In this article, we are going to take a good look at the purpose of Siemens SIMATIC Technology and Drives Control, or SIMATIC TDC for short, what makes it special, and how it stands out from a standard system.
We’re going to throw in a couple of examples of where they’re used, so you can understand the typical environments they are used in.
Overview
So we’ll start off with an overview of what you can expect from the SIMATIC TDC.
The SIMATIC TDC control system is a multiprocessor system, meaning that multiple processors can be housed in the rack.
They are designed to provide maximum performance, and as such, can process commands lightning fast.
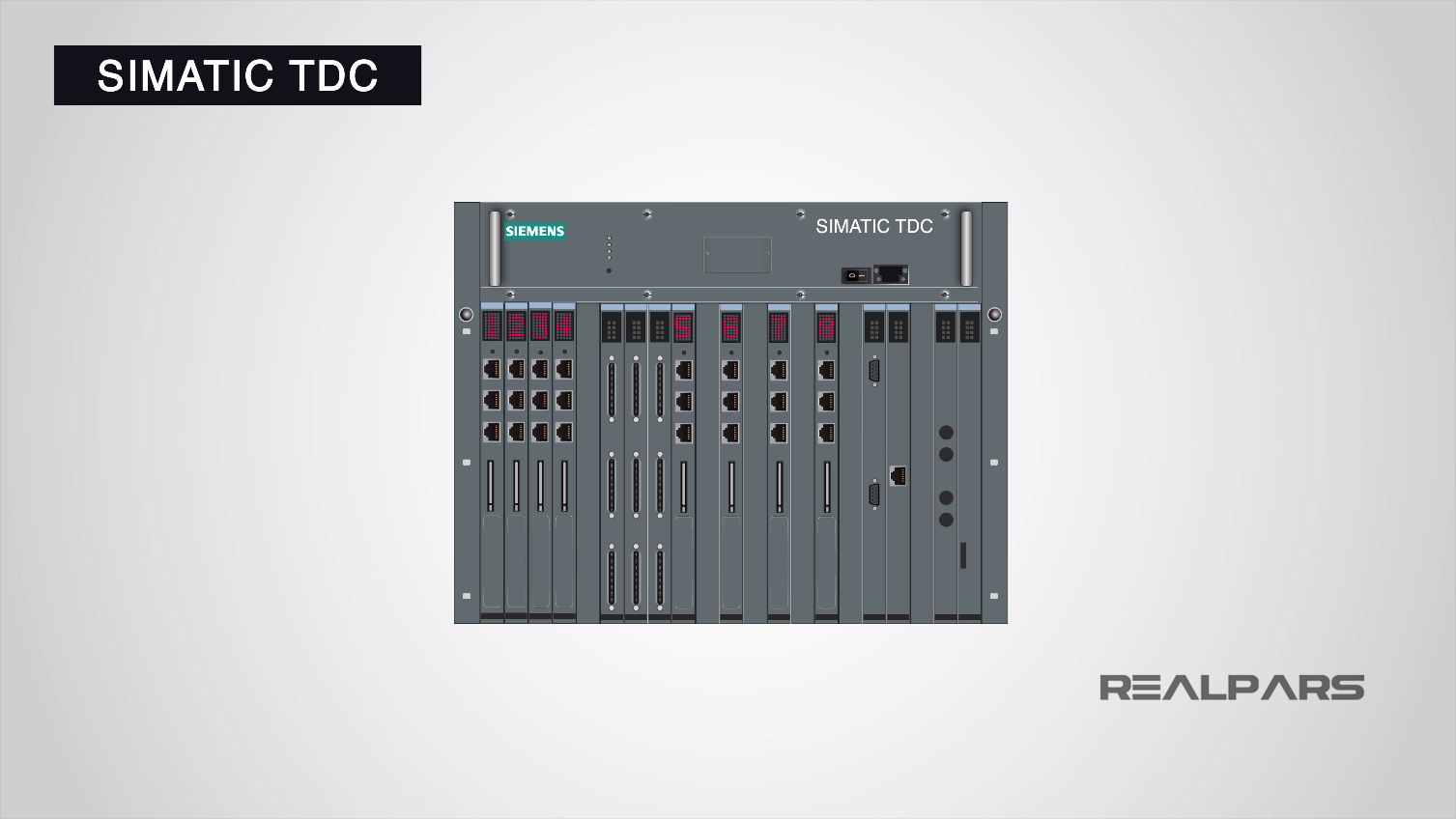
They are typically used for closed-loop control of drives to determine things like:
– Torque
– Position
– Angle
– Speed
If complex relationships exist between a number of drives, they are also extremely useful for this.
They can be used for calculating any number of process or plant variables such as temperature and pressure.
But those are functions of any PLC system. What makes SIMATIC TDC so special?
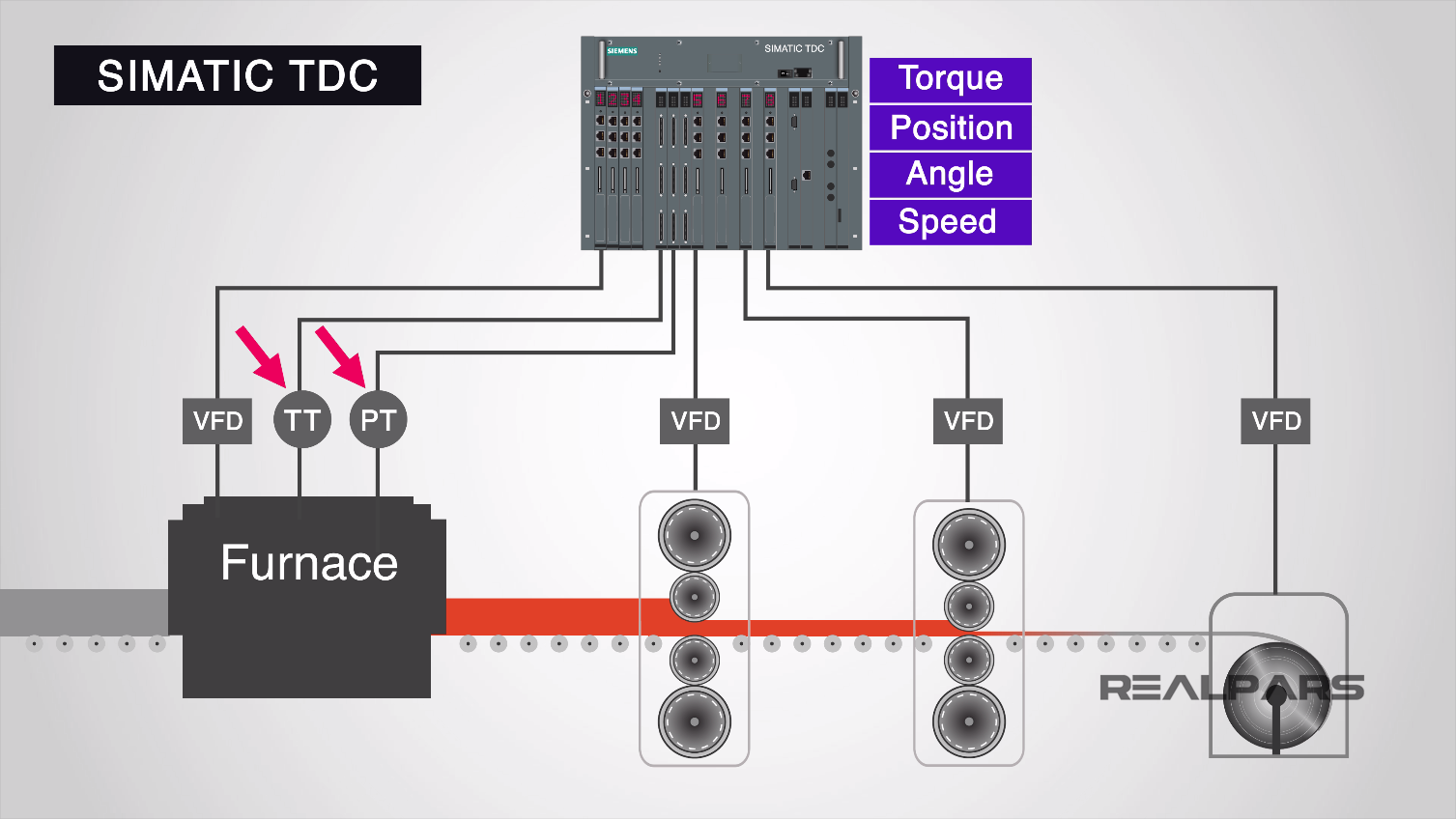
What Makes SIMATIC TDC So Special?
Well to try and understand why we use a SIMATIC Technology and Drives Control system over any other PLC based system, it’s best to look at the type of work that the SIMATIC TDC is known for.
This should help you understand why the demands put on the SIMATIC TDC are far greater than a standard control system, why this specialized hardware is used, and what it is truly capable of.
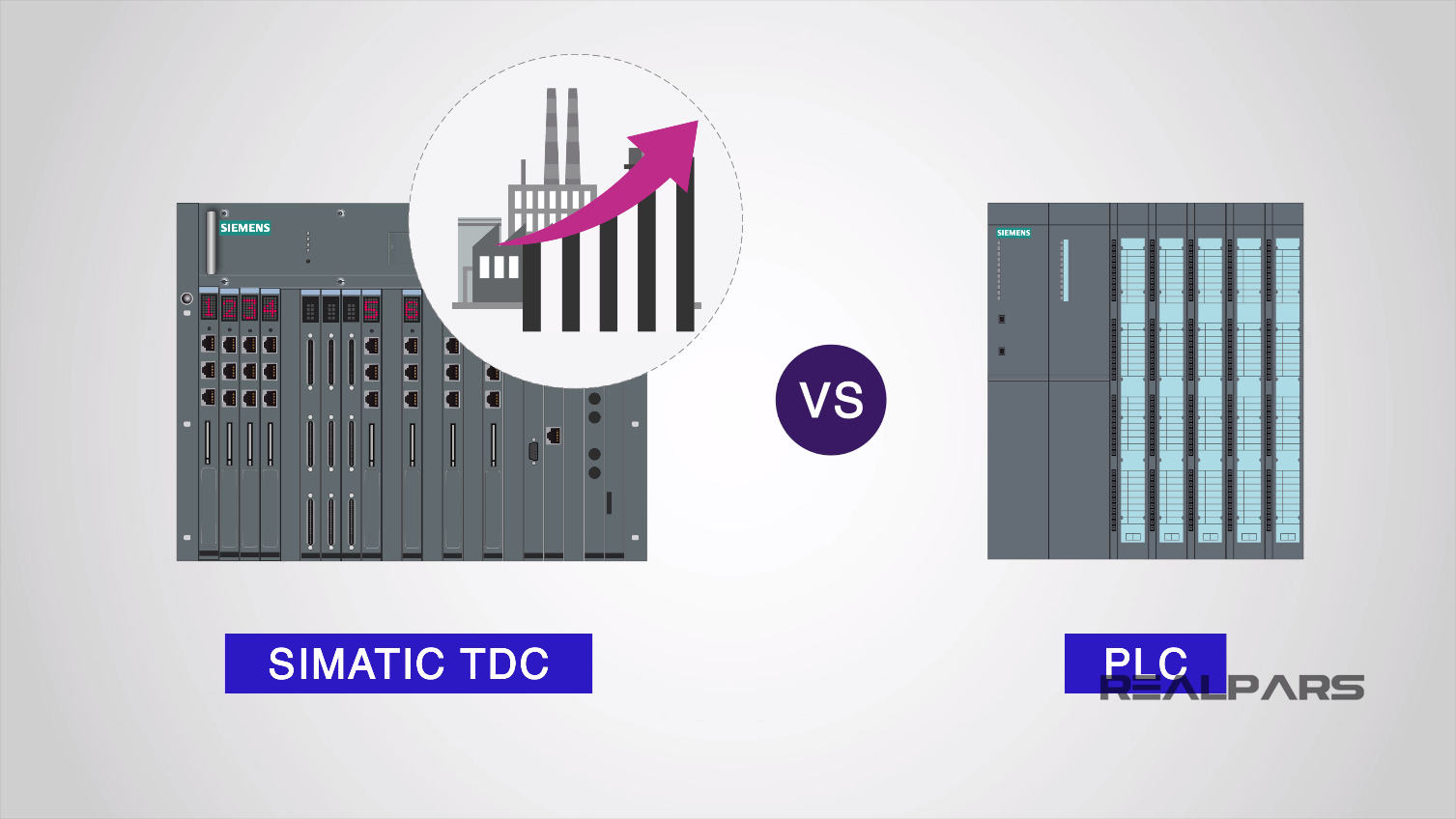
SIMATIC TDC is commonly used in large plant engineering environments, for example in a Steel Rolling Mill.
The complex nature of a Rolling Mill and the many stages the steel passes through to get to be the end product makes the SIMATIC TDC extremely useful.
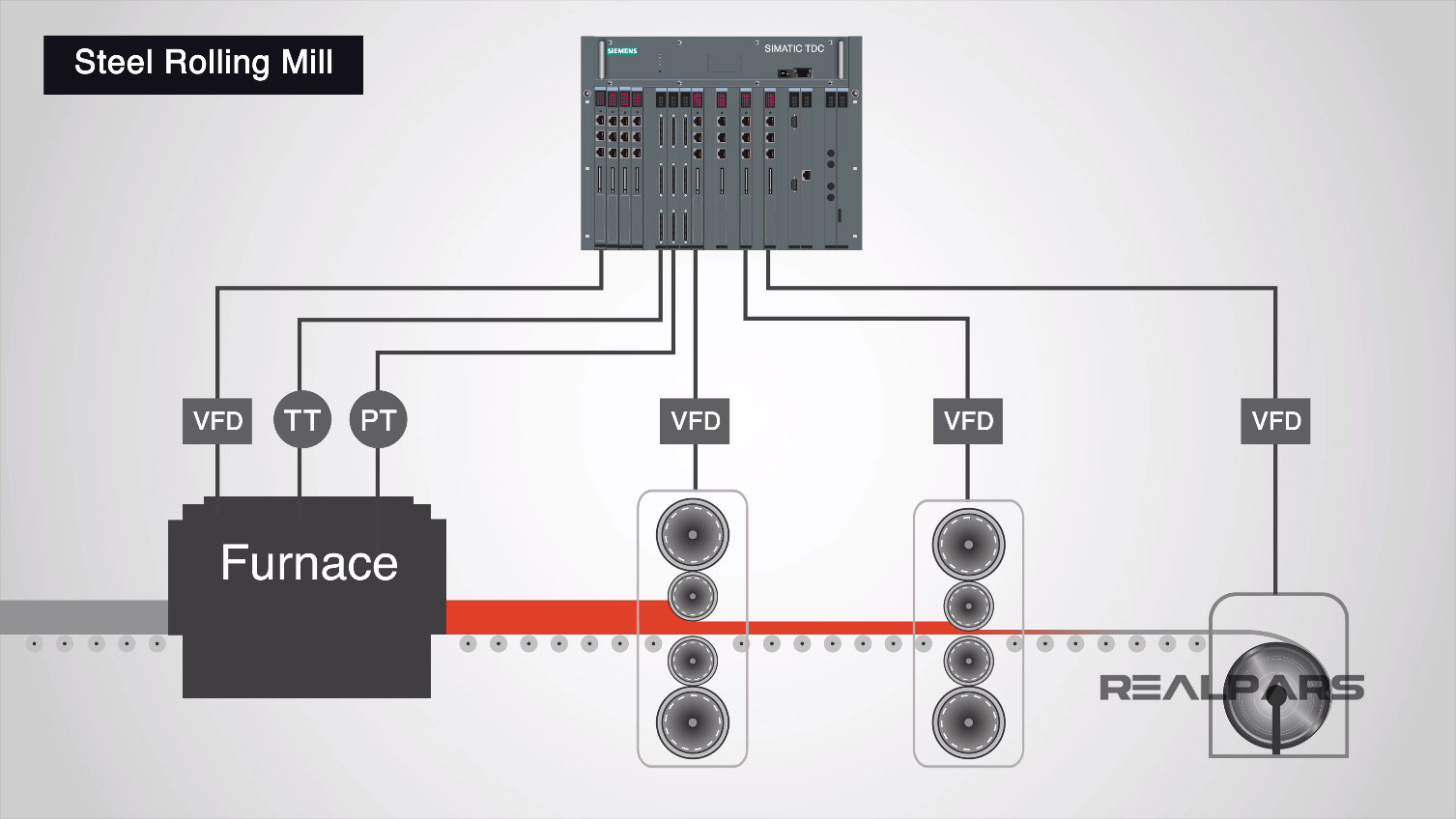
This is because each part of the process would have it’s own PLC controller in the SIMATIC TDC rack.
With the PLCs all being in the same rack, this means that there are no breaks in the chain when passing from one station to the next.
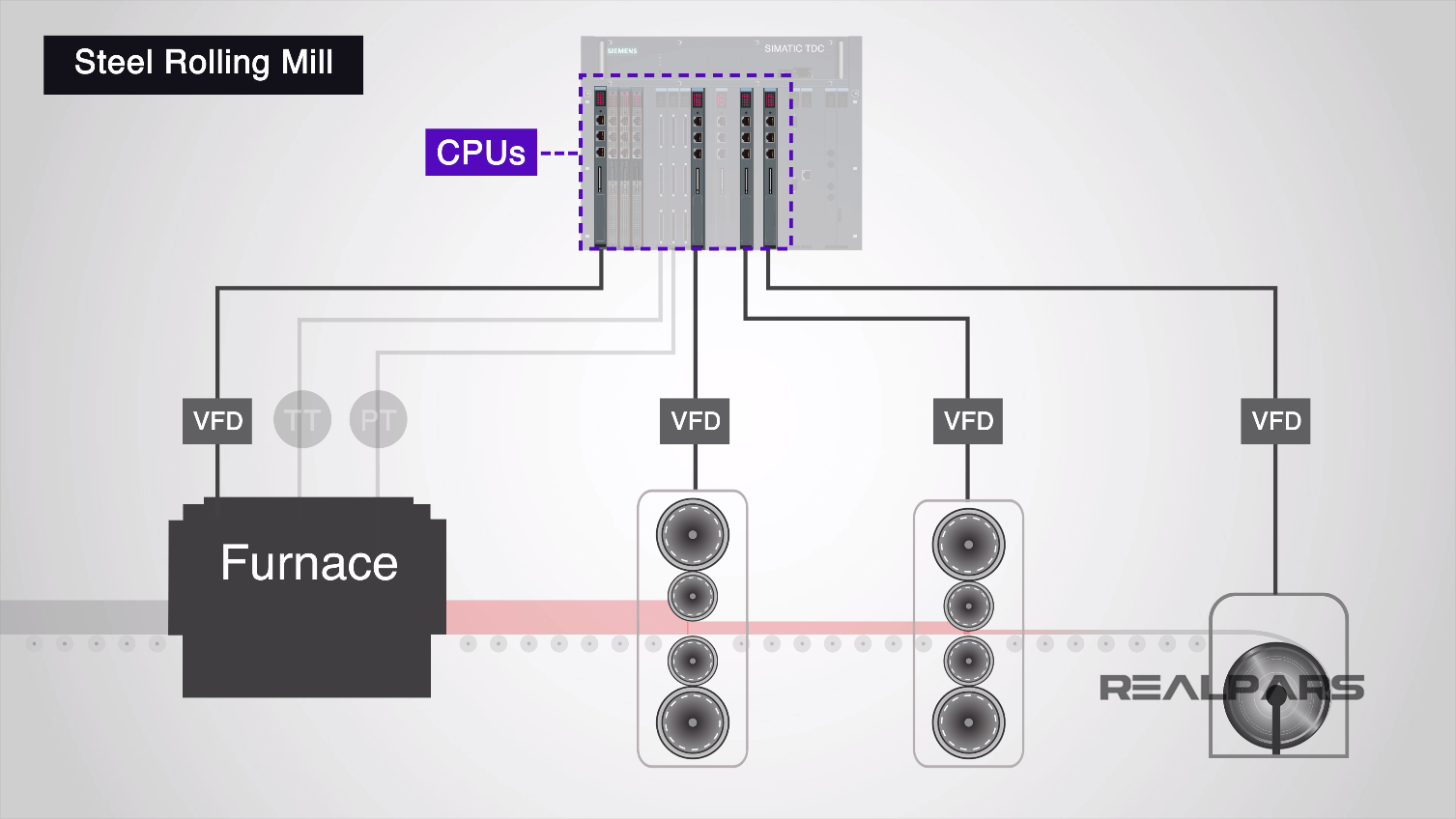
All of the modules are connected which allows data to be exchanged between all of the modules, almost in the same processor clock cycle.
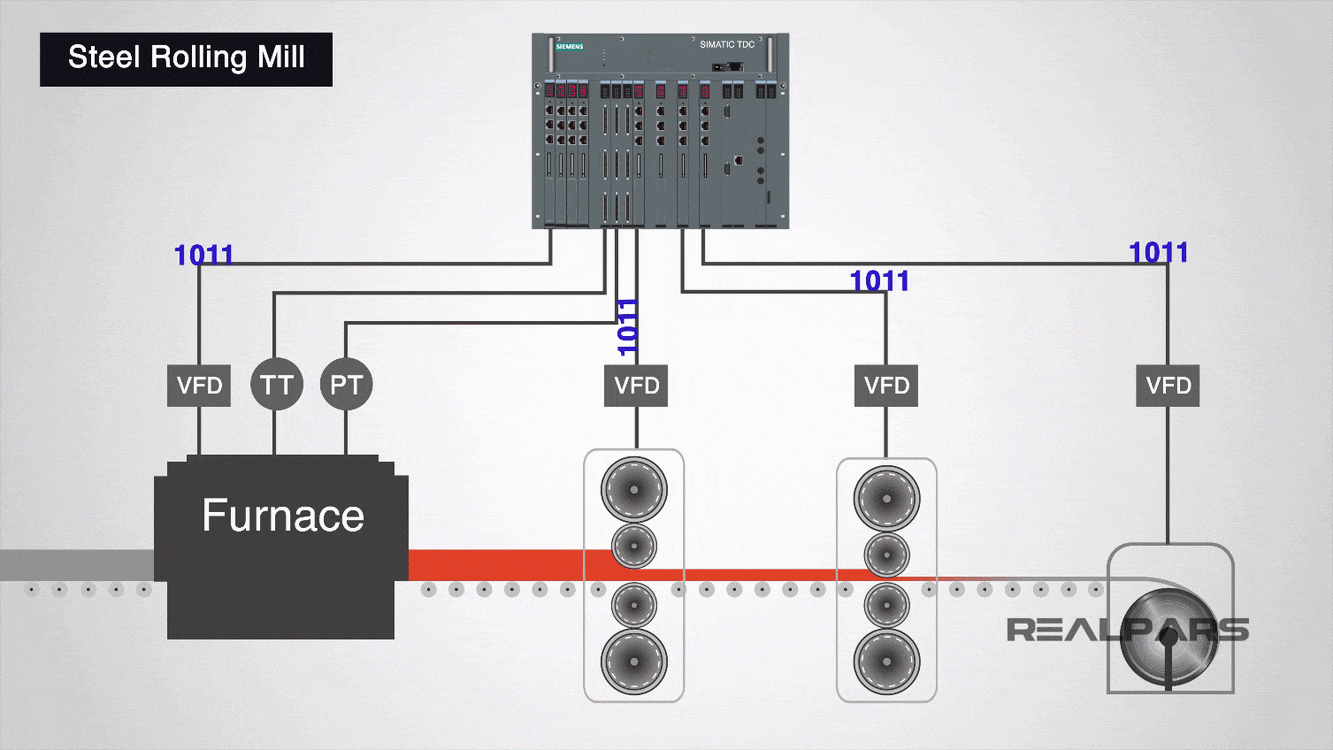
So, no slow PLC communications protocols are used, which would not only slow down the processor clock cycle, but also the transmission speeds would be much slower.
This enables the SIMATIC TDC to stand out when controlling roller drives connecting the parts of two systems.
Hot rolling uses large pieces of metal, such as slabs or steel billets, and heats them to a high temperature.
The metal pieces are then deformed between rollers creating thin cross-sections. This is followed by further rolling to turn the product into the plate, sheet, rod, bar, pipe and so on.
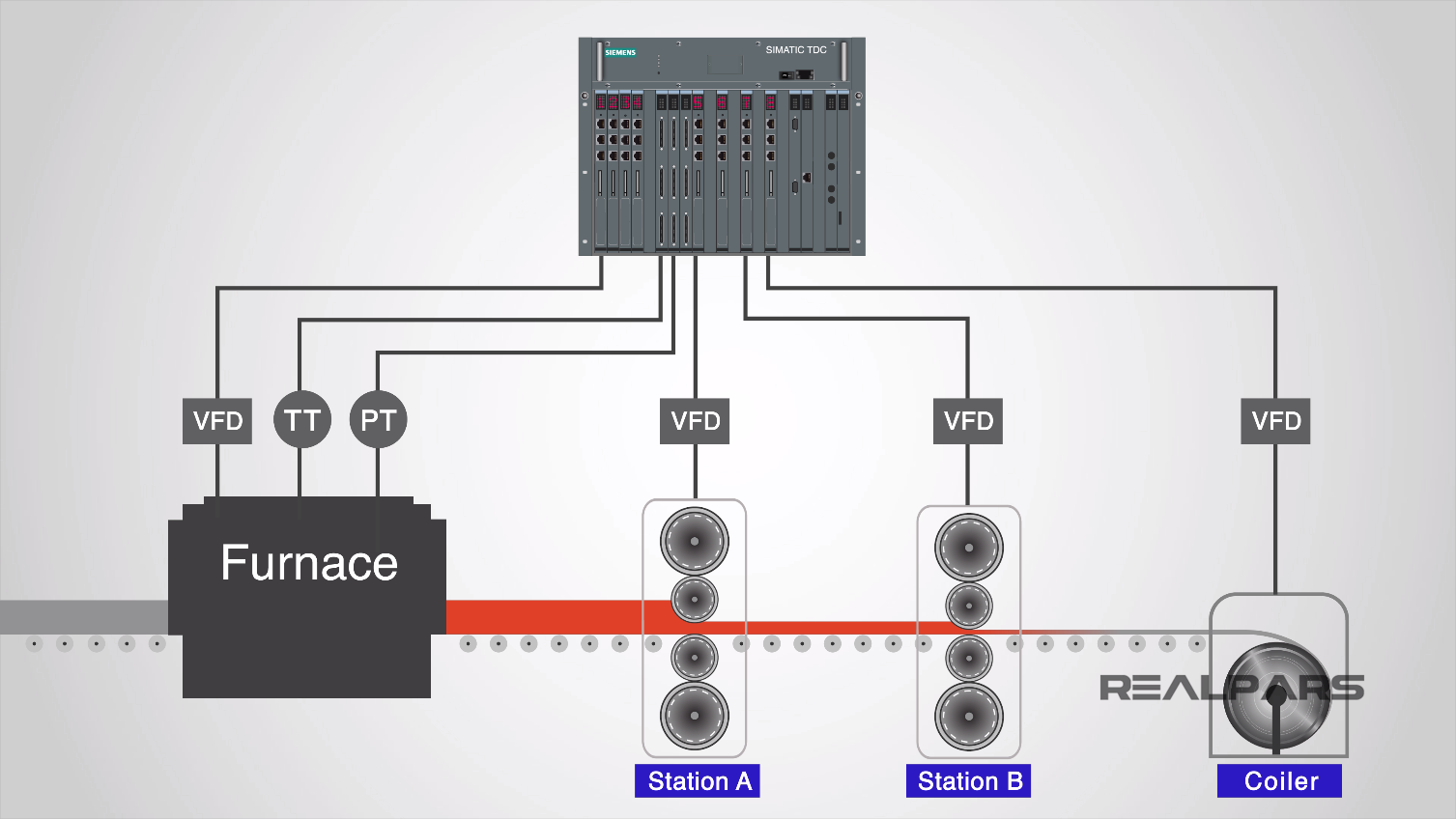
Let’s say that a large, extremely heavy, molten steel bar was on a transfer roller, moving from Station A to Station B.
As it is passing from Station A to Station B, the rollers on Station B begin to run.
The speed of the Rollers on Station B need to match the speed of the rollers on Station A, otherwise, large forces are put on the motors controlling the rollers.
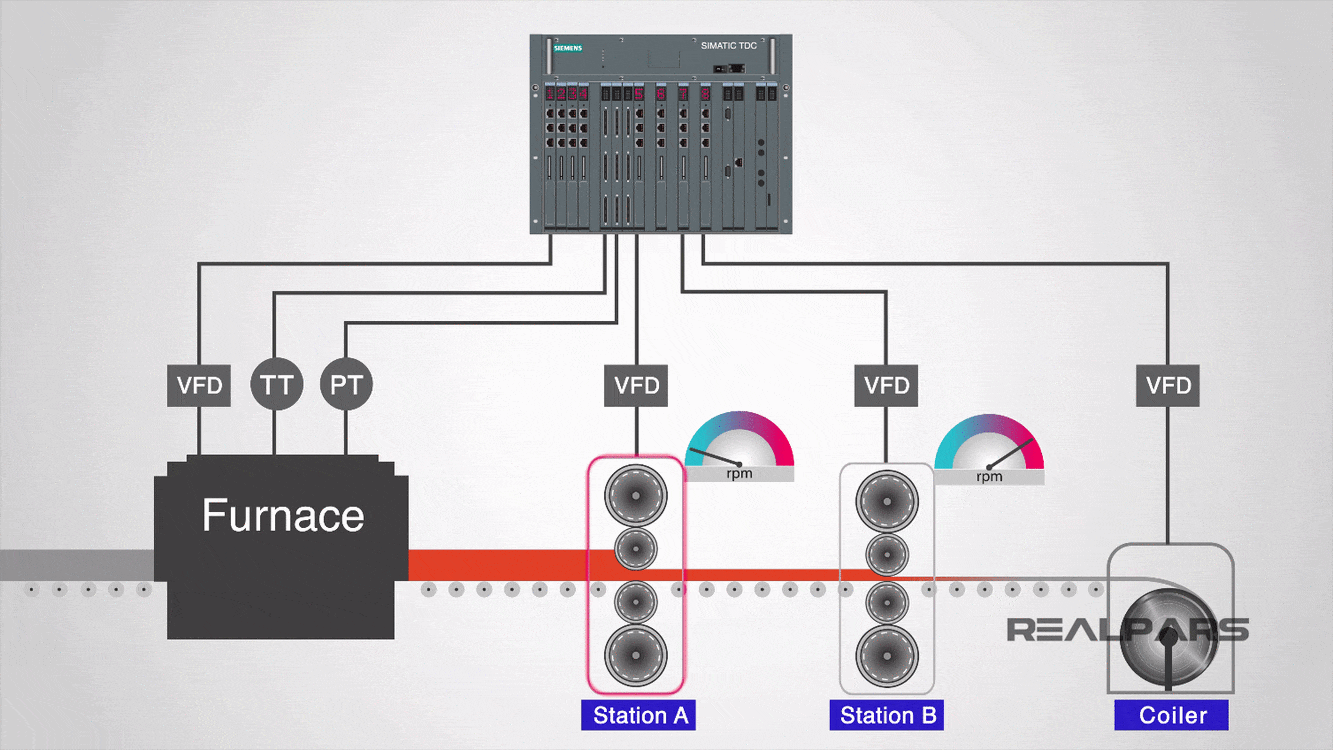
Because the controllers are connected via the backplane in the rack, there is no delay in getting the required speed, and any changes in speed are updated almost instantaneously, meaning the transfer is seamless.
Similarly, if Station A had to stop quickly, in an emergency situation, for example, the motors on Station B would also stop quickly, removing the potential to put excess stress on the motors on Station B.
The high precision nature of some processes requires the highest degree of performance, and that is what you get with Simatic Technology and Drives Control System. Powerful motion and closed-loop control are where it excels.
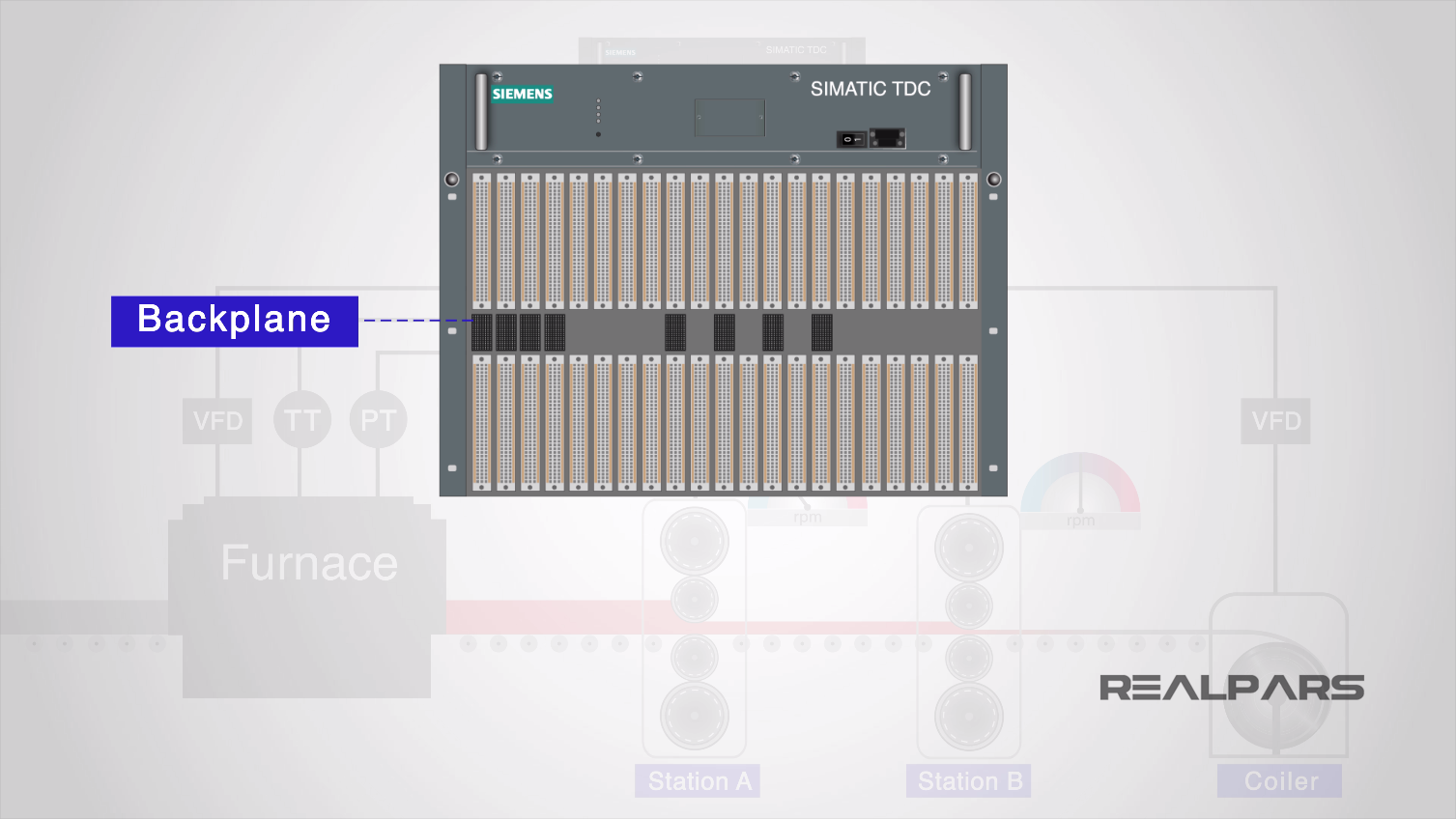
Summary
So what have we learned today? SIMATIC TDC is a high performance, high precision PLC system that allows multiple processors to be mounted in the same rack.
This means each PLC controller is connected by the backplane of the rack, which means that data can be transferred extremely quickly between controllers controlling different parts of the plant.
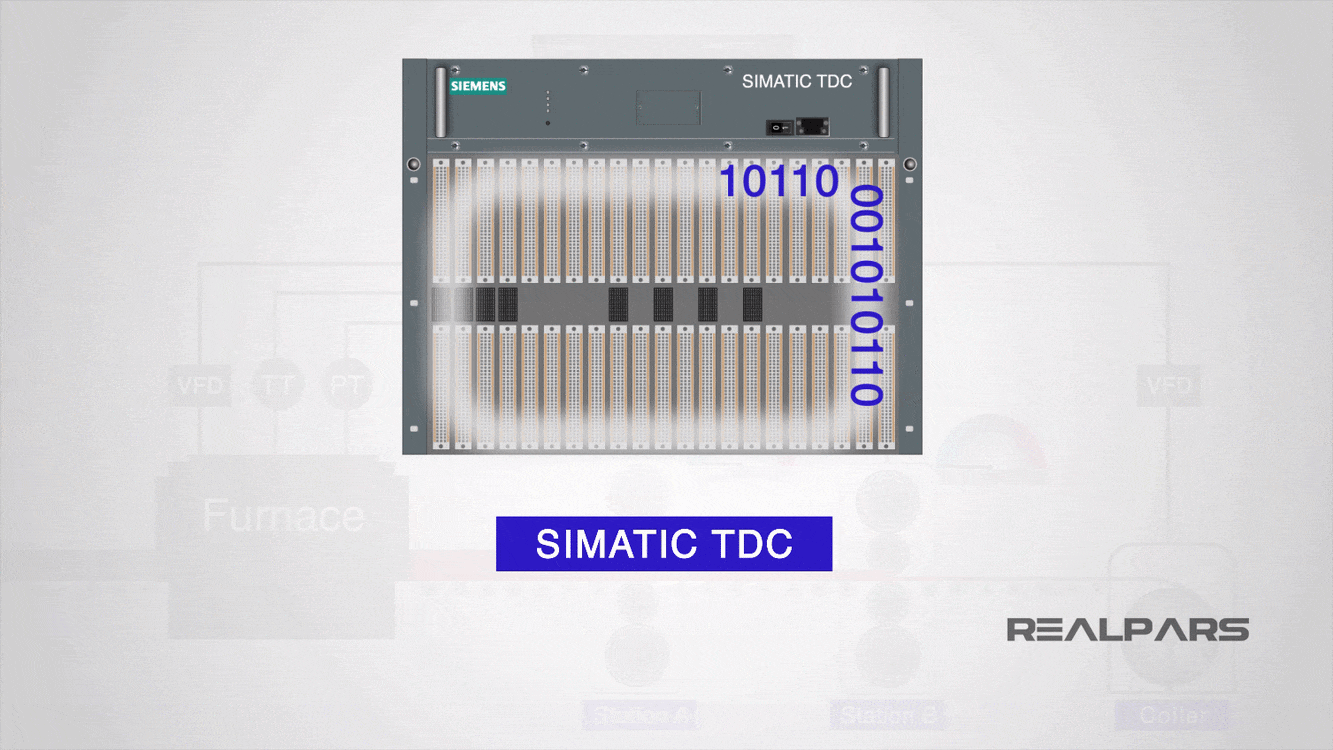
SIMATIC TDC systems are powerful motion and closed-loop control systems with a modular design making it extremely scalable to be able to handle small to very large applications.
Typically, SIMATIC TDC systems are used in large scale plant environments, such as a steel Rolling Mill.
This is because of the complexity of rolling steel means that it passes through a number of stations before reaching the end product.
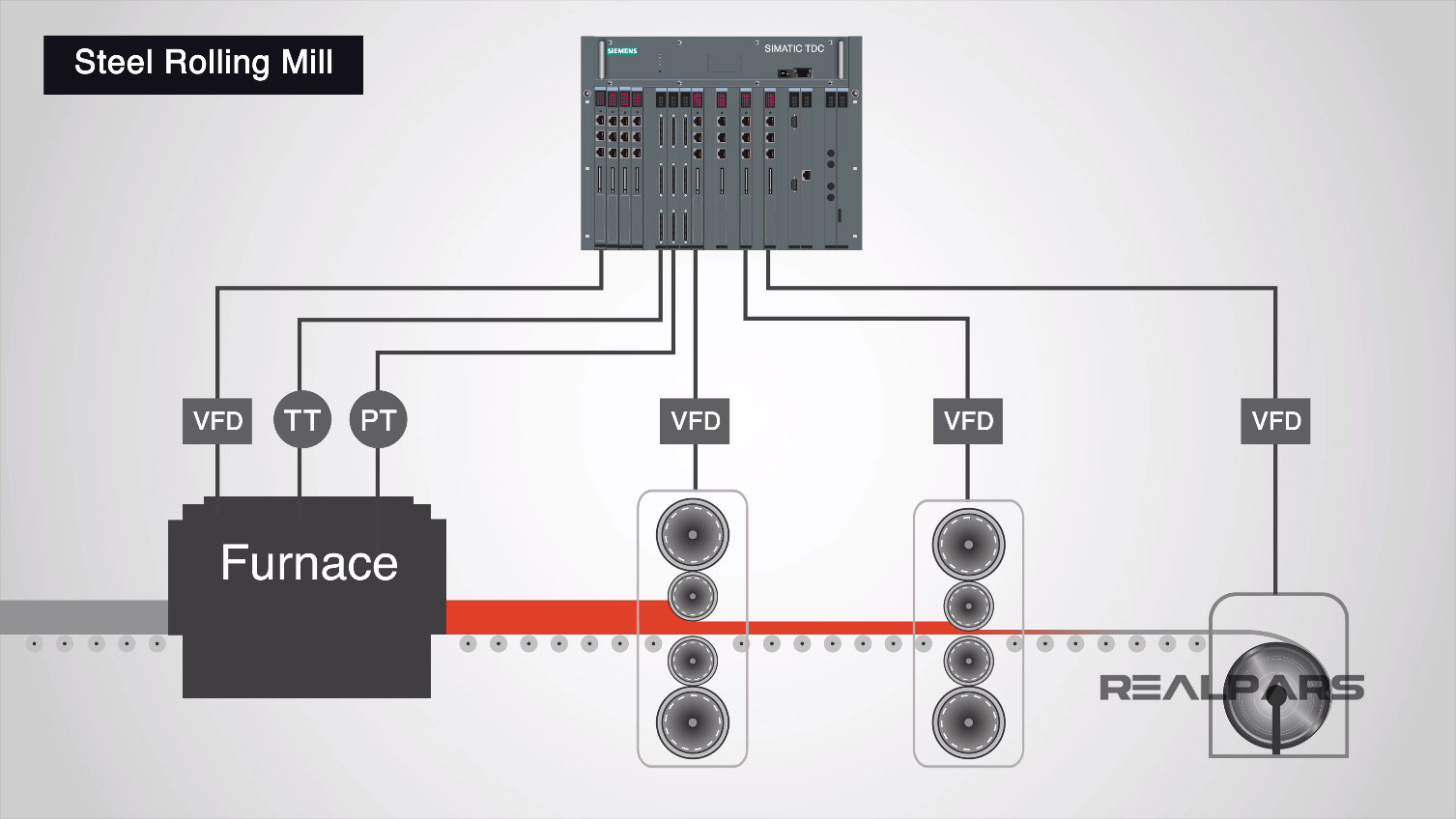
That’s it for this article! I hope you enjoyed learning about Siemens SIMATIC Technology and Drives Control.
They are an extremely versatile piece of equipment that are particularly useful when they are used in a large facility with processes that rely on each other to produce the end product.
Got a friend, client, or colleague who could use some of this information? Please share this article.
The RealPars Team