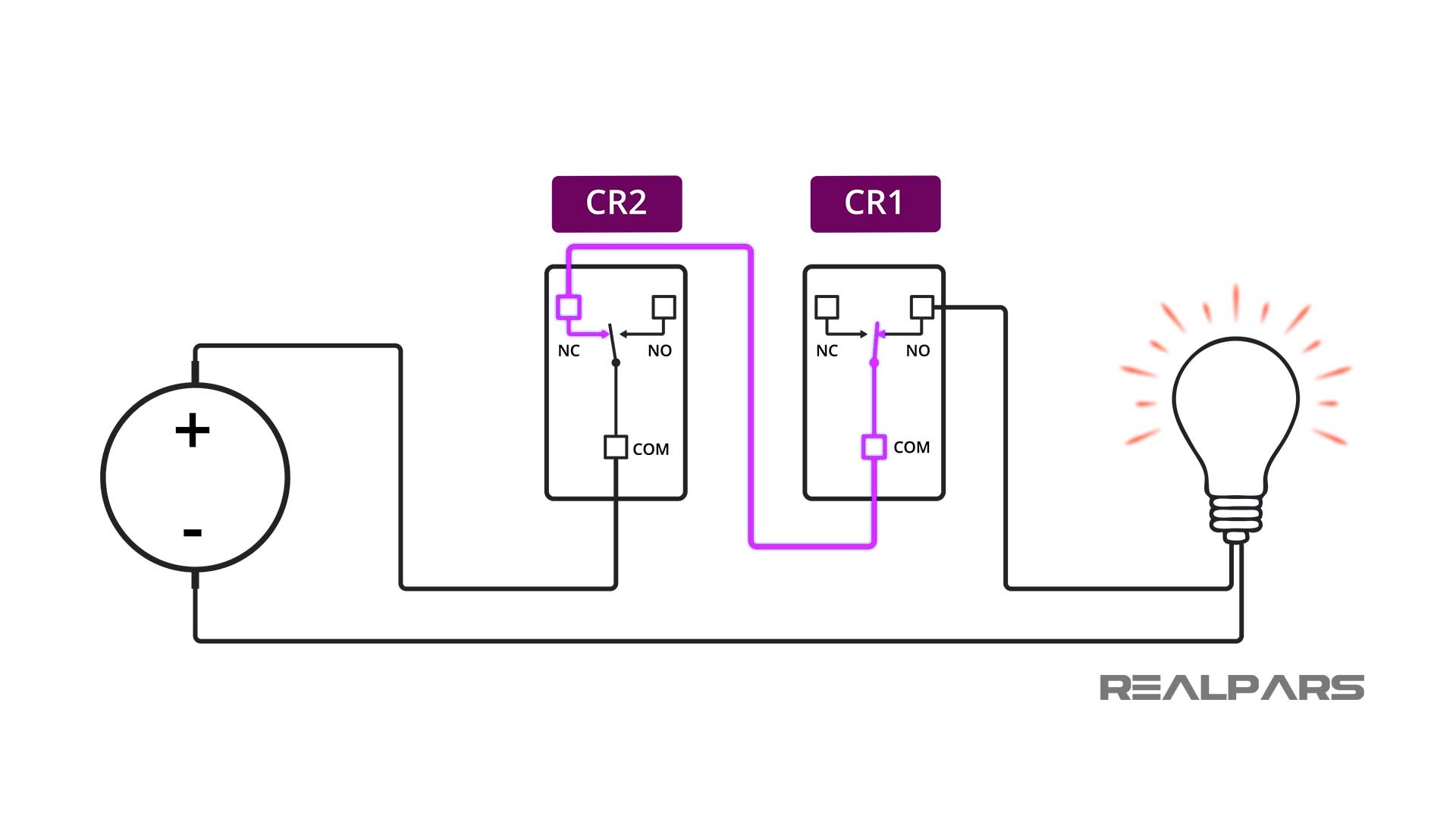
Electrical interlock example #2:
Motor starter thermal overload
Another example of an electrical interlock is the thermal overload on a motor starter. When the current is too great the coil circuit will open and cause a shutdown on the motor.
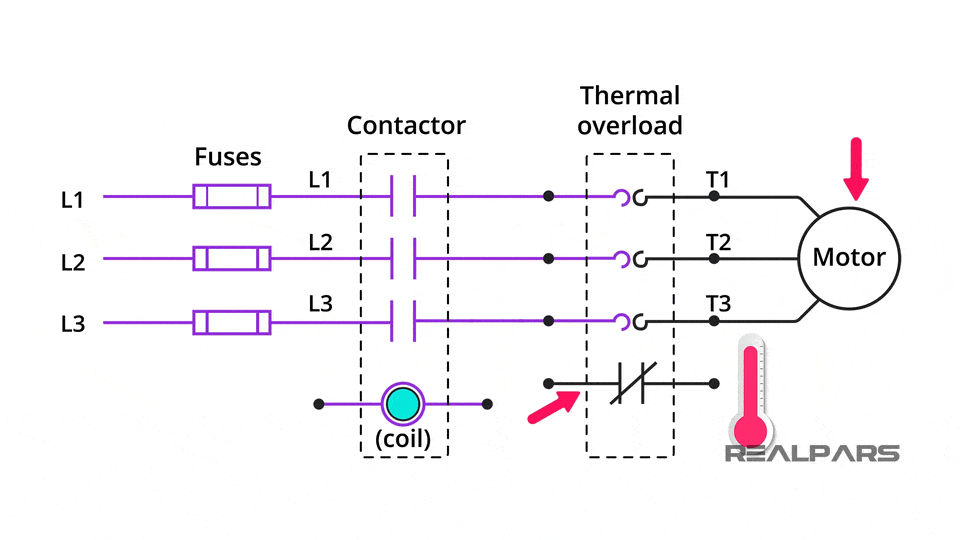
Once cooled the thermal overload allows current flow again. This is an electrical interlock because the voltage to the motor coil is lost which prevents it from turning on.
3) Logic interlock
A logical interlock has an instruction or variable which has to be true to allow a result. Logical interlocks are useful when the devices are not easily connected electrically or mechanically.
Logic interlock example #1:
Process pump downstream
An example of a logic interlock is a pump downstream of a process that needs to be running to start the next pump in line.
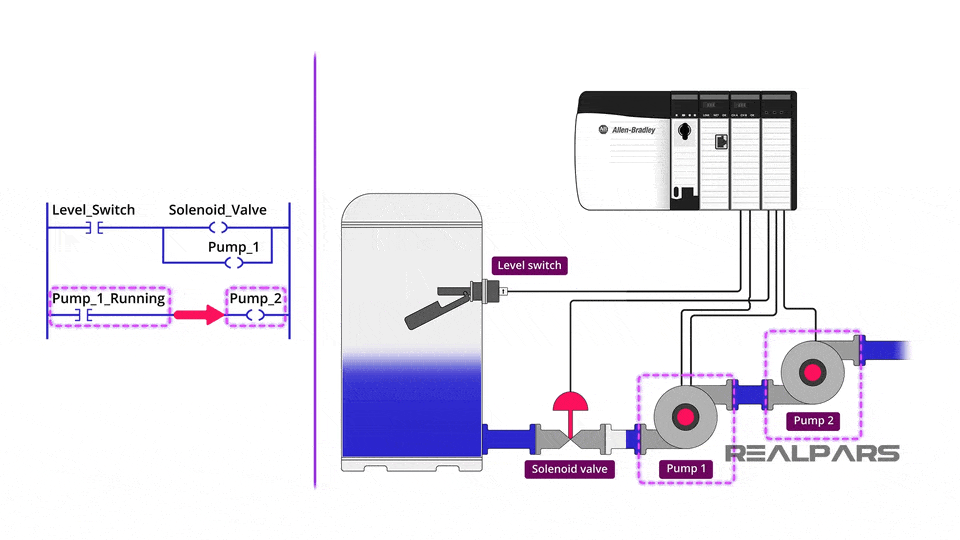
To do this you would take the pump’s running signal and put it in series with the output used for the next pump. This will ensure that the second pump will not start unless the first pump is running. So, here the first pump works as an interlock.
Logic interlock example #2:
Start button
Another example is pressing a start button for three seconds and when three seconds have elapsed the machine starts.
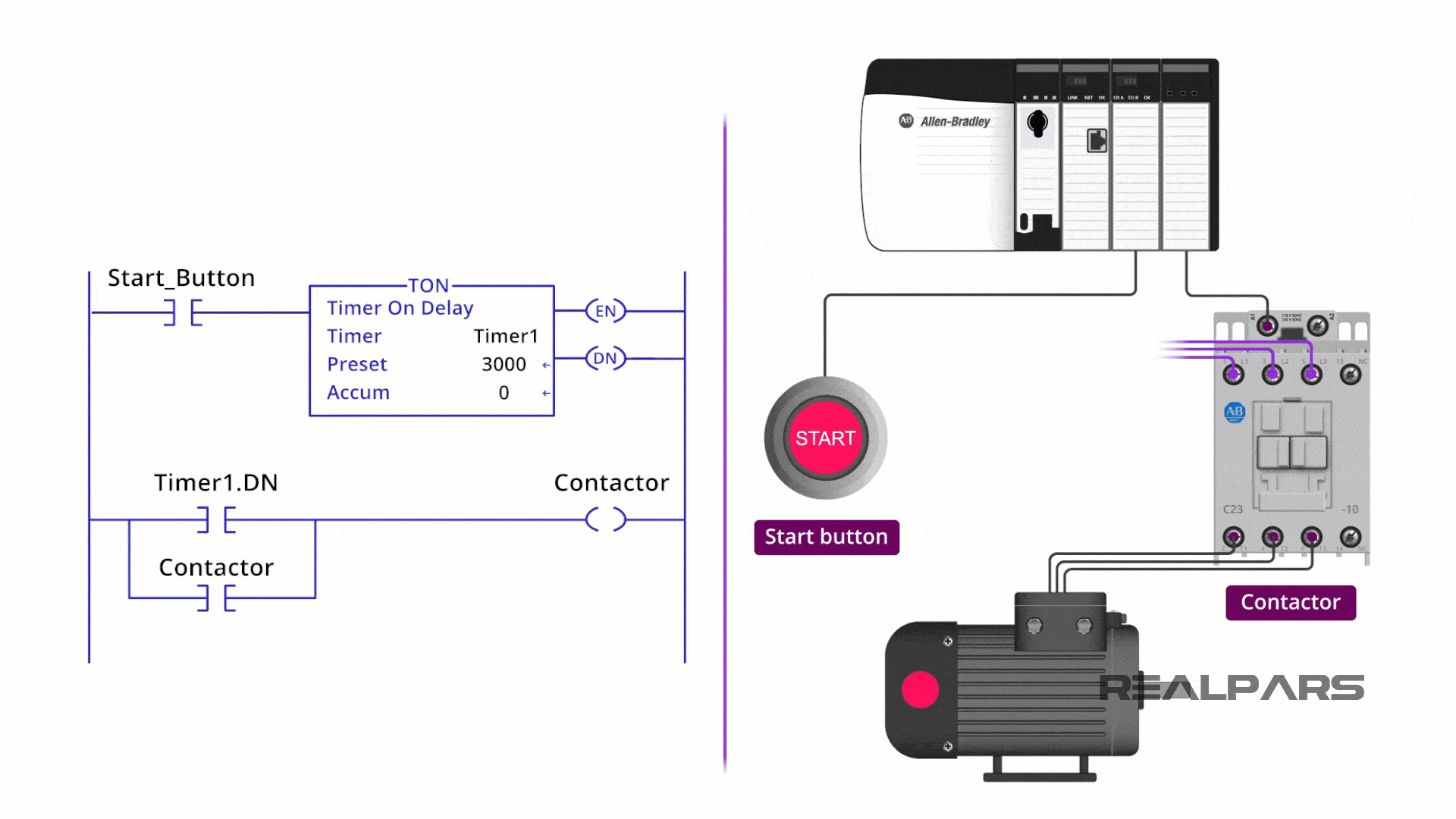
To program this you would put the start button pressed bit in series with an on-delay timer variable.
In the next rung, you would put the done bit of the on-delay timer in series with the start sequence variable. The start button being pressed for three seconds is the interlock for the start sequence.
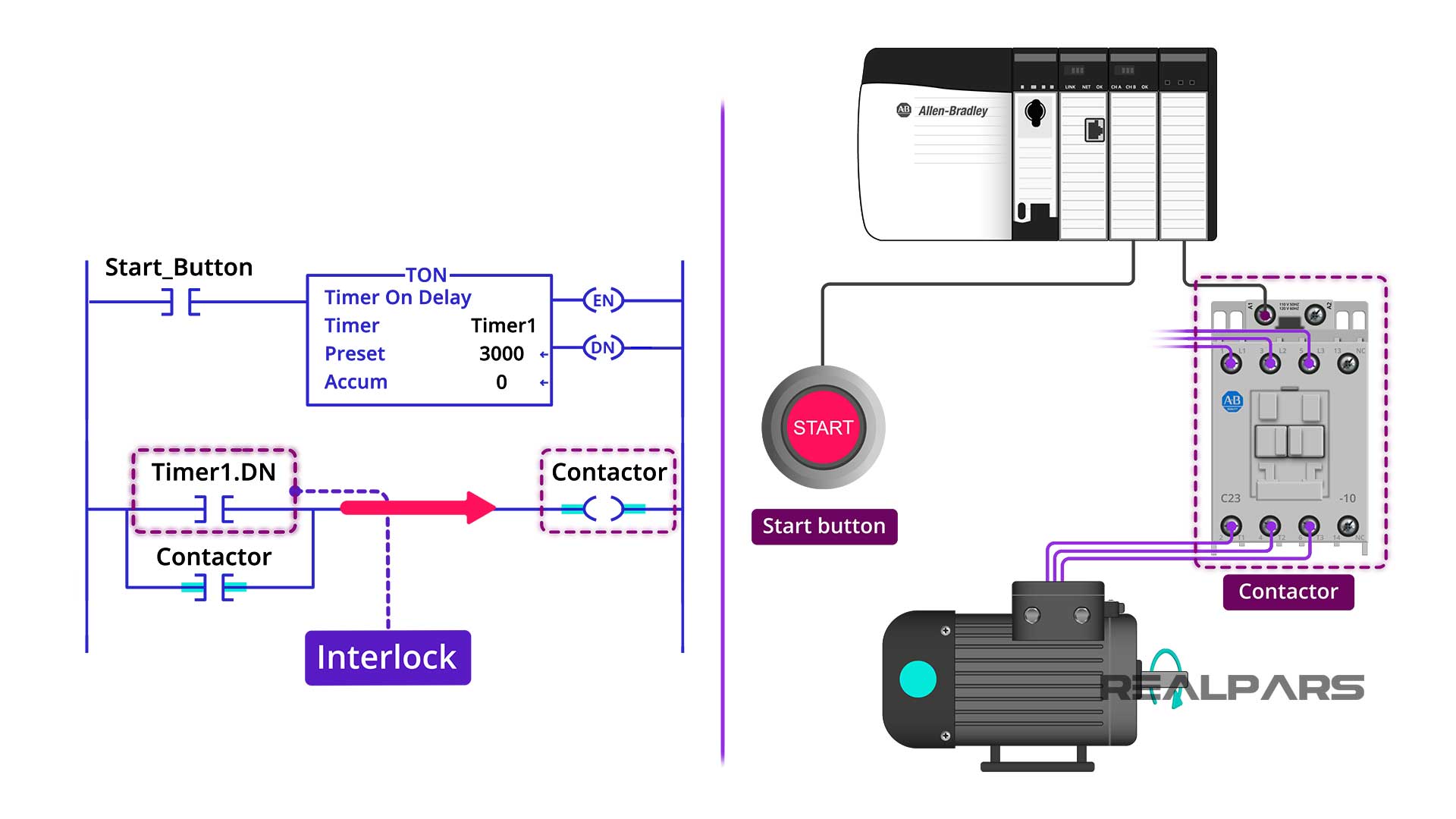
Logic interlock example #3:
Pneumatic Cylinder
Another example of a logical interlock is a pneumatic cylinder. Sometimes you need to prevent movement from two cylinders that could physically collide.
Cylinder A moves horizontally. Cylinder B moves vertically.
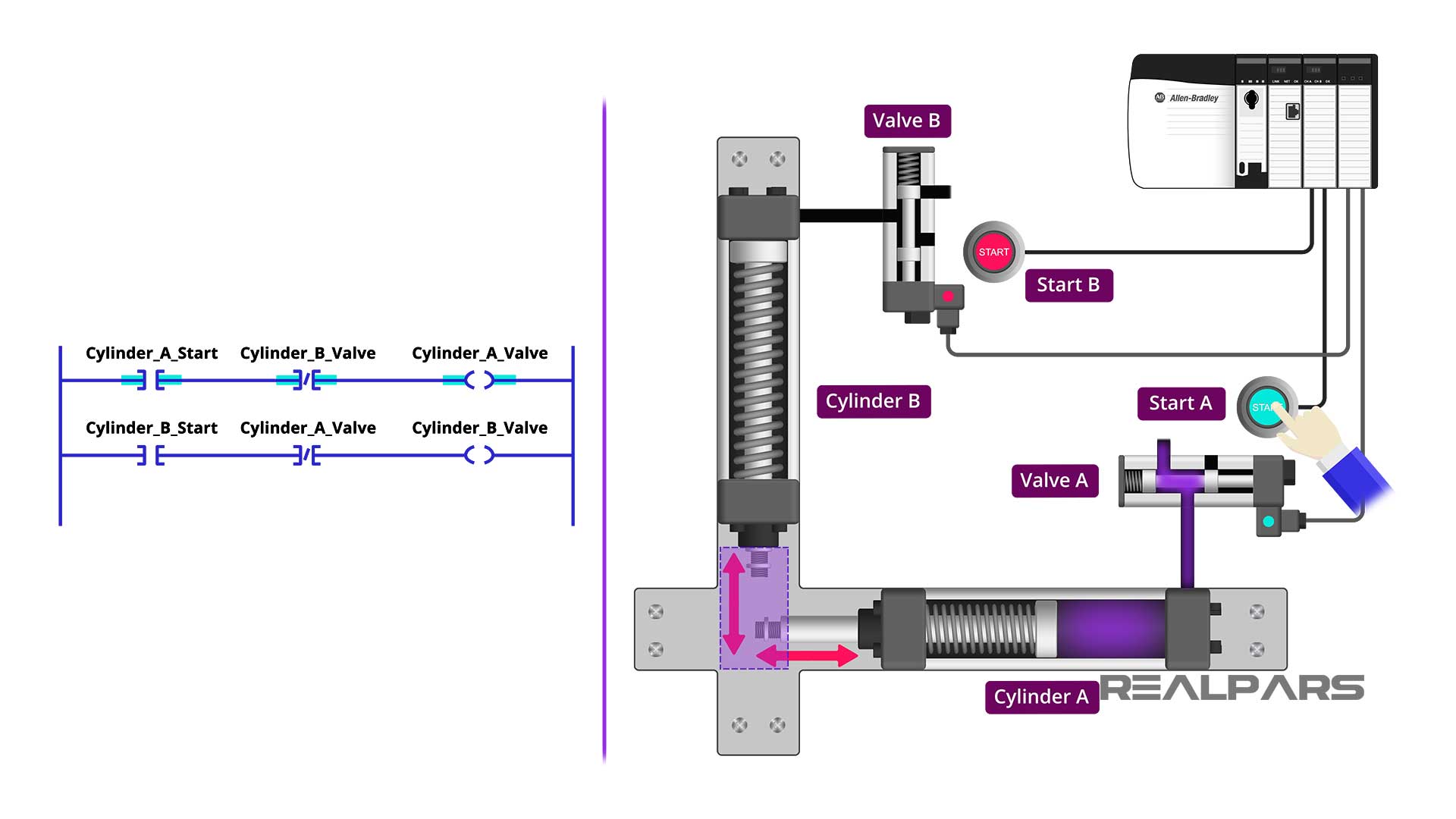
You must move cylinder A to the retracted position to allow cylinder B to move down. These cylinders are interlocked to make sure damage does not occur.
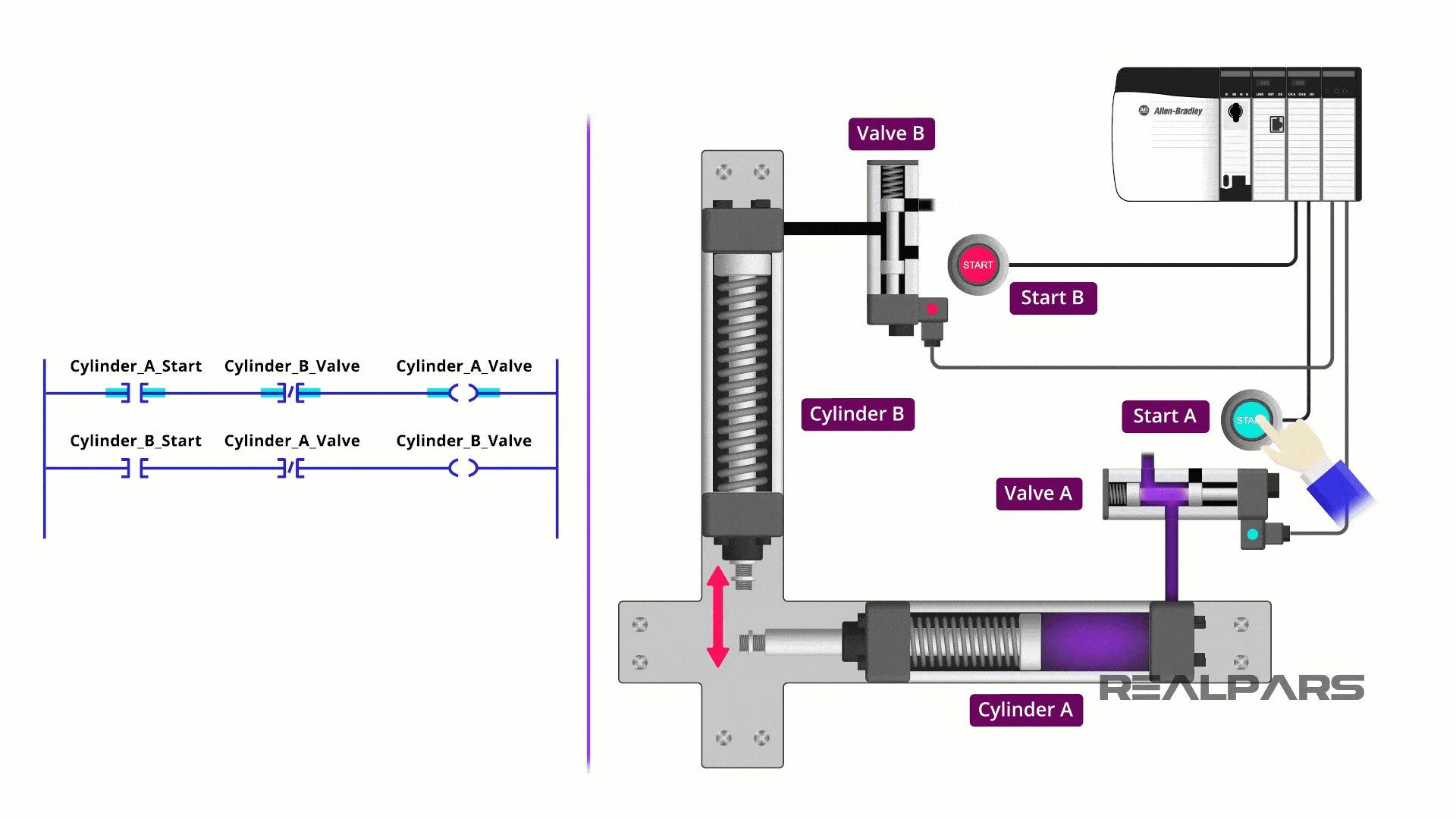
Logic interlock example #4:
Cascading conveyor system
Another example of a logical interlock is a cascading conveyor system. Simply put, the upstream conveyors are waiting for the downstream conveyors to start, and remain clear, to allow for boxes to move downstream.
This means we first need to start motor 3. When motor 3 is running, this interlock here is active.
Now if we press the start switch here, motor 2 will run as well. Having motor 3 and motor 2 running, if we press this start switch here, motor 1 will run as well.
So, to be able to turn on motor 1, we need to have motor 3 and motor 2 running, and to be able to turn on motor 2, we need to have motor 3 running.
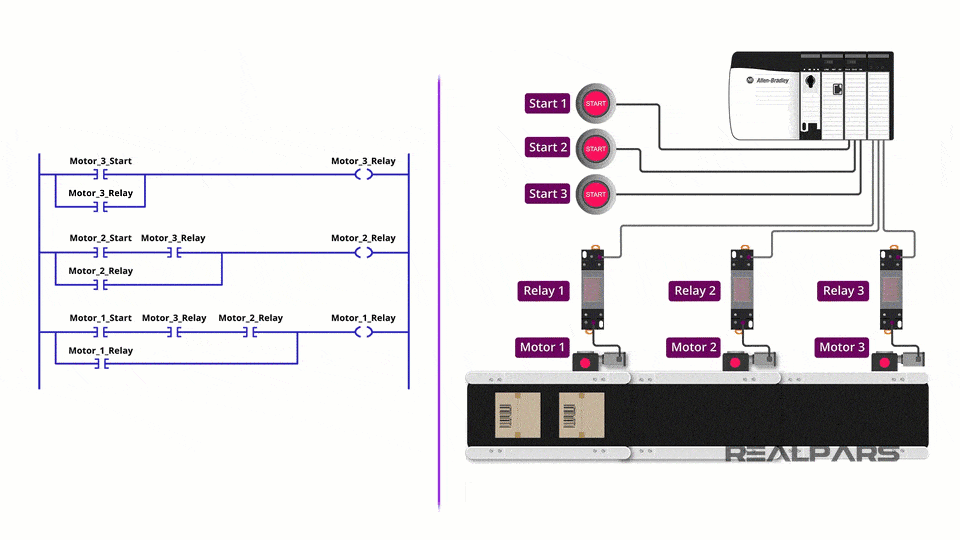
This means that the open contacts of motor 3 and motor 2 work as an interlock for motor 1 and the open contact of motor 3 works as an interlock for motor 2.
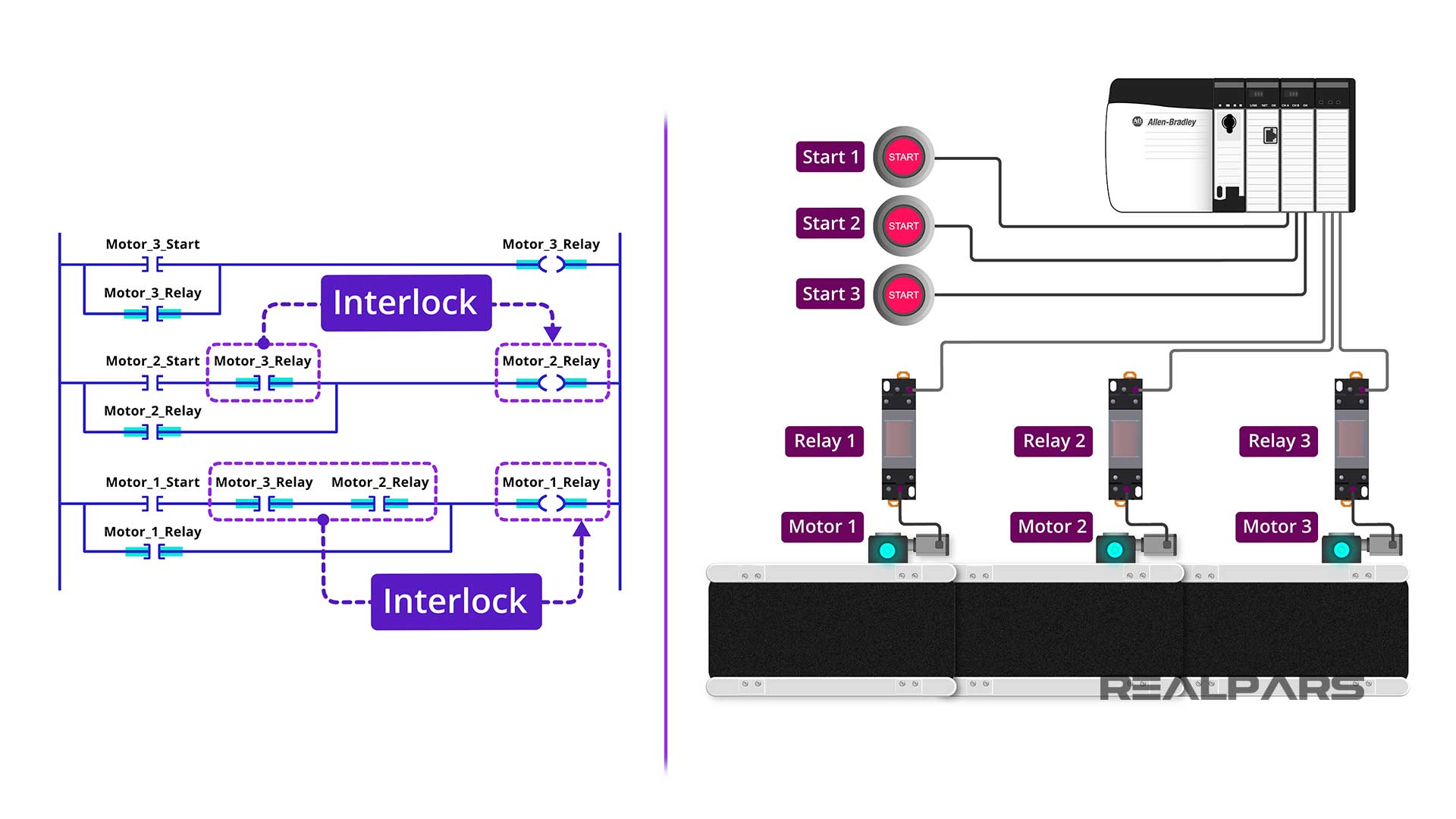
If there were not any interlocks on the conveyors then the running conveyors would jam the boxes regardless of whether the downstream conveyor was running or not.
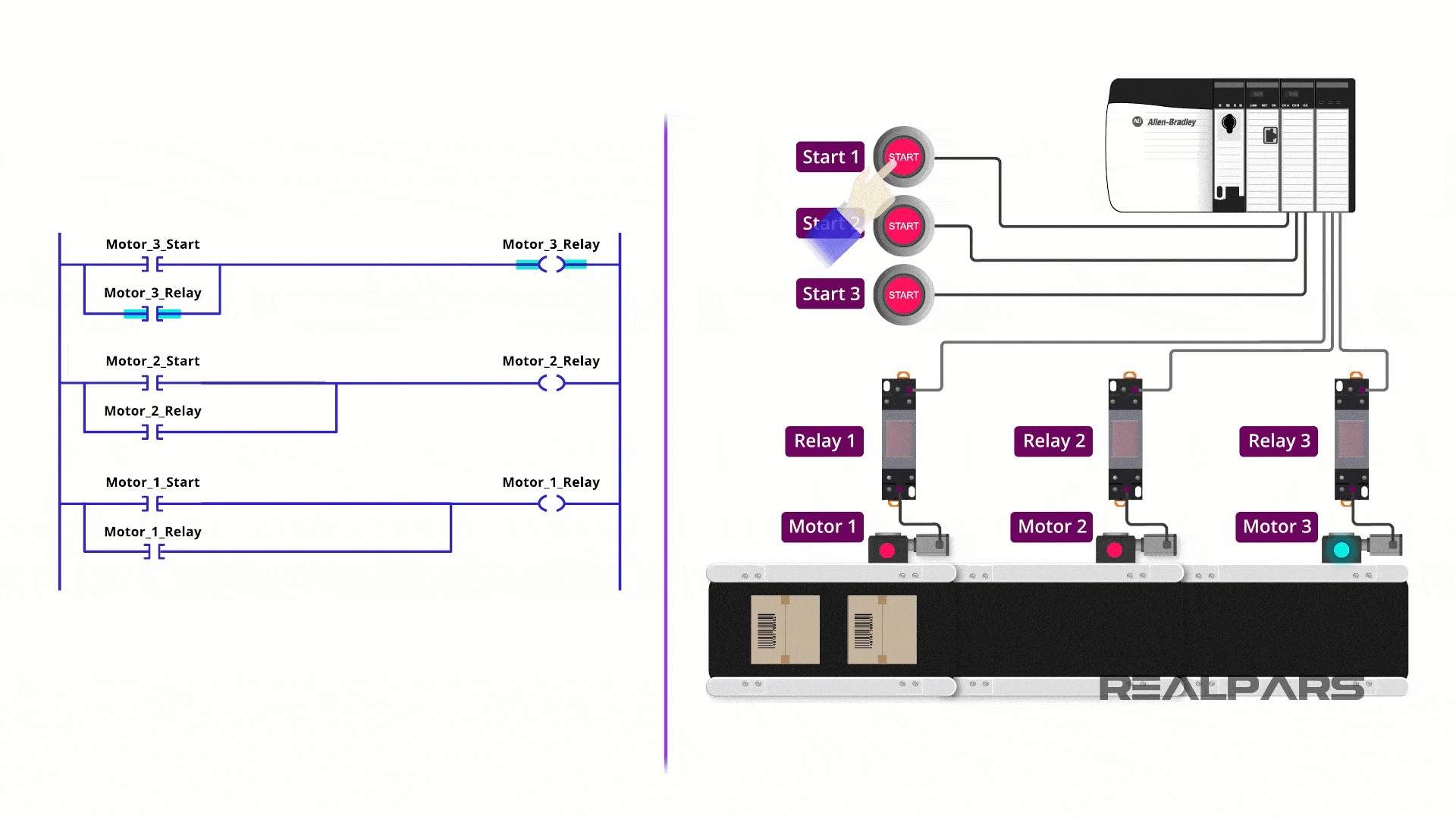
Summary
In summary, an interlock is a method for restricting action. There are two main types of interlocks:
– safe
– non-safe.
There are three types of interlocks:
– mechanical,
– electrical,
– logical.
Each interlock has a specific use to help take control of a system and prevent undesirable actions.
Please let us know if you have any questions about interlocks in the comments below and we will get back to you in less than 24 hours.
Got a friend, client, or colleague who could use some of this information? Please share this article.