PLC Troubleshooting 101: Basic Tips and Tricks
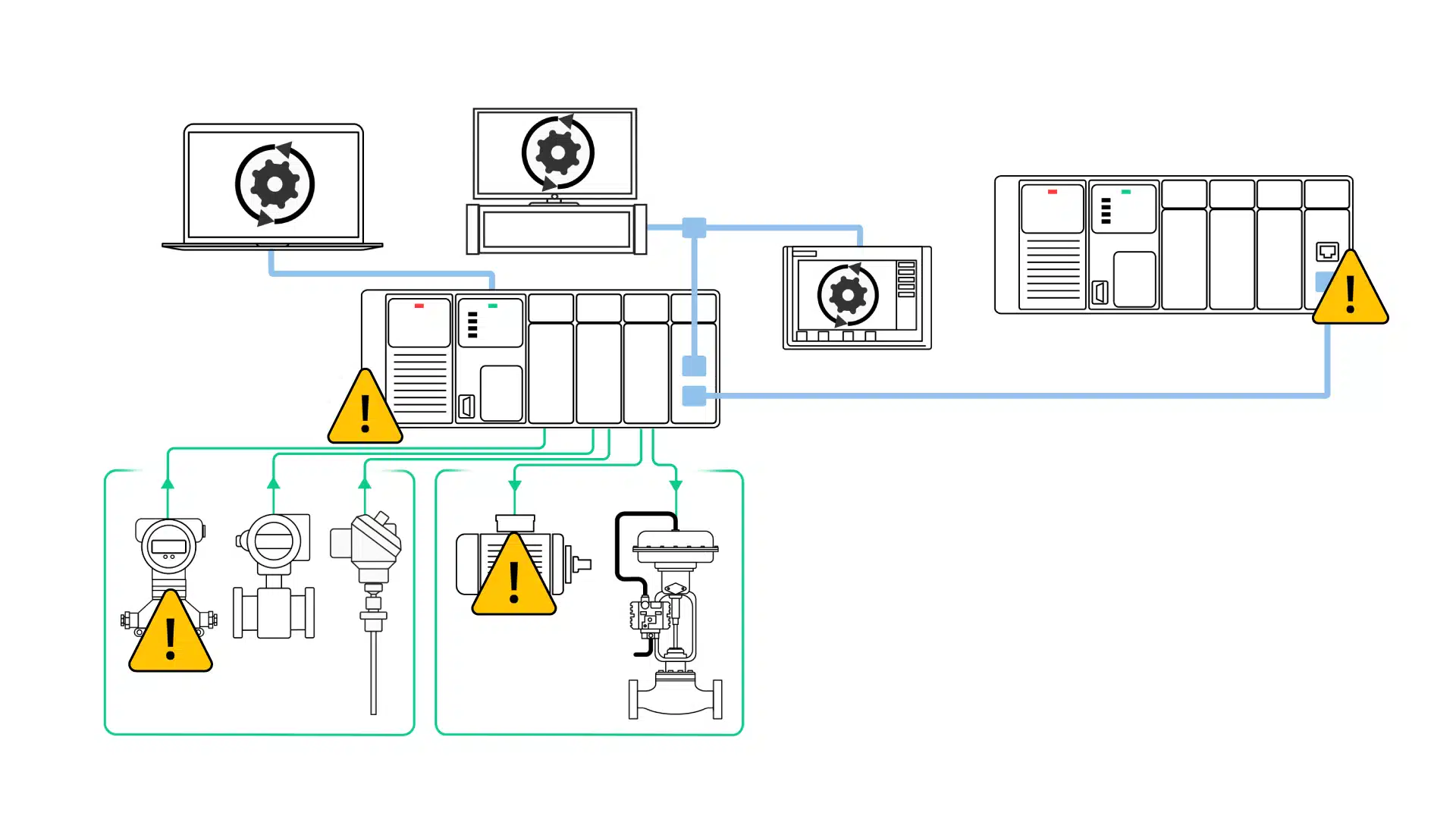
PLCs are essential components in modern control systems. Understanding the basic components of a PLC is crucial when it comes to troubleshooting and maintaining these systems.
In this article, we will review the fundamental components of a PLC and explore some basic and advanced troubleshooting techniques.
Understanding PLC Components
Let’s start by reviewing the basic components of a PLC that often need attention during troubleshooting.
The first component of a PLC is the processor or CPU. This is the brain of the PLC and is responsible for processing the logic and making output decisions based on the inputs received. The processor executes the code stored in memory and controls the operation of the I/O modules.
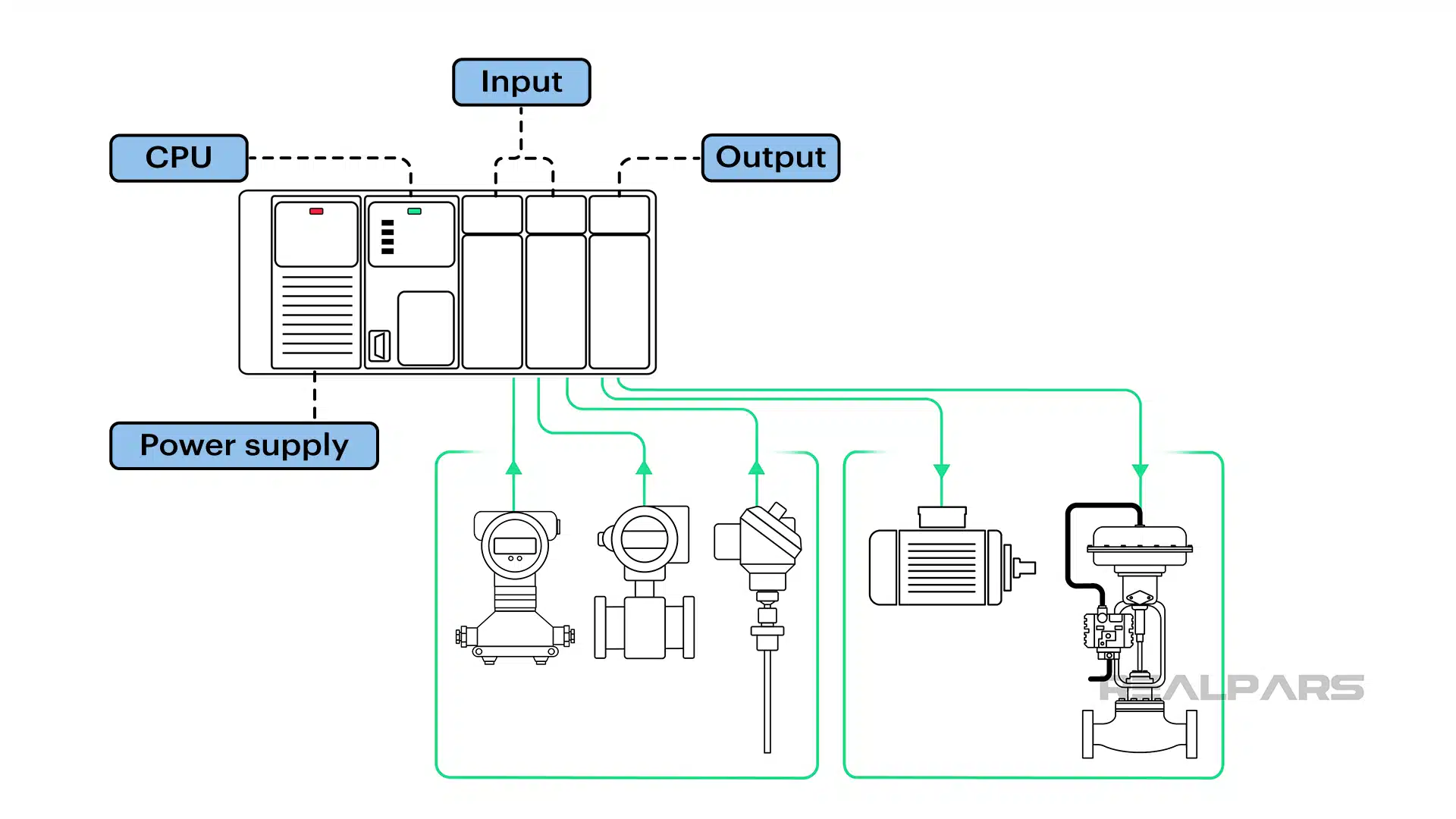
Next, we have the power supply, which provides the necessary voltage and current to power the PLC and its components. Without a stable and reliable power supply, the PLC would not function correctly and can experience errors, faults, or even complete failure.
I/O modules are responsible for communicating with the external devices in a control system.
Input modules receive digital or analog signals from sensors and convert them into a format that the processor can understand. Conversely, output modules receive digital or analog signals from the processor and convert them into signals that can control devices such as motors or valves.
Communication modules enable the PLC to communicate with other devices such as other PLCs, HMIs, SCADA systems, or other relevant devices.
These modules typically use protocols such as Ethernet/IP or Modbus to exchange data with other devices, but there are many communication protocols that exist.
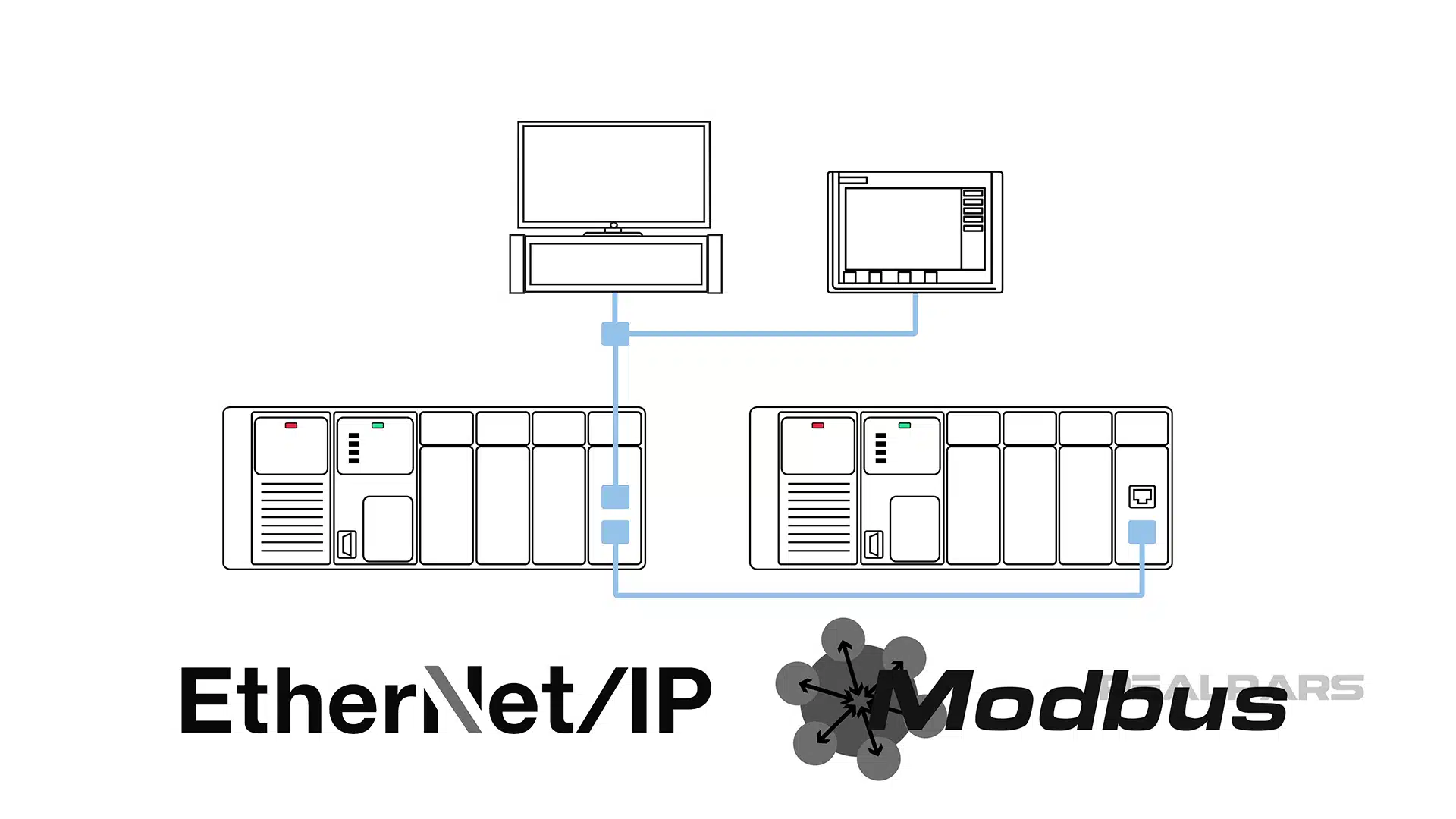
Basic Tips for PLC Troubleshooting
Now, let’s discuss several basic tips and steps to take during the troubleshooting process.
You’ll want to start by gathering as much information as possible, such as speaking with operators and engineers, reviewing data trends, and going out to witness the issue. Pinpoint the problem by identifying a specific system or component.
Troubleshoot by using trial and error methods and recording the outcome of each alteration. Once a solution is proposed, be cautious when implementing changes and consider adverse effects.
Verify and test the solution, then take careful notes and notify appropriate individuals to prevent future issues. It’s important to fully understand the problem and follow a structured approach to achieve successful troubleshooting.
Using Resources
During this process, it is crucial to use resources such as official vendor documentation, operation and maintenance manuals, and functional design specifications.
These resources can provide valuable insight into the system and may contain troubleshooting steps specific to your PLC or control system.
Don’t underestimate the power of the internet when troubleshooting your PLC. Online resources such as videos and forums can provide helpful tips and solutions from other professionals who have encountered similar issues.
PLC-related problem
It is common to experience issues with wiring in a control system. You’ll want to check for correct wiring throughout your PLC and control system.
This includes checking for any loose, disconnected, or damaged wires, as well as ensuring that everything is connected to the right input and output terminals.
You’ll also want to pay close attention to the main PLC components we touched on earlier.
Verify that your power supply is working properly, your I/O modules are wired correctly and that they have been configured properly in your programming software, and that all PLC communication is wired up right and configured correctly.
Finally, examine the program logic. This means looking at the ladder logic, function blocks, or structured text in your PLC program to see if there are any errors or issues.
This can be a bit more complicated, but it’s essential to identify any issues in the programming that may be causing problems.
Advanced PLC Troubleshooting Techniques
Let’s touch briefly on some more advanced PLC troubleshooting techniques.
First up, let’s talk about monitoring system behavior. This involves examining the system’s performance and identifying any unusual behavior. This can be done through a variety of tools such as trending, alarms, and event logs.
By carefully monitoring the system, you can detect patterns that can reveal issues to help you toward a solution during troubleshooting.
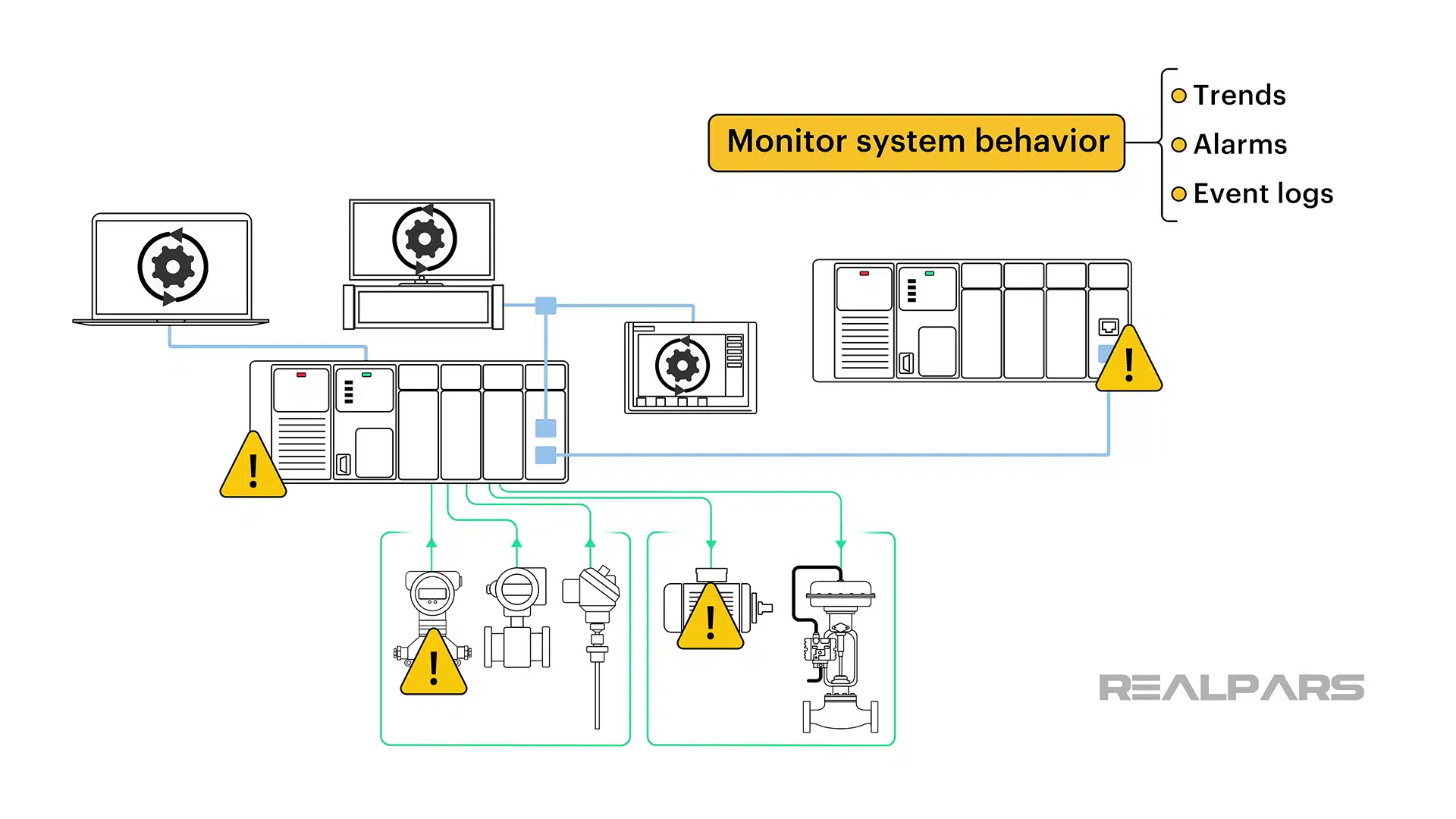
Next, we have system audits. This involves reviewing the system’s design and ensuring that it is properly configured.
This can be done by examining the system’s documentation, checking wiring and cable connections, verifying settings on devices, and diving into the nitty gritty details of the PLC program.
Take careful notes during system audits so they can be compared and contrasted against similar items within your system.
PID loop tuning is another technique that can be used to optimize the performance of a control system. This involves fine-tuning the parameters of the PID controller to ensure that the system responds quickly and accurately to changes in the process variable.
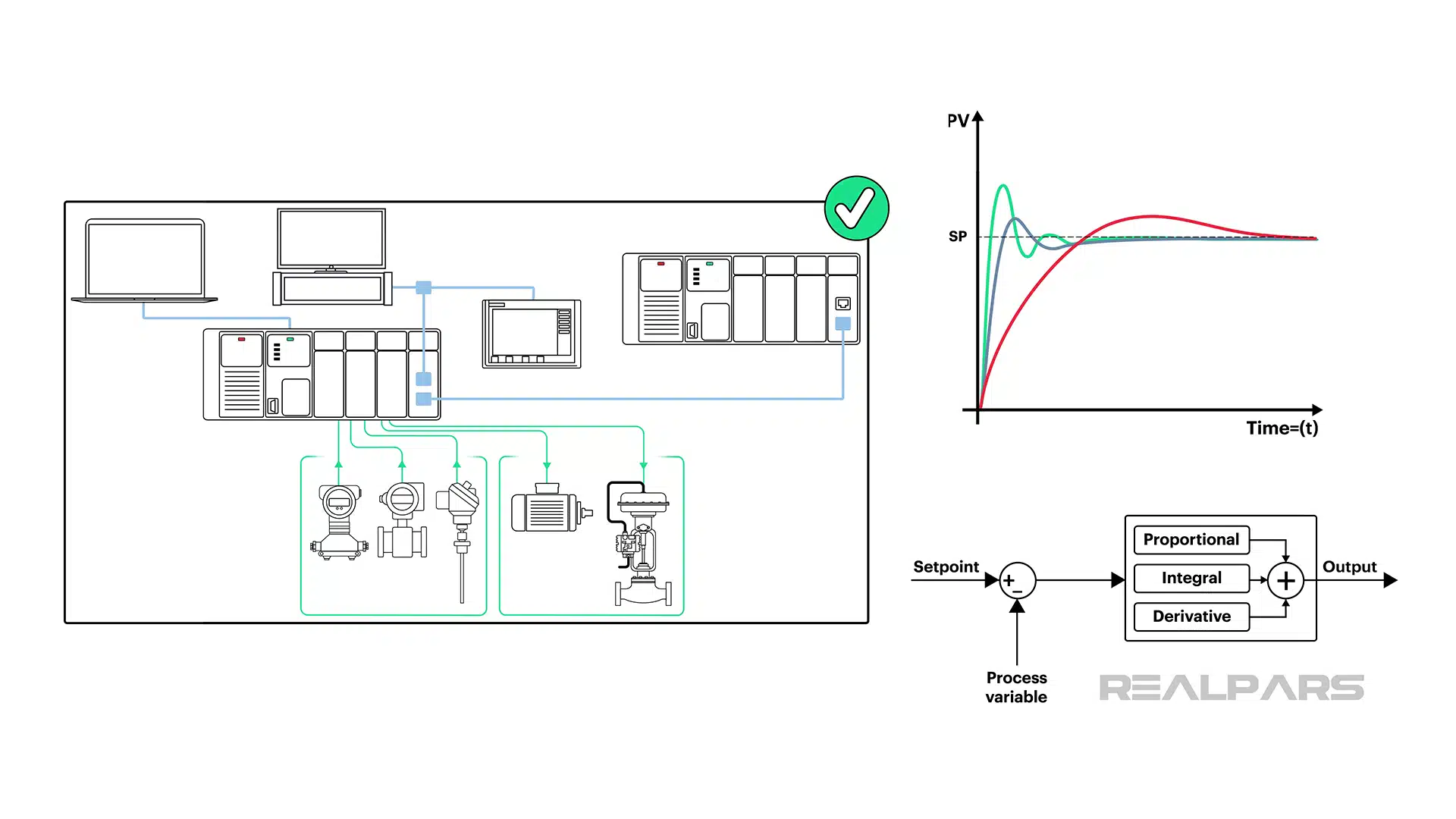
PLC program debugging is also a useful tool when working with more complicated PLC code. Program debugging is a methodical approach to problem-solving and often involves taking steps through the code to pinpoint where errors are occurring.
The various debugging tools available to use will depend greatly on the PLC brand and software that you’re using.
Conclusion
PLC troubleshooting requires a structured and methodical approach. Understanding the fundamental components of a PLC and how they work together is essential.
By following basic tips and utilizing advanced techniques, you can effectively troubleshoot your control system and minimize downtime.
Remember to gather information, use resources, check system wiring, examine program logic, monitor system behavior, perform system audits, fine-tune PID loops, and utilize PLC program debugging to help you diagnose and solve problems quickly and efficiently.
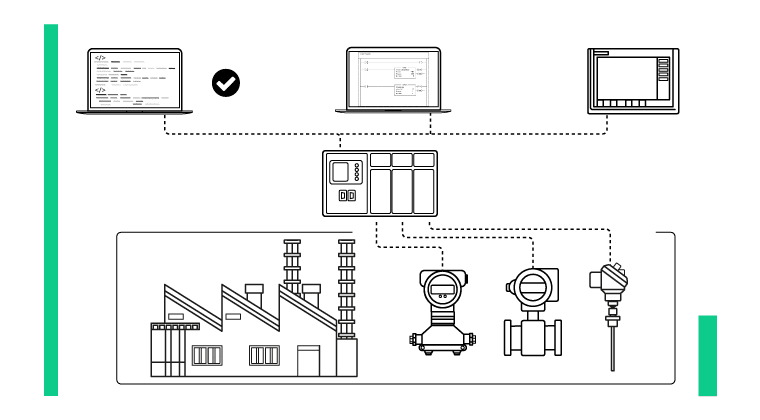
Unlock the secrets of PLC troubleshooting with RealPars’ free courses, where we take a closer look at all the details of PLC troubleshooting. Get your feet wet and embark on an exciting learning journey today! Don’t miss out on expanding your knowledge!
Frequently asked questions
Learn from Industry Experts
With a 7-day trial, then €35/month