In the industrial control world, we use the term I/O often. So, let’s begin our discussion today with an explanation of I/O. The focus of our discussion will be on Remote I/O, but we’re also going to talk about Local I/O too.
In this article, we’re going to:
– Explain the terms I/O, Local I/O, and Remote I/O
– Explain why Remote I/O is used in industrial applications
– List 2 transmission mediums used to connect between the local PLC and the Remote I/O
– List 2 transmission protocols used to communicate between the local PLC and the Remote I/O
What I/O Refers to in the Industrial World?
I/O stands for Input/Output.
In the industrial world, I/O refers to any device that transfers data to or from a computer such as a PLC.
For our discussion, we’ll refer to these I/O devices as I/O Modules.
Field Devices such as sensors and actuators are connected to the I/O modules.
The sensor signal representing a process variable such as liquid flow is converted by an Input I/O module and stored in the PLC memory.
The actuator receives an operating signal from an Output I/O module.
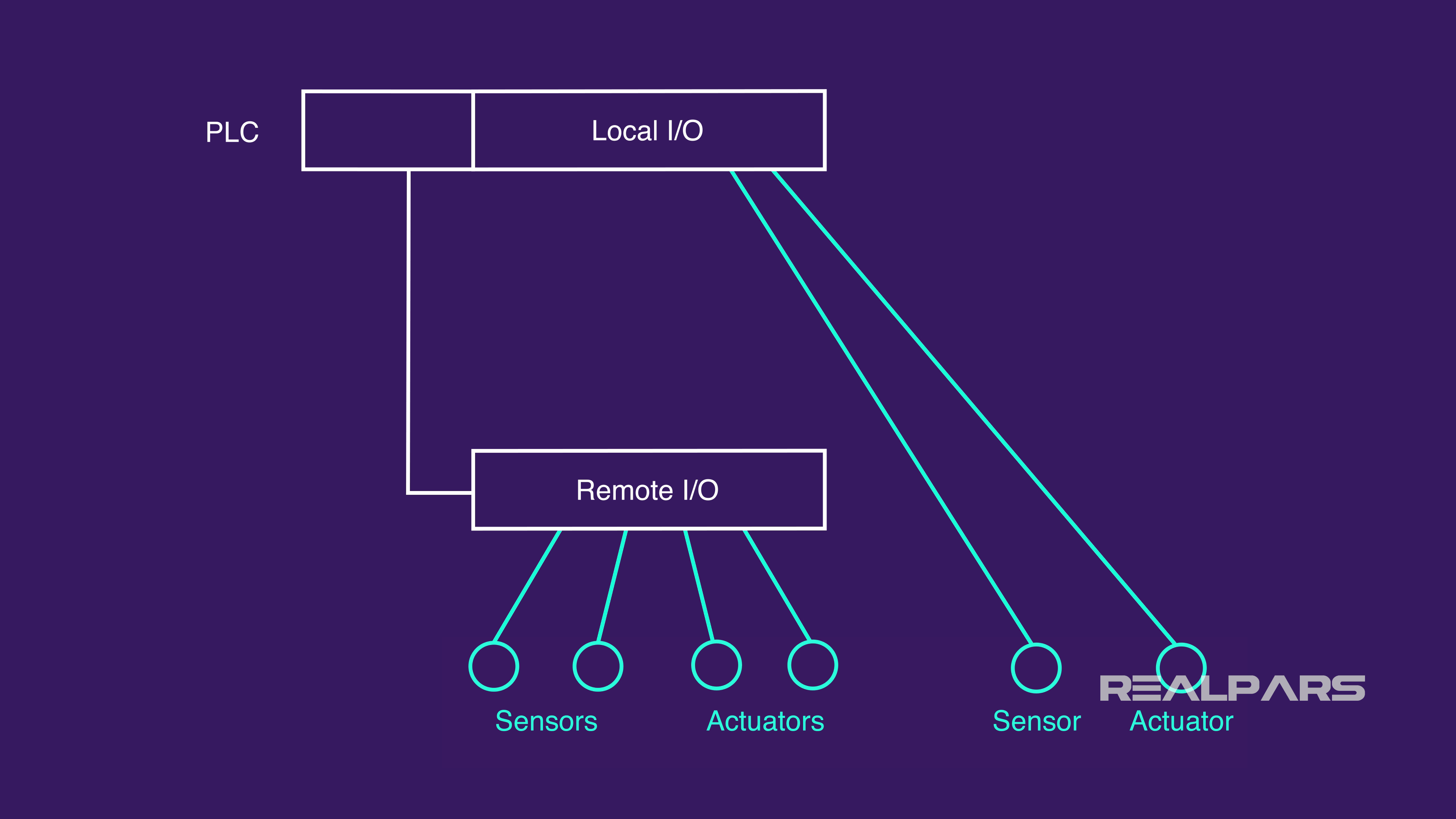
Local I/O VS Remote I/O
Local I/O refers to I/O modules that are housed in the same cabinet and likely connected to the controller backplane in the PLC rack.
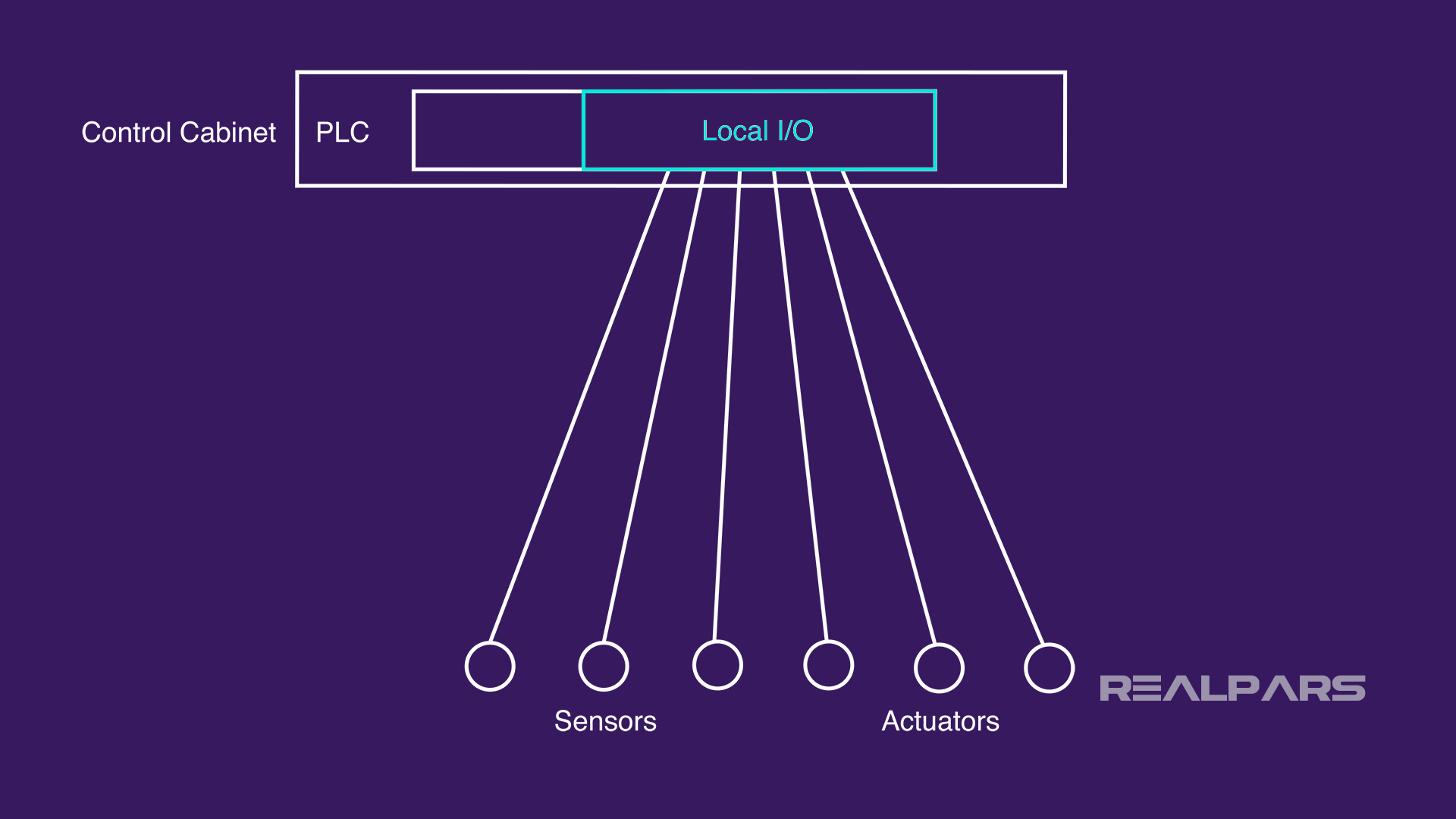
Remote I/O simply means that the I/O module is at a remote place physically located a distance from the control PLC.
A remote I/O module will speak to the PLC via an Adaptor Module connected to the controller backplane in the PLC rack.
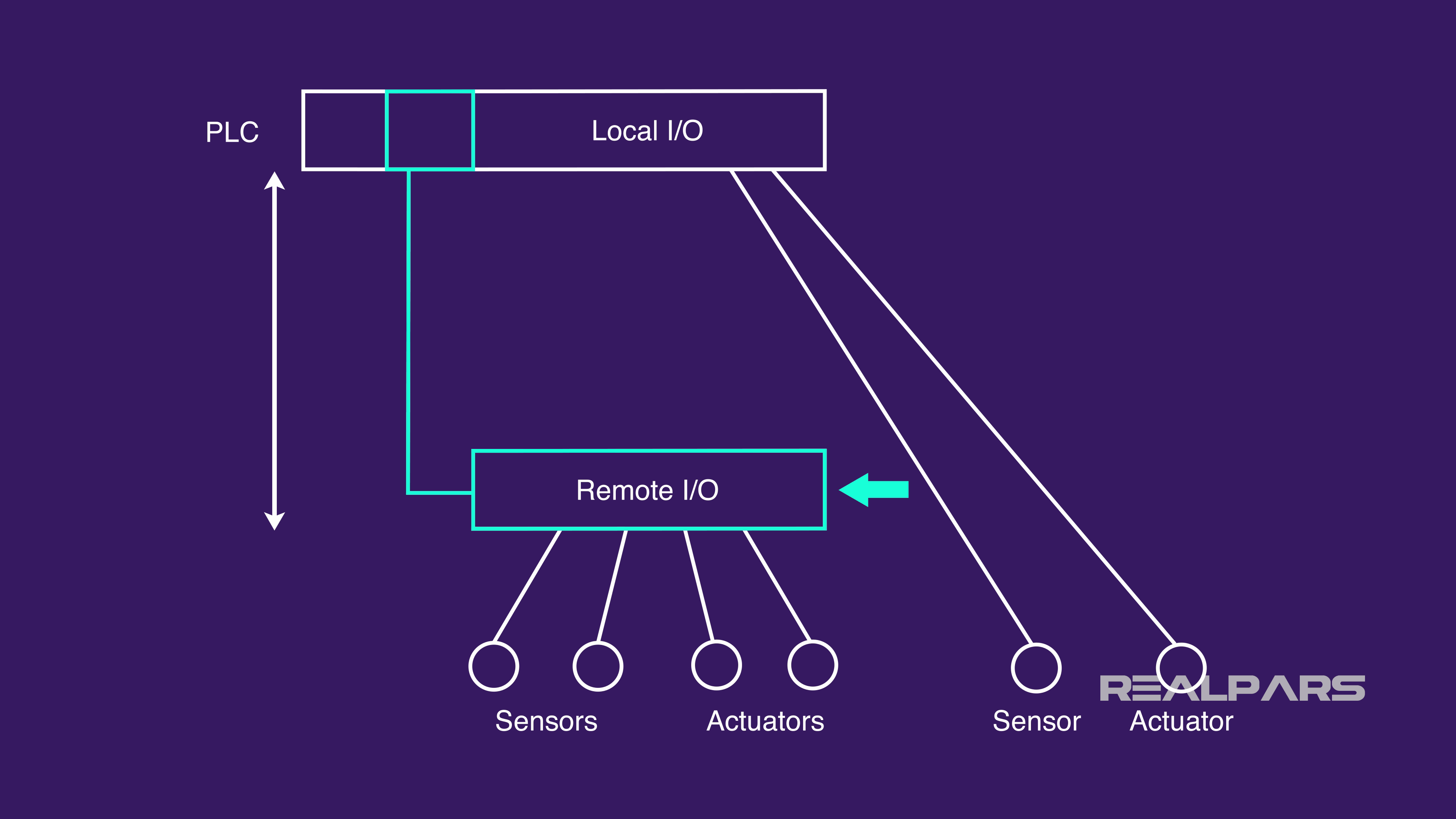
Why Do We Use Remote I/O?
There are several reasons…. let’s look at a few.
1) When it’s not possible to have a PLC near the field devices
In some industrial applications, it’s not possible to have a PLC with Local I/O Modules near the field devices because of the harsh environment.
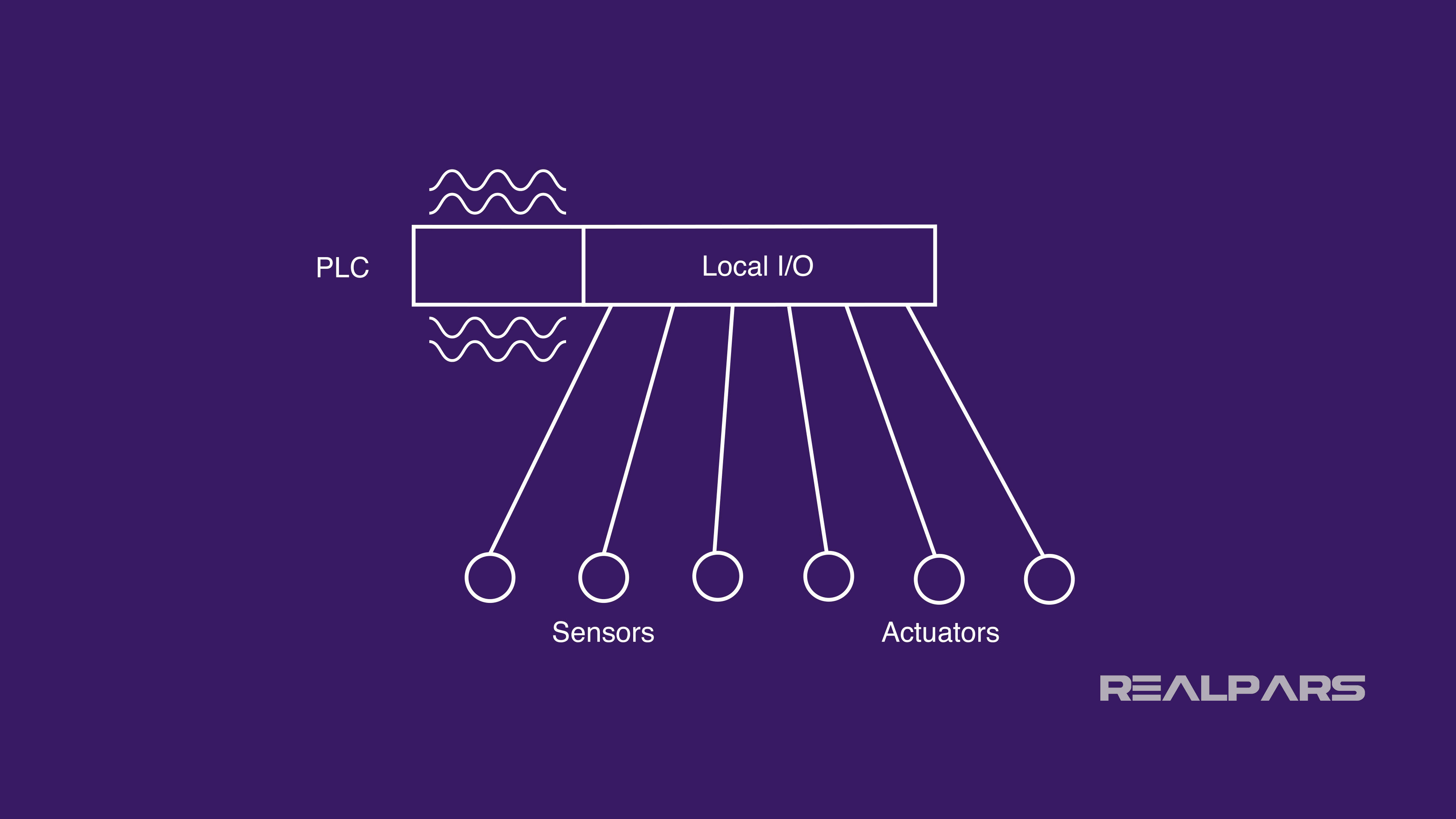
2) You want to eliminate long lengths of multi-conductor cable
Remote I/O is a solution when you want to place I/O modules close to the field devices in order to eliminate long lengths of multi-conductor cable.
With Remote I/O, signals can be received from far away sensors and control signals can be sent long distances to control valves, motors, and other final actuators.
Remote I/O Transmission Protocols
Signals can be sent any distance on a high-speed medium such as twisted-pair wires and fiber optics using a variety of transmission protocols such as Ethernet and Profibus.
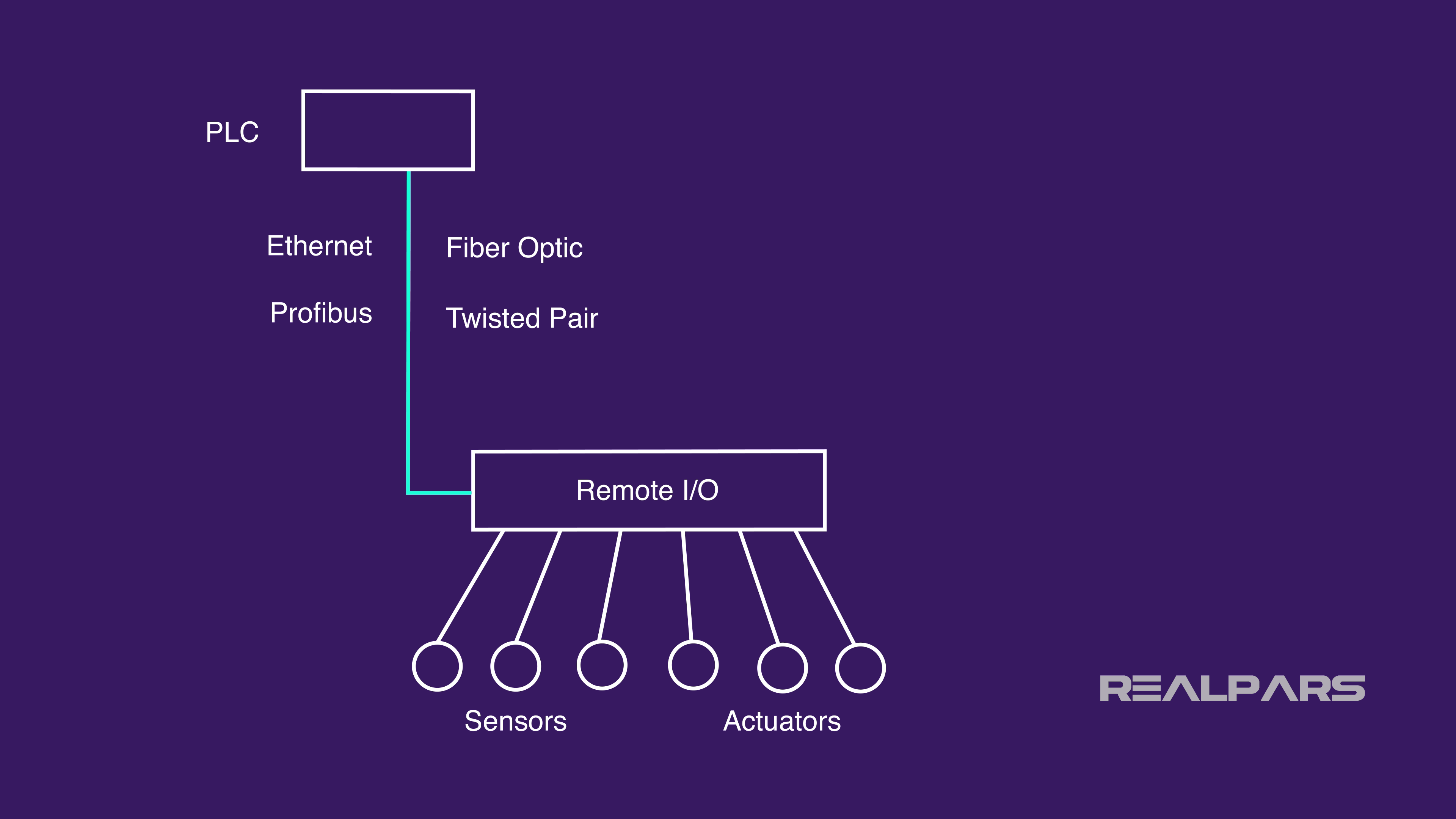
Summary
Let’s review what we’ve discussed.
– I/O stands for Input/Output
– I/O refers to any device that transfers data to or from a computer such as a PLC
– Field Devices such as sensors and actuators are connected to the I/O modules
– Local I/O refers to I/O modules connected to the controller backplane in the PLC rack
– A remote I/O module is physically located at a distance from the control PLC
Remote I/O’s are used:
– Because in some industrial applications, it’s not possible to have a PLC with Local I/O Modules near the field devices because of the harsh environment.
– When you want to place I/O modules close to the field devices to eliminate long lengths of multi-conductor cable
– Signals can be received from far away sensors and final actuators
– Signals can be sent any distance with a high-speed medium such as twisted-pair wires and fiber optics using a variety of transmission protocols such as Ethernet and Profibus
Want to Learn More?
You can gain instant access to a large number of exclusive RealPars courses covering a variety of industrial automation topics, including PLC and HMI programming, DCS, IIoT, and others, all for a small yearly membership fee.
It’s an amazing value for some really robust content and lots of support. And you’ll be getting the same course work that would cost you a few thousand for one week of offline training!
All of us on the RealPars team look forward to helping you continue to advance your PLC expertise and your career!
Got a friend, client, or colleague who could use some of this information? Please share this article.
The RealPars Team