In this article, we’re going to learn how an IO-Link works. It is a communications protocol that works point-to-point.
IO-Link Basics
IO-Link is a point-to-point communication protocol. A point-to-point connection is a communications connection between two separate endpoints or nodes.
It is bi-directional, meaning it works two ways and works over a short distance.
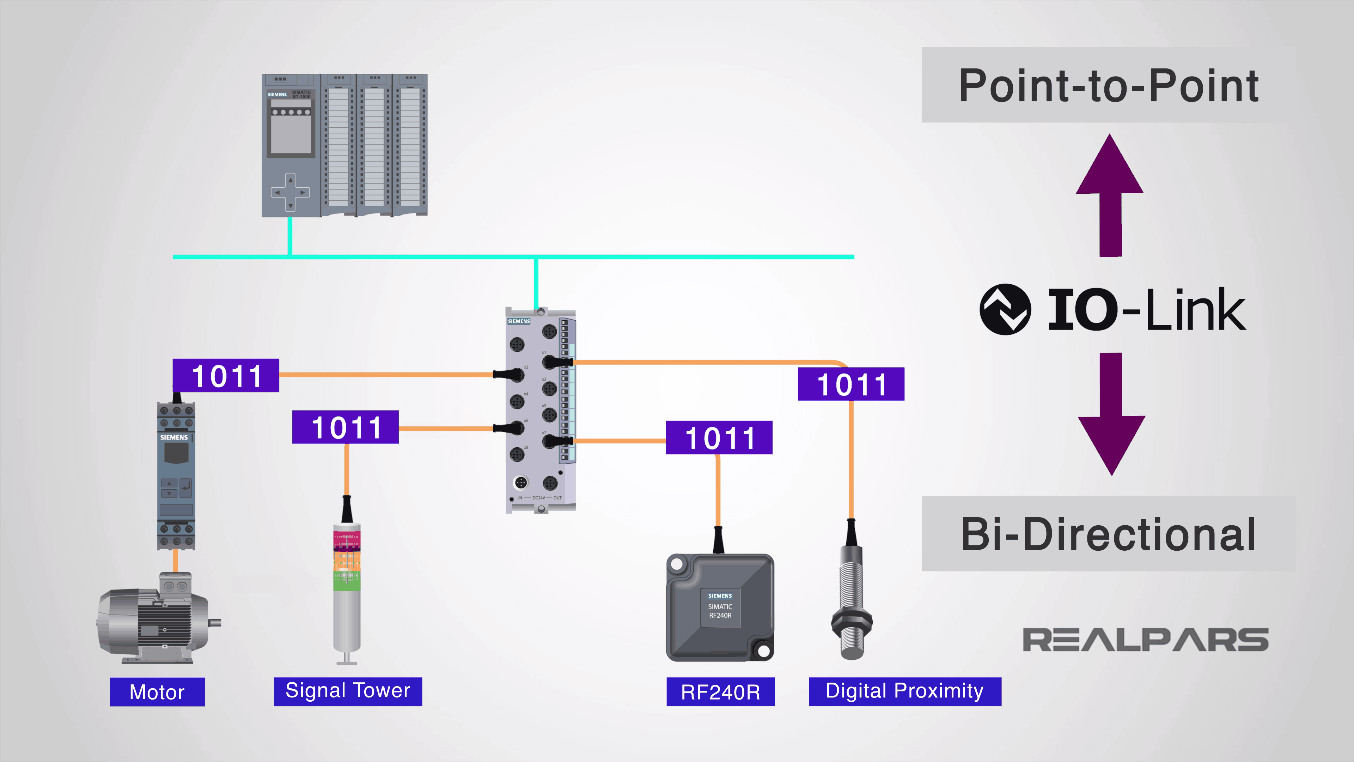
It is primarily used to communicate with sensors and actuators in plant or factory automation processes.
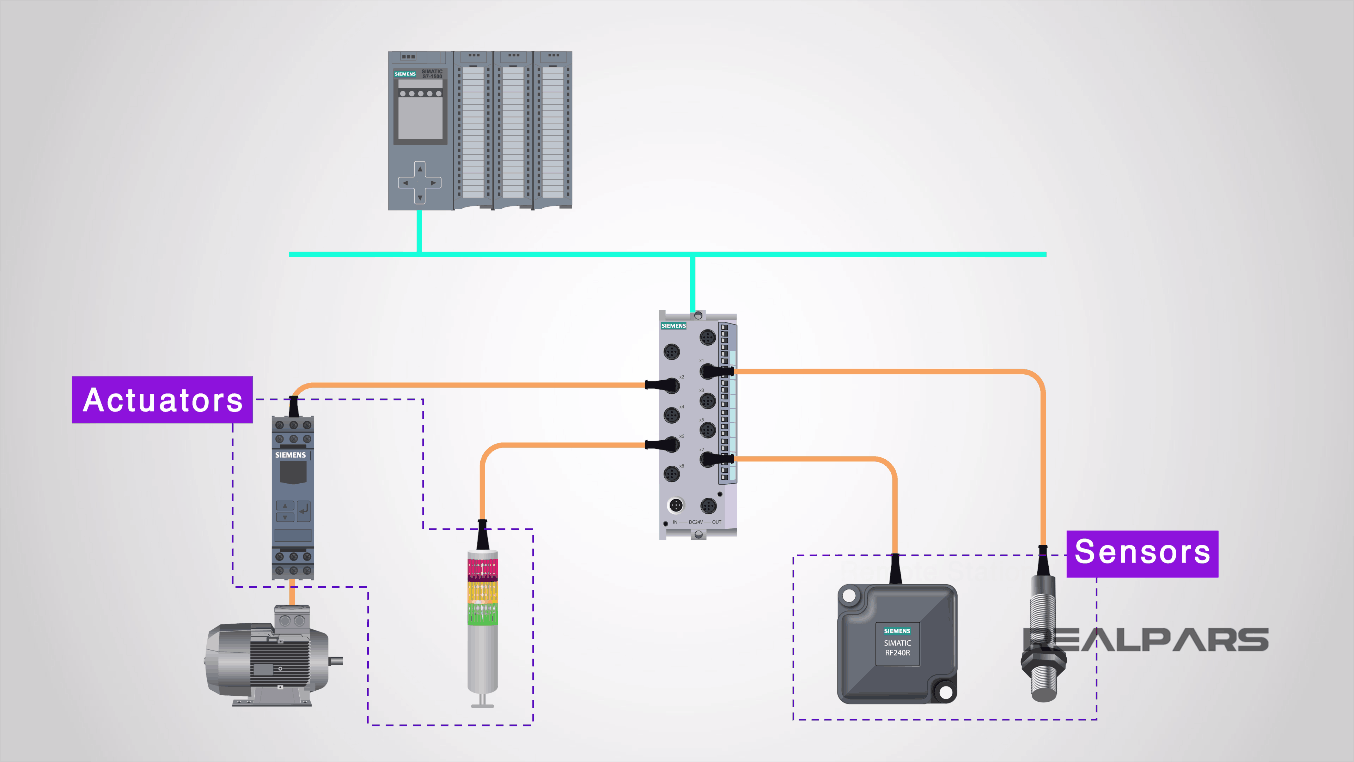
Sensors and actuators are usually connected via Fieldbus connections, allowing them to be in remote locations.
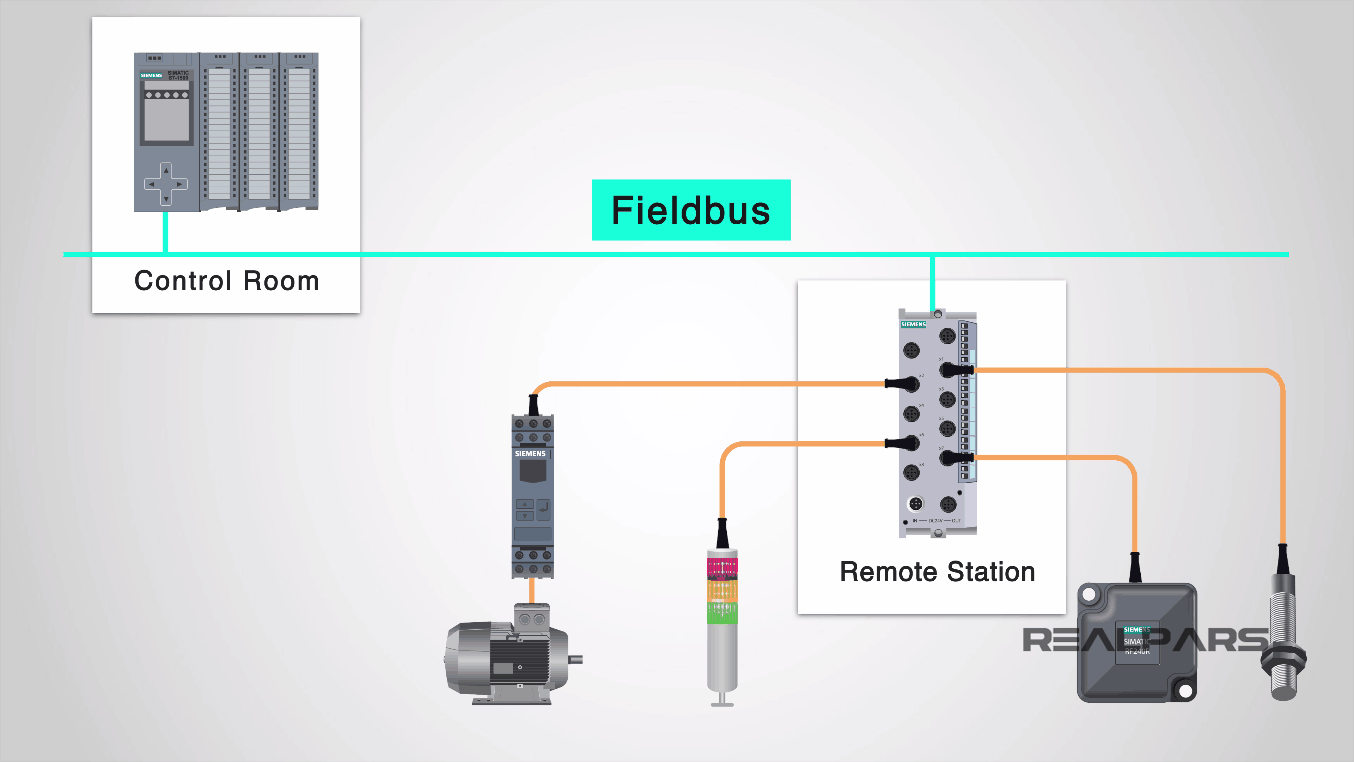
With IO-Link, the field devices, such as actuators or sensors, connect to a ‘Master’ device that communicates to a controller, usually a PLC, or Programmable Logic Controller.
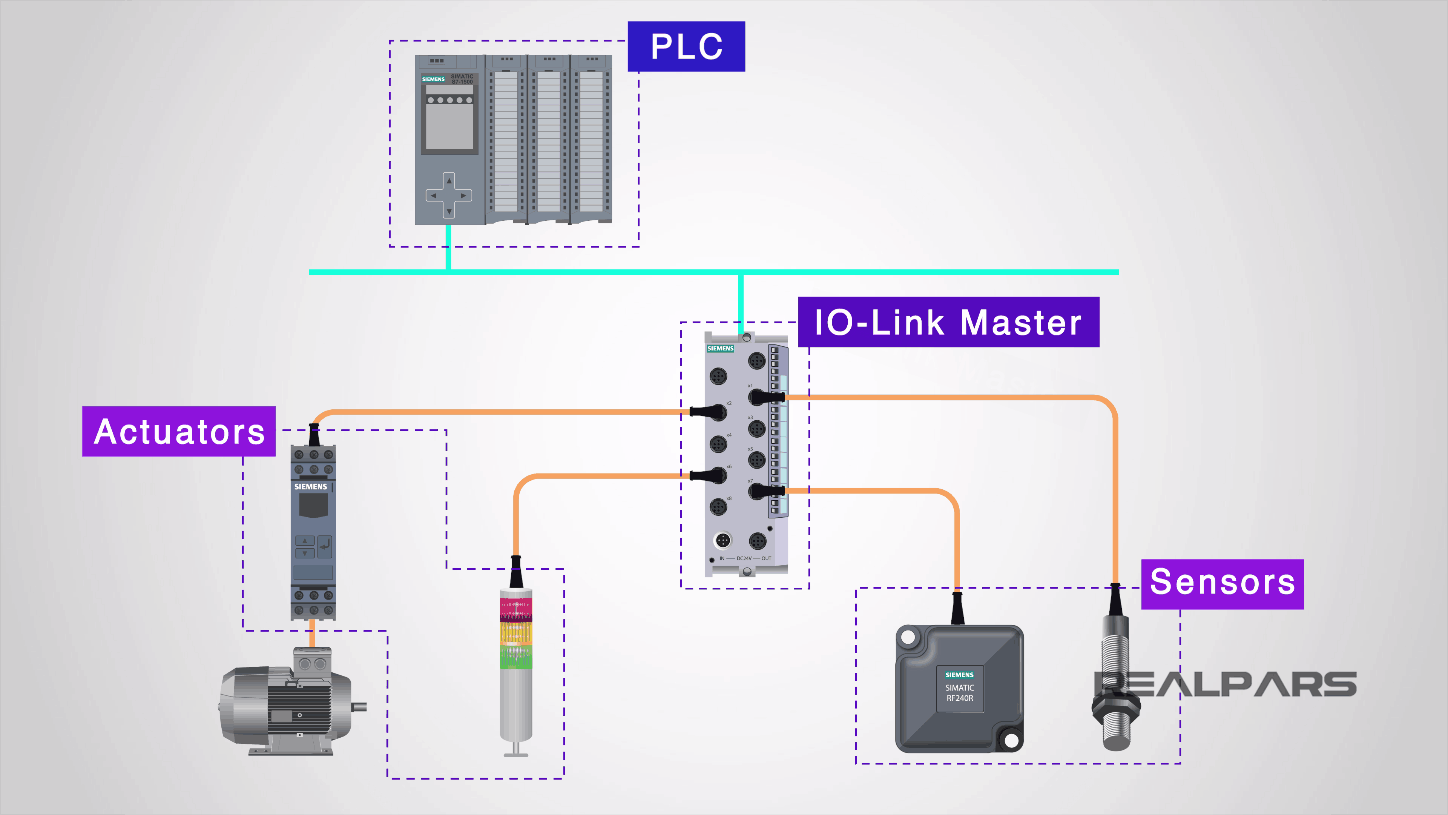
The connection between the IO-Link Master and the field device is established via an unscreened 3 wire cable, no more than 20 meters long.
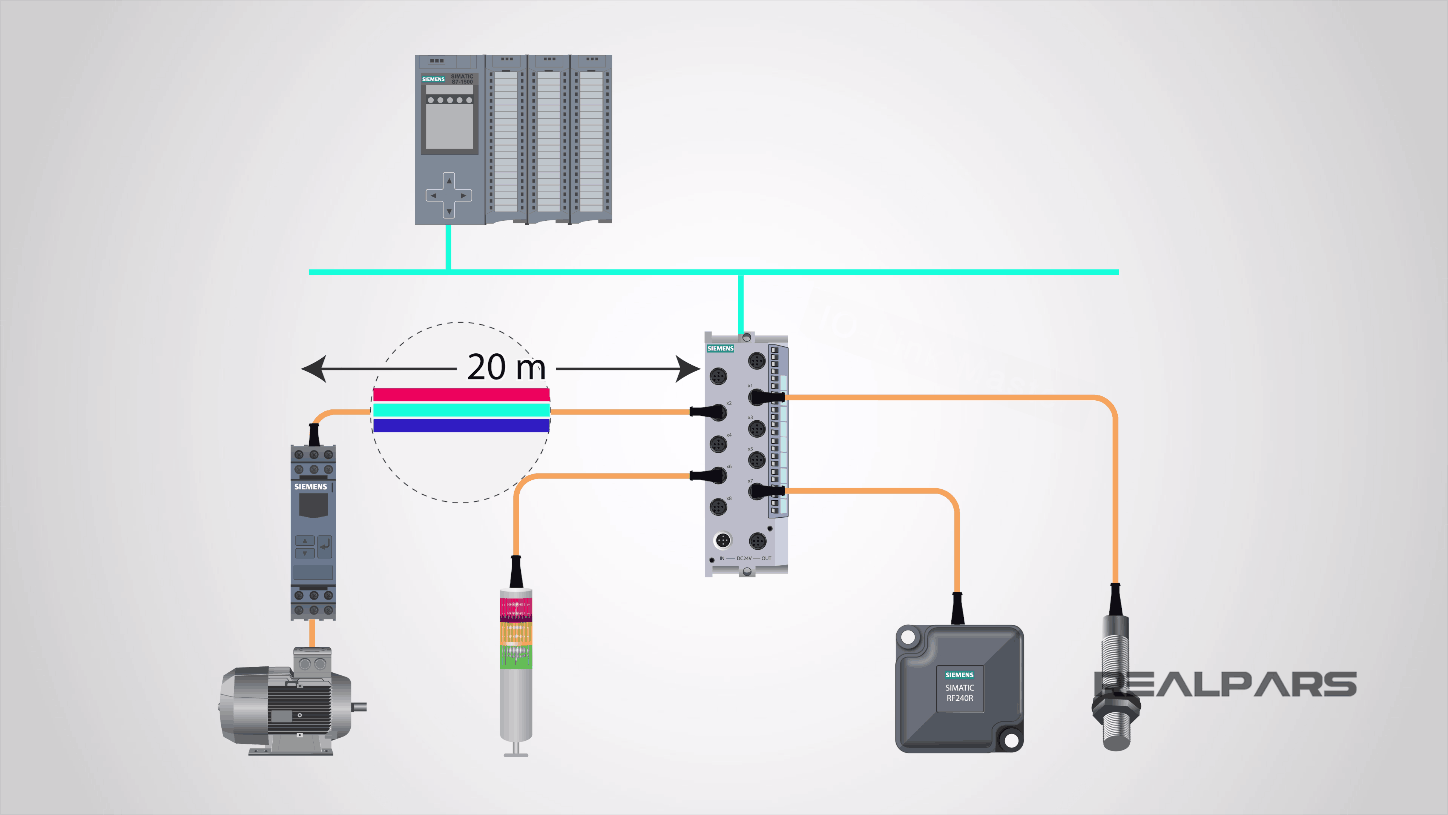
The master device is capable of processing digital signals and analog values.
Its versatility means it is capable of integrating into existing systems and can communicate using the industry-recognized Profinet, Profibus, and Modbus, to name a few.
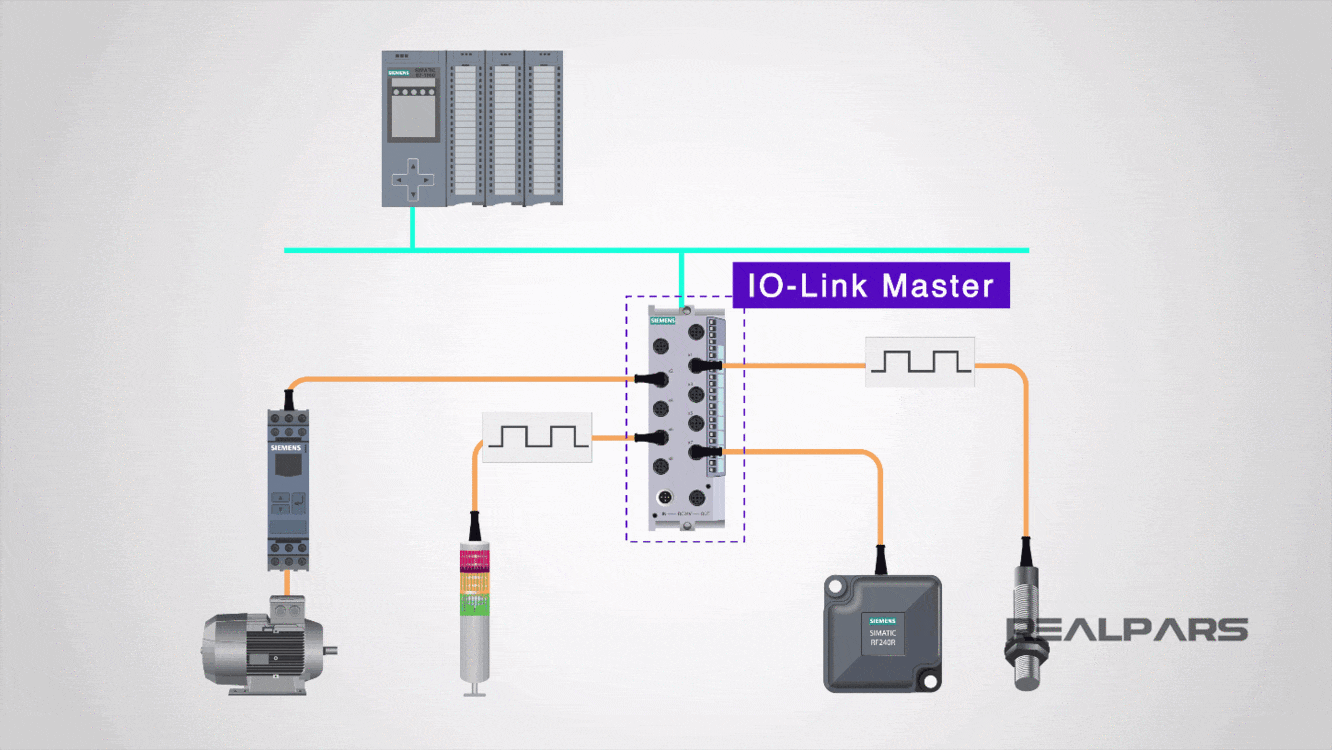
The IO-Link master establishes the connection between the IO-Link devices and the automation system.
As a component of an I/O system, the IO-Link master is installed either in the control cabinet or as remote I/O directly in the field.
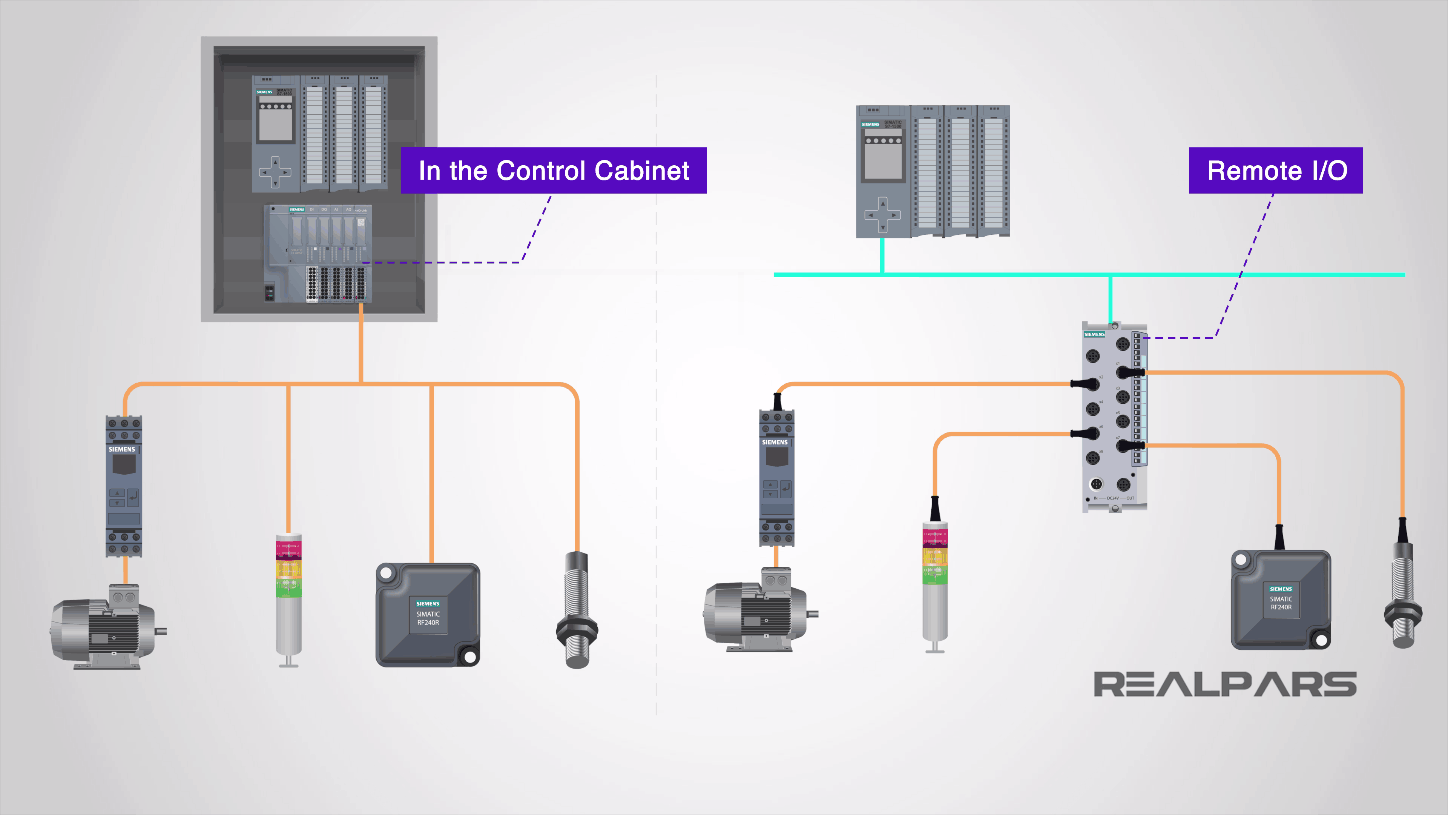
An IO-Link master can have several ports or channels.
An IO-Link device can be connected to each port, meaning IO-Link is a point to point communication and not a Fieldbus.
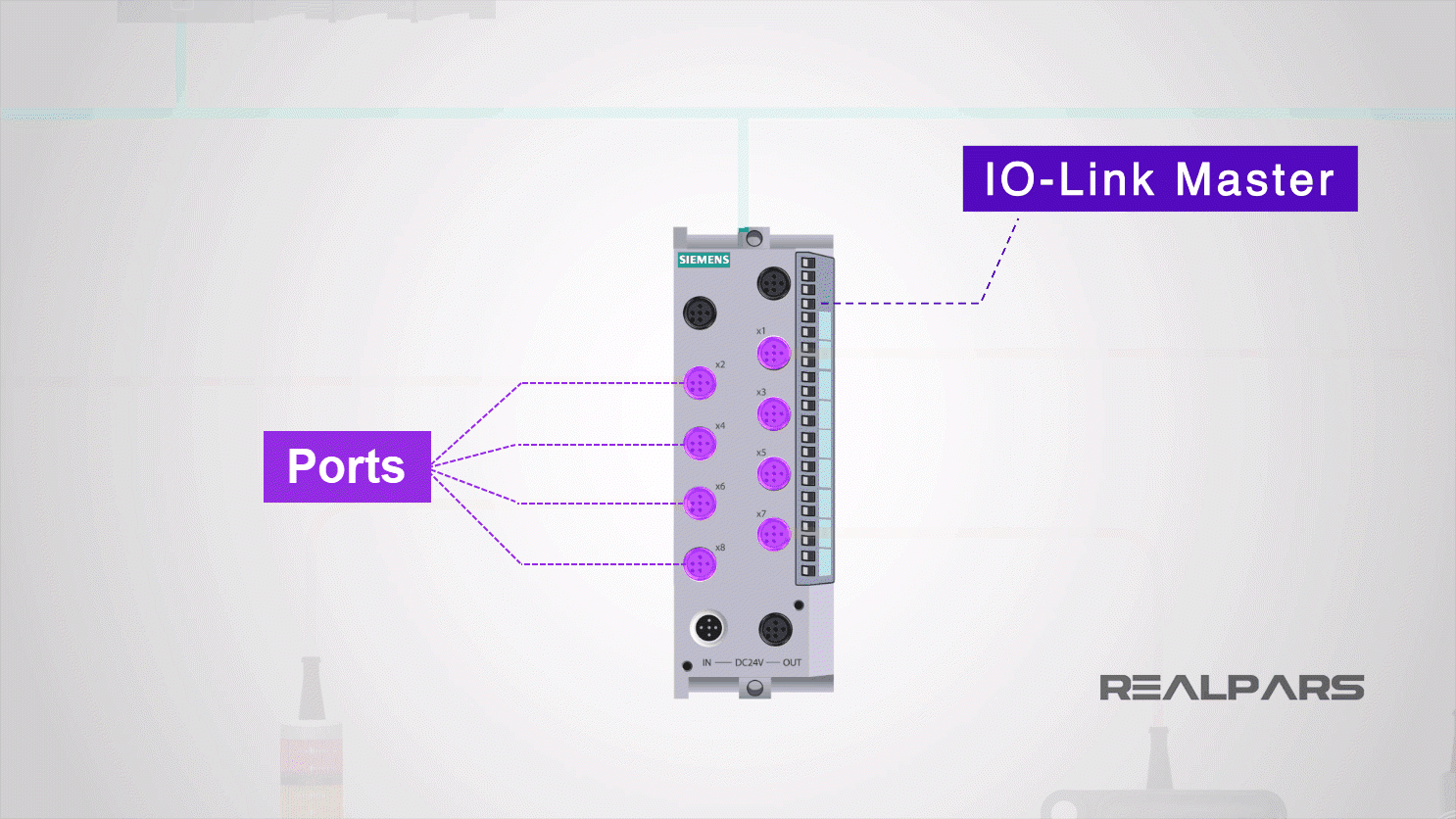
What are IO-Link Operating Modes?
The IO-Link protocol allows a port to be operated in one of four different operating modes.
1. IO-Link Operating Mode
The first mode is the IO-Link mode. This means that the port is used for IO-Link communication.
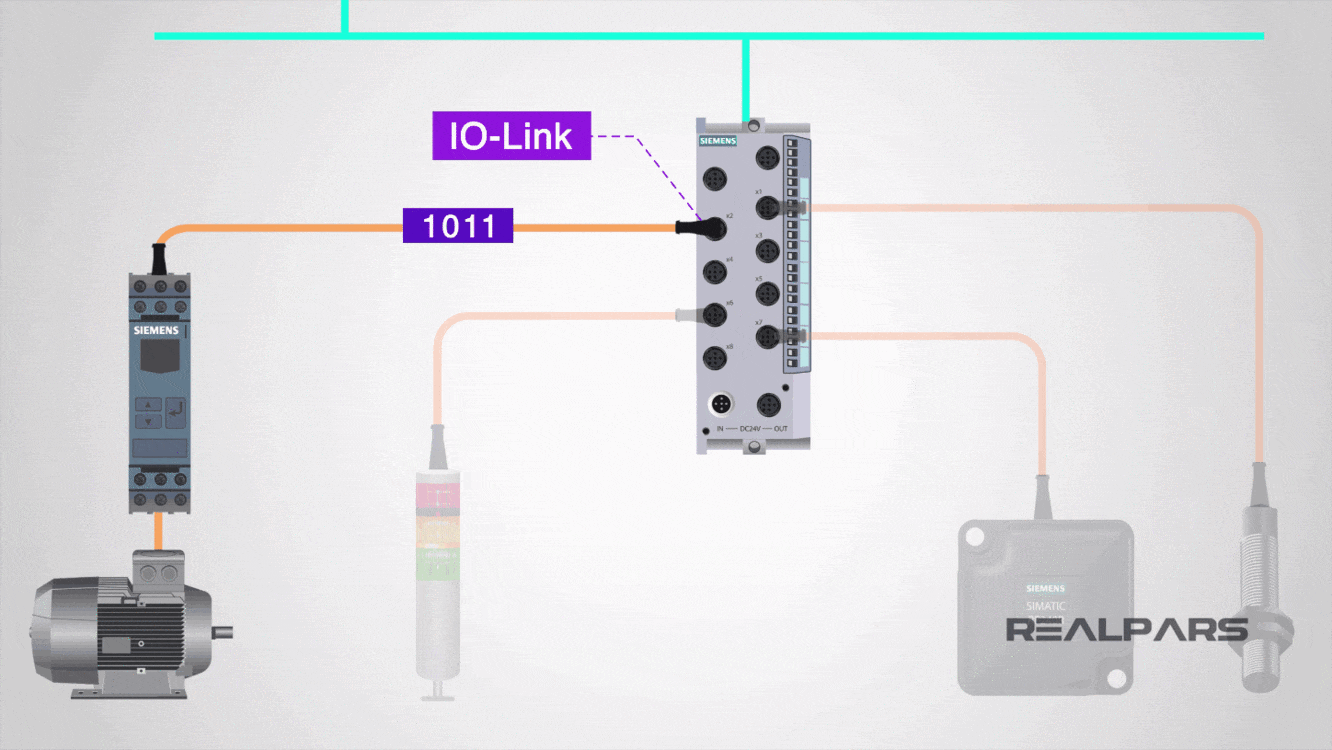
2. DI Operating Mode
The second mode is the DI mode.
This means that the port acts in the same way as a digital input device.
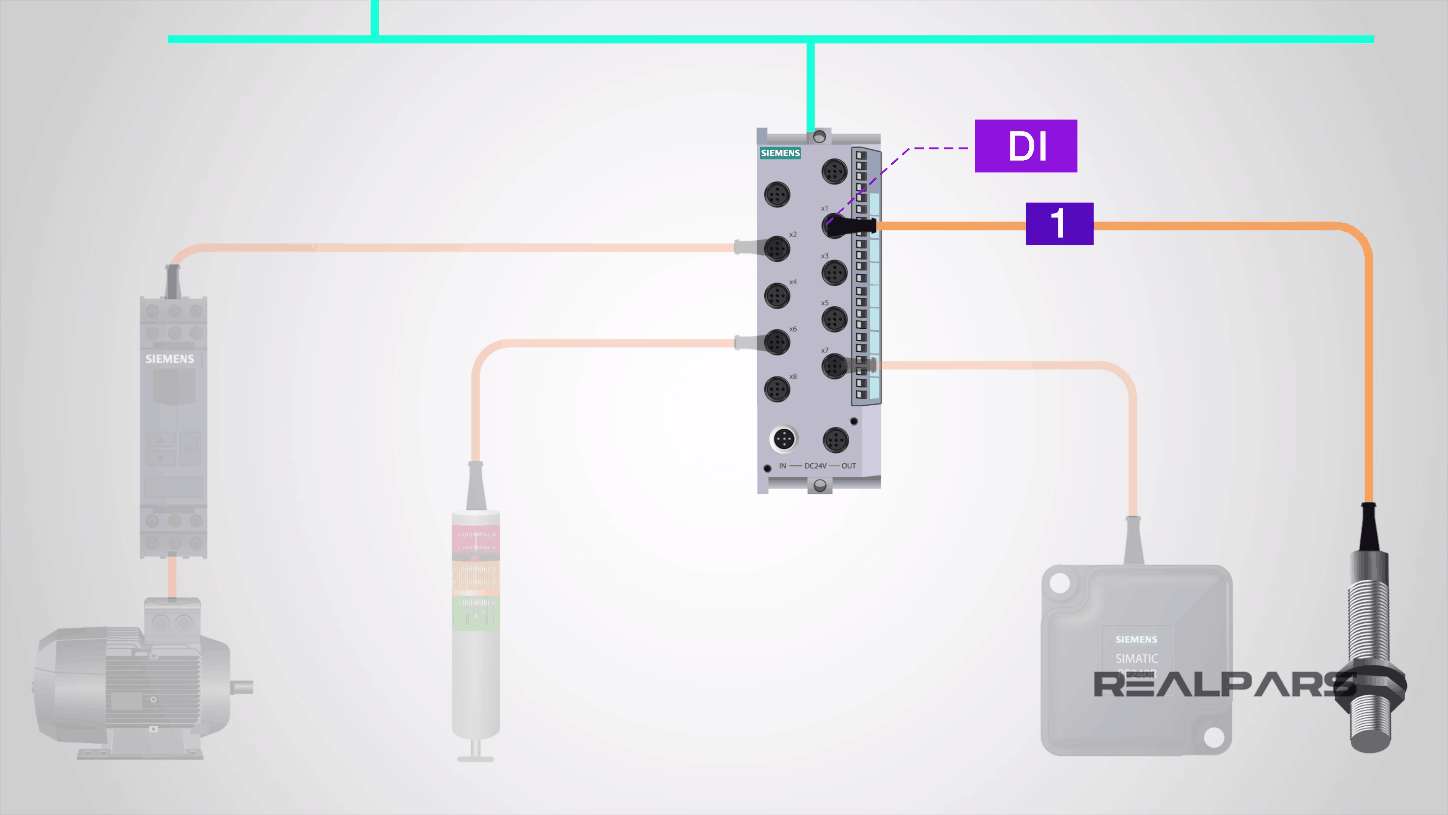
3. DQ Operating Mode
The third mode is the DQ mode.
This means that the port acts in the same way as a digital output device.
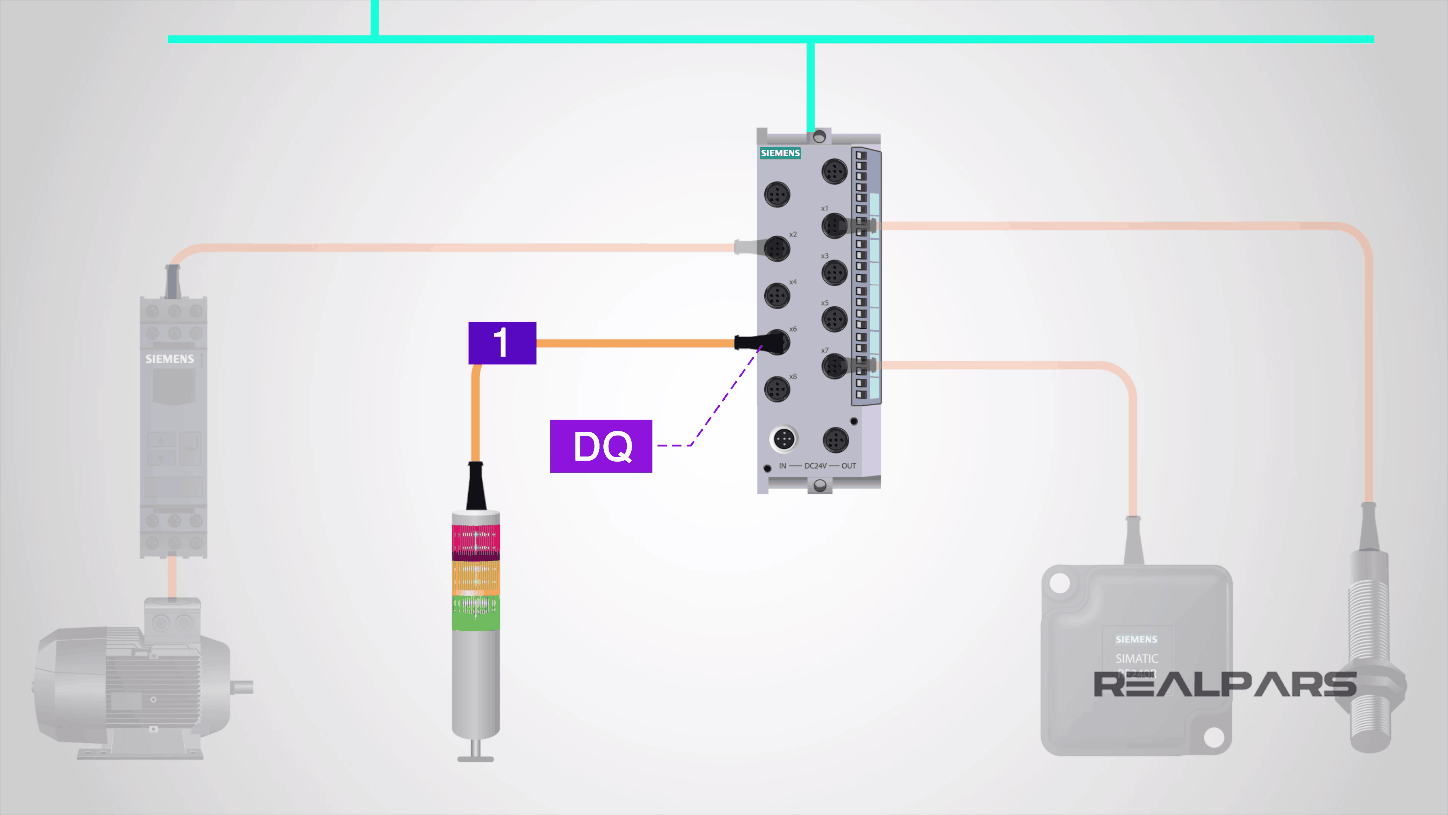
4. Deactivated Operating Mode
The fourth mode is Deactivated.
This means that the port is not assigned to any other modes and is reserved for when the port is unused.
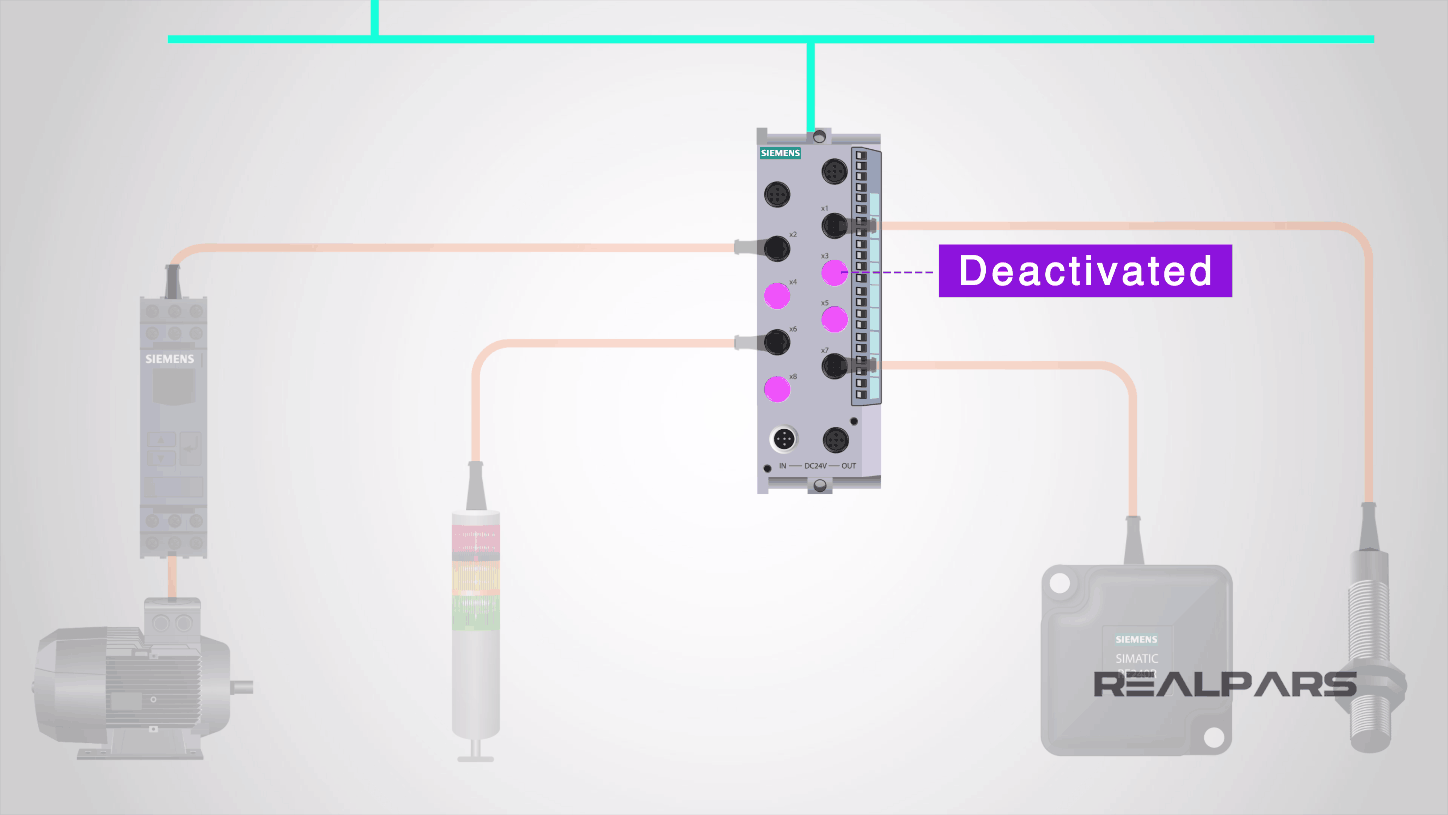
IO-Link is a very robust communication system that operates using 24 volts.
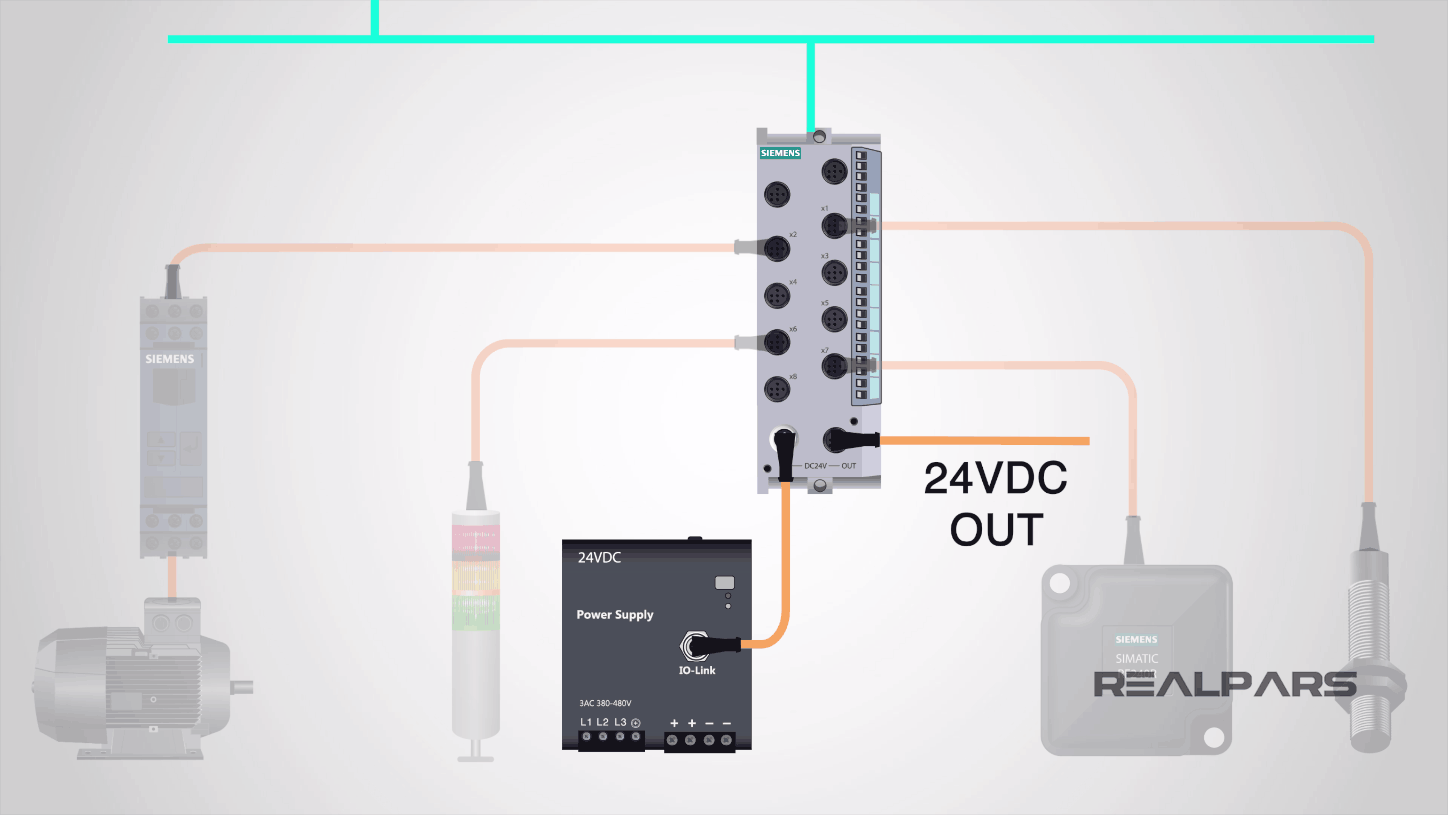
Transmission errors can occur for a number of reasons, in general, a cable fault or a power surge can temporarily interfere with transmissions.
If an error is detected, the message attempts transmission up to an additional two times.
Only after the transmission has failed for the third time does the IO-Link master recognize a communication failure. Upon recognizing this, the master will signal the communications failure to the higher-level controller. This can then alert operators or maintenance staff of the issue, so they can physically attend to and rectify the problem.
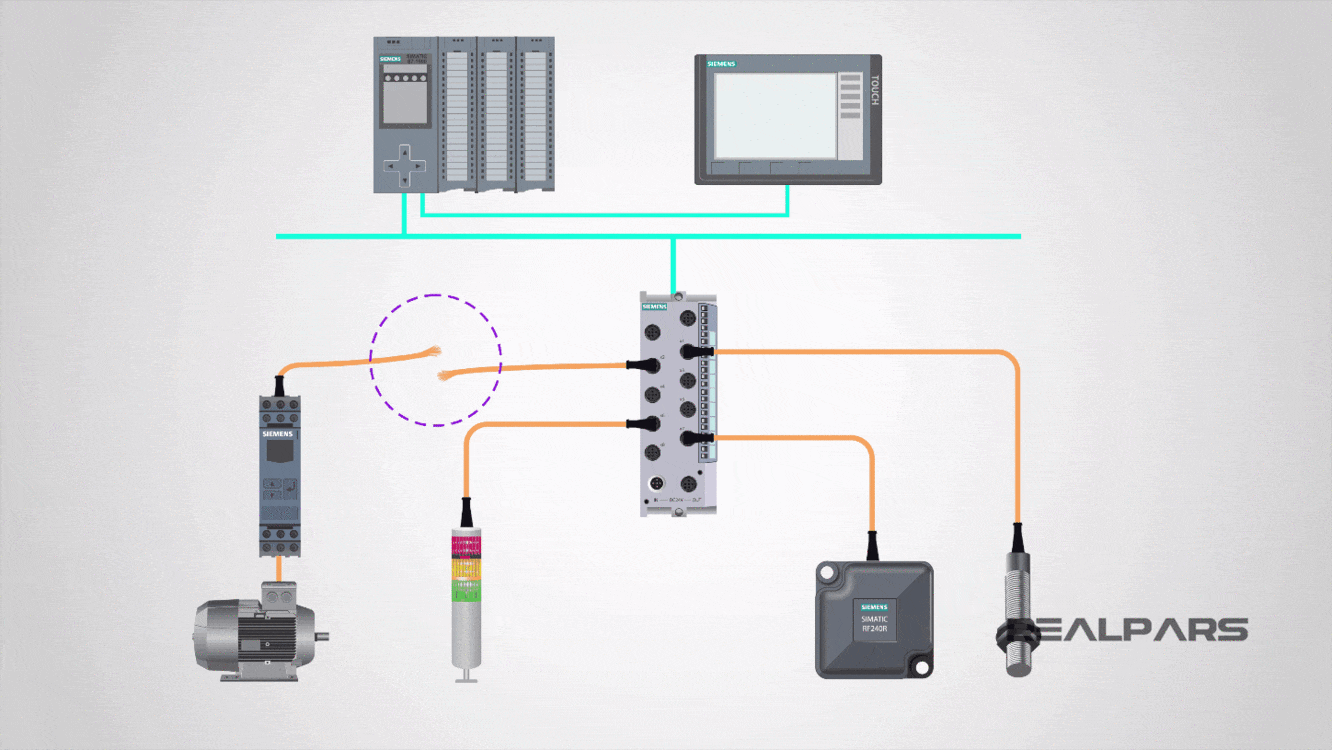
What are IO-Link Transmission Types?
An IO-Link device has four types of transmission. These are:
– Process Data
– Value Status
– Device Data
– Events
1. IO-Link Process Data Transmission
The Process Data is considered as the latest state of the sensor or actuator, such as speed.
Process Data is transmitted cyclically, which means automatically, at regular defined intervals. Up to 32 bytes of process data can be processed, and it’s defined by the high-level controller.
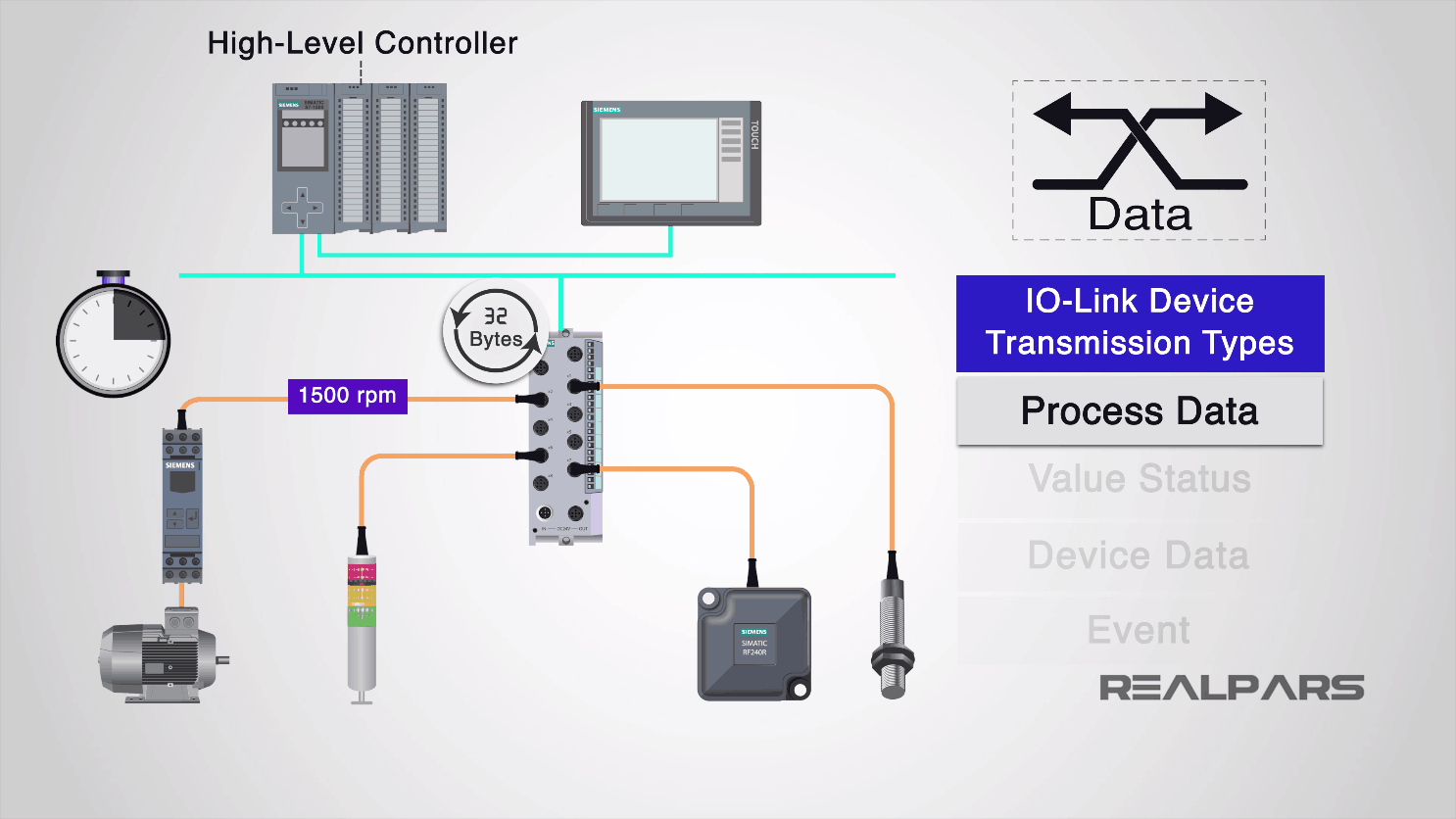
2. IO-Link Value Status Transmission
The Value Status indicates whether the Process Data is valid or invalid and is transmitted along with the Process Data cyclically.
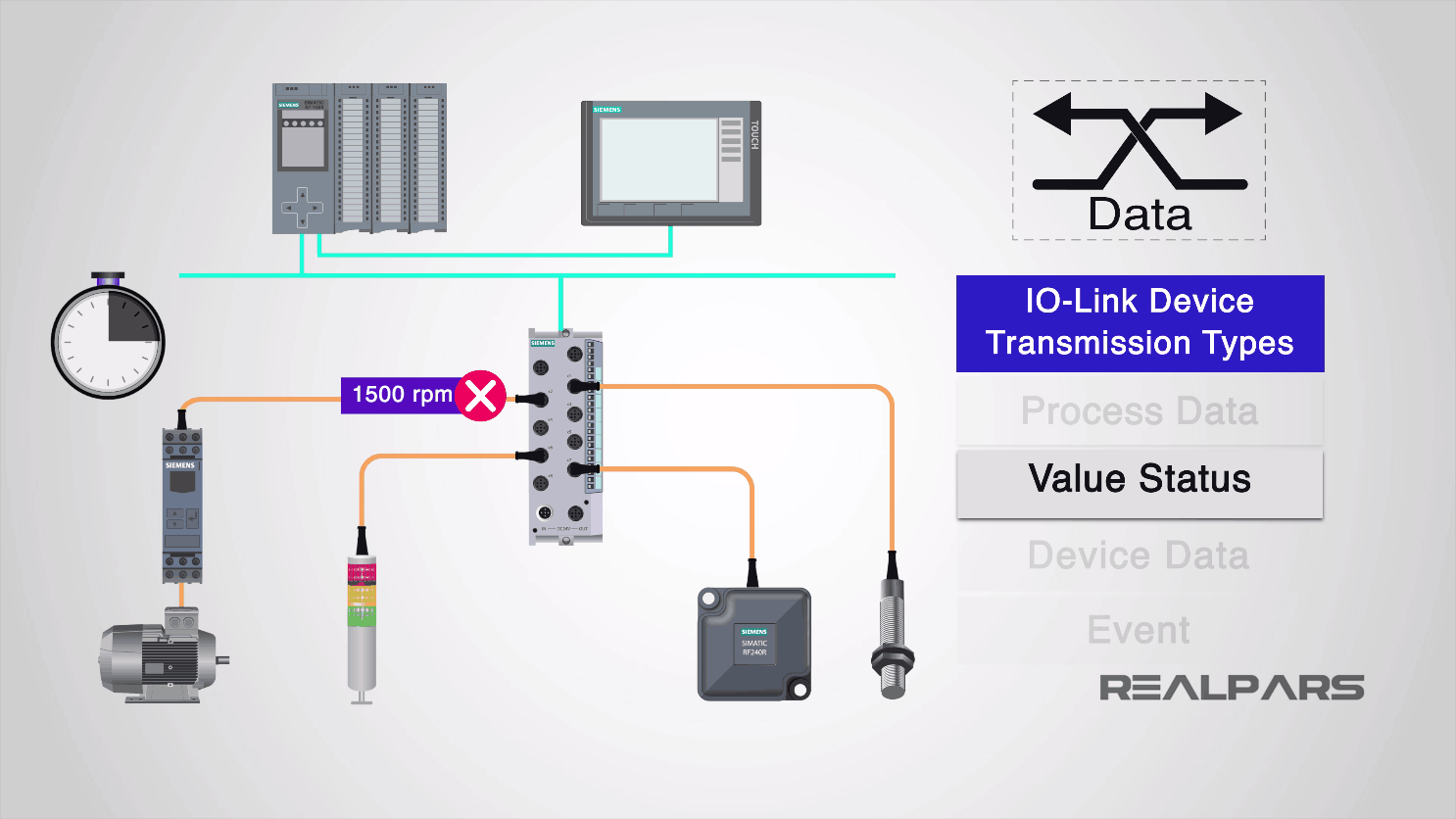
3. IO-Link Device Data Transmission
The Device Data holds detailed information about a device.
Basic information such as the serial number or version number and more advanced information such as parameters or diagnostic information are able to be retrieved from each IO-Link device.
Device Data is transmitted acyclically, at the request of the IO-Link master. This means that it is not automatically transmitted but will be transmitted after a request from the Master.
Device Data can be read from the device, but also written to.
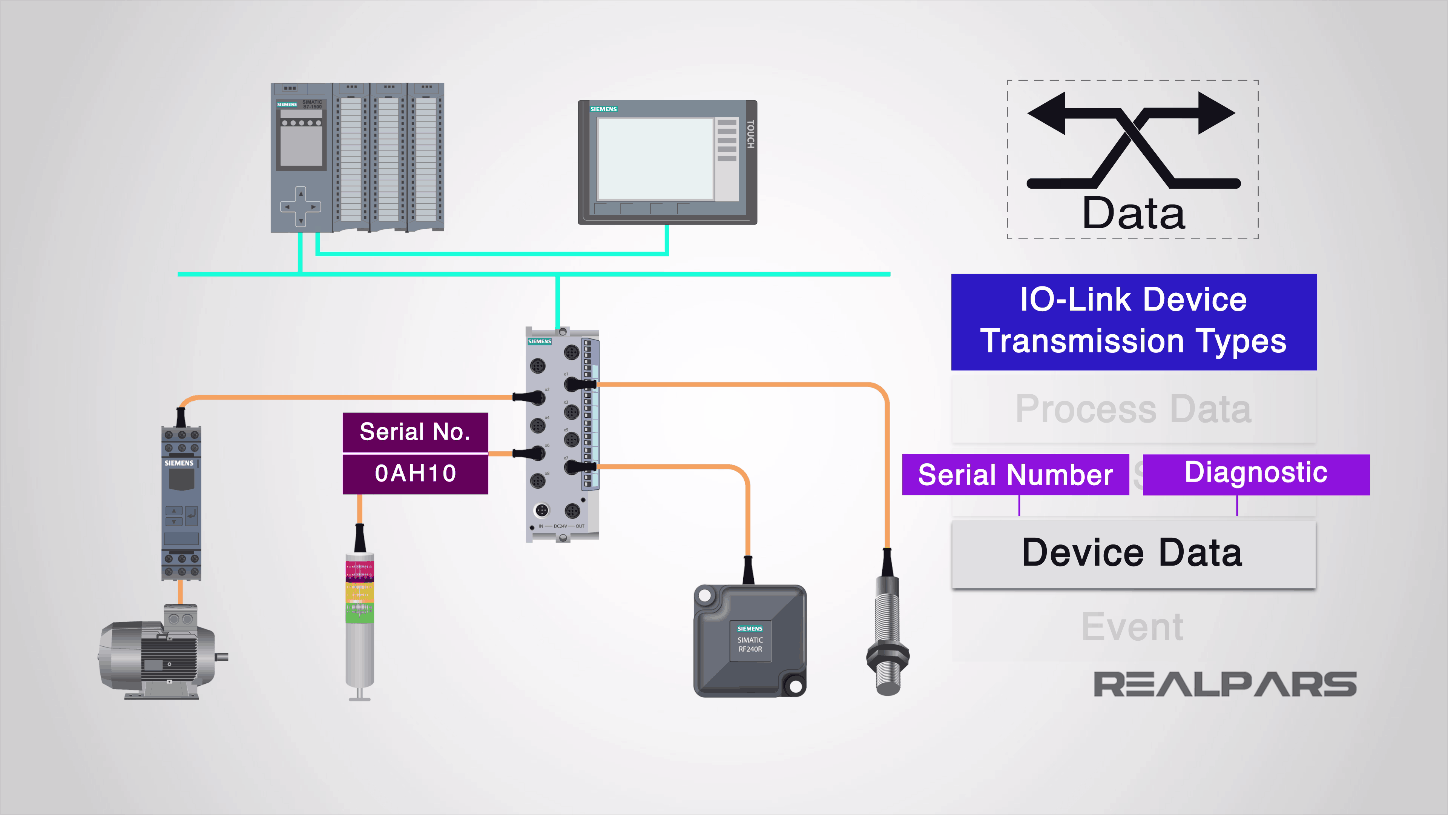
4. IO-Link Event Transmission
A device is able to trigger an Event, which in turn signals the presence of an Event to the IO-Link Master.
An example of an event is an error or warning message, for example a short circuit, or a device that is overheating.
This information can be used to display indicators or messages on HMI devices, such as error messages signalling a wire break or a communication failure, once the Master has processed the message to the High-Level controller.
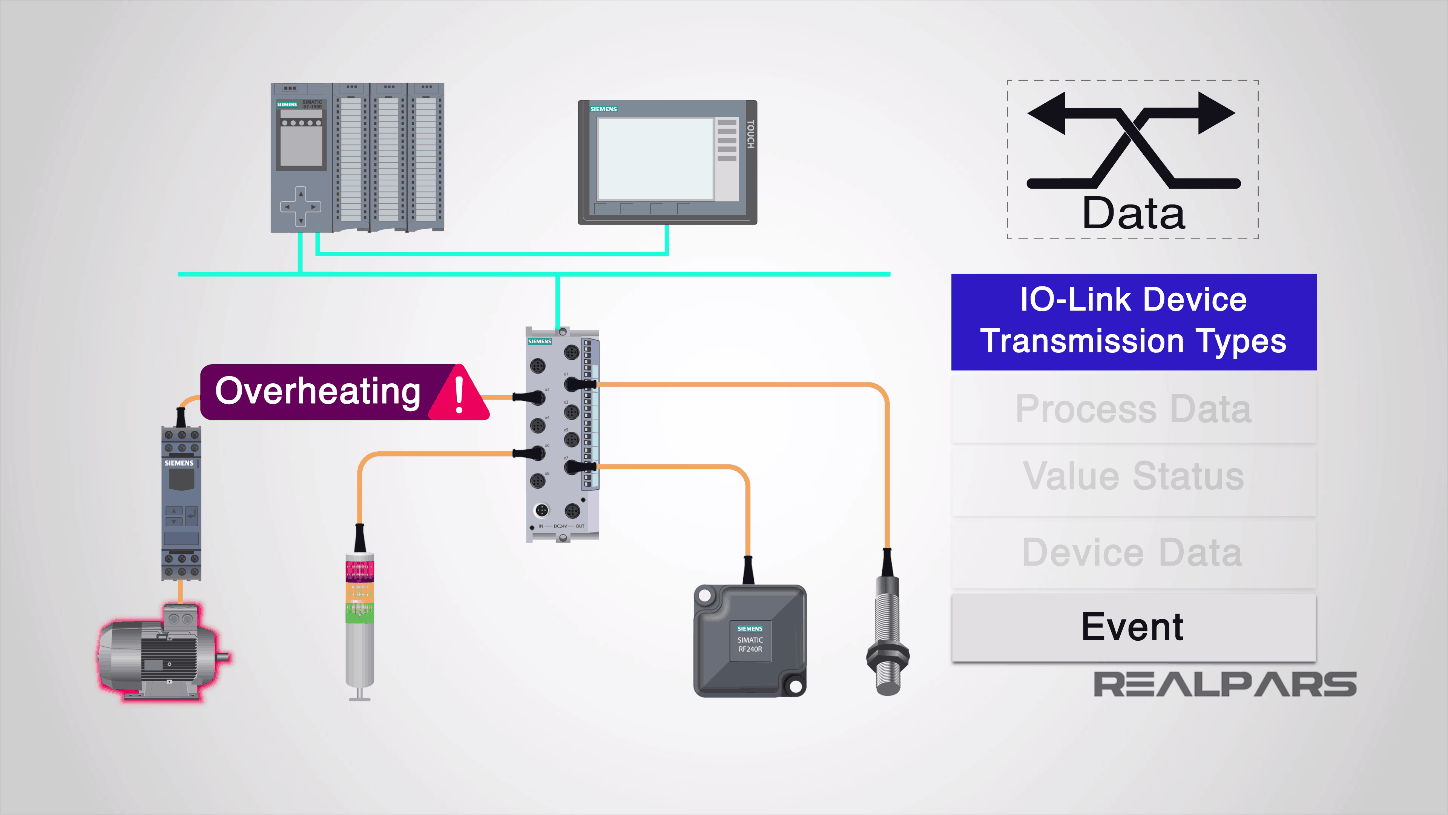
The transmission of device parameters and events occurs independently from the cyclic transmission of Process Data.
This means that they do not impact each other, so critical messages do not have to queue, until already buffered messages are sent.
Summary
So, let’s try and summarise what we’ve learned today.
IO-Link is a simple communications protocol. It is used primarily for communications to simple 3 wire sensors and actuators.
A Master has slave devices, such as an actuator or sensor, attached to it.
The Master can then communicate over a Fieldbus connection to the higher-level controller, most likely in our case, a PLC, or Programmable Logic Controller.
The ports can serve different purposes, from signaling that it is unused, to signal that it is in Input mode, Output mode or for IO-Link communication.
An IO-Link device transmits Process Data and Value Status periodically, at a regular defined interval. This is called cyclic transmission.
Device Data, such as diagnostics and Events are transmitted when they are needed. This is called acyclic transmission.
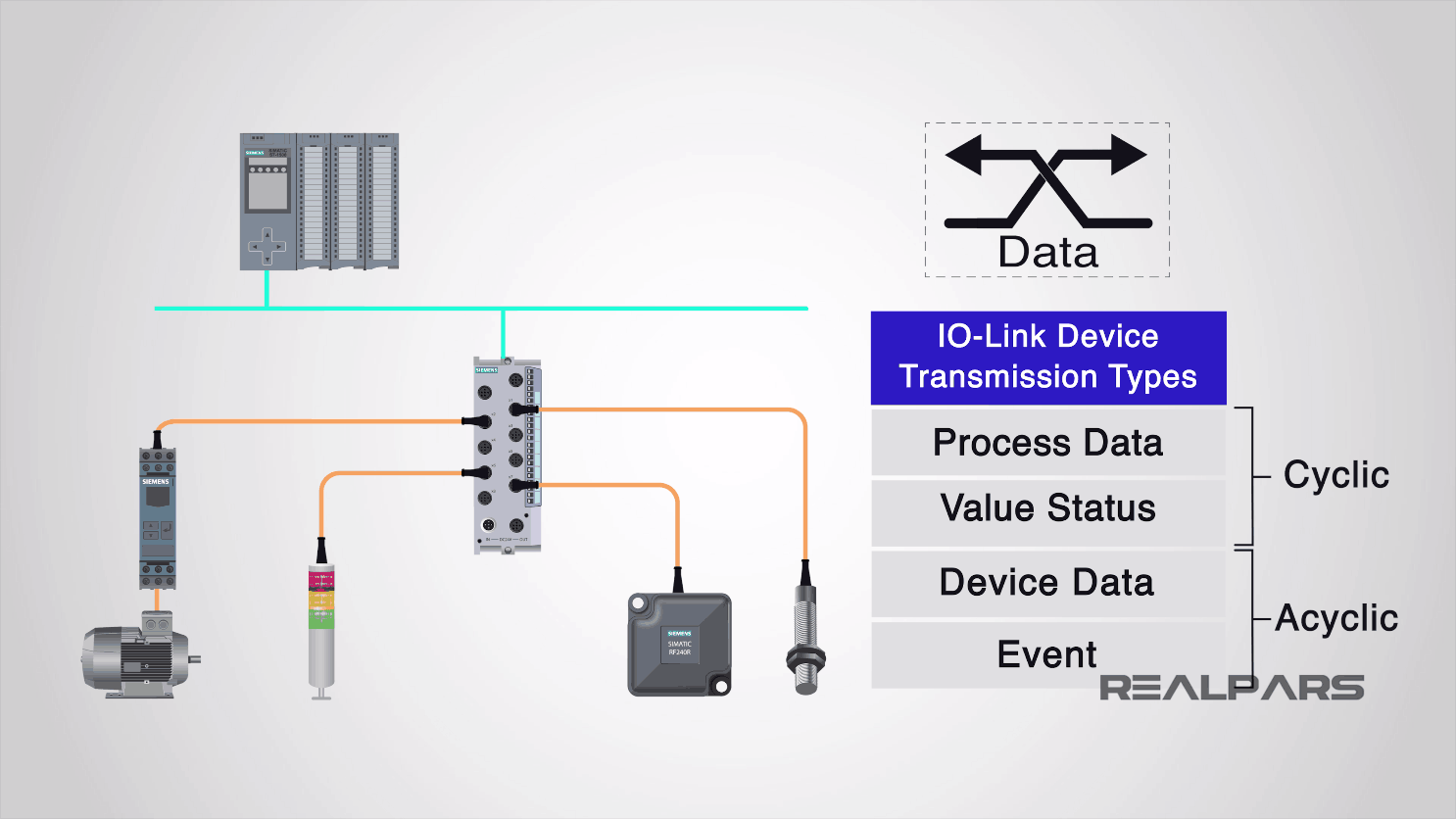
That’s it for this article! I hope you enjoyed learning about What IO-Link is.
It is a very simple communications protocol that can be quite complex to learn about!
Getting the set up of the IO-Link configuration correct is heavily dependant on the device that is being communicated with, so checking the field devices instructions is a necessity to be able to communicate correctly.
Don’t worry though, once it is set up, they are very easy to maintain, and often work seamlessly with no additional work required.
Got a friend, client, or colleague who could use some of this information? Please share this article.
The RealPars Team