Linear Variable Differential Transformer or LVDT is a long, and somewhat intimidating name for a device that can also simply be described as a linear displacement sensor.
What is an LVDT?
An LVDT can be defined as an electromechanical passive inductive transducer. Let’s take a step back and define all of those – also somewhat intimidating words!
– Devices that include both electrical and mechanical processes are called electromechanical devices.
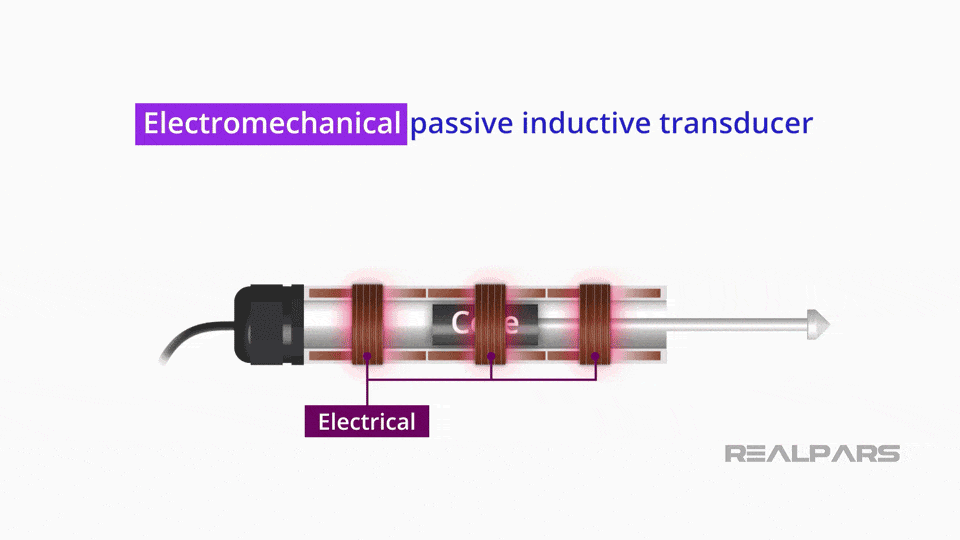
– As suggested by their own name, Passive devices are not capable of generating energy; they can, however, store and also dissipate energy.
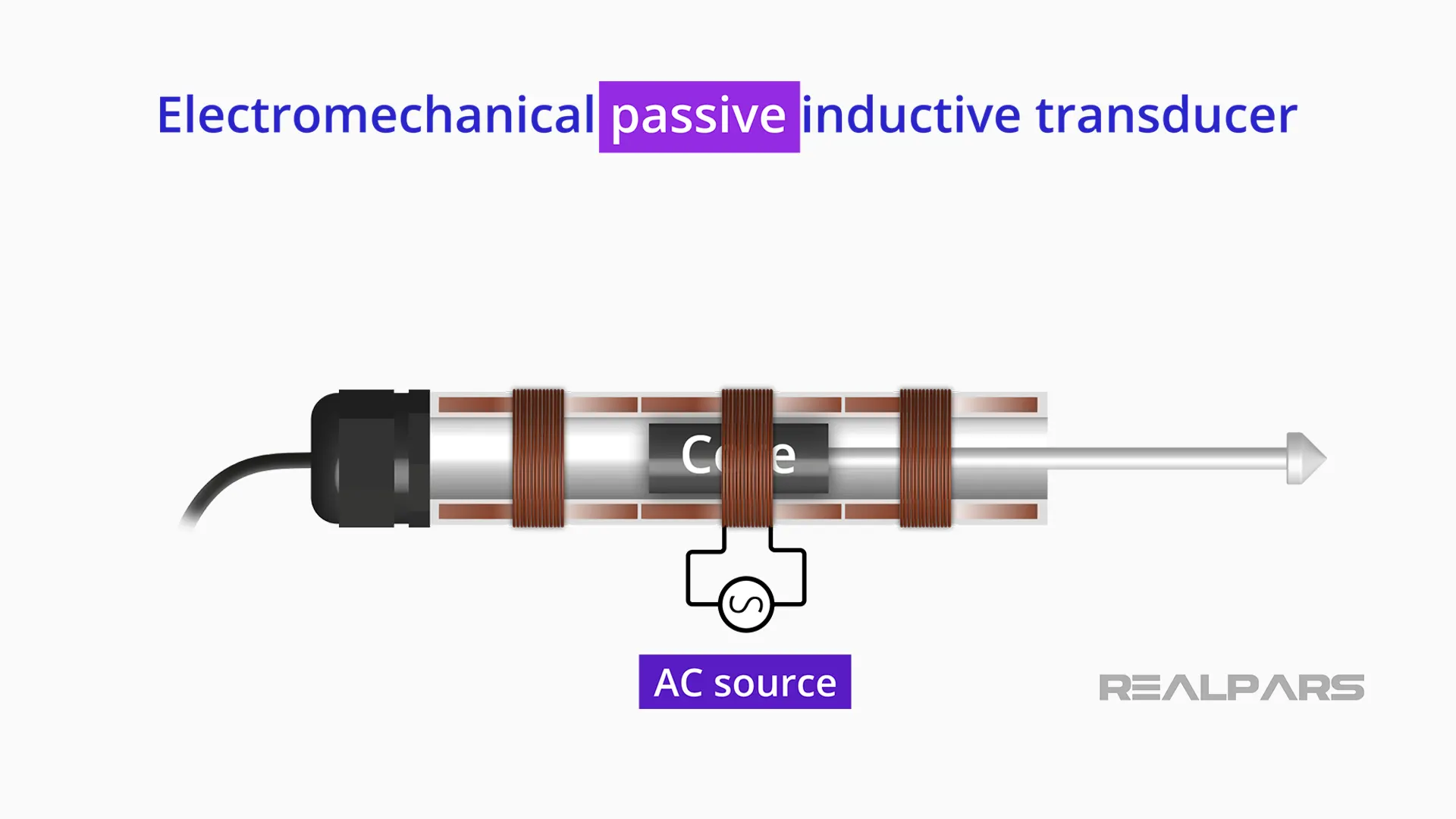
– Inductive refers to energy storage as an electromagnetic field.
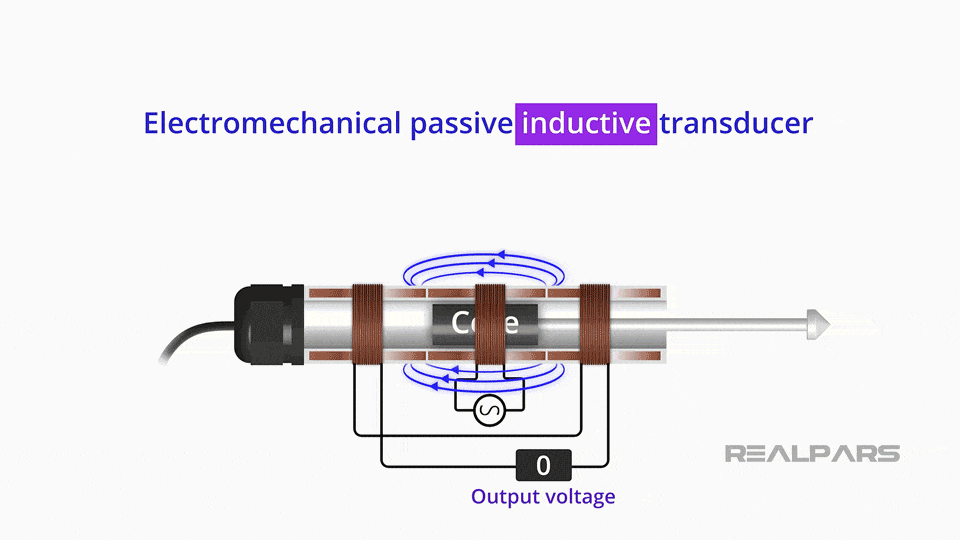
– An electronic device that is capable of converting energy between one form into another is called a transducer.
Therefore, from its definition, an LVDT is an electromechanical passive inductive transducer.
We now know that our LVDT is an electronic device that has both electrical and mechanical processes, it requires an external power source to be able to operate, it stores electromagnetic energy and converts some form of energy into a readable signal… to describe the movement of a body along a sole axis, or what we call linear displacement!
Areas of LVDT applications
An LVDT Sensor is one of the most accurate and reliable methods for determining linear distances.
They are commonly used in a very wide range of applications across numerous industries. They can be used to detect vibration, for stress testing, to measure great displacements such as actuator movement, brake pedal travel, among much else!
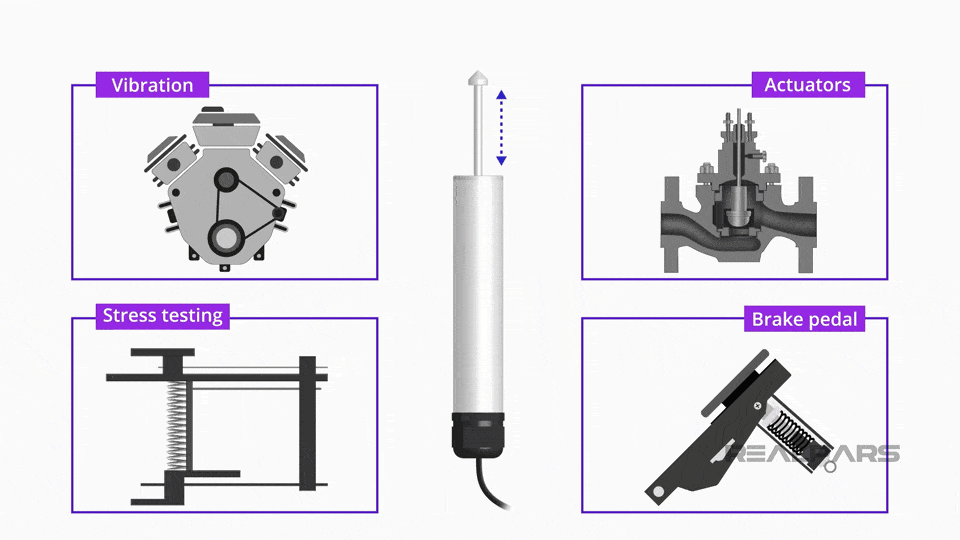
Structure of an LVDT
Looking at a cutaway of an LVDT, we can see that:
– The LVDT consists of three high-density glass-filled coils, wound around a hollow, insulated tube that is non-magnetic.
– The primary coil is located in the center, and the other two are identical secondary windings, located at an equal distance of the primary coil.
– The differential part of this sensor’s name comes from the fact that those two secondary coils are in opposite phases.
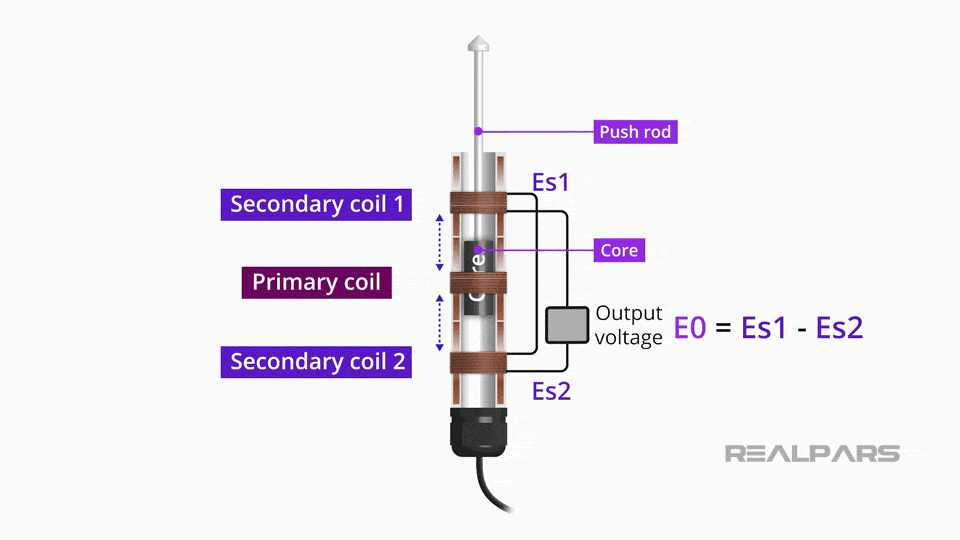
They are electrically 180 degrees out of phase with each other and are connected in series. This connection results in an output that is the difference between the voltages in these two windings.
On this cutaway we can also see a cylindrical-shaped soft iron core that is ferromagnetic, meaning that it is highly susceptible to magnetization.
This core is attached to a push rod that slides along the tube. This rod is attached to the body to measure its position displacement.
How does an LVDT work?
Continuous alternating current is applied to the primary coil, generating what we call primary excitation and a varying magnetic field. This primary excitation interacts with the secondary coils, which then induces current and voltage to be produced in the secondary coils.
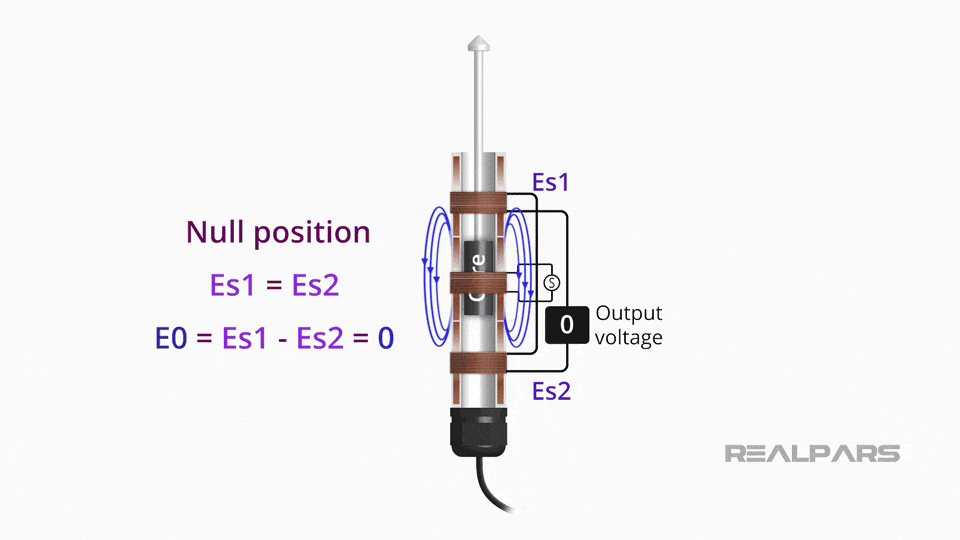
Core at null position
– When the ferrous core is dead centered, which is also called at the null position, the induced magnetic flux to each of the secondary coils is equal.
We know that they are electrically 180 degrees out of phase with each other, therefore, they will cancel each other, and the output voltage will be zero. This characteristic is used when calibrating an LVDT sensor.
Core displacement
As the core moves from this null position, the net induced voltage changes.
– When it moves upwards, the induced magnetic flux on the upper secondary winding is greater than the induced magnetic flux on the lower secondary winding. This results in a positive output voltage.
– When it moves downwards, the induced magnetic flux on the upper secondary winding is less than the induced magnetic flux on the lower secondary winding. This results in a negative output voltage.
Due to those characteristics, the direction in which the body is moving, and the distance can be determined by observing the voltage output increasing or decreasing, and its negative or positive value.
LVDT connection
LVDTs can have lead wires or be provided with connection sockets.

As both secondary coils are typically wired in series, the sensor has four wires or four connections in its connection socket. However, some LVDTs will provide the secondary coil lead pairs separately.
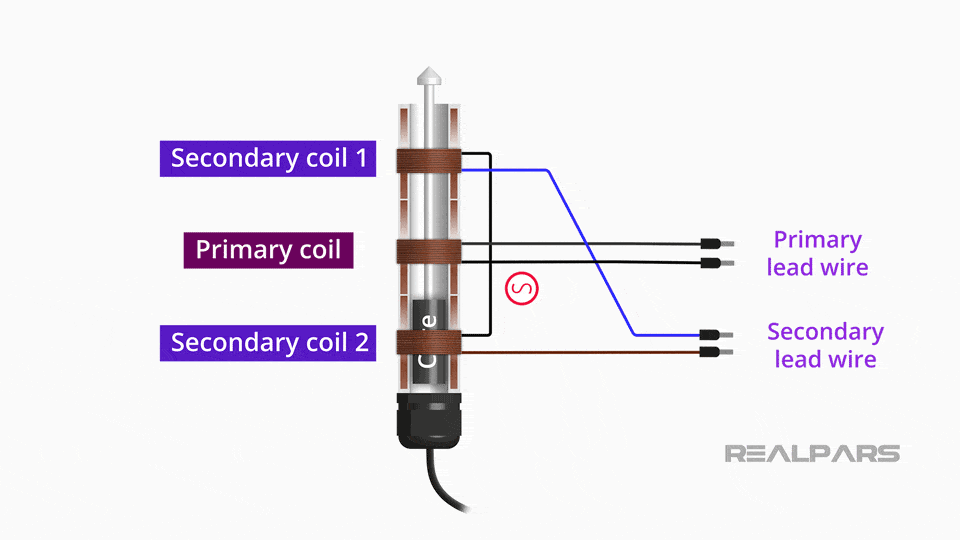
LVDT signal conditioning module
When initially introduced, all LVDT position sensors were operated by strictly alternating current.
Today’s technology, however, allows for signal conditioning, or in other words, it allows signal manipulation in a way that prepares it for the next processing phase to be done inside the sensor’s housing.
The ease of direct current operation can be applied, maintaining all desirable characteristics of the alternating current LVDT.
However, the electronic materials in the signal conditioning module bring limitations to the DC-operated LVDTs, such as the temperatures it can operate.
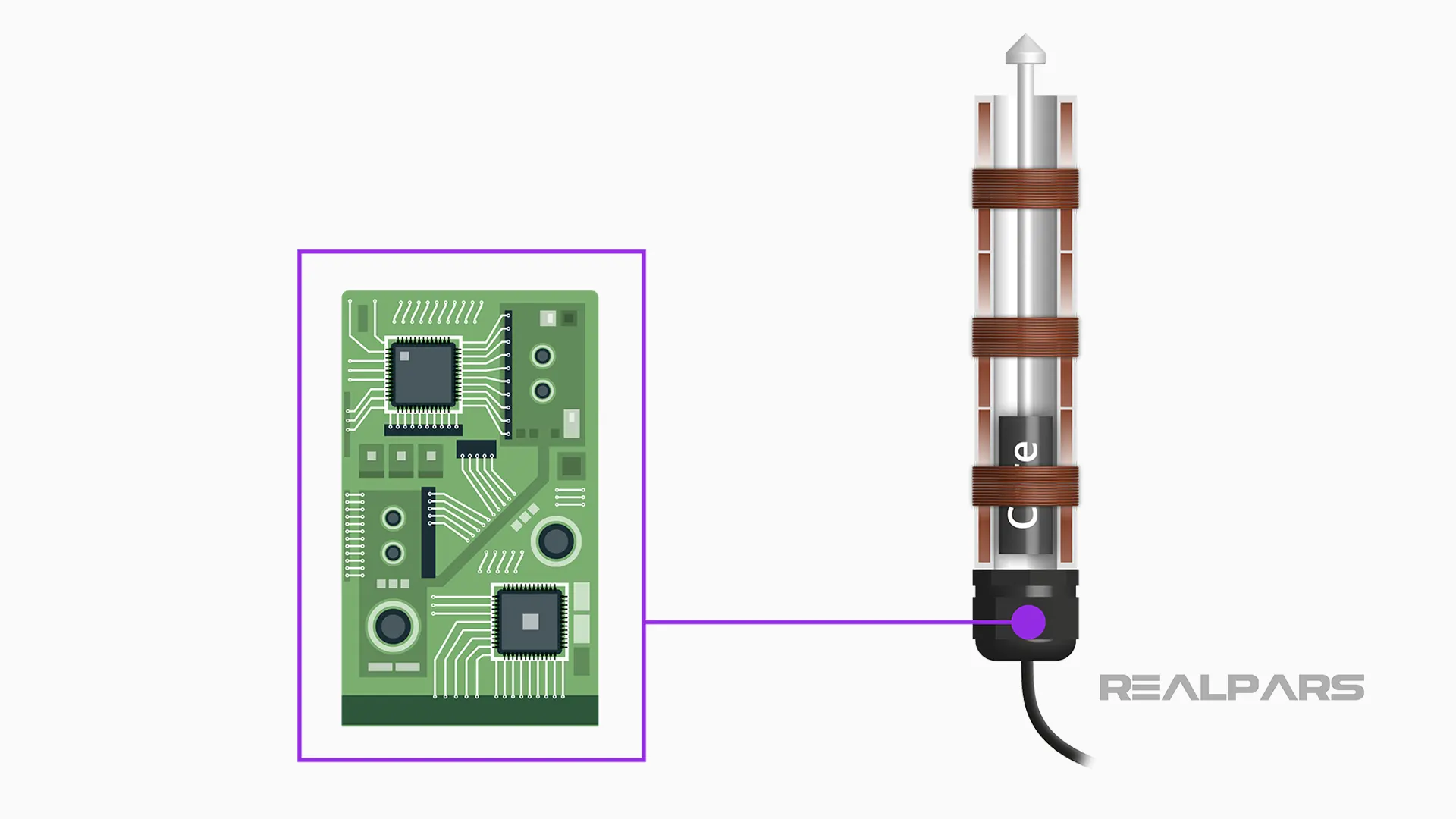
Summary
Now let’s review what we have learned…
– Linear Variable Differential Transformer is a sensor used to convert linear motion into an electrical signal.
– They are used in numerous applications throughout many different industries to detect vibration, for stress testing, to measure actuator movement, etc.
– The LVDT consists of a hollow cylindrical array of coils: primary and secondary windings.
– An alternating magnetic field in the primary coil induced magnetic field on both secondary coils.
– The magnetic fields induced on the secondary coils depend on the position of the cylindrical ferrous core that passes through the center of the hollowed tube.
– When the core is positioned in the null position, the output signal is zero. Moving the core to either direction causes the output signal to increase.
– Current technologies allow for AC and DC LVDT sensors.
If you have any questions LVDTs or about sensors and measuring instruments in general, add them in the comments below and we will get back to you in less than 24 hours.
Got a friend, client, or colleague who could use some of this information on linear variable differential transformers (LVDTs)? Please share this article.