Today you will learn about RS485. If you are familiar with RS232, then you may already know a little bit about it. If not, check out our other blog post What is RS232.
Just like it’s older brother RS232, RS485 is a form of serial communication. Think of RS485 as the younger, faster brother of RS232.
What made it such an advancement over RS232 was the fact that it could transmit not only a single device to device transmission, but also a communications bus to connect multiple devices at once.
The configuration and specifications of RS485 make it faster and extend the range of data transmission.
You aren’t limited to fifty feet of cable like with RS232. The maximum RS485 cable length is typically listed as 1200 meters or about 4000 feet.
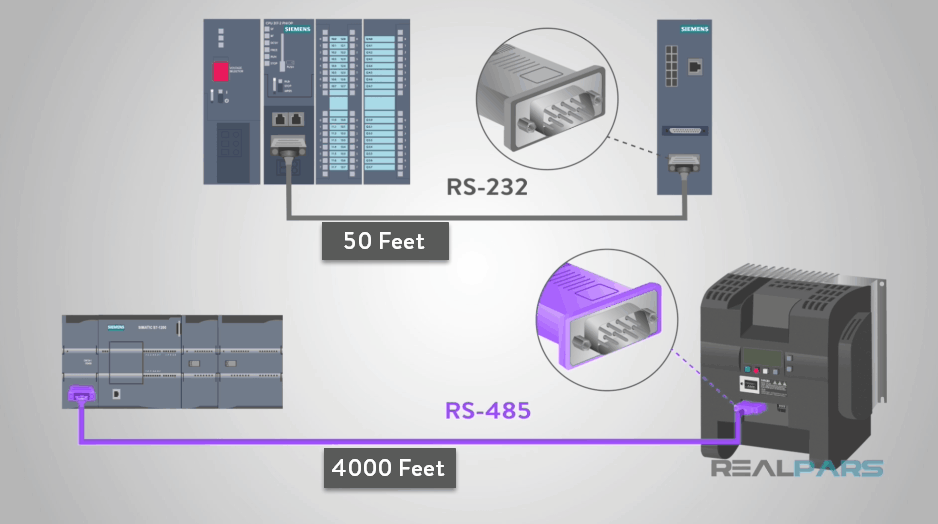
Much like RS232, RS485 doesn’t have an actual standard connector. Many times the old DB-9 connector is used.
In some applications, terminal strips were used in place of a connector. This helped RS485 become a widely used and very versatile form of serial communication.
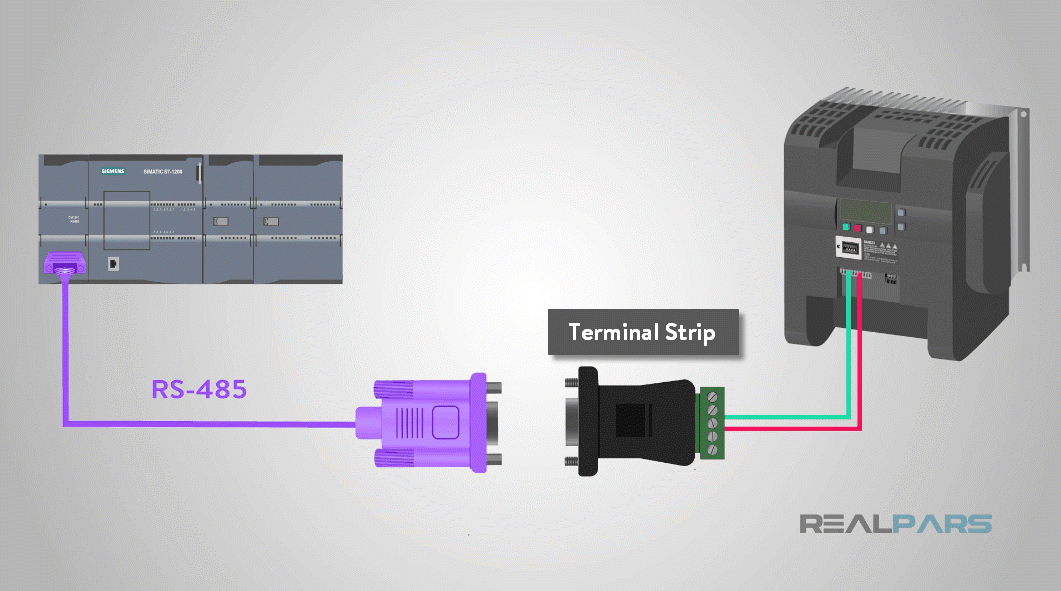
Another advantage over RS232 that I mentioned earlier is the number of connectable devices. RS485 can handle up to 32 connected devices. RS232 could only handle one. This allowed users in manufacturing facilities to connect larger applications and whole machines with one protocol.
Another plus for RS485 is that it is less susceptible to noise issues. Electric noise can cause all kinds of problems for electronics.
RS232 referenced ground to decipher the data it was transmitting. This allowed for electrical noise to cause interference.
RS485 avoids this issue which also allows for shielding of the cables to prevent noise. You may be wondering, what can I do with serial communications, especially RS485.
One very common example in the automation world is remote control of VFDs or Variable Frequency Drives. Many people just call them motor drives.
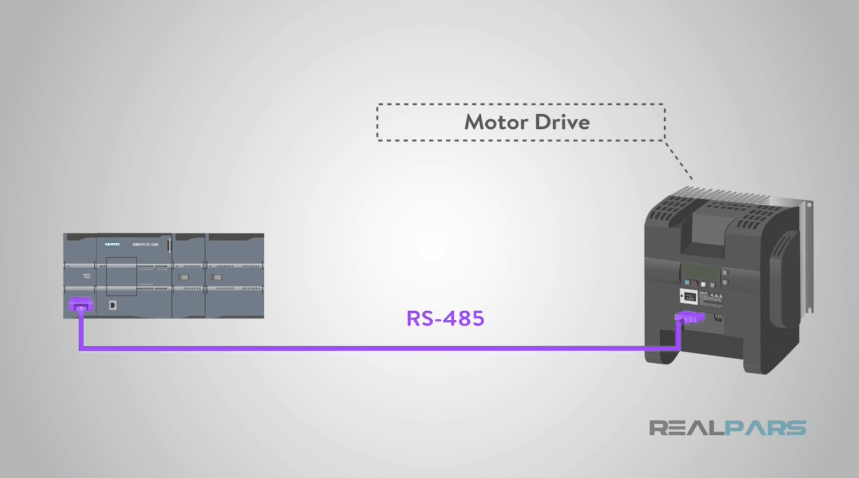
A simple network of a PLC, VFD, and an HMI allows remote control of motors in an industrial setting.
Let’s say you were monitoring a water pump filling a vessel. You decide that the water is not filling fast enough to keep up with demand. With your RS485 network, you can remotely monitor and control that pump from a control center.
This is possible since the HMI is connected to your PLC via RS485. The PLC is also connected to the VFD via RS485.
The PLC is programmed to monitor the level of the water in the vessel. It also allows manual flow control if needed.
All of this allows you to speed up the VFD that controls the speed of that water pump. Problem solved thanks to RS485 communications.
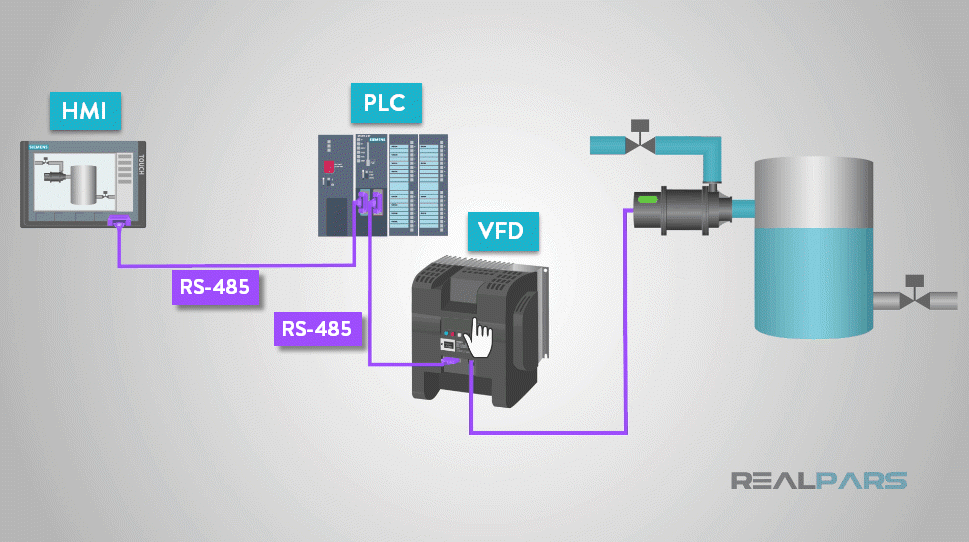
Let’s talk about what we now know about RS485. It is faster and much more versatile than the older RS232.
Users can utilize a longer cable, up to 1200 meters or 4000 feet.
The greatest feature of RS485 is the fact that you can connect up to 32 devices on one system. RS232 could only handle one at a time.
There is no standard connector for the protocol. Most manufacturers still utilize a DB-9 connector.
You can also still simply use a terminal strip. This makes utilizing RS485 simple. All in all, RS485 really allowed full automation possible with its ability to connect so many devices at once.
We at RealPars hope that you found it interesting, and that you will come back for more of our educational blogs. share your thoughts and ideas directly in the comments.
Thanks for reading and sharing our blog posts,
The RealPars Team