In this article, we’re going to talk about pneumatic actuators. We’ll look closely at the operation and application of the most common pneumatic actuator, the spring/diaphragm linear pneumatic actuator.
First of all, let’s look at Actuators in general. What is an Actuator? Simply stated, an actuator is a device that makes something move or operate.
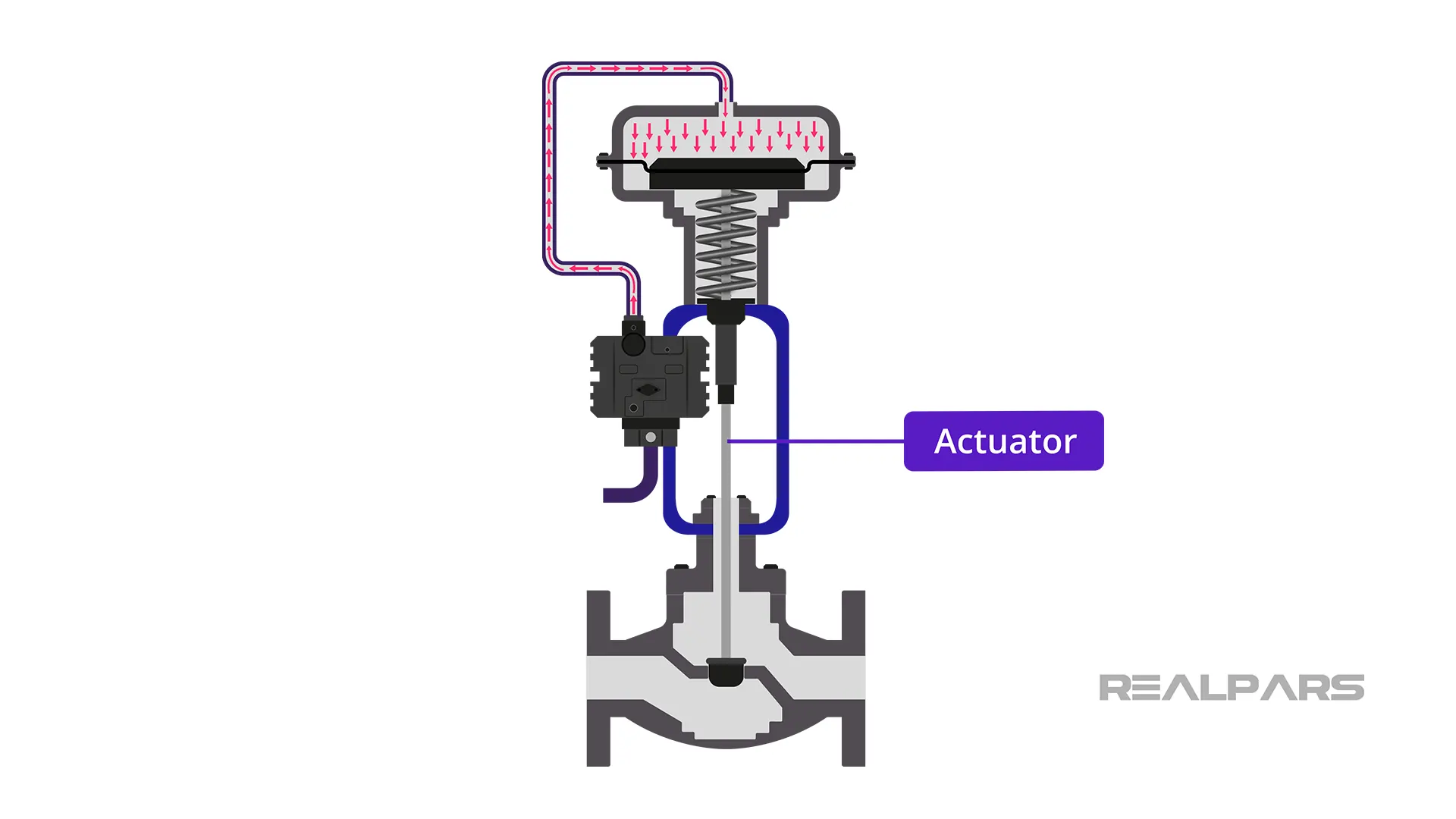
Actuators make life easier for us every day, and they are the workhorses of the industry. For example, your dentist uses an actuator to move the chair up and down.
Types of actuators by their energy source
There are three typical types of actuators used in industry as defined by their energy source.
The typical actuators in the industry include:
- Electric
- Hydraulic
- Pneumatic
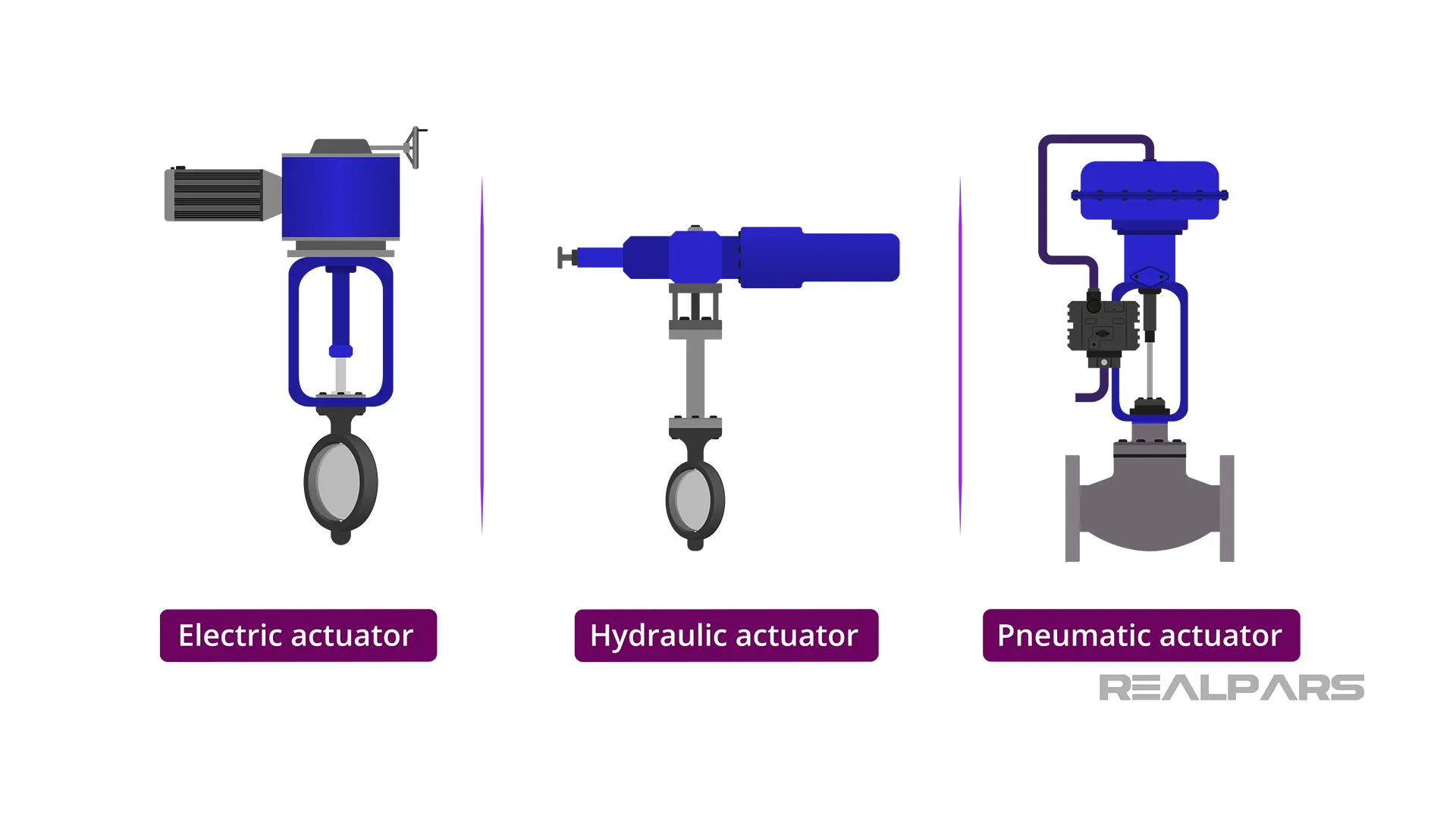
Pneumatic actuator working principle
Ok… Let’s move on to the focus of our article, the pneumatic actuator. A pneumatic actuator converts energy in the form of compressed air into movement.
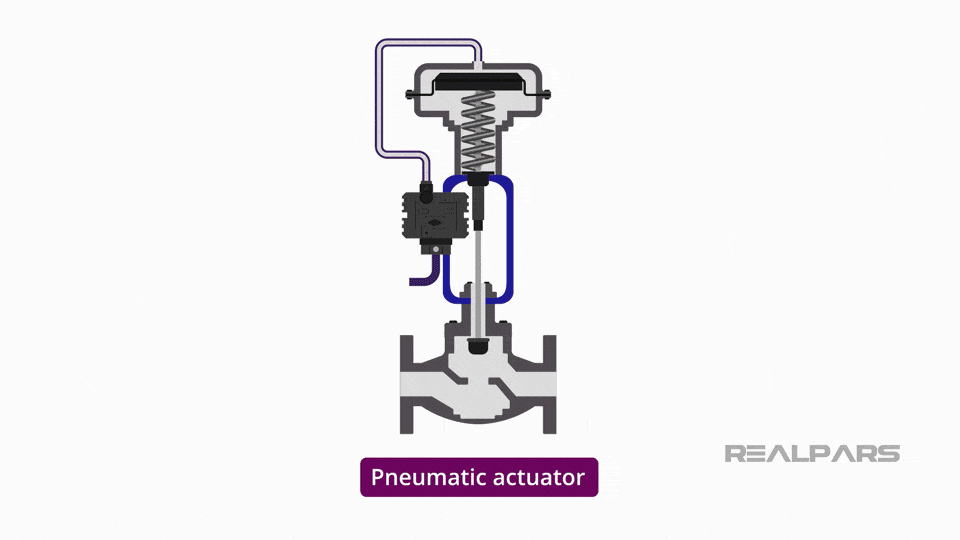
In other words, pneumatic actuators use compressed air to move a piston or diaphragm. By doing this, they convert air pressure into mechanical motion that drives a valve or lever.
By adjusting the air pressure, you can control the force and speed of the movement. This is usually done by PLCs in the industry.
Types of actuators by their motion
Pneumatic actuators are categorized by their type of motion. They are either Linear or Rotary.
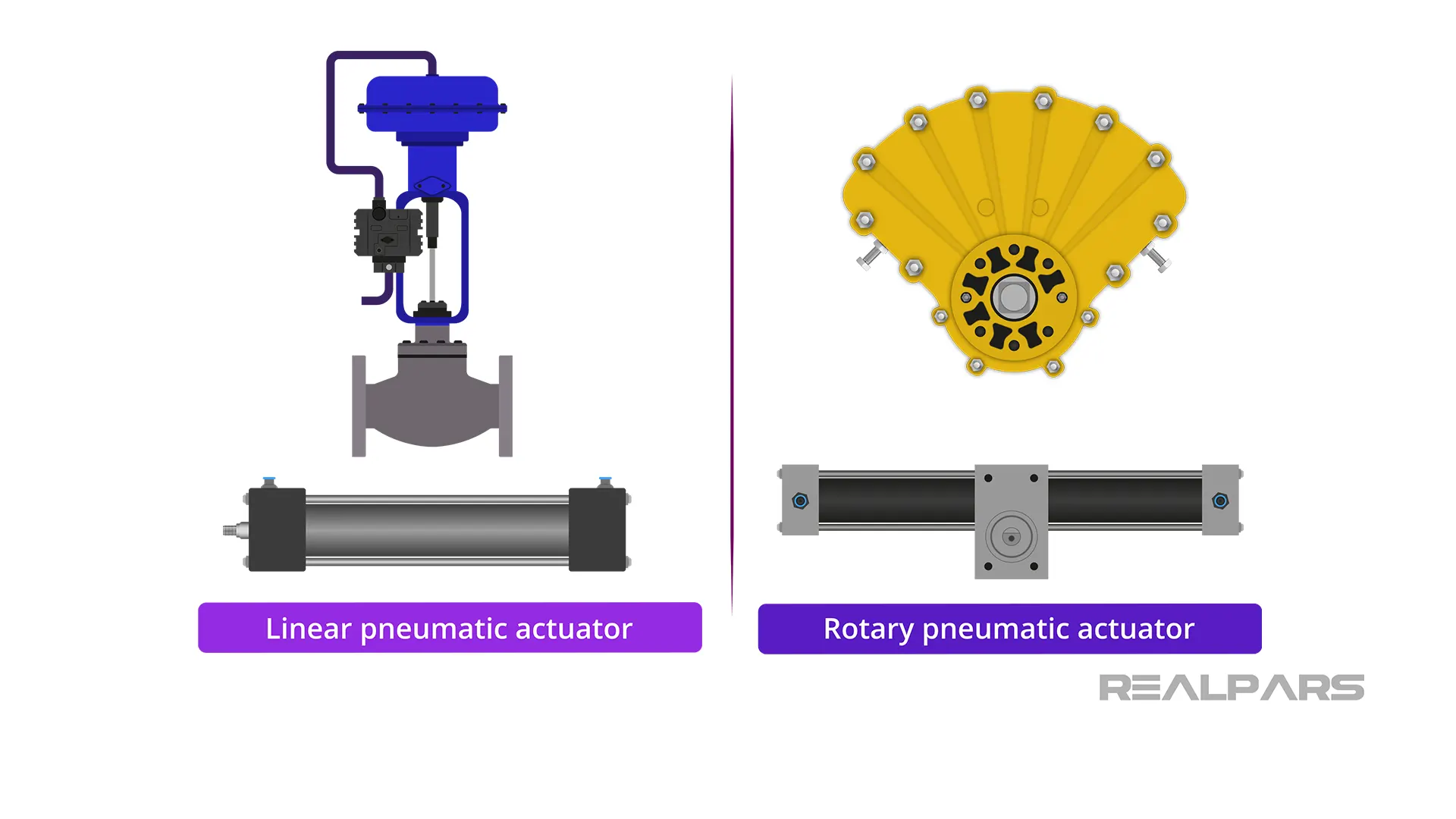
A linear pneumatic actuator can move something in a straight line. For example, a rod is moved in and out of a cylinder in a linear motion by a pneumatic energy source.
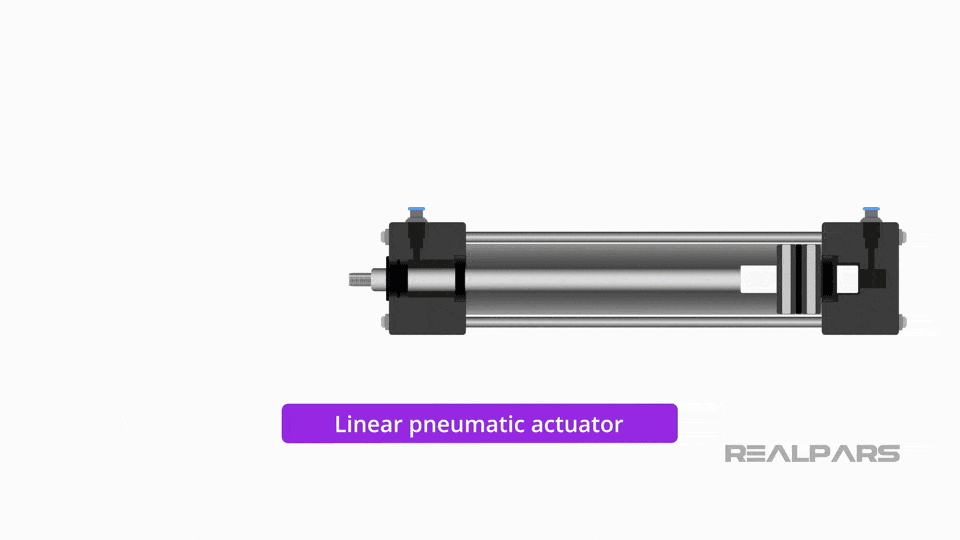
A rotary pneumatic actuator can make something move in a circular motion. For example, a rod in a rack and pinion drive system is used to produce rotary motion.
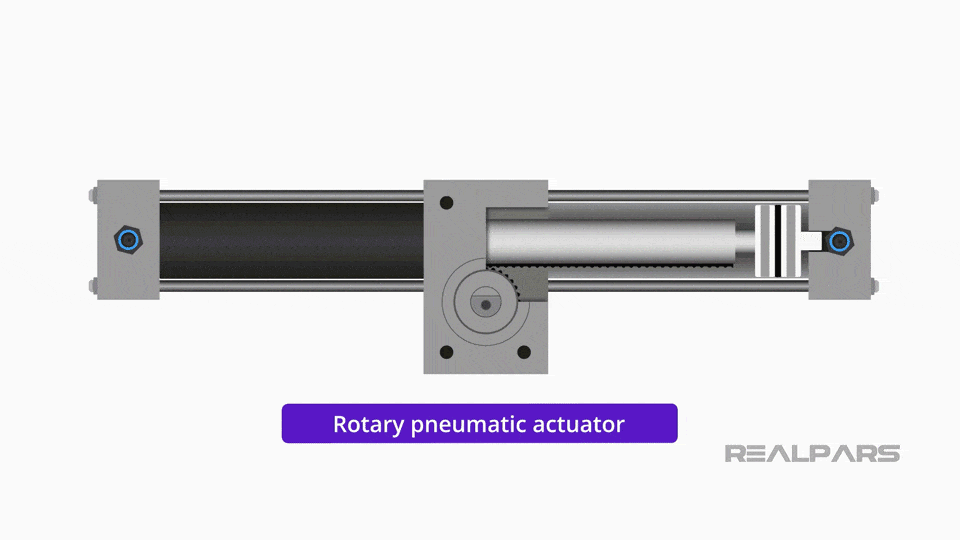
Let’s look at some examples of how Rotary and Linear pneumatic actuators are operated as there are many different types of each.
1) Rotary pneumatic actuator
In the Rotary pneumatic actuator category, the Vane style and the Rack and Pinion style are very common.
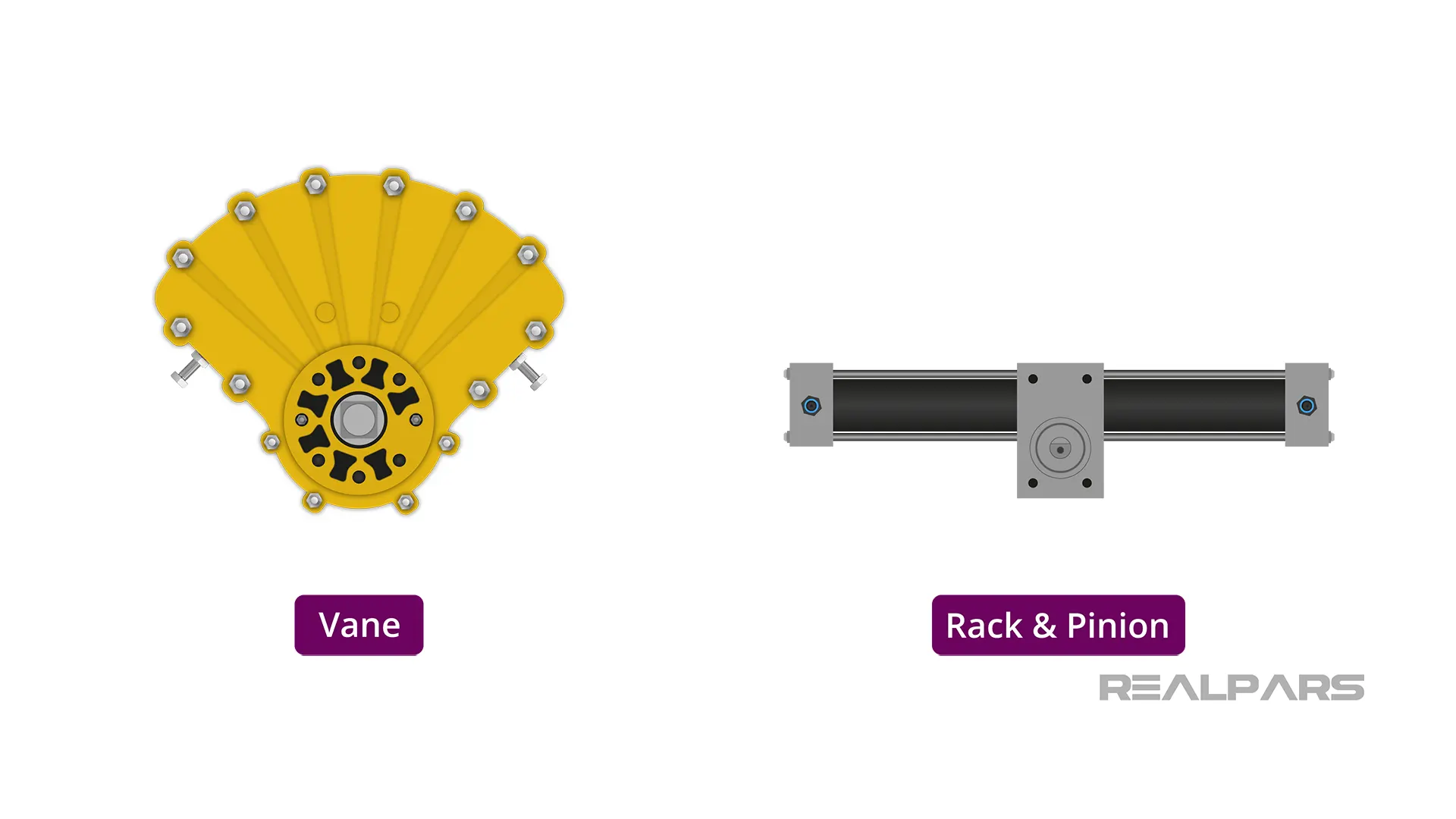
1-1) Vane Actuator
Vane Actuators have a cylindrical chamber in which a movable vane is mounted on a shaft. Pneumatic air under pressure applied on one side of the vane causes it to rotate through its stroke.
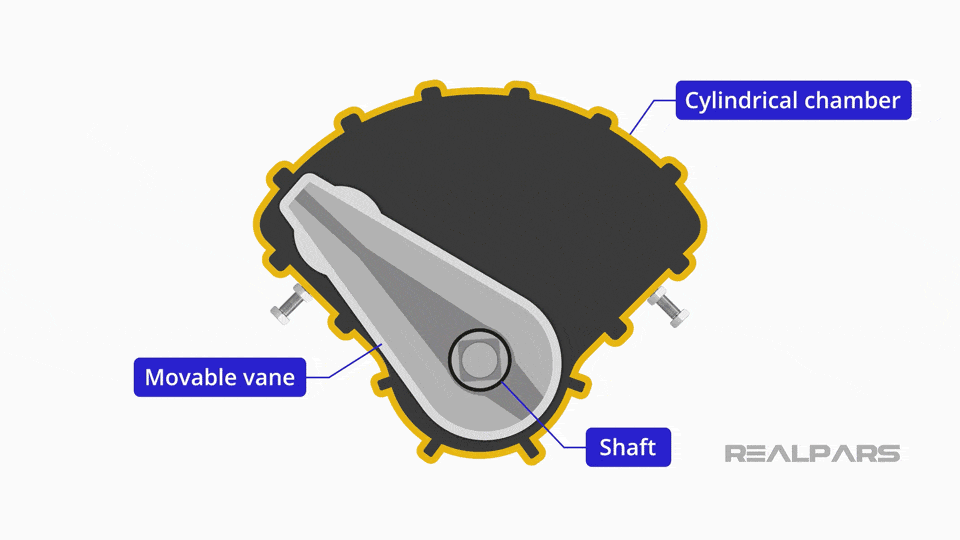
1-2) Rack and pinion
Rack and Pinion actuators use a piston attached to rack gear. When pneumatic pressure is applied, the piston and rack move linearly rotating the pinion gear and driveshaft.
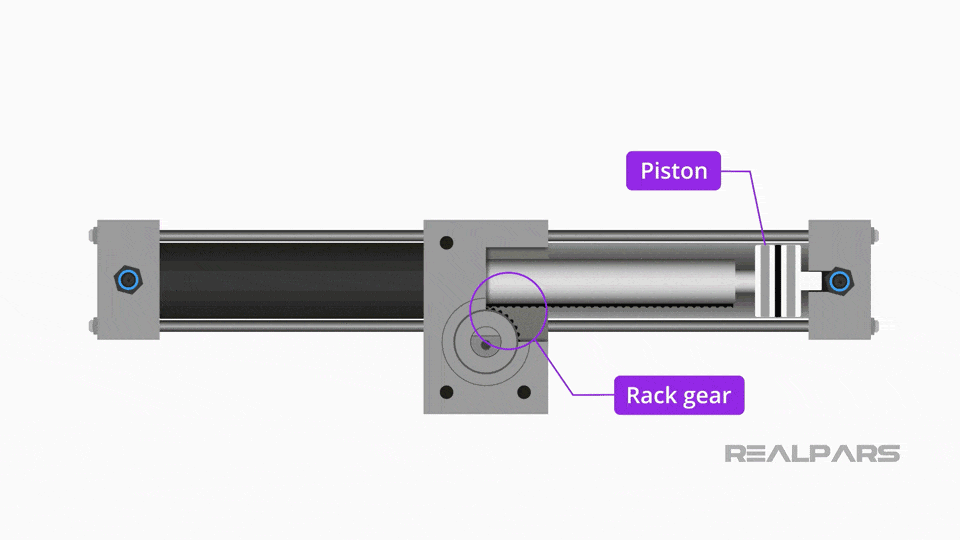
2) Linear pneumatic actuator
In the Linear pneumatic actuator category, the spring/diaphragm style and the piston style are very common.
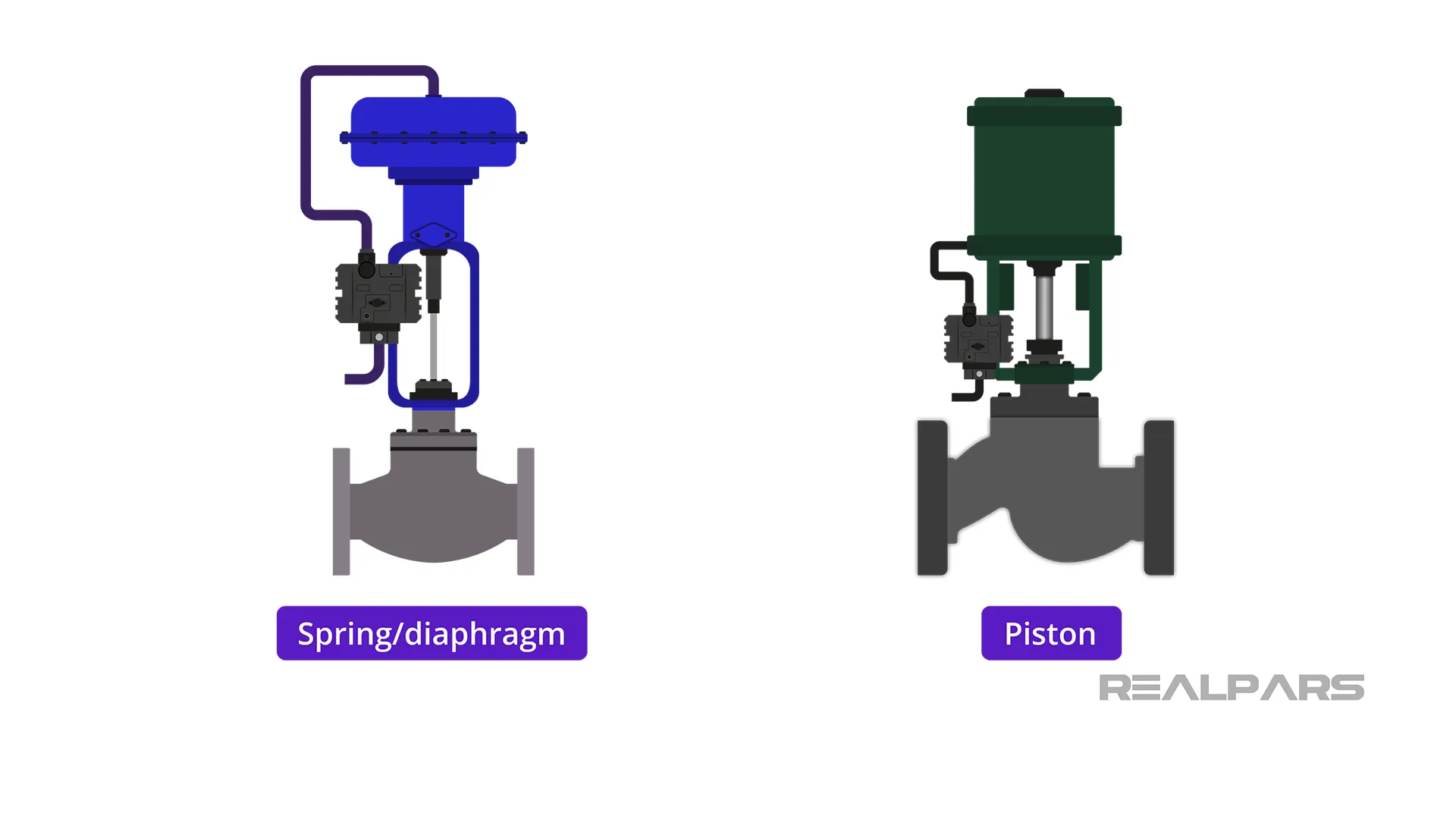
2-1) Piston
The piston-style pneumatic actuator utilizes a piston inside a cylinder. The movement of the piston is caused by applying pneumatic pressure thereby moving the piston upwards.
Removing the pneumatic pressure causes the piston to move downward due to the pressure of the spring. This motion is referred to as Air-to-Retract.
An Air-to-Extend motion can be also be achieved by rearranging the spring, piston, and pneumatic supply.
Here, you can see the two types of pneumatic piston actuators in action: an Air-to-Retract pneumatic valve actuator on the left and an Air-to-Extend pneumatic valve actuator on the right side.
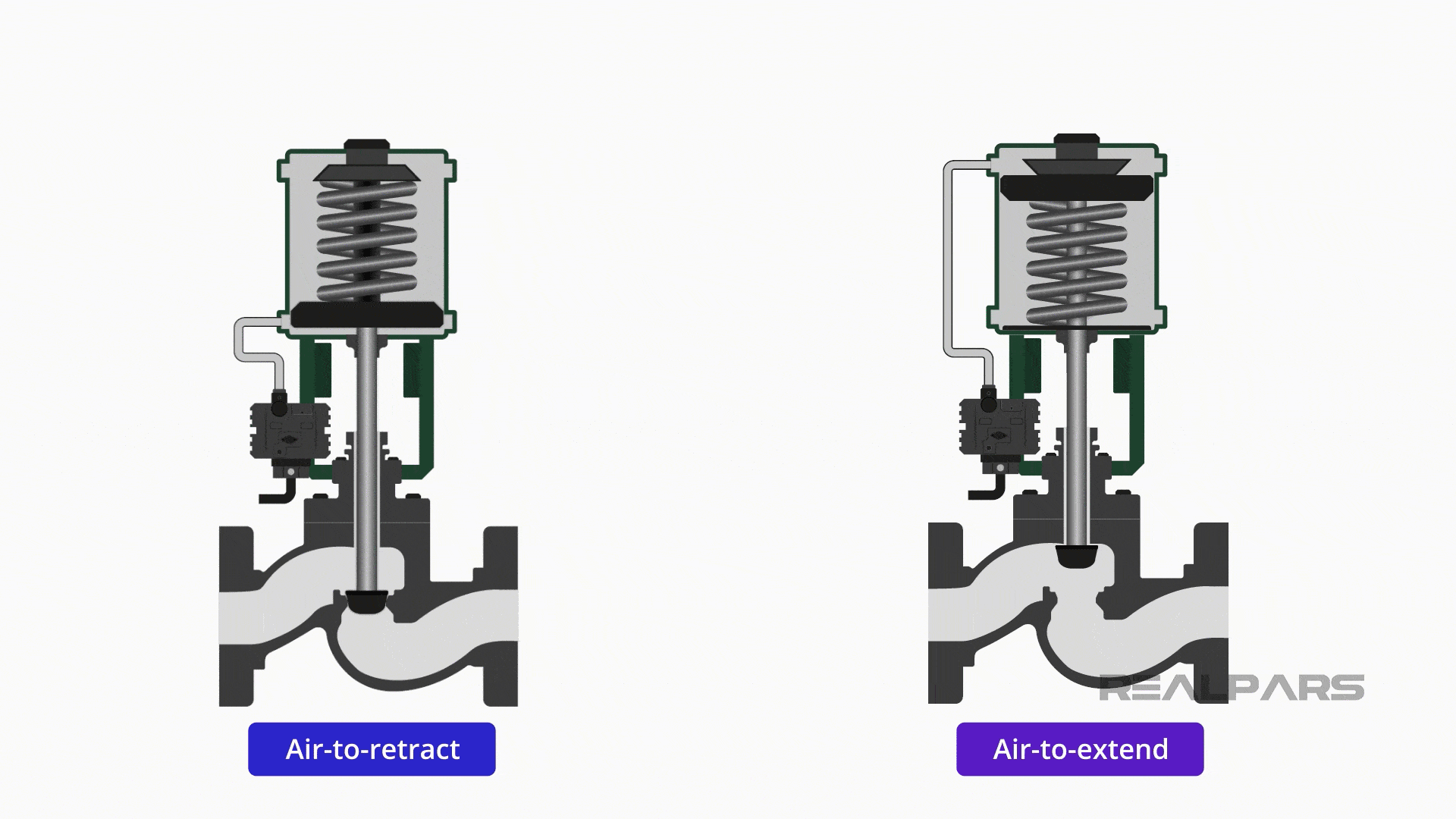
2-2) Spring/diaphragm
The spring/diaphragm pneumatic actuator is probably the most common actuator used to operate industrial process control valves. So, let’s have a closer look.
The spring/diaphragm pneumatic actuator consists of a diaphragm and plate that are connected to an actuator stem. A flexible diaphragm is enclosed in pressure-tight housing.
Here, you can see the different parts of a spring/diaphragm pneumatic valve actuator.
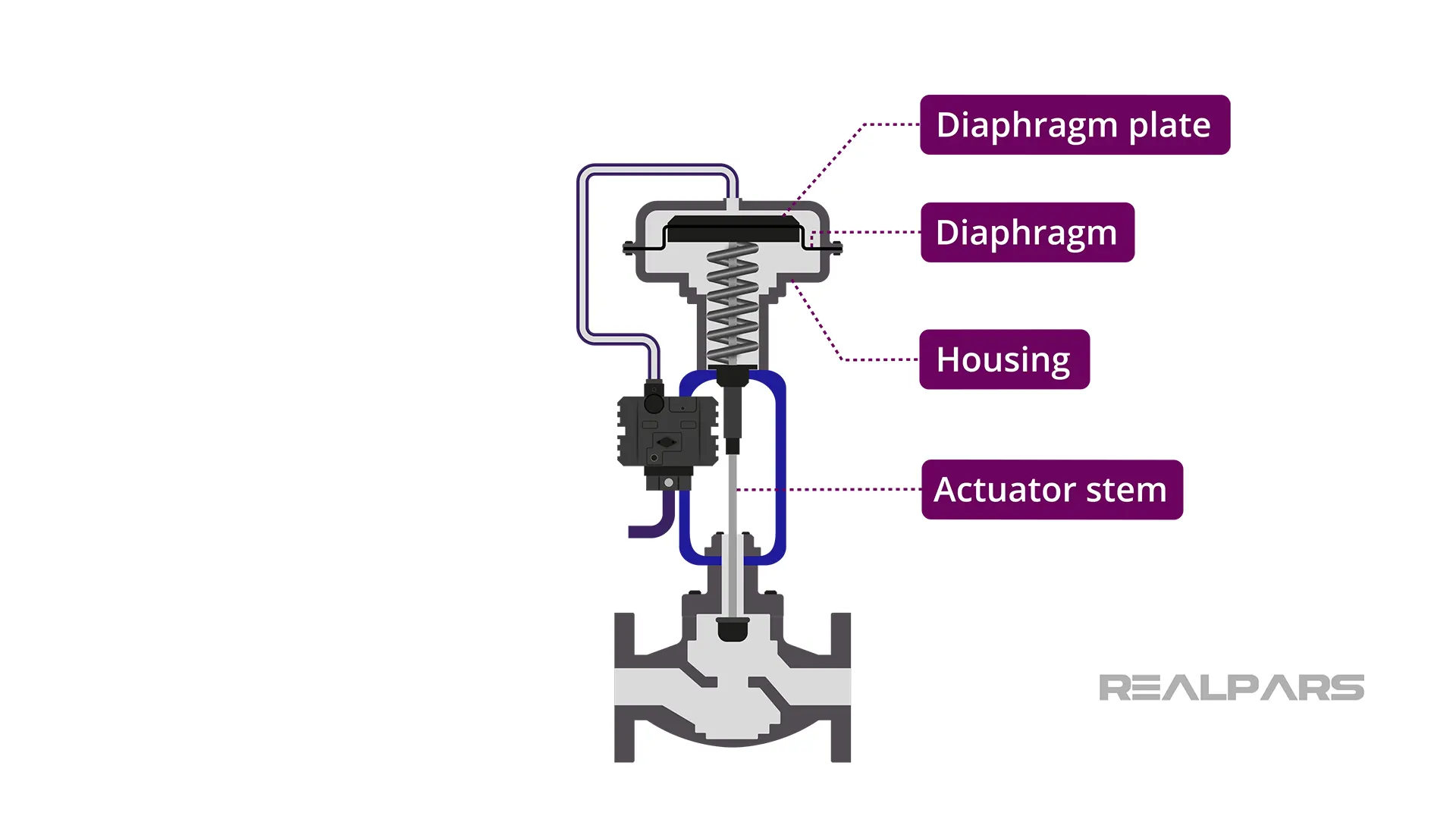
Pneumatic pressure enters this housing applying pressure to the diaphragm. As the air pressure increases to the diaphragm the force exerted against the spring increases causing the actuator stem to move.
Reducing the pneumatic pressure will cause the spring to retract the diaphragm.
The actuator stem will move a valve in or out of a valve body.
In an air-to-open operating condition, the spring forces the valve closed.
The air pressure on the diaphragm creates a force that overcomes the force of the spring and opens the valve.
By rearranging the spring pneumatic supply, this type of actuator can fail-open or fail-closed when air pressure is lost.
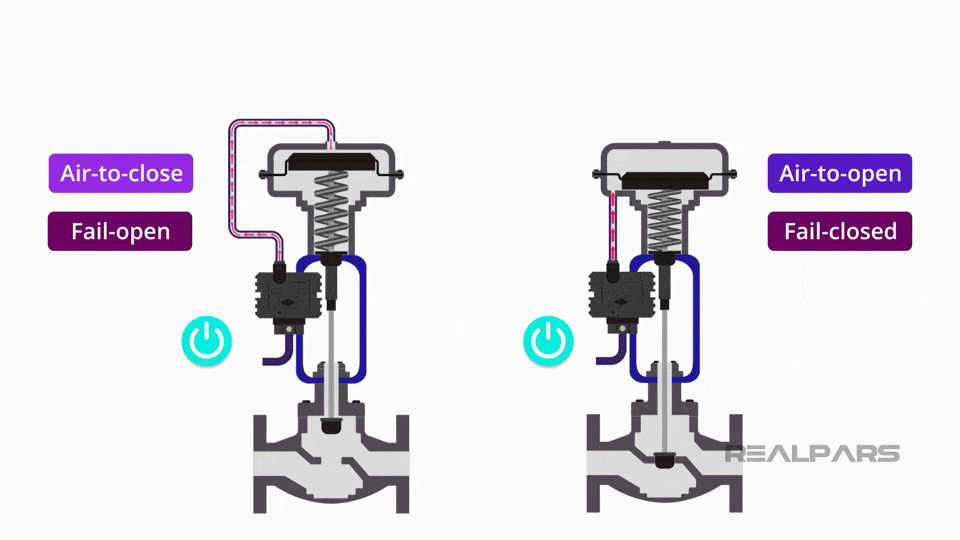
Pneumatic actuator in action
Let’s look at a typical spring/diaphragm pneumatic actuator connected to a flow control valve in action!
The PLC analog output card produces a 4 to 20 mA current to move the valve from fully open to fully closed.
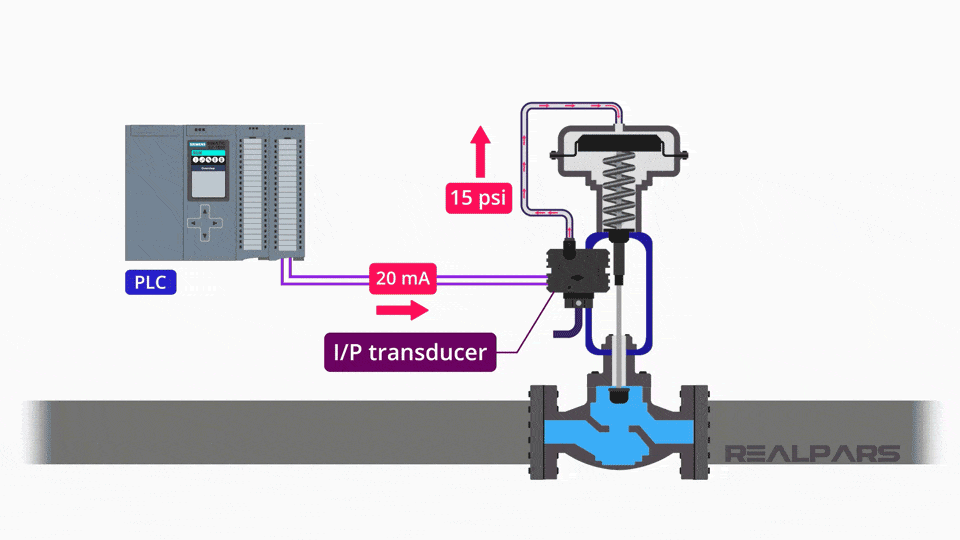
A signal conditioner called a current-to-pressure transducer or I/P will change the 4 to 20 mA into 3 to 15 psi.
Pneumatic actuators in robotics
Pneumatic actuators are widely used in robotics because they provide a fast solution for many motion applications. In robotics, these actuators are often used to control robot arms, grippers, and other components that require quick and repetitive movements.
While they might not offer the same precision as electric or hydraulic actuators, their high-speed operation makes them ideal for tasks where a rapid response is needed.
Summary
OK… Let’s review what we’ve discussed:
- An actuator is a device that makes something move or operate.
- An actuator receives a source of energy and uses it to move something.
- The three typical actuator energy sources are Pneumatic, Electric, and Hydraulic.
- A pneumatic actuator converts energy in the form of compressed air into motion.
- A pneumatic actuator can move something in a linear motion or a rotary motion.
- Linear pneumatic actuators include the spring/diaphragm style and the piston style.
- Rotary pneumatic actuators include the rotary vane style and the Rack and Pinion style.
If you have any questions about pneumatic actuators or about actuators in general, add them in the comments below and we will get back to you in less than 24 hours.
Got a friend, client, or colleague who could use some of this information? Please share this article.