Single-Pair Ethernet vs. Traditional Ethernet
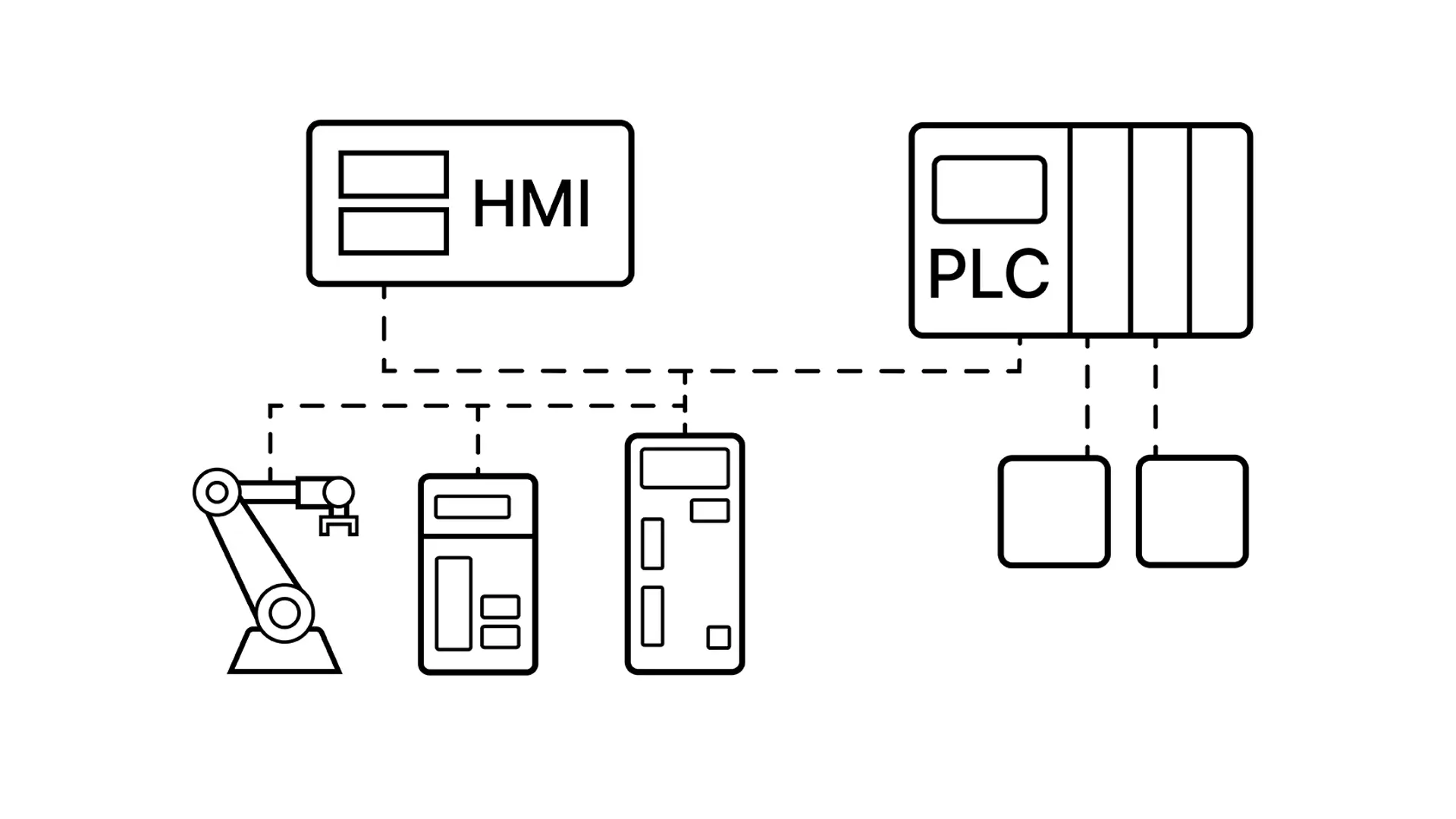
Ethernet communications are everywhere! We have it at home for internet connections to our computers, laptops, and tablets. There are even Ethernet-connected appliances, cars, and other devices. But what is Ethernet?
Ethernet is a family of computer networking technologies commonly used in local area networks and wide area networks such as is used for our cell phones.
It was commercially introduced in 1980 and first introduced as a standard in 1983 by the Institute of Electrical and Electronics Engineers as IEEE 802.3.
Ethernet has been used in industrial plant settings for decades for communication between PCs, PLCs, and HMIs, as well as to various devices and servo drives on the plant floor using communication protocols such as Ethernet/IP and Profinet.
Before we dive deep into the world of Ethernet if you’re thinking, How can I get a full handle on this? Well, there’s a great course called Single-Pair Ethernet Fundamentals just for you.
And if you’re a RealPars Pro Member, you can jump right in and take the course. Building on that, let’s jump into the core of today’s topic.
Ethernet as a physical protocol
The Ethernet standard describes the data transmission from one device to another over a cable, fiber, or wireless connection to a network of many devices.
For instance, over a wired network, these data are represented by a series of voltage transitions which translates into a string of 0’s and 1’s. In a fiber network, these data are represented by a series of light pulses.
A network is the means by which this data is routed from one device to another. Ethernet networks typically consist of routers, switches, and network interface cards.
The field of Information Technology arose from the need to provide fast, efficient, and secure data transmission via Ethernet.
So is Ethernet a method of physically connecting devices in a network or is it a communication protocol? Well, the answer is yes, and yes! While that sounds a little contradictory, I will explain.
Ethernet can be described using the OSI model. This model is explained in detail in a RealPars course on Single-Pair Ethernet. The OSI model describes any communication protocol as a collection of seven layers, as shown here.
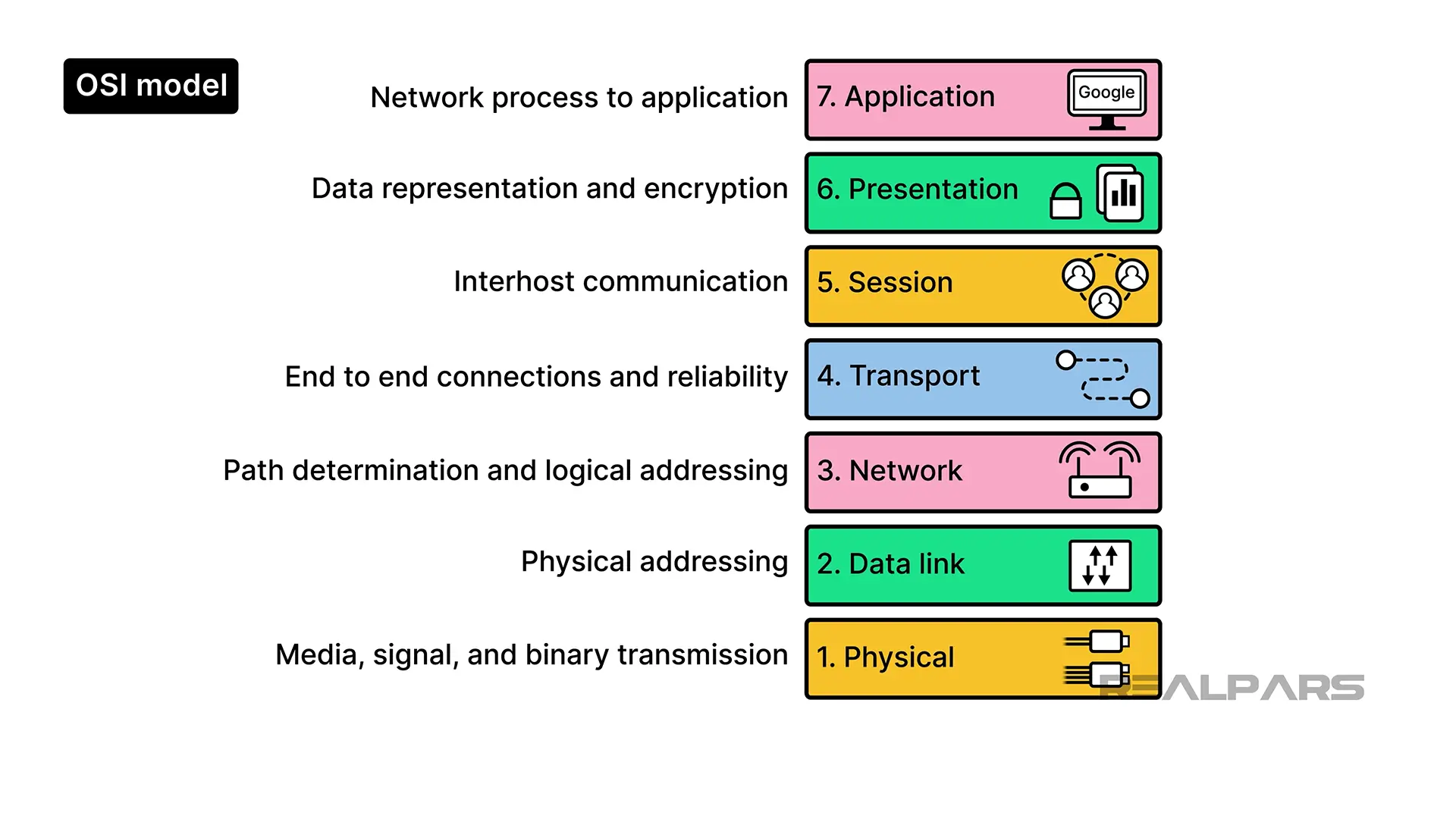
The bottom layer is called the physical layer. The Ethernet physical layer describes the hardware required to connect the device to the network.
It may consist of a wired connection using a 4-pair cable such as Cat-6 and connectors such as RJ-45 connectors, a wireless connection, a coax cable, or a fiber optic cable.
Ethernet as a communication protocol
OSI layers 2 – 7 that reside above the physical layer determine the structure of the Ethernet communication packets.
These packets are composed of many bytes of data arranged in a very specific way with the purpose of sending messages and data from one device to another.
The data structure used in this communication follows the specific rules for the communication protocol chosen, but all use TCP/IP at Layers 3 & 4.
An Ethernet physical layer requires an Ethernet data communication protocol.
When we refer to Ethernet, it could refer to a number of data communication protocols, including Ethernet II, Profinet, Ethernet/IP, as well as others.
All of these protocols fall under the IEEE 802.3 standard discussed earlier. These are distinguished from one another by additional identifiers. For example, Ethernet over coax cabling is identified as IEEE 802.3a.
Ethernet over a multi-pair, unshielded twisted pair cable, such as CAT 5E, and operating at a data communication speed of 1 gigabit per second is identified as IEEE 802.3 ab.
There is also a standard for delivering power over Ethernet which is IEEE-802.3bt.
These flavors of Ethernet can be called Traditional Ethernet since only data is transmitted over these physical and logical protocols.
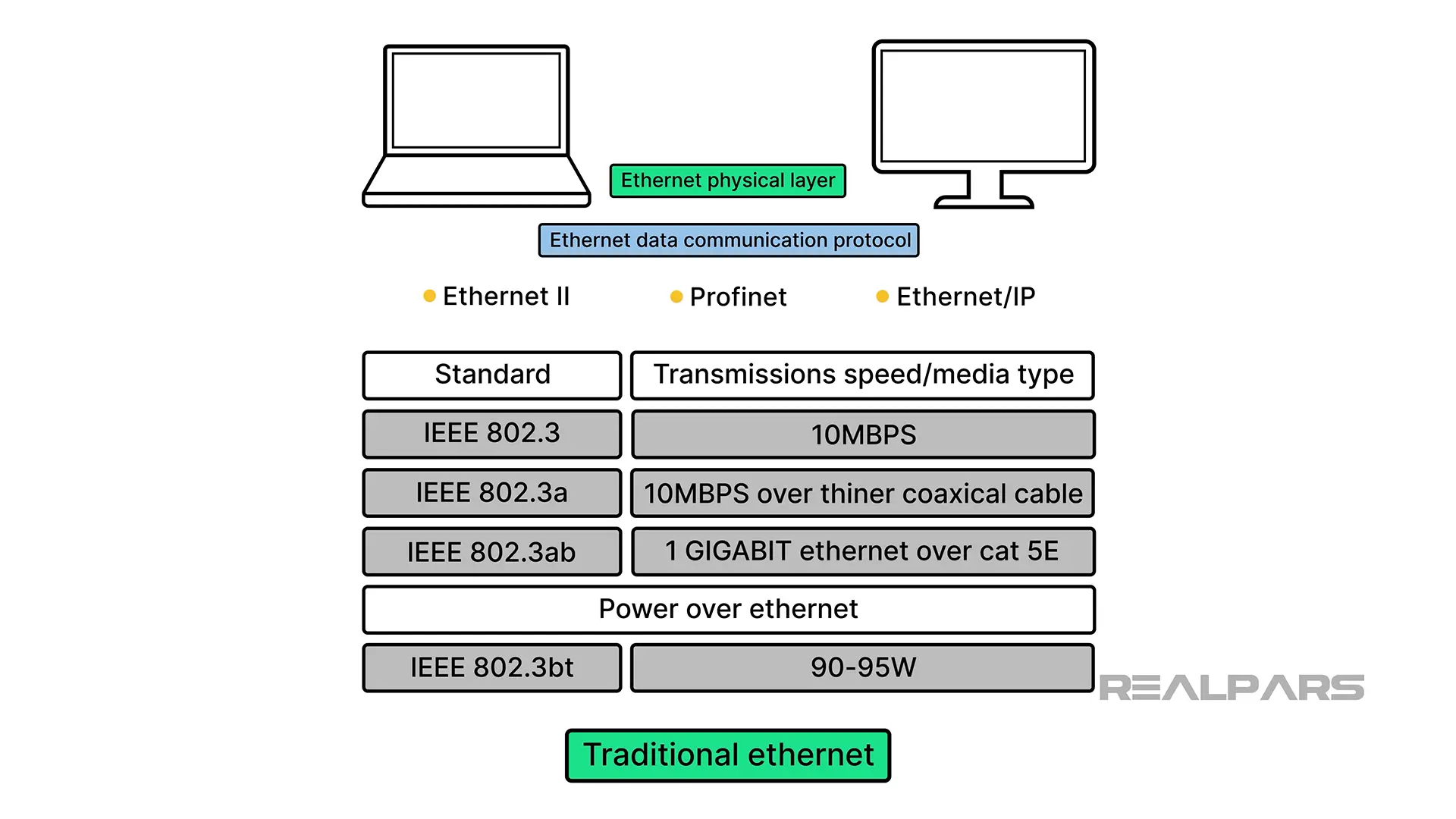
However, a new type of Ethernet physical layer has been introduced which has many advantages in an industrial manufacturing setting.
Enter the new kid: Single-Pair Ethernet
This new Ethernet physical standard is called Single-Pair Ethernet, or SPE, and uses only a single pair of wires to communicate data and may contain an extra 1 or 2 pairs of wires to supply power to the end device, like a transmitter or valve positioner.
For example, SPE, operating at a speed of 10 megabits per second is defined by IEEE 802.3cg.
Instead of multi-pair CAT-5 or CAT-6 unshielded cable, SPE uses cables that conform to standard IEC 63171. These cables may be constructed from a single pair of wires for data communication.
These cables are 50% lighter than CAT-6 cabling and use industry-standard M8 quick-connect barrel-type connectors. This makes SPE ideal for installations, such as inside robots.
The ability to wire a sensor or actuator directly to a network without having to use an intermediate box, such as a remote I/O panel, is now possible.
Data can be evaluated directly by a connected PLC or other device, such as SCADA software. This makes the overall architecture simple and cost-effective.
IEC 63171-6 SPE cabling may also include a separate pair for power, which can deliver up to eight amps to end devices arranged in a multi-drop configuration, called Power over Data Line.
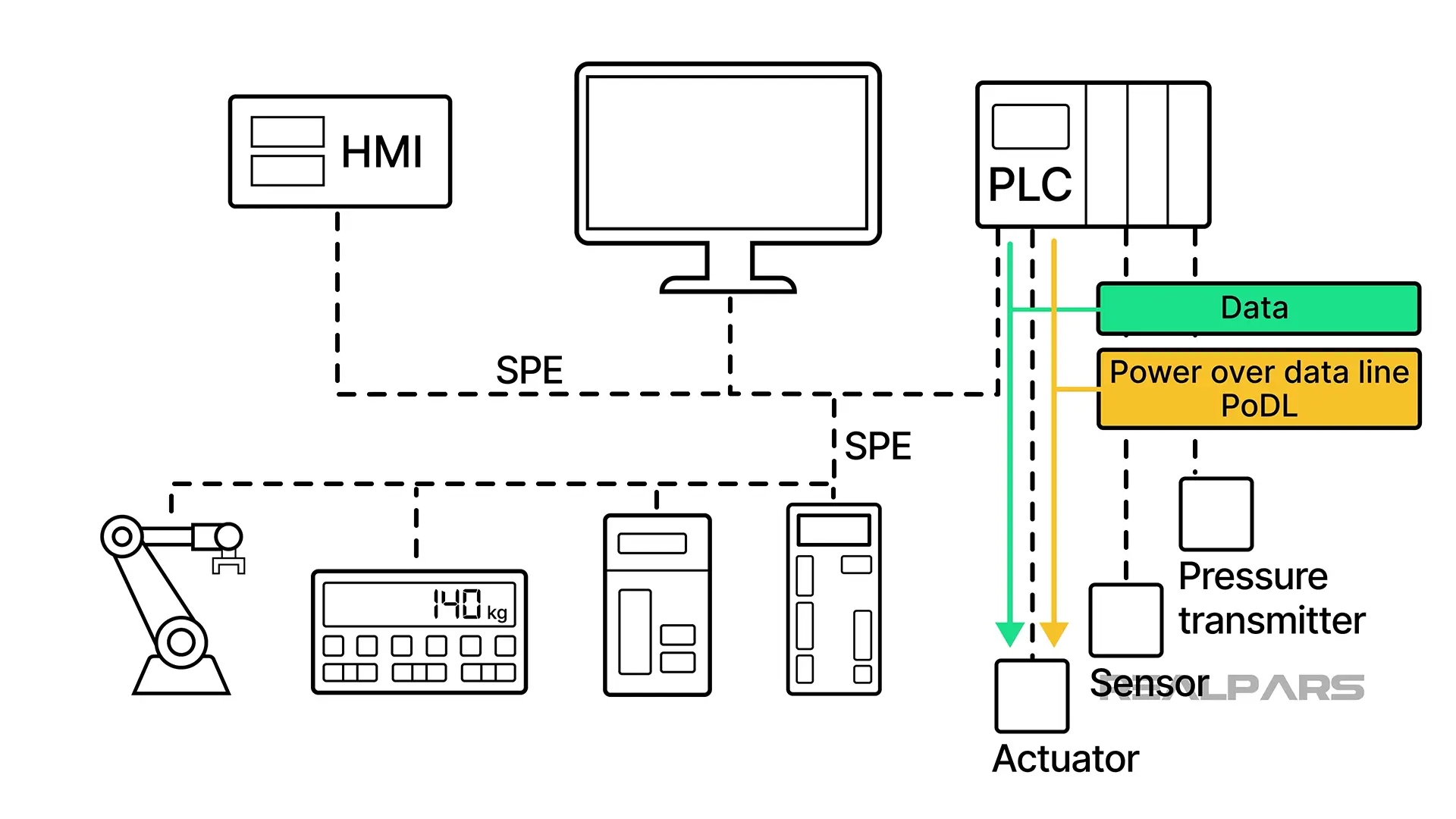
The reduction in the amount and complexity of wiring can translate into significant cost savings and increased data transmission speeds as opposed to traditional Fieldbuses.
Since SPE is a physical protocol, the same logical protocols for data communication can be used as with traditional Ethernet. Sensors and actuators are being developed for Profinet, Ethernet/IP, and others.
Which Ethernet is right for you?
So which Ethernet is right for your application? First, you need to determine your data needs and the requirements of your infrastructure.
If you have an existing infrastructure that is based on traditional Ethernet network devices and cabling, it would be logical to extend that network with similar components.
If a new system is to be installed, it would be advantageous to explore a Single-Pair Ethernet infrastructure.
SPE uses similar, but different, network switches and equipment, so an initial investment in SPE-compliant devices will need to be made.
However, this investment will pay itself back with savings in cabling and installation costs, even for small installations.
Of course, Ethernet of any kind is about the collection and transmission of data. In order to use SPE, a suitable end device, such as a pressure transmitter, is required.
As more and more SPE devices are introduced, the additional choices will allow for the selection of devices with the best features for the plant.
For plants undergoing upgrades or modifications, gateways are available to link new SPE subnetworks to existing plant fieldbus networks.
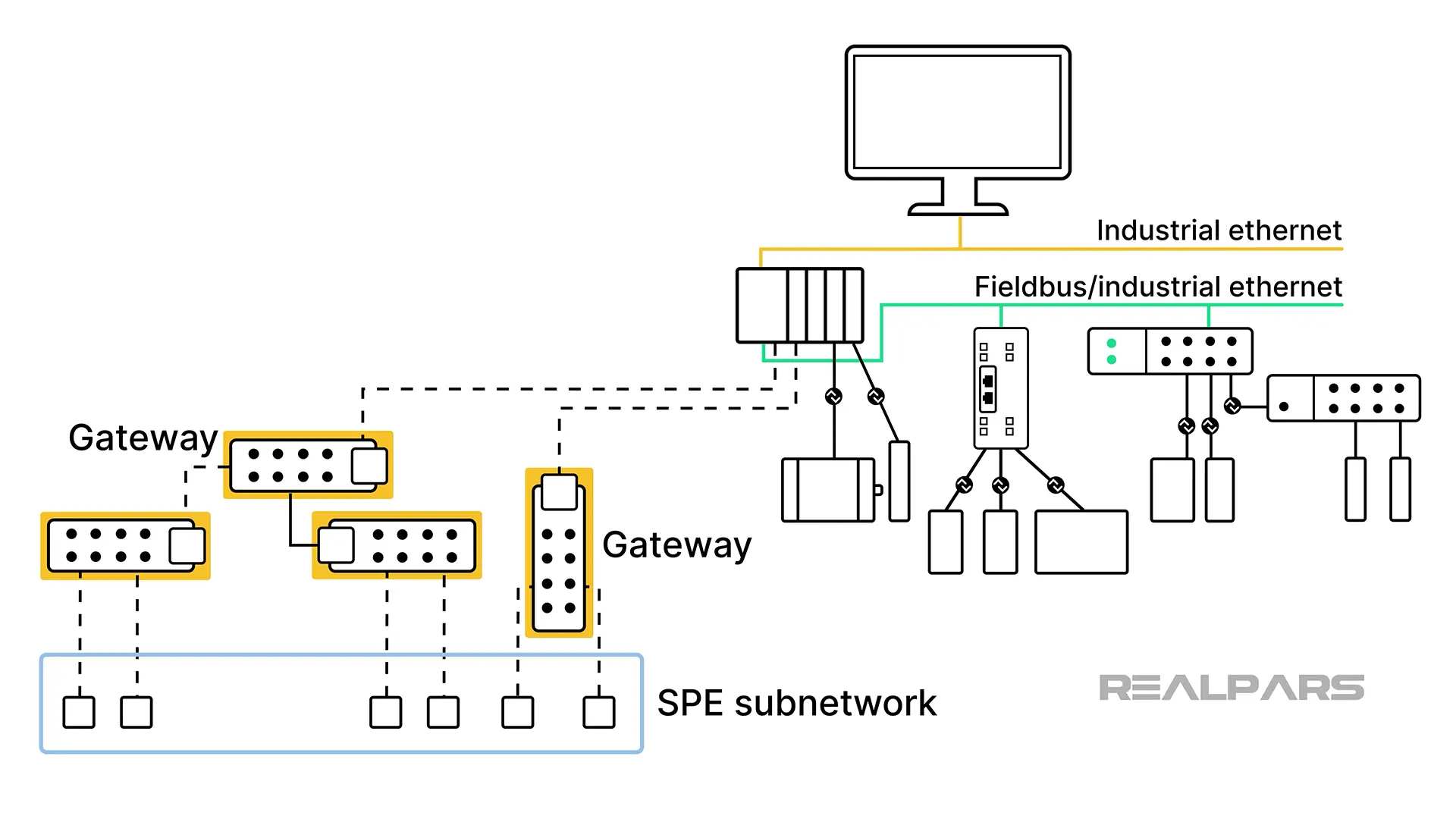
This step-wise approach to SPE can allow for the benefits of SPE to be obtained over multiple projects, allowing for a cost-effective approach to SPE without major downtime or interruption to plant operations.
The best news is: that you have a choice! Determine your data and network needs and plan for a successful installation of traditional Ethernet or Single-Pair Ethernet networks and devices on the plant floor.
That wraps up our discussion on Single-pair Ethernet vs. Traditional Ethernet.
Frequently asked questions
Learn from Industry Experts
With a 7-day trial, then €35/month