In this lesson we will continue the discussion on the topic of motion control. All of us at RealPars, hope you have been following our previous lessons on motion control and have begun to benefit from these lessons.
Now that we have learned about motion control motors, we can begin to explore some advantages and disadvantages when selecting, primarily between, the Servo Motor and Stepper Motor. In this lesson we discuss the disadvantages and advantages of Servo Motors when compared to Stepper Motors.
First let’s remember what we have learned about servo motor basics. The Servo Motor has the same construction of DC motor, it has a stator, rotor and controlling assemblies.
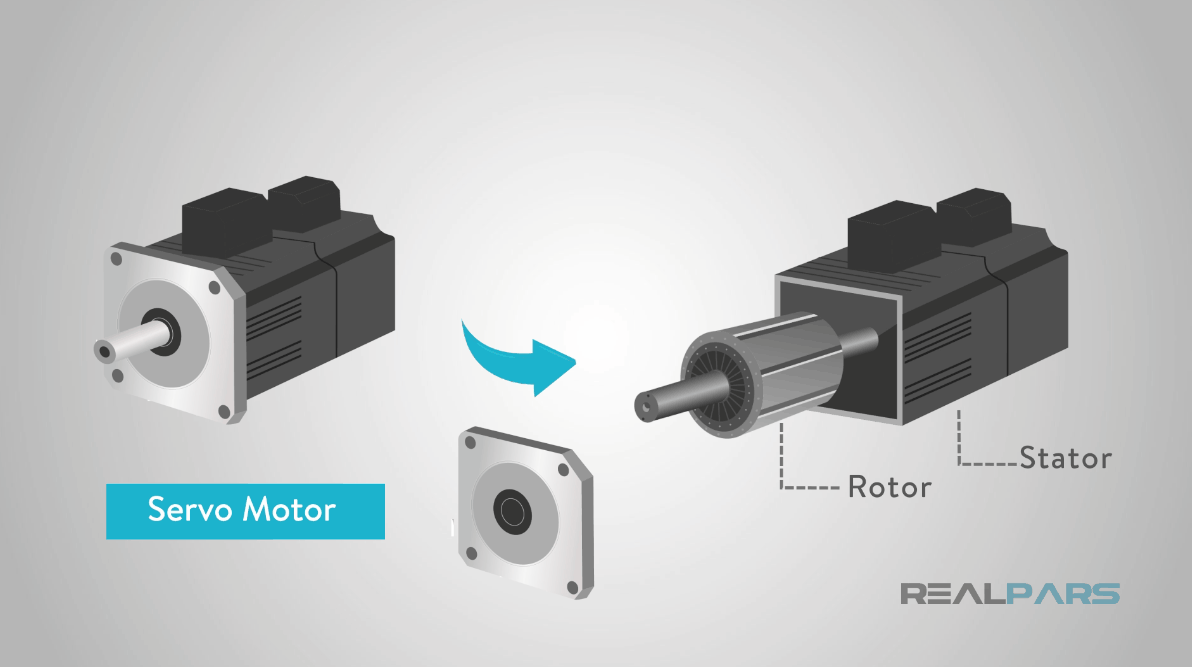
It also has feedback for controlling the speed & torque.
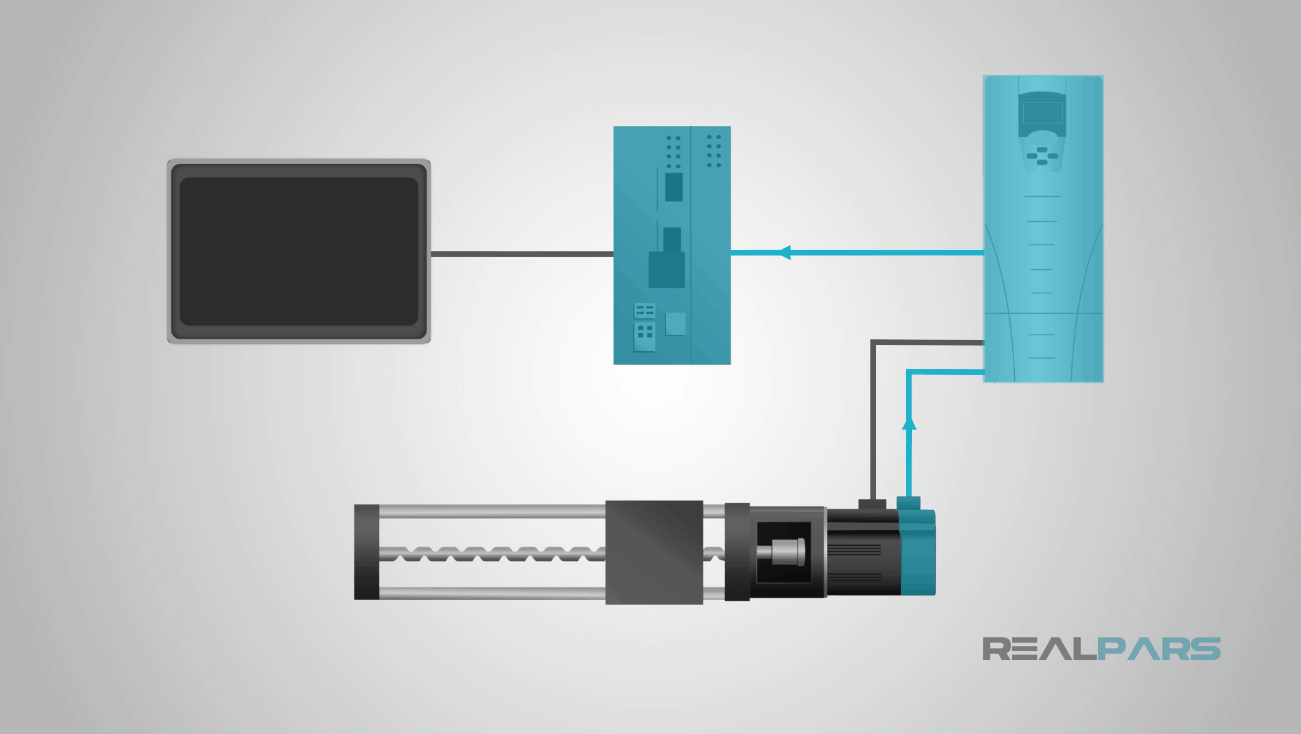
A Servo Motor is a self-contained electrical device, that rotate parts of a machine with high efficiency and with great precision.
The output shaft of this motor can be moved to a particular angle, position and velocity that a regular motor does not have.
The Servo Motor utilizes a regular motor and couples it with a sensor for positional feedback.
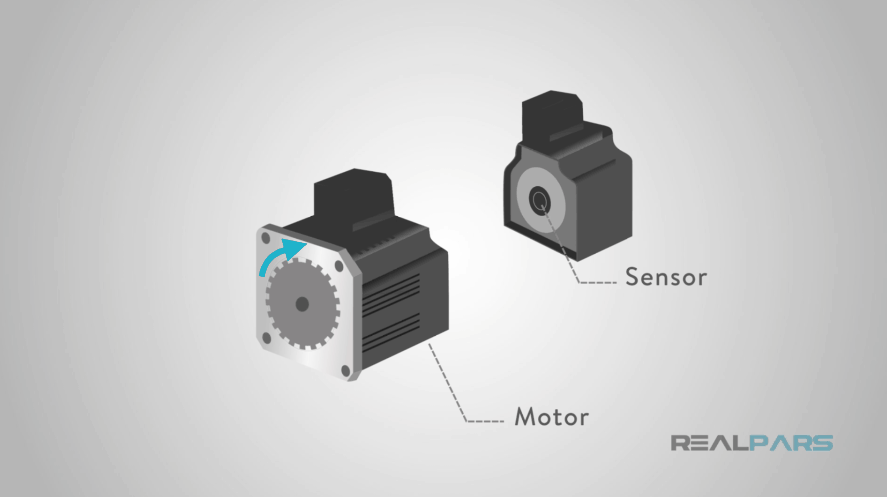
The controller is the most important part of the Servo Motor designed and used specifically for this purpose.
The Servo Motor is a closed-loop mechanism that incorporates positional feedback in order to control the rotational or linear speed and position.
The motor is controlled with an electric signal, either analog or digital, which determines the amount of movement which represents the final command position for the shaft.
A type of encoder serves as a sensor providing speed and position feedback. This circuitry is built right inside the motor housing which usually is fitted with gear system.
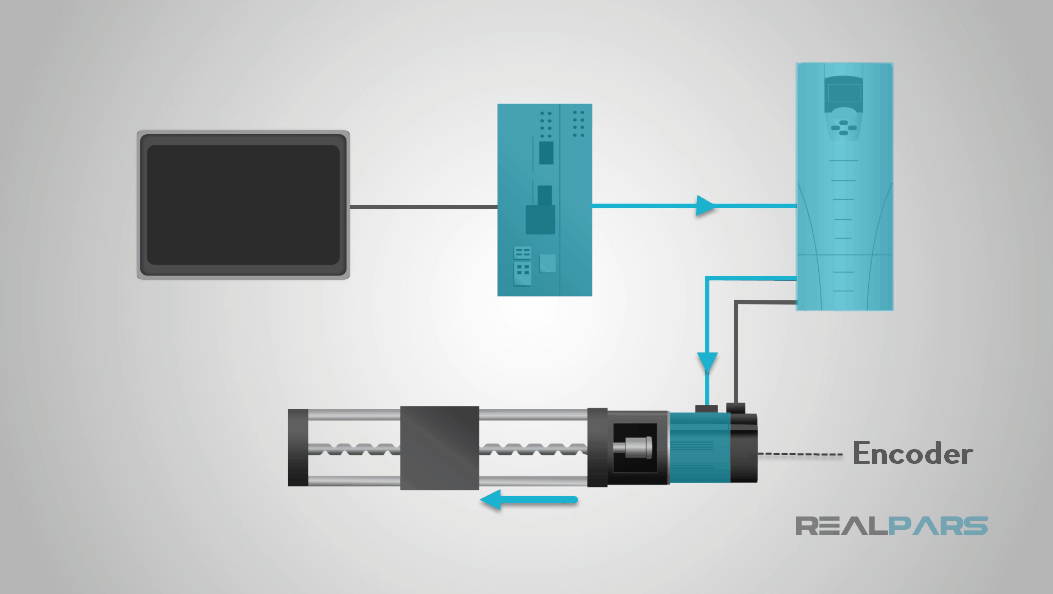
One of the main differences between Servo Motors and stepper motors is that Servo Motors, utilize a control loop and this requires position feedback.
The Servo Motor control loop uses feedback from the motor to help the motor arrive at a desired position and velocity.
These control loops come in a variety of electro-mechanical types. The controller or PLC software will generally use a PID (Proportional, Integral, Derivative) control loop for Servo Motors to achieve accurate speed, acceleration, and distance.
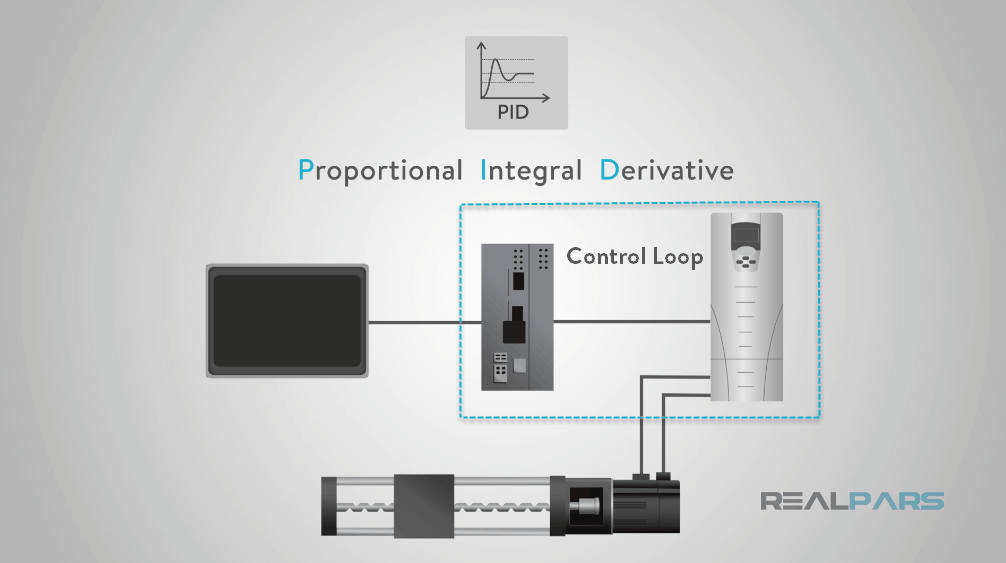
When using a control loop such as PID, you may need to tune the Servo Motor.
One of the disadvantages of a Servo Motor is tuning a motor can be a very difficult and a troublesome process, but the PID loop is also an advantage providing more control over the behavior of the motor.
Since Servo Motors have a control loop to monitor the current velocity and distance, they are for the most part more reliable than stepper motors.
For example, when a stepper motor loses a step for whatever reason, there is no control loop to compensate for the error in movement.
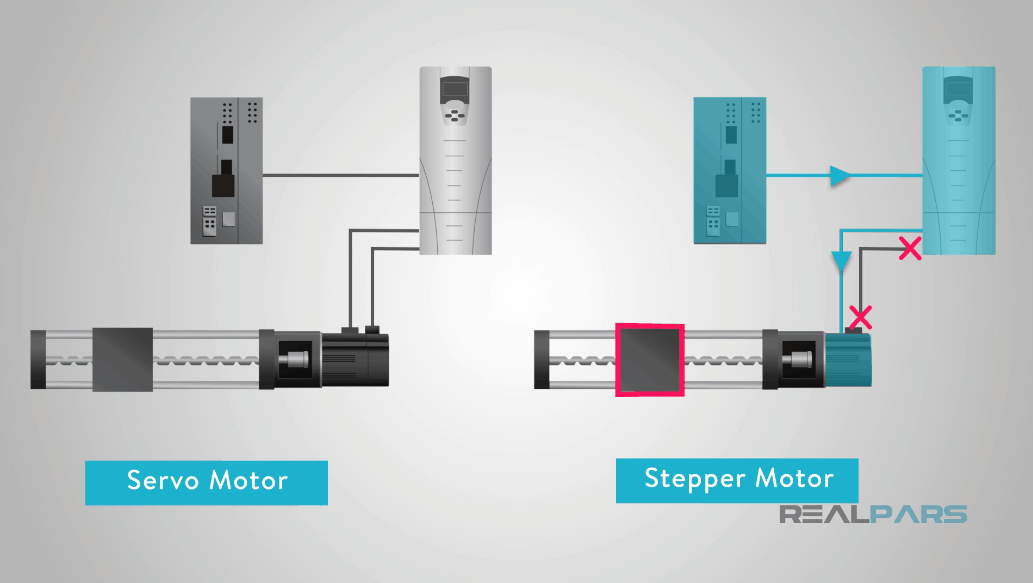
The control loop in a Servo Motor are constantly monitoring the critical control attributes of the path and will make the necessary adjustments when movement is in error.
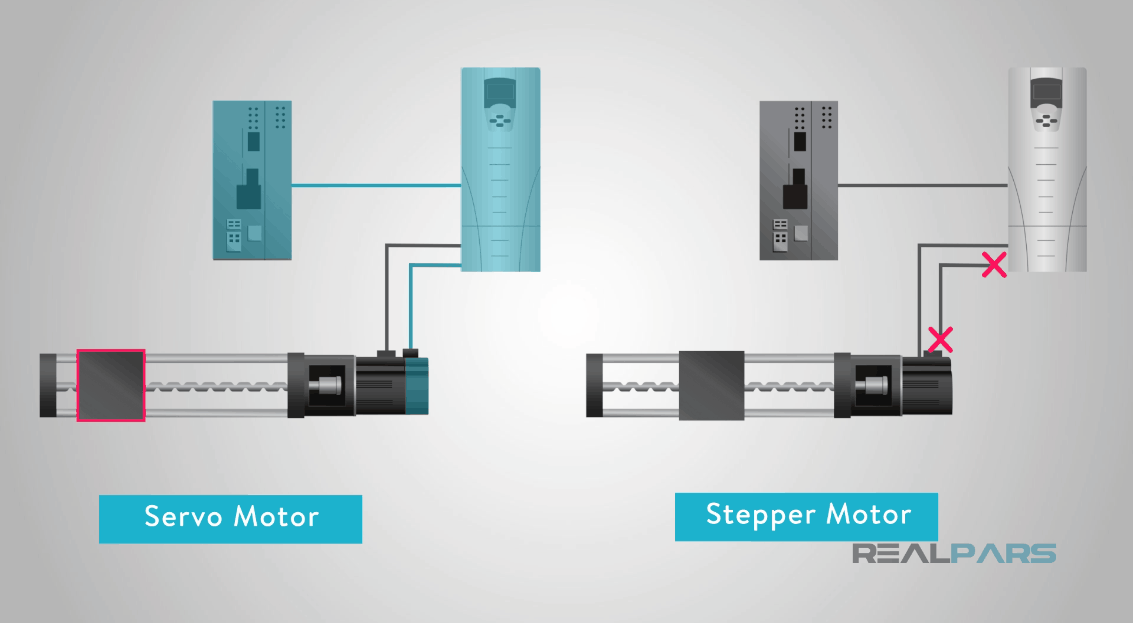
Like stepper motors, Servo Motors are available as conventional rotary motors and linear Servo Motors and have several advantages that are leading a growing numbers of machine builders to favor Servo Motors to boost overall performance.
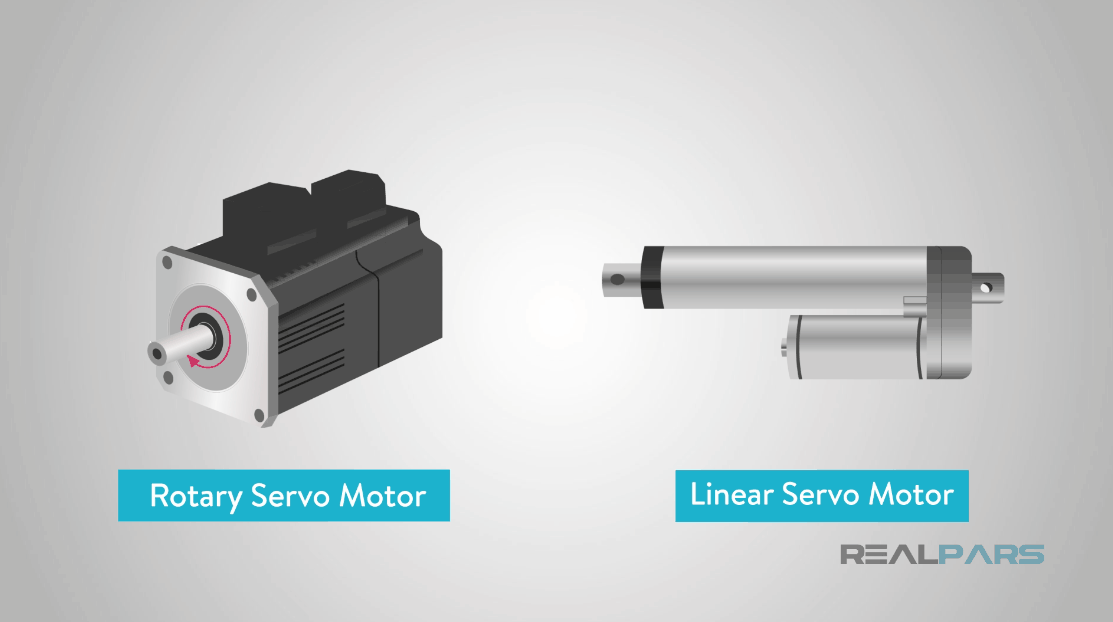
In general, Servo Motors run more smoothly than a stepper motor except when micro stepping are used.
A Servo Motor will typically provide 2-3 times the speed of a typical stepper motor as the Servo Motor speed increases, the torque (the twisting force that tends to cause rotation) of the Servo Motor remains constant, thus performing better than a stepper motor at higher speeds usually above 1000 RPM.
It is important to note that the continuous speed rating of the Servo Motor exceeds that of the comparable stepper motor.
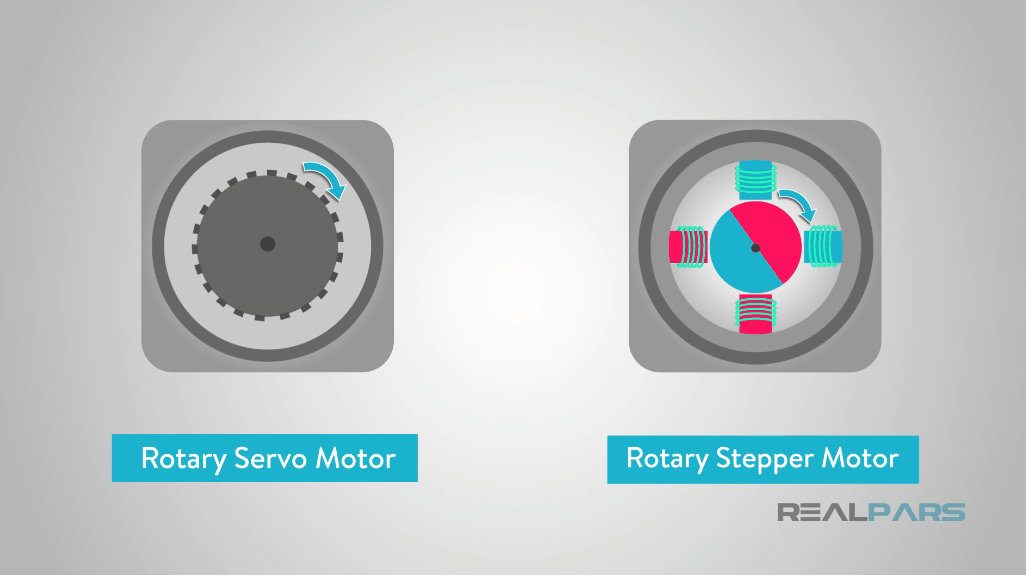
When we compare the performance of the stepper motor to that of the Servo Motor performance, the observer would notice a slight torque advantage in favor of the stepper motor at low RPMs, less than 1000.
However, once the RMPs cross over this 1000 RPM limit, the torque performance of the stepper motor decreases drastically, and speed-torque performance of the Servo Motor has the advantage.
The Servo Motor can only operate in this peak torque range for a short interval and must allow generated heat to be dissipated, but the Servo Motor operating in this range of operation is a Servo Motor Advantage.
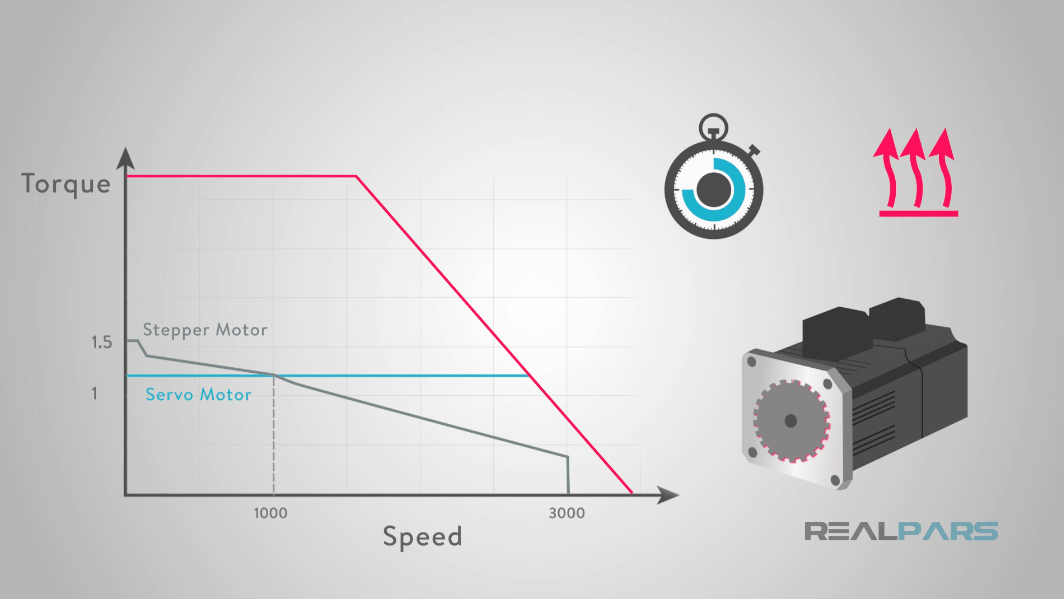
This prominent torque advantage of Servo Motors running at high speeds, can easily achieve speeds of 3,000 RPM and it is not uncommon for some Servo Motors to achieve speeds of 5,000, 6,000 and even 8,000 RPM while sustaining usable torque.
Servo Motors have an advantage with inherent sophisticated control algorithms, providing some control features that are simply not available in most stepper motor controllers.
With the advantages of torque control many applications accomplish all the required pressing, holding, pushing and twisting motions at very precise torques.
If the torque applied is too high, crushing of the widget and similar damage can result.
If the torque is too low, not enough holding force is created and the end result could be slippage resulting in defects or wasted product.
Many servo drives provide torque parameters to allow one to quickly and easily control the needed torque for a particular application.
Accuracy is a Servo Motor advantage. There is always a chance that the stepper motor may experience a misstep or stall that could go undetected.
In these situations, there is no indication from the stepper motor and by the time the error is noticed much time may have passed with undesirable results.
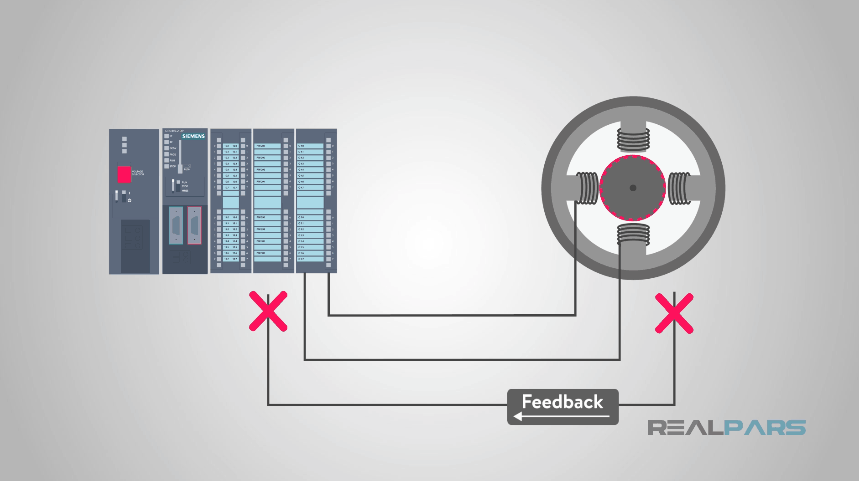
Servo Motors utilize position and speed feedback devices that may encompass the use of encoders to sense positional error in a system and provide path correction for this error to achieve the desired performance of the machine.
And so, with a Servo Motor, the inherent use of an encoder does not allow for position errors to go undetected.
A servo drive continuously reads in current position data and compares this feedback with the commanded position and calculates the error, then provides an updated command to the Servo Motor proportional to the degree of the error.
Therefore, a Servo Motor will continuously try to correct for any errors and will drive the motor as necessary to move the load to the desired position. This error correction is accomplished for Servo Motor torque, velocity, and/or position.
In addition, Servo drives have the added advantage of including a position fault error limit.
If the position error feedback by the encoder exceeds a limit, the Servo Motor controller will fault the motor, thereby preventing any erratic movement that could lead to potential damage to equipment, product or people.
And, the positioning error fault limit can be adjustable allowing for tighter, and better-defined control.
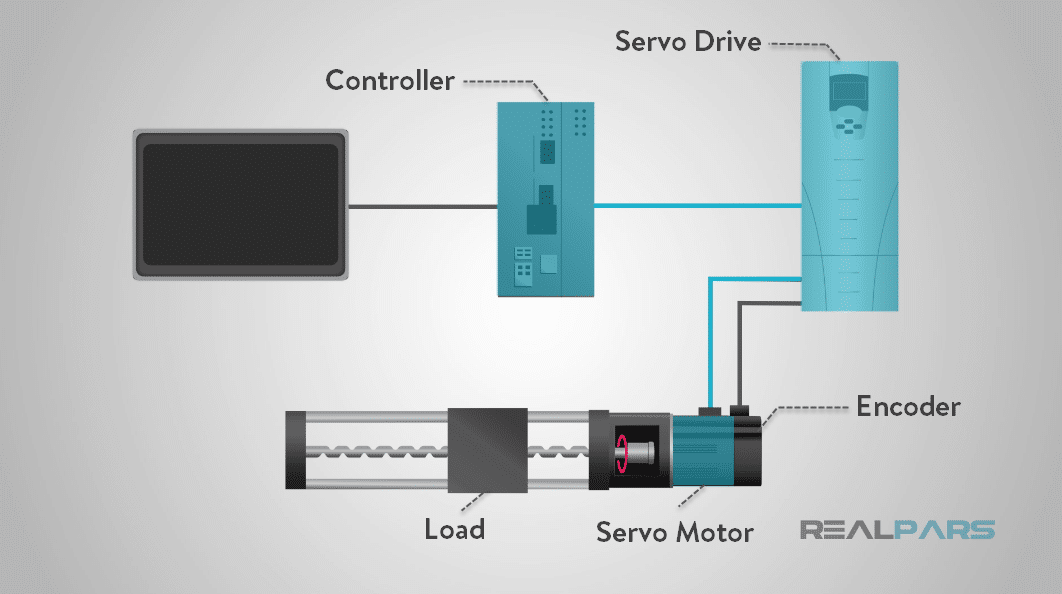
Properly tuned Servo Motors are extremely quiet. The biggest source of noise in servo-driven applications are often the drive train or bearing.
In comparison, stepper motors will typically emit around 68 dB during operation.
In the past, the desire to reduce costs has often dictated the use of lower-cost technologies such as stepper motors.
However, with growing pressures on machine and equipment designers to maximize the efficiency of machines, and now with the availability of lower-cost Servo Motors and positional feedback devices, are giving more thought to the advantages offered by Servo Motor technologies.
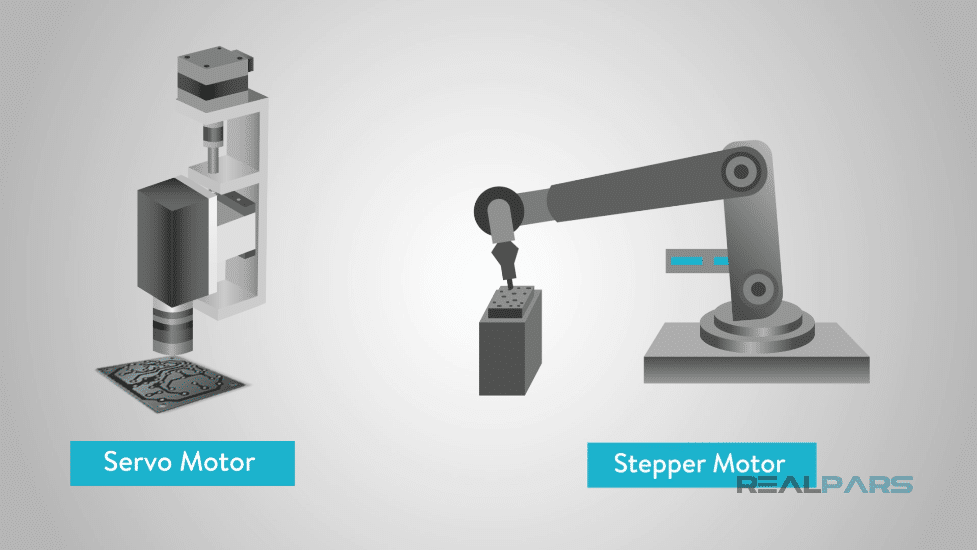
When purchasing Servo Motors (or stepper motors) standard designs help with competing and will offer the OEM (Original Equipment Manufacturer) and end-user an advantage in competitiveness and serviceability.
NEMA (an acronym for the National Electrical Manufacturers Association) and IEC (an acronym for the International Electro Technical Commission) include member companies that manufacture products used in the generation, transmission, distribution, control and end-use of electricity.
The goal is to promote competitiveness of the international electrical product industry through the development of standards.
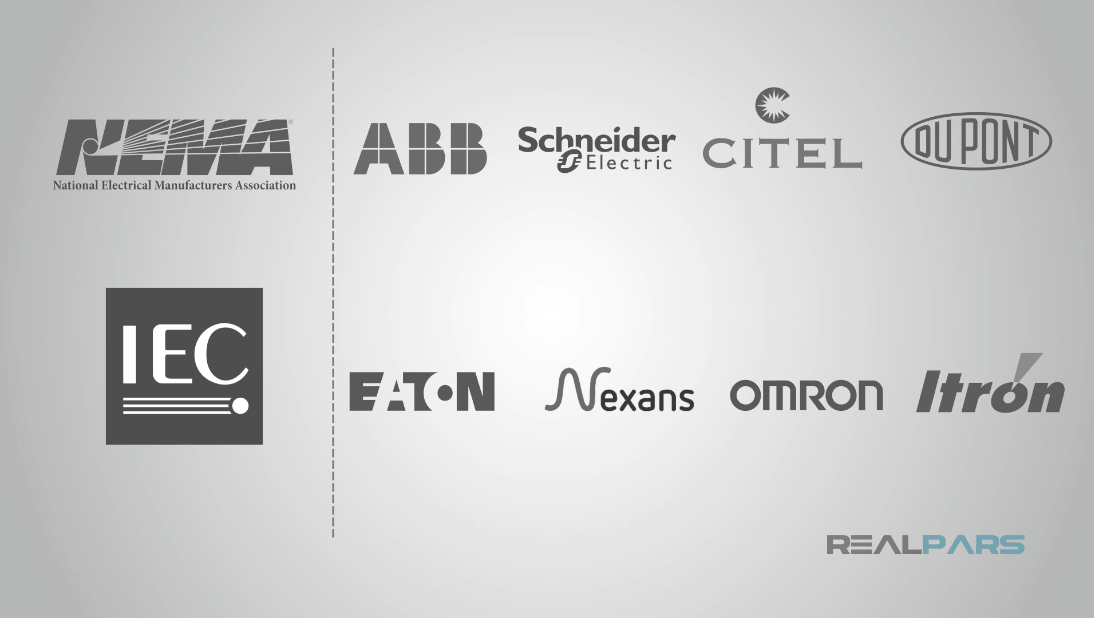
The advantage for using standard sized motors is so customers can reliably replace and ensure a compatible and dimensionally fit when a motor is sourced from one company and replaced by a motor of another company. You can easily visualize how standards will help to promote competitiveness in the electrical Servo Motor industry.
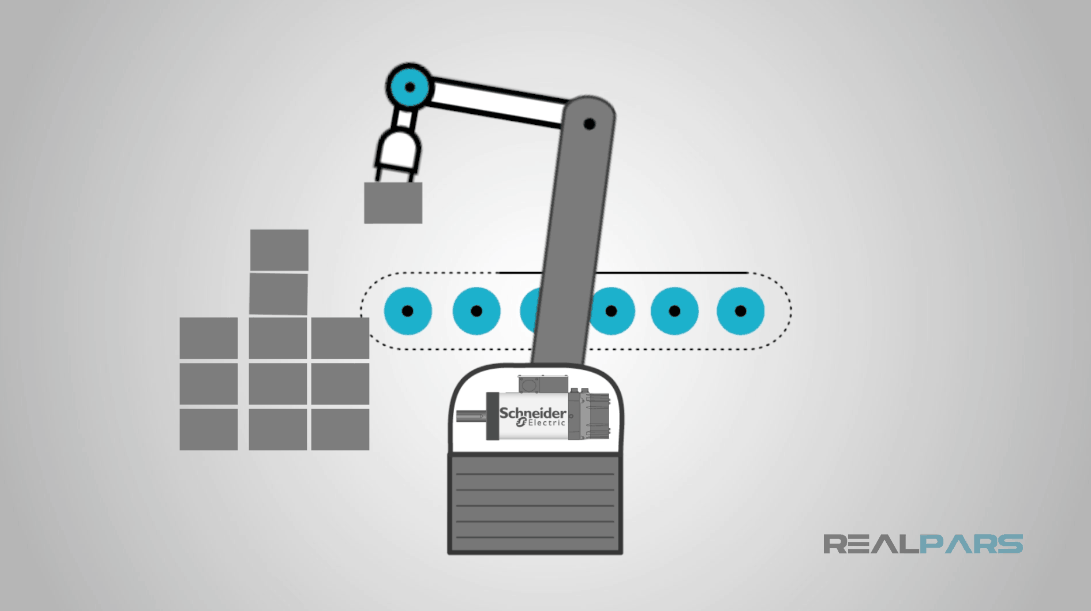
To be fair, there are some disadvantages that one should be aware of when determining and selecting the appropriate type of motion control solution. Let’s briefly review a few of these disadvantages.
A Servo Motor and drive solution is more expensive than a stepper motor solution because of the complex encoder feedback device found in the servo drive hardware and the algorithms required to drive the motor with the appropriate control signals.
The added performance capability found in Servo Motors comes at a premium price when compared to a properly sized stepper motor solution.
Another disadvantage is the complexity involved in configuring a Servo Motor solution. Servo Motors require tuning as mentioned earlier.
Tuning is a method by which the user optimizes the internal algorithms and electronics for physically controlling the torque, velocity and position of the motor.
The tuning process requires a continuous modification and adjustment of the servo drive output signals to the motor so the end result is achieved for the best smoothness, accuracy, and efficiency.
Servo Motor tuning is an arduous task that is often difficult and time consuming and becomes an art in performing the perfection required to obtain the accuracy required. Research indicates that tuning a servo drive can take anywhere up to 6 hours or more to complete.
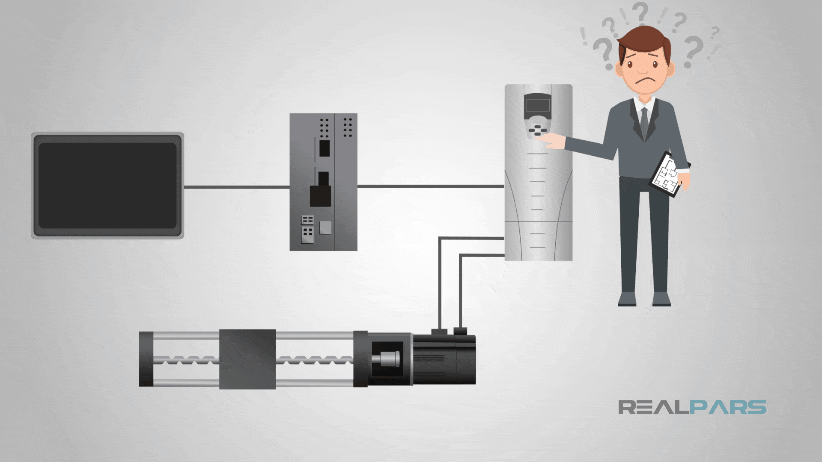
While many Servo Motor manufacturers and providers continue to improve upon the tools available for performing the tuning task, it is always recommended to select a Servo Motor drive combination that offers tools to help minimize the work required to tune the servo.
An example could be selecting a matched Servo Motor with a controller that has been designed to function together.
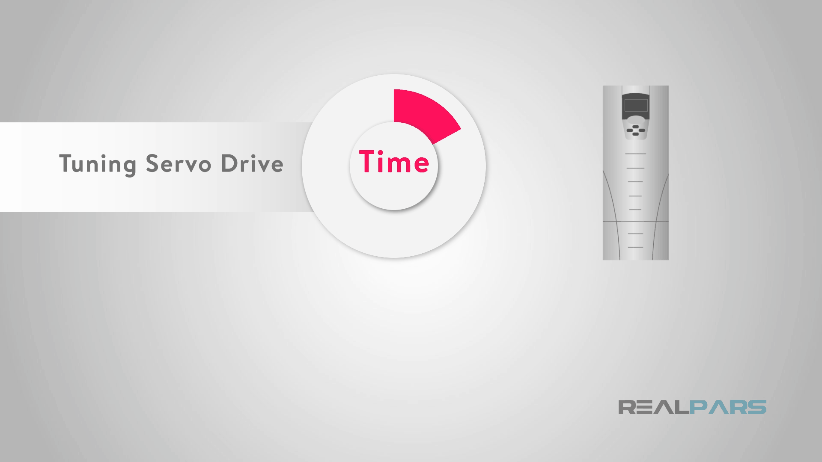
Now let’s summarize the top Servo Motor Advantages and Disadvantages.
Top Servo Motor advantages are:
- High output power relative to motor size and weight.
- Encoder determines accuracy and resolution.
- High efficiency. It can approach 90% at light loads.
- High torque to inertia ratio. Servo Motors can rapidly accelerate loads.
- Has 2-3 times more continuous power for short periods.
- Has 5-10 times more rated torque for short periods.
- Servo motors achieve high speed at high torque values.
- Quiet at high speeds.
- Encoder utilization provides higher accuracy and resolution with closed-loop control.
The top Servo Motor disadvantages are:
- Servos Motors requires tuning to stabilize the feedback loop.
- Servo Motor will become unpredictable when something breaks. So, safety circuits are required.
- Complex controller requires encoder and electronic support.
- Peak torque is limited to a 1% duty cycle. Servo Motors can be damaged by sustained overload.
- Gear boxes are often required to deliver power at higher speeds.
- Higher overall system cost and the installation cost of a Servo Motor system may be higher than that of a stepper motor due to the requirement for feedback components.
This concludes the video, Servo Motor Advantages and Disadvantages. I hope you have learned what’s required to move forward in creating your own motion control project.
This blog post about the applications of Servo Motors is one of a series of videos on motor | motion control, so please check back with us soon for more motion control topics.
We at RealPars hope that you found it interesting, and that you will come back for more of our educational blogs. share your thoughts and ideas directly in the comments.
Thank you 😉
The RealPars Team