In this article, we’re going to introduce you to a very popular Distributed Control System, the Yokogawa DCS Centum VP.
DCS basic structure and components
Before we dig into the Yokogawa Centum VP, let’s have a quick look at the basic structure and components of a typical DCS.
By definition, a DCS is a computerized control system with multiple autonomous controllers that operate and control many control loops. A DCS has no centralized supervisory control, and thus the name Distributed Control.
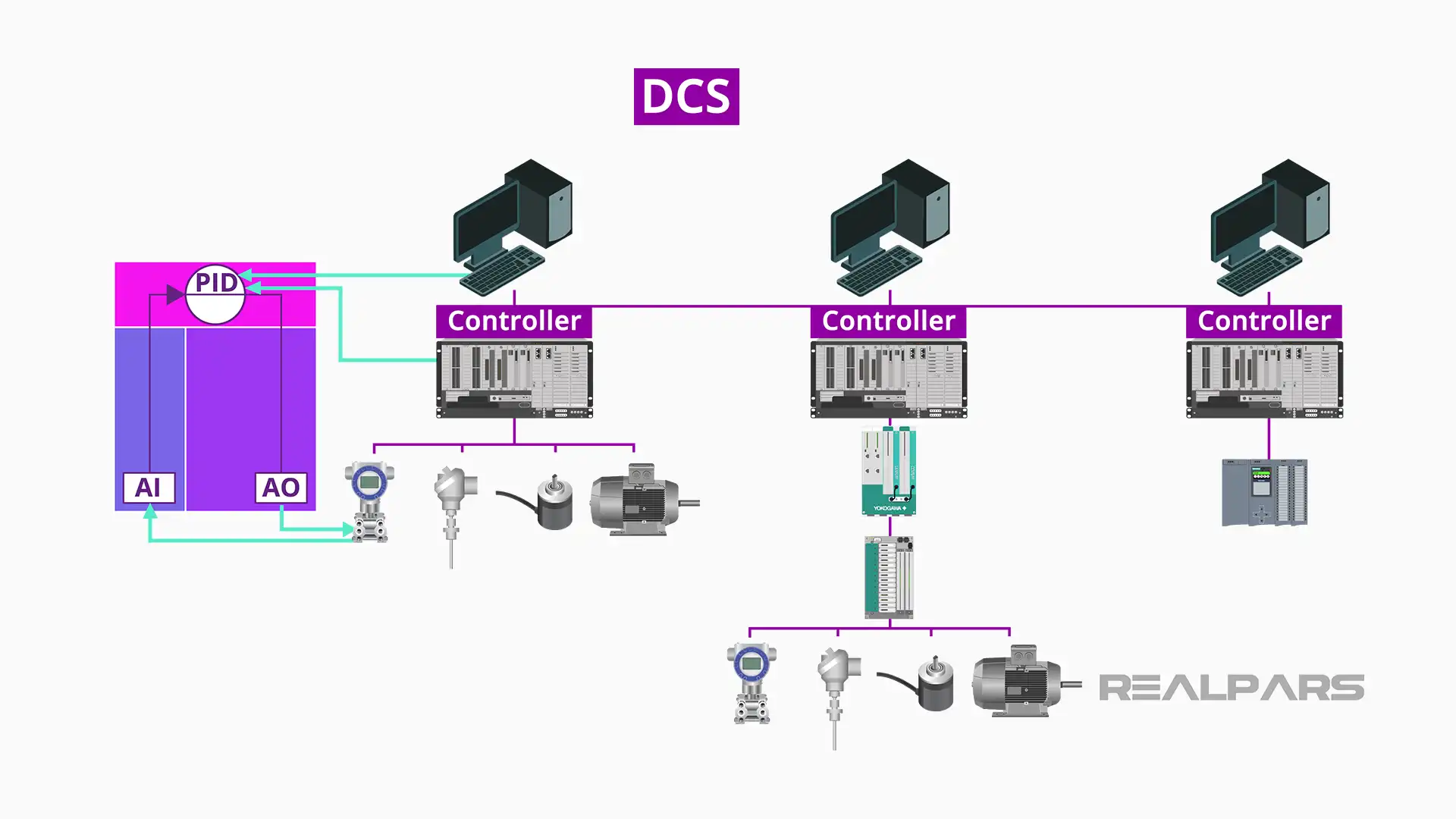
Field devices are connected to I/O modules located in cabinets alongside Controllers. The controllers are networked using many communication protocols such as Ethernet, Modbus, or a proprietary protocol.
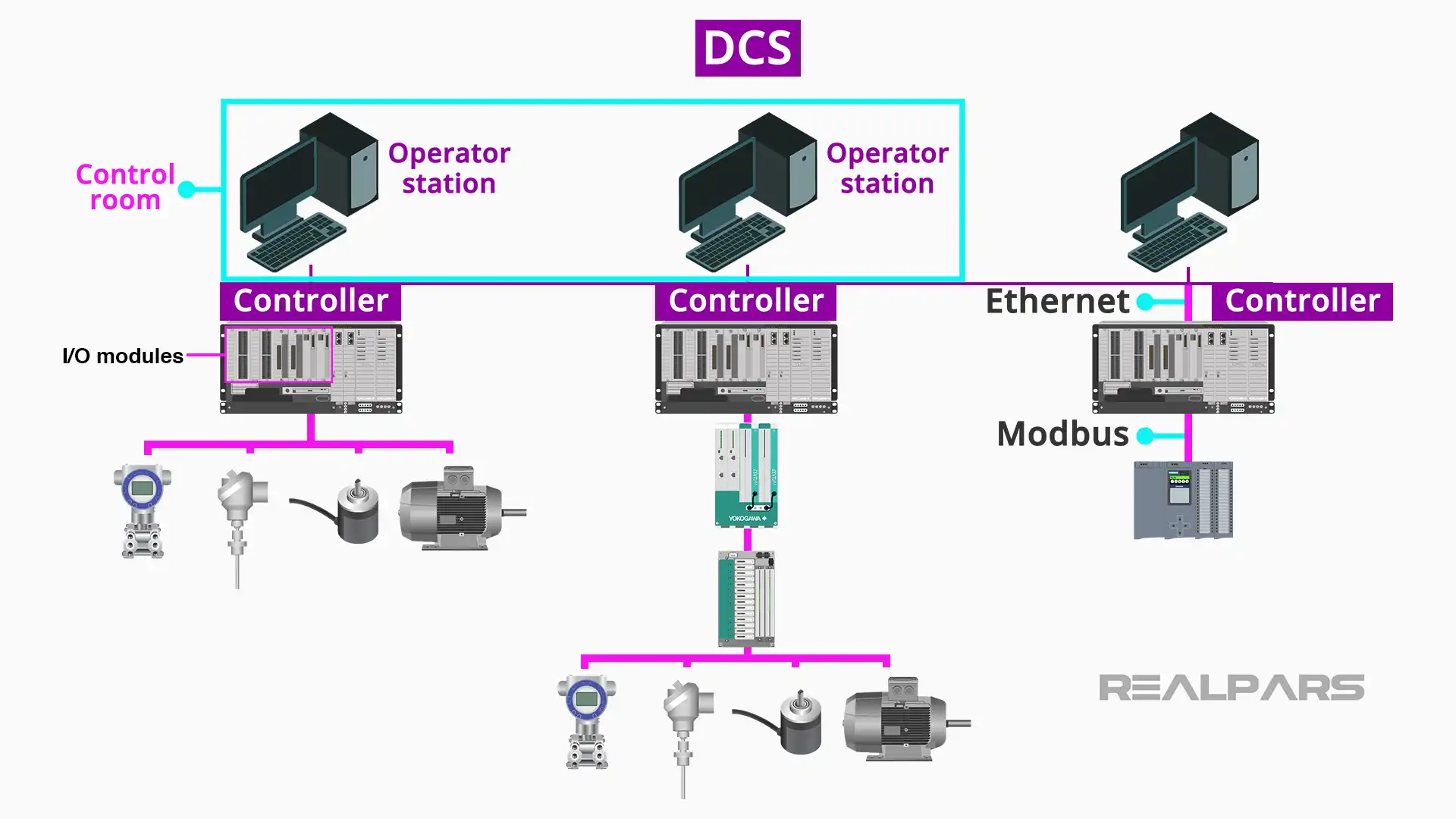
There are Operator stations HMI’s located in a centralized control room, or some may be located elsewhere. The Operator stations provide access to plant operators to observe and adjust real-time plant conditions.
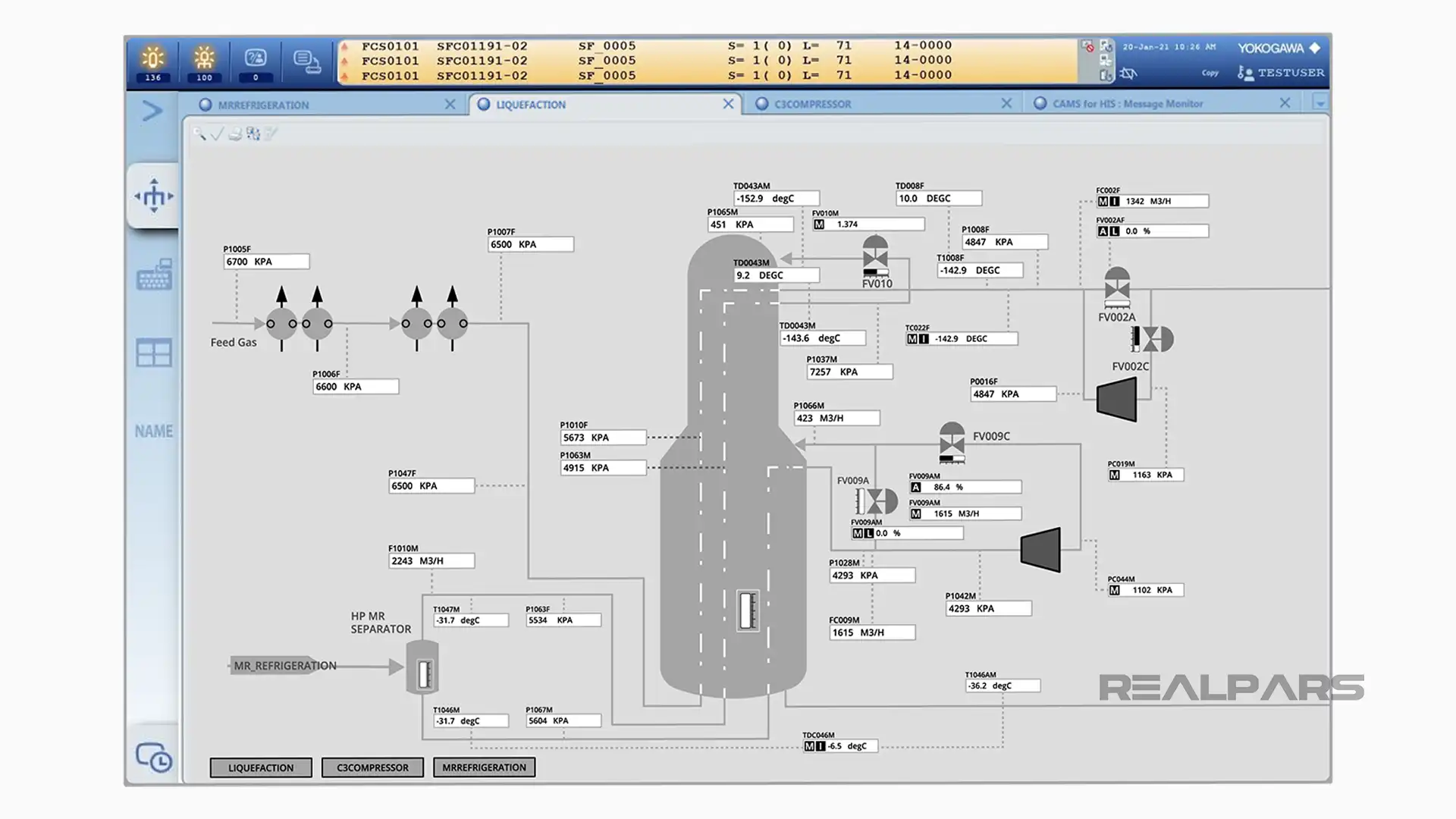
An Engineering station HMI is located in an area only accessible for actual control logic programming changes for any of the many control loops.
Yokogawa history
Yokogawa is a Japanese industrial company that started with the manufacture and sales of electric meters in 1915.
Yokogawa introduced its first CENTUM DCS in 1975. Centum V and Centum-XL followed in the 1980s. CENTUM CS and CS 3000 were introduced in the 1990s.
The CENTUM CS 3000 line continued in the 2000s which was also the decade where the ProSafe-RS SIS was introduced.
The 2010’s decade introduced us to CENTUM VP. The current version is Release 6 which was introduced in 2014.
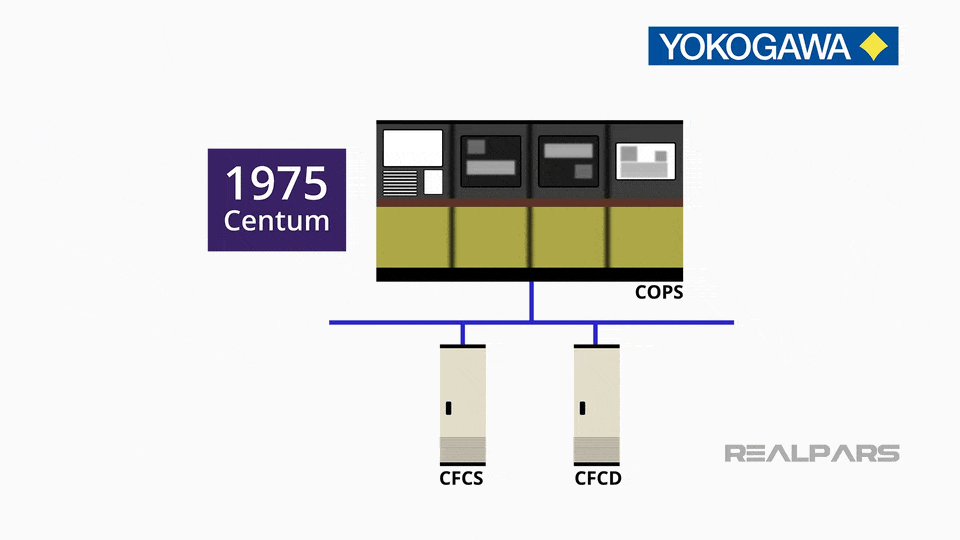
Centum VP system architecture
Ok… Let’s have a look at the overall system architecture of the CENTUM VP. Yokogawa refers to an HMI as a HIS (Human Interface Station). A HIS is mainly used for Operations, but additional stations can also be configured for Engineering.
The Field Control Station (FCS) provides the actual plant process control. All process information is placed on the control network called Vnet/IP.
All CENTUM devices are connected to the Vnet/IP network. If required, an SIS called ProSafe-RS is also installed and connected to the Vnet/IP network.
The unified gateway station (UGS) acts as an interface, allowing CENTUM VP to communicate with a variety of network-based subsystems such as Modbus RTUs, Modbus/TCP units, EtherNet/IP units, and others.
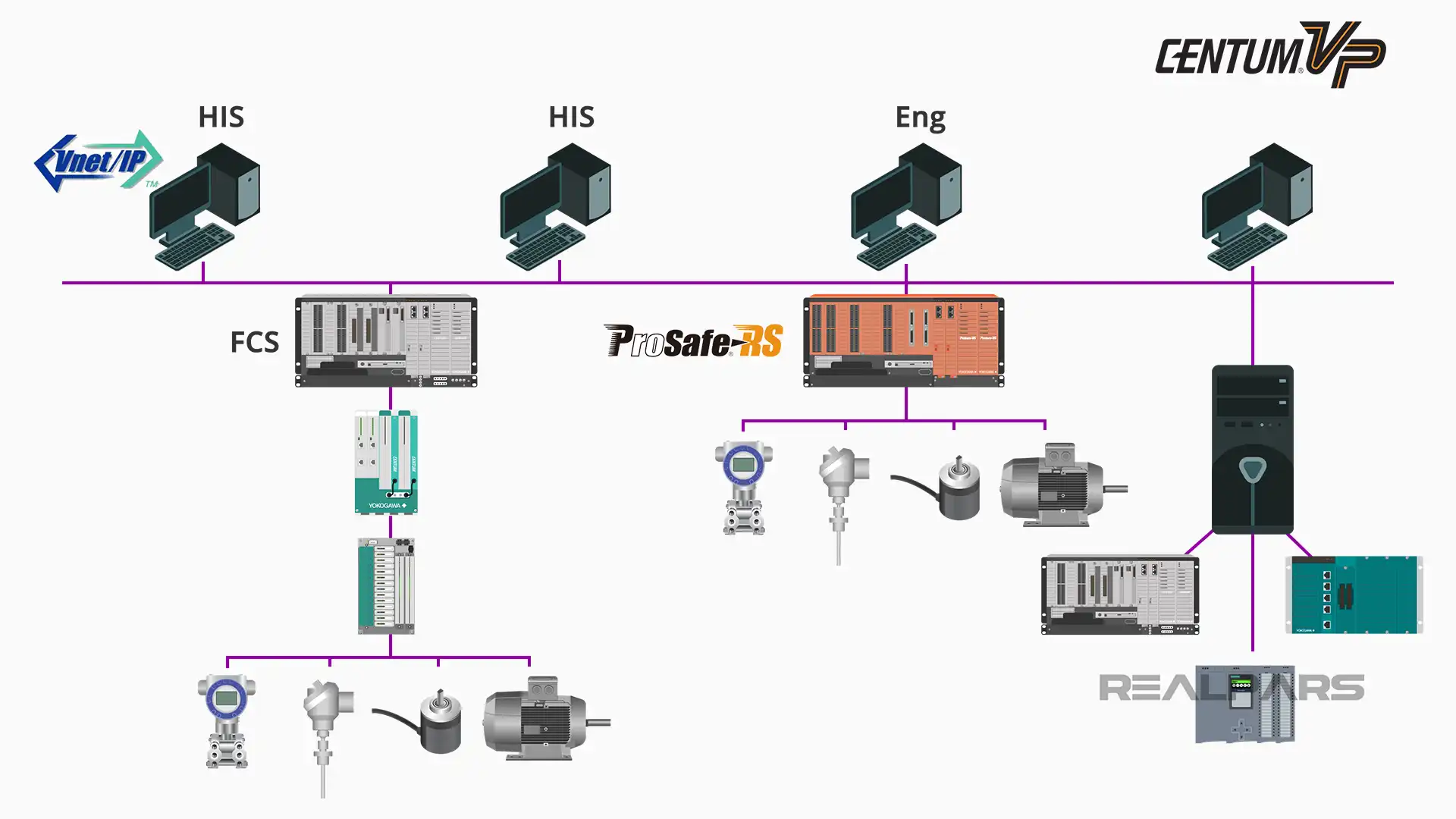
Yokogawa DCS network structure
Network switching is performed by layer switches. For example, L2SW is a layer 2 switch. Vnet/IP transmission media can be fiber optic or Unshielded Twisted Pair cables. Vnet/IP operates at a communication speed of 1 Gbps.
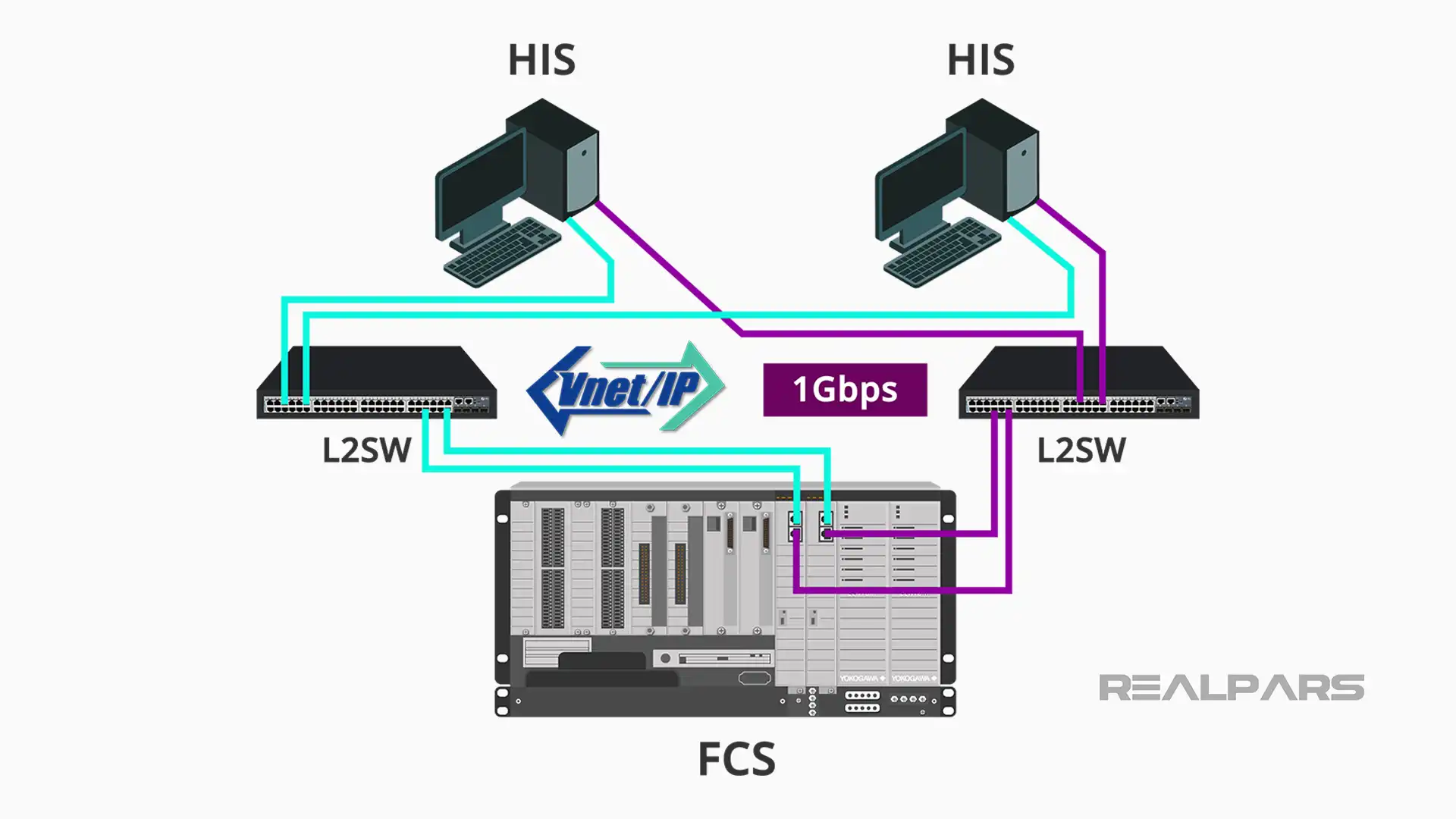
A closer look at the Vnet/IP domain shows us two separate subnets of bus 1 and bus 2. Each domain can have 64 stations. An L3SW switch is used for communicating between the two domains.
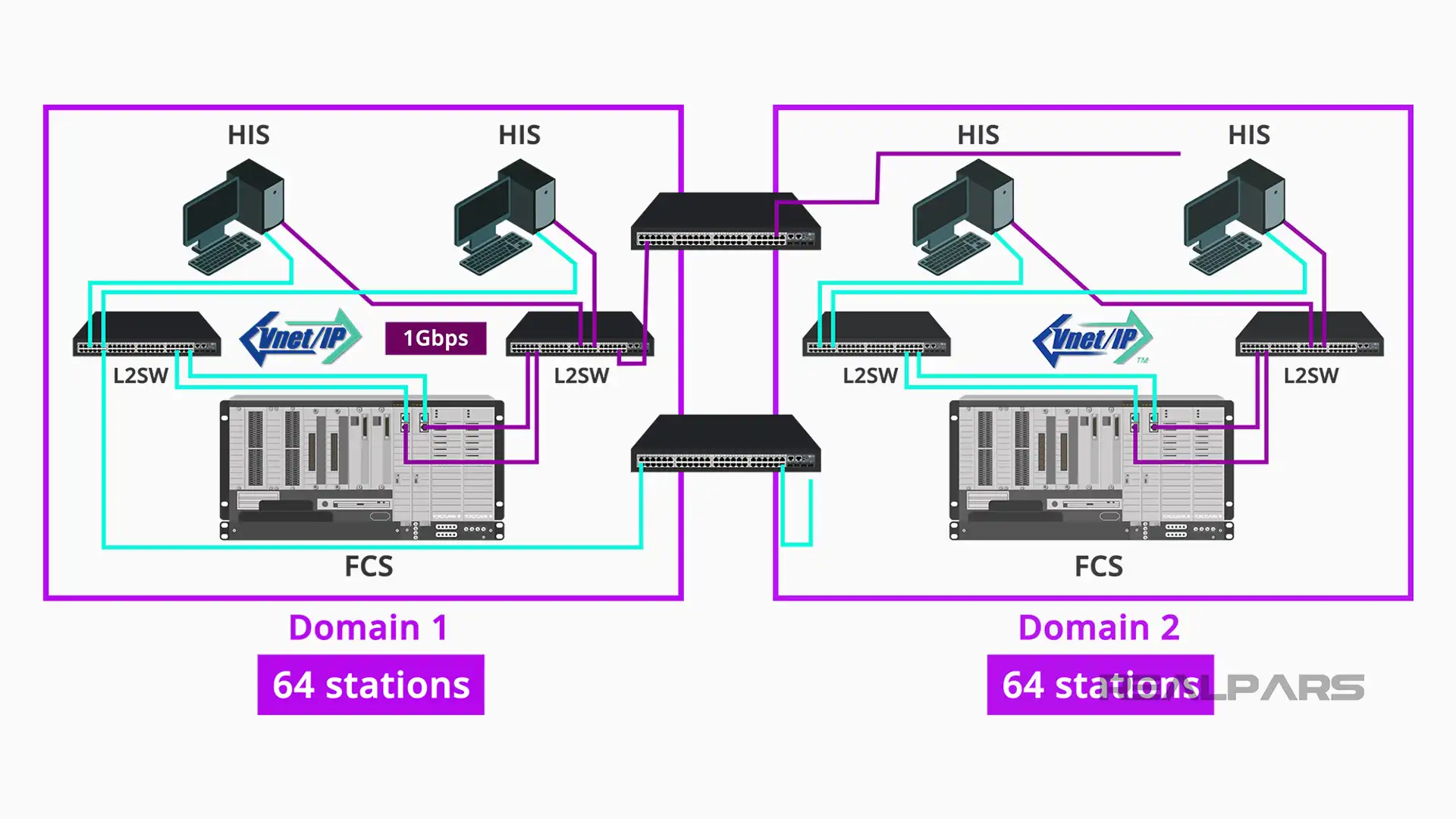
A Field Control Station (FCS) contains the Power Supply, Controller, and the Field Input/Output modules (FIO).
The I/O Modules include Analog, Digital, and Communication Modules. For example, the Analog Module AAI143 is a 4 to 20mA, 16 channel Isolated module.
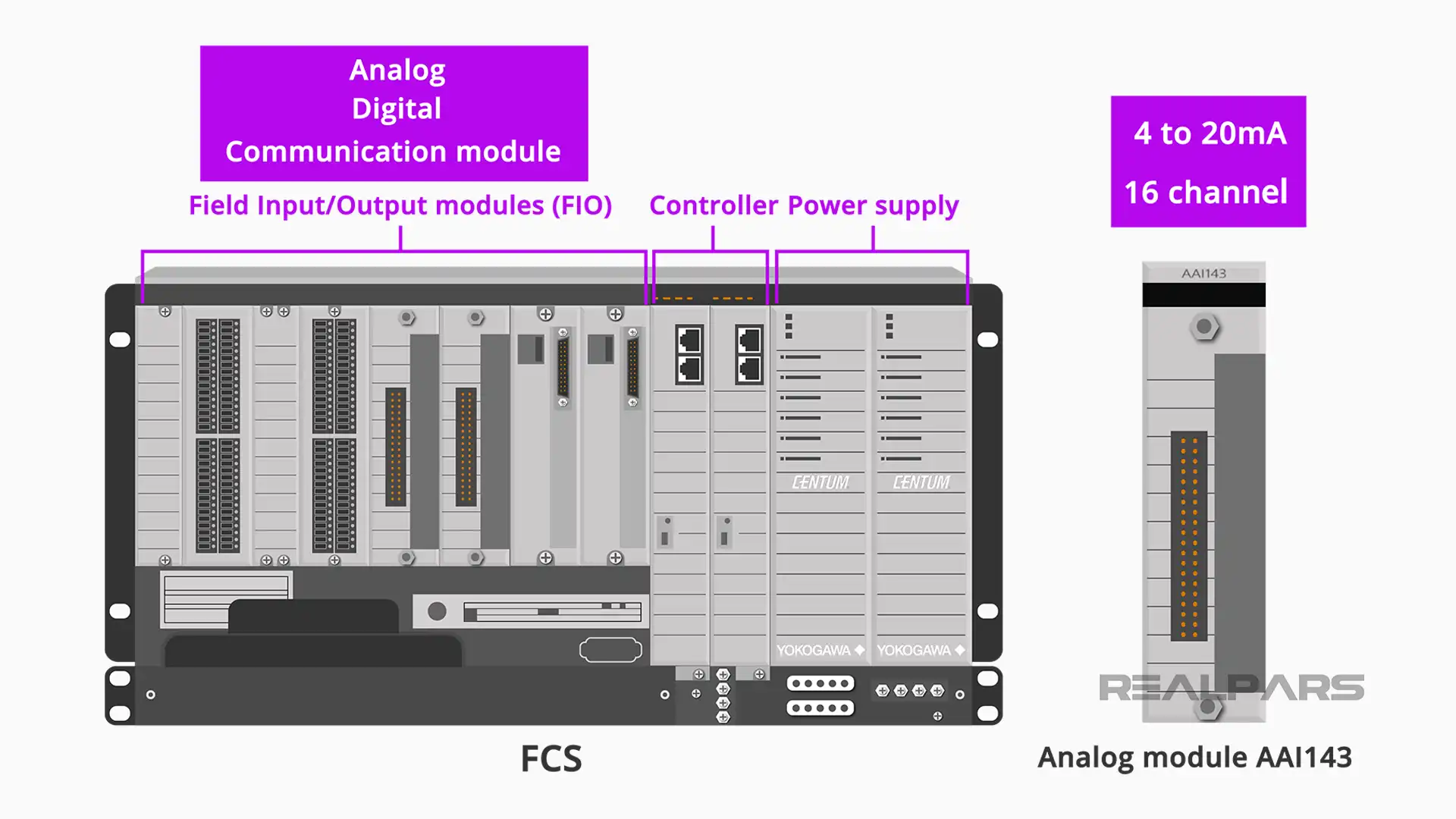
Optical node interface units (NIU) can be connected via communication modules in the Field control Unit (FCU) and do not require a switch.
The Node Interface Unit will also be connected to I/O modules or what we call NIO which stands for Network Input/Output.
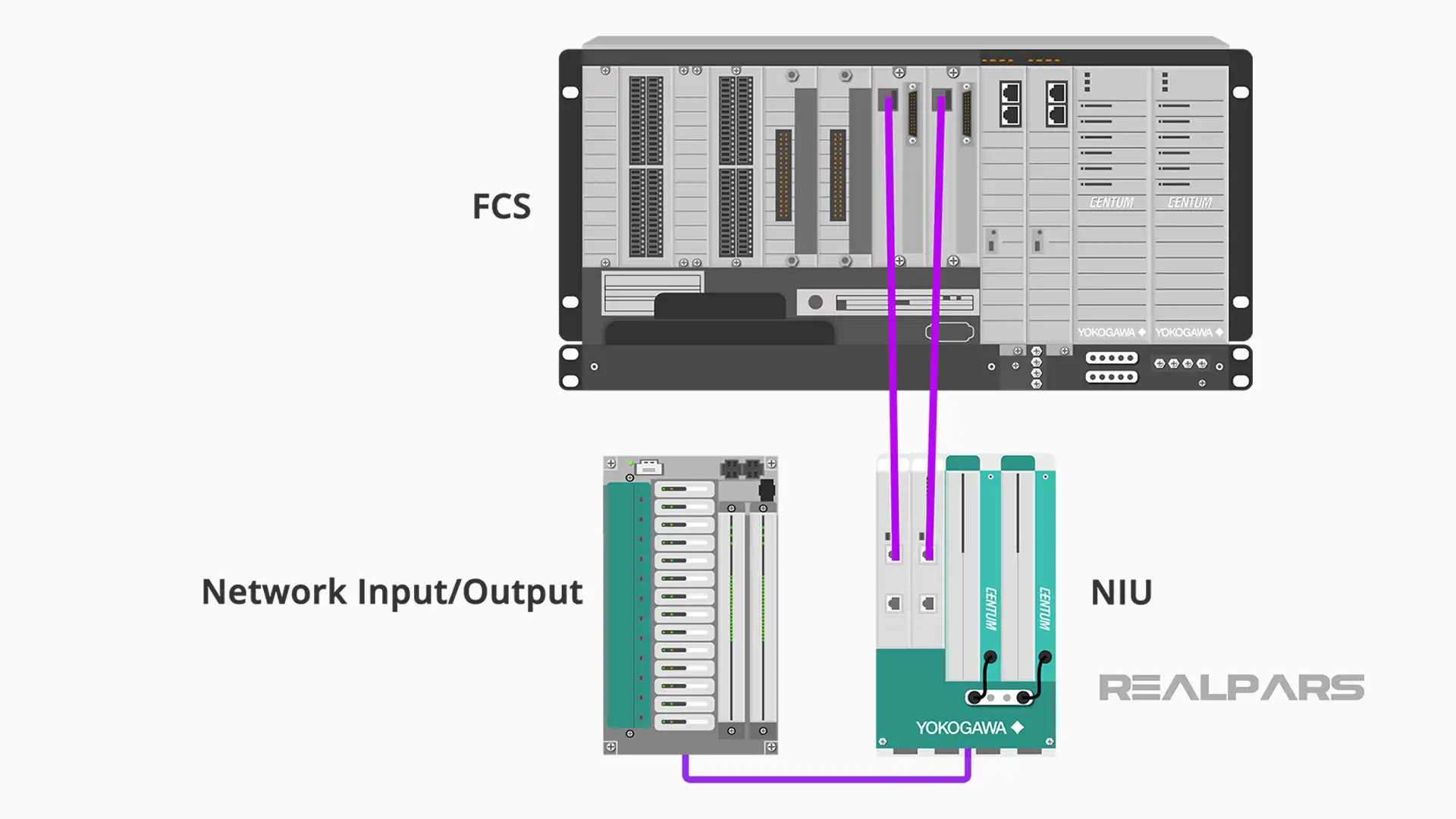
ProSafe-RS is a safety instrumented system (SIS) conforming to Safety Integrity Level SIL3 as defined by IEC 61508.
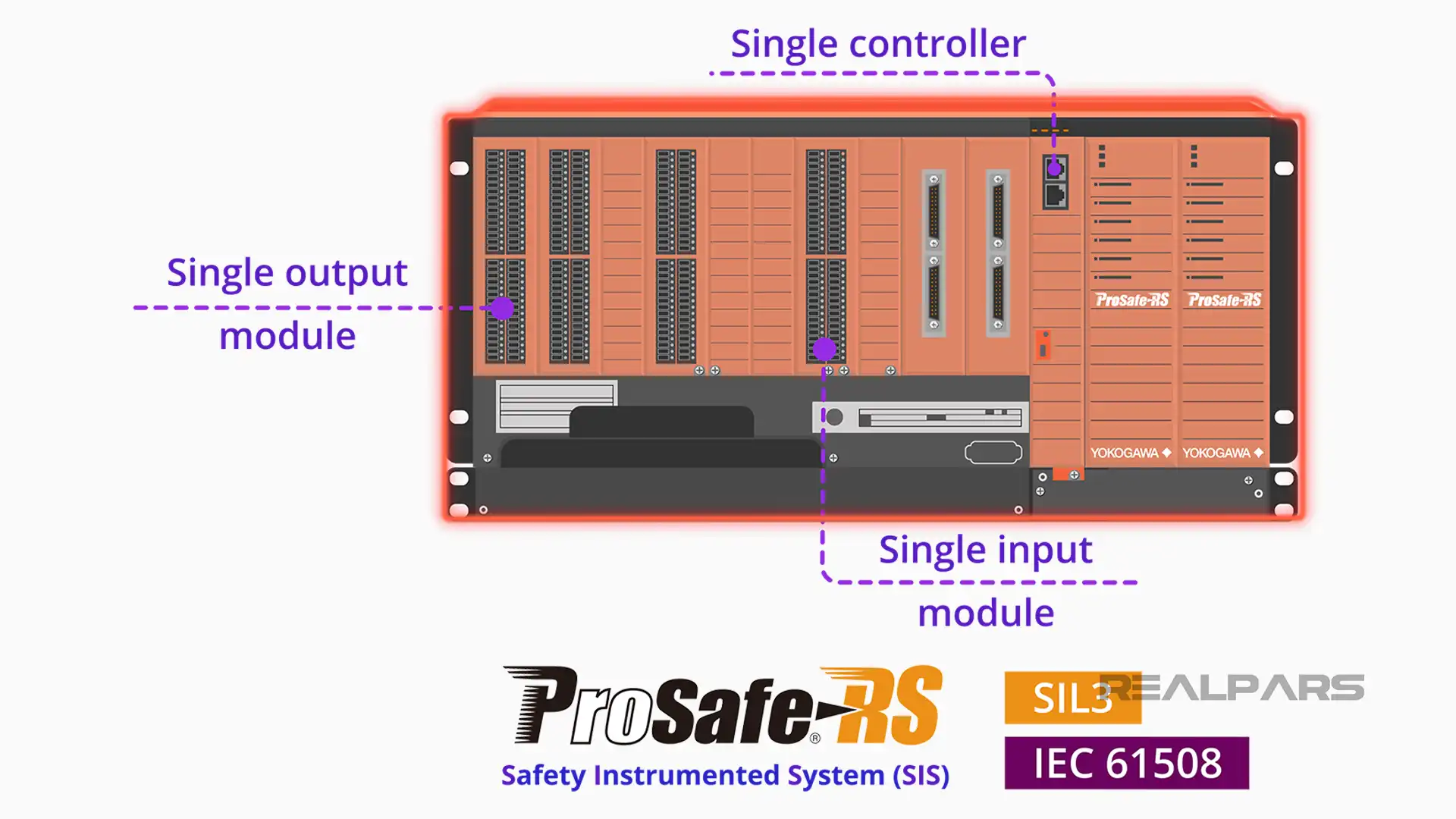
It is so rated with a single controller, single input, and single output module. All components of the ProSafe-RS system are a bright orange color.
The Plant Resource Manager (PRM) is the Asset Manager software package. PRM allows the use of diagnostic capabilities of smart devices like those with HART or Profibus communication.
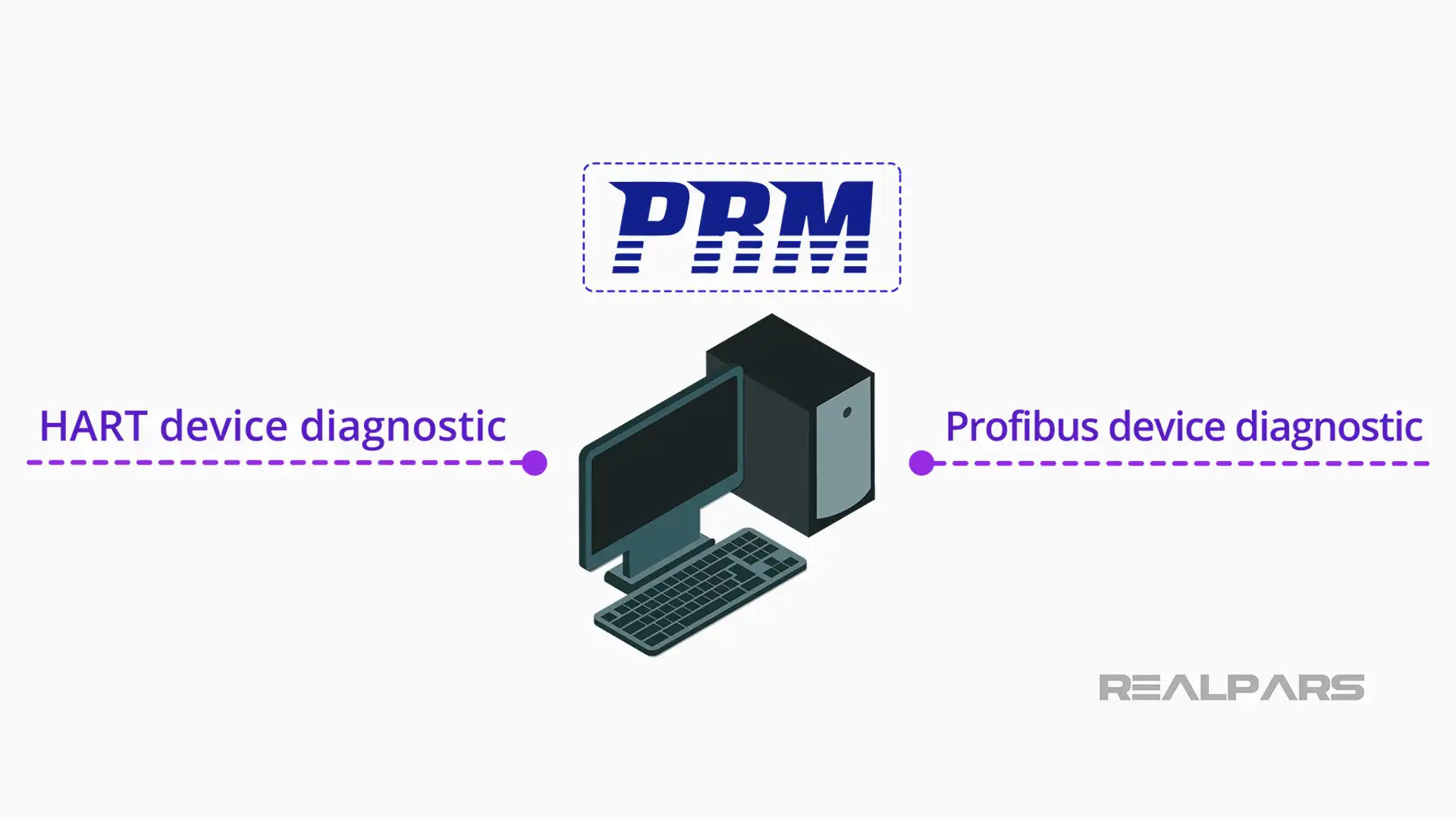
A unique 64 function USB keyboard is available for the CENTUM VP system.
Yokogawa DCS engineering software
The Automation Design Suite is Yokogawa’s engineering software. Plant graphics are easily created for Operator HIS terminals.
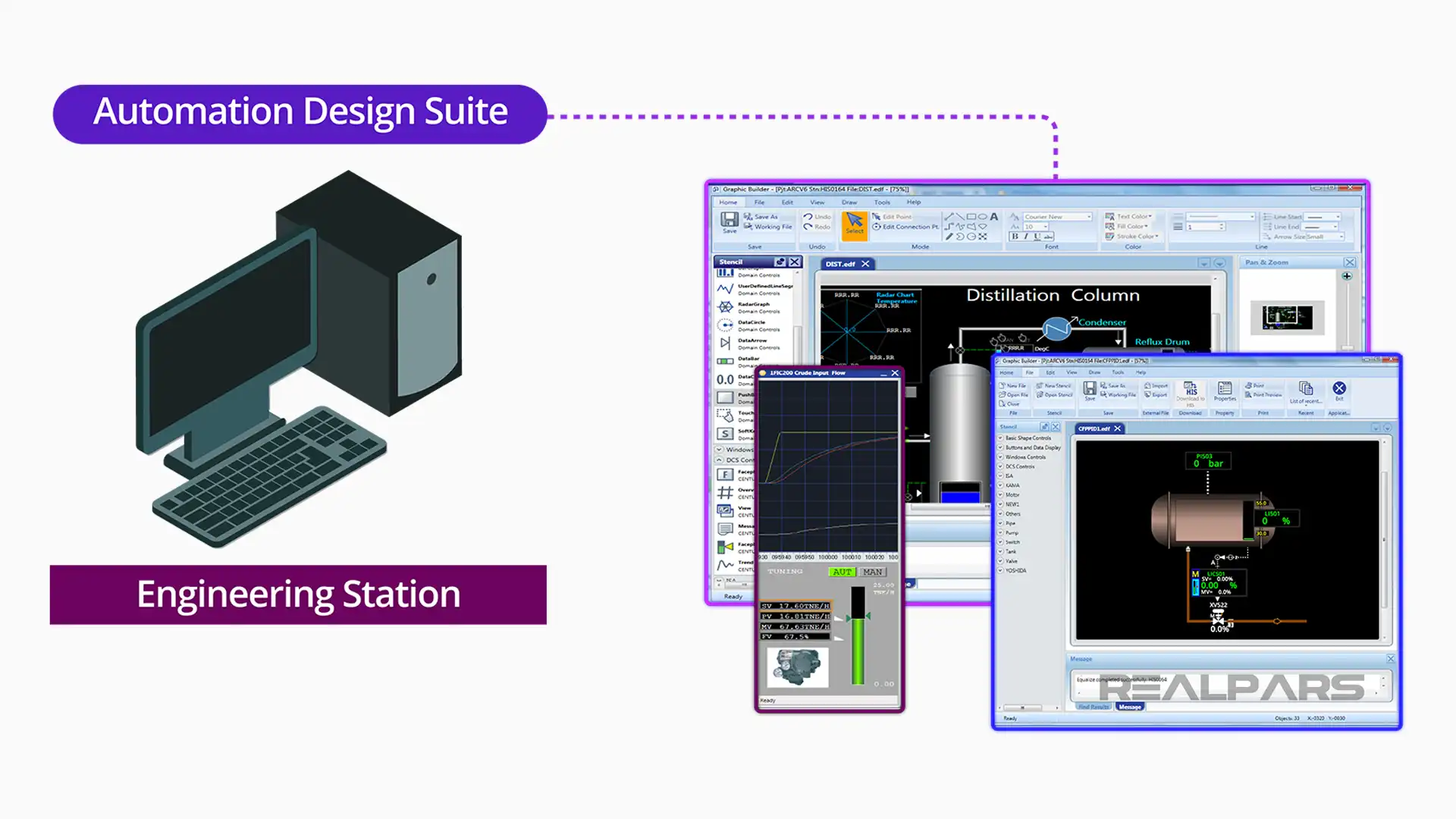
Here’s an example of an Operator HIS view. The graphic shows a pressure indication of 0 bar(g) on a vessel. A level controller LIC501 is shown at 0% and set to Manual. The output of the controller operates a valve XV522.
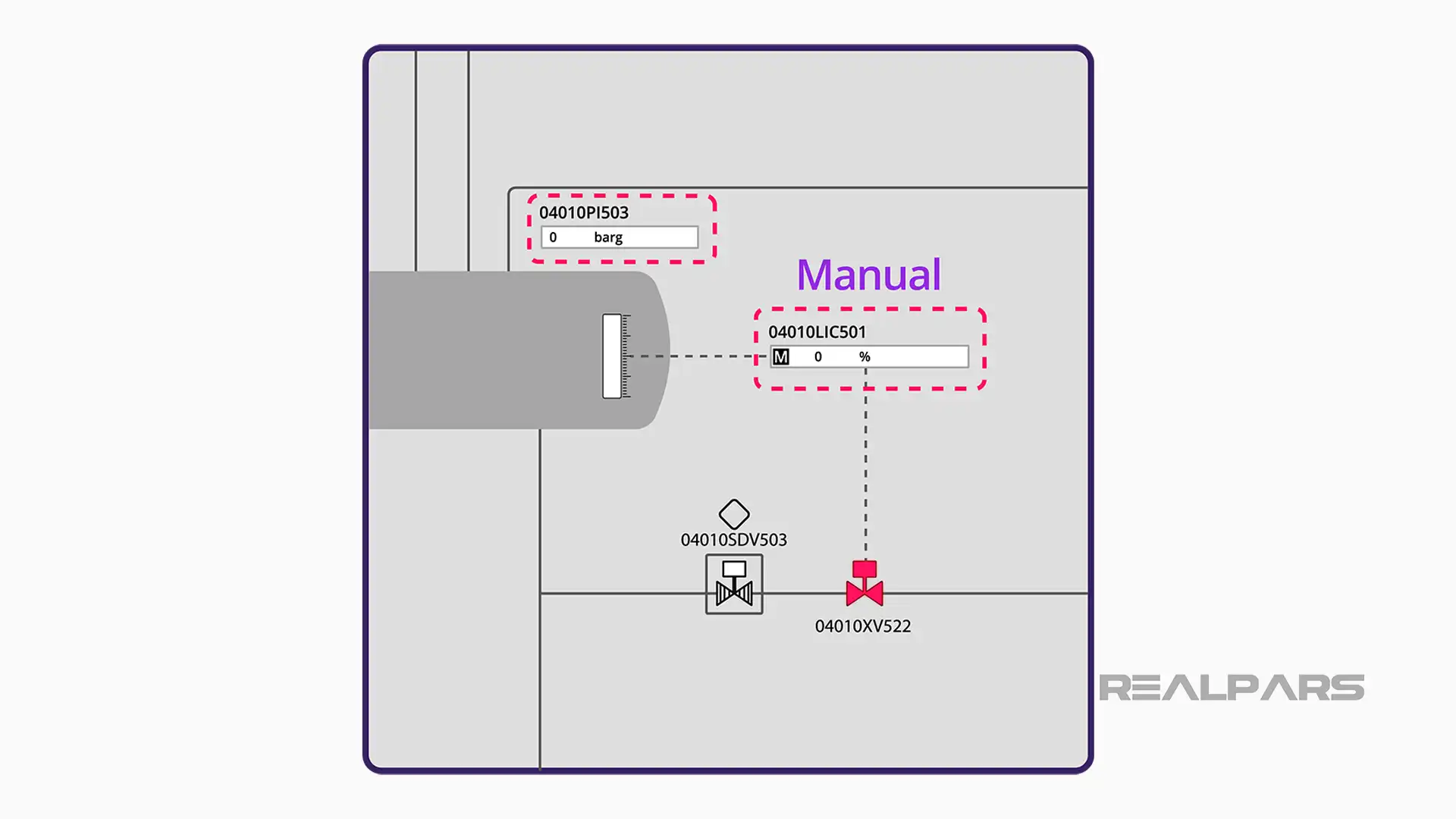
A simplified P&ID shows the level controller and the valve XV522.
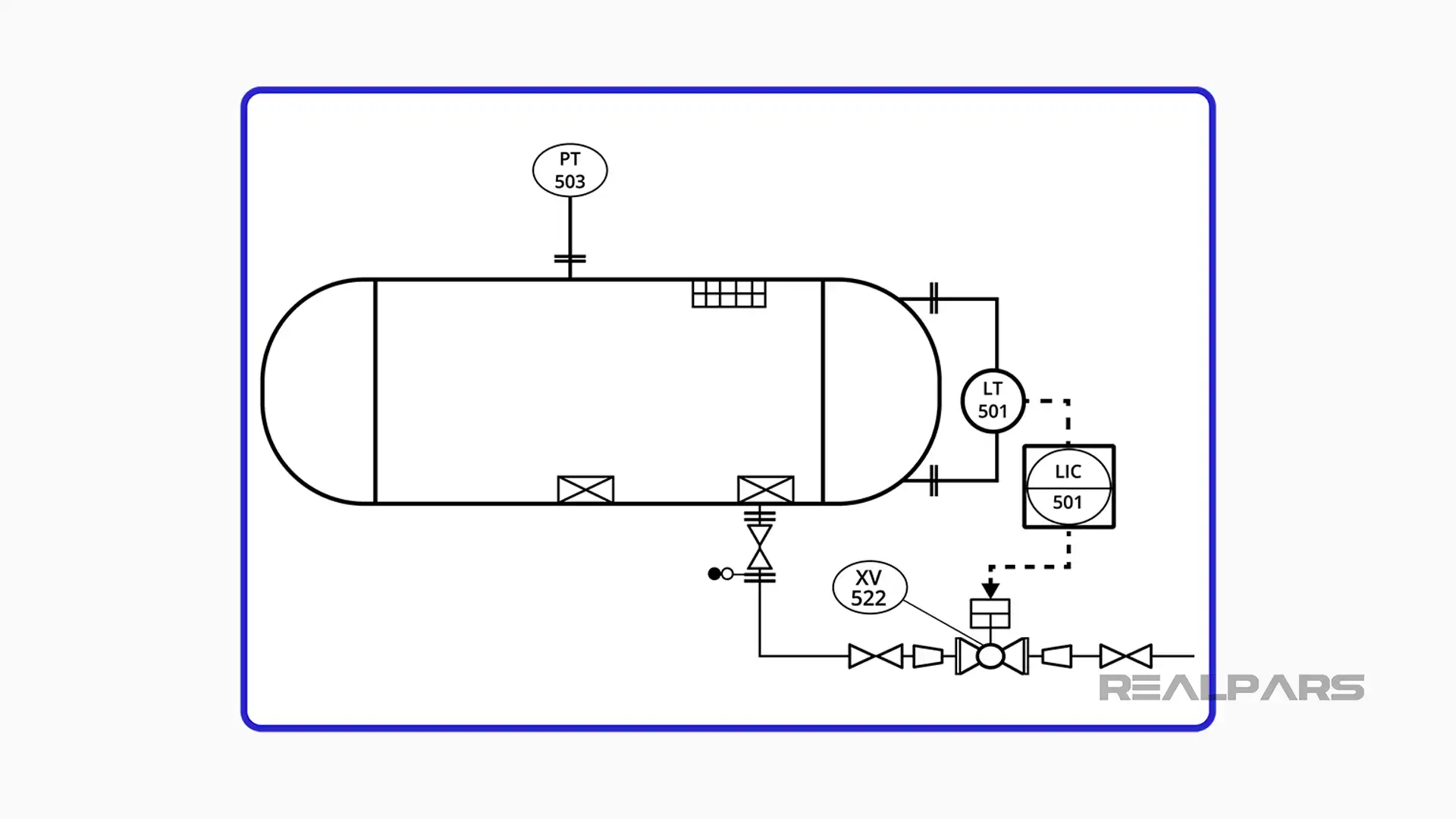
Going one step further, we’ve included a part of the loop diagram showing the 2-wire configuration for the Level Transmitter LT501. The FIO analog input module is an AAI143-H that has 16 channels.
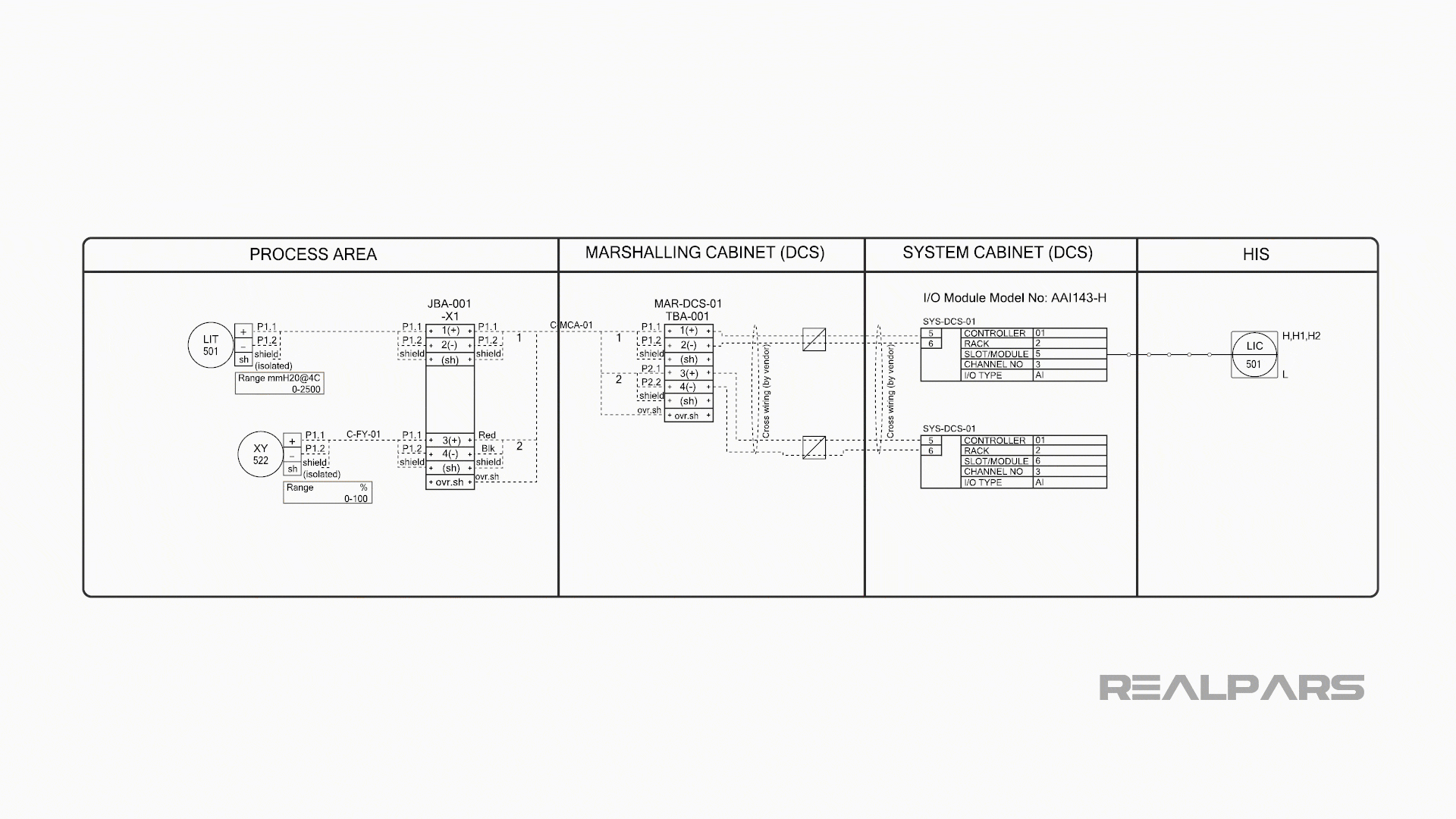
Summary
Ok… let’s summarize what we’ve discussed:
– Yokogawa has been around since 1915 when it began by selling electric meters.
– Yokogawa introduced its first CENTUM DCS in 1975 and its current flagship version is CENTUM VP.
– The Field Control Station (FCS) provides the actual plant process control and contains the Power Supply, Controller, and the Field Input/Output modules.
– Yokogawa refers to each HMI as a HIS meaning Human Interface Station.
– All process information is placed on the control network called Vnet/IP and all CENTUM and devices are connected to this network.
– The orange-colored ProSafe-RS is a SIL3 safety instrumented system compatible with the CENTUM VP DCS.
– The Plant Resource Manager (PRM) is the Asset Manager software package facilitating the diagnostic capabilities of smart, or intelligent devices.
– The Automation Design Suite is Yokogawa’s engineering software.
We recommend checking the following related articles, if you haven’t already, to have a better understanding of Yokogawa DCS:
– What is DCS (Distributed Control System)?
– What is the Difference Between PLC and DCS?
– What is a Safety Instrumented System?
Got a friend, client, or colleague who could use some of this information? Please share this article.