In the previous article, IIoT Implementation with Omron PLCs, we presented an overview of how IIoT-ready Omron PLCs can interact with the Cloud and store and use data on SQL databases in machine processes.
We also talked about how the Omron Sysmac Platform shares data from Omron PLCs using MQTT (Message Queuing Telemetry Transport). MQTT is a very popular publish/subscribe messaging communication protocol for IoT devices allowing the exchange of data via Cloud services.
In this article, we’re going to show you an example of how product quality can be greatly improved using an IIoT-ready Omron NX102 PLC and the MQTT industrial communication protocol to track work-in-process and finished goods.
We’ll show you how several technologies and innovations combined to utilize product and process data to ultimately improve quality and production efficiency in automated product traceability.
Automation traceability process
Omron uses the term Automation Traceability to describe the product quality improvement process.
There are four steps in the Automation Traceability process. These four steps are:
1) Mark: where the serial number or lot number is placed on the product.
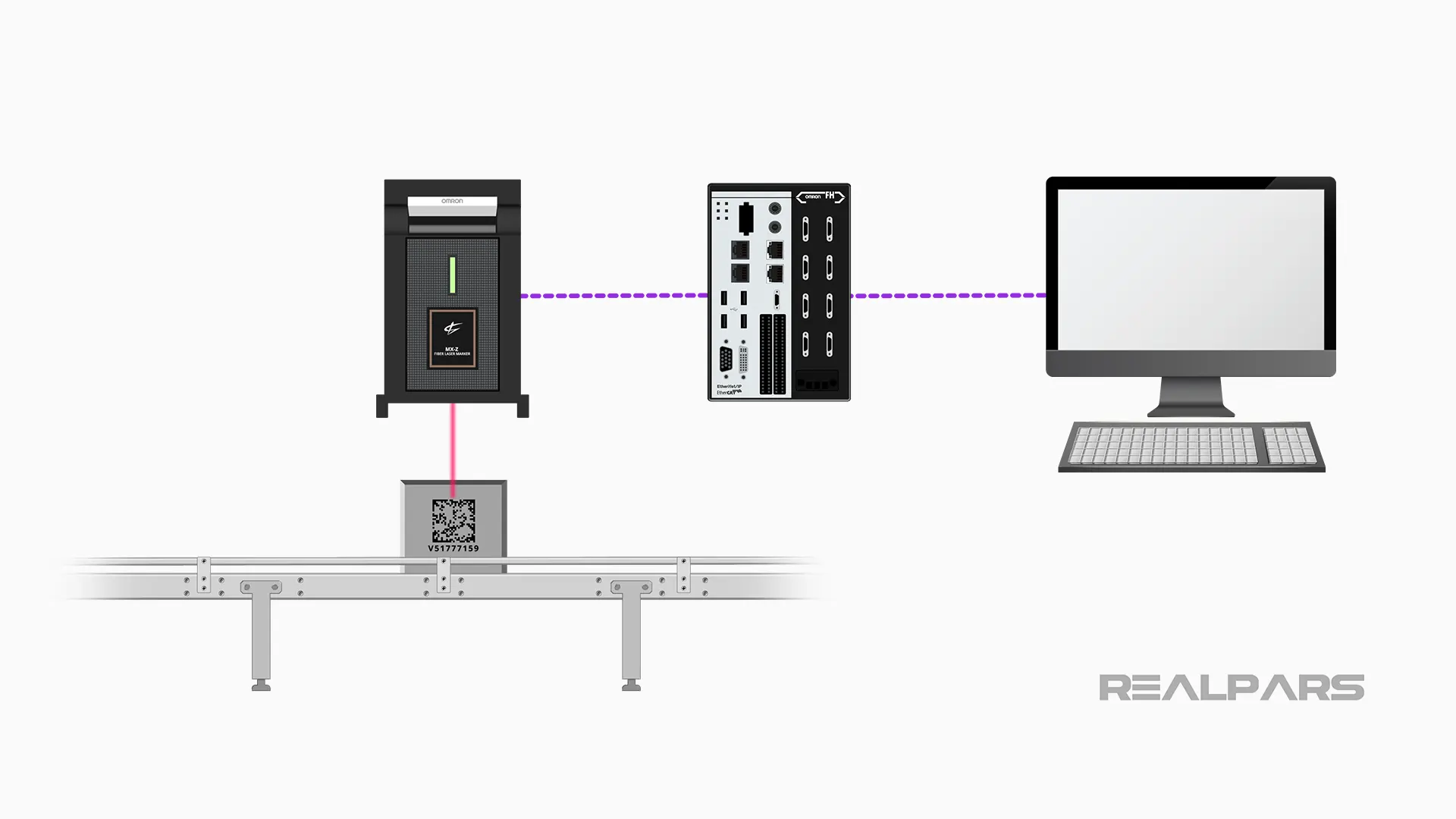
2) Verify: where the mark is confirmed to be made correctly, is readable, and complies with any additional requirements.
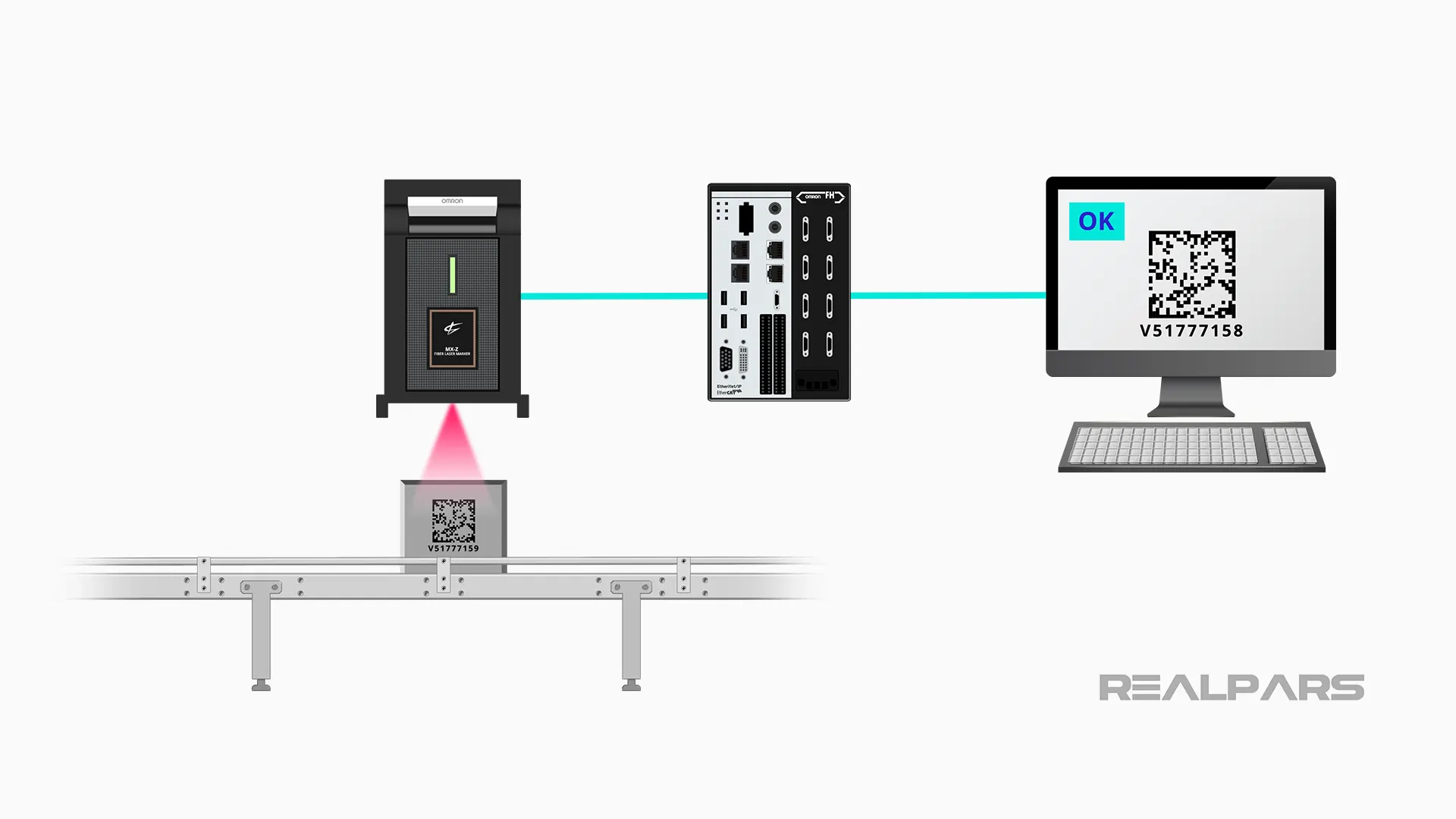
3) Read: where a vision system reads the mark to ensure proper routing and shipment.
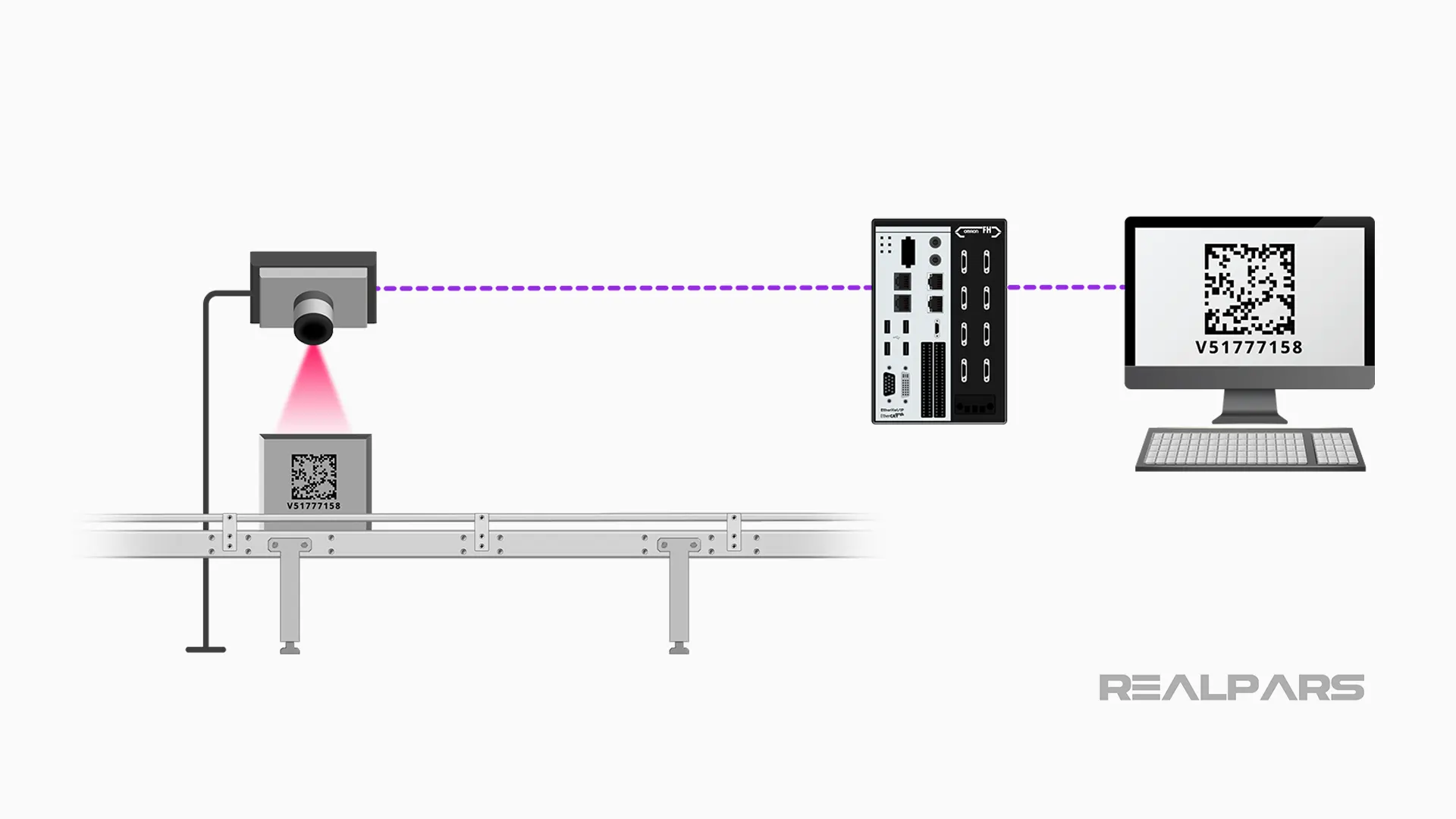
4) Communicate: this step involves incorporating the IIoT. The part mark details are sent to a local database or a Cloud-based resource.
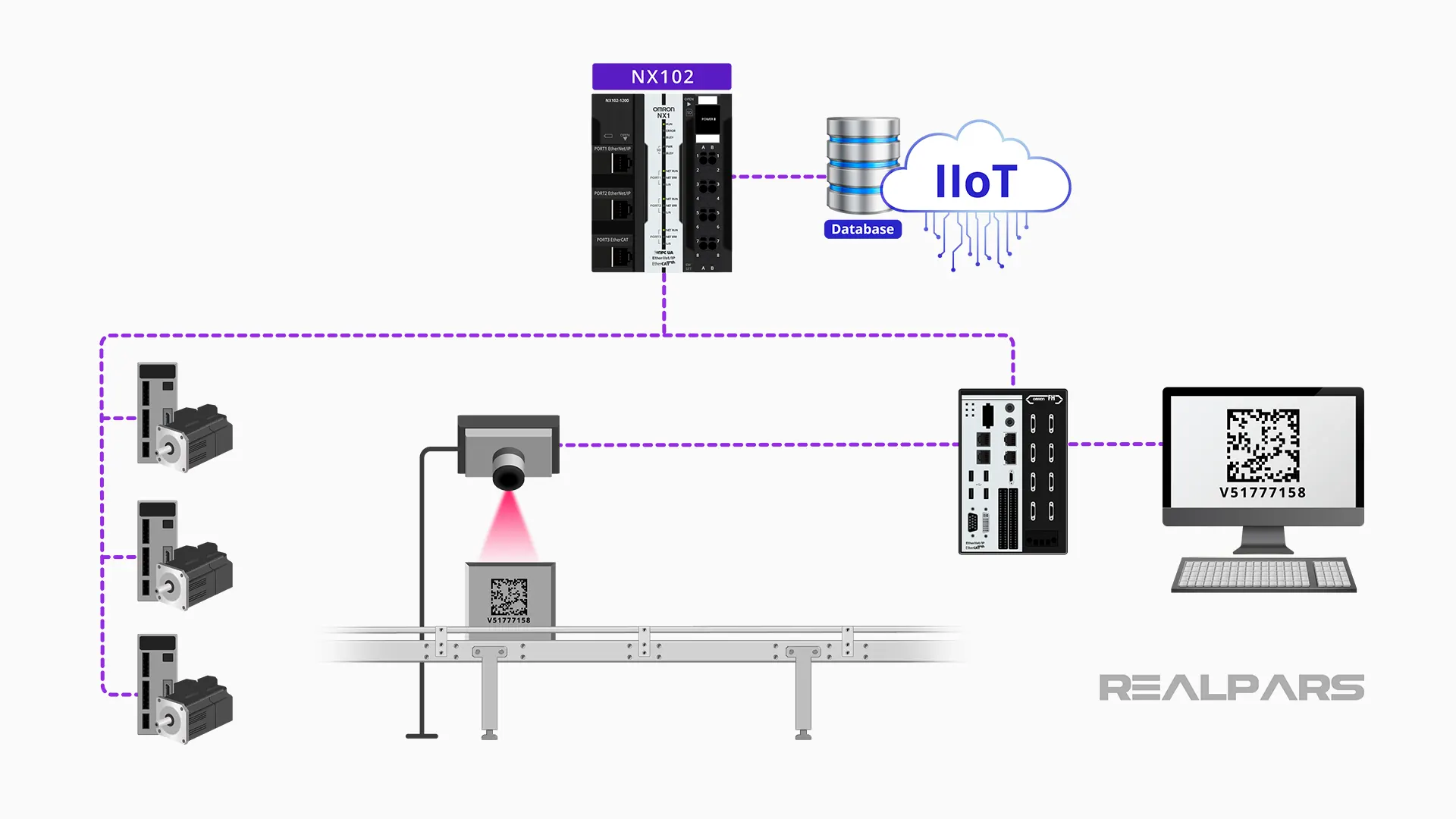
Product quality improvement example
Ok… Let’s get the product line rolling… Our product is a machined aluminum block that is to be further modified at a later stage in the overall process.
We have several of these machined blocks moving along on a conveyor. Each of these blocks is marked with a 2D matrix code.
One of the several markers available is the Omron MX-Z20xxH series of laser markers. This marker provides permanent identification using 1D or 2D codes.
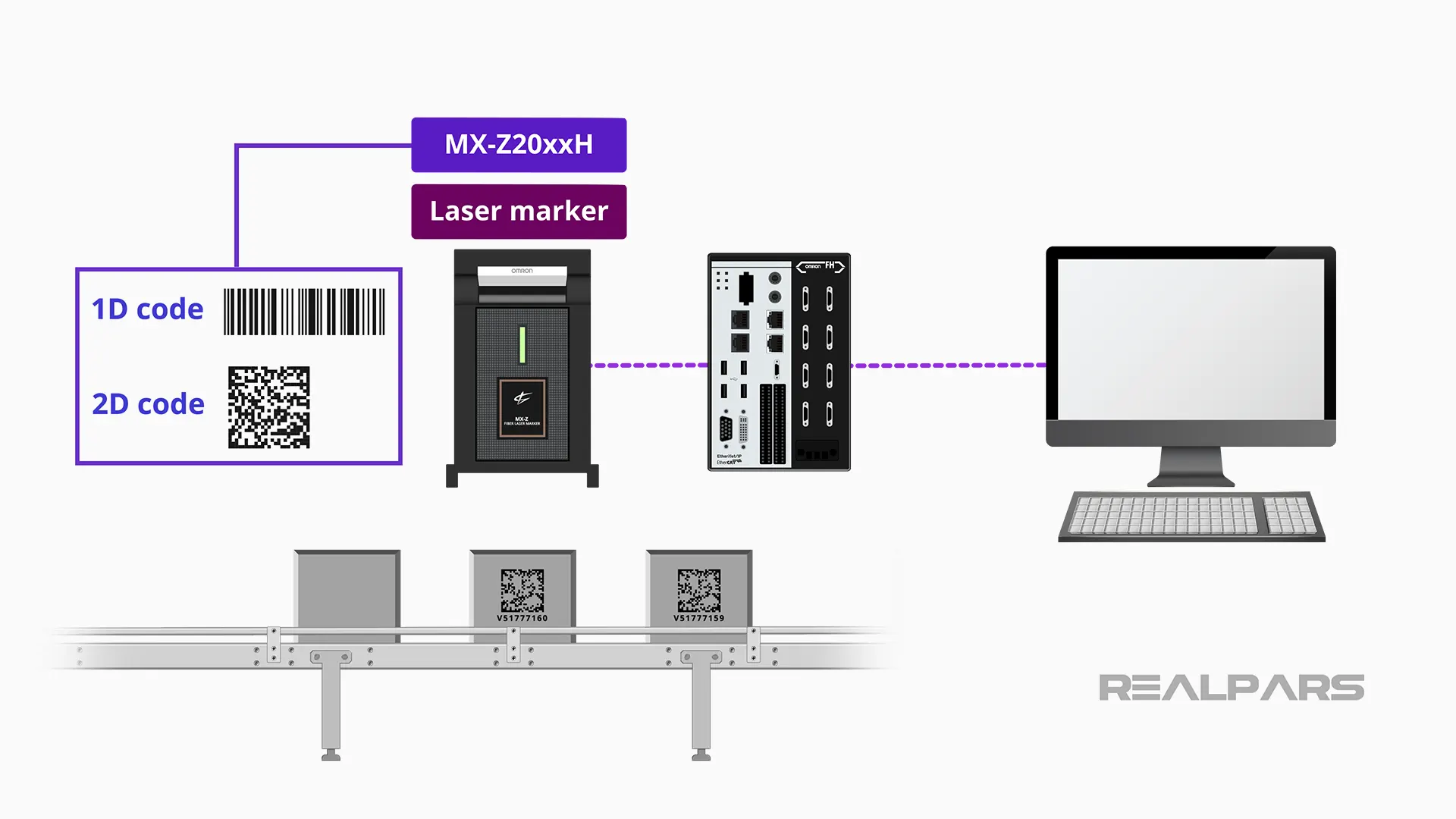
The Omron’s NX102 controller sends motion control signals via an EtherCAT network to an Omron G5 Servo System that drives the conveyor.
As the aluminum blocks move along on the production line, the Servo system sends position data back to the NX102 controller.
The controller then determines a time to trigger the camera and then sends a trigger signal to the Omron FH 5050 Vision system when required.
The vision system triggers the camera and the strobe light and the camera image is passed back to the vision system.
The FH-5050 processes the image and decodes the 2D code. Once the 2D mark has been decoded, the code value is sent back to the NX102 controller.
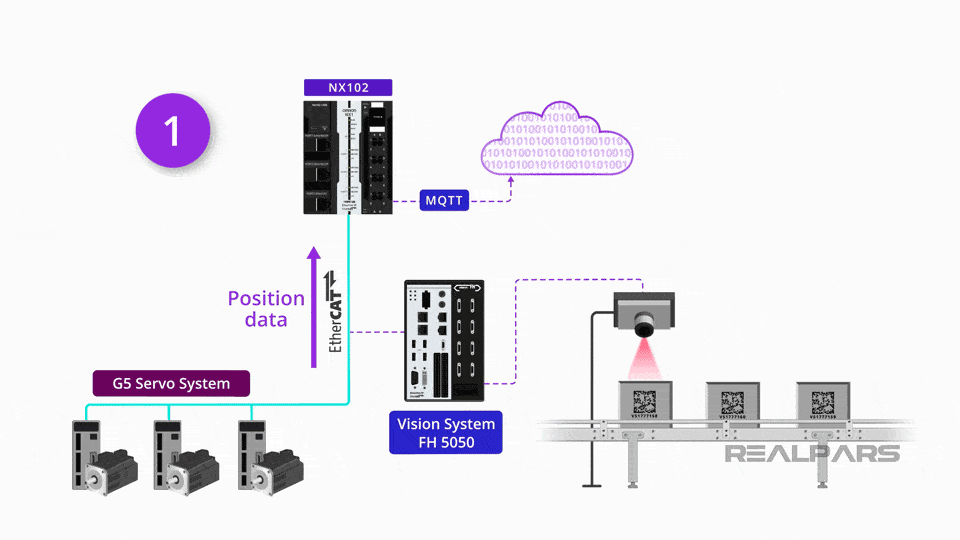
Cloud computing
OK… now it’s time to access Cloud resources. The NX102 controller sends the decoded data to the cloud using the MQTT protocol.
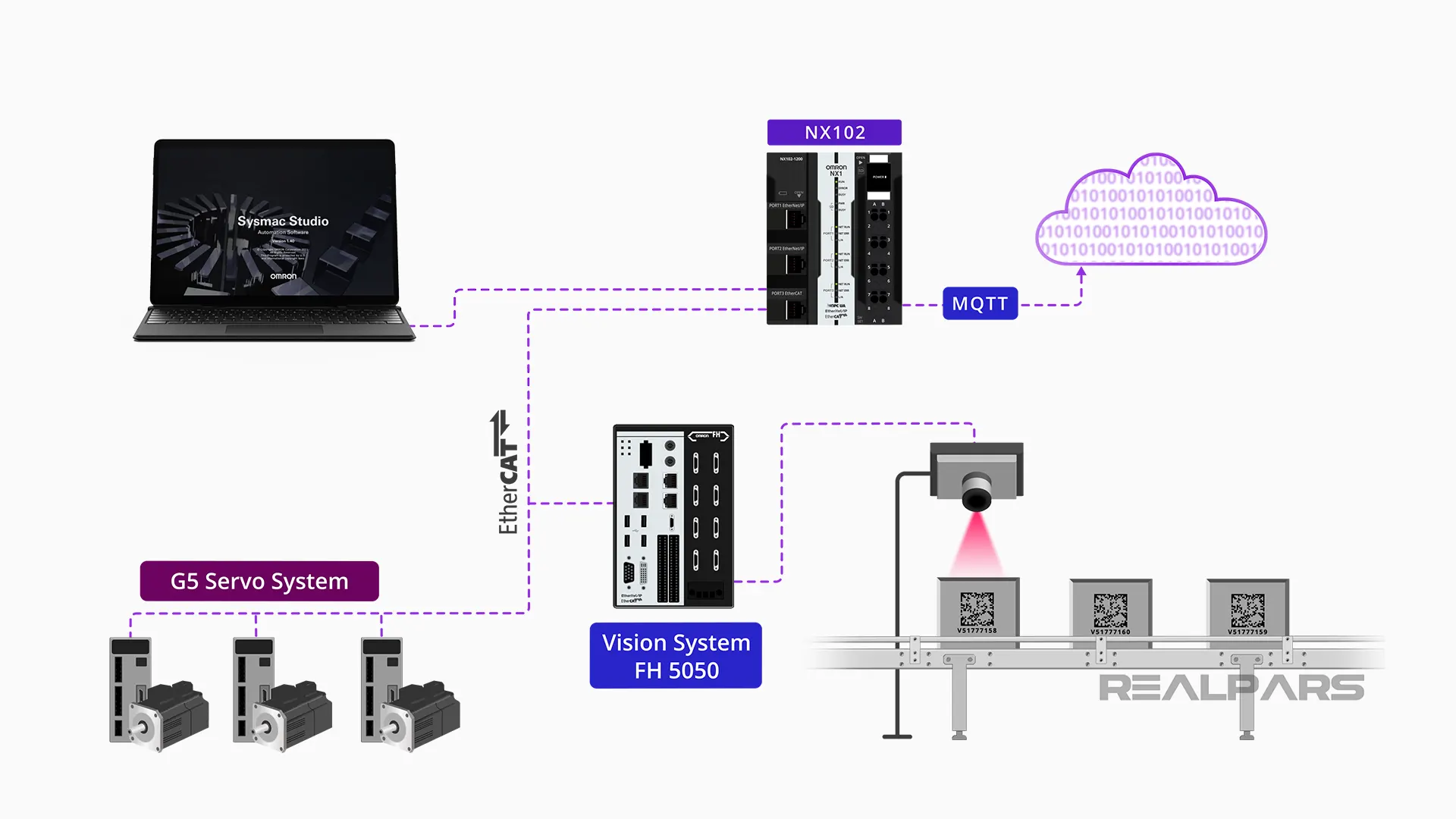
In the second article of this series, IIoT Implementation with Omron PLCs, we discussed the MQTT protocol in detail.
All of these Omron devices and processes can be programmed and monitored using Omron’s Sysmac Studio software.
An HMI communicating over EtherNet/IP is easily added offering an operator interface if desired.
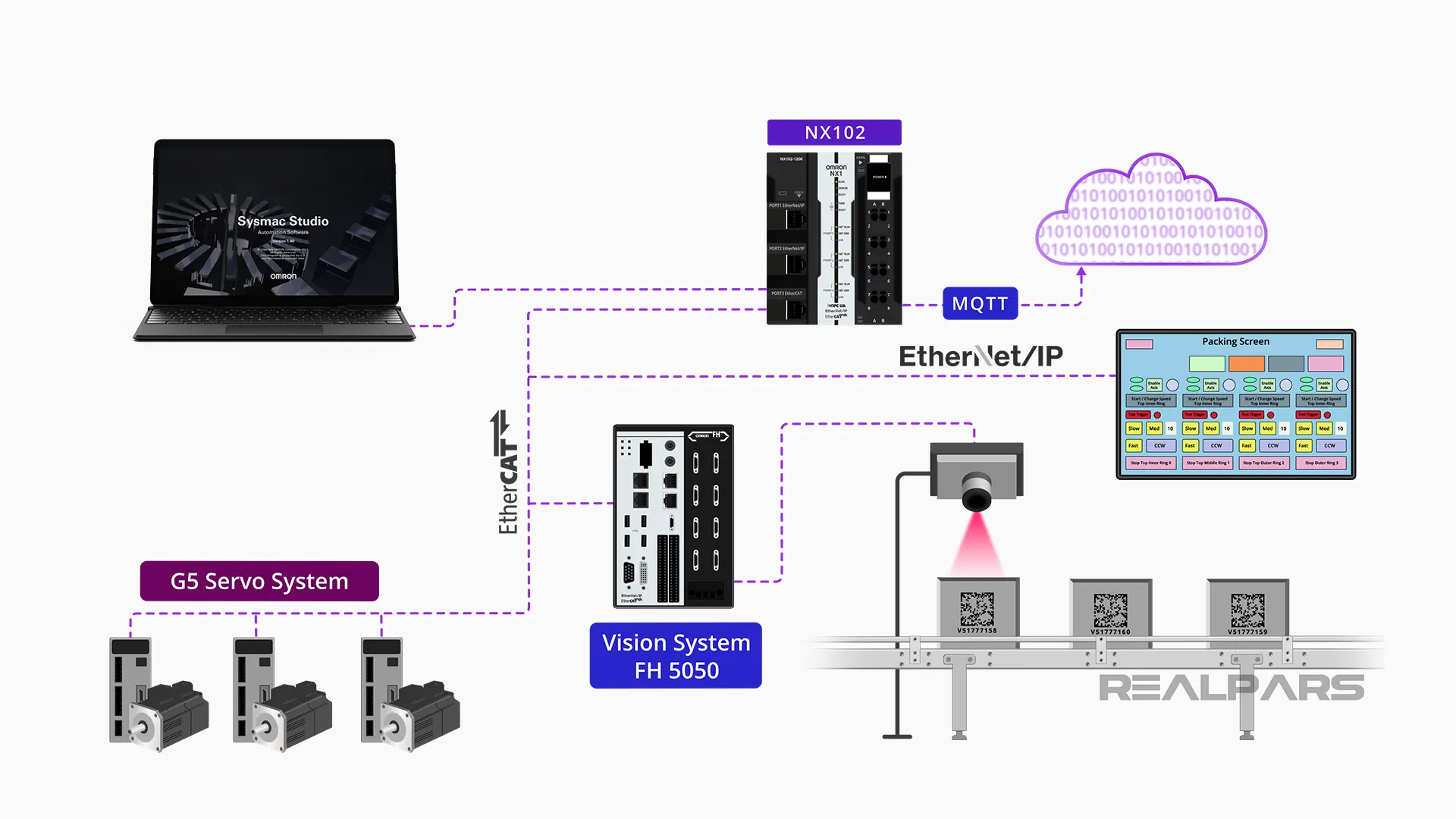
This is just one example of where these technologies can be applied.
Applications
A typical application for a system like this is individual product piece traceability in high-volume, high-mix production environments where there are lots of production lines at several locations.
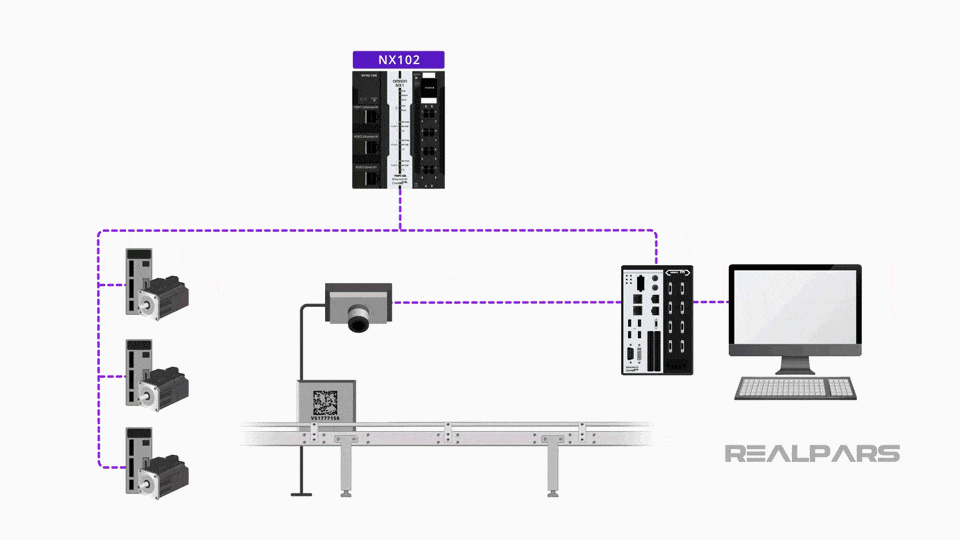
The ability to quickly access and analyze this kind of unit production data is critical to many industries.
With this level of detail and real-time analysis, it means that only the products with that specific lot number or serial number range would need to be discarded if defects are detected.
An obvious bonus with a Traceability system like this is the Omron controller’s ability to take advantage of the cloud.
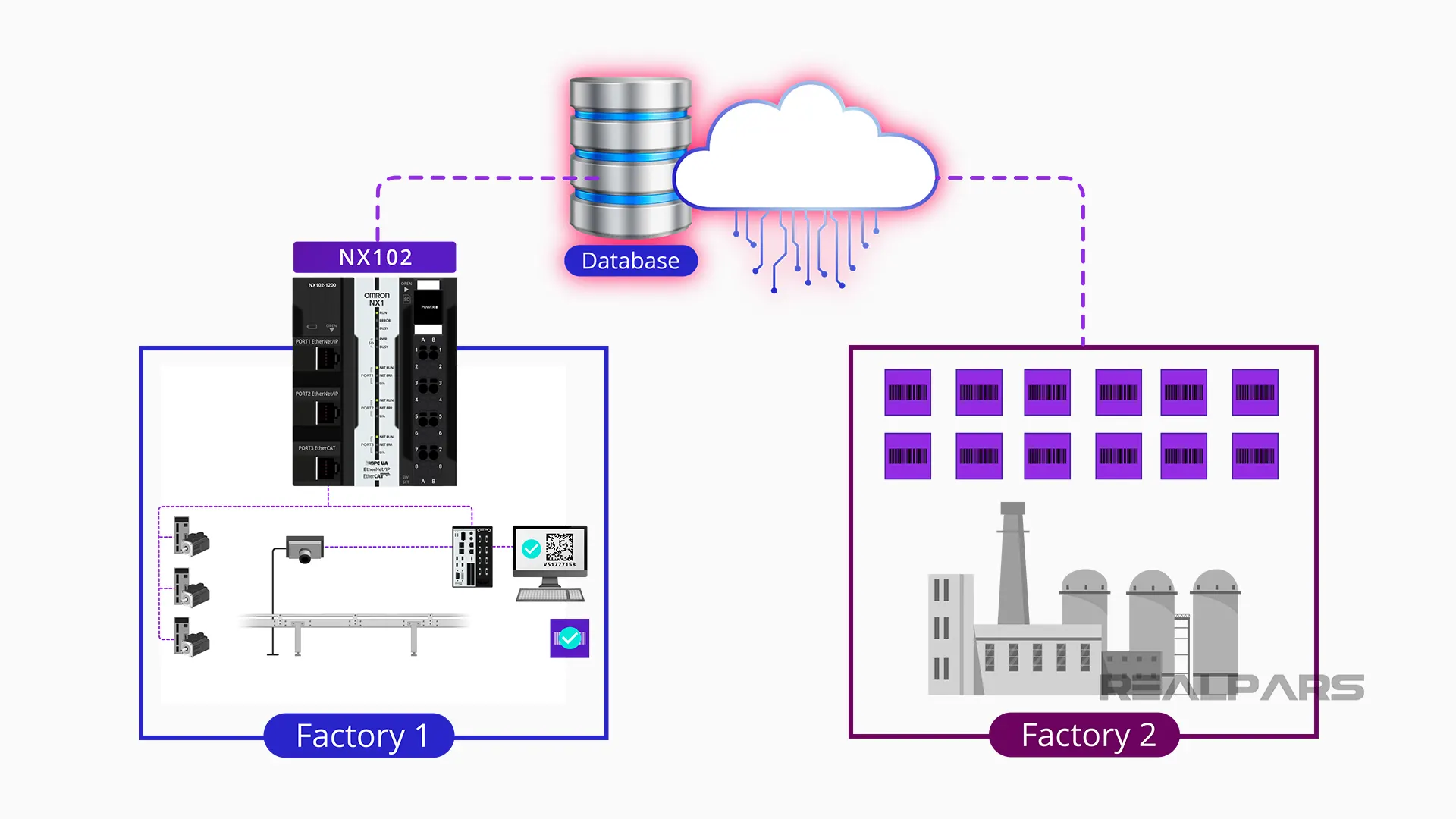
The ability to get information scanned at the point of origin and then become immediately available for analysis using cloud services makes the Omron controller very attractive.
The NX102 controller creates a direct connection between the system and the cloud or any local database.
Summary
Ok… let’s review what we have discussed.
– The Omron NX series of PLCs have the ability to perform real-time analysis and easily operate and control a Product Traceability System.
– The Omron NX102 controller can accomplish data sharing using MQTT messaging communication via the powerful Sysmac Studio programming software.
– Sysmac Studio is the Machine Control & Factory Automation software used for programming the NX series of PLCs.
– In our example, we discussed the four required steps in the Automation Traceability process. Using a number of other Omron products together with the NX102 PLC and Sysmac Studio accomplished the following four steps:
– Mark: The serial number or lot number is placed on the product.
– Verify: The mark is confirmed to be made correctly, is readable and complies with any additional requirements.
– Read: A vision system reads the mark to ensure proper routing and shipment.
– Communicate: The part mark details are sent to a local database or a Cloud-based resource using the IIoT.
If you have any questions about the Omron PLCs or about IIoT, add them in the comments below and we will get back to you in less than 24 hours.
Got a friend, client, or colleague who could use some of this information? Please share this article.