When you get in your car to go on a drive you often look at your gas gauge, which is a type of a level sensor. Industries use several different level sensor types to detect their products.
In this article, we are going to talk about the different types of level sensors used in the industry, in a very easy-to-follow format. So what is a level sensor?
Level Sensor Classification
Level Sensors can be broken into two classifications;
– Point level measurement
– Continuous level measurement
Point level measurement indicates when a product is present at a certain point and continuous level measuring indicates the continuous level of a product as it rises and falls.
The sensors for point level indication are:
– Capacitance
– Optical
– Conductivity
– Vibrating (Tuning fork)
– Float Switch
The sensors for continuous level measuring are:
– Ultrasonic
– Radar (Microwave)
We will talk about how they work and which applications are best suited for their technology, as well as their limitations in certain applications.
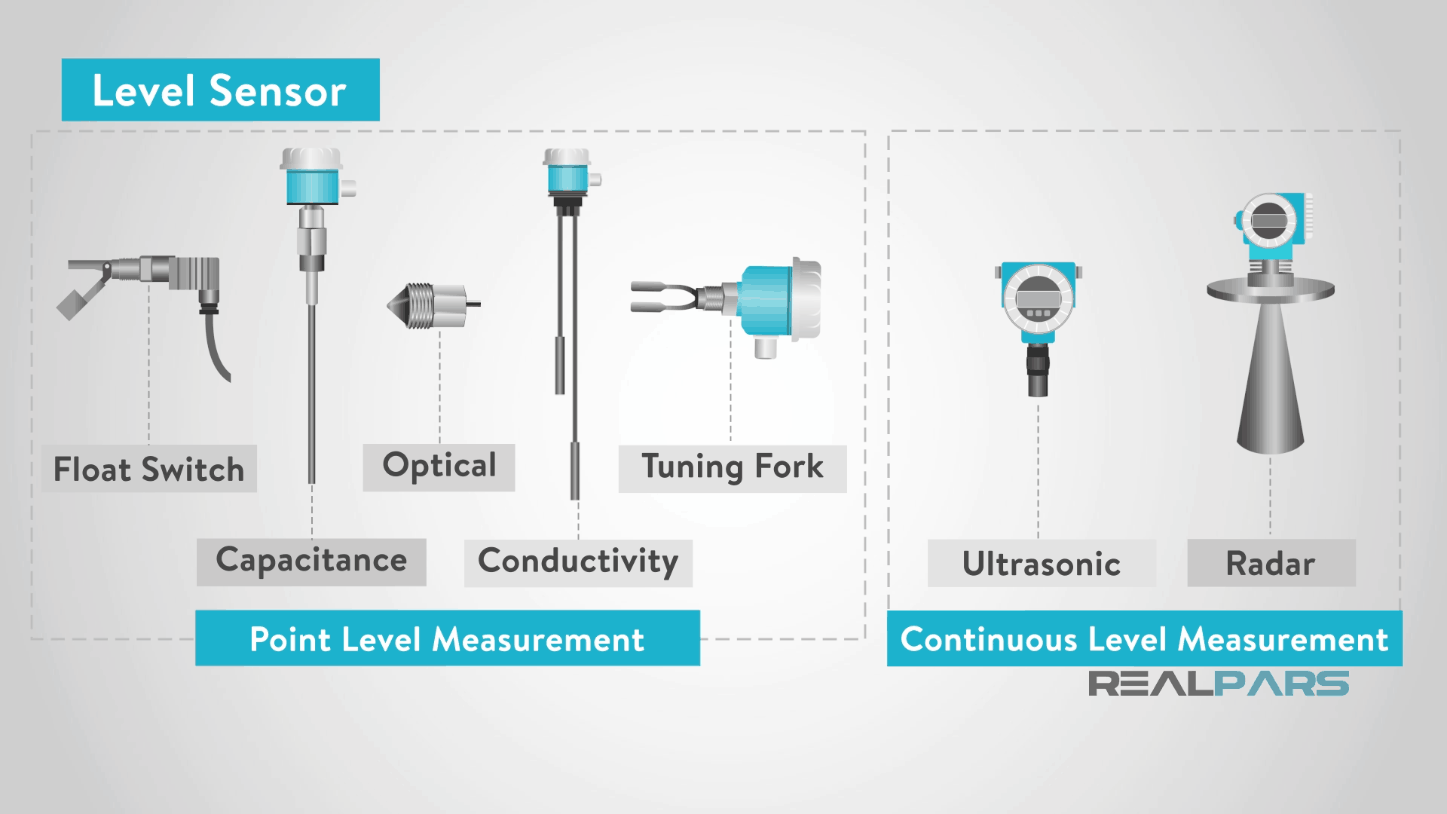
Point Level Measurement Sensors
Let’s talk about point level indication sensors first. Starting with capacitance level sensors.
1. Capacitance Level Sensor
Let’s talk about point level indication sensors first. Starting with capacitance level sensors.
A capacitance level sensor is a proximity sensor that gives off an electrical field and detects a level by the effect on its electrical field. These sensors are:
– Small
– Less expensive than other sensors
– Invasive to the product
– Accurate
– Have no moving parts
However, they do have to be calibrated and will only detect certain liquids.
Capacitance sensors can be used in liquid storage tanks. A water treatment facility that has storage tanks would be an ideal use for a capacitance sensor.
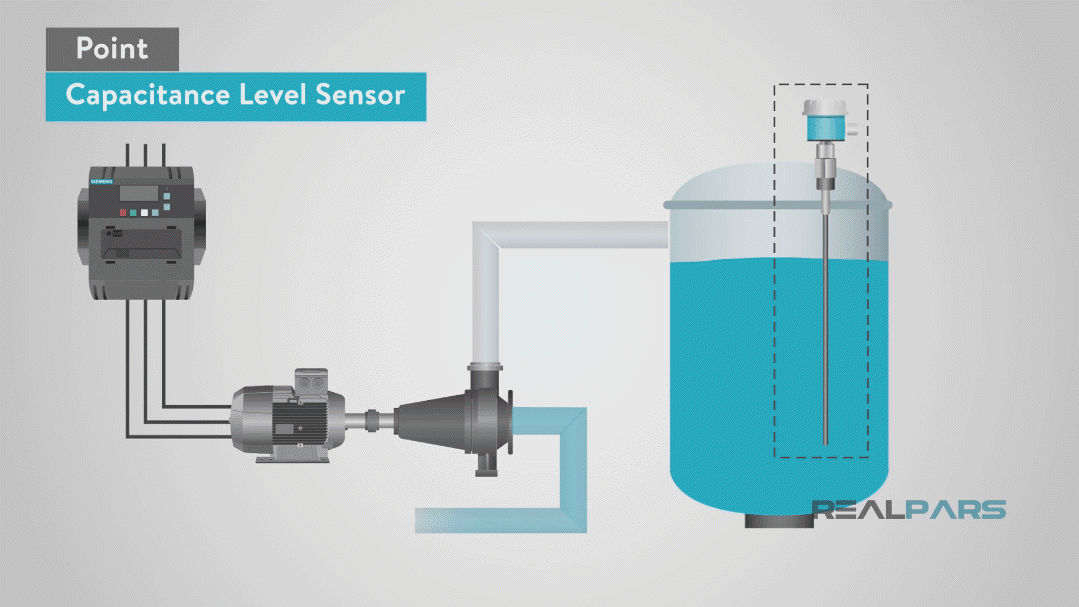
2. Optical Level Sensor
The next point level sensor we will talk about is an optical level sensor.
Optical sensors work by converting light rays into electrical signals which measure a physical quantity of light then translate it into a measurement.
– These sensors have no moving parts
– They are not affected by high pressure or temperature
– They are small in size
– They can be used in liquid applications
However, if the lens gets coated or dirty they would require cleaning.
They can be used as low-level indicators to prevent run dry conditions when using oil, coolant, or hydraulics.
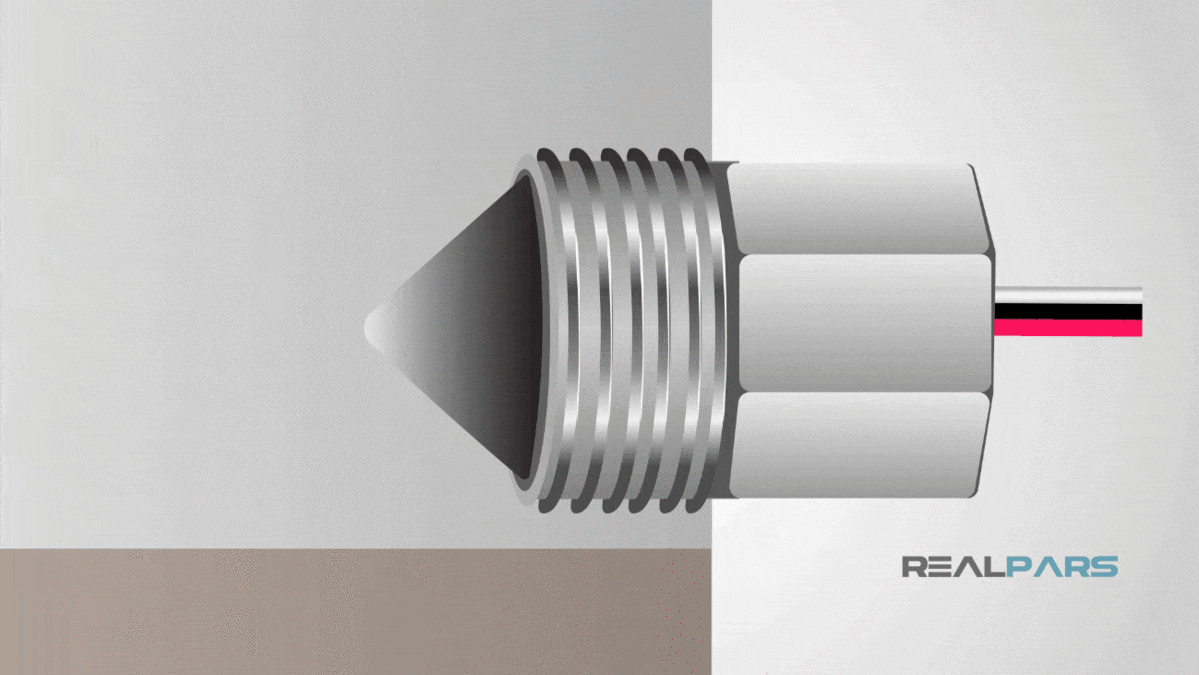
3. Conductivity (Resistance) Level Sensor
Another style of point level sensor is conductivity or resistance.
A conductivity or resistance sensor uses a probe to read conductivity. The probe has a pair of electrodes and applies alternating current to them.
When a liquid covers the probe its electrodes form a part on an electric circuit, causing current to flow which signals a high or low level.
The advantages of using a conductivity level sensor are:
– There are no moving parts
– They are low cost
– Fairly easy to use
The disadvantages are:
– They are invasive (meaning they must touch the product being sensed)
– They only sense conductive liquids
– The probe will erode over time
Appropriate use for these sensors would be for signaling high or low levels.
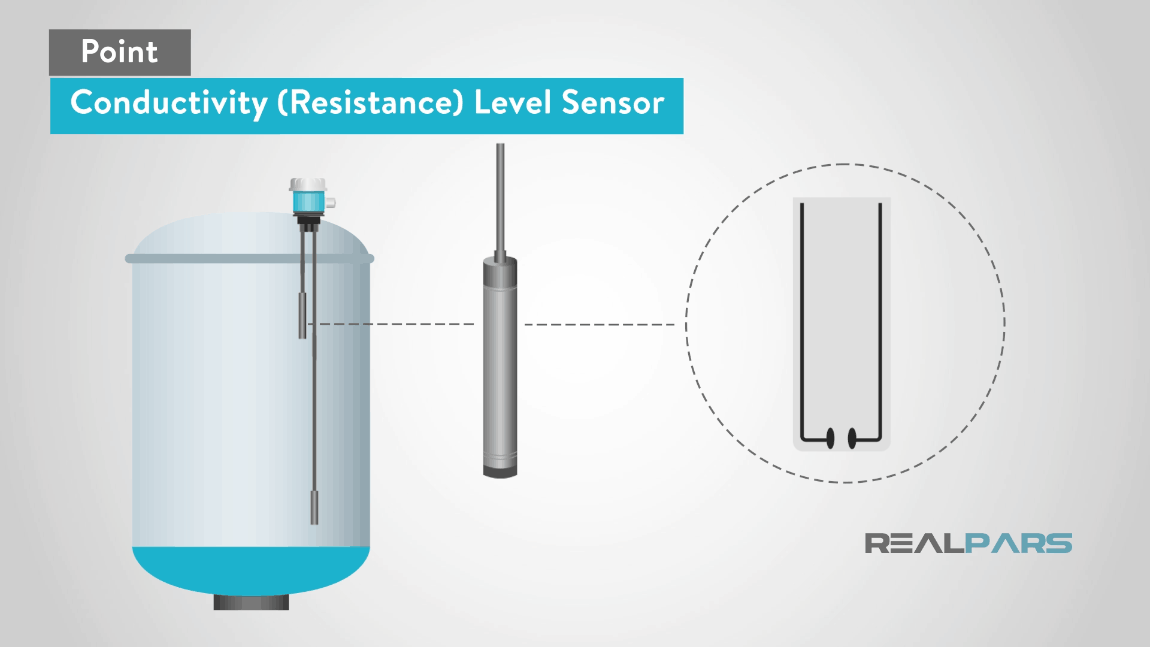
4. Vibrating (Tuning Fork) Level Sensor
Vibrating or tuning forks is another type of point level sensor.
They use a fork-shaped sensing element with two tines. The fork vibrates at its natural resonant frequency. As the level changes, the frequency of the fork will change detecting the level. These sensors are:
– Cost effective and compact
– Invasive to the product, meaning they have to touch the material to sense the level
– Easy to install
– Essentially maintenance-free
They have unlimited uses based on the material that they can sense. Mining, food and beverage, and chemical processing industries use these sensors for their applications.
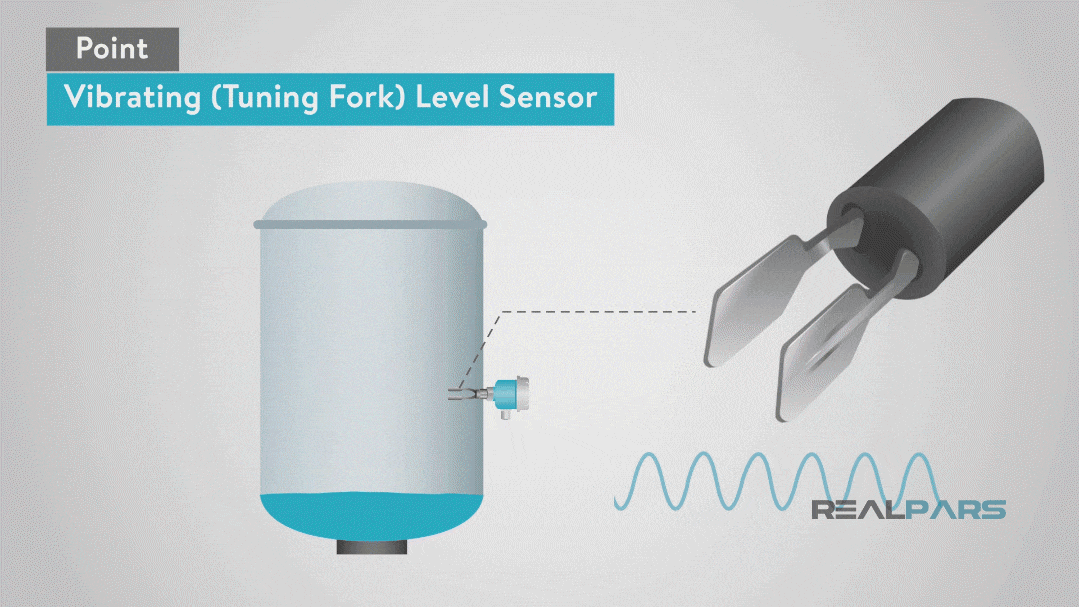
5. Float Switch
The last point level sensor that we will talk about is a float switch.
Float switches use a float, a device that will raise or lower when a product is applied or removed, which will open or close a circuit as the level raises or lowers moving the float.
The advantages of a float switch are:
– They are non powered device
– They provide a direct indication
– They are inexpensive
The disadvantages are:
– They are invasive to the product
– They have moving parts
– They can be large in size
Float switches will only give an indication for a high or low level, they cannot measure a variable level. A great use for float switches is in liquid storage tanks for high or low-level indication.
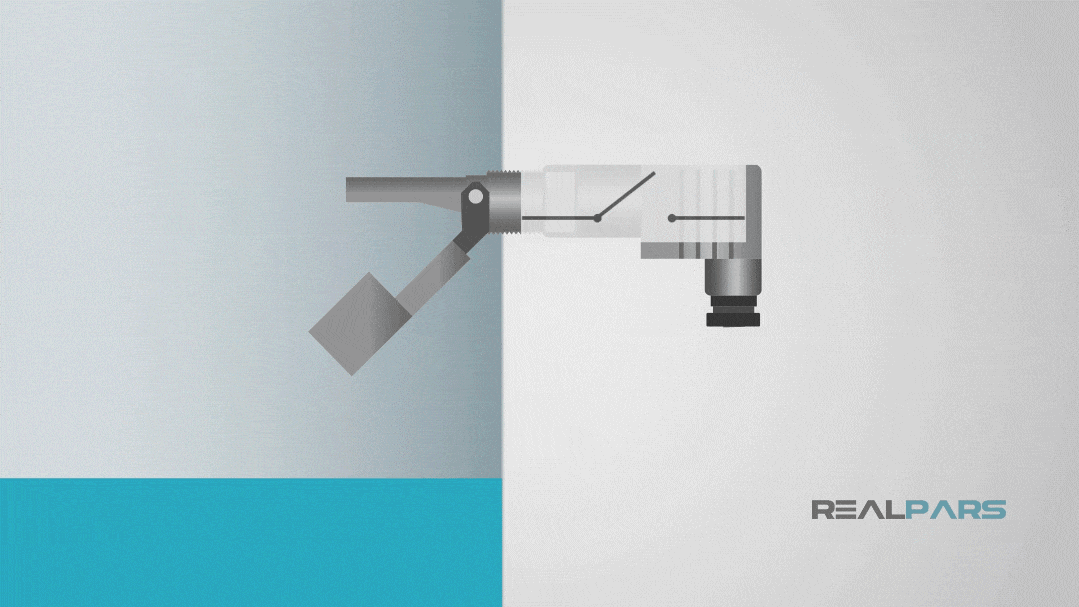
Continuous Level Measurement Sensors
Now, let’s talk about continuous level measurement sensors. We will start with ultrasonic sensors.
1. Ultrasonic Level Sensor
Ultrasonic level sensors work by emitting and receiving ultrasonic waves. The time it takes for the waves to reflect back is how distance is measured.
The advantage of using this type of sensor is that:
– These sensors have no moving parts
– They are compact
– They are reliable
– Non-invasive (Non-contact)
– Unaffected by the properties of the material they are sensing
– Self-cleaning because of the vibrations they give off
The disadvantage of using this type of sensor is that:
– They can be expensive
– In some situations, the environment can have a negative effect on them
An example application is a hot asphalt tank in a shingle manufacturing plant.
The ultrasonic sensor would be placed in the top of the tank away from the hot asphalt and used to sense the level in order to send a fill request for the tank.
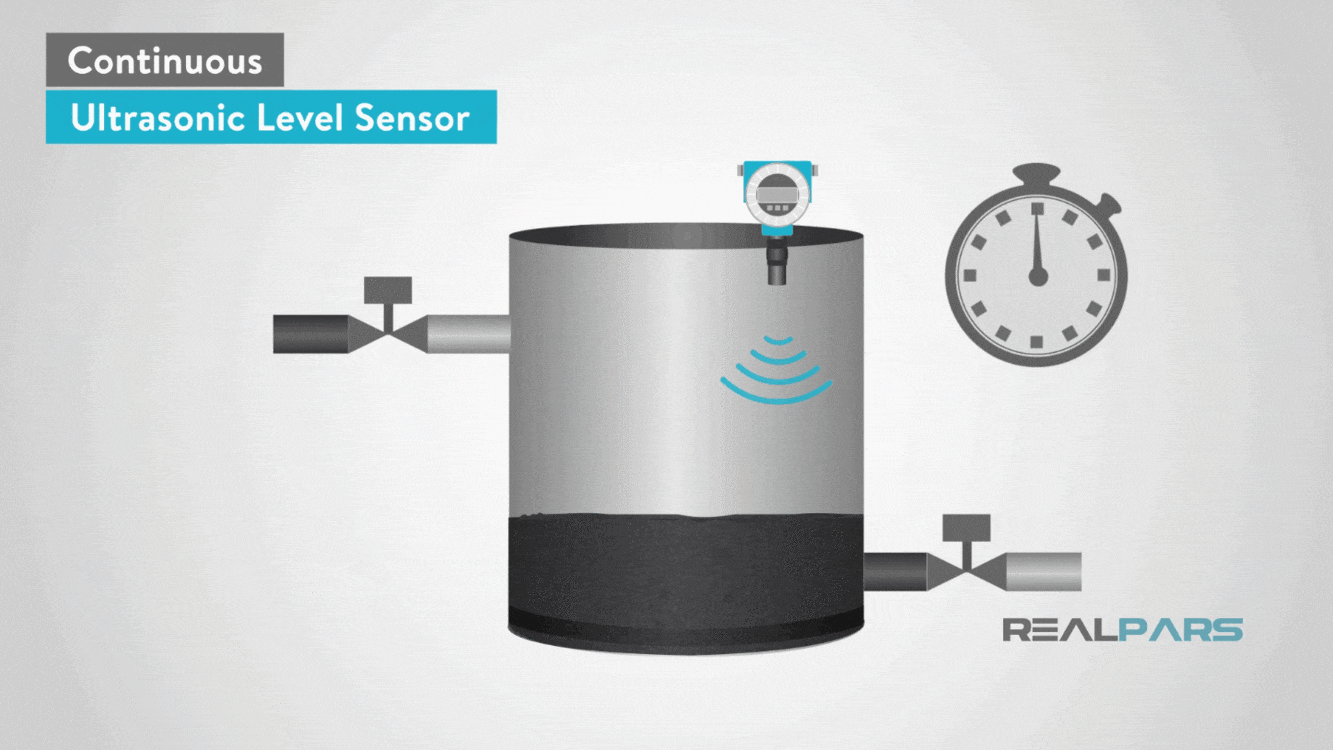
2. Radar Level Sensor
Radar or microwave is also a continuous level sensor.
These sensors transmit microwaves by an antenna on the radar sensor. The product that is being sensed reflects these microwaves back to the antenna and the time from emission to reception of the signal is proportional to the level of the product.
The advantages of radar sensors are that:
– They are not affected by temperature, pressure or dust
– They can also measure liquids, pastes, powders, and solids
– They are very accurate and require no calibration
– They are non-invasive because they do not have to touch the product that it is sensing
The disadvantages of radar sensors are that:
– They are expensive
– They have a limited detection range
If we go back to our shingle manufacturing plant example a Radar level sensor could be an ideal solution. Much like the ultrasonic sensor, radar sensors are ideal for hot liquid storage tanks.
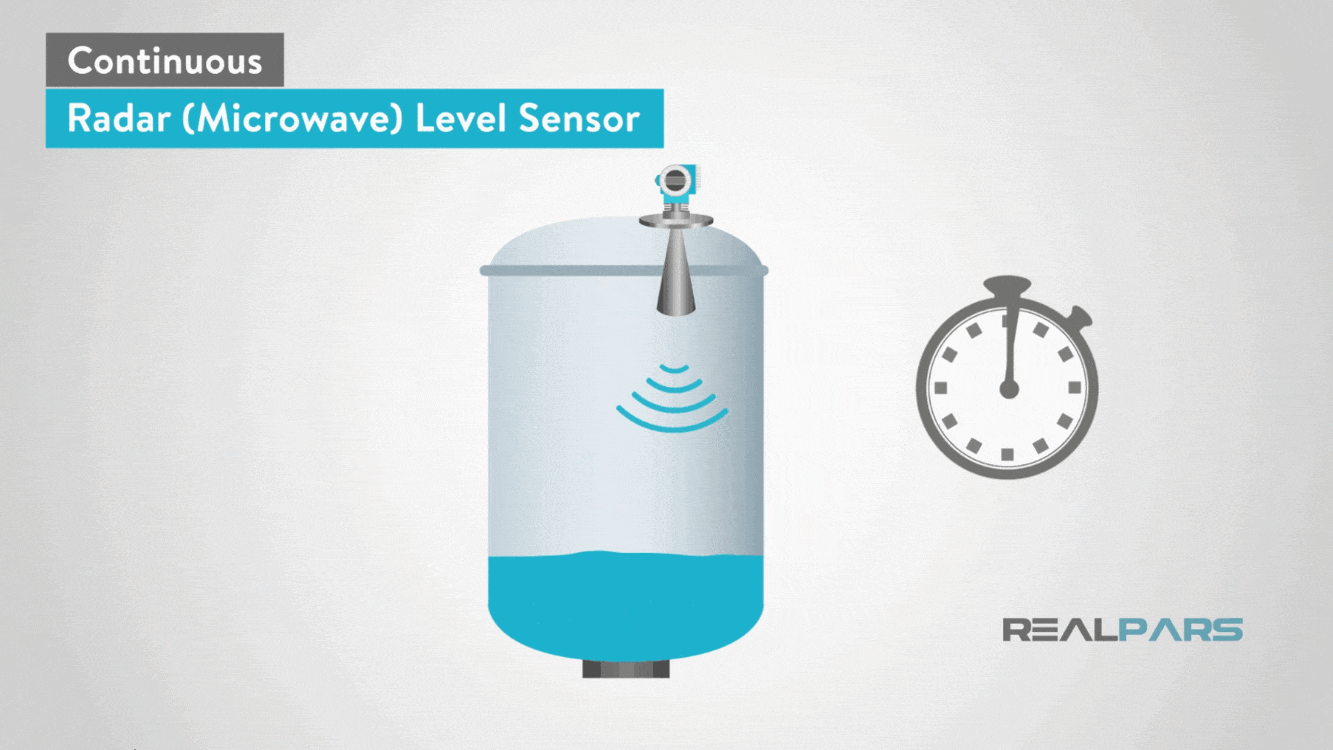
Summary
Let’s wrap up and review what we talked about today.
We talked about seven different types of level switches and their applications.
Some level sensor applications can overlap and when deciding on a sensor it is important to identify the product that you are sensing and the type of feedback that your application requires.
Sensors like conductivity or resistance, capacitance, Tuning Fork, float switches, and optical level sensors can be used to indicate a high or low level. While ultrasonic and radar level sensors can measure your level to give specific feedback to how much of product is in a tank.
Got a friend, client, or colleague who could use some of this information? Please share this article.
The RealPars Team